Open Access
REVIEW
Emerging Trends in Damage Tolerance Assessment: A Review of Smart Materials and Self-Repairable Structures
1 Department of Civil Engineering, Faculty of Engineering & Technology, University of Botswana, Gaborone, UB0061, Botswana
2 Department of Civil Engineering, University Kebangsaan Malaysia (UKM), Bangi, 43600, Malaysia
* Corresponding Author: Ali Akbar Firoozi. Email:
(This article belongs to the Special Issue: Health Monitoring and Rapid Evaluation of Infrastructures)
Structural Durability & Health Monitoring 2024, 18(1), 1-18. https://doi.org/10.32604/sdhm.2023.044573
Received 03 August 2023; Accepted 24 October 2023; Issue published 11 January 2024
Abstract
The discipline of damage tolerance assessment has experienced significant advancements due to the emergence of smart materials and self-repairable structures. This review offers a comprehensive look into both traditional and innovative methodologies employed in damage tolerance assessment. After a detailed exploration of damage tolerance concepts and their historical progression, the review juxtaposes the proven techniques of damage assessment with the cutting-edge innovations brought about by smart materials and self-repairable structures. The subsequent sections delve into the synergistic integration of smart materials with self-repairable structures, marking a pivotal stride in damage tolerance by establishing an autonomous system for immediate damage identification and self-repair. This holistic approach broadens the applicability of these technologies across diverse sectors yet brings forth unique challenges demanding further innovation and research. Additionally, the review examines future prospects that combine advanced manufacturing processes with data-centric methodologies, amplifying the capabilities of these ‘intelligent’ structures. The review culminates by highlighting the transformative potential of this union between smart materials and self-repairable structures, promoting a sustainable and efficient engineering paradigm.Keywords
Structural health monitoring (SHM) and damage tolerance assessment are integral facets of contemporary engineering disciplines. From aerospace and civil engineering to automotive and marine structures, the ability to accurately assess the state of structures and their resilience to damage is vital for safety, performance, and economic feasibility. The realm of damage tolerance and SHM has undergone a remarkable evolution, driven by advancements in material science, sensor technology, data processing capabilities, and modeling techniques.
Damage tolerance refers to a structure’s capacity to maintain service under predetermined loading conditions, even in the presence of defects or damage. This concept had its roots in the aeronautical industry’s drive to prevent catastrophic structural failures. Over time, our understanding and definition of damage tolerance have been refined and broadened, merging principles of fracture mechanics, and acknowledging that all practical structures operate with some level of imperfection or damage. This realization paved the way for the development of damage tolerance assessment methods, which strive to detect, monitor, and address these imperfections throughout a structure’s lifecycle [1,2].
Traditional methods for damage tolerance assessment have largely centered around non-destructive testing (NDT) techniques, including visual inspection, ultrasonic testing, and radiographic testing. These techniques have played a pivotal role in preventing structural failures by detecting damage before it reaches a critical stage. Yet, traditional NDT methods often require direct access to the inspection site, tend to react to the post-damage occurrence, and typically are limited to intermittent inspections. This creates potential gaps, allowing undetected damage propagation between checks [3].
The inherent limitations of traditional NDT prompted the exploration and adoption of more advanced SHM techniques. These modern methods prioritize continuous monitoring and real-time feedback, aiming to pinpoint and address damage as it initiates, rather than after its propagation. The integration of sensor technology, particularly fiber optic sensors and piezoelectric transducers, with machine learning and data analytics, has ushered in a new era of SHM [4,5].
Furthermore, the interplay between computational models and real-world sensor data is becoming increasingly sophisticated, enabling predictive modeling of damage growth. This holistic approach ensures not just the detection but also the projection of potential damage paths, offering a preemptive strategy to structural maintenance and repair. This has tremendous implications for industries, particularly those that manage large-scale infrastructure like bridges, dams, and skyscrapers, where the cost of failure is both financial and human [6,7].
Yet, as with all technological advancements, new challenges emerge. The sheer volume of data generated from advanced SHM systems can be overwhelming, necessitating efficient data processing techniques. Issues related to the power supply for sensors, data transmission, and the integration of heterogeneous sensor networks are still areas of active research. Moreover, while SHM provides the tools and methods for continuous monitoring, its full potential is realized only when combined with effective damage tolerance methodologies. This synergistic approach ensures that the information derived from SHM is appropriately used to assess and ensure structural safety [6,7].
In light of the above, this review aims to provide a comprehensive overview of the current state of SHM and damage tolerance methodologies, focusing on their advancements, challenges, and future prospects. Through this exploration, we seek to chart the roadmap for future research endeavors in this ever-evolving field.
2 Damage Tolerance: A Conceptual Overview
Damage tolerance is paramount to the longevity of structures, illustrating the capacity of structures to persist despite defects. This section delineates the development of the damage tolerance notion, beginning with its genesis in the aerospace sector and its evolution into other industries.
Fig. 1 underscores the pivotal role of damage tolerance in safeguarding a structure’s operational longevity. The journey commences with the emergence of initial damage, often subtle and undetected. As this damage propagates, there is a point of ‘Detectable Damage,’ marking the stage where smart materials, attuned to environmental changes, can identify irregularities. Progressing along the curve, ‘Critical Damage’ signifies a state where immediate action is warranted. Utilizing non-destructive techniques and fracture mechanics, the nature and severity of the damage are deciphered without compromising the structure. Following the assessment, the ‘Threshold of Restoration’ indicates a juncture where repair, using either traditional methods or innovative strategies like self-repairing systems, becomes imperative. Concluding the lifecycle, continuous monitoring is spotlighted, stressing that damage tolerance is a ceaseless endeavor. Collectively, the figure manifests an integrated, persistent approach to damage tolerance, quintessential for the structure’s security and prolonged service life.
Figure 1: Lifecycle of structural damage: From detection to restoration
2.1 Historical Perspectives and Evolution of the Damage Tolerance Concept
The inception of damage tolerance can be traced back to the nascent stages of aviation. During this era, unforeseen catastrophic failures, often due to material fatigue from cyclic loading, plagued aircrafts. Solutions such as the ‘safe-life’ and ‘fail-safe’ designs emerged in response. The ‘safe-life’ design banked on the hypothesis that a component starts service defect-free, an assumption often debunked. Conversely, ‘fail-safe’ incurred weight penalties due to its redundancy. The ‘damage tolerance’ paradigm evolved in the 1960s to address these shortcomings, anchored on the idea that structures should be designed to withstand inherent material defects and damage throughout their lifecycle [8,9].
2.2 Theories and Principles of Damage Tolerance Assessment
Central to damage tolerance is understanding the behavior of materials under stress. The balance between the stress-intensity factor (K) and fracture toughness (Kc) serves as the crux of most damage evaluations. It is crucial to appreciate that when K, representing the stress concentration at a crack tip, equals or surpasses Kc, failure is imminent. Such insights ensure that proactive measures can be taken before catastrophic failures occur [10].
