Open Access
REVIEW
Biofuel Recovery from Plantain and Banana Plant Wastes: Integration of Biochemical and Thermochemical Approach
1
School of Environment and Civil Engineering, Nanchang Institute of Science and Technology, Nanchang, 330108, China
2
School of Infrastructure Engineering, Nanchang University, Nanchang, 330031, China
3
Institute of Environmental Science, Shanxi University, Taiyuan, 030006, China
4
State Key Joint Laboratory of Environment Simulation and Pollution Control, School of Environment, Tsinghua University, Beijing,
100084, China
* Corresponding Author: Abdulmoseen Segun Giwa. Email:
Journal of Renewable Materials 2023, 11(6), 2593-2629. https://doi.org/10.32604/jrm.2023.026314
Received 30 August 2022; Accepted 20 October 2022; Issue published 27 April 2023
Abstract
Globally, fossil fuel dependence has created several environmental challenges and climate change. Hence, creating other alternative renewable and ecologically friendly bio-energy sources is necessary. Lignocellulosic biomass has gained significant attention recently as a renewable material for biofuel production. The large amounts of plantain and banana plant parts wasted after harvesting, as well as the peels generated daily by the fruit market and industries, demonstrate the potential of bioenergy resources. This review briefly assesses plantain and banana plant biomass (PBB) generated in the developing, developed, and underdeveloped countries, the consumable parts, and feasible products yield. It emphasized the advantages and disadvantages of the commonly adopted treatment technologies of composting, incineration, and landfilling. Further, the utilization of PBB as catalysts in biodiesel synthesis was briefly highlighted. To optimize recovery of biofuel, different integration routes of pyrolysis, anaerobic digestion, fermentation, hydrothermal carbonization, hydrothermal liquefaction, and hydrothermal gasification for the valorization of the PBB were proposed. The complex compounds present in the PBB (hemicellulose, cellulose, and lignin) can be converted into valuable bio-products such as methane gas and bio-ethanol for bioenergy, and nutrients to promote bioactive ingredients. The investigation of the viability and innovation potential of the integrated routes’ technology is necessary to improve the circular bio-economy and the recovery of biofuels from biomass waste, particularly PBB.Graphical Abstract
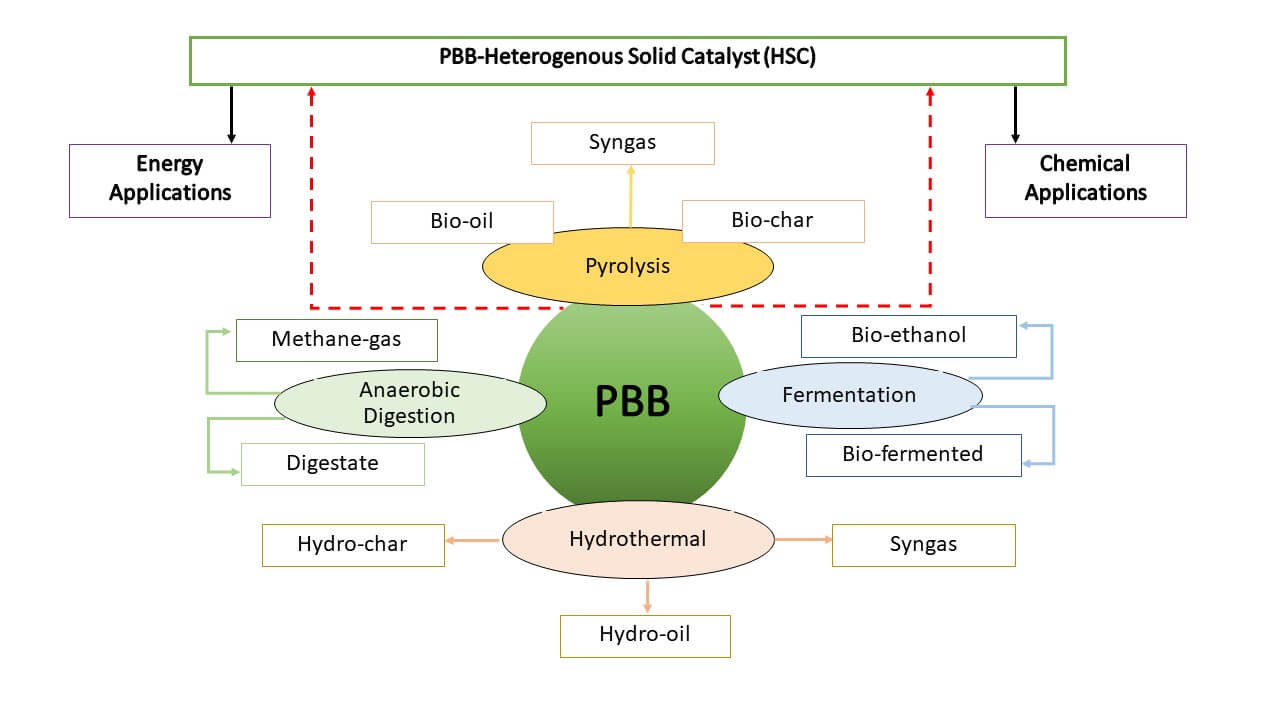
Keywords
All around the world, bio-energy has been a crucial life material, and its utilization has been growing gradually with industrial development and an increase in population. By 2030, it is anticipated that energy consumption will increase from 60% to 75%, with an accompanying increase in greenhouse gas (GHG) emissions, mostly from the burning of untreated biomass and carbon dioxide (CO2) emissions [1]. Centuries ago, fossil fuels were the primary source of energy. Unfortunately, the production is primarily via conventional crude materials, which will be exhausted and insufficient for the world’s energy demand in the immediate future. The usage of fossil fuels can play a significant role in air pollution and global warming due to burning, thus emitting a high amount of CO2 into the atmosphere, resulting in GHG and global warming [2]. Therefore, the production of biofuels, particularly bioethanol, has gained much attention due to its advantages in renewability, eco-friendliness, and local production.
Ecological and inexhaustible alternative energy resources have to be exploited for environmental pollution mitigation and to address other natural challenges. Currently, bioethanol production from sustainable feedstock such as lignocellulosic biomass (LCB), sugar, and starch materials is among those substitutes receiving attention. The dominant environmental contaminants and the high energy consumption were observed via the transportation field. The transport sector’s energy demand is expected to account for roughly 61% of global total oil consumption in 2040 [3], accounting for 1/5 of the CO2 emissions [4]. Bioethanol is considered a crucial bio-renewable energy resource to mitigate the environment’s fossil fuel dependence. Unlike nonrenewable energy sources such as fossil fuels, bioethanol can be produced through the fermentation process of sugar under specific conditions. Bioethanol production from different renewable biomass is highly profitable for the ecosystem. Furthermore, bioethanol within the near future will substitute gasoline, as it does not require any peculiar modification, demonstrating its direct utilization with the existing vehicle engines. Bioethanol has green properties as the combustion releases CO2, similar to the one used by plants to grow via the photosynthesis process. Therefore, bioethanol utilization does not contribute to GHGs [5].
The utilization of waste materials from plantain and banana plant biomass (PBB) leads to the development of an energy source that is renewable, suitable, and environmentally friendly. According to the Alzate Acevedo et al. [6] report, almost 60% of the biomass produced by bananas is wasted after harvest, and the banana waste loss amounts to roughly 114.08 million metric tons worldwide. Guerrero et al. [7] showed that about 18%–20% of produced banana peels are discharged as waste annually, which constitutes environmental degradation. The improper valorization and management of PBB would create global warming via GHG emissions. Further research revealed that removing them from the forest is preferable since allowing these items to naturally degrade can release not just CO2 but also methane (CH4) [8]. PBB is supersaturated with high industrial raw materials (starch, cellulose, hemicellulose, and abundant fibers). The raw materials in the PBB are modifiable into valuable materials with several techniques such as pyrolysis, anaerobic digestion (AD), and fermentation processes.
Numerous studies have reported improving bioethanol production from different kinds of biomass, such as hydrolysate of oil palm empty fruit [9], molasses [10], cassava peels [11], and cotton stalk lignocellulosic [12]. In China, plantain and banana (PAB) agronomy is mainly grown in Guangdong province, plus other provinces like Guangxi, Hainan, Fujian, and Yunnan Province. Globally, in 2020, 119 million tonnes of bananas were produced, and 11.9 million tons were from China [13]. Green PAB is a starch super-abundant material, where on a dry basis the amount of starch in plantain and peels is roughly 70% to 80% and 50%, respectively. Moreover, it can be extracted for various applications, for instance, biopolymers, textiles, paper, pharmaceuticals, waste water treatment, and be commercialized directly [14]. Plantains from different species have a specific amount of starch. Due to the ripening process, starch starts to break down into sugar, whereas a ripe banana contains 70% more glucose and fructose than fully ripe bananas. Kabenge et al. [15] reported that the LCB constituents in banana peel waste are hemicellulose (41.38%), cellulose (9.90%), and lignin (8.90%), while the higher and lower heating values were 16.15 and 14.80 MJ/kg. Hemicellulose and cellulose concentration proportions in banana agriculture waste vary by 24% and 57%, respectively. Cellulose, an active material, is applied mainly as organic matter in excipient production. As cellulose is a glucose monomer, it can be hydrolyzed into simple sugar to produce bioethanol by a fermentation process [16].
Many studies have been treating PBB through individual processes for harnessing bioenergy. However, to the best of our knowledge, only a few studies have been conducted to integrate different technological techniques to enhance nutrient recovery and bio-fuel yields. This review aims to propose the adaptation of existing treatment techniques and the integration of waste-to-energy technologies. The proposed technologies are fermentation, pyrolysis, AD, hydrothermal carbonization (HTC), hydrothermal liquefaction (HTL), and hydrothermal gasification (HTG) to avert PBB waste valorization challenges and associated environmental pollution for biofuel production. This paper will further evaluate the different treatment conditions of PBB and their correlated merits and disadvantages for developing enhanced biofuel production and bioactive ingredient recovery under distinct integration methods.
2 Assessment of Plantain and Banana Plant Wastes
PABs are very popular fruits all over the world. In 2018, 116 million tons of bananas and 40 million tons of plantains were harvested [17], while in 2020, it was reported that 119 50 million tons of bananas were produced globally [13]. Bananas are one of the most traded fruits in the world, with nearly 23 million tons (excluding plantains) exported in 2017, accounting for nearly 20% of global production. Precise figures on total global banana production are difficult to obtain because banana cultivation is often conducted by smallholder farmers and traded in an untraceable informal sector [18]. Local bananas, for example, account for 70%–80% of African production and have been around for over a thousand years. The majority of these are cooked bananas, which are a popular and important staple food. Only 15% of the total production is exported, and most of the production is ingested in India, China, Indonesia, etc., plus other African countries with high PAB production [19]. The Cavendish banana is the most traded, accounting for approximately 47% of global production. Around the world, approximately 11.3 million hectares are dedicated to PAB, with over 1000 varieties produced and consumed locally. Figs. 1a and 1b show the prevalence of PAB in high-productivity countries. The total amount of bananas exported from Asia in 2019 was 5.1 million tons, an increase of 42% from the 3.5 million tons exported in 2018 [6].
Figure 1: (A) and (B) World plantain production in 2016 and world banana production in 2019; redrawn from [20] and [6]
In recent decades, the world population has increased by up to 7 billion people, resulting in approximately 683 million tons of agri-food waste, 34% of which is related to food waste loss worldwide, including PBB [21,22]. PBB is made up of the following components: rotten/damaged fruits, peels, fruit-bunch-stem (stalks), leaves, fibers, pseudo-stem, and rhizome. These PBB fractions are produced by both PAB production and fruit processing. The former generates off-cuts such as pseudo-stems, leaves, fibers, and rhizomes that remain in the garden after harvesting PAB bunches, whereas the latter produces residues such as peels, fruit-bunch-stems (stalks), and rotten/damaged fruits [23]. Bananas contain 60% pulp and 40% peel, yielding 7.25 kg of peel from an 18.14 kg banana box [22]. The shell, on the other hand, contains carbon-rich organic compounds like cellulose (7.6%–9.6%), hemicel-lulose (6.4%–9.4%), pectin (10%–21%), lignin (6%–12%), chlorophyll pigments, and a few other low molecular weight compounds [22]. Suppose PAB and PBB are not adequately treated and are left in the field to decay. In that case, they emit an unpleasant odor due to natural decomposition and produce gases that contribute to GHG emissions and bioenergy loss [24].
Proper management and full-scale treatment for nutrients, biofuels, and industrial raw material recovery are thus required for PBB. PBB is considered a highly biodegradable biomass. In some underdeveloped, developing, and developed countries, unripened bulk quantities of PBB are discharged in landfills after harvesting. Around 40% of plantain produced is not commercialized, while after harvesting, approximately 60% of the PBB is left in the area for a long time and it decomposes [25]. Through eco-friendly bio-waste recovery and animal feed, plantains can produce bioethanol and other important industrial organic matters [26]. In addition, PAB crops are liable to be commercialized to develop a standard of living for the country’s rural society. PAB’s widespread consumption is a result of their appealing texture, flavor, and sensory qualities. It is also a great source of dietary fiber, vitamin C, vitamin B6, and manganese. It also has a high calorie count with little fat. The principal antioxidants that have health advantages are the phenols found in banana fruit. Bananas contain a number of phenolic compounds, including gallic acid, catechin, epicatechin, tannins, and anthocyanins [6].
About 135 tropical countries worldwide grow PAB, and it comes second in high-produced fruits, also included as the fourth-most crucial food after rice, corn, and wheat [27]. Additionally, in highly developed countries, bananas are widely valued as a food of convenience because they are affordable, transportable, and generally healthy. Asia and the American continent’s overall banana production peaks at 63 million tons and 29 million tons annually, respectively, while in the USA, about 12.247 kg of PAB is consumed per capita [28]. As previously mentioned, many PBBs are produced independently from country to country based on a variety of criteria, including the fact that several PAB plants exposed to the environment decompose after being harvested. Wasteful PBBs have enough renewable biomass potential for biofuel and nutrient recovery using thermochemical and biochemical methods [29,30].
When PABs are grown and harvested, a large amount of waste (including leaves, pseudo-stems, rhizomes, and peel, among other things) is collected along with the entire fruit at the storage stage to generate PBB, which does not meet the requirements for sale [31], though the PBB can reflect massive bioenergy potential for the future. Furthermore, PBB can be transformed and used in a variety of activities, including biofertilizers, textiles, polymer synthesis, waste water treatment, and others [32]. On the other hand, biomass energy waste and environmental pollution are still challenging due to inadequate treatment techniques, especially in highly biomass-developed producer countries. Furthermore, simulation techniques for treating PBB have been implemented in developed nations, but the energy and nutrient recovery is still limited based on the single treatment approach.
2.2 Developing and Underdeveloped Countries
PAB is a highly essential and staple crop in developing and under-developed countries. It assures food stability with high production and raises earnings for those small and local agriculturalists who are considered the biggest producers. In most poor societies with food challenges, plantain tubers, roots, and banana fruits are considered the leading diet sources as food for over 3 billion people in developing and under-developing countries, with a commercial value of US $339 billion [33]. Unlike developed countries, these nations possess severe problems such as water pollution, land, and air adulteration, and loss of bioenergy resources correlated with mismanagement of biomass waste. In West Africa, developing countries are suitable for growing PABs, with around 32% of global plantain production [34]. Much PAB is consumed locally in most underdeveloped and developing countries, leading to the most significant challenge on the industrial scale that uses this biomass as a raw material.
On the other hand, the PBB waste energy content can be converted into other forms of energy products, for instance, bio-CH4, bio-oil, biochar, syngas, and other crucial organic substances. Several studies have found PBB and its plants to be an excellent raw material source for biofuel production. Specifically, bioethanol from PBB [35] and biochar production by co-pyrolysis with other PBB for heavy metal extraction from waste water [29] or other valuable industrial processing products. Modern agriculture processing of biomass produces vast amounts of waste, and the quality of essential constituents like hemicellulose, starch, cellulose, simple sugar, and lignin is compromised if not properly managed [36]. LCB is the best feed for bioethanol, electricity, or syngas production via pyrolysis or gasification processes for commercialization and industrial purposes. The widely adopted techniques that convert LCB to bioenergy are thermochemical, biochemical, chemical, and biological processes [37]. These techniques can serve similar purposes in the valorization of PBB for bio-energy products and other resource recovery.
3 Utilization of Plantain and Banana Biomass as Catalysts in Biodiesel Synthesis
Because of the tremendous industrialization and population growth in today’s globe, the global demand for energy is rising drastically. Fossil fuels account for the majority of the world’s energy needs, but, because of excessive fuel consumption, they will run out by 2050 [38,39]. Global warming is being caused by an increase in the emissions of GHG from the use of non-renewable fossil fuels. Renewable fuels like bioethanol and biodiesel have therefore come to be thought of as viable fuels that could replace traditional energy sources in order to keep up with ongoing innovations and rising energy demands [40]. Being biodegradable, non-toxic, renewable, and carbon-neutral makes biodiesel an environmentally benign fuel, which has garnered it increased attention on a global scale. Biodiesel is often produced using waste oils, microalgae, animal fats, and vegetable oils. In the presence of an acid or alkali catalyst, the triglycerides from vegetable oils or animal fats react with alcohol, often of shorter chains, to generate fatty acid alkyl esters such as methanol, ethanol, propanol, and butanol [41]. The term “transesterification” has been used to describe this process. Fatty acid methyl esters (FAME) produced have molecular characteristics similar to paraffinic petroleum molecules. It is utilized as biodiesel in diesel engines without modifying them.
