Open Access
ARTICLE
Preparation of High Activity Admixture from Steel Slag, Phosphate Slag and Limestone Powder
College of Materials Science and Engineering, Xi’an University of Architecture & Technology, Xi’an, 710055, China
* Corresponding Authors: Ying Ji. Email: ; Xi Liu. Email:
Journal of Renewable Materials 2023, 11(11), 3977-3989. https://doi.org/10.32604/jrm.2023.028439
Received 17 December 2022; Accepted 06 February 2023; Issue published 31 October 2023
Abstract
The problem of low disposal and utilization rate of bulk industrial solid waste needs to be solved. In this paper, a high-activity admixture composed of steel slag-phosphate slag-limestone powder was proposed for most of the solid waste with low activity and a negative impact on concrete workability, combining the characteristics of each solid waste. The paper demonstrates the feasibility and explains the principle of the composite system in terms of water requirement of standard consistency, setting time, workability, and mechanical properties, combined with the composition of the phases, hydration temperature, and microscopic morphology. The results showed that the steel slag:phosphate slag:limestone = 5:2:3 gave the highest activity of the composite system, over 92%. Besides, the composite system had no significant effect on water demand and setting time compared to cement, and it could significantly increase the 7 and 28 d activity of the system. The composite system delayed the exothermic hydration of the cement and reduced the exothermic heat but had no effect on the hydration products. Therefore, the research in this paper dramatically improved the solid waste dissipation in concrete, reduced the amount of cement in concrete and positively responded to the national slogan of carbon neutral and peaking.Graphical Abstract
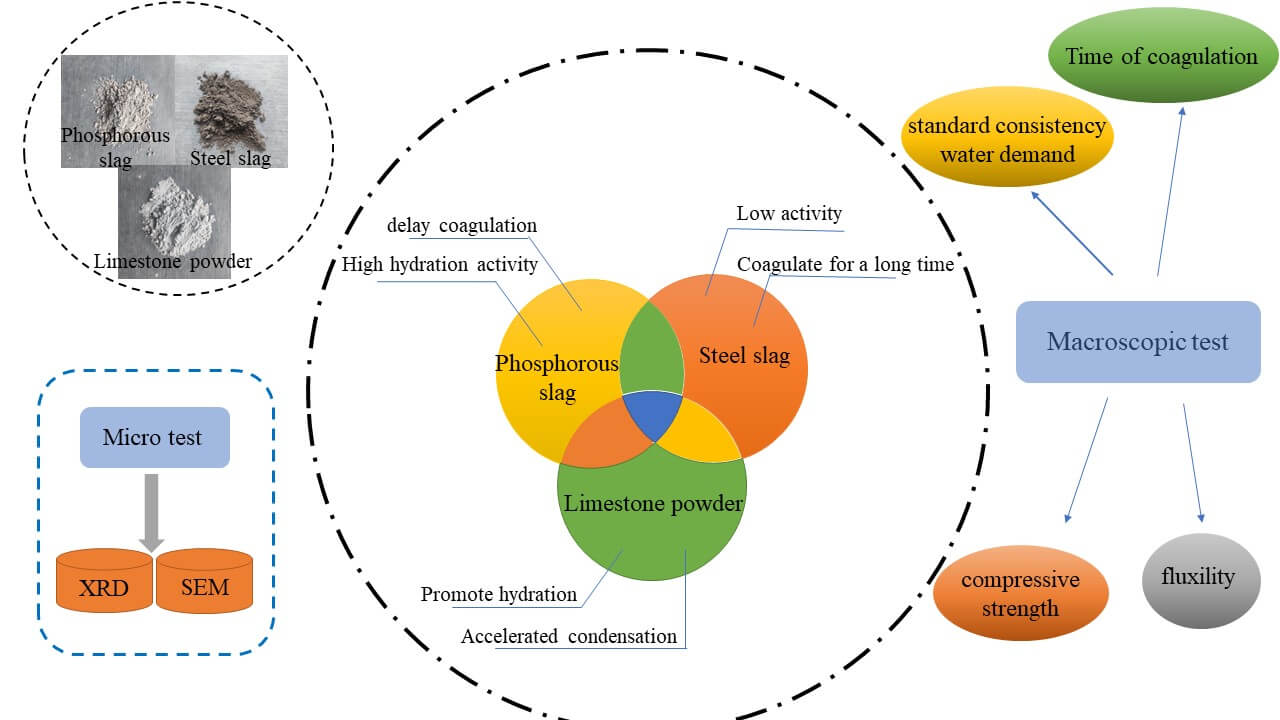
Keywords
With the rapid development of modernization, the discharge of industrial solid waste is also overgrowing [1]. Steel slag and phosphorus slag are industrial wastes with massive annual emissions. Among them, steel slag is the waste generated during the steel production process, and its annual production accounts for about 15%–20% of global steel production [2]. However, the current utilization rate of steel slag in China is only 22%, which is far behind that of developed countries, and a large amount of steel slag would be deposited. If steel slag is piled up for a long time, it will destroy the internal structure of the soil and contaminate the soil, causing environmental pollution and waste of resources [3]. It has been found that steel slag can be used as an aggregate component in asphalt mixtures to improve various properties of asphalt mixtures [4,5]. Also, steel slag has many other uses, such as soil improvement, sewage treatment, or as sintering flux [6,7]. However, the utilization rate of steel slag in China is relatively low at present, not more than 40% [8]. Secondly, the main chemical composition of steel slag is CaO, SiO2, and Al2O3, which is very similar to the composition of cement and theoretically has a specific cementitious activity [9]. Therefore, steel slag can be considered an admixture in concrete to reduce cement consumption and further reduce cement production. Using steel slag as a mineral admixture would have a higher value in terms of environmental, economic, and technical considerations [10]. Therefore, steel slag is one of the most popular new mineral admixtures. At the same time, there are some problems in using steel slag as a mineral admixture. For example, it contains a large amount of hydrated inert minerals, such as RO phase