2.3 Role of Material Properties in Damage Tolerance
Material properties undoubtedly play a pivotal role in determining the damage tolerance of any structure. But beyond the basic properties like fracture toughness and fatigue limits, it is essential to consider how environmental factors like corrosion, high temperatures, or UV radiation can impact these properties. This calls for a multi-faceted approach to damage tolerance assessments, one that integrates environmental impacts with intrinsic material behaviors [11–13]. In damage tolerance analysis, a fundamental formula known as Paris’ Law is typically utilized to predict crack growth. The law can be expressed as follows:
where:
C is a material constant, which depends on the units used.
ΔK is the stress intensity factor range.
m is another material constant, related to the specific material’s resistance to crack growth.
2.4 Non-Destructive Testing (NDT) in Damage Tolerance Assessment
While traditional NDT methods have served us well, there is an undeniable shift towards more advanced techniques. Methods like guided wave ultrasonics not only offer increased accuracy but also efficiency, ensuring faster and more reliable evaluations. Thermography, for instance, provides the advantage of being a contactless method, allowing for large-area assessments in relatively shorter times [3,14].
2.5 Damage Tolerance Analysis (DTA)
Damage Tolerance Analysis (DTA) is a process that scrutinizes a structure’s resilience against damage, harnessing the principles of fracture mechanics and material properties. Key in this procedure is the determination of critical crack size, prediction of crack growth rate, and estimation of a component’s service life expectancy [15]. Precision in the input data and underlying assumptions in computational models dictate the accuracy of DTA. Consequently, it is imperative that, where possible, DTA findings are juxtaposed against experimental tests for validation.
2.6 Integration of Damage Tolerance in Design and Manufacturing
Regulatory entities such as the Federal Aviation Administration (FAA) and the European Union Aviation Safety Agency (EASA) have established rigorous regulations centered on damage tolerance for aviation. This necessitates regular inspections, maintenance, and demonstrable damage tolerance in aircraft designs, often achieved through in-depth analysis and tests. For instance, the FAA mandates that structural safety against fatigue, corrosion, or accidental damage be ensured for the entire operational life of the aircraft [16]. This regulatory backdrop not only sets the pace for design and maintenance innovations but also underscores the importance of developing cost-effective methodologies for damage tolerance assessment.
2.7 Regulatory and Certification Aspects of Damage Tolerance
In sectors like aerospace, automotive, and nuclear, where safety is non-negotiable, damage tolerance morphs from a mere engineering parameter to a regulatory necessity. FAA and EASA, among others, enforce stringent damage tolerance criteria. The process of certification entails rigorous testing, proving the structure’s compliance with set standards. This includes defining a critical crack size and demonstrating the structure’s endurance against such damage [16]. Navigating these intricate mandates, especially in the wake of evolving materials and technological advancements, remains a complex challenge.
2.8 Evolving Techniques and Methodologies in Damage Tolerance
As industries and technologies progress, so too do the techniques and methodologies underpin damage tolerance. Modern approaches increasingly employ computational modeling and simulation tools, allowing engineers to predict potential failures and understand the interplay between materials and environmental stresses more effectively. Furthermore, with the rise of smart materials and sensors, real-time monitoring and damage assessment are becoming more accessible and accurate.
Recent literature also showcases the integration of Artificial Intelligence (AI) and Machine Learning (ML) in damage tolerance assessments, providing more refined and predictive analyses [17,18]. These technologies harness vast data sets, acquired during inspections and operations, to draw patterns and predictions that were previously difficult or impossible to discern.
2.9 Current Research Trends and Challenges in Damage Tolerance
Emerging research in damage tolerance is heavily oriented toward the integration of smart materials, real-time monitoring systems, and predictive analytics. However, challenges persist, particularly in scaling these technologies for large infrastructures and ensuring their interoperability. Balancing the cost of advanced solutions with the benefits they provide remains a key concern for industry practitioners.
2.10 Future Perspectives on Damage Tolerance
The future of damage tolerance lies in the nexus of interdisciplinary research, technology, and industry needs. As urbanization and technological advancements surge, the demand for structures with longer lifespans and minimal maintenance requirements will intensify. This calls for materials with superior damage tolerance capabilities and more sophisticated assessment tools.
The prospects of integrating nanotechnology in damage tolerance assessments are also on the horizon. By manipulating materials at the molecular level, there is potential to introduce unprecedented durability and self-repairing capabilities [19]. Such advancements would redefine the benchmarks of what is achievable in the realm of damage tolerance.
Damage tolerance, an once aerospace-centric concept, has expanded its roots across industries, emphasizing the importance of understanding, predicting, and mitigating structural failures. With the relentless evolution of materials science, engineering practices, and computational prowess, the field is set for transformative changes. However, staying abreast of these advancements, while navigating a maze of regulatory requirements, remains a challenging but crucial endeavor for industry professionals.
3 Damage Tolerance Assessment: A Comprehensive Overview of Traditional Methods
Historically, methodologies for damage tolerance assessment have emerged predominantly from disciplines such as mechanical engineering, materials science, and civil engineering. These methods aim to identify the presence of damage, gauge its severity, and forecast its potential impact on structural performance and safety. Traditional techniques for this evaluation are mainly categorized into two types: destructive NDT methods. As their names suggest, destructive methods entail procedures that cause damage to the material or structure to understand its characteristics and boundaries. On the other hand, NDT methods aim to appraise the damage tolerance of materials and structures without damaging or modifying them. Given the significance of inspecting structures that are in service and the necessity to maintain their original condition, this section will majorly spotlight NDT techniques.
3.1 A Closer Look at Traditional Non-Destructive Testing (NDT) Techniques
NDT methods are renowned across numerous sectors for damage tolerance evaluation due to their capacity to detect, pinpoint, and describe harm without causing any additional damage. This subsection presents an in-depth discussion of the primary NDT techniques adopted in damage tolerance assessments.
a) Visual Inspection: Serving as the most rudimentary yet essential NDT method, visual inspection involves a meticulous examination of a structure for indications of damage such as cracks, corrosion, wear, or leaks. While direct inspection by skilled professionals remains common, tools like borescopes, video probes, or remotely operated vehicles (ROVs) facilitate inspection in challenging or hazardous locations. Despite its simplicity and cost-efficiency, its subjective nature and dependency on the inspector’s expertise make it mainly apt for surface damage detection [3].
b) Ultrasonic Testing (UT): UT, a method capitalizing on high-frequency sound waves, allows the detection and location of flaws within materials. In essence, a transducer emits ultrasonic waves through the material, and upon encountering any inconsistency, these waves reflect back. The reflected wave pattern, when analyzed, reveals the nature and position of defects. While providing invaluable insights into the depth and dimensions of internal defects, the need for expert operators can make it less convenient for extensive structures [3].
c) Radiographic Testing (RT): RT leverages X-rays or gamma rays to peer into the internal configuration of a material or component. The radiation traverses the component, and a subsequent film or detector captures the resultant image. Any irregularities or anomalies within the material can be gleaned from the variations in radiation absorption on this image. Though providing a comprehensive internal view, it is imperative to acknowledge its use of ionizing radiation and its limitation to two-dimensional imaging [20].
d) Eddy Current Testing (ECT): Predominantly adopted for metal-based structures, ECT is effective for identifying surface and subsurface flaws. The method induces electromagnetic fields in the material, resulting in eddy currents. Discrepancies caused by defects or material property shifts can be discerned and measured. While sensitive and versatile for metals, its efficacy diminishes for deep defects and non-conductive materials [20].
