Open Access
REVIEW
A Review on Finite Element Alternating Methods for Analyzing 2D and 3D Cracks
Department of Safety Engineering, Chungbuk National University, Cheongju, Korea
* Corresponding Author: Jai Hak Park. Email:
(This article belongs to the Special Issue: Advances in Methods of Computational Modeling in Engineering Sciences, a Special Issue in Memory of Professor Satya Atluri)
Digital Engineering and Digital Twin 2024, 2, 79-101. https://doi.org/10.32604/dedt.2024.047280
Received 30 October 2023; Accepted 30 January 2024; Issue published 25 March 2024
Abstract
A finite element alternating method has been known as a very convenient and accurate method to solve two and three-dimensional crack problems. In this method, a general crack problem is solved by a superposition of two solutions. One is a finite element solution for a finite body without a crack, and the other is an analytical solution for a crack in an infinite body. Since a crack is not considered in a finite element model, generating a model is very simple. The method is especially very convenient for a fatigue crack growth simulation. Over the past 40 years, S. N. Atluri and his many collaborators have developed finite element alternating methods for two and three-dimensional cracks. In this paper, the developing history of the finite element alternating method was reviewed to understand the current status of the method. From this review process, it can be known what kinds of crack problems can be solved accurately with the current method, and what part of the method needs to be improved further.Keywords
Nomenclature
BEM | Boundary element method |
BEAM | Boundary element alternating method |
EPFEAM | Elastic-plastic finite element alternating method |
FEM | Finite element method |
FEAM | Finite element alternating method |
MSD | Multiple site damage |
SGBEM | Symmetric Galerkin boundary element method |
SIF | Stress intensity factor |
WFD | Widespread fatigue damage |
XFEM | Extended finite element method |
α | Constant or inclined angle |
εo | σo /E |
ν | Poisson’s ratio |
σo | Reference stress value |
σys | Yield strength |
a | Half crack length |
E | Elastic modulus |
h | Thickness of a plate |
K | Stress intensity factor |
Lext | The length shown in Fig. 12 |
Mo | Bending moment per unit length |
n | Strain hardening exponent |
t | Thickness |
Many kinds of techniques have been proposed in order to calculate fracture parameters, such as stress intensity factors (SIF) or J integrals, for the safety assessment of cracked structures. The techniques include analytic solutions, finite element method (FEM) [1–3], boundary element method (BEM) [4–7], Symmetric Galerkin boundary element method (SGBEM) [8–11], extended finite element method (XFEM) [12–14], meshfree method [15–18], s-version finite element method [19,20] and so on. Each technique may have some advantages and drawbacks. Analytic methods give the most accurate stress intensity factors and stress fields for a crack embedded in an infinite domain. However, it is difficult to solve a crack in a finite domain with complex geometry. The finite element method is a well-established method for structural analyses. However, it is not easy to generate a finite element model for a body with cracks and a remeshing procedure is necessary during crack growth.
The basic idea of a finite element of alternating method (FEAM) is simple. Since analytical methods give accurate solutions for an infinite body with a crack and constructing a finite element model is very simple for a body without a crack, it would be convenient to obtain the solution of a given problem using the advantages of the two methods. In FEAM, the solution of a finite body with a crack is obtained by a superposition of two solutions of an analytical method and FEM. A general explanation of the FEAM can be found in the references by Atluri et al. [21–23] and Wang et al. [24].
Shah et al. [25,26] solved the problems of a surface crack and an elliptical crack near a free surface using an alternating method. The alternating procedure was performed between two analytical solutions. One is the analytical solution for an uncracked body and the other is the analytical crack solution in an infinite domain. For the analytical crack solution, they used the solution for an infinite solid with an elliptical crack, subjected to normal pressure, which was expressed in terms of cubic polynomials of x and y [27]. Nishioka et al. [28] published the first paper introducing the finite element alternating method for a three-dimensional crack. As a required analytical solution, they used the solution presented by Vijayakumar et al. [29], who solved the problem of an elliptical crack in an infinite solid, where arbitrary normal and shear tractions were applied on the crack surfaces. Raju et al. [30] calculated stress intensity factors for small surface and corner cracks in plates using FEAM and found that the results agreed well with the solutions obtained from FEM with singularity elements.
Nikishkov et al. [31] proposed an SGBEM-FEM alternating method for analyzing non-planar as well as planar three-dimensional cracks. Instead of the crack solution by Vijayakumar et al. [29], they used the crack solution formulated with the symmetric Galerkin boundary element method (SGBEM) [8–11]. In SGBEM formulation, the kernels in integral equations are weakly singular, so that the boundary element matrices can be integrated numerically. And since the matrices are symmetric, it is convenient to handle. While Nikishkov et al. [31] used the SGBEM solution only for a crack in an infinite solid, Han et al. [32] used the SGBEM solution for a subdomain with a crack. They performed the alternating procedure between the SGBEM solution for a local finite-sized subdomain with a crack and the FEM solution for the uncracked body outside the subdomain.
For two-dimensional FEAM, solutions to the problem of an infinite plate with a crack subjected to arbitrary normal and shear tractions are necessary. Using the analytical solutions of a crack, where normal and shear tractions were expressed with polynomials, some practical two-dimensional crack problems were solved using FEAM by Raju et al. [33–36]. Rajiyah et al. [37] proposed a boundary element alternating method (BEAM), where a BEM solution was used instead of a FEM solution. Using the developed method, they obtained the mixed-mode stress intensity factors and weight functions for cracks in finite bodies. Raju et al. [38] also used BEAM to consider two-dimensional crack problems.
When tractions are distributed smoothly on two-dimensional crack surfaces, Park et al. [39] used the analytical solution presented by Gladwell et al. [40]. Gladwell et al. expressed the tractions on the crack surfaces with Chebyschev polynomials. However, when a hole crack was considered in an alternating method, traction was zero on a part of crack surfaces and traction had a peak value near a hole due to the stress concentration. Therefore, it was very hard to express the tractions with Chebyschev polynomials. For this reason, Park et al. [39] used an analytical solution for a crack subjected to normal and shear point forces on its surfaces. They used the solution as a Green’s function for a crack subjected to general normal and shear tractions.
Multiple site damage (MSD) represents multiple cracks growing from a row of fastener holes in a bonded and riveted lap joint used in a pressurized aircraft fuselage. Park et al. [41] used FEAM to examine the fatigue crack growth behavior of MSD. As a necessary analytical solution, they used the solution of collinear multiple cracks subjected to normal and shear point forces on their surfaces.
Based on the algorithm of elastic-plastic finite element alternating method (EPFEAM) presented by Nikishkov et al. [42], Pyo et al. [43,44] performed 2D elastic-plastic analyses for multiple hole cracks in ductile panels. To improve the accuracy of stress fields near crack surfaces in analytical solutions, Park [45] proposed the solution of multiple collinear cracks subjected to piecewise constant tractions on their surfaces. Later Wang et al. [46,24] used the solution for piecewise linear tractions on crack surfaces for EPFEAM.
