Open Access
ARTICLE
Investigation of the Severity of Modular Construction Adoption Barriers with Large-Scale Group Decision Making in an Organization from Internal and External Stakeholder Perspectives
Department of Civil Engineering, University of Southern California, Los Angeles, 90007, USA
* Corresponding Author: Muzi Li. Email:
(This article belongs to the Special Issue: AI and Machine Learning Modeling in Civil and Building Engineering)
Computer Modeling in Engineering & Sciences 2023, 137(3), 2465-2493. https://doi.org/10.32604/cmes.2023.026827
Received 27 September 2022; Accepted 07 March 2023; Issue published 03 August 2023
Abstract
Modular construction as an innovative method aids the construction industry in transforming to off-site construction production with high efficiency and environmental friendliness. Despite the obvious advantages, the uptake of modular construction is not booming as expected. However, previous studies have investigated and summarized the barriers to the adoption of modular construction. In this research, a Large-Scale Group Decision Making (LSGDM)- based analysis is first made of the severity of barriers to modular construction adoption from the perspective of construction stakeholders. In addition, the Technology-Organization-Environment (TOE) framework is utilized to identify the barriers based on three contexts (technology, organization, and environment). The Technique for Order Preference by Similarity to Ideal Solution (TOPSIS) and LSGDM models are both implemented for the first time to analyze the severity of the barriers to modular adoption based on questionnaire results from internal and external stakeholders in an organization. Finally, in this research, in-depth insights into the severity of barriers are gained, providing a reference for construction organizations to manage modular adoption.Keywords
Construction establishes the relationship between buildings and human-beings, creating space for various social activities. However, the construction industry is unlikely to step out of its comfort zone. Compared to other industries, reports have shown that less than 1% of revenues invest in technological innovation in the construction industry [1], which is lagging in turning to automation, sustainability, and technology-based collaboration. Existing conditions are pushing the construction industry to alter the inherent development model. The construction industry accounts for 40% of global environmental emissions, and advanced technology expects to alleviate this situation [2]. For society, low productivity is a common issue in the construction industry due to the shortage of workers, costs, and time overruns [3]. For the financial area, great revenue is generated by disrupting the surrounding environment at the expense of sustainability.
In addition, the government published regulations to put pressure on sustainable rectification in the construction industry. The EU and Canadian governments require greenhouse gas (GHG) emission reductions by placing more scrutiny on a project [4]. The US publishes Sustainable Materials Management (SMM) Strategic plans to encourage the use of secondary materials in the built environment [5]. The Paris Agreement [6] announced a 30% reduction in building energy consumption by 2030. More strict regulation pushes the construction industry to create strategies to mitigate the environmental burden. The increasingly strict environmental regulation makes the transformation of the construction industry compulsory.
The existence of modular construction will significantly ease the current situation. Modular construction, as an innovative and alternative method with high efficiency, plays a vital role in cleaner and technology-based production. The process of modular construction is mainly about off-site manufacturing and transporting elements from a factory to a site for assembly. Previous studies have proven that modular construction is the cleaner method. It relieves the environmental burden by decreasing the on-site working time [7]. Furthermore, the implementation of modular construction reduces construction waste and energy consumption [8,9]. In reference [10], the comparative analysis pinpointed 16%–24% energy reduction and 4%–14% energy saving in a modular method.
With its apparent advantages, modular construction has increasingly attracted the attention of different companies. Marriott, a hotel giant, began its research on modular construction in 2014 and launched a modular pilot initiative in 2015. After the launch of Marriott’s initiative, 31 low-rise hotels have opened with incorporated prefabricated guest rooms or restrooms. The coffee retail giant, Starbucks, established a location in Canada using an energy-efficient modular system. This building was completed in only six days, including building and assembling. For its global sustainability strategy, the coffee giant aims to utilize modular building techniques to achieve its energy-saving goal by 2023. According to the market report [11], the market size of modular construction is forecasted to increase to 108.8 billion in 2025.
Previous studies have concluded the advantages and barriers based on different contexts for modular construction. In this study, a large-scale group decision-making-based model was first utilized to evaluate the severity of the barriers faced by construction organizations. This study aims to contribute to sustainable and technology-based development in the construction industry by facilitating the adoption of modular construction and aiding stakeholders from construction organizations in transitioning their conventional methods to innovative, cleaner, and high-efficiency methods.
2.1 Modular Construction—An Overview of the Current Research
The debut of modular construction can trace back to the 1600s. Prefabricated three-dimensional elements are manufactured in factories and assembled as the main parts of buildings. Unlike the succession in conventional construction methods, construction activity can work simultaneously and 80%–95% [12] of activities can be completed in factories. Moreover, the specialty of modular construction methods results in tangible cost savings since less labor and equipment make on-site work [13]. The uniqueness of modular construction attracts multifaceted research.
For technology in construction, Thai et al. [14] mentioned that prefabricated benefits could maximize in high-rise buildings by increasing efficiency with lower cost. In addition, modular construction works as an empirical case to contextualize and verify a new model to promote the symbiotic development of innovative building technologies [15]. For the environment, one of the great virtues of prefabricated construction is lower emissions. Mao et al. [16] proved that the embodied emission of building materials could be reduced by 86.5% compared with traditional construction. The specialty of modular construction aids the industry in achieving a circular economy. Prefabricated elements are easier to demolish, recycle and reuse [17], which fits the ‘cradle to cradle’ definition. Previous research has also used geographic regions as a criterion to investigate development barriers in different countries. Wuni et al. [18] found 120 barriers in 15 countries. The Decision-Making Trial and Evaluation Laboratory (DEMATEL) method has been used to analyze the interrelationships between barriers in Germany [19]. Gan et al. explored the interaction of hindering prefabrication factors by using fuzzy cognitive maps in Chongqing, China [20].