There are some difficulties with using homogenous alkali or acid catalysts. These include excessive reactant use, soap creation, environmental contamination, and separation challenges that could raise the cost of producing biodiesel [38,41]. Numerous issues with homogeneous catalysts have been addressed by the use of heterogeneous solid catalysts (HSC). Due to its reusability, recoverability, eco-friendliness, non-corrosiveness, and lack of soap production, the development of HSC from waste biomass has attracted attention recently [42]. Fig. 2 depicts biodiesel production using HSC derived from processing PBB.
Figure 2: Depicting utilization of PBB as a catalyst in biodiesel synthesis
The effects of the waste’s negative environmental effects can be reduced by synthesizing HSC and using it as a catalyst in biodiesel synthesis. Biowaste-derived catalysts have been highlighted in previous papers as a potential source for catalysts to be employed in the transesterification process. Banana peel, banana trunk, and banana peduncle catalysts have already been investigated in the creation of biodiesel [43]. Odude et al. [41] reported the synthesis of HSC from fruit peels, mature bananas, unripe plantains, rubber seed wastes, sugarcane bagasse, banana trunks, cocoa pod husks, flamboyant pods, and biochar-based materials. HSC was developed and characterized using banana fruit peels and was subsequently applied to biodiesel synthesis using Napoleon plume oil and neem oil, respectively. It was claimed that by utilizing a catalyst consisting of 2.75 wt% of the ash from banana fruit peels, a methanol/oil molar ratio of 7.6:1, a reaction period of 69.02 min, and a reaction temperature of 65°C, the maximum biodiesel output (98.5 ± 0.18 wt%) from Napoleon plume’s oil could be achieved [44]. Plantain stem ash was studied by Sarma et al. [45] as an HSC for the production of biodiesel from Jatropha curcas oil. In the experiment, the dried underground plantain stem was burned to make the catalyst, which was then made by treating the ash in a muffle furnace at 550°C for two hours. SiO2 (36%), K2O (25%), CaO (10%), MgO (10%), P2O5 (4%), and Al2O3 (4%) were identified as the catalyst’s primary constituents by XRF analysis. According to reports, the catalyst has a surface area of 39 m2/g, and TEM scans confirmed its nanosize (less than 100 nm). Using a high pressure (4.2 MPa) and high temperature (275oC) reactor, the transesterification of Jatropha curcas oil produced biodiesel with a yield of 98% in one hour. The catalyst in this study was also found to be reusable up to three times. The usage of the catalyst for the third time resulted in a 20% reduction in efficiency, which may have been caused by potassium leaching from the catalyst.
Several studies on PBB-derived HSC in biodiesel production were conducted and reported. Seed oil samples were transesterified to the corresponding FAMEs using a catalyst derived from Musa balbisiana Colla (a variety of banana plant) at an ambient temperature of 30oC–35oC in less than 4 h with yields of 90–96 wt% [46]. In order to produce biodiesel from used cooking oil, Gohain et al. [47] examined the activity of a plantain peel ash catalyst. The plantain peels were first thoroughly cleansed with water, dried in a hot oven at 80oC for 48 h, and then burned. The ash that resulted from this process was further calcined at 700oC for 4 h and utilized as the solid catalyst in the experiment. By analyzing the catalyst using XRD, it was possible to confirm the existence of K and Ca as carbonates, oxides, silicates, and sulfides. It was discovered in the investigation that the calcined catalyst had 41.37% of K, 36.08% of Ca, 12.02% of Mg, and 10.41% of Na, along with a trace amount of Zn. The components present in the catalyst were also analyzed further by EDAX. The catalyst’s BET surface area was estimated to be 10.176 m2 g−1. Under ideal conditions, the transesterification of used cooking oil demonstrated a conversion of 100% biodiesel in 3 h with a catalyst load of 2% and a methanol to oil ratio of 6:1 at 60oC. The efficacy of the catalyst in the repeated reaction cycles was observed to have diminished due to K and Ca leaching in the examination of recycling and the reusability of the catalyst made from plantain peels up to five times. In comparison to commercial catalysts and other catalysts made from renewable biomasses like egg shells, fish scales, and bones, the HSC made from agricultural waste, including PBB, are highly active for catalyzing the transesterification of oil to biodiesel with a shorter reaction time and higher conversion up to 100% [38].
4 Conventional Plantain and Banana Plant Wastes Treatment Techniques
4.1 General Treatment Overview
Most countries worldwide use the peels, leaves, and plants from PAB crops for animal feeding. Numerous studies show that this fruit is well grown in tropical countries, which leads to a high generation of peels in those nations where PABs are consumed as staple foods [48]. Moreover, PBBs are generated as waste in rural and urban areas in both exporting and importing countries. As previously highlighted, in developing countries such as South America, Southeast Asia, and Africa, these fruits are essential dairy food for over 400 million people [18]. Most PAB importers are the USA, China, Japan, Germany, and the Netherlands, while exporters are Ecuador, the Philippines, Costa Rica, Guatemala, and Columbia. Typically, 40% of the fruits are from peels, with approximately 200 tonnes produced daily. PAB utilization will increase due to the industrial revolution for those who use PAB as a source of raw materials [49]. About 18%–20% of produced banana peels are discharged as waste annually, which constitutes environmental degradation [7].
PBBs are generated as kitchen waste material, which is taken as food for animals. This occurs widely in tropical nations. Many people provide fruits, plants, and peels to their cattle in developing countries due to the availability and low cost of these feed sources. For instance, the high demand and fabrication of unripe plantain chips in Nigeria also contribute to the tonnes of plantain peels produced, which can also be taken as animal feed [50]. Numerous studies have reported advanced fruit peel and plant applications for livestock feed optimization [51]. Because PBB contains a significant amount of organic material and water, it cannot be disposed of in a landfill under existing law [31]. PBB’s high moisture content makes it challenging to valorize using pyrolysis and incineration techniques. In this regard, the valorization of PBB into bioethanol using biorefinery technology appears as a possibility for this kind of industry’s energy integration. In general, the technologies (HTC and HTL) used for PBB valorization are effective, functionally equivalent, and appropriate for long-term resource recovery from PBB [23]. Their respective outputs demonstrate how these strategies differ from one another. Both technologies’ operating temperatures, which are respectively 200°C–290°C for HTC and 280°C–420°C for HTL, are rising and it is becoming more difficult to distinguish between them. Due to the competitive effect, the temperature of HT under the same system typically had an intermediate ideal value. When high moisture biomass is being valued, the HTL process outperforms the HTC in terms of hydrogenation and deoxygenation, which can be seen in the O/C content. Because of this, HTL products (bio-oil) have a comparatively greater HHV than HTC. But the HTL method will pay a higher price due to the higher treatment temperature [23].
Ripe plantain can replace maize and corn by up to 75% in broiler feeds [52]. The PAB provides food security in tropical nations [53], whereas about 90% of the produced PAB is consumed in producer countries. Approximately 250 kg per capita is consumed in underdeveloped and developing countries, especially in the poorest countries. PABs have become a staple food in many tropical and subtropical communities because of their significant contributions to food security and reducing hunger. The distribution of metabolites throughout the various sections still plays a crucial role in determining how nutritious and healing they can be. Oyeyinka et al. [54] carried out a study to determine the nutritional and mineral content of the flesh, peel, and peel extract components of the fruits of Musa sinensis L. and Musa paradisiaca L. as well as their nutritional and therapeutic potential. The results of the proximate analysis showed that the flesh and peel of M. sinensis L. and M. paradisiaca L. both contain significant amounts of moisture, fiber, carbohydrates, and low-fat content, while minerals K, Mg, Ca, Na, P, and N were significantly concentrated in the peels and peel extracts in particular. Safe levels of alkaloids, oxalate, saponin, and phytate were found according to the World Health Organization Standard. According to the study, M. sinensis’ peel, M. paradisiaca derivative extract, and its flesh all have potential health benefits. The use of PBB with its derivatives offers high adsorption affinity and selectivity towards gold extraction from bioactive components [55]. Okorie et al. [56] looked at the mineral and heavy metal content of the peels of unripe plantains, ripe plantains, unripe bananas, and ripe bananas in an effort to promote the bioconversion of PBB into beneficial compounds. Using established methods, the total protein, C, Mg, K, Na, P, Zn, Cu, and Pb composition of the peels of unripe plantains, ripe plantains, unripe bananas, and ripe bananas was examined. The levels of Ca, Mg, K, Na, P, Zn, Cu, and protein were all rather high in the peel samples under study. However, the amounts of Pb were all relatively low and unlikely to have any negative consequences. The study demonstrated the nutritional value of these plants’ peels.
The different treatments and applications of PBB are highlighted in (Table 1). Some of the mentioned technologies are further discussed in the sub-sections. Several conventional treatment approaches, such as pyrolysis, AD, composting, and other thermal processes, have been applied individually to valorize PBB for biofuel production.
Pyrolysis is an ecologically friendly and well-known method of renewable biomass waste treatment for bioenergy production. It contributes to replacing fossil fuel usage by putrefying biological substances in limited or no oxygen (O2) conditions to produce bio-oil, syngas, and biochar. Pyrolytic conditions determine the yield of the pyrolysis product, and there are distinct types such as conventional/slow, fast, and flash pyrolysis. Biomass can be expressed as organic matter, and the amount of biomass produced is almost 105 billion metric tons of carbon annually. Ideally, biomass decay over a long time emits CO2 and a limited amount of CH4, resulting in global warming. The primary biomass is still considered wood for numerous processes. In some studies, PAB plant and peel wastes were pyrolyzed for resource recovery and to avert environmental challenges [57,68]. Pyrolysis products have demonstrated excellent performance in biofuel production, waste water treatment, soil amendment, and contribution to the extraction of toxic heavy metals [69,70].
Pyrolysis can be performed under different pyrolytic conditions such as temperature, heating rate, and duration, and these parameters determine the applied pyrolysis type. Conventional pyrolysis has a heating rate of 0.1–1 °C/s, duration of 10–100 min, and a temperature of less than 300°C. It will offer a high biochar yield compared to bio-oil and syngas as products. Fast pyrolysis proceeds at a rapid heating rate of 10–200 °C/s with a moderate temperature range of 350oC to 700°C, which has been reported to yield an equal amount of biochar and bio-oil as syngas. In contrast, flash pyrolysis (usually called ultra-fast pyrolysis) applied at a temperature range of 900oC to 1300°C and a fast heating rate of >1000 °C/s, yields a high amount of bio-oil and syngas, but it depends on the types of biomass [71]. Flash pyrolysis temperatures dramatically altered the morphology of the chars, resulting in the loss of the original biomass cell structure, sintering, and macropore development [72]. From an industrial perspective, pyrolysis can produce chemical compounds and other essential materials. Acetic acid, furfural, and phenolic compounds are some of the representative chemicals obtained from the pyrolysis of LCB.
Biomass conversion by thermochemical methods, for example, pyrolysis, has shown tremendous potential in the treatment of carbonaceous materials. Its products can be used in many fields for bioenergy, nutrient recovery, and agronomy. Te et al. [73] reported the optimization of pyrolysis parameters for the production of biochar from banana peels. Based on pyrolytic characteristics and biochar yield, the ideal biochar with the greatest potential for agricultural use was selected. The elemental content of the biochar was used to calculate the elemental ratio on a molar basis, which is important in figuring out whether or not the banana peel is suitable for use in the slow pyrolysis process that produces biochar. Pyrolysis was recommended for LCB treatment (e.g., PBB) to generate bioethanol, produce syngas converted to bioethanol via catalytic conversion, and produce bio-oil, which shows the ability to compensate for fossil fuels if it is improved [74]. Organic materials can also be treated for reusable products through pyrolysis application [75]. The remarkable advantage is that pyrolysis is more flexible and suitable for application on a large scale to generate numerous different chemical materials. Fig. 3 illustrates the route of bioethanol production via pyrolytic syngas from PBB.
Figure 3: Production of bioethanol from plantain and banana plant waste via pyrolysis process
Lignocellulosic plants such as PAB waste are biomass with a potential renewable energy source for the future, which will lessen the use of non-renewable fuels. Safarian et al. [76] studied pyrolysis syngas with many other different kinds of agricultural biomass for bioethanol production and found that carbon monoxide (CO) and H2 in the syngas are the core paramount gases. High ethanol yield production is feasible to modify CO and H2 in pyrolytic syngas output. Hydrocarbon production from LCB under catalytic conversion of syngas products was investigated and reported [77].
Incineration is a well-known thermochemical technology. Waste stream incinerations often proceed with an ample supply of O2 to produce particulate matter, ash, water, CO, and CO2, trace hydrocarbons, heavy toxic metals, radioactive contaminants, and acid gases. The incineration of biomass offers waste to energy, and the thermal process has been applied to treating several wastes and gained prominence over time. The incineration technique has waste treatment potential for reducing the waste stream and energy recovery compared to landfill [78]. In the incineration of organic materials and biomass, energy is produced in the form of electricity or heat. It is associated with some challenges, such as environmental contamination in terms of GHG emissions (e.g., CO, CO2, SO2 plus dust) and other associated health problems [79]. The pollutants or contaminants discharged during the incineration of biomass materials are polymeric substances. These are polychlorinated biphenyls, polychlorinated dibenzodioxins, polycyclic hydrocarbons, and toxic metals.
About 2.01 billion tonnes of municipal solid waste (MSW) are produced annually worldwide, with approximately 33% directly discharged into the environment without specific treatment, while about 44% is generated from agricultural waste. MSW is projected to increase in 2050 by up to 27 billion tonnes, mainly in Sub-Saharan Africa, South Asia, and East Asia-Pacific [80]. Recently, highly advanced monitored incinerators have been designed to address the environmental pollution problem. Some modern cities have adopted Integrated Waste Management Facilities (IWMF) to reduce the amount of discharged waste to landfills. IWMF was conducted in the metropolitan areas of Barcelona in 2018–2019 and in Hong Kong, with developed incinerator reactors that can treat three thousand tonnes daily [81]. Japan’s small landmass leads to inadequate space for landfills, therefore, incineration is applied as an MSW treatment to generate electricity, especially in urban cities with massive biomass generation [82].
Numerous studies have proposed the incineration of MSW into ash before being discharged to landfills. Biomass incineration generates fly ash as a potential raw material source for other industrial products. In Wang et al. [83] designed cement production, he discovered the presence of silicon in municipal solid waste incinerated ash with magnesium oxysulfate to improve the stability with an outstanding binding of 99.8%. Due to the high generation of MSW in China [84], approximately 12.4% of bottom ash from incinerated MSW can be used as a raw material to substitute portland cement clinker [85]. Ash generated from incineration can amend soil properties [86]. The application of incineration to different biomass products is presented in (Fig. 4).
Figure 4: Different application of the incinerated biomass/PBB products
Recently, the incineration of organic and inorganic matter has been applied in different aspects. This process has been advanced by increasing efficiency and reducing environmental pollutants, and some studies have integrated these methods with other treatment techniques [87]. Even though it is a waste-to-energy method, PBB valorization appears to be a good fit for the technology. There may be a number of bottlenecks that present problems. The widespread use of this technique as a means of energy recovery is prohibited by the high capital, operating, and maintenance expenses of waste incineration facilities. The high moisture content of PBB has an impact on both direct combustion and incineration, making it challenging to operate a plant continuously and optimally due to the need for extra fuel [23]. Considering the high humidity feature of PBB, the incineration might pose a slight limitation on its flammability. Hence, the combination of PBB with other highly flammable organic materials such as wood and cardboard is suggested to enhance the incineration performance. Incinerated biomass and PBB products are applicable in different ways to enhance soil characteristics, raw materials for industries, mineral extraction, and electricity production. Incinerated biomass and PBB products are applicable in different ways to enhance soil characteristics, raw materials for industries, mineral extraction, and electricity production.
Hydrothermal Carbonization Process
The conversion of biomass by pressure and heat with water to produce hydro-oil, gas, and hydro-char is called the HTC process [88]. Pretreatment such as biomass drying is not required for this method, and HTC energy consumption is less than the pyrolysis process. According to Heidari et al. [89], this method improves biomass hydrophobicity and dehydration, as well as fuel characteristics, thus, water is regarded as an essential feature [90]. Operating HTC enlarges the amount of ash within the hydro-char, mostly from lignocellulosic-rich biomass [91]. The HTC products can be applied in diverse aspects. Hydro-char can be used as an additive in AD to stabilize and improve CH4 production yield [92]. It has been found that hydro-char can improve soil properties and act as a detachment for the reduction of GHG emissions. Several papers also refer to hydro-char from HTC as recalcitrant [93].
The different HTC carbonization routes of PBB or biomass are proposed in (Fig. 5). The HTC of the biomass/PBB produces three products (HTC-liquids, syngas, and char) and they are applied under different routes. Biomass can produce aqueous intermediates under the degradation process, which can be polymerized and condensed to generate biochar [94]. Through the HTC process, syngas produced can generate bioenergy (e.g., bioethanol) via catalytic conversion, and aqueous liquid with AD produces CH4 gas [95]. HTC was used to valorize giant bamboo, coffee wood, eucalyptus, and coffee parchment after 3 h of residence time and temperatures ranging from 180°C, 200°C, 220°C, and 240°C [96]. Below 220oC, high hydro-char content of 24.6–29.2 MJ kg−1 was produced, which shows the excellent ability for biofuel production. Based on the organic acid of aqueous HTC liquid with a pH in the range of 2.9–4.4, around 33.8%–53.0% of fixed carbon was generated. Different biomasses were processed via HTC at a temperature range of 160°C to 300°C. They discovered approximately 57% of H2 in HTC-syngas [58]. Based on the current energy demand, H2 is an excellent option for a green future and the environment.