To discern the apt technique for a particular assessment, comprehending the unique benefits and drawbacks of each method is crucial. Even with their efficacy, traditional methods might sometimes fall short in accuracy or applicability, especially for complex or large-scale structures.
3.2 Weighing the Pros and Cons of Traditional NDT Techniques
Each technique under the umbrella of NDT possesses a unique repertoire of strengths and challenges. Factors influencing their efficacy encompass material properties, damage to nature and position, environmental conditions, cost implications, and safety protocols. Below, we dissect the advantages and challenges associated with the previously enumerated techniques.
a) Visual Inspection Method: Advantages: The main strength of visual inspection lies in its simplicity and cost-effectiveness. It demands minimal equipment, and inspections can typically be performed swiftly, making it an ideal initial step in any damage assessment process. Visual inspection can be applied to almost any material or structure, enhancing its versatility [3].
Limitations: Despite its common use, visual inspection has considerable limitations. It only identifies surface-level damage, failing to detect internal defects. Furthermore, visual inspection is highly subjective, with results often hinging on the skill and experience of the inspector. Inconsistencies between inspectors can lead to variability in results, possibly resulting in overlooked or misidentified damage [3].
b) Ultrasonic Testing (UT) Method: Advantages: UT is valuable for detecting internal defects, a feature not commonly found in other traditional NDT methods. It provides extensive information about the location and size of defects, rendering it an effective tool for damage tolerance assessment. UT is applicable to a wide range of materials and is generally safe [3].
Limitations: The principal limitation of UT lies in its complexity. Carrying out UT requires specialized equipment and trained personnel, which can escalate costs. Additionally, the method may be less effective or even unsuitable for materials with complex geometries or coarse grain structures, as these can disrupt the propagation of ultrasonic waves [3].
c) Radiographic Testing (RT) Method: Advantages: RT can identify both internal and surface defects, providing a comprehensive overview of damage tolerance. It can yield detailed images of a component’s internal structure, proving invaluable for identifying and characterizing damage [20].
Limitations: RT involves the use of ionizing radiation, which raises significant safety concerns. These include the necessity for protective measures for operators and bystanders, as well as strict regulatory compliance. Furthermore, RT can only yield two-dimensional images, potentially limiting its capacity to detect and characterize three-dimensional or complex defects [20].
d) Eddy Current Testing (ECT) Method: Advantages: ECT is highly sensitive to minor defects and changes in material properties, making it an effective tool for detecting surface and near-surface defects. Unlike RT, ECT does not involve ionizing radiation and hence does not carry the same safety hazards. ECT can also be used for material characterization, which further enhances its utility for damage tolerance assessment [20].
Limitations: ECT is restricted to inspecting conductive materials, making it unsuitable for insulators or non-metallic materials. Additionally, the penetration depth of the eddy currents is generally limited, making ECT ineffective for detecting deep or internal defects [20].
In summary, while traditional NDT methods have significantly improved our capacity to assess damage tolerance, each method brings its unique set of strengths and limitations. These must be considered when selecting the most suitable method for a specific application. Table 1 delineates the principal strengths and limitations associated with various traditional NDT techniques. It emphasizes the importance of technique selection based on the specific application and material under examination.
3.3 Traditional NDT Methods: Versatility across Industries
NDT methods have etched their importance across a myriad of industries for damage tolerance evaluation. To cite a few examples, the aerospace sector relies heavily on techniques like visual inspection, UT, RT, and ECT to ensure aircraft structural robustness. The mainstay for these industries is the early detection and rectification facilitated by these methods, extending the life and safety of the structures [3,21].
In the oil and gas industry, visual inspection, UT, and RT are routinely employed to monitor pipelines for corrosion, cracks, and other defects that could result in leaks or failures. These methods contribute to ensuring the safety and efficiency of pipeline operations. In the manufacturing sector, these traditional NDT methods are leveraged for quality control, inspecting the integrity of raw materials, and finished products, and ensuring they conform to the necessary standards and specifications [3,22].
3.4 Peering into the Future: Prospects and Predicaments
While the merits of traditional NDT techniques are undeniable, the quest for perfection pushes the boundaries of research into addressing their existing limitations. Complexity in material and design poses challenges, and the dependency on human expertise for data collation and interpretation beckons for automation. Incorporating technologies like artificial intelligence (AI) into NDT can revolutionize data analysis, making it more nuanced and reliable. Merging traditional techniques with real-time structural health monitoring (SHM) systems might be the future of holistic, continuous structural surveillance [23].
Another critical research domain is the integration of traditional NDT methods with other burgeoning technologies, such as artificial intelligence (AI) and machine learning. AI and machine learning could potentially augment the analysis and interpretation of data collected via NDT methods, enabling the detection of more nuanced or complex patterns of damage, and leading to more accurate and reliable assessments. The future of damage tolerance assessment also lies in the exploration of more holistic strategies that integrate traditional NDT methods with structural health monitoring (SHM) systems. Such integrated strategies can provide real-time, continuous surveillance of structures, enhancing our ability to detect and mitigate damage before it compromises structural integrity [14,23].
The transition towards smart materials and self-healing structures signifies a significant evolution in the field of damage tolerance assessment, offering thrilling new possibilities for enhancing structural durability and reliability. However, as with any novel technology, there are new challenges to tackle and unanswered questions to investigate. Table 2 provides a comparative overview of conventional and emerging approaches to damage tolerance assessment. The ‘Cost’ represents the financial expenditure associated with the approach. ‘Complexity’ refers to the difficulty in the implementation and maintenance of the method. ‘Reliability’ indicates the trustworthiness of the method in accurately detecting and assessing damage. ‘Response Time’ signifies the speed at which the method can detect and respond to damage. ‘Applicability’ refers to the variety of scenarios or structures where the method can be effectively implemented. ‘Autonomous Response’ suggests the method’s ability to respond to damage without external intervention.
