Open Access
ARTICLE
Study of Oil-Bearing Drill Cuttings Cleaning and De-Oiling Treatment Method for Shale Gas Reservoirs
1
School of Petroleum Engineering, Yangtze University, Wuhan, 430100, China
2
Key Laboratory of Drilling and Production Engineering for Oil and Gas, Wuhan, 430100, China
3
State Key Laboratory of Petroleum and Petrochemical Pollutant Control and Treatment, Beijing, 102206, China
4
China National Petroleum Group Safety and Environmental Protection Technology Research Institute Co., Ltd., Beijing, 102206,
China
5
Underground Gas Storage Branch, CNPC, Beijing, 100101, China
* Corresponding Authors: Shanfa Tang. Email: ; Yuanpeng Cheng. Email:
Energy Engineering 2023, 120(8), 1899-1917. https://doi.org/10.32604/ee.2023.027650
Received 07 November 2022; Accepted 28 February 2023; Issue published 05 June 2023
Abstract
Due to its extensive use in shale gas exploration and development, oil-based drilling fluids generate large amounts of oil-bearing drill cuttings during the drilling process. The large amount of oil-bearing drill cuttings generated during the drilling process can lead to serious secondary contamination. In this study, a wetting agent FSC-6 with good hydrophobic and oleophobic properties was synthesized to construct an efficient oil removal system. For the first time, the mechanism of this system was analyzed by using the theory of adhesion function, interfacial tension and wettability. At the same time, a combined acoustic-chemical treatment process was applied to the wastewater and slag generated after the cleaning of the oil-bearing drill cuttings. The experimental results show that the application of this pollution-free technology can effectively solve the environmental pollution and resource recovery problems of oil-bearing drill cuttings. It meets the standard of drilling chips with oil content less than 2% in SY/T7422-2018 “Oil-based drilling fluid drilling chips treatment system for oil and gas drilling equipment”.Keywords
Authors are encouraged to use the Microsoft Word template when preparing the final version of their manuscripts. In introduction, authors should provide a context or background for the study (that is, the nature of the problem and its significance). State the specific purpose or research objective of, or hypothesis tested by, the study or observation. Cite only directly pertinent references, and do not include data or conclusions from the work being reported. Due to the hydration characteristics of shale reservoirs, the horizontal section of shale gas wells is mainly drilled with oil-based drilling fluid, which generates oil-bearing drilling chips. Oil-bearing drill cuttings are mainly a mixture of oil-based drilling fluid and rock chips produced by on-site solids control equipment, recirculation tank bottoms and shake dry reduction equipment when drilling with oil-based drilling fluid, containing base oil, surfactants, inorganic salts, drill chips, sewage, asphalt and lignite additives, etc. [1–3]. On the one hand, oil-based drill cuttings are listed in the National Hazardous Waste List (2021 Edition) because of their oil content, and their utilization and disposal are more stringent than water-based drill cuttings; on the other hand, the oil-bearing drill cuttings contain 10%–30% oil and have the value of recovery and reuse [4]. At present, domestic and foreign countries mainly adopt reinjection of strata to achieve safe isolation of oil-bearing drill cuttings from the natural environment, or use thermal degradation and biodegradation to completely degrade various types of petroleum hydrocarbons to reduce the harm of oil-bearing drill cuttings to the environment [5,6].
The chemical thermal washing method reduces the viscosity of the oil phase by steam heating or direct heating of the oil-bearing drill cuttings, and then adds chemical degreasing agents to achieve oil-solid separation of the oil-bearing drill cuttings, and finally uses high-speed centrifuges to achieve rapid three-phase separation of oil, water and drill cuttings [7]. After separation and purification, the oil phase can be used as base oil for oil-based drilling fluid formulation. At present, there are few studies on the properties of hydrophilic and oleophilic wettability and adhesion function on the surface of oil-bearing drill cuttings, and there are deficiencies in the application of chemical hot washing technology in the treatment of oil-bearing drill cuttings, such as poor applicability of degreasing agents, large randomness in the selection of degreasing agents and lack of theoretical guidance in the development of new agents, which restrict the oil washing effect and application of chemical hot washing technology [8,9]. In contrast, the fluorocarbon chains of fluorocarbon surfactants are hydrophobic and oleophobic, and as wetting agents can change the wettability of the oiled drill chip surface, increase the contact angle of oil droplets on the chip surface, and facilitate the removal of oil droplets from the chip surface. The introduction of penetrating agents to reduce the surface tension and the addition of degreasing agents to enhance the compatibility can make the drilling chip oil more soluble in solution for the purpose of cleaning and oil recovery [10–13].
Therefore, this paper intends to develop an efficient cleaning agent that can effectively reduce the adhesion of drill chips surface and oil droplets by preferably introducing surfactants with moderate interfacial activity, constructing a system consisting of degreasing agent, penetrating agent and wetting agent, and optimizing the cleaning process through the combination of centrifugal and ultrasonic technology, so as to thoroughly solve the problems of difficult cleaning of oily drill chips and complicated treatment process of residual oil after cleaning.