Using the developed FEAM, the integrity and fatigue life were evaluated for structures. Tian et al. [47–50] performed fatigue-crack growth simulations to estimate the life of attachment lugs, cracked I-beams, cylindrical bars and defective shield tunnel segments. Zhou et al. [51] performed real-time crack growth simulation for helicopter components. Wang et al. [52] performed a fatigue analysis for diagnostics and prognostics of aircraft structures.
There were attempts to couple BEM with FEM. In this method, a small subdomain with a crack is analyzed with BEM, and the other domain is analyzed with FEM. Some continuity conditions are imposed between the two domains [53–55]. The solutions can be obtained without alternating procedures. Rungamornrat et al. [56] used the SGBEM-FEM coupling method for the analysis of three-dimensional cracks in an anisotropic solid. Dong et al. [57] introduced “super element” for a two-dimensional crack problem. The super element with a crack was analyzed with SGBEM, and its stiffness matrix was coupled with the matrix of finite element methods. The SGBEM-FEM coupling method has some advantages when considering complicated solid structures, such as cracked stiffened panels. However, the stiffness matrix of FEM should be modified in the method.
Over the past 40 years, many researchers have contributed to the development of alternating methods for 2D and 3D crack problems. In this paper, the developing history was traced again in order to understand the current status of the finite element alternating methods. From this review, we can know what kinds of crack problems can be solved accurately with the current method, and what part of the method needs to be improved further.
2.1 Basic Idea of Alternating Methods
Nishioka et al. [28] published the first paper introducing the finite element alternating method for a three-dimensional crack problem. The basic idea of an alternating method is simple. The alternating method employs the advantages of FEM and analytical methods. The method obtains the solution for the given finite body with a crack using a superposition of two following solutions as shown in Fig. 1:
Figure 1: Alternating procedure for a given crack problem
1. Finite element solution for the given uncracked finite body subjected to external loading,
2. Analytical solution for an infinite body with a crack. Instead of analytical solutions, BEM or SGBEM solutions for an infinite body can be used.
2.2 Solution Procedure of Alternating Methods
Because a crack is not considered in a finite element model in FEAM, its generation is very easy. The same finite element model can be used during a crack growth simulation because a remeshing procedure is not necessary during the fatigue crack growth. The solution of FEAM is obtained using the following steps of alternating iteration procedure:
1. Using a FEM solution, calculate the stresses at the location of the crack in the given finite uncracked body subjected to the given boundary conditions.
2. Using the obtained stresses, determine the residual tractions on the crack surfaces in order to obtain traction-free boundary conditions.
3. Using an analytical method, solve the problem of an infinite body with a crack, the faces of which are subjected to the residual tractions.
4. Since the solution for an infinite body was used, the boundary conditions are not satisfied on the outer boundaries of the body. Calculate the stresses on the outer boundaries of the finite body, from the tractions on the crack surfaces. And determine the residual forces on the outer boundaries in order to make traction-free boundary conditions.
5. Using a FEM solution, solve a problem for the finite uncracked body subjected to the residual forces obtained from Step (4).
6. Calculate the stresses at the location of the crack in the FEM solution.
7. Repeat Steps (2)–(6) until the residual load becomes very small.
8. The final stress and stress intensity factor solutions are obtained by accumulating all the contributions in each iteration.
Fig. 2 shows a flowchart of a finite element alternating method when the maximum increment in stress intensity factor values is used as the parameter of convergence of alternating iteration.
Figure 2: Flowchart of a finite element alternating method
3 Two-Dimensional Crack Problems
3.1 Single and Multiple Straight Cracks
In order to analyze a two-dimensional crack problem using a finite element alternating method, an analytical solution is required for a crack in an infinite plate, where arbitrary tractions are applied on the crack surfaces. Park et al. [39] used the solution given by Gladwell et al. [40], where the crack tractions were assumed to be a sum of Chebyschev polynomials. Their solution could be used when the tractions were distributed smoothly on the crack surfaces. However, it was very hard to use the solution for cracks emanating from a hole, because residual tractions would arise on a part of crack surfaces. So, Park, Ogiso, and Atluri used an alternate analytical solution for a central crack in an infinite plate. The crack was subjected to a normal point force P at x = c on the upper crack surface and –P at x = c on the lower crack surface. This problem can be solved using the procedure formulated by Muskhelishvili [58]. By using the solution as a Green’s function, the stress intensity factors and the stress fields can be obtained for a crack subjected to arbitrary normal tractions on its surfaces.
Multiple site damage (MSD) represents multiple cracks growing from a row of fastener holes in a pressurized airplane fuselage. Park et al. [41] used the finite element alternating method to examine the fatigue crack growth behavior of MSD. In order to obtain the necessary analytical solution, they used the solution of the problem where a normal point force P and a shear point force Q are applied at x = c on the upper surface and –P and –Q are applied x = c on the lower surface of the k-th crack in collinear multiple cracks as shown in Fig. 3. The problem also can be solved using the procedure formulated by Muskhelishvili [58]. They used the solution as a Green’s function for collinear multiple cracks subjected to general normal and shear tractions.
Figure 3: Collinear multiple cracks subjected to point loads
Sing et al. [59] and Park et al. [60,61] examined the structural integrity of fuselage panels of aircraft structural with multiple site damage using the developed finite element alternating method. Park [62] also used the developed method in order to calculate the stress intensity factors for multiple cracks lying on several lines in an infinite plate.
In order to use the alternating method for the problems of curved cracks in a finite plate, an analytical solution for a curved crack in an infinite plate is required. Park et al. [63] used the integral equations formulated by Cheung et al. [64–66]. They modelled the cracks as continuous distributions of dislocations and derived the necessary formulation. The unknown dislocation density functions were obtained for the given tractions on crack surfaces. Stress intensity factors and stress fields could be calculated from the dislocation density functions.
Park et al. [63] simulated the fatigue crack growth behavior for small hole cracks until long curved cracks were formed near the fastener holes under mixed mode loading conditions. Park et al. [67] examined the fatigue crack growth trajectory of an edge crack in a beam with three rivet holes. The configuration of the beam is shown in Fig. 4. The initial crack length was 38.1 mm, and b was the offset distance. The beam material was PMMA and crack growth direction was determined by the maximum principal stress criterion. Fig. 5 shows the finite element mesh for the beam with three holes. Fig. 6 shows the simulated result for b = 25.4 mm. The result was also compared with the observed result conducted by Ingraffea et al. [68]. We can find that only a small difference was observed between the two results.
