Open Access
REVIEW
Little Secrets for the Successful Industrial Use of Tannin Adhesives: A Review
LERMAB, EA 4370-USC INRAE, University of Lorraine, Blvd des Aiguillettes, Nancy, 54506, France
* Corresponding Author: Antonio Pizzi. Email:
(This article belongs to the Special Issue: Renewable and Biosourced Adhesives-2023)
Journal of Renewable Materials 2023, 11(9), 3403-3415. https://doi.org/10.32604/jrm.2023.030930
Received 04 May 2023; Accepted 24 May 2023; Issue published 20 July 2023
Abstract
This brief article reviews a very particular and quite narrow field, namely what has been done and what is needed to know for tannin adhesives for wood panels to succeed industrially. The present fashionable focus on bioadhesives has led to producing chemical adhesive formulations and approaches for tannin adhesives as a subject of academic publications. These, as good and original they might be, are and will still remain a rather empty academic exercise if not put to the test of real industrial trials and industrial use. They will remain so without the “little” secrets and techniques outlined here that show that there is a great gap between developing an adhesive formulation in the laboratory and the hard reality to make it work where it does really count, in its industrial application. It outlines the fact that even more modern and excellent, newly developed bioadhesive formulations might well miserably fail once tried in the industry if the problems that always arise in their upgrading are not identified and solved, and solved well. It also outlines the fact that not only must costs always be taken into account and that a practical and possibly easy-to-handle approach must always be used, but too expensive or complex and unyielding adhesive systems are also often shown to be unusable or unsuitable in industry.Keywords
It has been a long time now, since the early 1970s, that tannin adhesives have been developed and are used commercially and industrially as thermosetting binders for wood panels [1–3]. The writer has been part of this development since its earliest stages [1,4]. There is now and in the last few years an increasing interest in condensed tannins for adhesives by a number of researchers [5,6]. However there are a number of “little secrets”, techniques in reality, developed for their successful industrial preparation and use that are mostly unknown to recent researchers and industry-interested people in this field. This is so because either they have never been published, or have been published a very long time ago, or in a widely dispersed manner, sometimes in journals relatively obscure, or even in journals that no more exist. This article is reviewing all these small but essential techniques for such bioadhesives to be prepared and used successfully industrially. Some of them will be known to the readers but I am equally certain that some of them will be unknown to them.
2 The Secret to Obtaining High Percentages of Extraction Yield
The technique described here has been developed more recently, in the 1980s, and applied industrially to two different commercial tannins. Its discovery was prompted by the relatively lower extraction yields for pine bark tannin adhesives in relation to more established commercial tannins such as mimosa and quebracho. With the traditional industrial countercurrent extraction with sodium bisulfite (with or without small amounts of sodium hydrogen carbonate) pine bark tannin yielded in average between 12%–13% yield of tannin extract on the weight of the bark used [7–9], against the industrial extraction yields of between 28% and 32% for quebracho and mimosa tannin extracts [10]. While 12%–13% still has a sure economical interest, such a percentage yield is much lower than the extraction yield of the more established commercial tannin extracts. This lower extraction yield was ascribed to the facile formation and precipitation of insoluble phlobaphenes (tanner’s red) [11] and tannins self-condensation [12–14] under the traditional conditions and techniques of extraction used. A system was then developed to block/minimize the forming of these compounds by blocking tannin self-condensation by the addition of a strong nucleophile, the lowest cost one being urea, this being used in very small quantities [8]. Urea reacted preferentially with the rearrangement intermediates leading to self-condensation and phlobaphenes formation, stopping it (Fig. 1). This technique proved to be effective at both the laboratory and industrial levels. Minimizing self-condensation and phlobaphenes formation in this manner led to an increase in yield to 19% and 25% in industrial pine tannin extraction [8] with more than significant economic consequences. Many years later in the 1990s or 2000s, the same technique was used in the industrial extraction of quebracho extract, increasing the yield from the traditional 28% to about 40% [15].