Figure 5: Hydrothermal carbonization routes of biomass wastes
HTL is a promising technique for renewable bio-crude oil generation from organic materials. HTL can be performed at a temperature and pressure in the range of 200°C to 400oC and 10–15 MPa, respectively, to produce bio-crude oil, solid-phase (Char), gas (HTL-syngas), and aqueous phase. The HTL aqueous phase, supersaturated with complex organic matters and nutrients, can be treated with AD for bioenergy production and nutrient recovery [97]. Several studies have improved the biomass-to-bioenergy conversation, particularly biofuels via thermochemical and biochemical technologies. Biomass liquefaction can be achieved directly via HTL, with no need for biomass pretreatment with drying [98]. Additionally, HTL produces bio-crude oil by converting the total carbohydrates, proteins, and lipids present in biomass [99]. HTL has attracted the attention of many researchers. The mechanism of organic matter transformation to produce bio-crude oil with HTL and the respective by-products applications for industrialization is essential to date.
Investigating various methods for converting PAB plants/biomass into bioenergy, HTL demonstrated remarkable and suitable potential for treatment and production of biofuels. PAB can produce good bio-oil due to the significant contribution of carbohydrates and proteins [100]. In addition, compared with most bio-oil producers’ technologies (flash pyrolysis), the HTL technique is more suitable for PAB plant biomass treatment, owing to the PAB moisture content of 60.44% and 71.37% [59]. At the same time, it does not require drying and dewatering pretreatments.
Recently, HTG has received excellent attention for biofuel production, and it is classified due to the applied temperature range. In contrast to HTL, which produced bio-crude oil at temperatures ranging from 300°C to 350oC. When the temperature increases above 374oC, biomass gasification occurs, producing CH4 and CO2 as the main products. The majority of H2 is created from fossil fuels by coal gasification, partial oxidation of heavier hydrocarbons, steam reforming of natural gas and other light hydrocarbons. Other techniques of producing H2 include electrolysis of water [101], zero-CO2-emission methane pyrolysis [102], and biomass gasification [103]. Li et al. [104] reported the conversion of glucose to H2 in a polymer exchange membrane electrolytic cell and an integrated device consisting of a liquid catalyst fuel cell stack. Glucose can act as a source of H2 for bioenergy production. Another way of producing H2 rich syngas is the valorization of PAB/biomass at a high temperature with catalytic support [105]. Receding energy demand makes H2 rich syngas an excellent option for energy and a green future.
With the aid of a catalyst, HTG with supercritical water gasification (SCWG) may be an effective green technique for producing H2 from PBB and other agricultural waste. Okolie et al. [60] reported alternate energy resources from agricultural waste/biomass with the application of SCWG for H2 recovery in light of growing fuel prices, diminishing fuel resources, increasing energy demand, and the environmental difficulties of biomass. They produced H2 by gasifying agricultural crop residues, including flax and soybean straw biomass, at subcritical and supercritical temperatures (400°C and 500°C, respectively). The effects of temperature (300°C–500°C), biomass-to-water ratio, BTW (1:5 and 1:10), biomass particle size (0.13 mm and 0.8 mm), and residence time (30–60 min) on H2 production were investigated at a pressure range of 22–25 MPa in order to maximize the non-catalytic process. Soybean straw biomass produced the highest H2 yield and total gas yields of 6.62 mmol/g and 14.91 mmol/g, respectively, at the highest temperature (500°C), lowest feed concentration (1:10 BTW), smallest particle size of biomass (0.13 mm), and longest residence time (45 min). For the respective biomass waste assessment, it was discovered that the KOH catalyst increased the H2, CO2, and CH4 yields.
PBB/biomass has high water content, thus, there is no need for water in the PBB/biomass conversion to energy during valorization with the HTG technology. Some proposed catalysts have been used and shown outstanding achievement: platinum monometallic, transition metal oxide, Ni/Al2O3, sodium silicate, and Ni catalysts [106] to enhance the production of H2 from biomass. Because biomass has a complex structure (lipids, carbohydrates, and proteins), the biofuels produced through direct thermochemical conversion contain a lot of heteroatoms (O2, nitrogen, and sulfur). Catalyst-based technologies have come to light as a viable remedy for the rise in biocrude generation [107]. In recent decades, HTG has been used as an alternative way to produce H2 gas at a low heating rate and temperature for bio-energy production. At temperatures above 374oC, the biomass oxidation reaction begins, and the by-product gases are N2, CH4, and CO2 as burnable gases to generate energy [61]. Another study, investigated how sewage sludge biomass and glucose may be used to produce H2 by SCWG/HTG. The authors of the study concluded that until H2 prices exceeded $5 kg−1, there were no profits associated with a glucose feed concentration of 15% with the bio-solid [108]. To maximize economic efficiency, the SCWG/HTG technology still requires a thorough understanding of process ideas and plant elements. HT processing technology can be commercially viable, but more research is required, notably in the valorization of PBB.
PBB is a biodegradable organic agricultural waste that contributes significantly to the circular agricultural waste stream. PBB biomass is widely grown in tropical countries such as Africa and Asia. Most of the biomass is left on the field for decomposition, notably in African countries, due to poor agro-wastes treatment in a sustainable way. Agricultural waste treatment and biomass suitable as renewable energy sources pose severe challenges in urban areas if inadvertently disposed of [109]. The associated advantages of composting biomass are that it affords a balance of minerals for agro-sectors. Several studies for microbial and chemical reactions such as ammonification, carbon pegmatite, hydrolysis, humification, and hydrolysis were examined, and composting was rated the most efficient of those treatments. However, according to Villar et al. [110] study, the optimal maturity of biomass composting is referred to as the curing phase, where many modifications take place. During composting maturity rate, biomass’s nitrification reaction, chemical and ecological conditions were reported as promoters for nitrogen modifications [111]. Improper composting of agro-wastes causes environmental issues such as GHG emissions and the release of other harmful substances into the ecological system, such as toxic heavy metals.
For contaminants’ minimization, it is essential that composting of organic substances be optimized. According to Al-Rumaihi et al. [112], fossil fuel combustion accounts for 60% of global warming, with composting coming in second at 40%. The hybrid AD method and SimaPro software, windrow composting, are ecologically friendly and are two advanced composting treatment techniques. The optimal composting of biomass requires other physico-chemical components such as aeration (supply of O2), temperature, moisture content, carbon to nitrogen ratio, compaction degree, size of particles, and pH [113]. Because the biomass treatment method is linked to the microbial community, a low supply level of O2 can have a significant impact on composting methods [114]. The O2 supply levels have an impact on the compost standard and microbial growth within the treatment method. The impact of active and passive aeration systems on compost processing showed that active aeration was satisfactory with around 37.30%, compared to passive aeration conditions [115]. LCB composted at a low aeration level leads to poor degradation, low temperature, and low NH3 content [116]. Composting is a long-term process to get completely composted biomass. The addition of some additives can enhance the composting rate and product. The additives are categorized as biological, mineral, and organic matters such as microbes, zeolite, charcoal, lime, red mud, fly ash, biochar, inoculum, phosphor gypsum, leaf filter, etc. [117]. The study extensively discussed additive and amendment effects on compost products and the composting period.
The process of converting organic matter into bioenergy in the absence of O2 is called AD. This treatment method has been performed for many decades and is considered eco-friendly. AD is carried out consecutively within four phases: hydrolysis, acidogenesis, acetogenesis, and methanogenesis [118]. Several factors influenced AD performance. Highly considered conditions are pH, temperature, C/N ratio, and temperature. Many researchers have recently shown great progress in optimizing this process by defining distinct digestion parameters. The high by-product is obtainable for LCB via developing the C/N ratio by co-digestion of different biomass, bio-physiochemical pretreatment promoting the hydrolysis process, and the use of several additives [119]. The lack of bio-electrochemical systems to monitor the AD process at an optimum level is a challenge for the AD process. Despite many shortcomings affecting AD operations, urgent efforts to attain the highest CH4 and nutrient recovery yield are necessary. Studies showed ammonia as the primary inhibitor, it mitigates methanogenesis at the last stage of the process and has a minor impact on the acidification and hydrolysis phase [120]. In AD, Total Ammonium Nitrate (TAN) not greater than 200 mg/L was observed to be conducive and acceptable [121]. Most of the studies described some techniques for ammonia reduction, such as co-digestion by changing the C/N ratio, exchange of ions, air stripping, and adsorption, and also pH monitoring in the range of 6.5 (±0.5) was observed as a suitable method, promoting sustainability, stability, and the increase of CH4 production [122]. The AD process for bioenergy production uses a variety of feedstocks, including animal and agricultural biomass. The core products of AD from biomass are CH4, CO2, and digestate with high-loaded minerals such as TAN and other recovered nutrients, which can be applied in the agriculture sector for enhancing soil properties. In addition, Deng et al. [123] recommended TAN extraction through different technologies as a source for nitrogen recovery.
Biologically, PBB is a LCB that is produced in large quantities and is considered an alternative source of bioenergy. Thus, PBB biomass can serve as a great feed to AD to produce CH4 instead of emitting GHGs into the environment. Banana tree plant biomass is an excellent feed to AD, where CH4 and CO2 production were around 65% and 40%, respectively, with saturated digestate [64]. The digestate product is applied in other agriculture sectors, bio-CH4 and electricity are retrievable during biogas refining [64]. Tambuwal et al. [124] studied the creation of biogas from banana and plantain peels that had been fertilized with cow dung. An improvised laboratory anaerobic digester was used to conduct the experiment for 35 days. The seeded sample produced the most gas throughout the retention period, followed by the fresh sample and the dried sample. When compared to plantain peels, banana peels were found to be a better biogas producer, with the biogas produced having a calorific value of 6684 kcal/kg as opposed to 6535 kcal/kg for plantain peels. The PAB peels both had a small decrease in pH, from 7.2 to 5.68 and 7.4 to 6.1, respectively.
Lignocellulosic plants constitute about 10% to 25% of the lignin, referred to as an AD inhibitor. In that sense, lignin has to be extracted through pretreatment to stabilize AD and promote biogas production. In the lignin extraction and pretreatment techniques, the organosolv method showed great purity, compared to sulfur extraction techniques, with the amount of potassium hydroxide (KOH), which acts as an activator for promoting porosity, leading to an increase in surface area for the adsorption of lignin [125]. Several studies, however, have found that LCB with a high C/N ratio can reduce CH4 production in AD. In contrast, the symbiotic co-digestion of poor and high C/N ratio feedstocks for AD can promote biogas production [126]. Africa and Asia are high producers of this kind of biomass, mostly in tropical countries, and AD seems to be a suitable biomass treatment. The African Biogas Partnership Program and Winrock International projects constructed 3660 biogas plants in Africa, Vietnam 140698, and Cambodia 17450 [127,128] to produce bio-gas and digestates from 2009 to 2015.
PBB (banana processing wastes like peel, peduncle, and pseudo stem) were taken as suitable feedstock for AD because they are considered putrid organic wastes [129]. Through the characterization and batch digestion studies, they are evaluated for their suitability and potential for biogas generation. An investigation of the physicochemical properties of banana wastes, specifically banana peel, pseudo stem, and fruit bunch stem, was conducted. The capacity of the banana wastes to produce biogas was also examined using an experimental batch AD setup. According to the characterization investigation, the concentration of total solids and volatile solids in banana waste ranges from 10.1% to 14.63% and 14% to 19%, respectively. The specific biogas production (L/kg of feed) from batch studies was discovered to be approximately 0.35 L/kg/day, and the mixture of 75% crushed banana peel and 25% cow dung produced the greatest results, with a greater gas production of 3.85 L. According to the batch digestion study and examination of its physicochemical characteristics, banana waste has the potential to be an efficient feedstock for the production of biogas. Using PBB as organic waste for biogas production through AD is a sustainable method of obtaining energy from waste. It addresses the two main issues of energy demand and environmental protection.
The landfill serves as a biochemical reactor with ecological and biodegrading features for LCB, and it is the source of hydrolytic enzymes [130]. An enzyme is essential to human and industrial applications as it catalyzes starch, protein, and lipid breakdown [131]. Besides, it can generate bio-energy and electricity when integrated with other technology. This process has been adopted and performed in many countries for many decades. The closed and active landfills in the European Union number are around 500,000 and 150,000, respectively. Although the incineration process requires enormous capital to construct facilities, it demands a high-temperature level. Other treatment techniques, such as pyrolysis, HTC, HTL, HTG, composting, and AD, are costly. Landfills are preferred over incineration because they require less labor and are less expensive. Evaluated GHG emissions from landfills show that if integrated with a gas monitoring device and channeled for power and bioenergy (CH4) production, it is environmentally friendly [132].
The improper disposal of LCB is one of the global warming challenges. The discharge of biomass in landfills contributes to environmental problems by emitting GHGs such as CH4 and CO2 into the atmosphere. Biogas produced in landfills constitutes about 50%–70% of CH4, and this gas is considered to degrade the environment 20–25 times more than CO2 [63]. Several ecological degradations such as phosphate water pollution, GHGs, and the discharge of toxic heavy metals into the environment have a connection to landfilling and lead to severe water, soil, and air difficulties [133]. After harvesting, most producer countries release PAB waste into the field for degradation. This is especially common in developed and developing tropical countries. Proper agro-biomass management and technological methods can reduce landfilled biomass and GHG by promoting bio-energy production and mineral recovery [59]. In China, the circular economy has been promoted. It modernizes and improves the efficiency of MSW treatment technology, including agro-wasted biomass, such as PBB [134].
Globally, energy dependence has risen due to population growth, transportation, and industrialization. However, numerous studies have examined and proposed some sustainable and renewable sources of bioenergy through diverse biomass treatments with AD, pyrolysis, incineration, HTL, HTC, and HTG [119]. Whenever a biomass undergoes several treatment stages, such as pretreatment, hydrolysis, and sugar conversion into bioethanol, it is referred to as the bio-fermentation process [135]. According to Gunes et al. [136], recently, fermentation is considered a merely renewable technology to produce bioethanol, which can be used instantly without any modifications. During fermentation for bioethanol production, the exhaust gas (CO2) is used by plants from the atmosphere for development. Bioethanol utilization does not contribute to global climate change during production, meaning no GHG emissions during its combustion. Highly fermented biomass is organic material that constitutes starch or carbohydrates. Bioethanol processing at an industrial scale demands a sizeable agricultural area for adequate biomass feedstock utilization. As a catalytic medium in the process, yeast cells can adsorb diverse sugar substrates. It is used to produce bio-ethanol because PABs are high in cellulose. The fermentation process can produce up to 80% ethanol [137]. Before the saccharification process, pretreatment is required to extract lignin so as to offer optimal biomass conversion to bioenergy because it is difficult to biodegrade and can inhibit the process. The hydrolysis of cellulose and hemicellulose to monomers such as sugars and other valuable chemical products does occur. Therefore, LCB, from PBB, comes as a solution for bioethanol production owing to its affordability and availability in large amounts, mostly in tropical countries.
LCBs are a natural source of carbon and exist abundantly, and they are made of different concentrations of lignin, hemicellulose, and cellulose [138]. According to Bernardi et al. [139], LCB is a polysaccharide biomass material that can be converted into simple sugar and bioethanol using bio-fermentation techniques. Ramawat et al. [140] examined that hemicellulose and cellulose have H2 and covalent bonds as lignin, and are present mainly in LCB at approximately 70%. According to some studies, cellulose is the backbone of LCB and the most widely used polymer on the planet, with 1.5 × 1012 tonnes produced annually [141]. Due to the recalcitrant nature of LCB, pretreatment is needed by different methods. The LCB pretreatment methods are mechanical, biological (laccases enzymes, peroxidase, and fungi), physiochemical (hydrothermal (HT) and steam explosion), and chemical (oxidizing agents, bases, and acids) to enhance the second-generation bioethanol production yield [142]. The first-generation bioethanol, generated via the conversion of amylaceous and monosaccharide plants, had critical challenges and competed with global food materials. Therefore, second-generation bioethanol has excellent potential and is a promising renewable source of biofuel as it only uses other parts of plants without any direct food competitiveness.
The main constituent of LCB is cellulose, defined as a homopolymer with linear glucose. Cellulose is composed of 95% glucose and other minor sugars such as mannose, galactose, and xylose, additionally, β-1, 4-osidic bonded 2-glucose, which results in the formation of 3-dimensional chains of glucose bonded by a H2 bond [143]. Fig. 6 shows the schematic diagram for bioethanol production from LCB. LCB can be pre-treated, and some constituents, including cellulose, hemicellulose, lignin, and starch, can be extracted. The supersaturated cellulose in LCB can be hydrolyzed and then fermented to produce bioethanol. The hydrolysis process decomposes polymer molecules of hemicellulose and cellulose into simple sugars. Cellulose’s microfibers are crystalline, making cellulose resistant to the hydrolytic enzymes [144].
Figure 6: Bio-fermentation schematic of LCB for bioethanol production
Diverse hydrolysis parameters between hemicellulose and cellulose exist, the use of a catalyst (e.g., enzymes or acids) is needed for cellulose hydrolysis. Several studies proposed diluting sulfuric acid (H2SO4) at a residence time of 180 sec and a temperature range of 180°C–240oC [145]. Enzyme applications (β-glucosidase, endoglucanase, and cellobiohydrolases) completely decompose cellulose and hemicellulose into glucose without generating inhibitors [146]. Hydrolysis and fermentation can be operated in two combined or separate processes. The separate process is commonly known as separate hydrolysis and fermentation (SHF), and it has potential because both processes (hydrolysis and fermentation) are performed at their peak levels [147]. The cellulose hydrolysis was recommended to be processed at an optimal temperature of between 45°C to 50oC, while bio-fermentation was operated at a temperature of between 30°C–37°C to produce bioethanol optimally. However, this process has challenges, such as forming inhibitors during the process. Geberekidan et al. [148] showed that, due to the high glucose production level, there was inhibition between cellulase and β-glucosidase.