Figure 4: Schematic of an example problem of a cracked beam [67]
Figure 5: Finite element mesh for the sample problem of a cracked beam [67]
Figure 6: Simulated fatigue crack growth trajectory was compared with the observed result when b = 25.4 mm [67]
3.3 Multiple Cracks in a Thin Plate under Bending and Twisting Moments
Based on the classical theory, Chen et al. [69,70] used FEAM to solve the problems of a cracked thin plate. Bending or twisting moments were applied on the horizontal boundary. They used the governing differential equations and Fourier transform to solve the analytical solution for a crack in an infinite thin plate. Park et al. [71] also used FEAM to solve the problem of multiple cracks in a thin plate subject to bending or twisting moments based on the classical theory. To obtain the necessary analytical solution, they considered the problem shown in Fig. 7. Bending moments of magnitude M* and twisting moments of magnitude H* are applied at x = c on the upper and lower crack surfaces of the k-th crack of collinear multiple cracks as shown in Fig. 7. Park and Atluri solved the problem using the method of Muskhelishvili [58].
Figure 7: Collinear multiple cracks in an infinite plate. Bending moments of magnitude M* and twisting moments of magnitude H* are applied on the surfaces [71]
As an example problem, Park et al. [71] solved the problem shown in Fig. 8, where two cracks were embedded symmetrically in a finite rectangular plate with H = 3 W, W = 10 h and a = h. Here h was the thickness of the plate and 2a was the crack length. A constant moment per unit length, Mo was applied on the upper and lower horizontal edges. The calculated SIF values were normalized with
Figure 8: Two symmetric cracks in a thin plate under constant bending moment [71]
Figure 9: Normalized SIF values as functions of d/a in a thin plate under constant bending moment [71]
3.4 Multiple Cracks in an Orthotropic Plate
Chen et al. [72] determined weight functions for the cracks in isotropic or orthotropic plates under mixed-mode loading using two-dimensional FEAM. Kim et al. [73] solved the problem of an orthotropic plate with multiple curved cracks using FEAM. They used the boundary integral method formulated by Zang et al. [74] as an analytical crack solution in an infinite orthotropic plate. Zang et al. modelled cracks as continuous distributions of dislocations, and derived an integral equation considering the resultant forces along cracks. Since the integral kernels show a weak logarithmic singularity, the numerical integration becomes very easy. Kim et al. [73] calculated the stress intensity factors for multiple cracks embedded in an infinite or finite orthotropic plate.
The algorithm for elastic-plastic finite element alternating method (EPFEAM) was presented by Nikishkov et al. [42]. Using the algorithm, Pyo et al. [43,44] performed 2D elastic-plastic analyses for ductile panels with widespread fatigue damage. Accurate stress values should be obtained near crack tips and crack surfaces for elastic-plastic analyses. However, it is not easy to calculate accurate stresses near point forces when we use point force solutions as in Fig. 3. To improve the accuracy in analytical solutions, Park [45] proposed a solution to the problem when piecewise constant tractions are applied on the crack surfaces of multiple collinear cracks. Later, Wang et al. [46,24] used the solution for piecewise linear tractions on crack surfaces. Wang et al. [75–77] used the developed EPFEAM program to predict the residual strength of aircraft structures with widespread fatigue damage (WFD). They performed fracture analysis, crack growth prediction and calculation of T*-integral fracture parameter using the EPFEAM program. Kawai et al. [78] used the method for the design and analysis of bonded composite repairs. They obtained SIF values and performed fatigue crack growth simulation considering the effects of stiffeners and repair patches.
3.6 SGBEM-FEA Alternating/Coupling Methods
Dong et al. [57] developed a two-dimensional weakly-singular symmetric Galerkin boundary element method (SGBEM), following the previous works of Okada et al. [79] and Han et al. [80]. The developed method could be used to analyze a finite plate containing arbitrary-shaped line cracks. They introduced a “super element”, which was a subdomain of general shape and could contain cracks inside it. The super element has a symmetric stiffness matrix and a force vector and can be directly coupled with the equations of the traditional finite element method. The super element has some advantages when considering complex structures, such as cracked stiffened panels. Since the iteration procedure is not necessary, this method is not an alternating method.
Dong et al. [81] discussed the SGBEM-FEM alternating/coupling method and compared the method with the extended finite element method (XFEM) for two-dimensional cracks. They concluded that the SGBEM and the SGBEM-FEM alternating/coupling methods are more effective and give more accurate SIF results than the XFEM. Sarkar et al. [82] also compared the computational efficiency of SGBEM-FEM alternating method with that of XFEM and concluded that SGBEM-FEM alternating method is more efficient than XFEM.
4 Three-Dimensional Crack Problems
An analytical solution for an elliptical crack in an infinite solid is required to solve three-dimensional crack problems using an alternating method. Vijayakumar et al. [29] presented the required solution for an elliptical crack subjected to arbitrary normal and shear tractions, generalizing the earlier solutions by Shah et al. [27] and Smith et al. [83]. After refining the solution of Vijayakumar et al. [29], Nishioka et al. [28] proposed a finite element alternating method and obtained the stress intensity factors for a circular crack, an elliptical crack, and a semi-elliptical surface crack. And they solved quarter elliptical corner cracks also [84].
Using the developed analytical solution and alternating method, O’Donoghue et al. [85,86] solved multiple embedded elliptical cracks in an infinite solid and determined stress intensity factors for semi-elliptical surface cracks in cylindrical pressure vessels. Simon et al. [87] obtained mixed mode stress intensity factors for part-elliptical surface cracks, using the finite element alternating method.
To improve the accuracy and the convenience of the method, Nishioka et al. [88] derived analytically the crack-surface displacement field and the gradients with respect to the crack dimensions, and presented the weight functions for the SIF values along the fronts of embedded elliptical cracks and part-elliptical surface cracks. Liao et al. [89] obtained SIF distribution for a semicircular surface flaw embedded in a finite-thickness plate. They used Love’s half-space solutions to make the traction-free boundary conditions on the front and back surfaces. Using the FEAM, Liao et al. [90] calculated SIF values of circular, semi-circular, and quarter-circular cracks. Rajiya et al. [91] derived the analytical solution for an elliptical crack embedded in an infinite, transversely isotropic solid, and obtained SIF values for embedded and surface elliptical cracks. Using FEAM, Mu et al. [92] also obtained SIF values and weight functions for semi-elliptical surface cracks. Pipkins et al. [93] solved surface flaw problems in various types of structures. O’Donoghue et al. [94] performed fatigue crack growth simulation for three-dimensional cracks in aircraft components.
4.2 SGBEM-FEM Alternating Method
Nikishkov et al. [31] proposed an SGBEM-FEM alternating method for analyzing non-planar as well as planar three-dimensional cracks. They replaced the earlier solution formulated by Vijayakumar et al. [29] with the symmetric Galerkin boundary element method (SGBEM) solution for a non-planar crack of arbitrary geometry. Since the kernels in integral equations of SGBEM are weakly singular, the boundary element matrices can be integrated numerically after a suitable coordinate transformation.