Reagents: Perfluorohexyl sulfonyl fluoride, N, N-dimethyl-1,3-propanediamine, sodium chloroacetate, acetone, anhydrous ethanol, petroleum ether, analytical purity; degreasing agent CY-A, degreasing agent CY-B, degreasing agent CY-C, industrial grade; penetrant ST-A, penetrant ST-B, penetrant ST-C, industrial grade.
Instruments: EU-2600 UV spectrophotometer, Shanghai Onra Instruments Co., Ltd., China; 95-1 magnetic heating and stirring water bath, Guangdong Foheng Instruments Co. Bruker Instruments, Germany; Dataphysics OCA50 video optical contact angle meter, Dataphysics, Germany.
Sampling: Oil-bearing drill cuttings were taken from a shale gas reservoir in Sichuan with 10% oil content and 0.79% water content.
The synthesis of FSC-6 was carried out in two steps. 0.1 mol of N, N-dimethyl-1,3-propanediamine was placed in a three-necked flask, an appropriate amount of dichloromethane solvent was added under an ice bath, and a certain amount of triethylamine was added and stirred. 0.05 mol of perfluorohexyl sulfonyl fluoride was taken in a constant pressure dropping funnel and added slowly dropwise to the reaction system at 0°C. The reaction was carried out for 1 h and then the temperature was raised to 45°C for 2 h. After the reaction, the temperature was raised to 45°C for 2 h. The reaction was spun dry in a rotary evaporator, ethanol was added to dissolve the excess impurities and filtered, and the filtered material was dried and recrystallized by adding acetone to obtain a white solid perfluorohexyl sulfonamide. The synthesis of intermediate perfluorohexyl sulfonamide is shown in Fig. 1.
Figure 1: Synthesis of intermediate perfluorohexyl sulfonamide
The second step is the synthesis of the desired product betaine fluorocarbon surfactant FSC-6, the steps are as follows: take 0.1 mol intermediate perfluorohexyl sulfonamide in a three-necked flask, add an appropriate amount of ethanol solvent, heat and stir under oil bath conditions to dissolve all solids, take 0.12 mol aqueous sodium chloroacetate solution in a constant pressure dropping funnel, slowly add dropwise to the reaction system, add an appropriate amount of aqueous sodium hydroxide solution, adjust the reaction system to pH = 8.8, and adjust the reaction system to pH = 8.8 for 10 h. After the reaction is completed, cool to room temperature, dissolve non-solvent or unreacted impurities with ethanol, filter, add acetone and dissolve to recrystallize. The reaction system was adjusted to pH = 8.8 and the reaction was carried out at 70°C for 10 h. After the reaction was completed and cooled to room temperature, the non-solvent or unreacted impurities were dissolved with ethanol, filtered, and recrystallized by adding acetone to obtain the light yellow solid betaine fluorocarbon surfactant FSC-6. The synthesis of FSC-6 betaine fluorocarbon surfactant is shown in Fig. 2.
Figure 2: Synthesis of betaine fluorocarbon surfactant FSC-6
2.2.2 Structural Characterization of FSC-6
Fourier transform infrared spectroscopy (FTIR): The samples to be tested were prepared using the KBr press method, and the results were measured and recorded using a Tensor 2703040404 Fourier transform infrared spectrometer with a scan range of 400 to 4000 cm−1.
Nuclear magnetic resonance spectroscopy (1HNMR and 19FNMR): The samples to be measured were dissolved in D2O (heavy water) and measured using an Avance 500 NMR instrument with TMS (tetramethyllsilane) as an internal standard, with 1HNMR and 19FNMR frequencies of 500.13 and 470.5 MHz, in that order.
2.2.3 Determination of Oil Content
The oil content (w0) of oil-based drill cuttings was determined by the Soxhlet extraction method, and the main operation steps were as follows:
(1) Wrap about 10 g of oil-based drill cuttings sample with square filter paper, weigh the sample m′, and then place the sample in a Soxhlet extractor.
(2) Add petroleum ether solvent to the round bottom flask, and then connect the round bottom flask, the Soxhlet extractor and the reflux condenser in order from the bottom to the top.
(3) Heat the flask to about 85°C in a water bath to make the solvent sublimate and then condense in the extractor to extract the oil from the sample gradually, and reflux it to the flask when the amount of solvent has accumulated to a certain amount.
(4) Stop heating when the solution in the soxhlet extractor is colorless and transparent, then remove the sample and place it in the oven for drying, then weigh it (with filter paper) and record it as m″; and recover the extract solution for centralized treatment. The oil content w0 (%) of oil-based drilling rock chips can be calculated according to the following equation:
2.2.4 Drill Chip Cleaning Experiment
Chemical cleaning method: Using the preferred high-efficiency detergent formulation to clean the drill chips, taking the oil content of the treated chips as the index, the cleaning process is optimized by single-factor experimental method on the solid-liquid ratio, temperature, Ph, cleaning time, compounding ratio and concentration, etc., and the three-phase separation is realized by centrifuge after cleaning.
Ultrasonic-chemical detergent coupling method: The experiments were conducted by cleaning the drill chips with the selected detergent, and the oil content of the chips was taken as the index after treatment, and the ultrasonic cleaning power, cleaning time and mechanical stirring speed were optimized through single-factor experimental method, and the three-phase separation was realized by centrifuge after cleaning.
