Open Access
PROCEEDINGS
Effects of Alignment and Dislocation on the Impact Mechanical Response of Tandem Nomex Honeycomb
1 School of Astronautic and Aeronautic, Shanghai Jiao Tong University, Shanghai, 201100, China
* Corresponding Author: Xiaojing Zhang. Email:
The International Conference on Computational & Experimental Engineering and Sciences 2023, 28(1), 1-4. https://doi.org/10.32604/icces.2023.010481
Abstract
1 IntroductionNomex honeycomb is widely used in aerospace field due to its formability and impact resistance. Tandem honeycomb structure is favored for its excellent energy absorption and controllable deformation sequence [1]. Because impact damage is inevitable in the use of sandwich structures, it is necessary to analyze the impact mechanical response of such structures. The research objects include single honeycomb and two layers align honeycomb. First, the drop weight impact test was carried out to compare the mechanical response of double-layer aligned and staggered honeycomb with that of single honeycomb. Then finite element method was used to simulate the experiment and results were compared.
2 Experimental methods
2.1 Test article
Two panels of the test article were composed of epoxy resin and glass fiber, with glass fiber ±45° layered. The size was 110×110mm, the thickness of one panel was 0.25mm. The core adopted regular hexagonal Nomex honeycomb with nominal density of 48 kg/m3, relative density of 0.042, and the side length of the honeycomb lattice was 1.85mm. The wall thickness of the monolayer was 0.05 mm. For the single honeycomb shown in Fig.1, the height of the core was 19.6mm. For two layers align honeycomb shown in Fig.2, high strength adhesive was used to bond two layers of 9.3mm honeycomb core and Membrane interlayer.
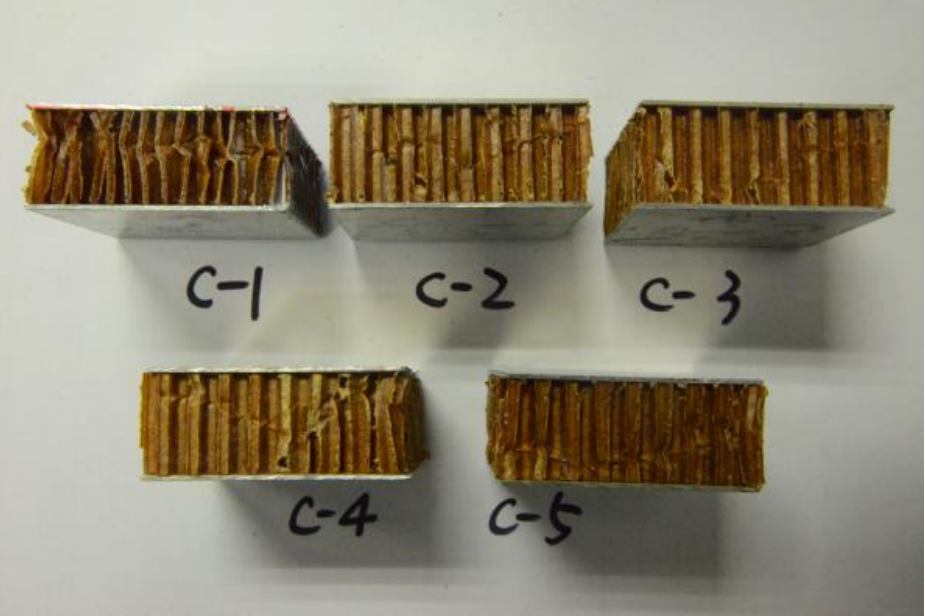
Figure 1: Single honeycomb samples
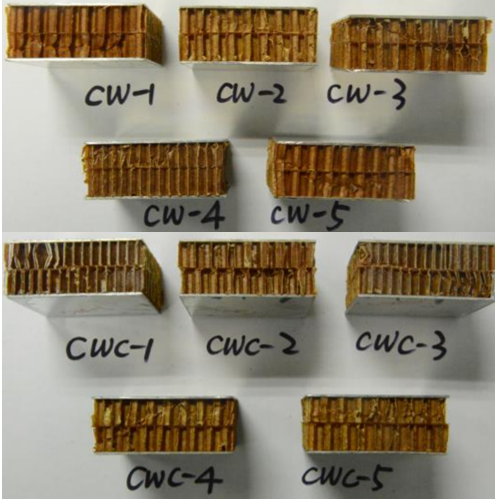
Figure 2: Two layers align honeycomb samples
2.2 Experimental methods
The experiment was carried out on the instrument INSTRON CEAST 9350 drop weight impact according to experimental standard ASTM-D3763. The mass of the impactor was 2.131kg. The test article was clamped by an annular standard fixture, then different energy levels were used to impact the test article, and the corresponding results were obtained.
