Open Access
ARTICLE
Fatigue Resistance and Cracking Mechanisms in an Aircraft AISI 4340 Steel with Surface Affected by Electro-Erosive and Water Jet Cutting
1 Strength Department, SVÚM a.s., Podnikatelská 565, 19011 Praha 9, Czech Republic
2 Corresponding author: Tel.: 00 420 222724098; Fax.: 00 420 222724509; E-mail: Ivo.Cerny@seznam.cz
Structural Durability & Health Monitoring 2010, 6(1), 43-52. https://doi.org/10.3970/sdhm.2010.006.043
Abstract
Alternative methods of material machining like electro-erosive or water jet cutting, respectively, represent modern technologies, which are perspective to be used as final end-to-shape operations due to their possibilities of automatization and cutting precision. The paper contains results of an investigation of resistance of an aircraft AISI 4340 steel against fatigue loading performed using specimens loaded by three point bending at ambient temperature and standard laboratory conditions. Results of fatigue tests of specimens with surface after electro-erosive and water jet cutting, respectively, are presented, whereas in the latter case, areas of water jet incidence and outfall are studied separately. The work programme contained metallographical analysis of material microstructure, hardness measurement and analyses of surface character from the macro- and microscopic viewpoints. In comparison with ground surface, both the technologies resulted in partial reduction of fatigue resistance and fatigue limit, by approximately 17 %, whereas the effect of both the technologies was comparable. The fact that fatigue strength did not depend on hardness of specimen bulk material, i.e. on strength, namely in a relatively large interval of values, which was affected by local microstructure differences, can be considered as surprising. The microstructure mostly was of ferritic-pearlitic type with local bainitic islands in some of the specimens. Contrariwise, reduction of fatigue strength with the hardness was observed in specimens with ground surface. These result indicate that in the studied case, development of preexisting microdefects in surface or subsurface layers was the deciding mechanism of fatigue damage rather than usual fatigue crack initiation on smooth surface. Fractographical analysis carried out confirmed these assumptions.Keywords
Cite This Article
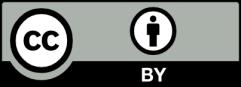