Fig. 2 offers a comprehensive illustration of how smart materials and self-healing hollow fibers collaborate to maintain structural integrity. The figure is split into two main panels. The first panel highlights the role of smart materials, specifically emphasizing their ability to detect damage. This could be represented by a piezoelectric material that morphs its shape in response to an applied electric field. In the scenario of damage detection, any alterations in the electric field within the smart material, induced by stress-related damage, could signal the existence of a potential structural flaw. The second panel of the figure underlines the function of self-healing hollow fibers. These fibers could be depicted as being embedded within a structure, loaded with a healing agent. When a crack forms and reaches these hollow fibers, it triggers their rupture, leading to the release of the healing agent. This healing agent then interacts with the surrounding material to ‘heal’ or seal the crack, effectively restoring the structural integrity. In summary, Fig. 2 provides a fascinating exploration of the cutting-edge technology of smart materials and self-healing hollow fibers. It elucidates their individual roles and their combined potential in guaranteeing the endurance and durability of structures.
Figure 2: Working mechanism of smart materials and self-repairable hollow fibers, CC BY-NC 4.0 license [21]
In a nutshell, this comprehensive overview underscores the enduring relevance of traditional NDT techniques, their evolution, and the frontier areas awaiting exploration.
4 Smart Materials: The Next Frontier in Damage Tolerance Assessment
Over the recent decades, we have observed an impressive rise in research and development focused on smart materials. These are materials characterized by their ability to adaptively alter their properties in response to external stimuli such as temperature, pressure, light, and electric or magnetic fields [24]. This unique adaptability allows them to dynamically engage with their surroundings, which holds myriad application potentials. Specifically, in the realm of damage tolerance assessment, smart materials usher in a new era. With the capability of embedding sensors or actuators into the very fabric of a structure, there is the potential to craft structures that can not only self-monitor their health but also proactively respond to damage, enhancing both resilience and longevity.
4.1 Piezoelectric Materials: Turning Stress into Signals
Piezoelectric materials are distinguished by their capacity to generate an electric charge in response to mechanical stress. Such a property has notable implications for sensing applications [22]. As the material deforms, it produces a charge, a measurable signal which conveys valuable data about the forces the material experiences. This characteristic has marked piezoelectric materials as prime candidates for structural health monitoring. Evidence of its promise is abundant. For instance, Li et al. [23] harnessed piezoelectric materials to establish a structural health monitoring system for wind turbine blades, revealing its aptitude for detecting issues such as delamination.
4.2 Shape Memory Alloys: Remembering and Recovering
Shape Memory Alloys (SMAs) are a novel breed of smart materials renowned for their ability to return to their original form after deformation. This transition can be instigated by specific triggers, like heat. Such a trait finds profound applications in damage tolerance assessment and restoration. The premise is simple yet revolutionary. Damage is detected, prompting a heat trigger that prompts SMAs to revert, sealing cracks or defects [25,26]. SMAs in the landscape of damage tolerance assessment remains a burgeoning research area, with studies like Rao et al. [27] spotlighting the alloy’s potential in self-repairing metallic structures.
4.3 Self-Healing Materials: Autonomy in Recovery
Emerging into the spotlight are self-healing materials, designed to repair autonomously post-damage without external intervention. The fundamental mechanism propelling this innovation is the infusion of a healing agent that reacts or solidifies to mend the damage. Such a leap not only propels damage tolerance capabilities but also reshapes maintenance dynamics. Instead of intensive repair, we witness real-time restoration, amplifying structural lifespan. Researchers are experimenting with capsule-based systems and vascular systems to channel the healing agent [28], painting a future where durability and self-repair coalesce seamlessly.
4.4 Nanocomposites: Nanoscale Solutions for Macro Challenges
Nanocomposites, infused with components of nanometric dimensions, are showing immense promise in damage tolerance assessment. Their enhanced mechanical, thermal, and electrical properties create avenues for embedding sensors directly into structural materials. Carbon nanotubes (CNTs) stand out, especially with their unique electrical properties changing in alignment with structural damage, enabling non-invasive damage monitoring [29,30]. Additionally, through the integration of nanoparticles, materials can be endowed with self-sensing capabilities, as seen in the work of D’Alessandro et al. [31].
4.5 Smart Materials: Charting the Path Forward
The confluence of smart materials and damage tolerance assessment marks a transformative shift from conventional techniques. The potential now exists for real-time, autonomous structures that can sense and heal themselves, fundamentally redefining our perceptions of structural resilience.
Nevertheless, challenges persist. Questions on the long-term reliability of these materials, scalable production, and integration need addressing. Furthermore, the data they produce mandates the creation of advanced analysis algorithms, hinting at a possible synergy with machine learning. As we navigate these challenges, smart materials stand poised to reshape the future of damage tolerance assessment, crafting structures that are not only durable but also intuitive to damage.
5 Self-Repairable Structures: Concepts and Applications
The idea of self-healing or self-repairable structures has garnered substantial interest over recent years due to their potential to enhance material longevity and reduce maintenance costs. Drawing inspiration from biological entities that mend their own wounds, self-repairable structures are designed to autonomously repair damage, restoring their original functionality, and obviating the need for external interventions. The self-repair mechanisms embedded within these materials can be activated when damage is detected, ensuring minor damages do not escalate into major structural problems [32].
Self-repairable structures utilize a variety of methods, encompassing microencapsulation, vascular networks, and intrinsic material properties. The integration of smart materials can further offer concurrent sensing and repair capabilities. In the upcoming subsections, we will provide a comprehensive overview of these mechanisms and their diverse applications.
The design of self-repairable structures often involves the inclusion of a healing agent in the material matrix. When the material sustains damage, this agent is released into the cracks and subsequently solidifies to restore the material’s original state [28]. The primary techniques to embed these healing agents include microencapsulation and vascular networks:
a) Microencapsulation: This process involves encasing healing agents in tiny capsules scattered throughout the material. If the material gets damaged or cracked, these capsules break open, releasing the healing agent. This agent then interacts with the material or a separate catalyst to mend the damage. This strategy has been adopted successfully in polymers, concrete, and metals [33].
b) Vascular Networks: Mirroring the circulatory systems of living organisms, this method consists of creating network-like channels within the material. These channels, loaded with healing agents, supply the agent to the damaged site when cracks form. Vascular networks offer a key advantage over microencapsulation: they allow for repeated healing events since the network can be replenished [34].
c) Intrinsic Material-Based Self-Healing: Beyond the previously mentioned methods, intrinsic self-healing mechanisms are also actively researched. This approach taps into the inherent characteristics of materials, enabling them to self-repair without external agents. While thermoset polymers have showcased this capability by undergoing reversible polymerization processes, certain metals and ceramics also exhibit such traits. These materials can naturally rearrange their structures upon damage, sealing cracks and regaining their integrity [35].
5.2 Applications of Self-Repairable Structures
From aerospace to civil infrastructure, self-repairable structures find applications in various domains. In the aerospace sector, integrating self-healing composites can amplify aircraft safety and lifespan. Often, aircraft damages are subtle and situated in hard-to-access areas, becoming evident only when they exacerbate. Embedding self-healing mechanisms can prompt autonomous repairs, ensuring continuous structural integrity. Furthermore, in the medical sector, self-repairable materials show promise in biocompatible implants, enhancing their safety and longevity. These materials can mend minor damages autonomously, reducing the risks associated with implant failures.