The fine-grained drill chips before and after the fluorocarbon surfactant treatment were compressed into flakes using a flake press, and the contact angle on the drill chip surface was measured with a needle absorbing deionized water and n-hexadecane under a video optical contact angle measuring instrument to determine the hydrophilicity and lipophilicity of the chips.
3.1 Infrared Characterization of Fluorocarbon Surfactants
The FT-IR, 1H-NMR and 19F-NMR spectra of the target products were determined by Fourier transform infrared spectroscopy and nuclear magnetic resonance for the graphical analysis of FSC-6.
The FTIR spectrum of FSC-6 is shown in Fig. 3, which shows that: 3,448.98 cm−1 is the N-H stretching vibration absorption peak; 3,015.51, 2,938.37, 2,842.86 cm−1 are the C-H stretching vibration absorption peaks; 1,614.98 cm−1 is the C=O stretching 1,614.98 cm−1, indicating that the carboxyl group has been introduced into the product; 1,358.78 cm−1 is the asymmetric stretching vibration absorption peak of O=S=O, 1,108.98 cm−1 is the symmetric stretching vibration absorption peak of O=S=O; 1,193.94, is the stretching vibration absorption peak of C-F. Therefore, it indicates the presence of amine group, C=O, S=O and C-F bonds in the target product. The Fourier transform infrared spectra showed that the absorption peaks of important chemical bonds and groups were present in the target products, which proved the correctness of the synthesized products.
Figure 3: FSC-6 FTIR spectroscopy
The NMR hydrogen spectrum of FSC-6 is shown in Fig. 4. 1HNMR: δ = 1.18 (d, 2H, CH2-CH2-CH2); 1.83 (s, 2H, CH2-CH2-N); 3.14 (s, 6H, N-(CH3)3); 3.5 (s, 2H, NH-CH2-CH2); 3.80 (s, 2H, N-CH2-COO). 1HNMR clearly characterized the attribution of hydrogen atoms and tentatively proved the correctness of the synthesized products.
Figure 4: FSC-6 1HNMR spectrum
The FSC-6 19FNMR spectra are shown in Fig. 5 19FNMR: δ = 80.50 (s, 3F, CF3-CF2), −112.49 (s, 2F, CF2-S), −120.61 (m, 2F, CF2-CF2-S), −121.55 (m, 2F, CF2-CF2-CF2), 122.46 (m, 2F, CF3-CF2-CF2), 125.56 (s, 2F, CF3-CF2) 19FNMR clearly indicated the attribution of fluorine atoms and proved the correctness of the synthesized products.
Figure 5: FSC-6 19FNMR spectrum
The combined results of FTIR, 1HNMR and 19FNMR spectra analysis proved that the synthesized product was the target compound FSC-6.
3.2 Development of High Efficiency Cleaning Agent for Oil-Bearing Drill Chips
3.2.1 Oil Removing Agent Screening and Dosage Optimization
Take 10 g of oily drill chips in a beaker, add 0.5% mass fraction of different degreasing agents to the beaker at a solid-liquid ratio of 1:10, and adjust the shaking frequency of the shaker to 150 rpm, and keep shaking for 60 min at 60°C. After cleaning, measure the oil content to investigate the effect of different types of surfactants on the cleaning effect of drill chips, a single-factor experiment was then used to investigate the effect of the concentration of the preferred degreasing agent on the degreasing effect of oil-bearing drill chips. and the results are shown in Fig. 6.
Figure 6: Effect of degreaser B concentration on the cleaning effect of drill chips
As can be seen from Fig. 6, The oil removal agent CY-B has lower interfacial tension and better oil washing effect, and the oil removal rate can reach 82.8%. The reason for this is that CY-B is a quaternary ammonium salt cationic surfactant, which is more easily adsorbed on the surface of oil-bearing drill cuttings and can significantly reduce the oil-water interfacial tension. When the mass fraction of CY-B is 0.25%, the residual oil rate of drill chips decreases not much when the concentration continues to increase, which is related to the oil-water interfacial tension of the solution. However, as the concentration of surfactant increases, the oil-water interfacial tension will reach an equilibrium value and will no longer rise, so the cleaning effect will be difficult to improve. Considering the cost factor and the effect of oil removal rate, CY-B with a dosage of 0.25% was finally selected as the best dosage of oil remover in the oil-bearing drill cuttings removal formula.
3.2.2 Permeant Screening and Dosage Optimization
On the basis of optimizing the dosing of degreasing agent, the effect of different penetrant concentrations on the cleaning effect of oil-bearing drill chips was studied by adding penetrant to drill chips with oil content of 10%, and the results are shown in Fig. 7.