In addition, combining two processes in a single reactor, this method is usually called simultaneous saccharification and fermentation (SSF), where the main problem with this method is partial cellulose hydrolysis. At the same time, the operation is not performed at the optimal hydrolysis temperature to avoid the denaturation of enzymes. That aspect can lead to a low level of glucose production and result in poor bioethanol production. In addition, Burman et al. [149] performed SHF and SSF methods with diverse substrates. After pre-treating biomass with H2SO4, they discovered that SHF could produce a large amount of bioethanol at a lower capital cost than SSF. Ntaikou et al. [150] also processed both techniques by utilizing domestic food waste with about 50% of carbohydrates. The SHF performs better than SSF with a bioethanol production level of 141.06 ± 6.81 g/kg with a carbohydrate of 0.40 ± 0.03 g ethanol/g as an influent without the amylolytic, cellulolytic, and yeast denaturation enzymes. Operating hydrolysis and bio-fermentation simultaneously has more advantages. For example, it is less expensive, and the inhibition problem is reduced because the glucose produced is immediately fermented into bioethanol.
Globally, approximately 100 million tonnes were produced in 2015, with a value of USD 732.7 million, and this figure is expected to rise to $913.1 million by 2025. Additionally, extracted lignin is used in pharmaceuticals, drug delivery materials, wound dressings, and other industrial operations [151]. PBB is composed of many parts, including pseudostems (a starch-rich part that is sometimes used in medical applications), fruits (a food source), leaves, and terminal inflorescence, in this regard, PAB harvesting generates a large amount of agro-waste. PAB peels, stalks, leaves, pseudostems, bunch-stems, rhizomes, and rotten fruits are categorized as agro-biomass [152]. Hossain et al. [153] estimated that, for each tonne of PAB harvested, 4 tonnes of pseudostem are produced and decomposed in the field without any specific treatment, contributing to ecological degradation. Improper disposal of PBB results in harmful emissions of H2S, CO2, CH4, and toxic heavy metals, which can be extracted for functional application for bioenergy production or other industrial applications. Biomass/PBB constitutes essential raw materials for human and industrial daily needs. According to Joshi et al. [154], annual residues from PAB (notably in India) are around 1.2 × 107 tonnes, producing 1421 MW of power. The management of PBB with two-dimensional treatment routes such as thermochemical and biochemical treatment and the integration of those two distinct techniques to optimize bioenergy production and nutrients recovered is recommended.
5 Conceptual Treatment for Biofuel Production and Nutrients Recovery Approach
Different kinds of literature were studied and reviewed, evaluating different techniques of biomass treatments for energy and mineral generation, such as AD, pyrolysis, HT, and bio-fermentation. For example, Shaharoshaha et al. [155] discovered that using unripe and ripe banana peels under AD in mesophilic conditions yields more CH4 gas than using unripe banana peels, with yields of 1405.31 and 847.57 mL/gVS, respectively. Other techniques conducted were HT (Alimi et al. [156]), pyrolysis, and fermentation [157]. Wang et al. [158] studied sludge co-pretreatment by fermentation and AD. The coupling of pyrolysis and AD can enhance carbon in organic substances, this technique treats recalcitrant wastes and food waste. Zero waste technology was achievable by integrating fermentation and pyrolysis for vegetable peels, fruits, and PBB with the same ratios that offered high production of H2 [159]. Therefore, this subsection’s core aim is to integrate diverse routes for biochemical and thermochemical processes to improve the yield of bioenergy production content from agro-biomass, notably for PBB valorization.
5.1.1 Integration of Anaerobic Digestion with Pyrolysis
AD and pyrolysis both performed admirably in the treatment of a wide range of wastes, including recalcitrant biomass, MSW, polymers, and a variety of other organic and inorganic wastes. The end products of AD are biogas and digestate, while pyrolysis produces biochar, bio-oil, and syngas. In the absence of O2, the AD effectively degrades and stabilizes various types of biomass to generate CH4 and digestate under mesophilic or thermophilic conditions. Several studies have found that adding additives can increase the yield of CH4 gas [160,161]. Three types of pyrolysis are differentiated according to their operating parameters. The process is classified as slow, fast, or ultra-fast pyrolysis [162]. Fig. 7 depicts the integration of AD and pyrolysis in terms of biomass/PBB valorization routes.
Figure 7: Schematic of anaerobic digestion coupled with pyrolysis
Due to the pyrolysis of PBB, biochar and bio-oil produced can be used as additives in the AD process to enhance the production of CH4 gas. High-rich carbon substances such as biochar obtained from pyrolysis of food waste can advance AD performance by adsorbing inhibitors (e.g., NH3, H2S, and CO2). Biochar accelerates direct interspecies electron transfer in the reactor, moderating buffer performance and stabilizing the AD process microbial source [160]. In the AD of organic waste, the performance of two distinct biochars, commercial biochar (CBC) and local biochar (LBC), was investigated. Prior to being oven dried at 105oC, it was rinsed with water to eliminate impurities. It was then sieved to produce 1.5–2 mm particle sizes for the experiment after cooling. Before being used, 0.25 g/d of CBC and LBC that had pH values of 9.01 and 7.85, respectively, were made as biochar additives. The biochars’ peculiar physisorption isotherms are (BET surface area: LBC 360.2 m2/g; CBC 340.1 m2/g; total pore volume: LBC 0.11 cm2/g; average pore diameter: LBC 10.5 nm; CBC 8.72 nm; additional biochar characteristics are described [163]. According to the AD performance results in this study, reactors containing biochar as additives encouraged high CH4 yield and reactor stability within 350 days at a higher OLR of 6.0 gVS/L-d. Furthermore, increased concentrations of the micro-and macronutrient elements in the digestate compared to the control have improved the quality that is beneficial for agriculture. In biochar reactors, methanothrix was discovered to be the most prevalent methanogen. Compared to the Methannosarcina that often rules in an AD system, this may have withstood long-term operations [163]. Different pyro-char surface area components generated at various temperatures were reported by Pecchi et al. [164]. as additives in AD bio-methanation. Only two studies reported values as high as 70 m2g−1for pyrolysis temperatures up to 700°C, and specific surface values were less than 30 m2g−1. The values of surface area larger than 100 m2 g−1 were attained in two separate works with pyrolysis temperatures of about 800°C. Only one publication reported surface values greater than 400 m2g−1 obtained from sugar beet digestate at 600°C.
Furthermore, using bio-oil from pyrolysis as an additive improves AD resistance to the inhibitor, hence the microbial acclimatization and stability to convert more organic matter, influencing CH4 gas production. In addition, Kaithal et al. [165] recommended syngas as a great source of H2. Andreides et al. [166] reported the conversion of CH4 to syngas, where syngas can be used as an additive in the AD process to create and increase the H2 level in the system by reacting with CO2 and CO to produce CH4. AD syngas bio methanation produced 94.7% of CH4. It can be converted and catalyzed with specific catalysts such as zeolites, FexCy, Ru, and Co, which act and promote CO production to lengthen the carbon chain for CH4 [167]. The combination of AD and pyrolysis technologies offers the possibility of significantly increasing the variety of organic feedstocks that can be transformed, in addition to PBB. Sustainable solutions for biosolids from waste water treatment, animal manure, non-recyclable paper and cardboard packaging, and agricultural and forestry wastes are also of great importance. While smooth-running operations and AD facilities involve a lot of effort, pyrolysis is an energy-intensive process that uses both heat and power. In order to assess the viability of merging both processes, coordinated and thorough technological and economic modeling input from engineers and scientists is essential.
5.1.2 Integration of Anaerobic Digestion with Hydrothermal
The treatment of high-moistured biomass to produce hydro-char, hydro-oil, and hydro-gas is referred to as the HT technique. This method can be classified into three categories: HTC, HTL, and HTG, due to its diverse operating conditions and different generated products. Based on Krylova et al. [168], more char can be produced via HTC than torrefaction, which can operate under 180oC [169]. The HTL process is conducted to make hydro-oil, and HTG generates syngas [170]. Yang et al. [171] proposed the modern application of HT technology to valorize biomass/PBB. LCB has gained attention for its availability and is an excellent sustainable source of bioenergy, organic acidic, oligosaccharides, and chemical products. Two principal prebiotic products, xylooligosaccharide and oligosaccharide, are extracted from LCB by microbial enzymes and biocatalysts [172]. Because of the high reliance on energy and the critical need for sustainable bioenergy sources, some researchers conducted studies combining AD with HTC [173], HTL [174], and HTG [164]. Those integration technologies showed outstanding achievement. Fig. 8 demonstrates distinct routes for integrating HT with AD to enhance energy production levels. Therefore, LCB is a solution to this problem, and coupling AD with HT enhances bioenergy generation in quantity and quality and promotes a no-waste system by reducing climate change and the emission of GHGs.
Figure 8: Routes diagram of anaerobic digestion integrated with hydrothermal
Different categories of HT techniques produce various outputs which can be used as additives to AD for performance optimization, which leads to high production by-products. Carbonizing macro-algae, hydrochar was added to the AD for product optimization. Hydrochar has the highest energy, more than the original biomass [173]. Coupling AD and HTC with hydrochar as additives can enhance the yield and quality of produced CH4 gas. Usman et al. [175] reported that utilizing the hydro-oil and hydrochar produced by HTL of sludge as an additive in AD improves CH4 generation. CH4 production increased to 259 mL/g COD compared with control of 202 mL/g COD with granular activated carbon addition. It increased microbial degradation and improved the performance of hydrogenotrophic methanogens and acetoclastic bacteria. Zhou et al. [176] investigated the viability of employing AD to treat aqueous post-hydrothermal liquefaction waste water (PHWW) with the use of activated carbon because the energy efficiency of the HTL process is decreased since the PHWW that is created by the process contains up to 40% of the carbon from the original feedstock. The outcomes show that successful AD occurred at relatively low PHWW concentrations (6.7%), resulting in a biogas production of 0.5 ml/mg CODremoved and a 53% energy recovery efficiency. The AD process was inhibited by PHWW concentrations above 13.3%, as shown by the delayed, sluggish, or nonexistent production of biogas.
Hydro-oil produced from HT can improve and stabilize the AD process for biogas production, though, some studies reported oil inhibition in AD process [176,177]. Hydro-oil has been directly used in AD in some previous studies. Haarlemmer et al. [178] conducted analysis of hydro oil obtained by HTL of beech wood biomass and reported the physical properties of hydro oil obtained at 500oC offered values of 1.1 density Kg m−3, 70 viscosity mpas at 40oC, while the chemical compositions values were 21.7 (±0.5) HHV (MJkg−1), 13 (±1) Residual carbon (%), 89 (±1) TAN (mgKOHpergramoil), 147 (±1) Iodine value, 11 (±1) Water content (%), 40.8 Carbon (%), 6.5 H2 (%), and 52.8 O2 (%). Because of the hydro-high oil’s viscosity and low volatility, chemicals to modify the pH, like sodium hydroxide, were added. This boosted oil yields and decreased viscosity, but did little to further improve the oil’s quality. The study demonstrates how thorough analysis can aid in process parameter optimization with a goal that goes beyond mass or energy yield and supports the use of hydro-oil in AD to increase biofuel production.
It has been reported that only around 44%–61% of the COD was removed and converted to biogas after AD for the hydro-oil obtained from the HTC of mixed-culture waste water algae biomass in the temperature range of 260°C–320°C, because a part of the organics was not bio-degradable or even toxic to the microorganisms. According to Usman et al. [179], the temperature of the HTC had a considerable effect on the CH4 output of hydro-oil in AD. For instance, when the straw biomass HTC was heated to 320°C, the hydro-CH4 oil’s output decreased from 314 mL CH4 per g COD to 217 mL CH4 per g COD. Further analysis showed that the amount of hardly biodegradable organics (such as furans, phenols, etc.) increased and the amount of readily biodegradable organics (such as saccharides) decreased as HTC temperatures increased. HT can generate syngas rich in H2, CO, and CO2 content, and H2 can be promoted and increased using KOH as a catalyst [60]. According to Chen et al. [180], catalytic conversion of syngas can produce more CH4 gas. Integrating AD with HT is an alternative technology to treat biomass/PBB for the generation of bioenergy and resource recovery, such as digestate for soil amendment and energy production.
5.1.3 Integration of Pyrolysis, Fermentation, and Anaerobic Digestion
Triple integration treatment of biomass can promote a zero-waste system due to the recycling of the waste to produce valuable products and equally act as an additive material to the other techniques. It will lead to a circular economy, and the coupling treatment process can solve the weaknesses of each method. Both pyrolysis and AD have recently shown incredible performance in LCB conversion for energy and waste water treatment. Several studies have been conducted to enhance performance and optimize output, some studies integrate those techniques for bioenergy and nutrient recuperation [181]. The pyrolysis product such as biochar can be used as a co-substrate in the AD process to promote the generation of CH4 by utilizing ampelodesmos mauritanicus as biomass [182]. Besides, the fermentation process is a potential alternative method to achieve energy, such as bioethanol, because its use requires low energy to operate, is cost-effective, and environmentally friendly. Zabed et al. [183] evaluated LCB as an excellent feedstock for the fermentation process. Moreover, Chen et al. [184] reported some methods to recycle LCB to produce bioethanol through fermentation, distillation, and hydrolysis of enzymes. Depending on the chemical and biological constituents of LCB, pretreatment through enzymes, chemical and microbiological processes, and subsequent fermentation will produce bioethanol and electricity. Fig. 9 demonstrates the triple integration routes of pyrolysis, AD, and fermentation. Integrating these three treatment techniques can significantly advance and promote the new productive conversion of biomass to biofuel technology.
Figure 9: Diagram of pyrolysis, fermentation and AD viz-viz routes
Pyrolysis can generate useful substrates in the AD and fermentation processes, where different pyrolytic products such as biochar, bio-oil, and syngas serve as additives for both processes. This process promotes the high production of biofuels by mitigating inhibitors, stabilizing the process, improving buffer capacity, and energizing microbes’ organic decomposition capacity. The process offers a source for the high generation of H2 to be catalyzed and increases bioenergy yield. In addition, pyrolytic products like syngas and aqueous (bio-oil) constitute hydroxy acids, soluble catechol, C2–C6 sugar, H2, and oligomers by catalytic conversion produce biofuels, for instance, CH4 and bioethanol, to address environmental problems [185]. Due to its recalcitrant characteristics, pretreatment via different methods and materials is necessary for LCB. The adopted pretreatment techniques are fragmentation, microwave radiation, sonication, spray drying with gamma radiation, pyrolysis, acid hydrolysis, alkaline pretreatment, oxidation and ozonation, treatment with ionic compounds or solvents, steam or CO2 explosion, and bacterial or enzymatic treatment [186].
PBB, after pretreatment, can be pyrolyzed to produce biochar, bio-oil, and syngas or taken directly to the fermentation or anaerobic digester for bioenergy generation. Subsequently, the residues can be pyrolyzed after fermentation and AD to increase resource utilization efficiency. In batch reactors, pyrochar with a high surface area, ash content, and potassium, calcium, and magnesium concentration was investigated for in-situ biogas cleaning and upgrading. The CH4 output, bio-methanation rate constant, maximum CH4 production rate, and average CH4 content in the biogas all rose in comparison to the control digester, with the biogas eventually reaching a CH4 concentration of over 90%. In addition, the digestate modified with pyrochar included more nutrients than the unmodified one, making it even more appropriate for soil applications [164]. These findings imply that the direct interspecies electron transfer between the bacteria in the consortium may be improved by conductive materials, such as pyrochar in AD, thus enhancing the process efficiency for bioenergy production.
Additionally, Doukeh et al. [187] studied the pyrolysis of digestate from AD. The result showed bio-oil supersaturated with branched and linear aliphatic and aromatic hydrocarbon compounds with 2 or 3 methyl-type substituents, phenols, and alcohols. In addition, phenolic compounds (e.g., lignin) were reported as inhibitors to the fermentation and AD of LCB. Chavan et al. [188] developed the extraction of the lignin by the presence of gallic acid to promote hydrolysis of the cellulose and hemicellulose to produce glucose to be fermented. The remaining residues are suitable for pyrolysis to avert fermentation and AD costs. The pyrolysis makes optimum use of the residues, generating more bio-products like bio-oil, biochar, and syngas to be applied in different ways. Both methods can also generate feedstock for pyrolysis in digestate or residue to enhance net energy by increasing carbon ratio and generate biochar applied in diverse fields (e.g., agriculture for advancing soil properties). In an environmental comparison of banana waste valorization strategies under a biorefinery approach. Santiago et al. [31] reported that bioethanol production from banana peels generates a solid waste flow that is managed in an AD plant, obtaining biogas to be converted into energy and digestate, which is considered as a potential biofertilizer. The drying of banana peels to lower their moisture content, heating the inflow stream prior to fermentation, and subsequent distillation in the appropriate columns are the operations that have the largest energy demands. Therefore, in order to improve the environmental profiles of various valorization technologies, special attention should be paid to the use of renewable energy sources as opposed to drawing energy directly from the national grid, optimizing energy requirements by reusing some internal steam, or taking alternative drying methods into consideration.
