Open Access
PROCEEDINGS
High-temperature Fatigue Performance of Laser Directed Energy Deposited Ni-Based Superalloy Under Different Heat Treatment
1 State Key Laboratory of Fluid Power and Mechatronic Systems, Center for X-Mechanics, Department of Engineering
Mechanics, Zhejiang University, Hangzhou, 310027, China
2 School of Mechanics, Civil Engineering and Architecture, Northwestern Polytechnical University, Xi’an, 710129, China
3 Research & Development Institute of Northwestern Polytechnical Polytechinal University in Shenzhen, Shenzhen,
518063, China
* Corresponding Author: Zhenan Zhao. Email:
The International Conference on Computational & Experimental Engineering and Sciences 2023, 25(3), 1-2. https://doi.org/10.32604/icces.2023.010342
Abstract
The hot section components are usually in service under cyclic loading in an extreme working environment with high rotational speed at high temperatures, which is prone to fatigue failure. It is reported that fatigue related failures have accounted for over 50% of all failures of hot section components. Consequently, fatigue related failure at high temperature is one of the most important factors that shortens the service life of hot section components. Ni-based superalloy GH4169, similar as Inconel 718 (IN718), is a γ′′ and γ′ precipitation strengthened alloy. For decades, GH4169 superalloy keeps being an important material in hot section components of gas turbines. It has been widely used for producing the hot section rotating components of aeroengines, gas turbines and nuclear power plants owing to its high strength, creep resistance at high temperature (up to 650 °C).However, Ni-based superalloys are well known for their difficulty in machining due to its high hardness and toughness. Therefore, one of the alternative manufacturing processes is Laser Directed Energy Deposition (LDED), being one of additive manufacturing (AM) techniques. In this process, the laser beam creates a melt pool on a substrate material, into which the metal powder is blown by the inert gas flow from the co-axial powder nozzle at the same time. Moving the laser beam together with the powder nozzle will create a weld track, and multiple overlapping weld tracks leads to a layer while multiple layers can build a 3D structure. In recent years, the L-DED process has attracted full attention and been applied in modern industries such as fast prototyping, coating, light-weight optimization etc., due to its ability to fabricate geometrically complex components in near-net shape, and to repair damaged parts, which is of high interest for the production and maintenance of hot section components. In this case, understanding the fatigue properties of laser directed energy deposited (L-DEDed) Ni-based superalloy is expected to be a major concern in adaptation of AM technology into the turbine industry.
This study investigates the fatigue behavior of GH4169 Ni-based superalloy at 650 °C fabricated by L-DED and proposes an improved high-temperature fatigue resistance by regulating the heat treatment. To this purpose, three conditions of solution and aging heat-treated fatigue specimens, namely 980STA, 980S5hDA, and 1050STA, were assessed by advanced material characterization technique including TEM, EBSD etc. Results show that the fatigue resistance of the L-DEDed GH4169 with different heat treatments is mainly determined by the short crack propagation behavior, which is influenced by the combined effect of grain size and morphology. Finer grains with less texture strength of the 1050STA fatigue specimen has the longest short crack propagation life, while a cluster of large grains oriented to the <001> orientation of 980S5hDA leads to the most significant short crack propagation rate. Besides, the long fatigue crack propagation under the effect of strength and precipitates also minorly influence the fatigue resistance. The microstructure of interconnected precipitates including the needle-like δ phase and slender-stripe shaped Laves phase in 980STA and 1050STA specimens has a better hindering effect on the fatigue crack propagation than that of the discrete δ phase in 980S5hDA specimen, and the 1050STA specimen has the best strength. As a result, the 980S5hDA specimen has the worst fatigue performance, while the 1050STA specimen has the best. Compared to longer solution time, higher solution temperature can improve the fatigue resistance of the LDEDed GH4169.
Cite This Article
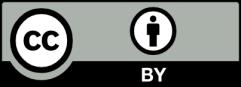