This research aims to stimulate modular construction by acquiring barrier information from insider and outsider perspectives in an organization. TOE, TOPSIS, and LSGDM (Large-Scale Group Decision Making) work cooperatively to analyze the severity of the barriers faced by organizations. TOE is utilized for technology adoption in companies, TOPSIS is a practical and valuable tool for the importance of barriers, and LSGDM deals with aggregating information and assisting decision-making.
2.2 TOE (Technology-Organization-Environment Framework)
The TOE framework was proposed in 1990. The TOE model is implemented for identifying barriers based on three contexts (Technology, Organization, and Environment) of technology adoption in organizations [6]. Previous research also noted that the TOE framework and the Diffusion of Innovation (DOI) theory [21,22] are mainly used for IT adoption [22].
Compared with DOI theory, TOE includes all the contexts from DOI and is more comprehensive. In this research, TOE provides a complete analysis of modular construction adoption.
Oliveira et al. [23] summarized the application of TOE in various examples and considered the TOE framework a reliable empirical tool. The application process of the TOE is a comprehensive analysis method based on three contexts of organizations. In more detail, three significant factors, Technological (T), organizational (O), and environmental (E) contexts (Fig. 1), are associated with the following things [24].
Figure 1: Technology, organization, and environment framework
The technological context includes the feasibility and characteristics of the technology adoption.
The organizational context incorporates a firm’s structure.
The environmental context refers to industries, markets, and regulation characteristics.
2.2.2 TOE and Modular Construction Barriers
Modular construction is an innovative technology for construction organizations. The TOE implementation in this research can assist in classifying barriers and provide a better understanding of the challenges emerging during modular adoption. First, a literature review of modular adoption in construction organizations is conducted. Then, challenges are identified through the TOE framework based on three contexts.
The technological barriers include inflexibility, aesthetics, and quality, and the organizational challenges include upfront costs, knowledge and expertise shortage, manufacturing capacity, logistics and communication, and cooperation issues. Finally, the environmental barrier group includes negative stigma and lack of regulations. Table 1 summarizes the TOE elements and the barriers.
The technological context includes inflexibility, aesthetic issues, and quality. Barriers to broader adoption stem from inadequate and immature construction technology, which challenges the wider use of modular construction. The software used for modular construction lacks customization, cannot work like AutoCAD (commercial computer-aided design) and freezes at the early stages [44], which means that further modification is not allowed. An early design freeze requires more time for preparation since decisions need to be made at an early stage [45]. Moreover, the deficiency reduces the aesthetic appeal and impedes the creativity of architects and building designers [46,47].
Industrialization in construction enables organizations to offer a broader portfolio of products. However, the standardized production mode causes similarity, monotony, and repetition [27]. In this way, the aesthetic value overshadows since the appeal of building aids perpetuates culture [28]. Another challenge that involves modular construction aesthetics is the clients. Therefore, modular construction needs to promote the technical system to be more open to innovation from clients instead of immutable design [29].
The last point in the technology context is quality. Although the quality requirement is not strictly associated with technology, it positively correlates with technology and plays an important role in persuading customers. Existing successful examples of fully modular houses are largely low-rise buildings. On the other hand, limited high-rise buildings are modular construction. Moreover, the inherently topological modular form of modular construction will maximize if it can successfully operate in high-rise buildings [24]. However, facing wind loads and typhoons, the ability of the external envelope of a modular building is considered a critical concern to avoid leakage in typhoons [14]. Overall, there is a lack of professional labs and expertise [44], which helps to prove the capabilities of providing solid and safe structures. For modular adoption, Goodier et al. [31] suggested that more initial costs should include the investment in increasing quality.
The organizational context includes factors and issues related to a company’s internal focus. In this section, barriers are illustrated based on the four aspects of finance, knowledge, manufacturing capacity, and logistics.
For financial constraints, unlike conventional methods, the modular construction startup has a high cost. For the appropriate machinery and prefabrication yards, the upfront costs include the purchase of all the material at the beginning of a project [47]. The capital cost of modular construction is 25% higher than that of the traditional method [33], which weakens one of the obvious advantages of the modular method [48].
Because of the lower familiarity with modular construction, SmartMarket report disclosed [49] severe conflicts that resulted from inefficient communication between stakeholders. In addition, the qualified labor shortage ultimately affects project completion. Experienced supervisors are scarce resource [36], resulting in project management risk. Inadequate knowledge and scarce experience cause inefficiency and delay modular development.
In the construction industry, the manufacturing capacity is in a backward position compared with other industries. As a result, the speeding up of modular construction demands cannot be satisfied [35]. The existing supply chain of modular construction fails to fulfill the requirements [38]. Moreover, a few firms own the patents on prefabrication technology and dominate the market [39], which negatively influences the expansion of modular construction.
There is another challenge in adopting modular construction due to logistical barriers. Logistic access is considered a critical barrier to implementing modularization [40]. Because of the legal height limits in countries, the shape of volumetric prefabrication increases transportation difficulty, especially in dense urban areas [9]. Another factor that makes organizations hesitate to invest in modular construction is the transportation cost. Prefabrication factories are usually located in remote areas for cheaper costs [50], resulting in an increase in transportation costs [49] since the average cost per module square footage is related to the distances [34].