For civil infrastructure, self-healing concrete promises extended structural lifespans and diminished maintenance expenditures. Integrating healing agents directly into the concrete allows cracks to be automatically repaired, safeguarding the structure’s durability, and thwarting further degradation [36].
In electronics, materials with self-repair capabilities can augment device durability and performance. Recent advancements have led to the creation of electronic circuits that can self-repair, restoring electrical connectivity after damages [37].
5.3 Integration of Smart Materials and Self-Repairable Structures
Merging the capabilities of smart materials with self-repairable structures heralds a new era in damage resilience. Such composite materials can simultaneously detect and respond to damage, maximizing longevity and functionality. Especially critical for industries such as aerospace, civil infrastructure, and electronics, these combined features can immensely improve system reliability [38].
One notable instance of this synergy is the development of self-healing polymers integrated with piezoelectric particles. These particles, when under mechanical stress, generate electrical charges, acting as early warning systems for damage detection. Upon identification of damage, the self-repair process can be immediately triggered, ensuring timely and efficient response [39].
Regarding concrete structures, amalgamating self-repair mechanisms with smart sensors can revolutionize structural durability. Consider, for example, a smart concrete blend enriched with carbon fibers. This composite can self-monitor due to variations in electrical conductivity arising from stress or damage. Concurrently, embedding bacterial spores provides the concrete with self-healing properties. When these spores encounter water and oxygen, they produce limestone, autonomously sealing cracks and enhancing the structural solidity [40,41].
5.4 Challenges and Future Perspectives
Despite the myriad advantages they offer, combining smart materials with self-repairable structures introduces certain complexities. Chief among these is the harmonious integration of both capabilities without compromising the individual efficacy of each. The manufacturing process can be intricate due to the meticulous integration of healing agents or smart components into the material matrix. Moreover, concerns linger about the long-term performance of these hybrid systems. Extreme operational environments might diminish the efficacy of repair mechanisms or hamper the sensing capabilities, potentially curtailing the benefits of these materials [28].
Forward-looking research must focus on these challenges, seeking novel materials and cutting-edge techniques to enhance the efficiency, longevity, and economic viability of integrated systems. Exploring synergies between distinct self-healing mechanisms or combining multiple sensing modalities might yield promising results. As the field progresses, leveraging advanced computational modeling and machine learning can be instrumental. Such tools can fine-tune the design and functionality of these avant-garde structures, setting the stage for a future adorned with resilient and self-sustaining infrastructures.
6 Synergy between Smart Materials and Self-Repairable Structures
The symbiosis of smart materials and self-repairable structures is nothing short of a landmark evolution in the realm of damage tolerance assessment. By bridging the responsive properties of smart materials with the innate repair capabilities of self-repairable structures, we have ushered in a new generation of ‘intelligent’ infrastructures. These structures possess the ability to independently perceive, adapt to, and remediate damages in real time. This inevitably ensures an extension in their functional lifespan, while bolstering safety levels. In this section, we dive deeper into the improvements this integration brings to damage detection and recovery, its widened application scope, the challenges it grapples with, and prospects for the future.
Fig. 3 offers a clear representation of the two primary configurations wherein smart materials can be harnessed: sensoric and actuatoric. Panel (a) showcases the sensoric setup of a smart material. Here, under the influence of mechanical forces, there is a transformation in the non-mechanical attributes (like chemical or physical properties) of the material. This is evident when materials, subjected to mechanical duress, undergo detectable property changes. A quintessential example is the generation of electric charges in piezoelectric entities. This intrinsic feature allows these materials to function as sensors, detecting shifts or damages in structures through constant property monitoring.
Figure 3: Functional dualities of smart materials: Sensing vs. actuation modes
Panel (b) of Fig. 3 throws light on the actuatoric setup. In this setup, the smart material responds to a non-mechanical stimulus, such as temperature shifts or light exposure, by undergoing deformation. A shape-memory alloy, which alters its form in response to temperature variations, serves as an apt illustration. This unique trait facilitates the use of smart materials as actuators, initiating specific actions in response to external stimuli. Collectively, Fig. 3 efficiently maps out the distinct, yet supplementary configurations of smart materials, shedding light on their dual roles as sensors and actuators, and their subsequent implications for structural health monitoring and damage tolerance appraisal.
6.1 Enhanced Damage Detection and Healing
Marrying the worlds of smart materials and self-repairable structures has undeniably made strides in damage tolerance assessment. When the sensing capabilities of smart materials (be it fluctuations in electrical resistance, piezoelectric reactions, or optical changes) are aligned with the self-repair mechanisms intrinsic to self-repairable structures, the resultant system emerges as a robust entity. It is a system proficient at recognizing and instantaneously addressing damages [42].
A case in point is the integration of carbon nanotubes (CNTs) into a self-healing polymer matrix. Known for their exceptional electrical attributes, CNTs exhibit resistance changes under mechanical stress, enabling micro-damage detection. Simultaneously, the embedded microcapsules within the polymer matrix can release healing agents, rejuvenating the material’s integrity upon damage detection [43].
6.2 Broadened Application Scenarios
By pairing smart materials with self-repairable structures, their applicative range has broadened remarkably. Consider the domain of space engineering. Smart sensors, combined with self-repairable structures, can tackle challenges stemming from space debris collisions or micrometeoroid-induced damages. These self-sustaining systems promise the continuous operational reliability of spacecraft during extended space missions. In the energy sector, amalgamation can birth smart self-repairing photovoltaic panels. These panels, by autonomously mending micro-cracks induced by environmental stimuli, can maintain optimum performance over extended durations. Such resilience enhances their lifespan and economic efficiency, making them robust candidates for sustainable energy harvesting [44,45].
6.3 Challenges and Future Perspectives
Despite their potential, marrying smart materials with self-repairable structures is not devoid of challenges. Technically speaking, crafting such integrated systems, especially embedding sensors or actuators within a self-healing matrix, is a complex feat demanding the utmost precision. Further, ensuring the enduring stability and dependable performance of these composite systems under diverse environmental and operational conditions emerges as a significant hurdle. Presently, there is an evident lack of standardized testing and validation protocols to authenticate the efficiency and reliability of these intertwined systems in tangible scenarios. Additionally, economic barriers, predominantly the elevated costs associated with smart materials and self-healing agents, could impede their broad-scale adoption [46].
However, the horizon is ripe with research opportunities and innovations. The introduction of progressive manufacturing techniques, like 3D printing and nanotechnology, herald new avenues for the design and realization of these integrated structures. Concurrently, harnessing data-driven methodologies, such as machine learning and artificial intelligence, can be pivotal in amplifying the system’s efficacy. These platforms, by processing and deciphering the vast data streams generated by smart sensors, can facilitate swifter and more precise damage identification and recovery responses [47,48].
