Open Access
ARTICLE
Potential of Thai Bast Fibers for Injection Molded PLA Composites
1 The Biological Materials Group, Department of Biomimetics, HSB-City University of Applied Sciences, Bremen, D-28199, Germany
2 Department of Botany, Faculty of Liberal Arts and Science, Kasetsart University, Kamphaeng Saen, Nakhon Pathom, 73140, Thailand
3 Bioproduct Science, Department of Science, Faculty of Liberal Art and Science, Kasetsart University, Kamphaeng Saen, Nakhon Pathom, 73140, Thailand
4 Department of Science and Mathematics, Faculty of Science and Technology, Rajamangala University of Technology Tawan-Ok, Chonburi, 20110, Thailand
* Corresponding Author: Nina Graupner. Email:
(This article belongs to the Special Issue: Natural Fibre Composites: Design, Materials Selection and Fabrication)
Journal of Renewable Materials 2023, 11(5), 2279-2300. https://doi.org/10.32604/jrm.2023.025529
Received 18 July 2022; Accepted 30 September 2022; Issue published 13 February 2023
Abstract
Thailand has a huge variability of bast fiber plants, some of which have been little researched regarding their applicability in composites. Bast fiber(bundle)s from different species were investigated and incorporated into a polylactide (PLA) matrix by injection molding. Hemp and kenaf were used as well-studied fibers, while roselle, Fryxell and paper mulberry are less extensively characterized. Tensile strength, tensile modulus and interfacial shear strength (IFSS) of single fiber(bundle)s were highest for hemp, followed by kenaf, roselle, Fryxell and paper mulberry. Despite the lower tensile strength and IFSS of paper mulberry, the highest tensile strength was achieved for the paper mulberry/PLA composite followed by hemp/PLA. Scanning electron microscope (SEM) analyses showed that the single cells in paper mulberry fiber bundles, in contrast to the other fiber types investigated, were only partially bonded to each other, which explains the lower strength of the fiber bundles. The higher aspect ratio of fiber(bundle)s of paper mulberry in the PLA composite can explain the good composite characteristics. Apart from hemp, paper mulberry shows the best reinforcing effect in the PLA matrix and offers interesting potential for composite applications. Compared to neat PLA, the tensile strength could be increased by 24% and the tensile modulus by 54%.Graphic Abstract
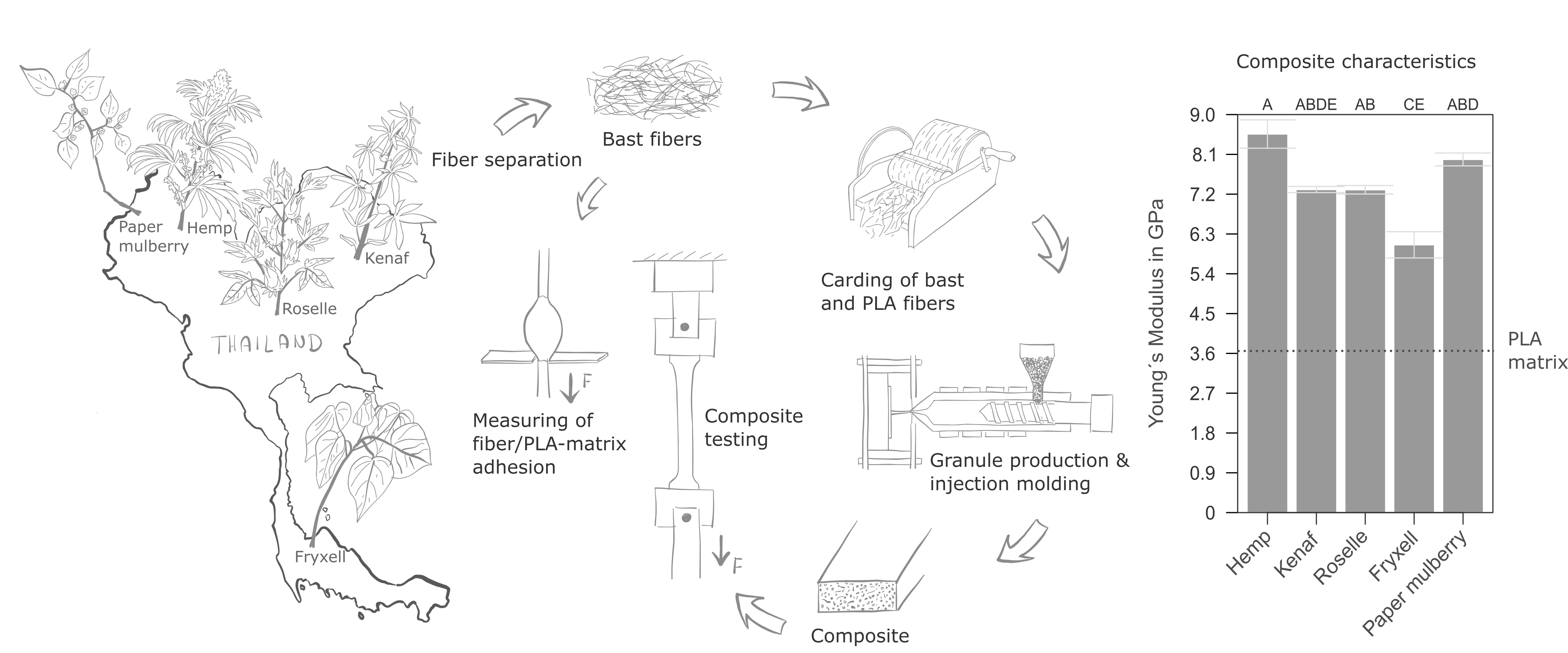
Keywords
Renewable raw materials for more sustainable applications have been increasingly used and investigated in Thailand in recent decades. Petrochemical plastics are to be replaced more and more by bio-based plastics [1,2]. One biobased plastic that has been very well studied in recent decades is polylactide (PLA). PLA is an aliphatic polyester that is used in various applications such as orthopedics, drug delivery, sutures and scaffolds, 3D printing, disposable tableware and packaging products. However, due to its low glass transition temperature, its applications are limited to lower temperatures. PLA is entirely biodegradable in industrial compost and is made from renewable raw materials, mainly corn starch. Due to its good strength and stiffness compared to many other thermoplastics, PLA is now also widely used as a matrix for fiber-reinforced plastics [3,4]. The processing of natural fiber-reinforced PLA composites can be done, e.g., by injection molding and extrusion (short fibres) with random fibre orientation or compression molding (short or long fibers with random or specific fiber orientation) [5–7].