In conventional construction methods, stakeholders take sole responsibility. Compared with conventional construction, modular construction emphasizes the holism of a project. Therefore, active communication and collaboration are essential during the complex management of modular construction [13]. However, with the accustomed interdependence, coordination and communication between parties are scarce, resulting in the slow adoption of modular construction [42].
The environmental barrier includes market perception and the regulatory environment. The stereotypes about modular construction severely affect its market. Failure or low-equality products are comments used by customers to describe modular construction products [42]. Due to the effects of the booming modular construction after World War II, the public perceives prefabricated houses as low-income housing [43]. Lower public confidence is responsible for the limited market share of modular construction [51].
For the regulatory environment, government codes and standards are insufficient [35]. The need for more monitoring from authorities hinders the broader use of modular methods. The small quantities of incentive measures from the government fail to encourage further modular construction [52]. Without comprehensive regulation and monitoring, there is a crisis of confidence, and the credibility of suppliers is challenge [53]. In addition to the scarcity of regulation, the process of acquiring approval takes a longer time compared to conventional methods because of the unfamiliarity of the modular construction process [40].
The TOE framework analyzes the barriers to adopting modular construction in an organization instead of the macro perspective used in the previous research. In the next section, the methodology for exploring the barriers in firms is introduced to exhibit the severity of barriers from internal and external stakeholder perspectives. As shown in Fig. 1.
The process of this exploratory research presents in the following flowchart (Fig. 2):
Figure 2: The process of research
3.1.1 Questionnaire Participants
Internal and External Stakeholders
This study separates stakeholders in construction projects into internal and external stakeholders. The internal stakeholders are practitioners who provide financial support and have direct contact with the projects [54]. The other group, external stakeholders, are outsiders to the project and have limited but not ignored influences on the project [54]. The role of internal stakeholders is the actual project participants: designer, contractor, project leader, and subcontractor; external stakeholders can be the local and national authority, society, the media, the general public, and others [50]. Briefly, internal stakeholders are suppliers, and external stakeholders are consumers. They both have an impact on modular adoption in organizations.
To better understand the severity of the barriers faced by construction organizations, two different surveys are designed for the two groups of internal and external stakeholders. The participating internal stakeholders include real estate investors, designers, constructors, and researchers. The external group includes various industries, including media, government, and others.
Section 2 summarizes the barriers to modular adoption. Ten barriers are selectively distributed in two questionnaires for internal and external stakeholders. The internal stakeholders, ass construction practitioners, are asked to examine all the summarized barriers
3.1.3 Survey Participant Weights
(1) The index system of internal stakeholder weights
This study develops an index system to analyze the weight of internal stakeholders based on two criteria, work experience and educational background. For the two criteria, the value positively correlates with the information’s reliability. The higher the value is, the more reliable the information that can be provided is. Construction enterprises have been interviewed with these two criteria. There is a consensus among them that these three elements can be used as qualifiers to decide the weight value of internal participants. In Section 4, the theory of TOPSIS analysis is introduced and used to assign weight to internal stakeholders.
(2) The index system of external stakeholder weights
External stakeholders are outsiders in the construction process. However, their evaluation still can affect the adoption of modular construction, and it is necessary to calculate their importance weight. The details of external stakeholder weights are introduced in Section 4.
3.2 The Model for the Degree of Modular Construction Barriers
For stakeholder evaluations of the degree of the summarized barriers, this research uses the Inter-valued 2-tuple linguistic information model to replace linguistic information. Compared with language phrases, the inter-valued 2-tuple linguistic information tool is better at presenting indecisiveness and the uncertainty of acquired information. Thus, the accuracy of information collection is improved.
The result often deviates from the initial expression during the process of collecting linguistic information. In order to improve the accuracy of the collected information, a 2-tuple fuzzy linguistic representation model was published in reference [55] to narrow the deviation. Based on this, Lin et al. [56] further proposed the Interval-Valued 2 tuple Linguistic Information model. In the following section, the principles of these two models are introduced.
(1) 2-Tuple Linguistic Representation Model
The term 2-tuple means using (
Definition 1 Letting S = {
Round (·) means round up to the nearest integer.
2-tuple (Si,α) can return to β ∈ [0, g] by using the
For the relationship between 2-tuples (
• If i < j, then (
• If i < j, then (
• If i = j, there are three situations:
• If
• If
• If
(2) Interval-Valued 2-Tuple Linguistic Information Model
Because of hesitation and uncertainty, the linguistic information from participants often falls between two 2-tuple linguistic information, and the single 2-tuple linguistic needs to accurately express the linguistic information. To eliminate these effects, a more accurate model, the interval-valued 2-tuple linguistic information model, was proposed by Sun et al. [32] for presenting information between two linguistic terms.
Definition 2 Letting S = {
Definition 3 To compare the relationship between a = [(
Based on the function, the rule of a = [(
If S(a) > S(b), then a > b;
If S(a) < S(b), then a < b;
If S(a) = S(b), then:
If H(a) > H(b), then a < b;
If H(a) < H(b), then a > b;
If H(a) = H(b), then a = b.
(3) The Rule——From Linguistic Information to a 2-Tuple Linguistic Model
The Linguistic Term
This section describes how the questionnaire is designed to investigate the severity degree of barriers
This research sets the linguistic term set S to illustrate the degree of participant evaluation,
S = {
The meaning of the linguistic term in set S is:
For convenience, the linguistic terms are assigned with various percentages, which can be seen in Table 3.
