Open Access
ARTICLE
Parametric Optimization of Wheel Spoke Structure for Drag Reduction of an Ahmed Body
1 Institute of Electrical and Information Engineering, Zhenjiang College, Zhenjiang, 212028, China
2 School of Automotive and Traffic Engineering, Jiangsu University, Zhenjiang, 212013, China
* Corresponding Author: Haichao Zhou. Email:
(This article belongs to the Special Issue: Computer Modeling in Vehicle Aerodynamics)
Computer Modeling in Engineering & Sciences 2024, 139(1), 955-975. https://doi.org/10.32604/cmes.2023.043322
Received 29 June 2023; Accepted 20 September 2023; Issue published 30 December 2023
Abstract
The wheels have a considerable influence on the aerodynamic properties and can contribute up to 25% of the total drag on modern vehicles. In this study, the effect of the wheel spoke structure on the aerodynamic performance of the isolated wheel is investigated. Subsequently, the 35° Ahmed body with an optimized spoke structure is used to analyze the flow behavior and the mechanism of drag reduction. The Fluent software is employed for this investigation, with an inlet velocity of 40 m/s. The accuracy of the numerical study is validated by comparing it with experimental results obtained from the classical Ahmed model. To gain a clearer understanding of the effects of the wheel spoke parameters on the aerodynamics of both the wheel and Ahmed model, and five design variables are proposed: the fillet angle α, the inside arc radius R1, the outside radius R2, and the same length of the chord L1 and L2. These variables characterize the wheel spoke structure. The Optimal Latin Hypercube design method is utilized to conduct the experimental design. Based on the simulation results of various wheel spoke designs, the Kriging model and the adaptive simulated annealing algorithm is selected to optimize the design parameters. The objective is to achieve the best combination for maximum drag reduction. It is indicated that the optimized spoke structure resulted in a maximum drag reduction of 5.7% and 4.7% for the drag coefficient of the isolated wheel and Ahmed body, respectively. The drag reduction is primarily attributed to changes in the flow state around the wheel, which suppressed separation bubbles. Additionally, it influenced the boundary layer thickness around the car body and reduced the turbulent kinetic energy in the wake flow. These effects collectively contributed to the observed drag reduction.Keywords
Cite This Article
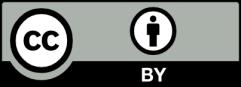