Figure 1: Mechanism of phlobaphene formation and of the system for blocking it with urea to maintain the reactivity of the tannin extract
Sulfitation by sodium bisulfite, is certainly the oldest modification of condensed tannin extracts to render them more soluble, decrease their viscosity and thus improve their ease of penetration in animal hides to make leather. Sulfitation consists in introducing sulfonic groups at the C2 site of some flavonoid units of the tannin resulting in some tannin heterocycle rings opening (Fig. 2). The introduction of the polar sulfonic group and a further phenolic hydroxyl induces increased solubility and helps reduce viscosity. Often, but not always, tannin extracts are sold with a certain level of sulfitation. As regards adhesives, there is a fine line between too little or too much sulfitation. Too little sulfitation may cause a problem of solubility in some tannin extracts of higher molecular weight or too high a viscosity, while too much sulfitation will so improve the hydrophilicity of the tannin extract to render the adhesive useless for exterior grade application absorbing far too easily water through its sulfonic groups excess and thus degrade the glue-line [16]. The results show that very little difference exists between the results of unsulfited and moderately sulfited tannin used for exterior grade tannin adhesives, the decrease of viscosity in moderately sulfited tannins sometimes favouring their application as they allow their use at a higher percentage solids content. Excessive sulfitation however tends to affect quite markedly the water resistance of the glueline of hardened tannin adhesives.
Figure 2: Reaction of sulfitation of tannin with the opening of the heterocyclic ring and introduction of a sulfonic group in the structure of the tannin
4 Treatments to Decrease Viscosity and Increase Reactivity
It always astonishes this writer when most new entrants in the tannin adhesives field insist on using raw tannin extracts, often obtaining results not acceptable for industrial application, without realizing that much better results can be obtained by treatments already developed and established, and used already for a long time both industrially and commercially. Treatments which have also been published [17–19].
Tannin extracts have in general too high a viscosity to be applied through the normal mechanical systems used in particleboard factories. Dilution with water causes lower adhesive solids content, hence unacceptably long hot press times due to the excess water that needs to be evacuated as steam during hot pressing. As seen above sulfitation too cannot really be used as it will introduce other problems. The treatment developed and used commercially for the most diffuse commercial tannins, namely mimosa and quebracho, was developed in the very early 1970s and it has been used industrially since then for tannin-based particleboard adhesives. It is based on a series of additions in the hot of small amounts of chemicals, first acetic anhydride, although also maleic anhydride works well, then caustic soda, and cooking this mix for about three hours, finally adjusting the pH to the one giving the reactivity wanted, originally with fine powder paraformaldehyde hardener. Generally under mechanical stirring, at 80°C−82°C, 3% of anhydride on tannin extract solids is added, then the temperature is increased over 45 min to 90°C−92°C by heating and 25%–30% NaOH solution is slowly added over about 15 min to bring the pH up to almost 8. The mix is then left under mechanical stirring while maintaining the temperature at 90°C−92°C for about 3 h from the beginning of the NaOH solution addition. The pH drops naturally during this heating period down to between 7.2 and 7.5. The mix is then cooled and the pH corrected with acetic acid to 6.7–6.9 if the hardener used is paraformaldehyde, to a different pH as needed if other types of hardener are used. Two points must be kept in mind: the temperature must neither go over 92°C nor the 3 h cooking period otherwise reactions of self-condensation and viscosity increases occur [17,18]. Originally, a small amount of raw unpurified phenyl acetate was also added between the anhydride and caustic soda additions, but this was discontinued earlier as just the increase of the anhydride to 3% rendered its addition useless.
What does this treatment cause? First and foremost it decreases drastically the viscosity of the extract by (i) hydrolyzing to smaller sizes the hydrocolloid gums, namely oligomeric fragments of hemicelluloses, always present in the extract, and (ii) opening a number of the flavonoid units heterocyclic ring. Thus, the material so obtained has a much lower viscosity, but also has acquired a flavonoid A-ring of higher reactivity with the transformation of the ether oxygen of the heterocycle to a phenolic –OH group in meta to the pre-existing phenolic –OH groups thus increasing the reactivity of the aromatic ring towards aldehydes and other reagents. Decreases to between 1/3 and 1/5 of the original extract viscosity at equal solids content have been recorded [19], allowing a higher adhesive percentage solids content to be used when applying the adhesive. Equally, the opening of a large number of the tannin flavonoid units heterocycle liberates one –OH group on the aromatic A-ring, –OH derived from the ether –O- of the heterocycle, markedly increasing the reactivity of the aromatic A-ring of the flavonoid units. The graph of gel times in Fig. 3 shows the difference in reactivity between raw extracts (continuous lines) and chemically treated ones (segmented lines).
