Open Access
ARTICLE
Wireless Self-Powered Vibration Sensor System for Intelligent Spindle Monitoring
1 Intelligent Sensing and Control of High-End Equipment Beijing International Science and Technology Cooperation Base, Beijing Information Science and Technology University, Beijing, 100192, China
2 Machinery Technology Development Co, Ltd., Beijing, 100044, China
3 Centre for Efficiency and Performance Engineering, University of Huddersfield, Queensgate, Huddersfield, West Yorkshire, HD1-3DH, UK
* Corresponding Author: Hongjun Wang. Email:
Structural Durability & Health Monitoring 2023, 17(4), 315-336. https://doi.org/10.32604/sdhm.2022.024899
Received 12 June 2022; Accepted 16 August 2022; Issue published 02 August 2023
Abstract
In recent years, high-end equipment is widely used in industry and the accuracy requirements of the equipment have been risen year by year. During the machining process, the high-end equipment failure may have a great impact on the product quality. It is necessary to monitor the status of equipment and to predict fault diagnosis. At present, most of the condition monitoring devices for mechanical equipment have problems of large size, low precision and low energy utilization. A wireless self-powered intelligent spindle vibration acceleration sensor system based on piezoelectric energy harvesting is proposed. Based on rotor sensing technology, a sensor is made to mount on the tool holder and build the related circuit. Firstly, the energy management module collects the mechanical energy in the environment and converts the piezoelectric vibration energy into electric energy to provide 3.3 V for the subsequent circuit. The lithium battery supplies the system with additional power and monitors’ the power of the energy storage circuit in real-time. Secondly, a three-axis acceleration sensor is used to collect, analyze and filter a series of signal processing operations of the vibration signal in the environment. The signal is sent to the upper computer by wireless transmission. The host computer outputs the corresponding X, Y, and Z channel waveforms and data under the condition of the spindle speed of 50∼2500 r/min with real-time monitoring. The KEIL5 platform is used to develop the system software. The small-size piezoelectric vibration sensor with high-speed, high-energy utilization, high accuracy, and easy installation is used for spindle monitoring. The experiment results show that the sensor system is available and practical.Keywords
Cite This Article
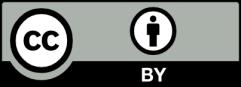