The Transition Formula
In the questionnaire, participants are asked to define the degree of the barrier. The percentage is a measure used to express the content of participant evaluation. The a% is the extent of barriers from participant opinions and can be transferred to 2-tuple linguistic information by using the following transformation rule:
Rule: Transform ‘a%’ to 2-tuple linguistic information
INT Represents the Integral Function
(4) The Transition Processes
In the questionnaire, participant evaluation is collected in the following two steps:
• Participants evaluate the severity degree of one of the barriers according to S = {
• If participants choose ‘impede’, then they need to determine the interval-value of the severity degree of barriers, [a%, b%], according to 0%–100%, the a% is defined to be less than b%.
According to the transformation rule, the interval degree [a%, b%] can transform to 2-tuple linguistic information. For example, if the evaluation for the degree of
Section 3.1.1 describes how targeted participants are divided into two groups, external and internal stakeholders. To improve the reliability of results, internal stakeholders are practitioners with expertise from the construction industry. External stakeholders are consumers, and their workplaces include the media, government, and others.
The data are collected from the questionnaire method. With this method, the number of effective samples is 106. The number of internal stakeholders is 62, and the number of external stakeholders is 44. The composition of samples is as follows. For the number of internal stakeholders, the number of real estate investors and designers is 13, and the numbers of constructors and researchers are 16 and 20. Of the 44 external stakeholders, the number of media and government personnel is 10, and the number of others is 24. As show in Fig. 3.
Figure 3: The number of internal and external stakeholders
3.4 Data Reliability and Validity Test
The questionnaire’s content for internal stakeholders is associated with the severity of barriers to modular adoption. There is a specific correlation and consistency among the questions. Therefore, the data from internal stakeholders can apply reliability and validity tests. However, for external stakeholders, the details in the questionnaire are different for internal stakeholders. Since four different questions are evaluated with the questionnaire, the content in the questionnaire needs to be more qualified for reliability and validity testing for the data from external stakeholders. The content of external stakeholders is illustrated in the following four aspects:
1. The acceptance degree of modular construction
2. The knowledge degree of modular construction
3. The deficiency degree of related regulation in modular construction
4. The publicity degree of modular construction
Overall, in this research, only the data from internal stakeholders are qualified for the data reliability and validity testing. The following section contains the result of the reliability and validity testing.
Cronbach’s alpha is a standard measure for testing the reliability of data. The value of Cronbach’s alpha represents the extent of reliability of data. Cronbach’s alpha usually falls between 0 and 1. When the value is less than 0.6, it proves the internal consistency is insufficient, and when the value is more significant than 0.7, the data is very reliable. When the value is over 0.8, it means that brilliant data is collected. The details of the evaluation of Cronbach’s alpha are given in Table 4 below.
N = Number of components
For the result of the reliability test of internal stakeholders, the value of α is 0.904, which shows excellent reliability. It means that the acquired data are qualified enough to provide reliable information. The following Table 5 shows the details.
The data validity test mainly includes Content-related Validity and Construct-related Validity. Content-related Validity is implemented to test the appropriate degree of content. The questionnaire’s content is designed based on the excellent index system and associated research content in this research. In this way, a guaranteed preference can be provided in this research to stakeholders.
Construct-related Validity represents the consistency between the theory and experiment. It can be used to test whether a sample qualifies for the factor analysis. KMO (Kaiser-Meryer-Olkin) and Bartlett’s test are standard methods used to measure whether variables are suitable for factor analysis. The evaluation criteria are illustrated in the following Table 6. The KMO value usually falls in the range of 0–1, and the relevance is low and unsuitable for analysis when the KMO value is close to 0. When the value KMO reaches 0.8, the sample data is qualified for analysis. Bartlett’s test tests whether the sample has equal variances to test the validity of the sample data.
For the result of the validity test of internal stakeholders, the value of KMO is 0.702. This shows good validity. The following Table 7 shows the details.
According to the tests, the acquired data is proven to have high reliability and validity and is qualified for further analysis.
4 The Individual Importance of Participants
The degree of barriers to modular construction adoption is transformed from linguistic information to interval 2-tuple linguistic information, as discussed in Section 3. This section discusses how the weight values of participants are determined.
4.1 The Details of the Data Collected from Internal and External Stakeholders
4.1.1 The Detail Information from Internal Stakeholders
The internal participants are all from the construction industry. The same work background is used as a qualifier to select the related information to define the importance of internal participants. This section describes how the three criteria of work experience (T1), and educational background (T2), are chosen to measure the weight value of the participating individuals. The higher the value is, the more reliable the information is.
(1) Work Experience (T1)
The 62 sample results for work experience (T1) are shown in the following Table 8 and Fig. 4. Twenty of the participants have more than five years of experience, and seven of the twenty participants have more than ten years of experience. Twenty-one percent of the participants have more than five years of experience and less than ten years of experience.
Figure 4: The proportions for work experience
(2) Educational Background (T2)
For the last factor, educational background, 92% of participants have bachelor’s degrees and above. Twenty-two internal stakeholders have master's degrees, and two participants have doctoral degrees. As show in Table 9 and Fig. 5.
Figure 5: The proportions for education
4.1.2 The Detail Information from External Stakeholders
For external stakeholders, their impact on modular construction adoption cannot be ignored. In addition, external participants with various characteristics from different backgrounds make it difficult to define the criteria to measure the importance of participants. In this section, educational background is the criterion for assigning weights. Over 93% participants have bachelor and above degree. As show in Table 10 and Fig. 6.