Figure 3: Gel time curves, as a function of pH, at parity of conditions of raw tannin extracts (continuous lines) vs. treated tannin extract adhesives (segmented lines). Note that the gel times of the fastest gelling extracts are already too quick to need the treatment for reactivity but can they still benefit from it to decrease their viscosity [24]
There is a third much less known effect that also contributes to the increase in reactivity of the tannin. As the treatment is done starting on a 50% tannin extract solution in water, the anhydride was initially thought to all go to acetic acid just contributing to acid hydrolysis of the hydrocolloid gums. This is not just the case, as tannin oligomers of higher molecular weight are in a colloidal state, with then part of the anhydride migrating within the colloidal micelles and acetylating (or maleating, according to the anhydride used) the tannin phenolic hydroxyls. Esters are well-known to function as accelerators of phenol-aldehyde reactions [20–23], this applying also to tannin reactions, a now well-known contributor to tannin reactivity [17].
It must be pointed out that while the treatment outlined in this paragraph is extensively used industrially and it is commercial since the early 1970s, by two companies under brand names, one using mimosa tannin and the other quebracho tannin, the author has been instrumental in developing such a treatment [4], the same system is only of very limited use for pine tannins and other procyanidin/prodelphinidin types. There is still a clear decrease in viscosity although not marked as for mimosa and quebracho, due to hydrocolloid gums hydrolysis, but there is no improvement in reactivity. This is due to procyanidin/prodelphinidin type tannins being so much more reactive than the mimosa and quebracho tannins, about 6 times more reactive [24] that the accelerating effect is not noticeable anymore. This can be seen in Fig. 3 as the pecan and pine tannin extract are considerably faster at all pHs to gel.
5 Plywood: The Zinc Salts Effect
While most of the industrial work on the application of thermosetting tannin adhesives has been focused on particleboard, fiberboard, oriented strand board type of composites, there is still a little secret of formulation also in the tannin adhesives for plywood that have been used and are still used industrially. This is based on the accelerating effect of small amounts of Zinc salts, in particular Zinc acetate, but the much cheaper Zinc chloride will also do [4,10,25]. Other metallic ions can also be used but they are either somewhat toxic or much more expensive [10,26–28]. The reason for this behavior of zinc ion salts is that they are able to improve the reactivity of tannins towards aldehydes without having to change their pH. This means that much lower pHs can be used, leading to lower water absorption of the hardened glueline when in operation, translating into much better weather resistance and exterior grade performance. This little trick can also be used for other applications other than plywood but, at present has just been used and is used industrially for tannin-bonded plywood.
6 The Development of Faster Hot Press Times and the Advantage and Problem of the High Moisture Content
While traditional tannin adhesives for particleboard cured by fine powder paraformaldehyde as hardeners have been successfully used industrially for many years and are still used in several plants around the world at relatively long press times, between 10 and 12 s per mm of board thickness, at 190°C, such pressing times are considered slow today for more modern plants applications. It is clear that while such press times are very slow in relation to aminoplastic resins such as UFs today using between 3 and 5 s/mm at 220°C, they are less slower but still slower than synthetic PF resins using a number of different technologies to be accelerated industrially to hot press times between 6 and 9 s/mm board thickness.
The challenge of fast press times for tannin adhesives clashes with a considerable problem. Tannin adhesives are used in water which is their favorite carrier, and does not melt on heating such as synthetic PF resins. Briefly speaking, they need water to spread and love water so much that industrially one can produce particleboards of really excellent quality at wood particles moisture content percentages that are unthinkable of and not tolerated by other particleboard adhesives. This author has seen excellent tannin-bonded particleboard being produced in the plant at 18% moisture content of resinated wood chips. While this is an advantage for a factory as the wood chips need to be much less dried, thus a clear economy of drying energy and time, to eliminate such amount of water needs more time, slowing to the values indicated above the hot press time.