For an alternating method, we have to solve a problem of a non-planar crack of arbitrary geometry in an infinite solid subjected to arbitrary tractions on the crack surfaces. In SGBEM formulation, a crack is modeled by a distribution of displacement discontinuity. The displacement discontinuity should satisfy the weakly-singular boundary integral equation [8–11]. To overcome the difficulty in numerical integration for double area integration of weakly singular kernels, the suitable coordinate transformations given in the references [95–98] were used.
Using the developed method, Nikishkov et al. [31] solved the problem of an inclined elliptical crack, a circular-arc crack, a spherical penny-shaped crack and semi-circular and semi-elliptical surface cracks. They also performed a non-planar fatigue crack growth simulation. For example, they considered the problem of an inclined semi-circular surface crack in a plate as shown in Fig. 10a. The crack surface inclined at an angle α = 30°, and relative dimensions were a/t = 1/3 and W = t. Fig. 10b shows the used finite element model and the crack element model. The finite element model consists of 192 20-node brick-type elements and the boundary element crack model consists of 42 quadratic elements. Note that the fictitious crack surface outside the body is not shown in the figure. The fictitious crack surface consists of 8 quadratic elements. The fictitious crack surface is necessary because it makes an effect on the accuracy of the calculated SIF results. Fig. 11 shows the calculated SIF distribution results. The stress intensity factors KI, KII and KIII are normalized with
Figure 10: (a) A plate with an inclined semi-circular surface crack; (b) finite-element and crack meshes of the problem [31]
Figure 11: Modes I, II and III SIF distributions for an inclined semi-circular surface crack [31]
While Nikishkov et al. [31] used the SGBEM solution only for a crack in an infinite body, Han et al. [32,80] used the SGBEM solution for a subdomain with a crack. The subdomain had an outer boundary and was embedded in the body of the considering problem. The alternating procedure was proceeded between the FEM solution for an uncracked body outside the subdomain and the SGBEM solution for a local finite-sized subdomain with a crack. They obtained SIF distributions for a semi-circular surface crack, a quarter-circular crack in a square bar, and a corner crack at a circular hole in a finite-thickness plate. They also performed a non-planar fatigue growth simulation for an inclined semi-circular surface crack in a plate.
Park et al. [101,102] used the SGBEM-FEM alternating method for analyzing a three-dimensional through-thickness crack. They obtained the SIF distributions along the crack front for a through-thickness crack and performed a fatigue crack growth simulation. Fig. 12 shows an example of the used boundary element mesh, i.e., the crack mesh for a through-thickness crack. The crack has different crack lengths, 2a1 and 2a2 on the outer surfaces of the plate. Note that the rectangles GCDH and AEFB are fictitious crack meshes, i.e., they are located outside the considered body. From the study, it was found that the fictitious portion of the boundary elements can influence on the accuracy of the SIF results of a through-thickness crack. In the boundary element mesh, edges GCAE and HDBF are crack tips. Different boundary conditions can be imposed on the edges of GH and EF. And the imposed boundary conditions also affect the solution.
Figure 12: Crack mesh for a through-thickness crack with unequal surface lengths [101]
As an example problem, they considered a through-thickness crack. The crack was a center crack with the length of 2a. The width, height and thickness, t of the plate were 0.64, 0.6, and 0.05 m, respectively. Normal stress σ was applied on the upper and lower edges of the plate. The material properties of the plate were elastic modulus
Figure 13: Example of the used finite element mesh and crack mesh. Only a half of the finite element mesh was drawn [101]
Fig. 14 shows the normalized stress intensity factors as a function of Lext/t for three a/t values and the results were compared with the two-dimensional solutions. Here zero COD (crack opening displacement) boundary conditions were imposed on the edges GH and EF. The SIF was calculated at the center of the plate in the thickness direction and normalized with
Figure 14: The normalized SIF values were plotted as functions of Lext/t and compared with the 2D solutions. Here zero COD condition was assigned on the boundaries EF and GH in Fig. 12 [101]
Park et al. [101] also obtained the normalized stress intensity factors as a function of Lext/t when free boundary conditions were imposed on the edges of GH and EF. They found that the converged solutions could be obtained only when large values of Lext/t were used. So, they concluded that zero COD boundary conditions should be imposed on the edges of GH and EF for better convergence.
Fig. 15 shows the normalized SIF distributions along the crack front for 4 kinds of crack meshes. In this case, the crack length 2a = 0.1 m and Lext/t = 2 in the boundary element mesh. It can be noted that 3 types of fine meshes give similar SIF distributions excluding the coarsest mesh.
Figure 15: The normalized SIF distributions along the thickness for four types of crack meshes [101]
Park et al. [105] considered the mesh generation for irregular-shaped cracks and calculated SIF values. They generated the mesh with seven-node quadrilateral elements and three-node triangular using the advancing-front mesh generation method. Dong et al. [106] discussed the SGBEM-FEM alternating method and compared the method with the extended finite element method (XFEM) for three-dimensional cracks. They concluded that the SGBEM and the SGBEM-FEM alternating methods are far more efficient and accurate than the XFEM in analyzing fracture and simulating 3D non-planar fatigue crack propagation. Tian et al. [47–49] performed fatigue-crack growth simulations using a three-dimensional SGBEM-FEM alternating method in order to estimate the life of attachment lugs, cracked I-beams, and cylindrical bars. Zhou et al. [51] performed real-time crack growth simulation to evaluate the remaining life of helicopter components.
Nikishkov et al. [42] presented the algorithm for an elastic-plastic finite element alternating method (EPFEAM). Based on the algorithm, Nikishkov et al. [107] performed an elastic-plastic analysis for a semi-elliptical surface crack in a tensile plate.
Using the SGBEM-FEM alternating method, Park et al. [108] performed an elastic-plastic analysis for a penny-shaped crack located in a cylindrical column and calculated elastic-plastic stress fields. They also obtained elastic-plastic stress fields from FEM using a very fine mesh. They found that the stress values from the alternating method are close to the values from FEM. However, a discrepancy between the two values was observed near the crack surfaces. Park [109] performed elastic-plastic analyses for a penny-shaped crack in a cylindrical column and an inner surface crack embedded in a cylinder. Park calculated elastic-plastic J integrals for the considering cracks. He assumed that the stress-strain relation of the material could be expressed by the following Ramberg-Osgood equation:
where σo is a reference stress value, usually the yield strength σys, and εo = σo/E. Here E is the elastic modulus. And α and n are constants determined from a tension test. The constant n is also called a strain hardening exponent. Hutchinson [110] and Rice et al. [111] showed that the stress field has a singularity of
Figure 16: Meshes used in the EPFEAM analysis (a) finite element mesh without crack (b) crack mesh [109]
Figure 17: Calculated elastic-plastic Syy from EPFEAM were plotted as a function of θ. Note that FEM results were obtained with very fine mesh [109]
Figure 18: J integral values from EPFEAM were plotted and compared the results of the handbook solution [109]
Finite element alternating methods and SGBEM-FEM alternating methods for analyzing two and three-dimensional cracks were reviewed. The developing history was traced in order to understand the current status of the methods. After the review, the following conclusions were obtained:
1. The finite element alternating methods and SGBEM-FEM alternating methods are very convenient and accurate methods to calculate stress intensity factors for two and three-dimensional cracks compared to other numerical methods.