Figure 6: The proportions for education
4.2 The TOPSIS Method Introduction
TOPSIS (Technique for Order Preference by Similarity to an Ideal Solution) was initially developed by Hwang et al. [57]. Since TOPSIS is flexible enough to handle various kinds of data, it has become a standard method for decision-making. The concept of TOPSIS is identifying the distance between alternatives and ideal solutions. The alternatives should have the shortest distance for positive ideal solutions and the longest distance for harmful ideal solutions [57]. Then the TOPSIS method utilizes the positive and negative ideal solutions to calculate participants’ weights. The following content introduces the detailed process of TOPSIS.
In the TOPSIS method, it is assumed that the total number of alternatives is m, and n is the number of attributes that are used to evaluate m. This can be regarded as a geometric system that has m points in the n-dimensional space [57].
Step 1: The A = matrix
i (i = 1,2…,m), j (j = 1,2,….,m).
Step 2: Benefit attributes are chosen according to the type of attribution in this research. The process consists of rescaling the value of attributes and transforming the attributes to benefit attributes.
M = Max {|
Step 3: Normalization: Matrix C is normalized. Then Matrix Z represents the normalized result.
In the matrix, the formula of
In the formula, i = 1,2,…, m; j = 1, 2,…, n; 0
Step 4: The positive ideal solution
Step 5: The calculation of the distance between the alternatives and ideal solutions is performed.
The distance between alternative pi and
The distance between alternative pi and
Step 6: The calculation of the comparative distance of the alternatives and positive ideal solution is performed:
i = 1, 2,…, m, 0 ≤
4.3 The Values of Internal Stakeholder Weights
According to the three criteria, work experience (T1), and educational background (T2), the values of the weights of internal stakeholders are determined. Since the benefit attributes are chosen, the more experienced participants are considered to have larger weights. Table 11 lists the distance information for internal stakeholders 1–20.
The values of
In the formula, 0 ≤
4.4 The Weight Values of External Stakeholders
According to the education background, the Tables 13 and 14 list the distance information for external stakeholders by using TOPSIS method.
5 The Evaluation of the Modular Construction Barrier Based on LSGDM
Through previous studies, the evaluation of the degree of barriers in construction management is acquired. Based on the analysis discussed in Section 4, this section summarizes the information and makes an aggregation. LSGDM (Large-Scale Group Decision Making) is used to rank the barriers according to their severity and score.
5.1 Interval-Valued 2-Tuple Linguistic Information Model
The model and transition rules introduce in Section 3.2. These rules transform linguistic information into 2-tuple information using Rules 1 and 2 (Section 3.2). Part of the transformed information is shown in the following Tables 15 and 16.
The concept of interval-valued 2-tuple linguistic information is introduced in Section 3.2. In this section, the interval 2-tuple aggregation operator is illustrated to aggregate all the participant evaluations.
Interval 2-Tuple Aggregation Operator
Definition 4 Zhang [48] proposed the IVTWA (Interval-Valued 2-tuple Weighted Average), letting I = {[(
The Δ and
In this research, Set S = {
According to the information, the degree of barriers is shown in Tables 3–5 below:
(1) Internal Stakeholders
According to Tables 17 and 18, the ranking order is
The second place is logistics
The Manufacturing capacity (
Lack of knowledge and expertise
Moreover, Coordination and communication (
Figure 7: The degree of barriers and ranking orders from internal stakeholders
(2) External Stakeholders
The highest severity is Regulation
Figure 8: The degree of barriers from external stakeholders
Technology adoption needs to catch up in the construction industry. Additionally, the construction industry has gained a bad reputation for sustainability. Modular construction is an innovative method with great potential and is considered a feasible method to solve these issues. Modular construction enables off-site construction, industrialization, sustainability, and technological advancement in the construction industry. Given these benefits, the adoption rate of modular methods could be better than expected. The main objective of this study is to evaluate the severity of the application barriers and assist organizations in managing the obstacles to stimulate modular adoption.
The barriers impeding the adoption of modular technology for construction are identified based on the theory and the TOE framework. Then two different questionnaires are designed to collect information from internal and external organizational stakeholders. Next, the TOPSIS analytics method calculates the importance of internal stakeholders. Finally, the application of LSGDM in research is used to determine the severity of modular barriers and the score of every barrier.
In order to facilitate the transition to modular construction in construction organizations, 106 valid samples were collected. The 2-tuple linguistic model replaces linguistic information to collect more accurate information. After the unbiased analysis, valuable data are secured. Internal and external stakeholders reach a consensus on the severity of the policy barrier. The familiarity with modular construction among policymakers needs to increase. The policy system for modular construction needs further improvement. With higher capital costs than conventional methods, financial constraints are a daunting challenge for organizations to apply the modular method. In the technological context, the aesthetic issue caused by monotonous design has the lowest severity. Participants explain that the architectural design technology improvement has brought them the confidence to solve the issue.
From the stakeholder perspective, the awareness of modular construction needs to be stronger, which is attributed to the scarcity of publicity. However, in general, the attitudes of external participants towards modular construction are headed in a positive direction. Although the modular construction industry needs to catch up with the speed of innovative technology adoption in other industries to occupy the construction market quickly, the increasing momentum between internal and external stakeholders implies great potential in modular development.
One of the contributions of this research is the comprehensive evaluation of the obstacles impeding the modular construction adoption provided by internal and external stakeholders. Internal and external stakeholders have prominent roles in modular adoption in a construction organization and have voices to decide the development of the modular method. Therefore, their evaluation can reflect the attitudes toward modular construction and guide further development. In this way, this research can offer reliable preferences for decision-makers in organizations regarding modular construction adoption. The other contribution is that this is the first work to investigate the modular construction barriers from internal and external stakeholder perspectives by simultaneously using three analytic models, TOE, TOPSIS, and LSGDM. In the previous research, practitioners and experts in the construction industry were the primary respondents, and external stakeholders were rarely considered. In addition, questionnaires are generally used for modular adoption, but only some research studies have combined various models to investigate the acquired data. In this research, three methods, TOE, TOPSIS, and LSGDM, are utilized to provide more accurate and reliable information to analyze the status quo of modular construction applications and assist the stimulation of further development.