Figure 7: Effect of ST-A concentration on the cleaning effect of drill cuttings
As can be seen from Fig. 7, the addition of penetrant can improve the cleaning efficiency of oily drill chips to some extent, and the oil removal rate of drill chips in the experimental group of ST-A was significantly higher than the other two groups, and ST-A was selected as one of the compound formulations of cleaning agents under the same conditions. And when the concentration of penetrant was 0.6%, the cleaning agent oil removal rate increased from 82.5% to 85.0%, and the formulation cleaning efficiency reached the best. This synergistic effect is related to the nature of drugs, CY-B is a cationic quaternary ammonium surfactant with straight chain alkane structure, similar to white oil or diesel used in oil-based drilling fluids, which has good wettability in oil phase. The combination of these two surfactants has good cleaning effect.
3.2.3 Fluorocarbon Surfactant FSC-6 Dosage Optimization
The optimum dosage of oil removing agent YT-6 was determined to be 0.25% and the optimum dosage of penetrating agent JFC-U was 0.6% based on the cleaning and oil removal effect, and the final oil removal rate reached 85.0%. In this section, the oil removal rate of the oiled drill chips will be further improved by adding wetting agent FSC-6, and the optimum dosage of FSC-6 will be determined to finalize the formulation of high efficiency cleaning agent for oiled drill chips.
As can be seen from Fig. 8, the addition of wetting agent FSC-6 can effectively improve the cleaning efficiency of oil-bearing drill chips. When the concentration of FSC-6 exceeds 1000 mg/L, continuing to increase its concentration has little effect on the oil content of drill chips. And FSC-6 has 6 fluorocarbon chains with good oleophobicity and less solubility. At this time, the oil content of the oiled drill chips was only 1.12% after cleaning, and the oil removal rate of the oiled drill chips was 88.8%. In summary of the above experimental analysis, the formula of the oil-bearing drill chips cleaner was finally determined as 0.25% CY-B + 0.6% ST-A + 0.1% FSC-6.
Figure 8: The concentration of FSC-6 affects the cleaning effect of drill chips
3.3 Cleaning Process Optimization Study
Through the single-factor method to change the solid-liquid ratio, cleaning temperature, ultrasonic power, cleaning time and other conditions, the above experiments to obtain a high-efficiency cleaning agent cleaning process optimization study to determine the best cleaning agent cleaning process [14].
3.3.1 Effect of Solid-Liquid Ratio on the Cleaning Effect of Oily Drill Chips
Study the effect of different solid-liquid ratio on the cleaning effect of oil-containing drill chips, keep the cleaning temperature of 35°C, cleaning time 2 h, ultrasonic power 100 W constant, determine the solid-liquid ratio of 1:1, 1:2, 1:5, 1:10, 1:20, 1:30 different conditions, the cleaning agent oil removal rate, the experimental results are shown in Fig. 9.
Figure 9: The effect of solid-liquid ratio on the cleaning effect of drill cuttings
As seen in Fig. 9, with the increasing solid-liquid ratio of the cleaning agent, the oil removal rate of the oil-bearing drill chips rises rapidly, and the growth rate slows down when the solid-liquid mass ratio is greater than 1:10, and there is no significant change in the oil washing effect. In the cleaning process, the cleaning agent is distributed on the surface of the drill chips, the surface of the emulsified oil droplets and the aqueous solution, there is a dynamic balance of adsorption in the solution, increasing the content of the cleaning agent in the solution, the drill chip oil will be accelerated emulsification and enter the aqueous phase, so the cleaning agent oil removal rate rises rapidly; and when the solid-liquid ratio exceeds 1:10, the oil on the surface of the drill chips is gradually removed from the cleaning, but the internal dirt oil by capillary force, it is difficult to be removed Therefore, the rate of oil removal slows down, and the amount of cleaning agent is too much, increasing the cost of cleaning [15–17], so take the best cleaning solid-liquid ratio of 1:10.
3.3.2 Effect of Temperature on the Cleaning Effect of Oily Drill Chips
Keep the solid-liquid ratio of 1:10, cleaning time 2 h, ultrasonic power 100 W constant, to determine the effect of different temperatures on the cleaning effect of oil-bearing drill chips, to determine the oil removal rate results are shown in Fig. 10.
Figure 10: The influence of temperature on the cleaning effect of drill chips
As can be seen from Fig. 10, under certain conditions, the cleaning temperature has a significant effect on the cleaning effect of oil-bearing drill chips. When the cleaning temperature is 25°C, the oil content of the cleaned oil-bearing drill chips is 99.09%, when the cleaning temperature increases, the oil content of the oil-bearing drill chips decreases with the increase in temperature, when the temperature rises to 40°C, at this time the oil content of the cleaned oil-bearing drill chips is 99.14%, there is a significant increase, when the cleaning temperature continues to rise, as can be seen from the graph, the oil content of the oil-bearing drill chips changes thereafter not much. This may be because, when the temperature of the system rises after mechanical agitation of the oil-bearing drill cuttings, the viscosity, interfacial film thickness and stability of the oil-bearing drill cuttings are reduced and easily broken, which helps to make the liquid phase desorb from the emulsion interfacial film of solid particles; at the same time, it also intensifies the molecular thermal motion and Brownian motion of the suspended particles in the system, which is conducive to the collision and agglomeration of small droplets into large droplets and promotes the aggregation of droplets, so that they can finally be separated under the action of centrifugal force. The separation is achieved by centrifugal force, which improves the removal rate of drilling chip oil from the surface of oil-bearing chips. However, when the temperature continues to rise, it will lead to the vaporization of light oil in the oil-bearing drill chips, which will affect the droplet settlement, and the higher the temperature, the greater the energy consumption [18–20], so from the consideration of operational safety and economic benefit and energy saving loss, the best cleaning temperature is determined to be 40°C.