and Fe3O4, so the activity of steel slag, especially the early activity, is much lower than that of cement [11]. Besides, the content of silicate minerals such as C3S, C3A and C4AF, with faster hydrate in steel slag, is less than that of cement, while the amount of slowly hydrated or unhydrated γ-C2S is higher [12]. And the cement mixed with steel slag generally has a longer setting time and lower early strength [13]. Sun et al. [14] found that the activity of steel slag can be improved by mechanical grinding, but it increases the risk of heavy metal leaching. Therefore, mechanical grinding still has shortcomings.
Phosphorus slag is an industrial waste product generated during the production of yellow phosphorus by the electric furnace method. About seven tons of slag are produced for every ton of phosphorus [15]. The main components of phosphorus slag are SiO2 and CaO, and its total content is generally greater than 80%. The vitreous silicate content of phosphate slag is greater than 85%, indicating that phosphate slag possesses a high potential hydration activity [16]. Phosphorus slag also has a retarding effect on the early hydration of cement, and its retarding effect is more significant than its accelerating effect [17]. Phosphor slag delays the setting time of cement by 40% [18]. Gao et al. [19] found that replacing cement with the appropriate amount of phosphorus slag could improve the concrete microstructure and increase its late strength, but the early strength would be reduced. The high P2O5 in phosphate slag, long initial setting time, and low early strength are the main reasons restricting its application. In order to solve these problems, many scholars found that limestone powder can also increase the early strength of concrete, improve the workability of cement paste, and reduce segregation and water secretion [20,21]. Limestone powder is a very abundant and widely distributed material, with easy processing and cheap availability [22]. The mechanism of limestone powder in cementitious materials can be divided into nucleation, filler, dilution, and chemical effect [23,24]. Kakali et al. [25] found that limestone powder delays the conversion of AFt to AFm, and accelerates the hydration of C3S and the early generation of calcium monocarbonate. Limestone powder mainly plays a filling role in the early stage, and its nucleation also promotes early hydration of cement and late hydration to produce calcium carbonate aluminate hydrate [26].
In summary, steel slag admixture reduces the early strength of concrete and slow setting rate [13], while phosphate slag admixture leads to a long setting time, low early strength, and rapid growth in the later period [19]. On the contrary, the limestone powder can accelerate the hydration rate, fill the pores, improve the working properties of concrete and increase the early strength [27,28]. Steel slag has similar cementing properties with silicate cement clinker [9], so compounding steel slag micronized powder with phosphate slag and limestone powder can bring out the advantages of different mineral admixtures and achieve the purpose of complementing the advantages and disadvantages of mineral admixtures.
The purpose of this paper was to resource the bulk industrial solid waste and to propose a composite admixture composed of steel slag as the primary material and with phosphate slag and limestone powder as the supplement. It could reduce the cement dosage and consume the industrial solid waste as much as possible to satisfy the concrete performance, thus realizing the resource utilization of industrial waste and reducing the damage to the environment.