2. Especially the finite element alternating methods and SGBEM-FEM alternating methods are very convenient for fatigue crack growth simulations, because the crack mesh is independent of the finite element model and remeshing of the finite element model is not necessary.
3. Some application cases were introduced in order to demonstrate the usefulness of the methods.
4. However, some additional efforts seem to be necessary to improve the accuracy of elastic-plastic stress fields and to extend the application field of the methods.
Acknowledgement: None.
Funding Statement: The author received no specific funding for this study.
Author Contributions: The author confirms contribution to the paper as follows: all contributions: J. H. Park. The author reviewed the results and approved the final version of the manuscript.
Availability of Data and Materials: Readers should contact the authors of the references in order to access the data used in the study.
Conflicts of Interest: The author declares that they have no conflicts of interest to report regarding the present study.
References
1. Bouchard, P. O., Bay, F., Chastel, Y., Tovena, I. (2000). Crack propagation modelling using an advanced remeshing technique. Computer Methods in Applied Mechanics and Engineering, 189(3), 723–742. [Google Scholar]
2. Maligno, A. R., Rajaratnam, S., Leen, S. B., Williams, E. J. (2010). A three-dimensional (3D) numerical study of fatigue crack growth using remeshing techniques. Engineering Fracture Mechanics, 77(1), 94–111. [Google Scholar]
3. Branco, R., Antunes, F. V., Costa, J. D. (2015). A review on 3D-FE adaptive remeshing techniques for crack growth modelling. Engineering Fracture Mechanics, 141, 170–195. [Google Scholar]
4. Okada, H., Atluri, S. N. (1994). Recent developments in the field-boundary element method for finite/small strain elastoplasticity. International Journal of Solids and Structures, 31(12–13), 1737–1775. [Google Scholar]
5. Mi, Y., Aliabadi, M. H. (1994). Three-dimensional crack growth simulation using BEM. Computers and Structures, 52(5), 871–878. [Google Scholar]
6. Peng, X., Atroshchenko, E., Kerfriden, P., Bordas, S. P. A. (2017). Isogeometric boundary element methods for three dimensional static fracture and fatigue crack growth. Computer Methods in Applied Mechanics and Engineering, 316, 151–185. [Google Scholar]
7. Carter, B. J., Wawrzynek, P. A., Ingraffea, A. R. (2000). Automated 3-D crack growth simulation. International Journal for Numerical Methods in Engineering, 47, 229–253. [Google Scholar]
8. Bonnet, M., Maier, G., Polizzotto, C. (1998). Symmetric Galerkin boundary element methods. Applied Mechanics Reviews, 51, 669–704. [Google Scholar]
9. Xu, G., Ortiz, M. (1993). A variational boundary integral method for the analysis of 3-D cracks of arbitrary geometry modelled as continuous distribution of dislocation loops. International Journal for Numerical Methods in Engineering, 36(21), 3675–3701. [Google Scholar]
10. Li, S., Mear, M. E. (1998). Singularity-reduced integral equations for displacement discontinuities in three-dimensional linear elastic media. International Journal of Fracture, 93, 87–114. [Google Scholar]
11. Li, S., Mear, M. E., Xiao, L. (1998). Symmetric weak-form integral equation method for three-dimensional fracture analysis. Computer Methods in Applied Mechanics and Engineering, 151, 435–459. [Google Scholar]
12. Moes, N., Dolbow, J., Belytschko, T. (1999). A finite element method for crack growth without remeshing. International Journal for Numerical Methods in Engineering, 46(1), 131–150. [Google Scholar]
13. Agathos, K., Chatzi, E., Bordas, S. P. A. (2016). Stable 3D extended finite elements with higher order enrichment for accurate non planar fracture. Computer Methods in Applied Mechanics and Engineering, 306, 19–46. [Google Scholar]
14. Bechet, E., Minnebo, H., Moes, N., Burgardt, B. (2005). Improved implementation and robustness study of the X-FEM method for stress analysis around cracks. International Journal for Numerical Methods in Engineering, 64(8), 1033–1056. [Google Scholar]
15. Belytschko, T., Lu, Y. Y., Gu, L. (1995). Crack propagation by element-free Galerkin methods. Engineering Fracture Mechanics, 51(2), 295–315. [Google Scholar]
16. Atluri, S. N., Zhu, T. (1998). A new meshless local Petrov-Galerkin (MLPG) approach in computational mechanics. Computational Mechanics, 22, 117–127. [Google Scholar]
17. Rabczuk, T., Zi, G. (2007). A meshfree method based on the local partition of unity for cohesive cracks. Computational Mechanics, 39(6), 743–760. [Google Scholar]
18. Bordas, S., Rabczuk, T., Zi, G. (2008). Three-dimensional crack initiation, propagation, branching and junction in non-linear materials by an extended meshfree method without asymptotic enrichment. Engineering Fracture Mechanics, 75(5), 943–960. [Google Scholar]
19. Fish, J. (1992). The s-version of the finite element method. Computers and Structures, 43(3), 539–547. [Google Scholar]
20. Yumoto, Y., Yusa, Y., Okada, H. (2016). An s-version finite element method without generation of coupling stiffness matrix by using iterative technique. Mechanical Engineering Journal, 3(5), 16-00001. [Google Scholar]
21. Atluri, S. N. (1986). Computational methods in the mechanics of fracture. Amsterdam: North Holland. [Google Scholar]
22. Atluri, S. N. (1997). Structural integrity and durability. USA: Tech Science Press. [Google Scholar]
23. Atluri, S. N. (2005). Applications of DTALE: Damage tolerance analysis and life enhancement [3-D non-planar fatigue crack growth]. Structural Integrity and Durability, 1(1), 1–20. [Google Scholar]
24. Wang, L., Atluri, S. N. (1996). Recent advances in the alternating method for elastic and inelastic fracture analysis. Computer Methods in Applied Mechanics and Engineering, 137(1), 1–58. [Google Scholar]
25. Shah, R. C., Kobayashi, A. S. (1972). On the surface flaw problem. In: Swedlow, J. L. (Ed.The surface crack: Physical problems and computational solutions, pp. 79–124. New York: The American Society of Mechanical Engineers. [Google Scholar]