The limitations of this study are regional issues associated with organizations. Since regulation varies with countries, more detailed research should be done to encourage wider modular construction adoption in organizations in different places. Another limitation is that some countries have a comparatively mature market for modular construction. In these countries, their deficiency focuses on aspects that are different from modular construction markets for these countries at the emerging stage. In this way, the challenges for modular adoption in organizations vary with the comprehensive extent of the market. Therefore, further detailed research needs to be explored to increase modular adoption in organizations.
Funding Statement: The author received no financial support for the research, authorship, and/or publication of this article.
Availability of Data and Materials: The datasets used and/or analyzed during the current study are available from the corresponding author on reasonable request.
Conflicts of Interest: The author declares that they have no conflicts of interest to report regarding the present study.
References
1. Agarwal, R., Chandrasekaran, S., Sridhar, M. (2016). Imagining construction’s digital future. McKinsey&Company. https://www.mckinsey.com, https://www.mckinsey.com/capabilities/operations/our-insights/imagining-constructions-digital-future [Google Scholar]
2. IPCC (2022). Mitigation of Climate Change Climate Change Working Group III Contribution to the Sixth Assessment Report of the Intergovernmental Panel on Climate Change. [Google Scholar]
3. Graham, A. (2022). Construction Industry Labor Report 2022: Shortages, Earnings, and Conditions. [Google Scholar]
4. Kylili, A., Fokaides, P. A. (2017). Policy trends for the sustainability assessment of construction materials: A review. Sustainable Cities and Society, 35, 280–288. https://doi.org/10.1016/j.scs.2017.08.013 [Google Scholar] [CrossRef]
5. EPA (2017). US EPA. https://www.epa.gov/ [Google Scholar]
6. UNFCCC (2015). The Paris Agreement. United Nations Framework Convention on Climate Change; United Nations. https://unfccc.int/process-and-meetings/the-paris-agreement/the-paris-agreement [Google Scholar]
7. Lawson, M., Ogden, R., Goodier, C. (2014). Design in modular construction. https://doi.org.10.1201/b16607 [Google Scholar] [CrossRef]
8. Cao, X., Li, X., Zhu, Y., Zhang, Z. (2015). A comparative study of environmental performance between prefabricated and traditional residential buildings in China. Journal of Cleaner Production, 109, 131–143. https://doi.org/10.1016/j.jclepro.2015.04.120 [Google Scholar] [CrossRef]
9. Jaillon, L., Poon, C. S. (2009). The evolution of prefabricated residential building systems in Hong Kong: A review of the public and the private sector. Automation in Construction, 18(3), 239–248. https://doi.org/10.1016/j.autcon.2008.09.002 [Google Scholar] [CrossRef]
10. Hong, J., Shen, G. Q., Mao, C., Li, Z., Li, K. (2016). Life-cycle energy analysis of prefabricated building components: An input-output-based hybrid model. Journal of Cleaner Production, 112, 2198–2207. [Google Scholar]
11. Modular Construction Market by Type (Permanent, RelocatableMaterial (Steel, Concrete, WoodModules, End-Use (Residential, Retail & Commercial, Education, Healthcare, Office, Hospitalityand Region–Global Forecast to 2025 (2020). MarketsandMarkets. https://www.marketsandmarkets.com/Market-Reports/modular-construction-market-11812894.html?gclid=Cj0KCQjwguGYBhDRARIsAHgRm4- [Google Scholar]
12. Hsu, P. Y., Angeloudis, P., Aurisicchio, M. (2018). Optimal logistics planning for modular construction using two-stage stochastic programming. Automation in Construction, 94(926–5805), 47–61. https://doi.org/10.1016/j.autcon.2018.05.029 [Google Scholar] [CrossRef]
13. Rahman, M. M. (2014). Barriers of implementing modern methods of construction. Journal of Management in Engineering, 30(1), 69–77. https://doi.org/10.1061/(asce)me.1943-5479.0000173 [Google Scholar] [CrossRef]
14. Thai, H. T., Ngo, T., Uy, B. (2020). A review on modular construction for high-rise buildings. Structures, 28(2352–0124), 1265–1290. https://doi.org/10.1016/j.istruc.2020.09.070 [Google Scholar] [CrossRef]
15. Young, B. E., Seidu, R. D., Thayaparan, M., Appiah-Kubi, J. (2020). Modular construction innovation in the UK: The case of residential buildings. https://openresearch.lsbu.ac.uk/item/8q1x6 [Google Scholar]
16. Mao, C., Shen, Q., Shen, L., Tang, L. (2013). Comparative study of greenhouse gas emissions between off-site prefabrication and conventional construction methods: Two case studies of residential projects. Energy and Buildings, 66, 165–176. https://doi.org/10.1016/j.enbuild.2013.07.033 [Google Scholar] [CrossRef]
17. Karthik, S., Sharareh, K., Behzad, R. (2020). Modular construction vs. traditional construction: Advantages and limitations: A comparative study. Proceedings of the Creative Construction E-Conference 2020. https://doi.org/10.3311/ccc2020-012 [Google Scholar] [CrossRef]