The reference cement is produced by Fushun AusAIL Technology Co., Ltd. (China). Its specific surface area is 355 m2/kg, and its 3, 7, and 28 d compressive strengths are 28.5, 38.2, and 49.7 MPa, respectively. The water demand for standard consistency is 25.8%, and the initial and final setting times are 116 and 176 min, respectively. The steel slag is from Longmen Steel Plant in Shanxi Province, with a specific surface area of 410 m2/kg, f-CaO content of 0.4%, 7, and 28 d activity of 65.9% and 73.4%, respectively. The volumetric stability is qualified to meet the requirements of GB/T 51003-2014 sary steel slag. Longma Phosphorus Industry Co produces phosphate slag. The specific surface area is 453 m2/kg, P2O5 content is 3.24%, SO3 content is 0.4%, 7, and 28 d activity is 62.1% and 87.6%, respectively, which meet the requirements of GB/T 51003-2014 L85 level. The limestone powder is from the Hebei area. Its color is off-white, CaCO3 content is 94%, fineness (45 μm square pore sieve residue) is 11%, density is 2.93 g/cm3, methylene blue value is about 1%, 7, and 28 d activity are 65.2% and 73.4%, respectively, which meet the requirements of GB/T 51003-2014. Fine aggregate is ISO standard sand. The chemical compositions of the four powders are shown in Table 1. Particle size distribution is shown in Fig. 1.
Figure 1: Water demand for standard consistency of cementitious materials with different proportions
According to GB/T 1346-2011, the standard consistency water requirement of the paste at 20°C was tested, and the water consumption within 6 ± 1 mm from the base plate of the standard consistency bar was regarded as the standard consistency water requirement. The setting time of the cementitious material system was measured according to the tested water requirement.
According to GB/T 2419-1994, the fluidity of the specimen was determined. After the standard disc jumps the table 25 times, the fluidity of the sample was measured, and the powder, water, and sand with mortar were prepared according to 450:225:1350 by GB/T 17671-1999 Test Method for Strength of Cement Mortar, in which the powder was prepared as shown in Table 2 and then injected into the 40 mm × 40 mm × 160 mm cement glue sand mold, cured for 1 d and put into the curing box (temperature of 20°C ± 1°C, humidity ≥95%) after demoulding. The compressive strength of the specimen was determined at 7 and 28 d.
Hydration is an exothermic reaction, and the type of hydration products may depend on the peak hydration temperature at a specific temperature, which can also be influenced by some factors [29]. The MT500P multi-channel temperature logger was selected to record the variation of hydration temperature of the paste during 24 h. The cement paste was prepared according to Table 2, loaded into the test vessel, inserted into a thermocouple in the center of the paste, and then placed in an insulating and thermal insulation device to wait for its hydration. The data acquisition was performed, and finally, the temperature vs. time variation curve for 24 h was plotted.
Paste specimens were prepared according to the ratio in Table 2. After the specimens were formed and standardized to age, the specimens were broken and soaked in anhydrous ethanol to terminate their hydration, removed and dried under vacuum before testing, and ground and passed through a 200 mesh sieve. X-ray diffraction (XRD) model D/MAX2200 was used to analyze the phase composition from 0° to 90° at a rate of 10°/min. The internal fragments of the specimens were selected for microscopic morphological observation using a scanning electron microscope (SEM) model Sigma 300.
3.1 Water Demand for Standard Consistency of Composite Admixture Paste
The standard consistency water demand of the paste prepared with composite admixtures under different ratios is shown in Fig. 2. The standard consistency water requirement for cement was 25.8%. 30% steel slag significantly increased the water requirement by 27.4%. When phosphate slag and limestone powder were added, the water requirement of the composite system decreased and showed a decreasing trend as the amount of limestone powder increased. When the limestone powder content in the ratio was not less than 12%, the water demand of the composite system was less than that of the cement group. At 15% of steel slag and 15% of limestone powder, the water requirement was the smallest, 24.6%, which was 1.2% lower than that of the cement group. Adding phosphorus slag, compared with 30% of steel slag, had a certain degree of reduction effect on the water demand of the composite system. Compared with limestone powder, the reduction effect of phosphorus slag on the water demand in the composite system was insignificant.
Figure 2: Particle size distribution of different raw materials
3.2 Setting Time of Paste Prepared by Composite Admixture
The setting time of the paste prepared with composite admixtures at different ratios is shown in Fig. 3. It can be seen that the setting time of the cementitious system after the addition of the three admixtures showed an overall trend of prolongation compared to the cement group. The most significant effect on the prolongation of the setting time of the composite system was observed after the addition of phosphorus slag. In the steel slag and phosphorus slag dosing of 15%, the initial and final setting time of the test piece group was 228 and 320 min, respectively, which was 96.55% and 81.82% longer than that of the cement. If used in the project, the early strength would have some negative effects due to the overlong setting time. After adding limestone powder, the setting time of the system began to show a trend of shortening, and the shortening effect was positively correlated with the amount of limestone powder. When the content of steel slag and limestone powder is 15%, the system’s initial and final setting time is 109 and 143 min, respectively, which was shortened by 6.03% and 18.75%, respectively, compared with the pure cement group. Some authors have obtained similar conclusions for the above trend [30,31].