3 Finite element model
Using Abaqus software to establish the finite models for two types of honeycomb structures, shown in Fig.3. Panels and honeycomb core were defined as C3D8R element. Equivalent modeling method was dopted for the core: the compressibility curve of honeycomb core obtained from the test was imported into the model as an elastoplastic constitutive relation. The impact was defined as a rigid body, The element type was R3D4. And Surface-to-Surface contact was used between the impact and panel as well as panel and honeycomb core. The remaining contact, including the self-contact of all components were defined as the general contact. The rest of the modules, such as material properties, fixed model and impact energy, were endowed according to the physical truth. Meanwhile, meshes of the contact part between the center of the panel and the impactor were refined and the hourglass values of the elements were added to make the calculation more stable.
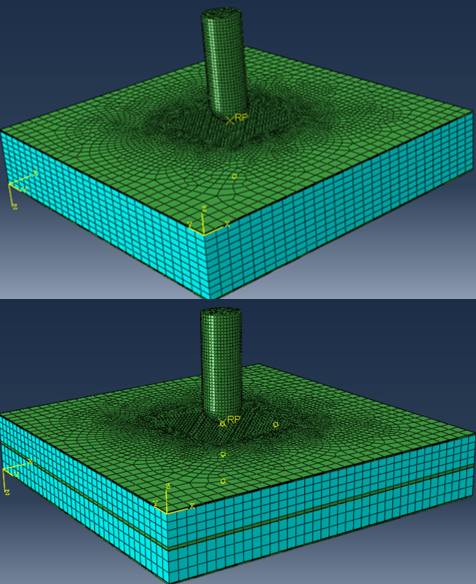
Figure 3: Finite element model
4 Analysis
4.1 Experimental results