The first way to shorten press time is of course to increase the press temperature as in modern factories to 220°C−230°C. This improves the situation a bit, but the press time is still slower than what is obtained with other adhesives. Thus, two systems have been developed and used industrially to decrease the percentage moisture content and thus achieve shorter hot press times. The first one, now obsolete, was used in two different factories in two different countries with some success. It consisted of adding to the gluing blender a small screw conveyor and through it adding a certain proportion of the tannin extract in spray-dried fine powder form as the rest of the tannin was sprayed on the wood chips as a water solution [29–32]. All the paraformaldehyde powder hardener and up to 30% of the tannin extract adhesive spray-dried powder was removed from the liquid tannin adhesive glue-mix in solution. The powder mix was then added to the wood chips just before the glue blender, where the glue-mix was sprayed or added to the chips. Core materials’ moisture contents of 10%–12% and surfaces of resinated wood chips’ moisture contents of 20%–22% can then be achieved with ease. The percentage of paraformaldehyde used varied from the early days 14% on adhesive solids content to 8% in later trials and productions, and even to 6%–8% with 5% of urea added later on. The pHs of the chemically pretreated tannin adhesive were 6.6–6.7 for application to the surface material and 6.9–7.3 for the adhesive for the core material. The resin solids percentage on dry wood used was 11% for the board core material and between 14%–18% for the face material. In reality the proportion of powder added was never higher than 20%–30% of the total tannin extract added, the rest being added simultaneously as a 50% solution in water. In this manner the amount of water was markedly decreased and the press time was shortened. The system was not only primitive, but difficult to control and frankly quite messy.
The second system is still used in a factory of an industrial group and was much more intelligent and worked very well. In the Bison particleboard system and other systems using a single daylight press, fast pressing times are absolutely essential to maintain the profitability of the plant. This second system is particularly suitable for Drais Turboplan glue-blenders and related/similar types of glue blenders (Fig. 4). In the Bison particleboard system the resinated wood chips are in general transported by an air current to the panels forming station. The factory inserted in this air-line, around the line mid-length, a powerful air-to-air plate heat exchanger (Fig. 5). The moisture of the resinated chips was then markedly lowered by a level of flash drying, notwithstanding that the tannin adhesive was added at the correct percentage load. The tannin adhesive was diluted with water down to approximately 30% solids content and blended as such to the wood chips in the glue blender, thus all the adhesive is applied as a liquid glue-mix. The resinated particles come out of the blender at 30% moisture content or even higher. The airflow/blowing transport of the resinated wood chips to the forming station is where a forced countercurrent drier is inserted generating a temperature between 70°C and 90°C. The longest time of residence of the wood chips in the air flow duct before reaching the forming station was of 4 s, and during this time their percentage moisture content decreased to 10%–14% for board core particles and to 16%–22% for the surface particles. The short permanence of the resinated chips in the air flow duct does not impair the effectiveness of bonding simply because the flash drying in the air duct and the water flash evaporation in relation cools down the resinated chips avoiding any pre-curing. The paraformaldehyde powder hardener was added to the wood chips in powder form before the addition of the liquid adhesive, or mixed to the liquid adhesive in the gluemix. Thus one can use the correct amount of water in the glue-mix ensuring its proper spreading in the glue blender while receiving the resinated wood chip at a much lower water content to ensure a faster press time, comparable to the fastest synthetic PF adhesives or even faster. Press times as low as 5–6 s/mm board thickness in industrial one-daylight Bison presses were obtained with this approach for several years production in South Africa [33].
Figure 4: Drais Turboplan type gluing blender. Note that this type of blender is completely filled with wood chips in continuous movement through the blender. The adhesive glue-mix is not sprayed but spread by centrifugal force through the rotating axe of the blender though a series of nozzles situated on it alternating with movement paddles
Figure 5: Schematic representation (top) of online heat exchange drier insertion on the air flow duct carrying the resonated wood chips from the glue blender to the forming station. A similar type of drier as the air to air type plate heat exchanger used for the purpose (bottom)
A further convenient and very effective system to speed up considerably the hot press time of tannin adhesives has been developed in cooperation with a sizeable Japanese company and it is industrially used to manufacture very tick particleboard between 40 and 120 mm thickness used as structural panels and beams of wood-based Japanese homes [34]. The tannin used was Tanzanian mimosa extract and the system has been used industrially with hexamethylenetetramine (hexamine) as the hardener, the board being mainly for internal use, resistant, however, to humidity and in protected/covered exterior areas. The system uses steam injection through the panel and nothing else, and the industrial hot press time achieved at 180°C hot press platen temperature was 7.5 s/mm board thickness for the 40 mm thick board and as fast as 2.5 s/mm board thickness for the 120 mm thick boards, with the results satisfying well the requirements of Japanese standard JIS A5908 for interior and semi-exterior grade panels for IB strength, 24 h cold water swelling, and formaldehyde emission [34]. This is a really remarkable industrial result, with a hot press time comparable to that of boards bonded with the fastest aminoplastic resins such as UFs and MUFs.