Figure 3: The setting time of cementitious materials with different ratios
Both phosphate slag and limestone powder affect the setting time, and the effect on the final setting time was greater than the initial setting time. When phosphate slag was mixed in excess, the hydration rate slowed down. The phosphorus and fluorine in phosphate slag and Ca(OH)2 generated by the fluorine hydroxyapatite wrapped around the cement particles hinder the contact between cement particles and water molecules [32], thus reducing the speed of cement paste setting. Macroscopically, it shows that the solidification time is prolonged. Due to its fine particles, the limestone powder could provide nucleation sites for the generation of cement hydration products, thus accelerating cement hydration, which was macroscopically manifested as promoting the setting of the paste [26].
3.3 Fluidity of Mortar Prepared with Composite Admixture
Fig. 4 shows the fluidity of mortars with different ratios. In the same water-cement ratio, the more limestone was added, the better the fluidity of the specimen. The fluidity under 15% limestone powder is 224 mm, which is 13.71% higher than that under 30% steel slag. It corresponds to the results in Fig. 1: the smaller the water requirement for the standard consistency, the greater the fluidity at the same water consumption. Limestone powder can improve the fluidity of the colluvium to some extent due to its fine particles and filling effect [33]. Phosphor slag powder particles were of vitreous structure and did not absorb water on the surface, which can fill the cement particle gaps and release excess water [34]. Moreover, the cement is not completely dense inside after hydration, while the particle size of phosphate slag and limestone powder is smaller than that of cement particles and has lower activity in the early stage of hydration. Therefore, in the early stage of hydration, it can fill the pores between the cement hydration products, increase the compactness and release the water in the pores [35], thus increasing the free water between the paste and improving the macro performance of liquidity. At the same time, the micro aggregates were much finer than cement. It consists of a reasonable intermittent gradation of microaggregates [36], which improves the pore structure of the cement substrate. The water in the original cement voids is replaced to contribute to the fluidity.
Figure 4: Fluidity of mortar under different proportions
3.4 Compressive Strength of Mortar Prepared with Composite Admixture
The compressive strengths of the mortars prepared under different composite cementitious systems are shown in Fig. 5. The compressive strengths of the cement group at 7 and 28 d were 38.2 and 49.7 MPa, respectively. At 7 d, the C1 group, after adding 30% steel slag, had the most apparent effect on the reduction of system strength, with a decrease of 34.03%. After adding phosphate slag and limestone powder, its compressive strength tended to rise, and the compressive strength of others exceeded C1. The steel slag, phosphate slag, and limestone powder ratio are 5:2:3. C4 has the highest strength, and the rate of decline in the strength does not exceed 12.3% compared to the C1 strength at this time. The proportion of improvement exceeded 32.93%. At 28 d, the strength of C1 specimen is 36.5 MPa. After adding other raw materials to form a composite cementitious system, the compressive strength significantly increased. However, when the ratio of steel slag and limestone powder was 1:1, C7 had the lowest compressive strength value of 34.8 MPa, while the strength of C1 and cement group decreased 4.66% and 29.97%, respectively. Currently, steel slag, phosphate slag, and limestone powder = 5:2:3. C4 had the highest strength, and its 28 d activity index was more than 93.36%, much higher than 73.44% of C1.
Figure 5: Compressive strength of mineral admixtures with different proportions
In summary, when the steel slag, phosphate slag, and limestone powder = 5:2:3 has the highest activity, more than 90% is much higher than 73% of the C1 group. That may be due to the low activity of steel slag. There are more voids in the hydration products of steel slag alone [6], and after adding phosphate slag powder, the “micro aggregate effect” of phosphate slag powder fills the gaps of cement particles [16]. However, the phosphate slag itself has a slow-setting effect, making the increase in early compressive strength not apparent. With the increase of limestone powder content, the surface of limestone powder was dense and smooth, which was good for dispersing cement particles. It acted as a dispersant, accelerating the deflocculation of cement particles at the early stage of hydration and improving the hydration rate. Moreover, the aggregate filling effect of limestone powder also reduced the void ratio and void diameter, improved the pore structure, increased the compactness of cement, and improved the early strength [37,38].
For the strength reduction of C7, it was mainly because the accelerating effect of limestone powder did not increase the content of cement hydration products but only accelerated the process of cement hydration and filled the pores after the cement hydration reaction. Limestone powder did not have excessive pozzolanic activity. At the later stage, compared with other substances, the role of limestone powder was still the filling effect of calcium carbonate powder, and the limestone powder sample group was added to the specimen group. The amount of hydration that can provide strength at the same age is reduced, so the macroscopic expression was a decrease in compressive strength at 28 d, which corresponded to the results in the XRD plots, where a higher amount of unhydrated cement products could still be observed in the C7 group.