As shown in table.1, The group C was the single honeycomb samples, group CW and group CWC were the two layers align honeycomb samples. With the increment of the impact speed, the peak force on the panel was also increasing. When the impactor breaked through the upper panel, it continued impacting the honeycomb core until it reached the down panel,then the impact force reached the second peak and was greater than the first one. Moreover, two layers align honeycomb samples had better impact impedance performance.
Table 1: Experiment results
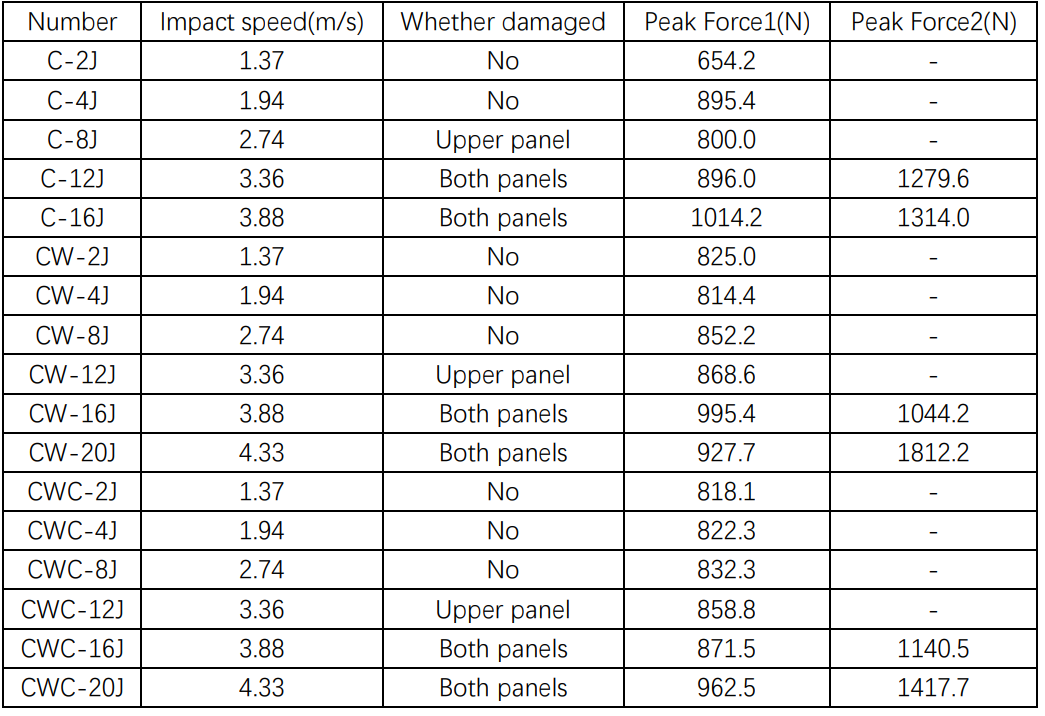
4.2 Finite element simulation results
It takes quite a lot of time to accomplish the Explicit Dynamic Analysis in ABAQUS, so limited results were used to compare with the experiments. As shown in Table.2, the finite element results are in good agreement with the experimental results.
Table 2: Finite element simulation results and error
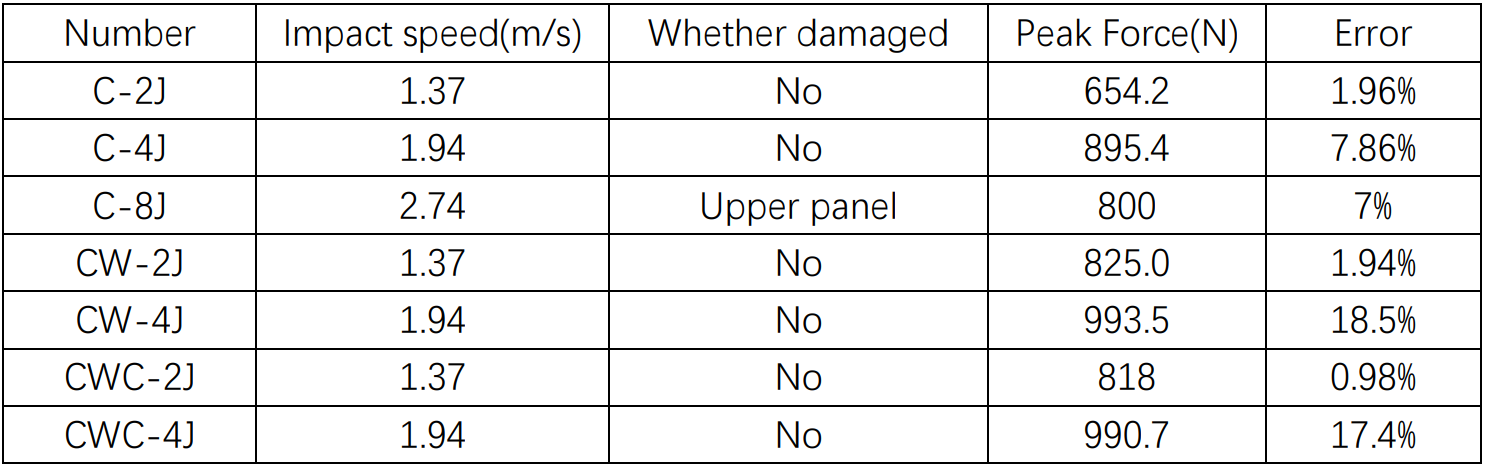
5 Conclusion and follow-up work
Two layers align honeycomb samples have better impact impedance performance compared with the single honeycomb samples. Meanwhile, the finite element model simulation work still needs to be carried out to get more data to verify the experiment.
Keywords
Cite This Article
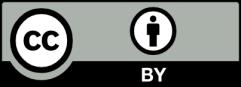