5.1.4 Hydrothermal and Fermentation Integration
Another promising approach for handling wet biomass is SCWG. This is another HT processing technology. However, an analysis of the SCWG design suggests that the feasibility of the process depends on feed type and concentration. Clogging, plugging, and char formation are major problems in the SCWG of biomass [108]. Different supercritical water (374oC and 22 MPa), subcritical water (100°C–374oC, saturated steam to 22 MPa), and ambient liquid water (25°C–100oC and 0.1 MPa) are the different HT operating temperatures and pressures [189]. Recent advances in combining HT with other biological methods were also investigated [190]. Moreover, organic solvents have been used for lignin dissolution, promoting the enzymatic activities of cellulose. The act of dissolving lignin via numerous solvents via Hansen’s solubility technical constant was reported previously [191]. Furthermore, organic solvents utilized in the HT pretreatment process are categorized as polar protic and polar aprotic, depending on physiochemical characteristics. Fig. 10 shows different scenarios for routes by integrating HT with fermentation. Soliman et al. [192] studied the integration of HT with fermentation by seaweed biomass as a sustainable source for bioethanol production, where HT of macro-algal and fungal-saccharification was suggested to optimize the generation of fermented sugars. The economic and technological utilization of LCB to produce bioethanol was studied [193] via H2SO4 pretreatment and the effect of enzymes in the saccharification process.
Figure 10: Diagram of coupled hydrothermal with bio-fermentation routes
Many studies showed various kinds of products produced from HT due to the different operating parameters. In addition, those outputs such as hydrochar, hydro-oil, and syngas can be used as an additive or catalytically converted to maximize and stabilize the fermentation process, which leads to the high yield of biofuel generation. Hydro-char as an additive can stabilize the fermentation process by increasing microbial activity in the system and promoting resource recovery [194]. The HTG can produce syngas, which is catalyzed to produce bioenergy. Pardo-Planas et al. [195] recommend that the fermentation of syngas can generate a higher bioethanol yield than biochemical treatment techniques. Supposedly, it is operated under medium pressure and temperature with no need for enzymes and costly pretreatment. Furthermore, rich H2 syngas materials can be used directly as additives in the fermentation process [196]. The H2 present in the syngas can react with C and CO, enhancing bioenergy production. In order to produce H2, the economics of employing sewage sludge biomass as a feedstock for SCWG-HTG were examined. If earnings from the disposal of sewage sludge biomass were not taken into account, the cost of producing H2 was around 35.2 € GJ−1, which was much higher than the price of H2 produced through electrolysis (26.82 € GJ−1) [108].
6 Insight and Future Perspectives
Currently, many authors focus on new alternative bio-energy sources that are renewable and eco-friendly to solve severe fuel challenges and lessen the contaminant effects on the ecological system. The LCB contained in PBB, as a new source for bio-fuel production, has gained much potential in promoting sustainable techniques for energy generation. The biochemical conversion of LCB to produce the second generation of bio-ethanol comes as a solution to the high demand for fuels. It reduces GHG emissions, which are considered the leading cause of global warming. Pretreatment of LCB in PBB has to be seriously examined. For example, lignin extraction from PBB can be investigated in the future, as it can lead to bioprocess failure due to its non-degradable properties. The use of chemicals and enzymes in the hydrolysis process to optimize the high yield production of fermented sugar must be investigated.
It was shown that SHF is a promising route for the fermentation process over SSF in bioethanol production, owing to the difference in temperature range during their operation. It is expensive and can lead to the rise of inhibitors during the process. Future studies must advance the SSF process, making it cost-effective and with fewer inhibitors developed. The sugar produced can be fermented directly, promoting bio-ethanol production. SSF methods are compelling and exciting due to their ability to ferment glucose and pentose. Research still has to be conducted to find the micro-organism that can ferment both sugars simultaneously for sustainability and simplification of the process, which allows the utilization of all sugars present in the reactor by unique micro-organisms. The monitoring biosensor also has to be observed to control and harmonize the process so it remains at the optimum level.
Recently, the fermentation of pentose sugar has been studied, but its challenges and optimization technologies remain unsolved. The impact of hydrochar and biochar on the fermentation process must be investigated. The effectiveness of the bio-oil and hydro-oil has to be examined before insertion into the AD of the fermentation process to avert oil toxicity and optimize the process. The integration arrangement of the treatment techniques has to be investigated for optimal bio-energy production and resource recovery.
This review shows the hypothetical routes by integrating distinct treatment directions to optimize biofuel production and associated digestate/residues treated to maximize resource recuperation. Comprehensive and intensive techno-economic designs from scientists and engineers are vital for appraising the practical applications of the proposed integrated technological routes for PBB valorization and biofuel recovery.
PAB generates a large amount of waste during harvesting and industrial processing that is used in various recovery processes, such as biofuels, waste water treatment, organic fertilizers, and the production of bioplastics focused on implementing a circular economy. In this review, the waste-to-energy technologies that are potentially applicable to PBB industrialization were highlighted. Different integration routes of pyrolysis, incineration, AD, fermentation, HTC, HTL, and HTG for the valorization of the PBB were proposed. Generally, the integration of both biochemical and thermo-chemical conversion technologies can positively generate net energy if the processes do not require additional fuel input, heat, or energy. PBB can be on positive net energy balance through direct thermo-chemical conversions when the substrate has had prior drying before thermal degradation since there will be a correlation between moisture content and energy yield. The application of the HTC, HTL, and HTG can offer superior product yield compared to pyrolysis and incineration at the downstream due to the associated challenges of PBB’s high moisture content. PBB valorization with AD and fermentation equally stood out as a feasible waste-to-energy technology at the downstream integrated section since they offer energy in the form of biogas, digestate as a cheap source of nutrient-rich plant biofertilizer, and bioethanol. However, it is clear that these integrated proposed approaches for PBB valorization require pilot-scale investigations and industrial implementation, indicating the necessity for additional studies on larger-scale applications. In order to add value to the PBB in a circular economy through integrated routes highlighted in this review. It is suggested to take into account a comprehensive and intense techno-economic design.
Acknowledgement: Thanks to the help provided by Ndungutse Jean Maurice of the Institute of Environmental Science, Shanxi University, Shanxi, China. The School of Environment and Civil Engineering, Nanchang, Jiangxi, China, and the fundamental technical route offered by Lab 913 in the School of Environment, Tsinghua University, Beijing, China.
Funding Statement: This work was supported by the Start-Up Funding for Research of Nanchang Institute of Science and Technology (NGRCZX-22-03), School of Environment and Civil Engineering, Nanchang, Jiangxi, China.
Conflicts of Interest: The authors declare that they have no conflicts of interest to report regarding the present study.
References
1. Abo, B. O., Gao, M., Wang, Y., Wu, C., Ma, H. et al. (2019). Lignocellulosic biomass for bioethanol: An overview on pretreatment, hydrolysis and fermentation processes. Reviews on Environmental Health, 34(1), 57–68. https://doi.org/10.1515/reveh-2018-0054 [Google Scholar] [PubMed] [CrossRef]
2. Martins, F., Felgueiras, C., Smitkova, M., Caetano, N. (2019). Analysis of fossil fuel energy consumption and environmental impacts in european countries. Energies, 12(6), 1–11. https://doi.org/10.3390/en12060964 [Google Scholar] [CrossRef]
3. González-Montaña, J. R., Alonso-Diez, A. J., Alonsodela-Varga, M. E., Avila-Téllez, S. (2016). Transportation sector energy consumption. Internacional de Ovinocultura, Asociación Mexicana de Especialistas en Ovinocultura (AMTEO), pp. 127–137. Mexico. [Google Scholar]
4. Goldemberg, J. (2008). Ennvironmental and ecological dimensions of biofuels. Proceedings of the Conference on the Ecological Dimensions of Biofuels, vol. 10, pp. 16–18. Washington DC. [Google Scholar]
5. Holmatov, B., Schyns, J. F., Krol, M. S., Gerbens-Leenes, P. W., Hoekstra, A. Y. (2021). Can crop residues provide fuel for future transport? Limited global residue bioethanol potentials and large associated land, water and carbon footprints. Renewable and Sustainable Energy Reviews, 149, 111417. https://doi.org/10.1016/j.rser.2021.111417 [Google Scholar] [CrossRef]
6. Alzate Acevedo, S., Díaz Carrillo, Á. J., Flórez-López, E., Grande-Tovar, C. D. (2021). Recovery of banana waste-loss from production and processing: A contribution to a circular economy. Molecules, 26, 1–30. https://doi.org/10.3390/molecules26175282 [Google Scholar] [PubMed] [CrossRef]
7. Guerrero, A. B., Aguado, P. L., Sánchez, J., Curt, M. D. (2016). GIS-Based assessment of banana residual biomass potential for ethanol production and power generation: A case study. Waste and Biomass Valorization, 7(2), 405–415. https://doi.org/10.1007/s12649-015-9455-3 [Google Scholar] [CrossRef]
8. PFPI (2011). Carbon emissions from burning biomass for energy: Is biomass “Worse than coal”? Yes, if you’re interested in reducing carbon dioxide emissions anytime in the next 40 years. https://doi.org/10.1016/j.jenvman.2021.114389 [Google Scholar] [CrossRef]
9. Kusfanto, H. F., Maggadani, B. P., Suryadi, H. (2017). Fermentation of bioethanol from the biomass hydrolyzate of oil palm empty fruit bunch using selected yeast isolates. International Journal of Applied Pharmaceutics, 9, 49–53. https://doi.org/10.22159/ijap.2017.v9s1.2126 [Google Scholar] [CrossRef]
10. Zentou, H., Abidin, Z. Z., Yunus, R., Biak, D. R. A., Zouanti, M. et al. (2019). Modelling of molasses fermentation for bioethanol production: A comparative investigation of monod and andrews models accuracy assessment. Biomolecules, 9(8), 308. https://doi.org/10.3390/biom9080308 [Google Scholar] [PubMed] [CrossRef]
11. Osemwengie, S. O., Osagie, E. I., Onwukwe, B. (2021). Optimization of bioethanol production from cassava peels. Journal of Applied Sciences and Environmental Management, 24(12), 2077–2083. https://doi.org/10.4314/jasem.v24i12.11 [Google Scholar] [CrossRef]
12. Malik, K., Salama, E. S., El-Dalatony, M. M., Jalalah, M., Harraz, F. A. et al. (2021). Co-fermentation of immobilized yeasts boosted bioethanol production from pretreated cotton stalk lignocellulosic biomass: Long-term investigation. Industrial Crops and Products, 159(10), 113122. https://doi.org/10.1016/j.indcrop.2020.113122 [Google Scholar] [CrossRef]
13. Voora, V., Larrea, C., Bermudez, S. (2020). Global market report: Bananas. Sustainable Commodities Marketplace Series 2019. Winnipeg, Canada. https://www.iisd.org/library/global-market-report-banana [Google Scholar]
14. Hernández-Carmona, F., Morales-Matos, Y., Lambis-Miranda, H., Pasqualino, J. (2017). Starch extraction potential from plantain peel wastes. Journal of Environmental Chemical Engineering, 5(5), 4980–4985. https://doi.org/10.1016/j.jece.2017.09.034 [Google Scholar] [CrossRef]
15. Kabenge, I., Omulo, G., Banadda, N., Seay, J., Zziwa, A. et al. (2018). Characterization of banana peels wastes as potential slow pyrolysis feedstock. Journal of Sustainable Development, 11(2), 14. https://doi.org/10.5539/jsd.v11n2p14 [Google Scholar] [CrossRef]
16. Chang, J. K. W., Duret, X., Berberi, V., Zahedi-Niaki, H., Lavoie, J. M. (2018). Two-step thermochemical cellulose hydrolysis with partial neutralization for glucose production. Frontiers in Chemistry, 6(117), 1–11. https://doi.org/10.3389/fchem.2018.00117 [Google Scholar] [PubMed] [CrossRef]
17. Rocha, A. D., Soares, J. M. S., Nascimento, F. D. S., Santos, A. S., Amorim, V. B. et al. (2021). Improvements in the resistance of the banana species to fusarium wilt: A systematic review of methods and perspectives. Journal of Fungi, 7(4), 249. https://doi.org/10.3390/jof7040249 [Google Scholar] [PubMed] [CrossRef]
18. FAO: Banana facts and figures (2020). https://www.fao.org/markets-and-trade/commodities/bananas/en/ [Google Scholar]
19. FAO (2020). The state of food and agriculture. In: Overcoming water challenges in agriculture. Rome-Italy: FAO. https://doi.org/10.4060/cb1447en [Google Scholar] [CrossRef]
20. WorldMapper (2016). Plaintain production. https://worldmapper.org/maps/plantain-production/ [Google Scholar]
21. Naranjo, D. M., Poveda, C. C., Bajana, C. B., Galeas, G. P. (2020). Evaluation of banana waste (Masa Acuminata Cavendish Subgroup) and cocoa (Theobroma cacaothrough the production of compost and biol. 3C Tecnología: Glosas de Innovación Aplicadas a la Pyme, 9(1), 17–28. https://doi.org/10.17993/3ctecno [Google Scholar] [CrossRef]
22. Sharma, R., Oberoi, H. S., Dhillon, G. S. (2016). Fruit and vegetable processing waste. In: Renewable feed stocks for enzyme production, pp. 23–59. USA: Elsevier Inc-Academic Press. https://doi.org/10.1016/B978-0-12-802392-1.00002-2 [Google Scholar] [CrossRef]
23. Gumisiriza, R., Hawumba, J. F., Okure, M., Hensel, O. (2017). Biomass waste-to-energy valorisation technologies: A review case for banana processing in Uganda. Biotechnology for Biofuels and Bioproduct, 10(1), 1–29. https://doi.org/10.1186/s13068-016-0689-5 [Google Scholar] [PubMed] [CrossRef]
24. Mahindrakar, K. V., Rathod, V. K. (2018). Utilization of banana peels for removal of strontium (II) from water. Environmental Technology and Innovation, 11, 371–383. https://doi.org/10.1016/j.eti.2018.06.015 [Google Scholar] [CrossRef]
25. Parra-Ramírez, D., Solarte-Toro, J. C., Cardona-Alzate, C. A. (2020). Techno-economic and environmental analysis of biogas production from plantain pseudostem waste in Colombia. Waste and Biomass Valorization, 11(7), 3161–3171. https://doi.org/10.1007/s12649-019-00643-8 [Google Scholar] [CrossRef]
26. Alonso-Gómez, L. A., Heredia-Olea, E., Serna-Saldivar, S. O., Bello-Pérez, L. A. (2019). Whole unripe plantain (Musa paradisiaca L.) as raw material for bioethanol production. Journal of the Science of Food and Agriculture, 99(13), 5784–5791. https://doi.org/10.1002/jsfa.9847 [Google Scholar] [PubMed] [CrossRef]
27. Farag, M. A., Xiao, J., Abdallah, H. M. (2022). Nutritional value of barley cereal and better opportunities for its processing as a value-added food: A comprehensive review. Critical Reviews in Food Science and Nutrition, 62(4), 1092–1104. https://doi.org/10.1080/10408398.2020.1835817 [Google Scholar] [PubMed] [CrossRef]
28. UNCTAD United Nations Conference on Trade and Development. Trust Fund on Market Information on Agricultural Commodities (2016). Banana An Infocom Commodity Profile UNCTAD Trust Fund on Market Information on Agricultural Commodities, New York and Geneva. [Google Scholar]