3.3.3 Effect of Ultrasonic Power on the Cleaning Effect of Oily Drill Chips
Keep the solid-liquid ratio of 1:10, the temperature of 40°C, cleaning time of 2 h conditions, to study the effect of different ultrasonic power on the cleaning effect of oil-containing drill chips, the results of the cleaning agent oil removal rate is shown in Fig. 11.
Figure 11: Effect of ultrasonic power on the cleaning effect of drill chips
As seen in Fig. 11, the ultrasonic power in the range of 25–160 W, the overall cleaning agent oil removal rate is gradually increasing trend, but in the ultrasonic frequency of 100 W to reach the maximum cleaning efficiency and slightly decreased. In the cleaning process, ultrasound with the help of cavitation effect, so that the volume of microbubble nucleus in the liquid quickly repeat the process of expansion, contraction, and then expansion, and then contraction, and finally collapse. Microbubble nucleus from the formation to the rupture will accumulate energy before its rupture release energy and generate shock waves, shock waves will instantly generate high temperature and high pressure, so that the drill chip surface oil stripped and dispersed in the cleaning agent, thus enhancing the cleaning efficiency, so the cleaning effect generally increases with the ultrasonic power; when the ultrasonic power reaches 100 W, due to the increase in ultrasonic power, cavitation effect is enhanced, the cleaning fluid produces a large number of tiny bubbles in the drill chip surface to form an air cover, resulting in the micro bubble nucleus rupture release of energy can not be directly on the surface of the oil-containing drill chips, resulting in a decrease in cleaning efficiency [21–24], so take the best ultrasonic power of 100 W.
3.3.4 The Effect of Cleaning Time on the Cleaning Effect of Oil-Containing Drill Chips
In the solid-liquid ratio of 1:10, temperature of 40°C, ultrasonic power of 100 W conditions, to study the effect of cleaning time on the cleaning effect of oil-containing drill chips, the results of the cleaning agent oil removal rate is shown in Fig. 12.
Figure 12: The influence of cleaning time on the cleaning effect of drill chips
As can be seen from Fig. 12, with the growth of cleaning time, the cleaning agent oil removal rate rises rapidly, after cleaning time more than 30 min, the cleaning agent oil removal rate does not change significantly, and the cleaning agent oil removal rate reaches the maximum value of 98.9%. In the cleaning process, the longer the reaction time of the cleaning agent, the oil layer on the surface of the oil-bearing drill chips will be fully reacted, so the cleaning agent oil removal rate is increasing; however, the oil-bearing drill chips cleaning process is a dynamic equilibrium of adsorption and desorption, and it is difficult to improve the cleaning effect after reaching the equilibrium point [25]. Taking into account, the best cleaning time is 30 min.
3.4 Study on the Mechanism of Oil-Bearing Drill Cuttings Removal
Fluorocarbon wetting agent FSC-6 can play the role of oil washing if it has good solubility in the oil, so that the fluorocarbon surfactant can easily “penetrate” the oil layer and adsorb to the drill chip surface, thus changing its wettability.
From Table 1, it can be seen that the fluorocarbon surfactant can adsorb and change its wettability on the surface of oily drill chips, and the water droplet contact angle can increase from 93.6° to 117.2°, and the n-hexadecane oil droplet contact angle increases from 30.1° to 75.5°. The addition of fluorocarbon surfactant FSC-6 can enhance the hydrophobic and oleophobic performance of drill chip surface.
As can be seen from Table 2, the fluorocarbon surfactant has a weak ability to reduce the interfacial tension, and can only reduce the oil-water interfacial tension to 2.22 mN/m at the lowest, which cannot significantly reduce the surface adhesion work of oil-bearing drill chips, and has little cleaning effect when used as a single agent. Therefore, the introduction of cationic quaternary ammonium salt type degreaser CY-B with straight chain alkane structure is similar to white oil or diesel oil used in oil-based drilling fluids, which has better oil phase wettability. The introduction of permeate ST-A containing hydrophilic polyoxyvinyl, which is easily adsorbed on the surface of the drill cuttings after cleaning and oil removal, acts as a permeate component. The combination of these two highly active hydrocarbon surfactants can reduce the oil-water interfacial tension to 0.11 mN/m. The cleaning agent QXJ can act directly with the solid surface of the oil-bearing drill cuttings and quickly adsorb on the surface of the oil-bearing drill cuttings and reduce the adhesion work, thus stripping the oil from the surface of the drill cuttings. At the same time, due to the enhanced hydrophobic and oleophobic properties of the drill chip surface (as shown in Figs. 13 and 14, the contact angle of water droplets is 117.2° and the contact angle of n-hexadecane is 75.5°), it is difficult for the eluted oil to be adsorbed on the drill chip again [26–28], which achieves the purpose of efficient cleaning and oil removal from the oil-bearing drill chips.