18. Wuni, I. Y., Shen, G. Q. (2021). Developing critical success factors for integrating circular economy into modular construction projects in Hong Kong. Sustainable Production and Consumption, 29. https://doi.org/10.1016/j.spc.2021.11.010 [Google Scholar] [CrossRef]
19. Feldmann, F. G., Birkel, H., Hartmann, E. (2022). Exploring barriers towards modular construction–A developer perspective using fuzzy DEMATEL. Journal of Cleaner Production, 367(959–6526), 133023. https://doi.org/10.1016/j.jclepro.2022.133023 [Google Scholar] [CrossRef]
20. Gan, X. L., Chang, R. D., Langston, C., Wen, T. (2019). Exploring the interactions among factors impeding the diffusion of prefabricated building technologies. Engineering, Construction and Architectural Management, 26(3), 535–553. https://doi.org/10.1108/ECAM-05-2018-0198 [Google Scholar] [CrossRef]
21. Salwen, M. B., Stacks, D. W. (2009). An integrated approach to communication theory and research. New York: Ny Routledge. [Google Scholar]
22. Pan W., Gibb A. G. F., Dainty A. R. J. (2008). Leading UK housebuilders’ utilization of offsite construction methods. Building Research & Information, 36(1), 56–67. https://doi.org/10.1080/09613210701204013 [Google Scholar] [CrossRef]
23. Oliveira, T., Martins, M. F. (2011). Literature review of information technology adoption models at firm level. The Electronic Journal Information Systems Evaluation, 14(1), 110–121. [Google Scholar]
24. Tornatzky, L. G., Internet Archive (1990). The processes of technological innovation. Internet Archive. Lexington, Mass: Lexington Books. https://archive.org/details/processesoftechn0000torn [Google Scholar]
25. Shin, J., Moon, S., Cho, B., Hwang, S., Choi, B. (2022). Extended technology acceptance model to explain the mechanism of modular construction adoption. Journal of Cleaner Production, 342, 130963. https://doi.org/10.1016/j.jclepro.2022.130963 [Google Scholar] [CrossRef]
26. Zhai, X., Reed, R., Mills, A. (2013). Factors impeding the offsite production of housing construction in China: An investigation of current practice. Construction Management and Economics, 32(1–2), 40–52. https://doi.org/10.1080/01446193.2013.787491 [Google Scholar] [CrossRef]
27. Zhang, X., Skitmore, M. (2012). Industrialized housing in China: A coin with two sides. International Journal of Strategic Property Management, 16(2), 143–157. https://doi.org/10.3846/1648715X.2011.638945 [Google Scholar] [CrossRef]
28. Clarke, L., Wall, C. (2000). Craft versus industry: The division of labour in European housing construction. Construction Management and Economics, 18(6), 689–698. [Google Scholar]
29. Larsson, J., Eriksson, P. E., Olofsson, T., Simonsson, P. (2013). Industrialized construction in the Swedish infrastructure sector: Core elements and barriers. Construction Management and Economics, 32(1–2), 83–96. [Google Scholar]
30. Gibb, A., Isack, F. (2003). Re-engineering through pre-assembly: Client expectations and drivers. Building Research & Information, 31(2), 146–160. https://doi.org/10.1080/09613210302000 [Google Scholar] [CrossRef]
31. Goodier, C., Gibb, A. (2007). Future opportunities for offsite in the UK. Construction Management and Economics, 25(6), 585–595. [Google Scholar]
32. Sun, Y., Wang, J., Wu, J., Shi, W., Ji, D. et al. (2020). Constraints hindering the development of high-rise modular buildings. Applied Sciences, 10(20), 7159. https://doi.org/10.3390/app10207159 [Google Scholar] [CrossRef]
33. Mao, C., Xie, F., Hou, L., Wu, P., Wang, J. et al. (2016). Cost analysis for sustainable off-site construction based on a multiple-case study in China. Habitat International, 57(197–3975), 215–222. https://doi.org/10.1016/j.habitatint.2016.08.002 [Google Scholar] [CrossRef]
34. Salama, T., Moselhi, O., Al-Hussein, M. (2018). Modular industry characteristics and barriers to its increased market share. Modular and Offsite Construction (MOC) Summit Proceedings, pp. 2562–5438. https://doi.org/10.29173/mocs34 [Google Scholar] [CrossRef]
35. Tam, V. W. Y., Tam, C. M., Ng, W. C. Y. (2007). On prefabrication implementation for different project types and procurement methods in Hong Kong. Journal of Engineering, Design and Technology, 5(1), 68–80. [Google Scholar]
36. Gan, Y., Shen, L., Chen, J., Tam, V., Tan, Y. et al. (2017). Critical factors affecting the quality of industrialized building system projects in China. Sustainability, 9(2), 216. [Google Scholar]
37. Polat, G. (2008). Factors affecting the use of precast concrete systems in the United States. ASCE Library, 143(3), 3–169. https://doi.org/10.1061/(ASCE)0733-9364(2008)134:3(169) [Google Scholar] [CrossRef]
38. Blismas, N., Wakefield, R. (2009). Drivers, constraints and the future of offsite manufacture in Australia. Construction Innovation, 9(1), 72–83. [Google Scholar]
39. Luo, L., Mao, C., Shen, L., Li, Z. (2015). Risk factors affecting practitioners’ attitudes toward the implementation of an industrialized building system. Engineering, Construction and Architectural Management, 22(6), 622–643. https://doi.org/10.1108/ECAM-04-2014-0048 [Google Scholar] [CrossRef]
