Open Access
PROCEEDINGS
Investigation on Spall Fracture in Metallic Material Generated in Laser Shock Peening via Fracture Phase Field Method
1 University of Michigan -- Shanghai Jiao Tong University Joint Institute, Shanghai Jiao Tong University, Shanghai, 200240, China
* Corresponding Author: Yongxing Shen. Email:
The International Conference on Computational & Experimental Engineering and Sciences 2023, 26(4), 1-1. https://doi.org/10.32604/icces.2023.09131
Abstract
The local surface crack has already been the main reason that has great negative influence on the fatigue life and the resistance of foreign object damage of important equipment, such as the blades of aviation engine. Laser shock peening (LSP) is a very effective technology for metallic surface treatment, which has been widely used to overcome the negative influence of local surface crack. However, when LSP is applied to a thin specimen, an undesirable result spall fracture, which is close to the free surface inside the specimen, may occur.The spall fracture phenomenon generated in LSP has already been investigated in many experiments. However, the numerical investigation about this phenomenon still lacks, which prevents a careful planning of such technique to prevent such disastrous defect. In this work, the spall fracture generated in LSP is investigated numerically. To this end, we adopt fracture phase field method to conduct numerical simulations. The simulations are aimed to propose a finite element framework via fracture phase field method to explore spall fracture, and study the spall fracture response of material in multiple-shock LSP process compared with experimental results.
In this work, the fracture phase field method is implemented in commercial software Abaqus by means of Abaqus subroutines user-defined element UEL. The three-dimensional finite element framework consists of both finite elements and infinite elements, the latter of which account for the infinite boundary by nonreflecting boundary conditions. The Johnson-Cook plasticity model is implemented combined with UEL to describe ductile material. Both strain hardening and strain rate hardening are considered in the model, which makes sure that the implementation is suitable for the high loading rate dynamic LSP process. The laser-induced shock wave load is modeled as a pressure load varying with time and position, and is realized via Abaqus subroutines user-defined load DLOAD.
The experimental results show that the spall fracture occurs after four continue shocks in the multiple-shock LSP process for Ti-17 alloy. According to that, a reasonable value of fracture toughness is explored to simulate this result. Then, the spall fracture responses in the eight-shock process are investigated based on this value and the influences of fracture toughness on this phenomenon is distinguished compared with the experimental results.
Keywords
Cite This Article
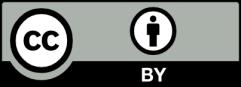