7 Industrial Use of Different Hardeners
While several hardeners of real future interest have been tried at the laboratory level for tannin adhesives bonding of wood boards, only a few of them have been industrially used, either extensively, or at least tried in extensive industrial trials. To date, these are paraformaldehyde fine powder [3,10,19], paraformaldehyde + urea [35–37], paraformaldehyde reinforced with pMDI [32], liquid formalin concentrate solution, namely a formaldehyde solution stabilized by urea [38,39], hexamethylene tetramine (hexamine) [3,19,34], furfuryl alcohol (for hardboards) [40] and tris(hydroxymethyl) nitromethane [41].
The classical hardener has been paraformaldehyde fine powder since the industrial inception of tannin adhesives for particleboard in 1971 in South Africa and other countries, and it still is in countries where its use is either not, or only partially restricted, when the boards are for exterior weather resistance unprotected use. The figure hereunder illustrates as an example the conditions of an industrially produced tannin-paraformaldehyde board in relation to a then good MUF bonded one, after 15 years of unprotected weather exposure in a high ultraviolet intensity area (Fig. 6). The visual conditions of the two boards speak for themselves.
Figure 6: Comparison of industrially manufactured particleboard respectively bonded with a pure melamine-formaldehyde synthetic adhesive and a tannin bio-adhesive after 15 years unprotected weather exposure in a high UV radiation area. Compare the conditions of edges and surfaces of the two panels
The paraformaldehyde + urea hardener is a later variation of the previous one to ensure even lower residual formaldehyde emission, already low even without urea. It is not necessary here to elaborate on either of these two hardeners as the literature is full of articles and also several in depth reviews on them [10,42]. The use of paraformaldehyde reinforced with very small amounts of pMDI (5%) has also been used industrially for pine tannin adhesives to bond particleboard and MDF at the beginning of their industrial use. At that time pine tannin had been found to be more difficult to handle due to its greater reactivity, but the need to use pMDI disappeared as the staff took confidence and learned to use the tannin resin without any isocyanate. The pine tannin adhesives were successfully used for 10 years in Chile for particleboard production in an old factory in Chiguayante [32]. Fig. 7 shows building exclusively built with tannin–bonded particleboard, more than 20 years after their construction.
Figure 7: Buildings exclusively built with double walls of tannin-based particleboard. Office building with walls of pine tannin adhesive bonded particleboard 20 years after its construction in Chile (left). Low cost house with walls of mimosa tannin adhesive bonded particleboard immediately after its construction and still standing today in coastal area in South Africa (right)
Hexamine, has been used industrially since 1974, first for a limited period of time just for interior grade particleboards [10,19] in the middle 1970s. It became of major interest only later as the rules limiting formaldehyde emission started to become of actuality and a priority. It is possible to produce exterior grade boards bonded with hexamine [10,19,36,37] but they are of a lesser quality than the paraformaldehyde-bonded ones. The formaldehyde emission is however even lower, but the conditions of application, mainly the pH at which this hardener works, are so totally different from the ones at which the previous hardeners do work that sometimes it is difficult to gauge what type of results are obtained. This notwithstanding, examples of successful industrial utilization with this hardener under the most suitable conditions of use are also reported in the literature [19,34].
Still remaining in the field of formaldehyde as the hardener, two factories of the same group in Australia have been using industrially since the middle 1970s a treated (cf. par. 3) mimosa tannin adhesive hardened with a formaldehyde liquid concentrate (formurea) solution, while still obtaining acceptable emission results, producing 18 mm thick exterior grade particleboard for houses suspended floors. A factory of an industrial group in Germany has also been using industrially tannin adhesives to manufacture particle boards for interior cabinets since the late 1970s, and not since 1988 as previously erroneously reported [43]. Originally they used paraformaldehyde as the hardener, but then they used a no-formaldehyde technology in later years as the panels were used only for exterior use.
There are two other hardeners that have also been tried in extended and successful industrial trials for bonding panels, one for thin hardboards and one for particleboards. They have not been used as they both were rather expensive at the time they were tried than the more traditional hardeners described above. These were the first tris(hydroxymethyl) nitromethane (Fig. 8), the smaller compound of the series of tris(hydroxylmethyl) nitromehanes, and the least expensive, used for bonding thin MDF [41].
