Open Access
ARTICLE
An Innovative Finite Element Geometric Modeling of Single-Layer Multi-Bead WAAMed Part
1 College of Mechanical and Power Engineering, China Three Gorges University, Yichang, 443002, China
2 School of Mechanical Science and Engineering, Huazhong University of Science and Technology, Wuhan, 430074, China
3 School of Metallurgy and Materials Engineering, Iran University of Science and Technology, Narmak, Iran
* Corresponding Authors: Xiangman Zhou. Email: ; Seyed Reza Elmi Hosseini. Email:
Computer Modeling in Engineering & Sciences 2024, 138(3), 2383-2401. https://doi.org/10.32604/cmes.2023.029249
Received 09 February 2023; Accepted 03 August 2023; Issue published 15 December 2023
Abstract
Finite element (FE) coupled thermal-mechanical analysis is widely used to predict the deformation and residual stress of wire arc additive manufacturing (WAAM) parts. In this study, an innovative single-layer multi-bead profile geometric modeling method through the isosceles trapezoid function is proposed to build the FE model of the WAAM process. Firstly, a straight-line model for overlapping beads based on the parabola function was established to calculate the optimal center distance. Then, the isosceles trapezoid-based profile was employed to replace the parabola profiles of the parabola-based overlapping model to establish an innovative isosceles trapezoid-based multi-bead overlapping geometric model. The rationality of the isosceles trapezoid-based overlapping model was confirmed by comparing the geometric deviation and the heat dissipation performance index of the two overlapping models. In addition, the FE-coupled thermal-mechanical analysis, as well as a comparative experiment of the single-layer eight-bead deposition process show that the simulation results of the above two models agree with the experimental results. At the same time, the proposed isosceles trapezoid-based overlapping models are all straight-line profiles, which can be divided into high-quality FE elements. It can improve the modeling efficiency and shorten the simulation calculation time. The innovative modeling method proposed in this study can provide an efficient and high-precision geometric modeling method for WAAM part FE coupled thermal-mechanical analysis.Keywords
Cite This Article
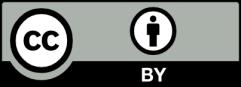