Open Access
ARTICLE
Experimental and Numerical Investigation on High-Pressure Centrifugal Pumps: Ultimate Pressure Formulation, Fatigue Life Assessment and Topological Optimization of Discharge Section
1 School of Engineering, University of Québec in Abitibi-Témiscamingue (UQAT), Rouyn-Noranda, Québec, J9X 5E4, Canada
2 National Engineering School of Monastir, LGM, University of Monastir, Monastir, 5019, Tunisia
3 Department of Applied Mechanical Engineering, College of Applied Engineering, Muzahimiyah Branch, King Saud University, Riyadh, 11421, Saudi Arabia
* Corresponding Author: Haykel Marouani. Email:
(This article belongs to the Special Issue: Structural Design and Optimization)
Computer Modeling in Engineering & Sciences 2023, 137(3), 2845-2865. https://doi.org/10.32604/cmes.2023.030777
Received 22 April 2023; Accepted 10 July 2023; Issue published 03 August 2023
Abstract
A high percentage of failure in pump elements originates from fatigue. This study focuses on the discharge section behavior, made of ductile iron, under dynamic load. An experimental protocol is established to collect the strain under pressurization and depressurization tests at specific locations. These experimental results are used to formulate the ultimate pressure expression function of the strain and the lateral surface of the discharge section and to validate finite element modeling. Fe-Safe is then used to assess the fatigue life cycle using different types of fatigue criteria (Coffin-Manson, Morrow, Goodman, and Soderberg). When the pressure is under 3000 PSI, pumps have an unlimited service life of 107 cycles, regardless of the criterion. However, for a pressure of 3555 PSI, only the Morrow criterion denotes a significant decrease in fatigue life cycles, as it considers the average stress. The topological optimization is then applied to the most critical pump model (with the lowest fatigue life cycle) to increase its fatigue life. Using the solid isotropic material with a penalization approach, the Abaqus Topology Optimization Module is employed. The goal is to reduce the strain energy density while keeping the volume within bounds. According to the findings, a 5% volume reduction causes the strain energy density to decrease from 1.06 to 0.66 106 J/m3. According to Morrow, the fatigue life cycle at 3,555 PSI is 782,425 longer than the initial 309,742 cycles.Keywords
Cite This Article
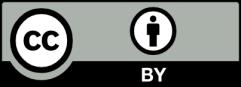