Figure 13: Effect of FSC-6 on oil phase contact angle
Figure 14: Effect of FSC-6 on the contact angle of the water phase
According to the theory of adhesion work, the smaller the adhesion work of oil-based drill chips, the smaller the work required to strip the oil substance from the chip surface, and the higher the oil washing efficiency. The adhesion work is related to the interfacial tension and contact angle, and the adhesion work decreases when the interfacial tension decreases or the contact angle increases.
By changing the contact angle of oil phase by fluorocarbon surfactant, such as increasing the contact angle θ, decreasing the cos θ value, making the drilling chip surface neutral and wetting, and reducing the oil-water interfacial tension to the low interfacial tension range (10−2 mN/m), the oil-based drilling efficiency can be greatly reduced. The oil-based drill chip surface adhesion can be reduced significantly (by 2 orders of magnitude), and the oil-based drill chip surface adhesion can be achieved. The oil-based drill cuttings can be cleaned and recovered efficiently by reducing the interfacial tension to a low interfacial tension range (10−2 mN/m) [29–32].
When the fluorocarbon degreaser is added to the oil-based drill chips, its carbon and fluorine chain has a “sparing” effect on the oil film on the drill chips, so that its degreaser molecules disturb the oil layer and form a fluorocarbon degreaser solution; then when the fluorocarbon degreaser solution percolates to the adsorption channel on the drill chip surface, it uses the electrostatic gravitational force and intermolecular force between itself and the drill chip surface to adsorb on the drill chip surface. After the water molecules in the degreasing agent oil sparing effect of water channel expansion, more water molecules through the water channel to the solid surface, and along the solid surface diffusion, constitute both hydrophobic and oleophobic adsorption layer, so that the interface energy decreases, and wettability reversal (oil wet or water wet to neutral), the oil droplets under the action of external forces from the solid surface, to complete the wetting reversal. As the surfactant adsorbed on the solid surface is not sufficient, a film is not formed, but a number of independent adsorption points are formed, and each adsorption point has a hydrophobic effect on the oil droplets, which is not conducive to the adsorption of oil droplets, thus realizing the stripping of oil droplets from the surface of oil-based drill chips [33–35].
3.5 Comparative Analysis of Resource-Based Treatment Technologies
Comparing the combined acoustic-chemical cleaning technology used in this paper with the existing resource-based treatment technology, as shown in Table 3 below, although the drilling fluid and base oil were recovered and the recycling of resources was achieved, there were still problems that needed improvement. Chemical cleaning method has incomplete cleaning and separation, secondary pollution potential; thermal analysis method is not fully mature, equipment coking deformation, processing temperature is too high oil cracking, resulting in the inability to recover base oil back to match the drilling fluid; solvent extraction method has a large amount of extractant poor universality, high processing costs, extractant toxicity may be hazardous to health and other disadvantages; ultrasonic and microwave technology is still in the laboratory research stage. Industrial application has not been achieved.
After the combined acoustic-chemical process used in this paper, the oil in the oil-bearing drill cuttings can be recovered and reused efficiently. The wastewater and slag are also properly treated, the entire process has a small footprint, and the surrounding environment of the treatment plant is restored. The oil removal rate of the oil-bearing drill cuttings exceeds 90%. The main indicators of the leachate and solidified waste sludge of the main oil-bearing wastewater met the comprehensive wastewater discharge standard SY/T7422-2018. The method proposed in this study can be used for the harmless treatment and resource recovery of oil-bearing drill cuttings.
(1) Betaine fluorocarbon surfactant FSC-6 was synthesized from N, N-dimethyl-1,3-propane- diamine, perfluorohexyl sulfonyl fluoride and sodium chloroacetate as a wetting agent in the cleaner formulation to clean drill chips in synergy with other components. The molecular structure of the synthesized product was characterized by FTIR, NMR hydrogen spectroscopy and NMR fluorine spectroscopy, which confirmed that the synthesized product was consistent with the target molecular structure.
(2) Aiming at the cleaning process characteristics of oil-containing drill chips, a high-efficiency cleaning agent was developed by synthesizing carbon and fluorine surfactants, screening degreasing agent and penetrating agent, with the formula of 0.25% degreasing agent CY-B + 0.6% penetrating agent ST-A + 0.10% FSC-6.
(3) Optimize the oil-containing drill chips cleaning process conditions through single-factor experiment, the best cleaning process conditions are solid-liquid ratio of 1:10, temperature of 40°C, ultrasonic power of 100 W, cleaning time of 30 min. under this condition the cleaning agent can reduce the oil content of oil-containing drill chips to 0.35%. It meets the standard of less than 2% oil content of drill chips in SY/T7422-2018 “Oil-based Drilling Fluid Drill Chip Treatment System for Oil and Gas Drilling Equipment”.
(4) The carbon fluorine surfactant effectively changes the wettability of the surface of the oil-bearing drill chips, combining the effect of the degreasing agent to reduce the oil-water interfacial tension and the penetrating agent to easily adsorb on the surface of the cleaned and degreased drill chips, reducing the adhesion work from the aspects of wettability and interfacial tension to achieve the cleaning effect.