3.5 Hydration Temperature Analysis
The hydration temperature profiles of the cementitious material system in 1 d for different ratios are displayed in Fig. 6. The exothermic hydration process of the composite cementitious material was similar to that of cement hydration. It can be divided into five stages: preinduction, induction, acceleration, deceleration, and stabilization [12]. The first exothermic peak corresponded to the initial reaction period of the hydration process, about fifteen minutes, which was mainly the reaction of the heat of dissolution and C3A, and started during the mixing process. When entering the induction period, a part of C3S hydrated rapidly and formed a dense protective layer around C3S this time, which hindered the further C3S for about 2–3 h. Therefore, there was a decreasing zone. It can be seen that with the increase of limestone powder, the exothermic peak value was higher, and the temperature gradually raised. At the same time, the exothermic peak gradually sharpened, and the reaction became more and more violent. Finally, it reached a stable period with the temperature close to room temperature.
Figure 6: Hydration temperature curve of samples with different proportions at 20°C
Phosphorus slag significantly prolonged the time of appearance of its exothermic peak while decreasing the peak exothermic heat. When the ratio of phosphorus slag to steel slag was 1:1, the time of its exothermic peak appearance was the longest, which was 45.81% longer than that of the C1 group, and the peak temperature was reduced by 5.31%. It showed that phosphorus slag has a significant reduction effect on the exothermic heat of the composite system. The main reason was that the high content of phosphate slag in the following generated calcium phosphate, which precipitated on the surface of cement clinker particles and generated a protective film, thus preventing hydration and prolonging the setting time, as well as reducing the heat of hydration. However, with the increase of limestone powder admixture, the tendency of prolonging the appearance time of the exothermic peak starts to decrease. And the time of the exothermic peak was shorter than that of the C1 group when the ratio of limestone powder to steel slag was 1:1.
The hydration temperature plus the exothermic peak of the multi-doped steel slag was smoother than the single-doped steel slag, with a broader exothermic peak curve, lower temperature, and more durable reaction. YOU C [29] pointed out that the type of hydration products at a specific temperature may depend on the peak hydration temperature. The hydration products would decompose at higher hydration temperatures, leading to structural changes that reduce strength and, conversely, lower the temperature and increase the hydration efficiency. Sample C2 had the latest exothermic peak and the lowest temperature, and slowing a reaction too much could lead to insufficient early strength, thus negatively affecting construction. The rapidity of the exothermic hydration could also be evidenced by the setting time (Fig. 3).
The results of the 7 d paste with different ratios of mineral admixtures by X-ray diffraction (XRD) are shown in Fig. 7. The products after hydration of the composite system at different ratios were examined for the presence of calcium hydroxide (CH), tricalcium silicate (C3S) and calcium carbonate (CaCO3). The content of limestone powder gradually increased from C3 to C7, and the intensity of the diffraction peaks of calcium carbonate after hydration also increased significantly. The intensity of the diffraction peaks of calcium carbonate was highest at C7. This proves that within 7 d of hydration, the calcium carbonate particles in limestone powder played a filling role and did not participate too much in the hydration reaction [25]. CH is a cement hydration product, so the CH content can qualitatively determine the degree of hydration of the cement. Therefore, it can be observed that the diffraction peaks of the corresponding CH show a tendency to increase first and then decrease with the increase of limestone powder admixture, which means that the addition of limestone promotes the hydration of cement to some extent. The intensity of the corresponding CH diffraction peaks was highest at 6%, but limestone powder did not participate directly in the reaction. In group C2, there was no significant difference between the diffraction peaks corresponding to group C1 after adding 15% phosphate slag, which proved that phosphate slag did not promote the hydration of cement. The above results were consistent with the compressive strength pattern in Fig. 5.
Figure 7: XRD spectrum of samples with different proportions
The microscopic morphology of the different ratios at 7 d of hydration is shown in Fig. 8. The presence of C-S-H and AFt could be seen in all figures. In the C4 specimen group, the matrix was denser than the other three groups, and more AFt was observed, which was one of the main strength providers of cement paste, so the strength of the C4 specimen was higher in macroscopic terms compared to the other groups. The structure of the cement system in specimen C1 structure was relatively dense. However, at this time, in addition to the agglomerated flocculent C-S-H gel, a small number of needle-like AFt crystals could be observed, indicating that the pre-reactivity of the steel slag micronized powder was low. Besides, the slow hydration and the presence of some inert substances such as RO equivalent [11] in the steel slag further made the hydration products more difficult to glue and lose structure, which led to a decreasing trend in the early strength of cement mortar. It was consistent with the compressive results in Fig. 5.