Figure 8: Formula of tris(hydroxymethyl)nitromentane, an effective, industrially tried, no formaldehyde emission hardener for tannin adhesives
The problems of this hardener, which worked well in industrial particleboard production, with no formaldehyde emission, were two: (i) the cost that was relatively high, although still somewhat tolerable, and (ii) the fact that it was manufactured by only one company/factory in the world. It is mainly this second reason that did not reasonably allow its more extensive use. It must be noticed that a very similar compound, namely tris(hydroxymethyl) aminomethane was patented much later for a similar use in New Zealand [6] for pine tannin resins, but it is not known if it was ever tried industrially, but probably not used for the same drawbacks outlined above.
The second hardener is furfuryl alcohol, also a biosourced material obtained from agricultural waste. Furfuryl alcohol is a very reactive compound and does react very readily with tannins as also demonstrated by the large literature on its use as a wood adhesive [42,44] and in tannin-furfuryl alcohol fire-resistant foams [45] and hard plastics and other binders [46–49]. Its use as both a tannin hardener and a simultaneous co-monomer for adhesives has been described at the laboratory level, but few people know that relevant industrial trials with tannin-furfuryl alcohol bonding of exterior grade hardboard were carried out at the end of the 1990s [40]. The results were most acceptable, although simultaneous trials in particleboard bonding at 180°C hot press temperature gave results somewhat below the requirements of the relevant standards [40]. However this co-monomer of tannin, as much as hydroxymethyl furfural (a furfuryl alcohol derivate), shows promise as demonstrated by an extensive industrial trial of tannin-furfuryl alcohol foams [50]; the present major problem which it presents is its upgrading by the European Commission to a higher level of toxicity to humans when not polymerized.
This brief review has been aimed at collating together all those little and little-known techniques that are anyhow essential to allow the use of tannin resins as adhesives of wood panel products. Without knowing such little techniques that have allowed the successful industrial use of tannin adhesives, optimal results in this field cannot be achieved by the newer generation of technologists working, or hoping to work, on bioadhesives and bioresins. It is a series of glaring examples that while adhesives chemical formulation is a science in itself, even the best formulated adhesive is bound to fail if sometimes simple techniques, mechanical or others are not used for the real final purpose of adhesives, namely industrial bonding.
Funding Statement: The author received no specific funding for this study.
Conflicts of Interest: The author declares that he has no conflicts of interest to report regarding the present study.
References
1. Pizzi, A. (1977). Hot-setting tannin-urea-formaldehyde exterior wood adhesives. Adhesives Age, 20(12), 27–29. [Google Scholar]
2. Pizzi, A., Scharfetter, H. (1978). The chemistry and development of tannin-based adhesives for exterior plywood. Journal of Applied Polymer Science, 22(6), 1745–1761. [Google Scholar]
3. Pizzi, A. (1978). Wattle-based adhesives for exterior grade particleboard. Forest Products Journal, 28(12), 42–47. [Google Scholar]
4. Pizzi, A. (2000). Tannery row—the story of some natural and synthetic wood adhesives. Wood Science and Technology, 34(4), 277–316. [Google Scholar]
5. Oktay, S., Pizzi, A., Köken, N., Bengü, B. (2023). Tannin-based wood panels adhesives. Wood Science and Technology, submitted. [Google Scholar]
6. Grigsby, W. J., McIntosh, C. D., Martin, M., Suckling, I. D., Anderson, C. R. (2008). Adhesives, US patent 7,319,115B2. [Google Scholar]
7. Von Leyser, E., Pizzi, A. (1990). The formulation and commercialization of glulam pine tannin adhesives in Chile. Holz als Roh und Werkstoff, 48(1), 25–29. [Google Scholar]