29. Gamboa-Herrera, J. A., Ríos-Reyes, C. A., Vargas-Fiallo, L. Y. (2021). Mercury speciation in mine tailings amended with biochar: Effects on mercury bioavailability, methylation potential and mobility. Science of the Total Environment, 760, 143959. https://doi.org/10.1016/j.scitotenv.2020.143959 [Google Scholar] [PubMed] [CrossRef]
30. Ighalo, J. O., Adeniyi, A. G. (2019). Thermodynamic modelling and temperature sensitivity analysis of banana (Musa spp.) waste pyrolysis. SN Applied Sciences, 1(9), 1086. https://doi.org/10.1007/s42452-019-1147-3 [Google Scholar] [CrossRef]
31. Santiago, B., Moreira, M. T., Feijoo, G., González-García, S. (2022). Environmental comparison of banana waste valorisation strategies under a biorefinery approach. Waste Management, 142, 77–87. https://doi.org/10.1016/j.wasman.2022.02.005 [Google Scholar] [PubMed] [CrossRef]
32. Laxshaman Rao, B., Makode, Y., Tiwari, A., Dubey, O., Sharma, S. et al. (2021). Review on properties of banana fiber reinforced polymer composites. Materials Today Proceedings, 47, 2825–2829. https://doi.org/10.1016/j.matpr.2021.03.558 [Google Scholar] [CrossRef]
33. Scott, G. J. (2021). A review of root, tuber and banana crops in developing countries: Past, present and future. International Journal of Food Science and Technology, I56(3), 1093–1114. https://doi.org/10.1111/ijfs.14778 [Google Scholar] [PubMed] [CrossRef]
34. Olumba, C. C., Onunka, C. N. (2020). Banana and plantain in West Africa: Production and marketing. African Journal of Food, Agriculture, Nutrition and Development, 20(2), 15474–15489. https://doi.org/10.18697/AJFAND.90.18365 [Google Scholar] [CrossRef]
35. Ferreira-Villadiego, J., García-Echeverri, J., Vidal, M. V., Pasqualino, J., Meza-Castellar, P. L. et al. (2018). Chemical modification and characterization of starch derived from plantain (Musa paradisiaca) peel waste, as a source of biodegradable material. Chemical Engineering Transactions, 65, 763–768. https://doi.org/10.3303/CET1865128 [Google Scholar] [CrossRef]
36. Agama-Acevedo, E., Sañudo-Barajas, J. A., Vélez De La Rocha, R., González-Aguilar, G. A., Bello-Peréz, L. A. (2016). Potential of plantain peels flour (Musa paradisiaca L.) as a source of dietary fiber and antioxidant compound. Journal of Food, 14(1), 117–123. https://doi.org/10.1080/19476337.2015.1055306 [Google Scholar] [CrossRef]
37. Mankar, A. R., Pandey, A., Modak, A., Pant, K. K. (2021). Pretreatment of lignocellulosic biomass: A review on recent advances. Bioresource Technology, 334, 125235. https://doi.org/10.1016/j.biortech.2021.125235 [Google Scholar] [PubMed] [CrossRef]
38. Basumatary, S., Nath, B., Kalita, P. (2018). Application of agro-waste derived materials as heterogeneous base catalysts for biodiesel synthesis. Journal of Renewable and Sustainable Energy, 10(4), 5043328. https://doi.org/10.1063/1.5043328 [Google Scholar] [CrossRef]
39. Bankovi, I. B., Miladinovi, M. R., Stamenkovi, O. S., Veljkovi, V. B. (2017). Application of nano CaO–based catalysts in biodiesel synthesis. Journal of Renewable and Sustainable Energy, 72, 746–760. https://doi.org/10.1016/j.rser.2017.01.076 [Google Scholar] [CrossRef]
40. Barua, P., Dutta, K., Basumatary, S., Deka, D. C. (2014). Seed oils from non-conventional sources in north-east India: Potential feedstock for production of biodiesel. Natural Product Research, 28(8), 577–580. https://doi.org/10.1080/14786419.2014.881361 [Google Scholar] [PubMed] [CrossRef]
41. Odude, V. O., Adesina, A. J., Oyetunde, O. O., Adeyemi, O. O., Ishola, N. (2017). Application of agricultural waste-based catalysts to transesterification of esterified palm kernel oil into biodiesel: A case of banana fruit peel versus cocoa pod husk. Waste and Biomass Valorization, 10(4), 877–888. https://doi.org/10.1007/s12649-017-0152-2 [Google Scholar] [CrossRef]
42. Betiku, E., Ajala, S. O. (2014). Modeling and optimization of thevetia peruviana (yellow oleander) oil biodiesel synthesis via musa paradisiacal (plantain) peels as heterogeneous base catalyst: A case of artificial neural network vs. response surface methodology. Industrial Crops Production, 53, 314–322. https://doi.org/10.1016/j.indcrop.2013.12.046 [Google Scholar] [CrossRef]
43. Laskar, I. B., Deshmukhya, T., Biswas, A., Paul, B., Changmai, B. et al. (2022). Utilization of biowaste-derived catalysts for biodiesel production: Process optimization using response surface methodology and particle swarm optimization method. Energy Advances, 1(5), 287–302. https://doi.org/10.1039/d2ya00011c [Google Scholar] [CrossRef]
44. Betiku, E., Akintunde, A. M., Ojumu, T. V. (2016). Banana peels as a biobase catalyst for fatty acid methyl esters production using napoleon’s plume (Bauhinia monandra) seed oil: A process parameters optimization study. Energy, 103, 797–806. https://doi.org/10.1016/j.energy.2016.02.138 [Google Scholar] [CrossRef]
45. Sarma, A., Kumar, P., Pratap, A., Chouhan, S., Mohammad, A. (2014). Preparation and characterization of Musa balbisiana colla underground stem nano-material for biodiesel production under elevated conditions. Catalysis Letters, 144(7), 1344. https://doi.org/10.1007/s10562-014-1206-8 [Google Scholar] [CrossRef]
46. Deka, D. C., Basumatary, S. (2011). High quality biodiesel from yellow oleander (Thevetia peruviana) seed oil. Biomass and Bioenergy, 35(5), 1797–1803. https://doi.org/10.1016/j.biombioe.2011.01.007 [Google Scholar] [CrossRef]
47. Gohain, M., Devi, A., Deka, D. (2017). Musa balbisiana colla peel as highly effective renewable heterogeneous base catalyst for biodiesel production. Industrial Crops Production, 109, 8–18. https://doi.org/10.1016/j.indcrop.2017.08.006 [Google Scholar] [CrossRef]
48. Varma, V., Bebber, D. P. (2019). Climate change impacts on banana yields around the world. Nature Climate Change, 9(10), 752–757. https://doi.org/10.1038/s41558-019-0559-9 [Google Scholar] [PubMed] [CrossRef]
49. Bhuiyan, F. R., Campos, N. A., Swennen, R., Carpentier, S. (2020). Characterizing fruit ripening in plantain and cavendish bananas: A proteomics approach. Journal of Proteomics, 214, 103632. https://doi.org/10.1016/j.jprot.2019.103632 [Google Scholar] [PubMed] [CrossRef]
50. OLUTOMILOLA, E. O. (2021). A review of raw plantain size reduction. Scientific African, 12, e00773. https://doi.org/10.1016/j.sciaf.2021.e00773 [Google Scholar] [CrossRef]
51. Diarra, S. S. (2018). Peel meals as feed ingredients in poultry diets: Chemical composition, dietary recommendations and prospects. Journal of Animal Physiology and Animal Nutrition, 102(5), 1284–1295. https://doi.org/10.1111/jpn.12954 [Google Scholar] [PubMed] [CrossRef]
52. Agubosi, O. C. P., Oluwafemi, R. A., Ibrahim, T. U. (2019). Performance of broiler chickens fed graded levels of ripe plantain peel meal (RPPM) as replacement for maize. Journal of Agricultural Science and Practice, 4(1), 1–3. https://doi.org/10.31248/jasp2018.117 [Google Scholar] [CrossRef]
53. Ji, T., Li, X., Meng, G., Gu, Y., Zhang, Q. et al. (2020). The association between banana consumption and the depressive symptoms in Chinese general adult population: A cross-sectional study. Journal of Affective Disorders, 264, 1–6. https://doi.org/10.1016/j.jad.2019.12.008 [Google Scholar] [PubMed] [CrossRef]
54. Oyeyinka, B. O., Afolayan, A. J. (2019). Comparative evaluation of the nutritive, mineral, and antinutritive composition of musa sinensis l. (banana) and musa paradisiaca l. (plantain) fruit compartments. Plants (Basel), 8(12), 598. https://doi.org/10.3390/plants8120598 [Google Scholar] [PubMed] [CrossRef]
55. Bediako, J. K., Choi, J. W., Song, M. H., Zhao, Y., Lin, S. et al. (2020). Recovery of gold via adsorption-incineration techniques using banana peel and its derivatives: Selectivity and mechanisms. Waste Management, 113, 225–235. https://doi.org/10.1016/j.wasman.2020.05.053 [Google Scholar] [PubMed] [CrossRef]
56. Okorie, D. O., Eleazu, C. O., Nwosu, P. (2015). Composition of plantain (Musa paradisiaca) and banana (Musa paradisiaca) peels. Journal of Nutrition & Food Sciences, 5(3), 370. https://doi.org/10.4172/2155-9600.1000370 [Google Scholar] [CrossRef]
57. Efeovbokhan, V. E., Akinneye, D., Ayeni, A. O., Omoleye, J. A., Bolade, O. et al. (2020). Experimental dataset investigating the effect of temperature in the presence or absence of catalysts on the pyrolysis of plantain and yam peels for bio-oil production. Data in Brief, 31, 105804. https://doi.org/10.1016/j.dib.2020.105804 [Google Scholar] [PubMed] [CrossRef]
58. Yang, L., Lu, C., Gao, Y., Lin, Y., Xu, J. et al. (2021). Hydrogen-rich gas production from the gasification of biomass and hydrothermal carbonization (HTC) aqueous phase. Biomass Conversion and Biorefinery. https://doi.org/10.1007/s13399-020-01197-9 [Google Scholar] [CrossRef]
59. Obiageli, O. A., Izundu, I. A., Adachukwu Pauline, I., Geraldine Ukamaka, O. (2016). Proximate compositions of fruits of three musa species at three stages of development. IOSR Journal of Dental and Medical Sciences, 15(6), 107–117. https://doi.org/10.9790/3008 [Google Scholar] [CrossRef]
60. Okolie, J. A., Nanda, S., Dalai, A. K., Kozinski, J. A. (2020). Hydrothermal gasification of soybean straw and flax straw for hydrogen-rich syngas production: Experimental and thermodynamic modeling. Energy Conversion and Management, 208, 112545. https://doi.org/10.1016/j.enconman.2020.112545 [Google Scholar] [CrossRef]
61. Fózer, D., Tóth, A. J., Varbanov, P. S., Klemeš, J. J., Mizsey, P. (2021). Sustainability assessment of biomethanol production via hydrothermal gasification supported by artificial neural network. Journal of Cleaner Production, 318, 128606. https://doi.org/10.1016/j.jclepro.2021.128606 [Google Scholar] [CrossRef]
62. Smith, M., Aber, J. (2014). Heat recovery from compost. Biocycle, 55(2), 26–29. [Google Scholar]
63. Sandoval-Cobo, J. J., Casallas-Ojeda, M. R., Carabalí-Orejuela, L., Muñoz-Chávez, A., Caicedo-Concha, D. M. et al. (2020). Methane potential and degradation kinetics of fresh and excavated municipal solid waste from a tropical landfill in Colombia. Sustainable Environment Research, 30(1), 7. https://doi.org/10.1186/s42834-020-00048-6 [Google Scholar] [CrossRef]
64. Bhushan, S., Rana, M. S., Nandan, N., Prajapati, S. K. (2019). Bioresource technology reports energy harnessing from banana plant wastes: A review. Bioresource Technology Reports, 7, 100212. https://doi.org/10.1016/j.biteb.2019.100212 [Google Scholar] [CrossRef]
65. Pisutpaisal, N., Boonyawanich, S., Saowaluck, H. (2014). Feasibility of biomethane production from banana peel. Energy Procedia, 50, 782–788. https://doi.org/10.1016/j.egypro.2014.06.096 [Google Scholar] [CrossRef]
66. Itelima, J., Onwuliri, F., Onwuliri, E., Onyimba, I., Oforji, S. (2013). Bio-ethanol production from banana, plantain and pineapple peels by simultaneous saccharification and fermentation process. International Journal of Environmental Science and Development, 4(2), 213–216. https://doi.org/10.7763/ijesd.2013.v4.337 [Google Scholar] [CrossRef]
67. Pulyaeva, V. N., Kharitonova, N. A., Kharitonova, E. N. (2020). Advantages and disadvantages of the production and using of liquid biofuels. IOP Conference Series: Materials Science and Engineering, 976(1), 012031. https://doi.org/10.1088/1757-899X/976/1/012031 [Google Scholar] [CrossRef]
68. Fatimah, Napitupulu, M. (2021). Lead (II) adsorption by biochar prepared from tanduk banana peels (Musa X Paradisiaca). Journal of Physics: Conference Series, 1763(1), 012024. https://doi.org/10.1088/1742-6596/1763/1/012024 [Google Scholar] [CrossRef]
69. Maurice, N. J., Shahin, A., Xiong, X., Giwa, S. (2021). Preliminary studies on the performance of vacuum black water with biochar additives in anaerobic digestion process. International Journal of Technical & Scientific Research Engineering, 4(1), 1–7. [Google Scholar]
70. Vishnu, D., Dhandapani, B., Vaishnavi, G., Preethi, V. (2022). Synthesis of tri-metallic surface engineered nanobiochar from cynodon dactylon residues in a single step-batch and column studies for the removal of copper and lead ions. Chemosphere, 286, 131572. https://doi.org/10.1016/j.chemosphere.2021.131572 [Google Scholar] [PubMed] [CrossRef]
71. Yogalakshmi, K. N., Poornima, D. T., Sivashanmugam, P., Kavitha, S., Yukesh, R. et al. (2022). Lignocellulosic biomass-based pyrolysis: A comprehensive review. Chemosphere, 286, 131824. https://doi.org/10.1016/j.chemosphere.2021.131824 [Google Scholar] [PubMed] [CrossRef]
72. Guizani, C., Jeguirim, M., Valin, S., Limousy, L. (2017). Biomass chars: The effects of pyrolysis conditions on their morphology, structure. Chemical Properties and Reactivity. Energies, 10(6), 796. https://doi.org/10.3390/en10060796 [Google Scholar] [CrossRef]
73. Te, W. Z., Muhanin, K. N. M., Chu, Y. M., Selvarajoo, A., Singh, A. et al. (2021). Optimization of pyrolysis parameters for production of biochar from banana peels: Evaluation of biochar application on the growth of ipomoea aquatica. Frontiers in Energy Research, 8, 1–16. https://doi.org/10.3389/fenrg.2020.637846 [Google Scholar] [CrossRef]
74. Zuur, K., Bosch, P., Wijaya, J. B. W. (2018). Syngas to bio-ethanol fermentation. https://fse.studenttheses.ub.rug.nl/17562/1/BA_2_Report_Final_03072018.pdf [Google Scholar]
75. He, J., Strezov, V., Zhou, X., Kumar, R., Weldekidan, H. et al. (2021). Effects of co-pyrolysis of heavy metal contaminated biomass with magnesium carbonate on heavy metal deportment and pyrolytic product properties. Fuel, 294, 120545. https://doi.org/10.1016/j.fuel.2021.120545 [Google Scholar] [CrossRef]
76. Safarian, S., Unnthorsson, R., Richter, C. (2021). Bioethanol production via herbaceous and agricultural biomass gasification integrated with syngas fermentation. Fermentation, 7(3), 139. https://doi.org/10.3390/fermentation7030139 [Google Scholar] [CrossRef]
77. Han, X., Guo, Y., Liu, X., Xia, Q., Wang, Y. (2019). Catalytic conversion of lignocellulosic biomass into hydrocarbons: A mini review. Catalysis Today, 319, 2–13. https://doi.org/10.1016/j.cattod.2018.05.013 [Google Scholar] [CrossRef]
78. Nanda, S., Berruti, F. (2021). A technical review of bioenergy and resource recovery from municipal solid waste. Journal of Hazardous Materials, 403, 123970. https://doi.org/10.1016/j.jhazmat.2020.123970 [Google Scholar] [PubMed] [CrossRef]
79. Cudjoe, D., Acquah, P. M. (2021). Environmental impact analysis of municipal solid waste incineration in african countries. Chemosphere, 265, 129186. https://doi.org/10.1016/j.chemosphere.2020.129186 [Google Scholar] [PubMed] [CrossRef]
80. Kumar, A., Agrawal, A. (2020). Recent trends in solid waste management status, challenges, and potential for the future Indian cities–A review. Current Research in Environmental Sustainability, 2, 100011. https://doi.org/10.1016/j.crsust.2020.100011 [Google Scholar] [CrossRef]
81. van Drooge, B. L., Abalos, M., Abad, E., Adrados, M. A., Gomez, A. et al. (2021). Qualitative and quantitative changes in traffic and waste incineration PCDD/Fs in urban air and soils under different seasonal conditions (Metropolitan area of barcelona). Science of the Total Environment, 753, 142149. https://doi.org/10.1016/j.scitotenv.2020.142149 [Google Scholar] [PubMed] [CrossRef]
82. Babalola, M. A. (2020). A Benefit-cost analysis of food and biodegradable waste treatment alternatives: The case of Oita City, Japan. Sustainability, 12(5), 1916. https://doi.org/10.3390/su12051916 [Google Scholar] [CrossRef]
83. Wang, L., Zhang, Y., Chen, L., Guo, B., Tan, Y. et al. (2022). Designing novel magnesium oxysulfate cement for stabilization/solidification of municipal solid waste incineration fly ash. Journal of Hazardous Materials, 423, 127025. https://doi.org/10.1016/j.jhazmat.2021.127025 [Google Scholar] [PubMed] [CrossRef]
84. Cui, C., Liu, Y., Xia, B., Jiang, X., Skitmore, M. (2020). Overview of public-private partnerships in the waste-to-energy incineration industry in China: Status, opportunities, and challenges. Energy Strategy Review, 32, 100584. https://doi.org/10.1016/j.esr.2020.100584 [Google Scholar] [CrossRef]