26. Shah, R. C., Kobayashi, A. S. (1973). Stress intensity factors for an elliptical crack approaching the surface of a semi-infinite solid. International Journal of Fracture, 9, 133–146. [Google Scholar]
27. Shah, R. C., Kobayashi, A. S. (1971). Stress intensity factor for an elliptical crack under arbitrary normal loading. Engineering Fracture Mechanics, 3(1), 71–96. https://doi.org/10.1016/0013-7944(71)90052-X [Google Scholar] [CrossRef]
28. Nishioka, T., Atluri, S. N. (1983). Analytical solution for embedded elliptical cracks and finite element alternating method for elliptical surface cracks, subjected to arbitrary loadings. Engineering Fracture Mechanics, 17(3), 247–268. [Google Scholar]
29. Vijayakumar, K., Atluri, S. N. (1981). An embedded elliptical crack, in an infinite solid, subject to arbitrary crack-face tractions. Journal of Applied Mechanics, 103(1), 88–96. [Google Scholar]
30. Raju, I. S., Atluri, S. N., Newman, J. C.Jr (1989). Stress-intensity factors for small surface and corner cracks in plates. In: Wei, R. P., Gangloff, R. P. (Eds.Fracture mechanics: Perspectives and directions, pp. 297–316. Philadelphia: ASTM. [Google Scholar]
31. Nikishkov, G. P., Park, J. H., Atluri, S. N. (2001). SGBEM-FEM alternating method for analyzing 3D non-planar cracks and their growth in structural components. Computer Modeling in Engineering & Sciences, 2(3), 401–422. [Google Scholar]
32. Han, Z. D., Atluri, S. N. (2002). SGBEM (for cracked local subdomain)–FEM (for uncracked global Structure) alternating method for analyzing 3D surface cracks and their fatigue-growth. Computer Modeling in Engineering & Sciences, 3(6), 699–716. [Google Scholar]
33. Raju, I. S., Fichter, W. B. (1989). A finite-element alternating method for two-dimensional mode I crack configurations. Engineering Fracture Mechanics, 33(4), 525–540. [Google Scholar]
34. Chen, W. H., Chang, C. S. (1989). Analysis of two-dimensional mixed-mode crack problems by finite element alternating method. Computers and Structures, 33(6), 1451–1458. [Google Scholar]
35. Chen, W. H., Chang, C. S. (1989). Analysis of two-dimensional fracture problems with multiple cracks under mixed boundary conditions. Engineering Fracture Mechanics, 34(4), 921–934. [Google Scholar]
36. Krishnamurthy, T., Raju, I. S. (1990). A finite-element alternating method for two-dimensional mixed-mode crack configurations. Engineering Fracture Mechanics, 36(2), 297–311. [Google Scholar]
37. Rajiyah, H., Atluri, S. N. (1989). Evaluation of K-factors and weight functions for 2-D mixed-mode multiple cracks by the boundary element alternating method. Engineering Fracture Mechanics, 32(6), 911–922. [Google Scholar]
38. Raju, I. S., Krishnamurthy, T. (1992). A boundary element alternating method for two-dimensional mixed-mode fracture problems. Computational Mechanics, 10, 133–150. [Google Scholar]
39. Park, J. H., Ogiso, T., Atluri, S. N. (1992). Analysis of cracks in aging aircraft structures with and without composite patch repairs. Computational Mechanics, 10, 169–201. [Google Scholar]
40. Gladwell, G. M. L., England, A. H. (1977). Orthogonal polynomial solutions to some mixed boundary-value problems in elasticity theory. The Quarterly Journal of Mechanics and Applied Mathematics, 30(2), 175–185. [Google Scholar]
41. Park, J. H., Atluri, S. N. (1993). Fatigue growth of multiple cracks near a row of fastener-holes in a fuselage lap-joint. Computational Mechanics, 13, 189–203. [Google Scholar]
42. Nikishkov, G. P., Atluri, S. N. (1994). An analytical-numerical alternating method for elastic-plastic analysis of cracks. Computational Mechanics, 13, 427–442. [Google Scholar]
43. Pyo, C. R., Okada, H., Atluri, S. N. (1995). An elastic-plastic finite element alternating method for analyzing wide-spread fatigue damage in aircraft structures. Computational Mechanics, 16, 62–68. [Google Scholar]
44. Pyo, C. R., Okada, H., Atluri, S. N. (1995). Residual strength prediction for aircraft panels with multiple site damage, using the EPFEAM for stable crack growth analysis. Computational Mechanics, 16(3), 190–196. [Google Scholar]
45. Park, J. H. (1993). Improvement of the accuracy of stress fields in multiple hole crack problems. Internal Report for Computational Modeling Center, Georgia Institute of Technology. [Google Scholar]
46. Wang, L., Atluri, S. N. (1995). Implementation of the Schwartz-Neumann alternating method for collinear multiple cracks with mixed type of boundary conditions. Computational Mechanics, 16(4), 266–271. [Google Scholar]
47. Tian, L., Dong, L., Phan, N., Atluri, S. N. (2014). Three-dimensional SGBEM-FEM alternating method for analyzing fatigue-crack growth in and the life of attachment lugs. Journal of Engineering Mechanics, 141(4), 04014142. [Google Scholar]
48. Tian, L., Dong, L., Bhavanam, S., Phan, N., Atluri, S. N. (2014). Mixed-mode fracture & non-planar fatigue analyses of cracked I-beams, using a 3D SGBEM-FEM alternating method. Theoretical and Applied Fracture Mechanics, 74, 188–199. [Google Scholar]
49. Tian, L. G., Dong, L. T., Phan, N., Atluri, S. N. (2015). Non-planar mixed-mode growth of initially straight-fronted surface cracks, in cylindrical bars under tension, torsion and bending, using the symmetric Galerkin boundary element method-finite element method alternating method. Fatigue and Fracture of Engineering Materials and Structures, 38(8), 923–935. [Google Scholar]
50. Tian, L. G., Hu, Z. Q., Chen, J. (2021). Experimental and numerical research on defective shield segment under cyclic loading. Shock and Vibration, 2021, 8567899. [Google Scholar]
51. Zhou, X., He, S., Dong, L., Atluri, S. N. (2022). Real-time prediction of probabilistic crack growth with a helicopter component digital twin. AIAA Journal, 60(4), 2555–2567. [Google Scholar]
52. Wang, H. K., Haynes, R., Huang, H. Z., Dong, L., Atluri, S. N. (2015). The use of high-performance fatigue mechanics and the extended Kalman/particle filters, for diagnostics and prognostics of aircraft structures. Computer Modelling in Engineering & Sciences, 105(1), 1–24. [Google Scholar]
53. Zienkiewicz, O. C., Kelly, D. W., Bettes, P. (1977). The coupling of the finite element method and boundary solutions procedures. International Journal for Numerical Methods in Engineering, 11, 355–375. [Google Scholar]