8. Sealy-Fisher, V. J., Pizzi, A. (1992). Increased pine tannins extraction and wood adhesives development by phlobaphenes minimization. Holz als Roh und Werkstoff, 50(5), 212–220. [Google Scholar]
9. Baeza, J. (1989). University of Concepcion, Chile, personal communication. [Google Scholar]
10. Pizzi, A. (1983). Tannin-based adhesives. In: Wood adhesives chemistry and technology. New York: Marcel Dekker. [Google Scholar]
11. Young, D. A., Cronje, A., Botes, A. L., Ferreira, D., Roux, D. G. (1985). Synthesis of condensed tannins, part 14: Biflavonoids profisetinidins as synthons. The acid induced “phlobaphene” reaction. Journal of the Chemical Society Perkins Transactions, 1, 2521–2527. [Google Scholar]
12. Roux, D. G. (1989). Activation of some condensed tannins via facile ring isomerization. In: Hemingway, R. W., Conner, A. H. (Eds.Adhesives from renewable resources, pp. 217–228. Washington DC: American Chemical Society. [Google Scholar]
13. Steenkamp, J. A., Steynberg, J. P., Brandt, E. V., Ferreira, D., Roux, D. G. (1985). Phlobatannins, a novel class of ring-isomerized condensed tannins. Journal of the Chemical Society, Chemical Communications, 1678–1679. [Google Scholar]
14. Steynberg, J. P., Young, D. A., Burger, J. F. W., Ferreira, D., Roux, D. G. (1986). Phlobatannins via facile ring isomerization of profisetinidin and prorobinetinidin condensed tannin units. Journal of the Chemical Society, Chemical Communications, 1013–1015. [Google Scholar]
15. Indunor, S. A. (2000). Silvateam Group, La Escondida, Argentina, private comunication. [Google Scholar]
16. Pizzi, A. (1979). Sulphited tannins for exterior wood adhesives. Colloid Polymer Science, 257(1), 37–40. [Google Scholar]
17. Pizzi, A., Stephanou, A. (1992). Theory and practice of non-fortified tannin adhesives for particleboard. Holzforschung und Holzverwertung, 44(4), 62–68. [Google Scholar]
18. Pizzi, A. (1980). Effect and mechanism of hot caustic soda treatment on wattle tannin adhesives. International Journal of Adhesion and Adhesives, 1(2), 107–108. [Google Scholar]
19. Pizzi, A. (1978). Chemistry and technology of cold-and thermosetting tannin-based exterior wood adhesives (Ph.D. Thesis). University of the Orange Free State, South Africa. [Google Scholar]
20. Pizzi, A., Stephanou, A. (1993). On the chemistry, behaviour and cure acceleration of phenol-formaldehyde resins under very alkaline conditions. Journal of Applied Polymer Science, 49(12), 2157–2160. [Google Scholar]
21. Stephanou, A., Pizzi, A. (1993). Rapid curing lignins-based exterior wood adhesives, Part 2: Acceleration mechanisms and application to panel products. Holzforschung, 47(6), 501–506. [Google Scholar]
22. Lei, H., Pizzi, A., Despres, A., Pasch, H., Du, G. (2006). Ester acceleration mechanisms in phenol-formaldehyde resin adhesives. Journal of Applied Polymer Science, 100, 3075–3093. [Google Scholar]
23. Pizzi, A., Garcia, R., Wang, S. (1997). On the networking mechanisms of additives-accelerated phenol-formaldehyde polycondensates. Journal of Applied Polymer Science, 66, 255–266. [Google Scholar]
24. Pizzi, A. (1994). Advanced wood adhesives technology. New York: Marcel Dekker. [Google Scholar]
25. Kroon, R. (1971; 1976). Leather Industries Research Institute, Grahamstown, South Africa, private communication. [Google Scholar]
26. Pizzi, A. (1979). Phenolic resins by reactions of coordinated metal ligands. Journal of Polymer Science: Polymer Letters Edition, 17(8), 489–492. [Google Scholar]
27. Pizzi, A. (1979). Phenolic and tannin-based adhesive resins by reactions of coordinated metal ligands. I. Phenolic chelates. Journal of Applied Polymer Science, 24(5), 1247–1255. [Google Scholar]
28. Pizzi, A. (1979). Phenol and tannin-based adhesive resins by reactions of coordinated metal ligands, Part II: Tannin adhesives preparation, characteristics and application. Journal of Applied Polymer Science, 24(5), 1257–1268. [Google Scholar]