85. Kleib, J., Aouad, G., Abriak, N. E., Benzerzour, M. (2021). Production of portland cement clinker from French municipal solid waste incineration bottom Ash. Case Studies in Construction Materials, 15, e00629. https://doi.org/10.1016/j.cscm.2021.e00629 [Google Scholar] [CrossRef]
86. Wierzbowska, J., Sienkiewicz, S., Zarczyński, P., Krzebietke, S. (2020). Environmental application of ash from incinerated biomass. Agronomy, 10(4), 482. https://doi.org/10.3390/agronomy10040482 [Google Scholar] [CrossRef]
87. Nakatsuka, N., Kishita, Y., Kurafuchi, T., Akamatsu, F. (2020). Integrating wastewater treatment and incineration plants for energy-efficient urban biomass utilization: A life cycle analysis. Journal of Cleaner Production, 243, 118448. https://doi.org/10.1016/j.jclepro.2019.118448 [Google Scholar] [CrossRef]
88. Czerwińska, K., Śliz, M., Wilk, M. (2022). Hydrothermal carbonization process: Fundamentals, main parameter characteristics and possible applications including an effective method of SARS-CoV-2 mitigation in sewage sludge. A review. Renewable and Sustainable Energy Reviews, 154, 111873. https://doi.org/10.1016/j.rser.2021.111873 [Google Scholar] [CrossRef]
89. Heidari, M., Dutta, A., Acharya, B., Mahmud, S. (2019). A review of the current knowledge and challenges of hydrothermal carbonization for biomass conversion. Journal of the Energy Institute, 92(6), 1779–1799. https://doi.org/10.1016/j.joei.2018.12.003 [Google Scholar] [CrossRef]
90. Nizamuddin, S., Baloch, H. A., Griffin, G. J., Mubarak, N. M., Bhutto, A. W. et al. (2017). An overview of effect of process parameters on hydrothermal carbonization of biomass. Renewable and Sustainable Energy Reviews, 73, 1289–1299. https://doi.org/10.1016/j.rser.2016.12.122 [Google Scholar] [CrossRef]
91. Wilk, M., Magdziarz, A., Jayaraman, K., Szymańska-Chargot, M., Gökalp, I. (2019). Hydrothermal carbonization characteristics of sewage sludge and lignocellulosic biomass. A comparative study. Biomass and Bioenergy, 120, 166–175. https://doi.org/10.1016/j.biombioe.2018.11.016 [Google Scholar] [CrossRef]
92. Ahmed, M., Sartori, F., Merzari, F., Fiori, L., Elagroudy, S. et al. (2021). Anaerobic degradation of digestate based hydrothermal carbonization products in a continuous hybrid fixed bed anaerobic filter. Bioresource Technology, 330, 124971. https://doi.org/10.1016/j.biortech.2021.124971 [Google Scholar] [PubMed] [CrossRef]
93. Cárdenas-Aguiar, E., Gascó, G., Paz-Ferreiro, J., Méndez, A. (2019). Thermogravimetric analysis and carbon stability of chars produced from slow pyrolysis and hydrothermal carbonization of manure waste. Journal of Analytical and Applied Pyrolysis, 140, 434–443. https://doi.org/10.1016/j.jaap.2019.04.026 [Google Scholar] [CrossRef]
94. Ischia, G., Fiori, L. (2021). Hydrothermal carbonization of organic waste and biomass: A review on process, reactor, and plant modeling. Waste and Biomass Valorization, 12(6), 2797–2824. https://doi.org/10.1007/s12649-020-01255-3 [Google Scholar] [CrossRef]
95. Taufer, N. L., Benedetti, V., Pecchi, M., Matsumura, Y., Baratieri, M. (2021). Coupling hydrothermal carbonization of digestate and supercritical water gasification of liquid products. Renewable Energy, 173, 934–941. https://doi.org/10.1016/j.renene.2021.04.058 [Google Scholar] [CrossRef]
96. Mendoza Martinez, C. L., Sermyagina, E., Saari, J., Silva de Jesus, M., Cardoso, M. et al. (2021). Hydrothermal carbonization of lignocellulosic agro-forest based biomass residues. Biomass and Bioenergy, 147, 106004. https://doi.org/10.1016/j.biombioe.2021.106004 [Google Scholar] [CrossRef]
97. Lu, J., Watson, J., Liu, Z., Wu, Y. (2022). Elemental migration and transformation during hydrothermal liquefaction of biomass. Journal of Hazardous Materials, 423, 126961. https://doi.org/10.1016/j.jhazmat.2021.126961 [Google Scholar] [PubMed] [CrossRef]
98. Dimitriadis, A., Bezergianni, S. (2017). Hydrothermal liquefaction of various biomass and waste feedstocks for biocrude production: A state of the art review. Renewable and Sustainable Energy Reviews, 68, 113–125. https://doi.org/10.1016/j.rser.2016.09.120 [Google Scholar] [CrossRef]
99. Djandja, O. S., Wang, Z., Chen, L., Qin, L., Wang, F. et al. (2020). Progress in hydrothermal liquefaction of algal biomass and hydrothermal upgrading of the subsequent crude bio-oil: A mini review. Energy and Fuels, 34(10), 11723–11751. https://doi.org/10.1021/acs.energyfuels.0c01973 [Google Scholar] [CrossRef]
100. Chen, W. H., Lin, Y. Y., Liu, H. C., Baroutian, S. (2020). Optimization of food waste hydrothermal liquefaction by a two-step process in association with a double analysis. Energy, 199, 117438. https://doi.org/10.1016/j.energy.2020.117438 [Google Scholar] [CrossRef]
101. Yuzer, B., Selcuk, H., Chehade, G., Demir, M. E., Dincer, I. (2020). Evaluation of hydrogen production via electrolysis with ion exchange membranes. Energy, 190, 116420. https://doi.org/10.1016/j.energy.2019.116420 [Google Scholar] [CrossRef]
102. Giwa, A. S., Chang, F., Xu, H., Zhang, X., Huang, B. et al. (2019). Pyrolysis of difficult biodegradable fractions and the real syngas bio-methanation performance. Journal of Cleaner Production, 233, 711–719. https://doi.org/10.1016/j.jclepro.2019.06.145 [Google Scholar] [CrossRef]
103. Wang, Z., Li, L., Zhang, G. (2018). Life cycle greenhouse gas assessment of hydrogen production via chemical looping combustion thermally coupled steam reforming. Journal of Cleaner Production, 179, 335–346. https://doi.org/10.1016/j.jclepro.2018.01.063 [Google Scholar] [CrossRef]
104. Li, Y., Liu, W., Zhang, Z., Du, X., Yu, L. et al. (2019). A self-powered electrolytic process for glucose to hydrogen conversion. Communications Chemistry, 2(1), 1–9. https://doi.org/10.1038/s42004-019-0169-5 [Google Scholar] [CrossRef]
105. Okolie, J. A., Epelle, E. I., Nanda, S., Castello, D., Dalai, A. K. et al. (2021). Modeling and process optimization of hydrothermal gasification for hydrogen production: A comprehensive review. Journal of Supercritical Fluids, 173, 105199. https://doi.org/10.1016/j.supflu.2021.105199 [Google Scholar] [CrossRef]
106. Lee, C. S., Conradie, A. V., Lester, E. (2021). Review of supercritical water gasification with lignocellulosic real biomass as the feedstocks: Process parameters, biomass composition, catalyst development, reactor design and its challenges. Chemical Engineering Journal, 415, 128837. https://doi.org/10.1016/j.cej.2021.128837 [Google Scholar] [CrossRef]
107. Zuorro, A., García-Martínez, J. B., Barajas-Solano, A. F. (2021). The application of catalytic processes on the production of algae-based biofuels: A review. Catalysts, 11(1), 1–25. https://doi.org/10.3390/catal11010022 [Google Scholar] [CrossRef]
108. Kumar, M., Olajire Oyedun, A., Kumar, A. (2018). A review on the current status of various hydrothermal technologies on biomass feedstock. Renewable and Sustainable Energy Reviews, 81, 1742–1770. https://doi.org/10.1016/j.rser.2017.05.270 [Google Scholar] [CrossRef]
109. Chen, G., Wang, X., Li, J., Yan, B., Wang, Y. et al. (2019). Environmental, energy, and economic analysis of integrated treatment of municipal solid waste and sewage sludge: A case study in China. Science of the Total Environment, 647, 1433–1443. https://doi.org/10.1016/j.scitotenv.2018.08.104 [Google Scholar] [PubMed] [CrossRef]
110. Villar, I., Alves, D., Garrido, J., Mato, S. (2016). Evolution of microbial dynamics during the maturation phase of the composting of different types of waste. Waste Management, 54, 83–92. https://doi.org/10.1016/j.wasman.2016.05.011.0 [Google Scholar] [CrossRef]
111. Cáceres, R., Malińska, K., Marfà, O. (2018). Nitrification within composting: A review. Waste Management, 72, 119–137. https://doi.org/10.1016/j.wasman.2017.10.049 [Google Scholar] [PubMed] [CrossRef]
112. Al-Rumaihi, A., McKay, G., Mackey, H. R., Al-Ansari, T. (2020). Environmental impact assessment of food waste management using two composting techniques. Sustainability, 12(4), 1595. https://doi.org/10.3390/su12041595 [Google Scholar] [CrossRef]
113. Nsimbe, P., Mendoza, H., Wafula, S. T., Ndejjo, R. (2018). Factors associated with composting of solid waste at household level in masaka municipality, Central Uganda. Journal of Environmental and Public Health, 7, 1284234. https://doi.org/10.1155/2018/1284234 [Google Scholar] [PubMed] [CrossRef]
114. Rastogi, M., Nandal, M., Khosla, B. (2020). Microbes as vital additives for solid waste composting. Heliyon, 6(2), e03343. https://doi.org/10.1016/j.heliyon.2020.e03343 [Google Scholar] [PubMed] [CrossRef]
115. Bhave, P. P., Kulkarni, B. N. (2019). Effect of active and passive aeration on composting of household biodegradable wastes: A decentralized approach. International Journal of Recycling of Organic Waste in Agriculture, 8, 335–344. https://doi.org/10.1007/s40093-019-00306-7 [Google Scholar] [CrossRef]
116. Zhang, L., Sun, X. (2016). Improving green waste composting by addition of sugarcane bagasse and exhausted grape marc. Bioresource Technology, 218, 335–343. https://doi.org/10.1016/j.biortech.2016.06.097 [Google Scholar] [PubMed] [CrossRef]
117. Barthod, J., Rumpel, C., Dignac, M. F. (2018). Composting with additives to improve organic amendments. A Review. Agronomy for Sustainable Development, 38(7), 17. https://doi.org/10.1007/s13593-018-0491-9 [Google Scholar] [CrossRef]
118. Laiq Ur Rehman, M., Iqbal, A., Chang, C. C., Li, W., Ju, M. (2019). Anaerobic digestion. Water Environment Research, 91, 1253–1271. https://doi.org/10.1002/wer.1219 [Google Scholar] [PubMed] [CrossRef]
119. Giwa, A. S., Memon, A. G., Vakili, M., Ge, Y., Wang, B. (2022). The resource recovery potential of blackwater and foodwaste: Anaerobic co-digestion in serial semi-continuous stirred tank reactors. International Journal of Environmental Science and Technolology, 19(6), 5401–5408. https://doi.org/10.1007/s13762-021-03414-y [Google Scholar] [CrossRef]
120. Giwa, A. S., Zhang, X., Memon, A. G., Ali, N. (2021). Co-digestion of household black water with kitchen waste for a sustainable decentralized waste management: Biochemical methane potential and mixing ratios effects. Environmental Engineering Science, 38(9), 877–885 https://doi.org/10.1089/ees.2020.0276 [Google Scholar] [CrossRef]
121. Sheng, K., Chen, X., Pan, J., Kloss, R., Wei, Y. et al. (2013). Effect of ammonia and nitrate on biogas production from food waste via anaerobic digestion. Biosystems Engineering, 116(2), 205–212. https://doi.org/10.1016/j.biosystemseng.2013.08.005 [Google Scholar] [CrossRef]
122. Mutegoa, E., Hilonga, A., Njau, K. N. (2020). Approaches to the mitigation of ammonia inhibition during anaerobic digestion–A review. Water Practice and Technology, 15(3), 551–570. https://doi.org/10.2166/wpt.2020.047 [Google Scholar] [CrossRef]
123. Deng, Z., van Linden, N., Guillen, E., Spanjers, H., van Lier, J. B. (2021). Recovery and applications of ammoniacal nitrogen from nitrogen-loaded residual streams: A review. Journal of Environmental Management, 295, 113096. https://doi.org/10.1016/j.jenvman.2021.113096 [Google Scholar] [PubMed] [CrossRef]
124. Tambuwal, A. D., Okoh, E. V. C., Ogbiko, C. (2020). Biogas production from banana and plantain peels blended with Cow dung in an in vitro biodigester system. Lapai Journal of Applied and Natural Science, 4, 160–164. [Google Scholar]
125. Lobato-Peralta, D. R., Duque-Brito, E., Villafán-Vidales, H. I., Longoria, A., Sebastian, P. J. et al. (2021). A review on trends in lignin extraction and valorization of lignocellulosic biomass for energy applications. Journal of Cleaner Production, 293, 126123. https://doi.org/10.1016/j.jclepro.2021.126123 [Google Scholar] [CrossRef]
126. Paul, S., Dutta, A. (2018). Challenges and opportunities of lignocellulosic biomass for anaerobic digestion. Resource Conservation and Recycling, 130, 164–174. https://doi.org/10.1016/j.resconrec.2017.12.005 [Google Scholar] [CrossRef]
127. Berhe, T. G., Tesfahuney, R. G., Desta, G. A., Mekonnen, L. S. (2017). Biogas plant distribution for rural household sustainable energy supply in Africa. Energy and Policy Research, 4(1), 10–20. https://doi.org/10.1080/23815639.2017.1280432 [Google Scholar] [CrossRef]
128. Subedi, P. S. (2013). Medium sized biogas plants: Pakistani experiences and regional prospects. Winrock International Methane EXPO 2013. www.winrock.org [Google Scholar]
129. Divyabharathi, R., Angeeswaran, R., Jagadeeshkumar, K., Pugalendhi, S. (2017). Characterization and batch anaerobic digestion study of banana wastes. International Journal of Current Microbiology and Applied Sciences, 6(7), 2307–2315. https://doi.org/10.20546/ijcmas.2017.607.331 [Google Scholar] [CrossRef]
130. Emma Ransom-Jones, A. J., McCarthy, S. H., James, D., McDonalda, J. E. (2017). Lignocellulose-degrading microbial communities in landfill sites represent a repository of unexplored biomass degrading diversity. Applied and Environmental Science, 2(4), 1–13. [Google Scholar]
131. Nothling, M. D., Xiao, Z., Bhaskaran, A., Blyth, M. T., Bennett, C. W. et al. (2019). Synthetic catalysts inspired by hydrolytic enzymes. ACS Catalysis, 9(1), 168–187. https://doi.org/10.1021/acscatal.8b03326 [Google Scholar] [CrossRef]
132. Lee, U., Han, J., Wang, M. (2017). Evaluation of landfill gas emissions from municipal solid waste landfills for the life-cycle analysis of waste-to-energy pathways. Journal of Cleaner Production, 166, 335–342. https://doi.org/10.1016/j.jclepro.2017.08.016 [Google Scholar] [CrossRef]
133. Yadav, V., Sherly, M. A., Ranjan, P., Tinoco, R. O., Boldrin, A. et al. (2020). Framework for quantifying environmental losses of plastics from landfills. Resource Conservation and Recycling, 161, 104914. https://doi.org/10.1016/j.resconrec.2020.104914 [Google Scholar] [CrossRef]
134. Chen, Z., Chen, S., Liu, C., Nguyen, L. T., Hasan, A. (2020). The effects of circular economy on economic growth: A quasi-natural experiment in China. Journal of Cleaner Production, 271, 122558. https://doi.org/10.1016/j.jclepro.2020.122558 [Google Scholar] [CrossRef]
135. Mora-Villalobos, J. A., Montero-Zamora, J., Barboza, N., Rojas-Garbanzo, C., Usaga, J. et al. (2020). Multi-product lactic acid bacteria fermentations: A review. Fermentation, 6(1), 1–21. https://doi.org/10.3390/fermentation6010023 [Google Scholar] [CrossRef]
136. Gunes, B. (2021). A critical review on biofilm-based reactor systems for enhanced syngas fermentation processes. Renewable and Sustainable Energy Reviews, 143, 110950. https://doi.org/10.1016/j.rser.2021.110950 [Google Scholar] [CrossRef]
137. Lopez-Olmos, C., Guerrero-Ruiz, A., Rodríguez-Ramos, I. (2020). Optimization of Cu-Ni-Mn-catalysts for the conversion of ethanol to butanol. Catalysis Today, 357, 132–142. https://doi.org/10.1016/j.cattod.2019.05.058 [Google Scholar] [CrossRef]
138. Leu, S. Y., Zhu, J. Y. (2013). Substrate-related factors affecting enzymatic saccharification of lignocelluloses: Our recent understanding. Bioenergy Resources, 6(2), 405–415. https://doi.org/10.1007/s12155-012-9276-1 [Google Scholar] [CrossRef]
139. Bernardi, A. V., Gerolamo, L. E., DeGouvêa, P. F., Yonamine, D. K., Pereira, L. M. S. et al. (2021). LPMO AfAA9_B and cellobiohydrolase AfCel6A from A. fumigatus boost enzymatic saccharification activity of cellulase cocktail. International Journal of Molecular Sciences, 22(1), 1–23. https://doi.org/10.3390/ijms22010276 [Google Scholar] [PubMed] [CrossRef]
140. Ramawat, K. G., Mérillon, J. M. (2015). Polysaccharides. In: Bioactivity and biotechnology, pp. 1–2241. Switzerland: Springer Nature. https://doi.org/10.1007/978-3-319-16298-0 [Google Scholar] [CrossRef]