Figure 8: Micromorphology after 7 d hydration with different ratios
The problems in the application of bulk solid waste, such as steel slag and phosphorus slag in cement, combined with other materials that can be used in cement, discussed the treatment of bulk solid waste such as steel slag and phosphorus slag is discussed in this paper. It proposed the main body of steel slag, compounded phosphate slag, and limestone to prepare a highly active mixture of ideas. It is tested to verify: the steel slag: phosphate slag: limestone ratio of 5:2:3 could make the three composite systems composed of the highest activity, more than 92%, compared to cement. The composite system had no pronounced effect on water demand and setting time, which can significantly improve the 7 and 28 d activity of the system, further expanding the application of steel slag, phosphate slag, etc., and providing a theoretical basis for the disposal of such bulk solid waste.
Steel slag and phosphate slag would significantly extend the setting time and increase the water demand. Adding limestone powder would shorten the setting time and reduce the water demand when the steel slag: limestone powder ratio = 1:1, the water demand of the system is lower than the cement group.
When steel slag:phosphate slag:limestone = 5:2:3, the composite system has the highest compressive strength at all ages. At 28 d, the system activity is more than 92%. In the system where the ratio of steel slag and limestone powder is 1:1, the pozzolanic activity is lower than C1.
The mixture of steel slag, phosphate slag, and limestone would not affect the composition of cement hydration products but would delay the exothermic time and peak appearance of cement hydration.
This study has a positive significance for the elimination and treatment of steel slag, and its blending amount could be further increased to improve the disposal efficiency of steel slag.
Funding Statement: Key Research and Development Plan of Shaanxi Province (2019TSLGY05-04).
Conflicts of Interest: The authors declare that they have no conflicts of interest to report regarding the present study.
References
1. Lü, Y., Yang, K., Che, Y., Shang, Z., Tai, J. et al. (2012). Industrial solid waste flow analysis of eco-industrial parks: Implications for sustainable waste management in China. Frontiers of Environmental Science & Engineering, 6(4), 575–587. https://doi.org/10.1007/s11783-011-0344-0 [Google Scholar] [CrossRef]
2. Fisher, L. V., Barron, A. R. (2019). The recycling and reuse of steelmaking slags—A review. Resources, Conservation and Recycling, 146, 244–255. https://doi.org/10.1016/j.resconrec.2019.03.010 [Google Scholar] [CrossRef]
3. Lai, M. H., Zou, J., Yao, B., Ho, J. C. M., Zhuang, X. et al. (2021). Improving mechanical behavior and microstructure of concrete by using BOF steel slag aggregate. Construction and Building Materials, 277, 122269. https://doi.org/10.1016/j.conbuildmat.2021.122269 [Google Scholar] [CrossRef]
4. Rodríguez-Fernández, I., Lastra-González, P., Indacoechea-Vega, I., Castro-Fresno, D. (2019). Recyclability potential of asphalt mixes containing reclaimed asphalt pavement and industrial by-products. Construction and Building Materials, 195, 148–155. https://doi.org/10.1016/j.conbuildmat.2018.11.069 [Google Scholar] [CrossRef]
5. Yang, C., Wu, S., Cui, P., Amirkhanian, S., Zhao, Z. et al. (2022). Performance characterization and enhancement mechanism of recycled asphalt mixtures involving high RAP content and steel slag. Journal of Cleaner Production, 336, 130484. https://doi.org/10.1016/j.jclepro.2022.130484 [Google Scholar] [CrossRef]
6. Jiang, Y., Ling, T. C., Shi, C., Pan, S. Y. (2018). Characteristics of steel slags and their use in cement and concrete—A review. Resources, Conservation and Recycling, 136, 187–197. https://doi.org/10.1016/j.resconrec.2018.04.023 [Google Scholar] [CrossRef]
7. Rashad, A. M. (2019). A synopsis manual about recycling steel slag as a cementitious material. Journal of Materials Research and Technology, 8(5), 4940–4955. https://doi.org/10.1016/j.jmrt.2019.06.038 [Google Scholar] [CrossRef]
8. Guo, J., Bao, Y., Wang, M. (2018). Steel slag in China: Treatment, recycling, and management. Waste Management, 78, 318–330. https://doi.org/10.1016/j.wasman.2018.04.045 [Google Scholar] [PubMed] [CrossRef]