The incessant advancements in materials science and engineering have birthed an era resonating with the brilliance of smart materials and self-repairable structures. While both these technologies are commendable in their individual capacities, their union elevates the damage tolerance assessment paradigm. While challenges persist, the horizon looks promising, filled with avenues for innovation in design, fabrication, and system optimization. As the domain matures, transcending existing limitations, the fusion of smart materials with self-repairable structures is poised to significantly boost the resilience, safety, and performance of engineering structures, propelling them closer to genuine ‘intelligence’.
Table 3 delineated below, encapsulates the prime challenges and prospective solutions tied to the synergy of smart materials and self-repairable structures. While the ‘Challenges’ column elucidates the prevalent roadblocks in this arena, the ‘Future Perspectives’ column articulates potential solutions or areas of research that might address these impediments.
In conclusion, the alliance between smart materials and self-repairable structures offers a dynamic avenue to reimagine and redefine damage tolerance in modern engineering. By integrating the sensing prowess of smart materials with the repair mechanisms of self-repairable structures, we pave the way for structures that are not only durable but also adaptive. The journey, while filled with technical and economic challenges, promises significant advancements that could redefine the benchmarks of safety and efficiency in engineering designs. As we continue to research and innovate in this domain, we remain hopeful and excited about the boundless possibilities this synergy presents.
In the vast domain of engineering and materials science, damage tolerance stands as an ever-adapting cornerstone, meeting the requirements of diverse industries. Originating from its inception in the aviation sector, this concept has extended its relevance to civil infrastructures, biomedical domains, and myriad other sectors, emphasizing the lastingness, safety, and reliability of engineered constructs.
• Traditional techniques of assessing damage tolerance, encompassing aspects like fracture mechanics, non-destructive evaluation, and structural health monitoring, have been instrumental. These foundational methods have endowed engineers with robust tools for foreseeing, pinpointing, and addressing damage. Yet, as the engineering realm incessantly seeks enhanced outcomes in terms of performance, resilience, and efficiency, the urge for pioneering solutions intensifies.
• With the introduction of smart materials and the concept of self-repairable structures, a bright horizon in this domain emerges. Smart materials, distinguished by their ability to react to environmental changes, function as intrinsic sensors within structures, providing instantaneous feedback on structural well-being and robustness. In parallel, self-repairable designs offer the capability to self-correct identified impairments, enriching their endurance and functional longevity.
• The convergence of these avant-garde technologies signifies a transformative shift in damage tolerance assessment-evolving into a system proficient in both discerning and rectifying damage promptly. Such frameworks showcase an adeptness and ‘intelligence’ hitherto unmatched by traditional avenues.
• However, the path to fully leveraging the combined might of these innovations presents intricate hurdles. Concerns encompassing manufacturing accuracy, enduring reliability, validation frameworks, and economic viability are forefront. Yet, these hurdles simultaneously spotlight arenas ripe for innovative strides, driven by breakthroughs in fabrication methodologies, computational prowess, and data-centric strategies.
In the advancing trajectory of this discipline, it is projected that the harmonious fusion of smart materials with self-repairable architectures will profoundly amplify the essence of damage tolerance, redefining existing limits. This evolution promises not just to elevate the efficacy and safety of engineered constructs but also to pave the way for a more resilient and optimized engineering panorama.
Acknowledgement: The authors would like to extend their sincere gratitude to the Department of Civil Engineering, Faculty of Engineering & Technology, University of Botswana, and the Department of Civil Engineering, University Kebangsaan Malaysia (UKM) for their continued support and for providing the necessary resources required for this study. Special thanks are also extended to all colleagues and peers who provided valuable insights and critiques that significantly improved the quality of this manuscript.
Funding Statement: This research received no specific grant from any funding agency in the public, commercial, or not-for-profit sectors.
Author Contributions: The manuscript titled “Emerging Trends in Damage Tolerance Assessment: A Review of Smart Materials and Self-Repairable Structures” was collaboratively developed by both authors. Dr. Ali Akbar Firoozi, the corresponding author, conceptualized and designed the study. He carried out an extensive literature review, identified relevant studies, and extracted significant findings. He was responsible for the drafting of the manuscript and made critical revisions related to the content. Dr. Ali Asghar Firoozi contributed to the analysis and interpretation of the literature data. He provided significant feedback and played a crucial role in shaping the manuscript. He also revised the manuscript critically for important intellectual content. Both authors read and approved the final version of the manuscript to be published, and agreed to be accountable for all aspects of the work in ensuring that questions related to any part of the work are appropriately investigated and resolved.
Availability of Data and Materials: The data used and/or analyzed during the current study are available from the corresponding author upon reasonable request. However, due to privacy and ethical restrictions.
Conflicts of Interest: The authors declare that they have no conflicts of interest to report regarding the present study.