(5) Appropriate treatment technologies should be selected according to the specific characteristics of oil-bearing drill cuttings and according to local conditions. It accelerates the process of putting the ultrasonic/microwave treatment technology, which is currently in the laboratory research stage, into industrial application, and use the flotation technology, which is widely used in the field of oily wastewater and oily sludge treatment, to recover base oil and barite from oily drill cuttings, so as to realize the resourceful and harmless treatment of oily drill cuttings.
Funding Statement: The authors received no specific funding for this study.
Conflicts of Interest: The authors declare that they have no conflicts of interest to report regarding the present study.
References
1. Li, X., Yang, J. R., Yin, C. L. (2013). Research and development of new technology for harmless treatment of drilling fluid waste. Petroleum and Natural Gas Chemicals, 42(4), 439–442. [Google Scholar]
2. Li, X. Q., Yang, J. R., Yin, Z. L., Wang, R. C. (2013). Oil-based drilling fluids with oil-containing drill cuttings harmless treatment process technology. Drilling and Completion Fluids, 30(4), 81–83+98. [Google Scholar]
3. Chen, C. (2012). Discussing oil-bearing drill cuttings treatment technology. Science and Technology Innovation and Application, 2012(12), 18. [Google Scholar]
4. Sankaran, S., Pandey, S., Sumathy, K. (1998). Experimental investigation on waste heat recovery by refinery oil sludge incineration using fluidized-bed technique. Journal of Environmental Science and Health, Part A, 33(5), 829–845. [Google Scholar]
5. Hui, S., Zhai, Y. J., Wang, T. Y. (2018). Research progress of oil-bearing drill cuttings treatment technology. Journal of Wuhan Engineering University, 40(5), 473–478. [Google Scholar]
6. Nadali, A., Ali-Reza, M., Kazem, N., Ghasemali, M., Hiua, D. et al. (2014). Biodegradation of petroleum hydrocarbons in a soil polluted sample by oil-based drilling cuttings. Soil & Sediment Contamination, 23(5), 586–597. [Google Scholar]
7. Yi, S., Xiang, X. J., Xiao, S. (2001). Treatment technology for oil-bearing drill cuttings in offshore drilling. China Offshore Oil and Gas Engineering, 2001(6), 52–54+6–26. [Google Scholar]
8. Xiang, X. J., Yi, S. J., Dai, X. D., Xiao, W. F., Wang, C. F. (1996). Regulations and countermeasures for offshore drilling waste discharge. Oil and Gas Field Environmental Protection, 1996(3), 31–35. [Google Scholar]
9. Jiang, X. L., Wang, X. S. (2020). Application of oil-bearing drill cuttings extraction and treatment technology in the East China Sea. Offshore Oil, 40(4), 71–74+84. [Google Scholar]
10. Xu, J., Zhang, X. F., Li, S. Y. (2020). Research progress of thermal analysis treatment technology for oil-bearing drill cuttings. Oil and Gas Field Environmental Protection, 30(3), 11–13+60. [Google Scholar]
11. Song, L. Y. (2021). Design, synthesis, performance and application of comb-type polymeric surfactants containing carbon and fluorine short chains (Ph.D. Thesis). Nankai University, China. [Google Scholar]
12. Wang, L. (2013). Synthesis and compounding performance of fluorocarbon surfactants (Ph.D. Thesis). Shaanxi University of Science and Technology, China. [Google Scholar]
13. Fan, X. F. (2007). Preparation of sodium perfluorooctanoate surfactant and its properties for emulsion breaking and lint washing (Ph.D. Thesis). China University of Geosciences, China. [Google Scholar]
14. Zheng, T. T., Tu, M., Liu, S. L. (2015). Research on thermal analysis and incineration treatment technology of oil-bearing drill cuttings. Chemical Management, 363(4), 146–147. [Google Scholar]
15. Hu, W. Y., Jiang, Z. A. (2016). Research on the mechanism of action and formulation of penetrant in coal seam water injection. Coal Mine Safety, 47(6), 5–8. [Google Scholar]
16. Deng, H., Xie, S. X., Wang, R. S. (2013). Research on high-efficiency degreasing agent and degreasing mechanism of oil-bearing drill chips. Journal of Environmental Engineering, 7(9), 3607–3612. [Google Scholar]
17. Cong, P. C., Qin, Z. L., Liu, Y. (2014). A discussion of oil-bearing waste management technologies for shale gas drilling platforms. China Petroleum and Petrochemical Engineering Research Society, 2014(7), 156–162. [Google Scholar]
18. Zhou, Y. T., Tang, Y. J., Jin, Y. (2020). Research progress on the compounding of fluorinated surfactants and their applications. Leather Science and Engineering, 30(5), 26–32. [Google Scholar]
19. Wang, M. L., Zhang, H., Zhang, L. (2018). Combined acoustic-chemical method for cleaning oil-containing drill chips. Chemical Environmental Protection, 38(2), 222–226. [Google Scholar]