9. Jing, W., Jiang, J., Ding, S., Duan, P. (2020). Hydration and microstructure of steel slag as cementitious material and fine aggregate in mortar. Molecules, 25(19), 4456. https://doi.org/10.3390/molecules25194456 [Google Scholar] [PubMed] [CrossRef]
10. Liu, C., Huang, S., Wollants, P., Blanpain, B., Guo, M. (2017). Valorization of BOF steel slag by reduction and phase modification: Metal recovery and slag valorization. Metallurgical and Materials Transactions B, 48(3), 1602–1612. https://doi.org/10.1007/s11663-017-0966-0 [Google Scholar] [CrossRef]
11. Cao, L., Shen, W., Huang, J., Yang, Y., Zhang, D. et al. (2019). Process to utilize crushed steel slag in cement industry directly: Multi-phased clinker sintering technology. Journal of Cleaner Production, 217, 520–529. https://doi.org/10.1016/j.jclepro.2019.01.260 [Google Scholar] [CrossRef]
12. Zhao, J., Li, Z., Wang, D., Yan, P., Luo, L. et al. (2023). Hydration superposition effect and mechanism of steel slag powder and granulated blast furnace slag powder. Construction and Building Materials, 366, 130101. https://doi.org/10.1016/j.conbuildmat.2022.130101 [Google Scholar] [CrossRef]
13. Li, Z., Zhao, X., He, T., Zhao, S., Liu, Y. et al. (2017). A study of high-performance slag-based composite admixtures. Construction and Building Materials, 155, 126–136. https://doi.org/10.1016/j.conbuildmat.2017.08.054 [Google Scholar] [CrossRef]
14. Sun, X., Liu, J., Zhao, Y., Zhao, J., Li, Z. et al. (2022). Mechanical activation of steel slag to prepare supplementary cementitious materials: A comparative research based on the particle size distribution, hydration, toxicity assessment and carbon dioxide emission. Journal of Building Engineering, 60, 105200. https://doi.org/10.1016/j.jobe.2022.105200 [Google Scholar] [CrossRef]
15. Allahverdi, A., Pilehvar, S., Mahinroosta, M. (2016). Influence of curing conditions on the mechanical and physical properties of chemically-activated phosphorous slag cement. Powder Technology, 288, 132–139. https://doi.org/10.1016/j.powtec.2015.10.053 [Google Scholar] [CrossRef]
16. Peng, Y., Zhang, J., Liu, J., Ke, J., Wang, F. (2015). Properties and microstructure of reactive powder concrete having a high content of phosphorous slag powder and silica fume. Construction and Building Materials, 101, 482–487. https://doi.org/10.1016/j.conbuildmat.2015.10.046 [Google Scholar] [CrossRef]
17. Zhang, Z., Wang, Q., Yang, J. (2017). Hydration mechanisms of composite binders containing phosphorus slag at different temperatures. Construction and Building Materials, 147, 720–732. https://doi.org/10.1016/j.conbuildmat.2017.04.202 [Google Scholar] [CrossRef]
18. Pang, M., Sun, Z., Chen, M., Lang, J., Dong, J. et al. (2020). Influence of phosphorus slag on physical and mechanical properties of cement Mortars. Materials, 13(10), 2390. https://doi.org/10.3390/ma13102390 [Google Scholar] [PubMed] [CrossRef]
19. Gao, P., Lu, X., Yang, C., Li, X., Shi, N. et al. (2008). Microstructure and pore structure of concrete mixed with superfine phosphorous slag and superplasticizer. Construction and Building Materials, 22(5), 837–840. https://doi.org/10.1016/j.conbuildmat.2006.12.015 [Google Scholar] [CrossRef]
20. de Weerdt, K., Haha, M. B., Le Saout, G., Kjellsen, K. O., Justnes, H. et al. (2011). Hydration mechanisms of ternary Portland cements containing limestone powder and fly ash. Cement and Concrete Research, 41(3), 279–291. https://doi.org/10.1016/j.cemconres.2010.11.014 [Google Scholar] [CrossRef]
21. Schankoski, R. A., Pilar, R., Prudêncio Jr, L. R., Ferron, R. D. (2017). Evaluation of fresh cement pastes containing quarry by-product powders. Construction and Building Materials, 133, 234–242. https://doi.org/10.1016/j.conbuildmat.2016.12.056 [Google Scholar] [CrossRef]
22. Chouhan, H. S., Kalla, P., Nagar, R., Gautam, P. K. (2019). Gainful utilization of dimensional limestone waste as fine aggregate in cement mortar mixes. Construction and Building Materials, 221, 363–374. https://doi.org/10.1016/j.conbuildmat.2019.06.097 [Google Scholar] [CrossRef]