141. Wang, Y., Liu, P., Zhang, G., Yang, Q., Lu, J. et al. (2021). Cascading of engineered bioenergy plants and fungi sustainable for low-cost bioethanol and high-value biomaterials under green-like biomass processing. Renewable and Sustainable Energy Reviews, 137, 110586. https://doi.org/10.1016/j.rser.2020.110586 [Google Scholar] [CrossRef]
142. Li, J., Solhi, L., Goddard-Borger, E. D., Mathieu, Y., Wakarchuk, W. W. et al. (2021). Four cellulose-active lytic polysaccharide monooxygenases from cellulomonas species. Biotechnology for Biofuels, 14(1), 1–19. https://doi.org/10.1186/s13068-020-01860-3 [Google Scholar] [PubMed] [CrossRef]
143. Hussain, M. A., Shad, I., Malik, I., Amjad, F., Kausar, T. et al. (2020). Hydroxypropylcellulose-flurbiprofen conjugates: Design, characterization, anti-inflammatory activity and enhanced bioavailability. Saudi Pharmaceutical Journal, 28(7), 869–875. https://doi.org/10.1016/j.jsps.2020.06.009 [Google Scholar] [PubMed] [CrossRef]
144. Jiang, J., Oguzlu, H., Jiang, F. (2021). 3D printing of lightweight, super-strong yet flexible all-cellulose structure. Chemical Engineering Journal, 405, 126668. https://doi.org/10.1016/j.cej.2020.126668 [Google Scholar] [CrossRef]
145. Shrotri, A., Kobayashi, H., Fukuoka, A. (2018). Cellulose depolymerization over heterogeneous catalysts. Accounts of Chemical Research, 51(3), 761–768. https://doi.org/10.1021/acs.accounts.7b00614 [Google Scholar] [PubMed] [CrossRef]
146. Farrow, M. F., Arnold, F. H. (2011). High throughput screening of fungal endoglucanase activity in Escherichia coli. Journal of Visualized Experiments, 21(54), 7–10. [Google Scholar]
147. Acharya, S., Hu, Y., Abidi, N. (2021). Cellulose dissolution in ionic liquid under mild conditions: Effect of hydrolysis and temperature. Fibers, 9(1), 1–14. https://doi.org/10.3390/fib9010005 [Google Scholar] [CrossRef]
148. Geberekidan, M., Zhang, J., Liu, Z. L., Bao, J. (2019). Improved cellulosic ethanol production from corn stover with a low cellulase input using a Β-glucosidase-producing yeast following a dry biorefining process. Bioprocess and Biosystems Engineering, 42(2), 297–304. https://doi.org/10.1007/s00449-018-2034-9 [Google Scholar] [PubMed] [CrossRef]
149. Burman, N. W., Sheridan, C. M., Harding, K. G. (2020). Feasibility assessment of the production of bioethanol from lignocellulosic biomass pretreated with acid mine drainage (AMD). Renewable Energy, 157, 1148–1155. https://doi.org/10.1016/j.renene.2020.05.086 [Google Scholar] [CrossRef]
150. Ntaikou, I., Antonopoulou, G., Lyberatos, G. (2021). Sustainable second-generation bioethanol production from enzymatically hydrolyzed domestic food waste using pichia anomala as biocatalyst. Sustainability, 13(1), 1–16. https://doi.org/10.3390/su13010259 [Google Scholar] [CrossRef]
151. Bajwa, D. S., Pourhashem, G., Ullah, A. H., Bajwa, S. G. (2019). A concise review of current lignin production, applications, products and their environment impact. Industrial Crops Production, 139, 111526. https://doi.org/10.1016/j.indcrop.2019.111526 [Google Scholar] [CrossRef]
152. Guerrero, A. B., Muñoz, E. (2018). Life cycle assessment of second generation ethanol derived from banana agricultural waste: Environmental impacts and energy balance. Journal of Cleaner Production, 174, 710–717. https://doi.org/10.1016/j.jclepro.2017.10.298 [Google Scholar] [CrossRef]
153. Hossain, N., Razali, A. N., Mahlia, T. M. I., Chowdhury, T., Chowdhury, H. et al. (2019). Experimental investigation, techno-economic analysis and environmental impact of bioethanol production from banana stem. Energies, 12(20), 1–16. https://doi.org/10.3390/en12203947 [Google Scholar] [CrossRef]
154. Joshi, G., Pandey, J. K., Rana, S., Rawat, D. S. (2017). Challenges and opportunities for the application of biofuel. Renewable and Sustainable Energy Reviews, 79, 850–866 https://doi.org/10.1016/j.rser.2017.05.185 [Google Scholar] [CrossRef]
155. Shaharoshaha, A. M., Sulaiman, S. M., Seswoya, R. (2019). Energy recovery from anaerobic digestion of banana peels. International Journal of Recent Technology and Engineering, 8(3), 6269–6273. https://doi.org/10.35940/ijrte.C5876.098319 [Google Scholar] [CrossRef]
156. Alimi, B. A., Workneh, T. S., Oke, M. O. (2016). Effect of hydrothermal modifications on the functional, pasting and morphological properties of South African cooking banana and plantain. CyTA-Journal of Food, 14(3), 489–495. https://doi.org/10.1080/19476337.2015.1137356 [Google Scholar] [CrossRef]
157. Chong, P. A., Newman, D. J. (2020). New biotechnology promising approaches for disease control on bananas and plantains. In: Agricultural, forestry and bioindustry, biotechnology and biodiscovery, pp.13–23. Switzerland: Springer Nature. https://doi.org/10.1007/978-3-030-51358-0 [Google Scholar] [CrossRef]
158. Wang, X., Gao, C., Qi, X., Zhang, Y., Chen, T. et al. (2021). Enhancing sludge fermentation and anaerobic digestion by mechanical cutting pretreatment. Journal of Water Process Engineering, 40, 101812. https://doi.org/10.1016/j.jwpe.2020.101812 [Google Scholar] [CrossRef]
159. Soltan, M., Elsamadony, M., Mostafa, A., Awad, H., Tawfik, A. (2019). Harvesting zero waste from co-digested fruit and vegetable peels via integrated fermentation and pyrolysis processes. Environmental Science and Pollution Research, 26(10), 10429–10438. https://doi.org/10.1007/s11356-019-04647-8 [Google Scholar] [PubMed] [CrossRef]
160. Kumar, M., Dutta, S., You, S., Luo, G., Zhang, S. et al. (2021). A critical review on biochar for enhancing biogas production from anaerobic digestion of food waste and sludge. Journal of Cleaner Production, 305, 127143. https://doi.org/10.1016/j.jclepro.2021.127143 [Google Scholar] [CrossRef]
161. Wen, C., Moreira, C. M., Rehmann, L., Berruti, F. (2020). Feasibility of anaerobic digestion as a treatment for the aqueous pyrolysis condensate (APC) of birch bark. Bioresource Technology, 307, 123199. https://doi.org/10.1016/j.biortech.2020.123199 [Google Scholar] [PubMed] [CrossRef]
162. Dhyani, V., Bhaskar, T. (2018). A comprehensive review on the pyrolysis of lignocellulosic biomass. Renewable Energy, 129, 695–716. https://doi.org/10.1016/j.renene.2017.04.035 [Google Scholar] [CrossRef]
163. Giwa, A. S., Xu, H., Chang, F., Wu, J., Li, Y. et al. (2019). Effect of biochar on reactor performance and methane generation during the anaerobic digestion of food waste treatment at long-run operations. Journal of Environmental Chemical Engineering, 7, 103067. https://doi.org/10.1016/j.jece.2019.103067 [Google Scholar] [CrossRef]
164. Pecchi, M., Baratieri, M. (2019). Coupling anaerobic digestion with gasification, pyrolysis or hydrothermal carbonization: A review. Renewable and Sustainable Energy Reviews, 105, 462–475. https://doi.org/10.1016/J.RSER.2019.02.003 [Google Scholar] [CrossRef]
165. Kaithal, A., Hölscher, M., Leitner, W. (2021). Carbon monoxide and hydrogen (syngas) as a C1-building block for selective catalytic methylation. Chemical Science, 12(3), 976–982. https://doi.org/10.1039/d0sc05404f [Google Scholar] [PubMed] [CrossRef]
166. Andreides, D., Bautista Quispe, J. I., Bartackova, J., Pokorna, D., Zabranska, J. (2021). A novel two-stage process for biological conversion of syngas to biomethane. Bioresource Technology, 327, 124811. https://doi.org/10.1016/j.biortech.2021.124811 [Google Scholar] [PubMed] [CrossRef]
167. Yerga, R. M. N. (2021). Catalysts for production and conversion of syngas. Catalysts, 11(6), 2–5. https://doi.org/10.3390/catal11060752 [Google Scholar] [CrossRef]
168. Krylova, A. Y., Zaitchenko, V. M. (2018). Hydrothermal carbonization of biomass: A review. Solid Fuel Chemistry, 52(2), 91–103. https://doi.org/10.3103/S0361521918020076 [Google Scholar] [CrossRef]
169. El-Desouky, M. G., Khalil, M. A., El-Bindary, A. A., El-Bindary, M. A. (2022). Biological, biochemical and thermochemical techniques for biofuel production: An updated review. Biointerface Research in Applied Chemistry, 12(3), 3034–3054. https://doi.org/10.33263/BRIAC123.30343054 [Google Scholar] [CrossRef]
170. Paida, V. R., Brilman, D. W. F., Kersten, S. R. A. (2019). Hydrothermal gasification of sorbitol: H2 optimisation at high carbon gasification efficiencies. Chemical Engineering Journal, 358, 351–361. https://doi.org/10.1016/j.cej.2018.10.008 [Google Scholar] [CrossRef]
171. Yang, G., Park, S. J. (2019). Conventional and microwave hydrothermal synthesis and application of functional materials: A review. Materials, 12(7), 1177. https://doi.org/10.3390/ma12071177 [Google Scholar] [PubMed] [CrossRef]
172. Kumar, V., Bahuguna, A., Ramalingam, S., Kim, M. (2021). Developing a sustainable bioprocess for the cleaner production of xylooligosaccharides: An approach towards lignocellulosic waste management. Journal of Cleaner Production, 316, 128332. https://doi.org/10.1016/j.jclepro.2021.128332 [Google Scholar] [CrossRef]
173. Brown, A. E., Finnerty, G. L., Camargo-Valero, M. A., Ross, A. B. (2020). Valorisation of macroalgae via the integration of hydrothermal carbonisation and anaerobic digestion. Bioresource. Technology, 312, 123539. https://doi.org/10.1016/j.biortech.2020.123539 [Google Scholar] [PubMed] [CrossRef]
174. Mao, L., Tsui, T. H., Zhang, J., Dai, Y., Tong, Y. W. (2021). System integration of hydrothermal liquefaction and anaerobic digestion for wet biomass valorization: Biodegradability and microbial syntrophy. Journal of Environmental Management, 293, 112981. https://doi.org/10.1016/j.jenvman.2021.112981 [Google Scholar] [PubMed] [CrossRef]
175. Usman, M., Hao, S., Chen, H., Ren, S., Tsang, D. C. W. et al. (2019). Molecular and microbial insights towards understanding the anaerobic digestion of the wastewater from hydrothermal liquefaction of sewage sludge facilitated by granular activated carbon (GAC). Environment International, 133, 105257. https://doi.org/10.1016/j.envint.2019.105257 [Google Scholar] [PubMed] [CrossRef]
176. Zhou, Y., Schideman, L., Zheng, M., Martin-Ryals, A., Li, P. et al. (2015). Anaerobic digestion of post-hydrothermal liquefaction wastewater for improved energy efficiency of hydrothermal bioenergy processes. Water Science and Technology, 72(12), 2139–2147. https://doi.org/10.2166/wst.2015.435 [Google Scholar] [PubMed] [CrossRef]
177. Alhraishawi, A. A., Alani, W. K., Chaichan, M. T., Jawad, R. S. (2020). Performance of oil on bio-methane creation under anaerobic Co-fermentation condition. review. IOP Conference Series: Materials Science and Engineering, 881(1), 012189. https://doi.org/10.1088/1757-899X/881/1/012189 [Google Scholar] [CrossRef]
178. Haarlemmer, G., Guizani, C., Anouti, S., Déniel, M., Roubaud, A. et al. (2016). Analysis and comparison of bio-oils obtained by hydrothermal liquefaction and fast pyrolysis of beech wood. Fuel, 174, 180–188. https://doi.org/10.1016/j.fuel.2016.01.082 [Google Scholar] [CrossRef]
179. Usman, M., Chen, H., Chen, K., Ren, S., Clark, J. H. et al. (2019). Characterization and utilization of aqueous products from hydrothermal conversion of biomass for bio-oil and hydro-char production: A review. Green Chemistry, 21(7), 1553–1572. https://doi.org/10.1039/c8gc03957g [Google Scholar] [CrossRef]
180. Chen, Y., Mu, X., Luo, X., Shi, K., Yang, G. et al. (2020). Catalytic conversion of methane at low temperatures: A critical review. Energy Technology, 8(8), 1–12. https://doi.org/10.1002/ente.201900750 [Google Scholar] [CrossRef]
181. Feng, Q., Lin, Y. (2017). Integrated processes of anaerobic digestion and pyrolysis for higher bioenergy recovery from lignocellulosic biomass: A brief review. Renewable and Sustainable Energy Reviews, 77, 1272–1287. https://doi.org/10.1016/j.rser.2017.03.022 [Google Scholar] [CrossRef]
182. Luz, F. C., Cordiner, S., Manni, A., Mulone, V., Rocco, V. et al. (2018). Ampelodesmos mauritanicus pyrolysis biochar in anaerobic digestion process: Evaluation of the biogas yield. Energy, 161, 663–669. https://doi.org/10.1016/j.energy.2018.07.196 [Google Scholar] [CrossRef]
183. Zabed, H. M., Akter, S., Yun, J., Zhang, G., Awad, F. N. et al. (2019). Recent advances in biological pretreatment of microalgae and lignocellulosic biomass for biofuel production. Renewable and Sustainable Energy Reviews, 105, 105–128. https://doi.org/10.1016/j.rser.2019.01.048 [Google Scholar] [CrossRef]
184. Chen, J., Zhang, B., Luo, L., Zhang, F., Yi, Y. et al. (2021). A review on recycling techniques for bioethanol production from lignocellulosic biomass. Renewable and Sustainable Energy Reviews, 149, 111370. https://doi.org/10.1016/j.rser.2021.111370 [Google Scholar] [CrossRef]
185. Seyedi, S., Venkiteshwaran, K., Zitomer, D. (2019). Toxicity of various pyrolysis liquids from biosolids on methane production yield. Frontiers in Energy Research, 7(5), 1–12. https://doi.org/10.3389/fenrg.2019.00005 [Google Scholar] [CrossRef]
186. Kucharska, K., Rybarczyk, P., Hołowacz, I., Łukajtis, R., Glinka, M. et al. (2018). Pretreatment of lignocellulosic materials as substrates for fermentation processes. Molecules, 23(11), 1–32. https://doi.org/10.3390/molecules23112937 [Google Scholar] [PubMed] [CrossRef]
187. Doukeh, R., Bombos, M., Bombos, D., Vasilievici, G., Radu, E. et al. (2021). Pyrolysis of digestate from anaerobic digestion on tungsten oxide catalyst. Reaction Kinetics, Mechanisms and Catalysis, 132(2), 829–838. https://doi.org/10.1007/s11144-021-01952-7 [Google Scholar] [CrossRef]
188. Chavan, S., Gaikwad, A. (2021). Extraction and recovery of lignin derived phenolic inhibitors to enhance enzymatic glucose production. Biomass and Bioenergy, 144, 105897. https://doi.org/10.1016/j.biombioe.2020.105897 [Google Scholar] [CrossRef]
189. Sarker, T. R., Pattnaik, F., Nanda, S., Dalai, A. K., Meda, V. et al. (2021). Hydrothermal pretreatment technologies for lignocellulosic biomass: A review of steam explosion and subcritical water hydrolysis. Chemosphere, 284, 131372. https://doi.org/10.1016/j.chemosphere.2021.131372 [Google Scholar] [PubMed] [CrossRef]
190. Song, B., Lin, R., Lam, C. H., Wu, H., Tsui, T. H. et al. (2021). Recent advances and challenges of inter-disciplinary biomass valorization by integrating hydrothermal and biological techniques. Renewable and Sustainable Energy Reviews, 135, 110370. https://doi.org/10.1016/j.rser.2020.110370 [Google Scholar] [CrossRef]
191. Zhang, Q., Tan, X., Wang, W., Yu, Q., Wang, Q. et al. (2019). Screening solvents based on hansen solubility parameter theory to depolymerize lignocellulosic biomass efficiently under Low temperature. ACS Sustainable Chemistry and Engineering, 7(9), 8678–8686. https://doi.org/10.1021/acssuschemeng.9b00494 [Google Scholar] [CrossRef]
192. Soliman, R. M., Younis, S. A., El-Gendy, N. S., Mostafa, S. S. M., El-Temtamy, S. A. et al. (2018). Batch bioethanol production via the biological and chemical saccharification of some Egyptian marine macroalgae. Journal of Applied Microbiology, 125(2), 422–440. https://doi.org/10.1111/jam.13886 [Google Scholar] [PubMed] [CrossRef]
193. Dreiblatt, A. (2003). Process Design. In: Pharmaceutical extrusion technology, pp. 153–170. New York: Marcel Dekker, Inc. https://doi.org/10.4324/9780429290602-8 [Google Scholar] [CrossRef]
194. Oladosu, Y., Rafii, M. Y., Abdullah, N., Magaji, U., Hussin, G. et al. (2016). Fermentation quality and additives: A case of rice straw silage. BioMed Research International, 2016, 1–14. https://doi.org/10.1155/2016/7985167 [Google Scholar] [PubMed] [CrossRef]
195. Pardo-Planas, O., Atiyeh, H. K., Phillips, J. R., Aichele, C. P., Mohammad, S. (2017). Process simulation of ethanol production from biomass gasification and syngas fermentation. Bioresource Technology, 245, 925–932. https://doi.org/10.1016/j.biortech.2017.08.193 [Google Scholar] [PubMed] [CrossRef]
196. Dittrich, L., Nohl, M., Jaekel, E. E., Foit, S. B., de HaartL. G. J. et al. (2019). High-temperature Co-electrolysis: A versatile method to sustainably produce tailored syngas compositions. Journal of the Electrochemical Society, 166(13), 971–975. https://doi.org/10.1149/2.0581913jes [Google Scholar] [CrossRef]
Cite This Article
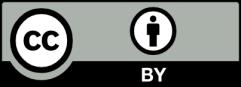