29. Pizzi, A. (1979). Glue blenders effect on particleboard using wattle tannin adhesives. Holzforschung und Holzverwertung, 31(4), 85–86. [Google Scholar]
30. Pizzi, A., Barray, R., Lajouesse, M. (1977). Bondtite-Novoboerd-Isoroy, Port Elizabeth, South Africa, unpublished results. [Google Scholar]
31. Pizzi, A., Valenzuela, J., Westermeyer, C., von Leyser, E. P. (1991). Masisa, Chiguayante, Chile, unpublished results. [Google Scholar]
32. Valenzuela, J., von Leyser, E., Pizzi, A., Westermeyer, C., Gorrini, B. (2012). Industrial production of pine tannin-bonded particleboard and MDF. European Journal of Wood and Wood Products, 70(5), 735–740. [Google Scholar]
33. Breytenbach, P., Pizzi, A., van Niekerk, J. (1980). Bisonboard (Pty.) Ltd, Piet Retief, South Africa, unpublished results. [Google Scholar]
34. Pichelin, F., Nakatani, M., Pizzi, A., Wieland, S., Despres, A. et al. (2006). Structural beams from thick wood panels bonded industrially with formaldehyde free tannin adhesives. Forest Products Journal, 56(5), 31–36. [Google Scholar]
35. Pizzi, A., Roll, W., Dombo, B. (1995). Bakelite AG, Duisburg, Germany, unpublished results. [Google Scholar]
36. Pizzi, A., Roll, W., Dombo, B. (1995). Hitzehärtende bindemittel, European patent EP-B 0 639 608 A1 (1994); B1(1998); German patent DE 44 02 159 A1 (1995); USA patent 5,532,330. [Google Scholar]
37. Pizzi, A., Roll, W., Dombo, B. (1995). Bindemittel auf der basis von gerbstoffen, European patent EP-B 0 648 807 (1998); German patent DE 44 06 825 A1 (1995); USA patent 5,532,330. [Google Scholar]
38. Pizzi, A., Sorfa, P. (1979). Liquid formaldehyde concentrates as hardener for tannin-based adhesives. Holzforschung und Holzverwertung, 31(5), 113–115. [Google Scholar]
39. Presently Australian Panels (BorgMt Gambier then Oberon particleboard plants, liquid formaldehyde concentrate, Unpublished results, Australia, since 1974. [Google Scholar]
40. Trosa, A., Pizzi, A. (1998). Industrial hardboard and other panel binders from tannin/furfuryl alcohol in absence of formaldehyde. Holz als Roh und Werkstoff, 56(3), 213–214. [Google Scholar]
41. Trosa, A., Pizzi, A. (2001). A no-aldehyde emission hardener for tannin-based wood adhesives. Holz als Roh und Werkstoff, 59(4), 266–271. [Google Scholar]
42. Pizzi, A., Mittal, K. M. (2023). Handbook of adhesive technology, 2nd editionNew York: Marcel Dekker. [Google Scholar]
43. Dunky, M. (2023). Applications and industrial implementations of naturally-based adhesives. In: Dunky, M., Mittal, K. L. (Eds.Biobased adhesives. New York: Scrivener-Wiley. [Google Scholar]
44. Abdullah, U. H. B., Pizzi, A. (2013). Tannin-Furfuryl alcohol wood panel adhesives without formaldehyde. European Journal of Wood and Wood Products, 71(1), 131–132. [Google Scholar]
45. Pizzi, A. (2019). Tannin-based biofoams–A review. Journal of Renewable Materials, 7(5), 477–492. [Google Scholar]
46. Li, X., Nicollin, A., Pizzi, A., Zhou, X., Sauget, A. et al. (2013). Natural tannin/furanic thermosetting moulding plastics. RSC (Royal Chemical Society) Advances, 3(39), 17732–17740. [Google Scholar]
47. Lagel, M. C., Pizzi, A., Basso, M. C., Abdalla, S. (2014). Development and characterisation of abrasive grinding wheels with a tannin-furanic resin matrix. Industrial Crops and Products, 65(3), 333–348. [Google Scholar]
48. Lagel, M. C., Zhang, J., Pizzi, A. (2015). Cutting and grinding wheels for angle grinders with a bioresin matrix. Industrial Crops and Products, 67, 264–269. [Google Scholar]
49. Abdullah, U. H. B., Pizzi, A., Zhou, X., Rode, K., Delmotte, L. et al. (2013). Mimosa tannin resins for impregnated paper overlays. European Journal of Wood and Wood Products, 71(2), 153–162. [Google Scholar]
50. Basso, M. C., Pizzi, A., Lacoste, C., Delmotte, L., Al-Marzouki, F. A. et al. (2014). Tannin-furanic-polyurethane foams for industrial continuous plant lines. Polymers, 6(12), 2985–3004. [Google Scholar]
Cite This Article
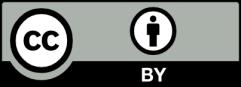