23. Wang, D., Shi, C., Farzadnia, N., Shi, Z., Jia, H. et al. (2018). A review on use of limestone powder in cement-based materials: Mechanism, hydration and microstructures. Construction and Building Materials, 181, 659–672. https://doi.org/10.1016/j.conbuildmat.2018.06.075 [Google Scholar] [CrossRef]
24. Ahmad, I., Shen, D., Khan, K. A., Jan, A., Khubaib, M. et al. (2022). Effectiveness of limestone powder in controlling the shrinkage behavior of cement based system: A review. Silicon, 14(2), 359–371. https://doi.org/10.1007/s12633-020-00897-1 [Google Scholar] [CrossRef]
25. Kakali, G., Tsivilis, S., Aggeli, E., Bati, M. (2000). Hydration products of C3A, C3S and Portland cement in the presence of CaCO3. Cement and Concrete Research, 30(7), 1073–1077. https://doi.org/10.1016/S0008-8846(00)00292-1 [Google Scholar] [CrossRef]
26. Liu, S., Wang, H., Wei, J. (2017). The role of various powders during the hydration process of cement-based materials. Advances in Materials Science and Engineering, 2017, 1–9. https://doi.org/10.1155/2017/8394834 [Google Scholar] [CrossRef]
27. Devi, K., Aggarwal, P., Saini, B. (2020). Admixtures used in self-compacting concrete: A review. Iranian journal of science and technology. Transactions of Civil Engineering, 44(2), 377–403. [Google Scholar]
28. Li, L. G., Huang, Z. H., Tan, Y. P., Kwan, A. K. H., Chen, H. Y. (2019). Recycling of marble dust as paste replacement for improving strength, microstructure and eco-friendliness of mortar. Journal of Cleaner Production, 210, 55–65. https://doi.org/10.1016/j.jclepro.2018.10.332 [Google Scholar] [CrossRef]
29. You, C., Qian, J., Qin, J., Wang, H., Wang, Q. et al. (2015). Effect of early hydration temperature on hydration product and strength development of magnesium phosphate cement (MPC). Cement and Concrete Research, 78, 179–189. https://doi.org/10.1016/j.cemconres.2015.07.005 [Google Scholar] [CrossRef]
30. Li, D. X., Shen, J. L., Lin, C., Wu, X. Q. (2001). The influence of fast-setting/early-strength agent on high phosphorous slag content cement. Cement and Concrete Research, 31(1), 19–24. https://doi.org/10.1016/S0008-8846(00)00442-7 [Google Scholar] [CrossRef]
31. Han, F. H., Wang, Q., Liu, M. T., Mei, Y. J. (2016). Early hydration properties of composite binder containing limestone powder with different finenesses. Journal of Thermal Analysis and Calorimetry, 123(2), 1141–1151. https://doi.org/10.1007/s10973-015-5088-9 [Google Scholar] [CrossRef]
32. Zhao, H., Poon, C. S., Ling, T. C. (2013). Utilizing recycled cathode ray tube funnel glass sand as river sand replacement in the high-density concrete. Journal of Cleaner Production, 51, 184–190. https://doi.org/10.1016/j.jclepro.2013.01.025 [Google Scholar] [CrossRef]
33. Vance, K., Arora, A., Sant, G., Neithalath, N. (2015). Rheological evaluations of interground and blended cement–limestone suspensions. Construction and Building Materials, 79, 65–72. https://doi.org/10.1016/j.conbuildmat.2014.12.054 [Google Scholar] [CrossRef]
34. Chen, X., Fang, K., Yang, H., Peng, H. (2011). Hydration kinetics of phosphorus slag-cement paste. Journal of Wuhan University of Technology. Materials Science Edition, 26(1), 142–146. https://doi.org/10.1007/s11595-011-0186-4 [Google Scholar] [CrossRef]
35. Dhandapani, Y., Santhanam, M., Kaladharan, G., Ramanathan, S. (2021). Towards ternary binders involving limestone additions—A review. Cement and Concrete Research, 143, 106396. https://doi.org/10.1016/j.cemconres.2021.106396 [Google Scholar] [CrossRef]
36. Uysal, M., Sumer, M. (2011). Performance of self-compacting concrete containing different mineral admixtures. Construction and Building Materials, 25(11), 4112–4120. https://doi.org/10.1016/j.conbuildmat.2011.04.032 [Google Scholar] [CrossRef]
37. Li, L. G., Kwan, A. K. (2015). Adding limestone fines as cementitious paste replacement to improve tensile strength, stiffness and durability of concrete. Cement and Concrete Composites, 60, 17–24. https://doi.org/10.1016/j.cemconcomp.2015.02.006 [Google Scholar] [CrossRef]
38. Şahmaran, M., Christianto, H. A., Yaman, İ. Ö. (2006). The effect of chemical admixtures and mineral additives on the properties of self-compacting mortars. Cement and Concrete Composites, 28(5), 432–440. https://doi.org/10.1016/j.cemconcomp.2005.12.003 [Google Scholar] [CrossRef]
Cite This Article
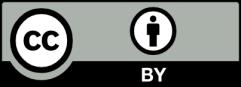