54. Li, H. B., Han, G. M., Mang, H. A., Torzchy, P. (1986). A new method for the coupling of finite element and boundary element discretized subdomains of elastic bodies. Computer Methods in Applied Mechanics and Engineering, 54, 161–185. [Google Scholar]
55. Aour, B., Rahmani, O., Nait-Abdelaziz, M. (2007). A coupled FEM/BEM approach and its accuracy for solving crack problems in fracture mechanics. International Journal of Solids and Structures, 44, 2523–2539. [Google Scholar]
56. Rungamornrat, J., Mear, M. E. (2011). SGBEM-FEM coupling for analysis of cracks in 3D anisotropic media. International Journal for Numerical Methods in Engineering, 86(2), 224–248. [Google Scholar]
57. Dong, L., Atluri, S. N. (2012). SGBEM (using non-hyper-singular traction BIEand super elements, for non-collinear fatigue-growth analyses of cracks in stiffened panels with composite-patch repairs. Computer Modeling in Engineering & Sciences, 89(5), 417–458. [Google Scholar]
58. Muskhelishvili, N. I. (1953). Some basic problems of the mathematical theory of elasticity. Groningen: Noordhoff. [Google Scholar]
59. Singh, R., Park, J. H., Atluri, S. N. (1994). Growth of multiple cracks and their linkup in a fuselage lap joint. AIAA Journal, 32, 2260–2268. [Google Scholar]
60. Park, J. H., Singh, R., Pyo, C. R., Atluri, S. N. (1995). Integrity of aircraft structural elements with multi-site fatigue damage. Engineering Fracture Mechanics, 51, 361–380. [Google Scholar]
61. Park, J. H., Singh, R., Pyo, C. R., Atluri, S. N. (1995). Structural integrity of fuselage panels with multisite damage. Journal of Aircraft, 32, 656–662. [Google Scholar]
62. Park, J. H. (1996). Analysis of an isotropic infinite plate with many collinear multiple cracks by the alternating method. Transactions of the Korean Society of Mechanical Engineers A, 20(12), 3838–3846. [Google Scholar]
63. Park, J. H., Atluri, S. N. (1998). Mixed mode fatigue growth of curved cracks emanating from fastener holes in aircraft lap joints. Computational Mechanics, 21, 477–482. [Google Scholar]
64. Cheung, Y. K., Chen, Y. Z. (1987). Solutions of branch crack problems in plane elasticity by using a new integral equation approach. Engineering Fracture Mechanics, 28(1), 31–41. [Google Scholar]
65. Cheung, Y. K., Chen, Y. Z. (1987). New integral equation for plane elasticity crack problems. Theoretical and Applied Fracture Mechanics, 7, 177–184. [Google Scholar]
66. Chen, Y. Z. (1993). Numerical solution of a curved crack problem by using hypersingular integral equation approach. Engineering Fracture Mechanics, 46(2), 275–283. [Google Scholar]
67. Park, J. H., Kim, M. W., Atluri, S. N. (1999). Analysis of multiple curved cracks embedded in an isotropic plate using the finite element alternating method. Computer Modeling and Simulation in Engineering, 4, 58–63. [Google Scholar]
68. Ingraffea, A. R., Grigoriu, M. D., Swenson, D. V. (1991). Representation and probability issues in the simulation of multi-site damage. In: Atluri, S. N., Sampath, S. G., Tong, P. (Eds.Structural integrity of aging airplanes, pp. 183–197. Berlin: Springer-Verlag. [Google Scholar]
69. Chen, W. H., Yang, K. C., Chang, C. S. (1992). A finite element alternating approach for the bending analysis of thin cracked plates. International Journal of Fracture, 56, 93–110. [Google Scholar]
70. Chen, W. H., Shen, C. M. (1993). A finite element alternating approach to the bending of thin plates containing mixed mode cracks. International Journal of Solids and Structures, 30, 2261–2276. [Google Scholar]
71. Park, J. H., Atluri, S. N. (1999). Analysis of a cracked thin isotropic plate subjected to bending moment by using FEAM. KSME International Journal, 13(12), 912–917. [Google Scholar]
72. Chen, K. L., Atluri, S. N. (1990). A finite-difference alternating method for a cost-effective determination of weight-functions for orthotropic materials in mixed-mode fracture. Engineering Fracture Mechanics, 36(2), 327–340. [Google Scholar]
73. Kim, M. W., Park, J. H. (2003). Analysis of multiple cracks in an orthotropic plate. Transactions of KSME A, 27(6), 969–980. [Google Scholar]
74. Zang, W. L., Gudmundson, P. (1991). Kinked cracks in an anisotropic plane modeled by an integral equation method. International Journal of Solids and Structures, 27, 1855–1865. https://doi.org/10.1016/0020-7683(91)90016-9 [Google Scholar] [CrossRef]
75. Wang, L., Brust, F. W., Atluri, S. N. (1997). The elastic-plastic finite element alternating method and the prediction of fracture under WFD conditions in aircraft structures. Computational Mechanics, 19(5), 356–369. [Google Scholar]
76. Wang, L., Brust, F. W., Atluri, S. N. (1997). The elastic-plastic finite element alternating method and the prediction of fracture under WFD conditions in aircraft structures. Computational Mechanics, 19(5), 370–379. [Google Scholar]
77. Wang, L., Brust, F. W., Atluri, S. N. (1997). The elastic-plastic finite element alternating method (EPFEAM) and the prediction of fracture under WFD conditions in aircraft structures. Computational Mechanics, 20, 199–212. [Google Scholar]
78. Kawai, H., O’Sullivan, K. G., O’Donohgue, P. E., Pipkins, D. S., Park, J. H. et al. (1998). Next generation design and analysis procedures for bonded composite repairs. Computer Modeling and Simulation in Engineering, 3, 153–160. [Google Scholar]
79. Okada, H., Rajiyah, H., Atluri, S. N. (1988). A novel displacement gradient boundary element method for elastic stress analysis with high accuracy. Journal of Applied Mechanics, 55(4), 786–794. [Google Scholar]
80. Han, Z. D., Atluri, S. N. (2003). On simple formulations of weakly-singular traction & displacement BIE, and their solutions through Petrov-Galerkin approaches. Computer Modeling in Engineering & Sciences, 4(1), 5–20. [Google Scholar]
81. Dong, L., Atluri, S. N. (2013). Fracture & fatigue analyses: SGBEM-FEM or XFEM? Part 1: 2D structures. Computer Modeling in Engineering & Sciences, 90(2), 91–146. [Google Scholar]
82. Sarkar, S., Apetre, N., Iyyer, N., Phan, N., Goel, K. et al. (2014). Comparison of SGBEM-FEM alternating method and XFEM method for determining stress intensity factor for 2D crack problems. Advanced Materials Research, 891–892, 345–350. [Google Scholar]
