Open Access
ARTICLE
Multi-Scale Design and Optimization of Composite Material Structure for Heavy-Duty Truck Protection Device
1 School of Mechanical and Automotive Engineering, Guangxi University of Science and Technology, Liuzhou, 545006, China
2 Commercial Vehicle Technology Center, Dongfeng Liuzhou Automobile Co., Ltd., Liuzhou, 545005, China
3 School of Mechanical and Automotive Engineering, South China University of Technology, Guangzhou, 510641, China
* Corresponding Author: Hailiang Su. Email:
(This article belongs to the Special Issue: Structural Design and Optimization)
Computer Modeling in Engineering & Sciences 2024, 139(2), 1961-1980. https://doi.org/10.32604/cmes.2023.045570
Received 31 August 2023; Accepted 30 October 2023; Issue published 29 January 2024
Abstract
In this paper, to present a lightweight-developed front underrun protection device (FUPD) for heavy-duty trucks, plain weave carbon fiber reinforced plastic (CFRP) is used instead of the original high-strength steel. First, the mechanical and structural properties of plain carbon fiber composite anti-collision beams are comparatively analyzed from a multi-scale perspective. For studying the design capability of carbon fiber composite materials, we investigate the effects of TC-33 carbon fiber diameter (D), fiber yarn width (W) and height (H), and fiber yarn density (N) on the front underrun protective beam of carbon fiber composite materials. Based on the investigation, a material-structure matching strategy suitable for the front underrun protective beam of heavy-duty trucks is proposed. Next, the composite material structure is optimized by applying size optimization and stack sequence optimization methods to obtain the higher performance carbon fiber composite front underrun protection beam of commercial vehicles. The results show that the fiber yarn height (H) has the greatest influence on the protective beam, and the H1 matching scheme for the front underrun protective beam with a carbon fiber composite structure exhibits superior performance. The proposed method achieves a weight reduction of 55.21% while still meeting regulatory requirements, which demonstrates its remarkable weight reduction effect.Keywords
Cite This Article
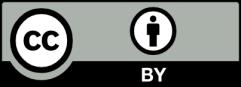