40. Choi, J. O., Chen, X. B., Kim, T. W. (2017). Opportunities and challenges of modular methods in dense urban environment. International Journal of Construction Management, 19(2), 93–105. [Google Scholar]
41. Salama, T., Moselhi, O., Al-Hussein, M. (2021). Overview of the characteristics of the modular industry and barriers to its increased market share. International Journal of Industrialized Construction, 2(1), 30–53. https://doi.org/10.29173/ijic249 [Google Scholar] [CrossRef]
42. Kamali, M., Hewage, K. (2016). Life cycle performance of modular buildings: A critical review. Renewable and Sustainable Energy Reviews, 62, 1171–1183. https://doi.org/10.1016/j.rser.2016.05.031 [Google Scholar] [CrossRef]
43. Nadim, W., Goulding, J. S. (2011). Offsite production: A model for building down barriers. Engineering, Construction and Architectural Management, 18(1), 82–101. [Google Scholar]
44. Shin, J., Choi, B. (2022). Design and implementation of quality information management system for modular construction factory. Buildings, 12(5), 654. https://doi.org/10.3390/buildings12050654 [Google Scholar] [CrossRef]
45. Xu, Z., Zayed, T., Niu, Y. (2020). Comparative analysis of modular construction practices in mainland China, Hong Kong and Singapore. Journal of Cleaner Production, 118861. [Google Scholar]
46. Aziz, S., Abdullah, M. R. (2015). Modular construction system in Malaysia: Issues for research in sustaining an affordable home project. Proceedings of Postgraduate Conference on Global Green Issues (Go Green), Malaysia. [Google Scholar]
47. Rahman, M., Sobuz, H. R. (2018). Comparative study of IPS & PPVC precast system–A case study of public housing buildings project in Singpore. Conference on Civil Engineering for Sustainable Development, KUET, Khulna, Bangladesh. [Google Scholar]
48. Zhang, H. (2012). The multiattribute group decision making method based on aggregation operators with interval-valued 2-tuple linguistic information. Mathematical and Computer Modelling, 56(1–2), 27–35. https://doi.org/10.1016/j.mcm.2012.01.001 [Google Scholar] [CrossRef]
49. Prefabrication and Modularization: Increasing Productivity in the Construction Industry (n.d.). https://www.nist.gov/system/files/documents/el/economics/Prefabrication-Modularization-in-the-Construction-Industry-SMR-2011R.pdf [Google Scholar]
50. Chan A. P. C., Oppong G. D. (2017). Managing the expectations of external stakeholders in construction projects. Engineering, Construction and Architectural Management, 24(5), 736–756. https://doi.org/10.1108/ECAM-07-2016-0159 [Google Scholar] [CrossRef]
51. Gan, X., Chang, R., Zuo, J., Wen, T., Zillante, G. (2018). Barriers to the transition towards off-site construction in China: An Interpretive structural modeling approach. Journal of Cleaner Production, 197, 8–18. [Google Scholar]
52. Yang, Y., Pan, M., Pan, W. (2019). Co-evolution through interaction of innovative building technologies: The case of modular integrated construction and robotics. Automation in Construction, 107(926–5805), 102932. https://doi.org/10.1016/j.autcon.2019.102932 [Google Scholar] [CrossRef]
53. Schoenborn, J. (2012). A case study approach to identifying the constraints and barriers to design innovation for modular construction (Doctoral Dissertation). Virginia Tech. [Google Scholar]
54. Chinyio, E., Olomolaiye, P. (2009). Construction stakeholder management. In: Google books. John Wiley & Sons. https://books.google.com/books?hl=en&lr=&id=ptPD8zz-vTcC&oi=fnd&pg=PP2&dq=Construction+stakeholder+management&ots=BOKnZG-0Au&sig=eHhCdKfoOVYsqSHeTqJpKu7Q4Zg#v=onepage&q=Construction%20stakeholder%20management&f=false [Google Scholar]
55. Rodríguez, R. M., Martínez, L., Herrera, F. (2011). Hesitant fuzzy linguistic term sets. In: Wang, Y., Li, T. (Eds.Foundations of intelligent systems, pp. 287–295. Berlin, Heidelberg: Springer. https://doi.org/10.1007/978-3-642-25664-6_34 [Google Scholar] [CrossRef]
56. Lin, J., Lan, J. B., Lin, Y. H. (2009). Multi-attribute group decision-making method based on the aggregation operators of interval 2-tuple linguistic information. Journal of Jilin Normal University, 1, 5–9. [Google Scholar]
57. Hwang, C. L., Yoon, K. (1981). Multiple attribute decision making. In: Lecture notes in economics and mathematical systems, pp. 58–191. Berlin, Heidelberg: Springer. https://doi.org/10.1007/978-3-642-48318-9 [Google Scholar] [CrossRef]
58. Mao, C., Shen, Q., Pan, W., Ye, K. (2015). Major barriers to off-site construction: The developer’s perspective in China. Journal of Management in Engineering, 31(3), 04014043. [Google Scholar]
59. Zhang, W., Lee, M. W., Jaillon, L., Poon, C. S. (2018). The hindrance to using prefabrication in Hong Kong’s building industry. Journal of Cleaner Production, 204, 70–81. https://doi.org/10.1016/j.jclepro.2018.08.190 [Google Scholar] [CrossRef]
60. Wuni, I. Y., Shen, G. Q. (2019). Barriers to the adoption of modular integrated construction: Systematic review and meta-analysis, integrated conceptual framework, and strategies. Journal of Cleaner Production, 249(959–6526), 119347. [Google Scholar]
Cite This Article
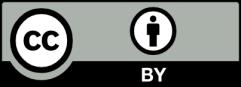