83. Smith, F. W., Sorensen, D. R. (1974). The elliptical crack subjected to nonuniform shear loading. Journal of Applied Mechanics, 41, 502–506. [Google Scholar]
84. Nishioka, T., Atluri, S. N. (1983). An alternating method for analysis of surface flawed aircraft structural components. AIAA Journal, 21, 749–757. [Google Scholar]
85. O’Donoghue, P. E., Nishioka, T., Atluri, S. N. (1984). Multiple surface cracks in pressure vessels. Engineering Fracture Mechanics, 20(3), 545–560. [Google Scholar]
86. O’Donoghue, P. E., Nishioka, T., Atluri, S. N. (1985). Multiple coplanar embedded elliptical cracks in an infinite solid subject to arbitrary crack face tractions. International Journal for Numerical Methods in Engineering, 21, 437–449. [Google Scholar]
87. Simon, H. L., O’Donoghue, P. E., Atluri, S. N. (1987). A finite-element-alternating technique for evaluating mixed mode stress intensity factors for part-elliptical surface flaws. International Journal for Numerical Methods in Engineering, 24(4), 689–709. [Google Scholar]
88. Nishioka, T., Atluri, S. N. (1990). The first-order variation of the displacement field due to geometrical changes in an elliptical crack. Journal of Applied Mechanics, 57(3), 639–646. [Google Scholar]
89. Liao, C. Y., Atluri, S. N. (1989). Stress intensity factor variation along a semicircular surface flaw in a finite-thickness plate. Engineering Fracture Mechanics, 34(4), 957–976. [Google Scholar]
90. Liao, C. Y., Atluri, S. N. (1991). A finite element alternating method for evaluation of stress intensity factors for part-circular cracks subjected to arbitrary loadings. Computer Methods in Applied Mechanics and Engineering, 91, 1253–1270. [Google Scholar]
91. Rajiyah, H., Atluri, S. N. (1991). Analysis of embedded and surface elliptical flaws in transversely isotropic bodies by the finite element alternating method. Journal of Applied Mechanics, 58(2), 435–443. [Google Scholar]
92. Mu, R., Reddy, D. V. (1994). Stress intensity factors and weight functions for semi-elliptical cracks using finite element alternating method. Engineering Fracture Mechanics, 48(3), 305–323. [Google Scholar]
93. Pipkins, D. S., Atluri, S. N. (1996). Applications of the three dimensional alternating method. Finite Elements in Analysis and Design, 23, 133–152. [Google Scholar]
94. O’Donoghue, P. E., Atluri, S. N., Pipkins, D. S. (1995). Computational strategies for fatigue crack growth in three dimensions with application to aircraft components. Engineering Fracture Mechanics, 52(1), 51–64. [Google Scholar]
95. Andra, H. (1998). Integration of singular integrals for the Galerkin-type boundary element method in 3D elasticity. Computer Methods in Applied Mechanics and Engineering, 157, 239–249. [Google Scholar]
96. Erichsen, S., Sauter, S. A. (1998). Efficient automatic quadrature in 3-D Galerkin BEM. Computer Methods in Applied Mechanics and Engineering, 157, 215–224. [Google Scholar]
97. Frangi, A., Novati, G., Springhetti, R., Rovizzi, M. (2000). Fracture mechanics in 3D by the symmetric Galerkin boundary element method. VIII Conference on Numerical Methods in Continuum Mechanics, Slovak Republic, Liptovsky Jan. [Google Scholar]
98. Frangi, A., Novati, G., Springhetti, R., Rovizzi, M. (2002). 3D fracture analysis by the symmetric Galerkin BEM. Computational Mechanics, 28, 220–232. [Google Scholar]
99. Shivakumar, K. N., Raju, I. S. (1992). An equivalent domain integral method for three-dimensional mixed-mode fracture problems. Engineering Fracture Mechanics, 42, 935–959. [Google Scholar]
100. He, M. Y., Hutchinson, J. W. (2000). Surface crack subject to mixed mode loading. Engineering Fracture Mechanics, 65, 1–14. [Google Scholar]
101. Park, J. H., Kim, M. W., Nikishkov, G. P. (2010). SGBEM-FEM alternating method for simulating 3D through-thickness crack growth. Computer Modeling in Engineering & Sciences, 68(3), 269–296. [Google Scholar]
102. Park, J. H., Nikishkov, G. P. (2011). Growth simulation for 3D surface and through-thickness cracks using SGBEM-FEM alternating method. Journal of Mechanical Science and Technology, 25(9), 2335–2344. [Google Scholar]
103. Okada, H., Kamibeppu, T. (2005). A virtual crack closure-integral method (VCCM) for three-dimensional crack problems using linear tetrahedral finite elements. Computer Modeling in Engineering & Sciences, 10, 229–238. [Google Scholar]
104. Murakami, Y. (1987). Stress-intensity factors handbook. Oxford: Pergamon Press. [Google Scholar]
105. Park, J. H., Nikishkov, G. P. (2011). Modeling and analysis of arbitrary shaped three-dimensional cracks. Transactions of the Korean Society of Mechanical Engineers A, 35(9), 1091–1097. [Google Scholar]
106. Dong, L., Atluri, S. N. (2013). Fracture & fatigue analyses: SGBEM-FEM or XFEM? Part 2: 3D solids. Computer Modeling in Engineering & Sciences, 90(5), 379–413. [Google Scholar]
107. Nikishkov, G. P., Atluri, S. N. (2002). Combining SGBEM and FEM for modeling 3D cracks. In: Topping, B. H. V., Bittnar, Z. (Eds.Engineering computational technology, pp. 167–192. UK: Civil-Comp Press. [Google Scholar]
108. Park, J. H., Park, S. Y. (2007). Elastic-plastic analysis of a 3-dimensional inner crack using finite element alternating method. Transactions of the Korean Society of Mechanical Engineers A, 31(10), 1009–1016. [Google Scholar]
109. Park, J. H. (2009). Analysis of elastic-plastic J integrals for 3-dimensional cracks using finite element alternating method. Transactions of the Korean Society of Mechanical Engineers A, 33(2), 145–152. [Google Scholar]
110. Hutchinson, J. W. (1968). Singular behavior at the end of a tensile crack tip in a hardening material. Journal of the Mechanics and Physics of Solids, 16, 13–31. [Google Scholar]
111. Rice, J. R., Rosengren, G. F. (1968). Plane strain deformation near a crack tip in a power-law hardening material. Journal of the Mechanics and Physics of Solids, 16, 1–12. [Google Scholar]
112. Zahoor, A. (1991). Ductile fracture handbook. Palo Alto, USA: Electric Power Research Institute. [Google Scholar]
Cite This Article
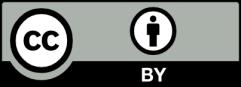