References
1. Argatov, I. (2019). Artificial neural networks (ANNs) as a novel modeling technique in tribology. Frontiers in Mechanical Engineering, 5, 30. https://doi.org/10.3389/fmech.2019.00030 [Google Scholar] [CrossRef]
2. Khaleghi, M., Haghighat, E., Vahab, M., Shahbodagh, B., Khalili, N. (2022). Fracture characterization from noisy displacement data using artificial neural networks. Engineering Fracture Mechanics, 271, 108649. https://doi.org/10.1016/j.engfracmech.2022.108649 [Google Scholar] [CrossRef]
3. Ida, N., Meyendorf, N. (2019). Handbook of advanced nondestructive evaluation. Cham, Switzerland: Springer International Publishing. [Google Scholar]
4. Kot, P., Muradov, M., Gkantou, M., Kamaris, G. S., Hashim, K. et al. (2021). Recent advancements in non-destructive testing techniques for structural health monitoring. Applied Sciences, 11(6), 2750. https://doi.org/10.3390/app11062750 [Google Scholar] [CrossRef]
5. Chen, H., Nie, X., Gan, S., Zhao, Y., Qiu, H. (2021). Interfacial imperfection detection for steel-concrete composite structures using NDT techniques: A state-of-the-art review. Engineering Structures, 245, 112778. https://doi.org/10.1016/j.engstruct.2021.112778 [Google Scholar] [CrossRef]
6. Dang, H. V., Tatipamula, M., Nguyen, H. X. (2021). Cloud-based digital twinning for structural health monitoring using deep learning. IEEE Transactions on Industrial Informatics, 18(6), 3820–3830. https://doi.org/10.1109/TII.2021.3115119 [Google Scholar] [CrossRef]
7. Górriz, J. M., Ramírez, J., Ortíz, A., Martinez-Murcia, F. J., Segovia, F. et al. (2020). Artificial intelligence within the interplay between natural and artificial computation: Advances in data science, trends and applications. Neurocomputing, 410, 237–270. https://doi.org/10.1016/j.neucom.2020.05.078 [Google Scholar] [CrossRef]
8. Pascoe, J. A. (2021). Slow-growth damage tolerance for fatigue after impact in FRP composites: Why current research won’t get us there. Theoretical and Applied Fracture Mechanics, 116, 103127. https://doi.org/10.1016/j.tafmec.2021.103127 [Google Scholar] [CrossRef]
9. Yao, W., Xia, K. (2019). Dynamic notched semi-circle bend (NSCB) method for measuring fracture properties of rocks: Fundamentals and applications. Journal of Rock Mechanics and Geotechnical Engineering, 11(5), 1066–1093. https://doi.org/10.1016/j.jrmge.2019.03.003 [Google Scholar] [CrossRef]
10. Xiang, C., Wang, Z., Yang, C., Yao, X., Wang, Y. et al. (2020). Stretchable and fatigue-resistant materials. Materials Today, 34, 7–16. https://doi.org/10.1016/j.mattod.2019.08.009 [Google Scholar] [CrossRef]
11. Hertzberg, R. W., Vinci, R. P., Hertzberg, J. L. (2020). Deformation and fracture mechanics of engineering materials. Hoboken, NJ: John Wiley & Sons. [Google Scholar]
12. Bao, Y., Li, H. (2021). Machine learning paradigm for structural health monitoring. Structural Health Monitoring, 20(4), 1353–1372. https://doi.org/10.1177/1475921720972416 [Google Scholar] [CrossRef]
13. Zabrady, K., Li, A. W., Doherty, A. J. (2023). Mechanism of primer synthesis by primase-polymerases. Current Opinion in Structural Biology, 82, 102652. https://doi.org/10.1016/j.sbi.2023.102652 [Google Scholar] [PubMed] [CrossRef]
14. Shittu, A. A., Mehmanparast, A., Shafiee, M., Kolios, A., Hart, P. et al. (2020). Structural reliability assessment of offshore wind turbine support structures subjected to pitting corrosion-fatigue: A damage tolerance modelling approach. Wind Energy, 23(11), 2004–2026. https://doi.org/10.1002/we.2542 [Google Scholar] [CrossRef]
15. Ram Mohan, M. P., Gopakumar, K. V., Smith, T. (2020). Nuclear energy safety, regulatory independence, and judicial deference: The case of the atomic energy regulatory board of India. Administration & Society, 52(7), 1009–1037. https://doi.org/10.1177/0095399719882640 [Google Scholar] [CrossRef]
16. Vavilov, V., Burleigh, D. (2020). Infrared thermography and thermal nondestructive testing. New York, NY, USA: Springer International Publishing. https://doi.org/10.1007/978-3-030-48002-8 [Google Scholar] [CrossRef]
17. Zhang, J., Zhu, J., Guo, W., Guo, W. (2022). A machine learning-based approach to predict the fatigue life of three-dimensional cracked specimens. International Journal of Fatigue, 159, 106808. https://doi.org/10.1016/j.ijfatigue.2022.106808 [Google Scholar] [CrossRef]
18. Tabatabaeian, A., Jerkovic, B., Harrison, P., Marchiori, E., Fotouhi, M. (2023). Barely visible impact damage detection in composite structures using deep learning networks with varying complexities. Composites Part B: Engineering, 264, 110907. https://doi.org/10.1016/j.compositesb.2023.110907 [Google Scholar] [CrossRef]
19. Ma, Y., Rong, H., Zhang, Y., Lu, X. (2023). A self-repairing transparent film with reprocessable, ultra-high strength and outstanding elasticity based on interlocking hydrogen bonds and reversible topological networks. Chemical Engineering Journal, 456, 141137. https://doi.org/10.1016/j.cej.2022.141137 [Google Scholar] [CrossRef]
20. Mishra, M., Bhatia, A. S., Maity, D. (2019). Support vector machine for determining the compressive strength of brick-mortar masonry using NDT data fusion (case study: Kharagpur, India). SN Applied Sciences, 1(6), 564. https://doi.org/10.1007/s42452-019-0590-5 [Google Scholar] [CrossRef]
21. Shah, K. W., Huseien, G. F. (2020). Biomimetic self-healing cementitious construction materials for smart buildings. Biomimetics, 5(4), 47. https://doi.org/10.3390/biomimetics5040047 [Google Scholar] [PubMed] [CrossRef]
22. Lu, F., Liu, Y., Chen, W., Deng, J., Li, K. et al. (2022). Radial disturbance compensation device of cylindrical cantilever beam using embedded piezoelectric ceramics with bending mode. Mechanical Systems and Signal Processing, 172, 109009. https://doi.org/10.1016/j.ymssp.2022.109009 [Google Scholar] [CrossRef]
23. Li, Y., Feng, W., Meng, L., Tse, K. M., Li, Z. et al. (2021). Investigation on in-situ sprayed, annealed and corona poled PVDF-TrFE coatings for guided wave-based structural health monitoring: From crystallization to piezoelectricity. Materials & Design, 199, 109415. https://doi.org/10.1016/j.matdes.2020.109415 [Google Scholar] [CrossRef]
24. Piorunek, D., Frenzel, J., Jöns, N., Somsen, C., Eggeler, G. (2020). Chemical complexity, microstructure and martensitic transformation in high entropy shape memory alloys. Intermetallics, 122, 106792. https://doi.org/10.1016/j.intermet.2020.106792 [Google Scholar] [CrossRef]
25. Akbar, I., El Hadrouz, M., El Mansori, M., Lagoudas, D. (2022). Toward enabling manufacturing paradigm of 4D printing of shape memory materials: Open literature review. European Polymer Journal, 168, 111106. https://doi.org/10.1016/j.eurpolymj.2022.111106 [Google Scholar] [CrossRef]