20. Li, Z. Y., Wei, H. Y., Ma, H. T. (2017). A new oil removal mechanism and oil-bearing drill cuttings removal technology. Natural Gas Industry, 37(2), 77–83. [Google Scholar]
21. Zhang, J., Li, J. B., Thring, R. W. (2012). Oil recovery from refinery oily sludge via ultrasound and freeze/thaw. Journal of Hazardous Materials, 203, 195–203. [Google Scholar] [PubMed]
22. Sui, X., Ji, G. D. (2010). Impact of ultrasonic power density on elution of super heavy oil and its biomarkers from aging soils using Triton X-100 micellar solution. Journal of Hazardous Materials, 176(1–3), 473–480. [Google Scholar] [PubMed]
23. Ji, G. D., Sui, X. (2010). Impact of ultrasonic time on hot water elution of severely biodegraded heavy oil from weathered soils. Journal of Hazardous Materials, 179(1–3), 230–236. [Google Scholar] [PubMed]
24. Onwuka, O. S., Igwe, O., Ifediegwu, S. I., Uwom, C. S. (2018). An assessment of the effectiveness of drilling waste treatment process in X-gas field, Niger Delta, Nigeria. Geology, Ecology, and Landscapes, 2(4), 288–302. [Google Scholar]
25. Jéssika, M. S., Irineu, J. P., Ana, C. S. M. (2018). Optimization of the batch decontamination process of drill cuttings by microwave heating. Journal of Petroleum Science and Engineering, 163, 349–358. [Google Scholar]
26. Hu, J. J., Xie, S. X., Tang, S. F., Li, X. C., Cheng, Y. P. et al. (2021). Synthesis and application of fluorocarbon surfactants. Applied Chemistry, 50(5), 1372–1376. [Google Scholar]
27. Zhang, W. C., You, L. Y. (2016). Adsorption properties of fluorocarbon surfactants on rock mineral surfaces. Journal of Yangtze University (Self Science Edition), 13(28), 6–12+3. [Google Scholar]
28. Ding, Z., Min, S., Pan, R. M., Lin, X. Y., Ping, X. et al. (2019). Synthesis and properties study of novel fluorinated surfactants with perfluorinated branched ether chain. Journal of Fluorine Chemistry, 219, 62–69. [Google Scholar]
29. Mao, S. Q., Tang, M. F., Gu, C. (1994). Synthesis of fluorosulfonated betaine-based amphoteric surfactants and their oil collection properties. Organic Fluorine Industry, 1994(2), 1–3. [Google Scholar]
30. Zheng, J. J. (2011). Study on the performance of sulfobetaine fluorocarbon surfactants (Ph.D. Thesis). China University of Petroleum, China. [Google Scholar]
31. Jiang, N., Sheng, Y., Li, C. (2018). Surface activity, foam properties and aggregation behavior of mixtures of short-chain fluorocarbon and hydrocarbon surfactants. Journal of Molecular Liquids, 268, 249–255. [Google Scholar]
32. Tim, C., Kenneth, M., Allison, Y. (2014). Fluorinated sulfamido amphoteric surfactants. Journal of Fluorine Chemistry, 161, 41–50. [Google Scholar]
33. Lin, C. (2019). Synthesis, conformational relationships and applications of branched fluorocarbon surfactants (Ph.D. Thesis). Nanjing University of Science and Technology, China. [Google Scholar]
34. Yin, Z., Zheng, Y. C., Wu, C. (2017). Study on the solution properties of two sulfobetaine species. Fine Petrochemicals, 34(5), 65–70. [Google Scholar]
35. Li, Y. F., Wang, Y. L., Wang, Q. (2017). Research and application progress of special fluorocarbon surfactants. Chemical Progress, 36(9), 3453–3464. [Google Scholar]
36. Wang, Z. H., Zhang, L., Li, J. X. (2015). Disposal of oily sludge. Petroleum Science Technology, 3, 1045–1052. [Google Scholar]
37. Hou, B. F., Liang, C., Deng, H. (2012). Oil removing technology of residues from waste oil-based drilling fluid treated by solid-liquid separation. Journal of Residuals Science and Technology, 9(4), 143–150. [Google Scholar]
38. Huang, X. B., Jiang, G. C., Deng, Z. Q. (2015). Oil extraction from oil-contaminated drill cuttings using a recyclable single-phase O/W micro emulsion. Tenside Surfactants Detergents, 52(6), 454–463. [Google Scholar]
39. Li, Y. F., Wang, Y. L., Guo, G. (2018). The effect of fluorocarbon surfactant on the gas-wetting alteration of reservoir. Petroleum Science Technology, 36(13), 951–958. [Google Scholar]
40. Jin, J. F., Wang, Y. L., Ren, J. H. (2016). The effect of fluoropolymer on wettability alteration of sandstone at elevated temperatures. Journal of Surfactants Detergents, 19(6), 1241–1250. [Google Scholar]
41. Ren, W., Xie, S. X., Cheng, Y. P., Li, X. C. (2021). Synthesis and properties of novel betaine fluorocarbon surfactants. Journal of Dispersion Science and Technology, 44(6), 1000–1009. https://doi.org/10.1080/01932691.2021.1984940 [Google Scholar] [CrossRef]
Cite This Article
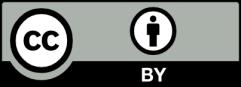