26. Tabrizikahou, A., Kuczma, M., Łasecka-Plura, M., Farsangi, E. N., Noori, M. et al. (2022). Application and modelling of shape-memory alloys for structural vibration control: State-of-the-art review. Construction and Building Materials, 342, 127975. https://doi.org/10.1016/j.conbuildmat.2022.127975 [Google Scholar] [CrossRef]
27. Rao, Z., Wang, X., Leng, J., Yan, Z., Yan, X. (2022). Design methodology of the Ni50Ti50 shape memory alloy beam actuator: Heat treatment, training and numerical simulation. Materials & Design, 217, 110615. https://doi.org/10.1016/j.matdes.2022.110615 [Google Scholar] [CrossRef]
28. Ramesh, M., Ramnath, R. A., Khan, A., Khan, A. A. P., Asiri, A. M. (2020). Electrically conductive self-healing materials: Preparation, properties, and applications. In: Self-healing composite materials, pp. 1–13. Cambridge, UK: Woodhead Publishing. https://doi.org/10.1016/B978-0-12-817354-1.00001-6 [Google Scholar] [CrossRef]
29. Han, Y., Shi, X., Yang, X., Guo, Y., Zhang, J. et al. (2020). Enhanced thermal conductivities of epoxy nanocomposites via incorporating in-situ fabricated hetero-structured SiC-BNNS fillers. Composites Science and Technology, 187, 107944. https://doi.org/10.1016/j.compscitech.2019.107944 [Google Scholar] [CrossRef]
30. Wang, H., Zhou, R., Li, D., Zhang, L., Ren, G. et al. (2021). High-performance foam-shaped strain sensor based on carbon nanotubes and Ti3C2Tx MXene for the monitoring of human activities. ACS Nano, 15(6), 9690–9700. https://doi.org/10.1021/acsnano.1c00259 [Google Scholar] [PubMed] [CrossRef]
31. D’Alessandro, A., Ubertini, F., Laflamme, S., Materazzi, A. L. (2019). Towards smart concrete for smart cities: Recent results and future application of strain-sensing nanocomposites. Journal of Smart Cities, 1(1), 3–14. https://doi.org/10.18063/JSC.2015.01.002 [Google Scholar] [CrossRef]
32. Musala, S., Neelam, A. K., Sreenivasulu, V., Vardhan, B., K., V. (2022). Concurrent error detectable and self-repairable carry select adder. International Journal of Electronics, 109(11), 1954–1972. https://doi.org/10.1080/00207217.2021.2001862 [Google Scholar] [CrossRef]
33. Brown, E. N., Kessler, M. R., Sottos, N. R., White, S. R. (2003). In situ poly(urea-formaldehyde) microencapsulation of dicyclopentadiene. Journal of Microencapsulation, 20(6), 719–730. https://doi.org/10.3109/02652040309178083 [Google Scholar] [CrossRef]
34. Wen, N., Song, T., Ji, Z., Jiang, D., Wu, Z. et al. (2021). Recent advancements in self-healing materials: Mechanicals, performances and features. Reactive and Functional Polymers, 168, 105041. https://doi.org/10.1016/j.reactfunctpolym.2021.105041 [Google Scholar] [CrossRef]
35. Kosarli, M., Bekas, D., Tsirka, K., Paipetis, A. S. (2020). Capsule-based self-healing polymers and composites. In: Thomas, S., Surendran, A. (Eds.Self-healing polymer-based systems, pp. 259–278. Amsterdam, Netherlands: Elsevier. https://doi.org/10.1016/B978-0-12-818450-9.00010-6 [Google Scholar] [CrossRef]
36. Anglani, G., Tulliani, J. M., Antonaci, P. (2020). Behaviour of pre-cracked self-healing cementitious materials under static and cyclic loading. Materials, 13(5), 1149. https://doi.org/10.3390/ma13051149 [Google Scholar] [PubMed] [CrossRef]
37. Kim, D. H., Lee, H. E., You, B. K., Cho, S. B., Mishra, R. et al. (2019). Flexible crossbar-structured phase change memory array via mo-based interfacial physical lift-off. Advanced Functional Materials, 29(6), 1806338. https://doi.org/10.1002/adfm.201806338 [Google Scholar] [CrossRef]
38. Gonzalez-Torre, I., Norambuena-Contreras, J. (2020). Recent advances on self-healing of bituminous materials by the action of encapsulated rejuvenators. Construction and Building Materials, 258, 119568. https://doi.org/10.1016/j.conbuildmat.2020.119568 [Google Scholar] [CrossRef]
39. Yang, M., Liu, J., Liu, D., Jiao, J., Cui, N. et al. (2021). A fully self-healing piezoelectric nanogenerator for self-powered pressure sensing electronic skin. Research, 2021, 9793458. https://doi.org/10.34133/2021/9793458 [Google Scholar] [PubMed] [CrossRef]
40. Aygun, B. F., Bastan, Z., Bilir, T. (2023). Review and outlook of self-sensing, self-healing, piezoelectric pozzolans, and piezoelectric fibers in “smart” engineered cementitious composites (ECC). Iranian Journal of Science and Technology, Transactions of Civil Engineering, 47(2), 639–662. https://doi.org/10.1007/s40996-022-00924-8 [Google Scholar] [CrossRef]
41. Jogi, P. K., Lakshmi, T. V. (2021). Self healing concrete based on different bacteria: A review. Materials Today: Proceedings, 43, 1246–1252. https://doi.org/10.1016/j.matpr.2020.08.765 [Google Scholar] [CrossRef]
42. Foorginezhad, S., Mohseni-Dargah, M., Falahati, Z., Abbassi, R., Razmjou, A. et al. (2021). Sensing advancement towards safety assessment of hydrogen fuel cell vehicles. Journal of Power Sources, 489, 229450. https://doi.org/10.1016/j.jpowsour.2021.229450 [Google Scholar] [CrossRef]
43. Shumuye, E. D., Li, W., Liu, J., Wang, Z., Yu, J. et al. (2022). Self-healing recovery and micro-structural properties of slag/fly-ash based engineered cementitious composites under chloride environment and tidal exposure. Cement and Concrete Composites, 134, 104789. https://doi.org/10.1016/j.cemconcomp.2022.104789 [Google Scholar] [CrossRef]
44. Wu, W., Hu, W., Qian, G., Liao, H., Xu, X. et al. (2019). Mechanical design and multifunctional applications of chiral mechanical metamaterials: A review. Materials & Design, 180, 107950. https://doi.org/10.1016/j.matdes.2019.107950 [Google Scholar] [CrossRef]
45. Sam, E. K., Sam, D. K., Lv, X., Liu, B., Xiao, X. et al. (2019). Recent development in the fabrication of self-healing superhydrophobic surfaces. Chemical Engineering Journal, 373, 531–546. https://doi.org/10.1016/j.cej.2019.05.077 [Google Scholar] [CrossRef]
46. Cyriac, S. L., Bindhu, B., Midhun, C. V., Musthafa, M. M. (2021). Emerging trends in nano structured silicon detectors for neutron spectroscopy. Silicon, 14, 1–7. https://doi.org/10.1007/s12633-021-00961-4 [Google Scholar] [CrossRef]
47. Tahir, D., Zhang, M., Hu, H. (2022). Auxetic materials for personal protection: A review. Physica Status Solidi (B), 259(12), 2200324. https://doi.org/10.1002/pssb.202200324 [Google Scholar] [CrossRef]
48. Gordan, M., Sabbagh-Yazdi, S. R., Ismail, Z., Ghaedi, K., Carroll, P. et al. (2022). State-of-the-art review on advancements of data mining in structural health monitoring. Measurement, 193, 110939. https://doi.org/10.1016/j.measurement.2022.110939 [Google Scholar] [CrossRef]
Cite This Article
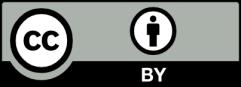