The conditions for cultivating bast fiber plants in Thailand are excellent [8,9]. Bast fibers such as hemp (Cannabis sativa L.), kenaf (Hibiscus cannabinus L.) and jute (Corchorus capsularis L.) are well known in Europe; whereas hemp can also be grown in Europe and jute and kenaf are mainly imported from Asia. Roselle (Hibiscus sabdariffa L.), Fryxell (Hibiscus tiliaceus L.) and paper mulberry (Broussonetia papyrifera (L.) Vent), on the other hand, are rarely used in technical applications. They also belong to the group of bast fibers; however, there is less research activity in this area concerning their use in composites. For this reason, this study aims to evaluate to what extent these fiber types can lead to comparable properties of hemp and kenaf fiber-reinforced PLA composites. Many studies deal with the fiber and composite properties of hemp and kenaf. The overview articles of Amaducci et al. [10], Shazad [11], Müssig et al. [12], Rehman et al. [13] or Manaia et al. [14] should be mentioned here for hemp and Aji et al. [15], Ramesh [16], Ayadi et al. [17], Bourmaud et al. [18] or Inder Preet Singh et al. [19] for kenaf, for example.
Research on roselle (Hibiscus sabdariffa L.) fiber properties and composite materials has been intensified in recent years. Roselle belongs to the same family as kenaf (Malvaceae). An overview of the origin, cultivation and use is given in the study by Ilyas et al. [20]. Nadlene et al. [21] stated that roselle fibers have a comparable potential to kenaf and jute and give an overview of the history of roselle and its characteristics. Thiruchtitrambalam et al. [22] described the extraction of fiber(bundle)s from the plant stem and the use of roselle in high strength ropes in India. In general, the use of roselle fibers does not seem to be widespread, although Crane [23] already referred to the plant and the properties of the fibers in 1949, and it was already known at that time that roselle fibers display similar properties to jute fibers. In 1967, Wilson [24] already published a study in which fibers and fiber bundles of 13 different Hibiscus bast fiber plants were comparatively examined. However, more and more studies have been carried out in recent years on the use of roselle in composite materials. Nadlene et al. [25] investigated the suitability of roselle (thermal, physical and morphological properties) and concluded that roselle fibers are well suited for composite applications. Junkasem successfully prepared injection molded roselle fiber-reinforced isotactic polypropylene (iPP) composites with random fiber orientation. It was found that the addition of roselle bast fibers resulted in the overall improvement in the tensile, flexural, and impact properties of the composites compared to pure iPP [26]. Naraprateep [27] investigated the influence of pretreatment of roselle fibers with mixed solvent and sodium hydroxide (NaOH) solution, maleic anhydride grafted polypropylene (MAPP), vinyltriethoxysilane (VTES) and octadecyltrimethoxysilane (OTMS) for the use in injection molded PP composites with random fiber orientation. By using MAPP, the properties of the composites were significantly increased. Treatment with VTES also increased the characteristic values; OTMS, on the other hand, did not improve the results. Overall, only a few studies were found that dealt with roselle-reinforced thermoplastic matrices. In most cases, thermoset matrices have been used in the recent past. Manickam et al. [28] prepared roselle fiber-reinforced vinyl ester (VE) composites by hand lay-up with different fiber content and random fiber orientation. It was found that the characteristics of the roselle fiber-reinforced composites could be effectively improved. Other authors also examined the influence of fiber content in thermoset composites. For example, Nallusamy [29] reported an increase in strength for compression molded roselle/epoxy composites with random fiber orientation up to a fiber mass content of 30%. Above this value, the characteristic values were significantly reduced. Manickam et al. [30] stated that for compression molded roselle/VE composites with random fiber orientation, the tensile, flexural, and impact strength values of roselle fiber-reinforced composites increased with increasing fiber content up to 40 mass-% and then dropped. Navaneethakrishnan et al. [31] and Ramakrishnan et al. [32] came to similar results and showed for roselle in a VE matrix produced by hand lay-up with random fiber orientation that the Young’s modulus can be increased up to 50% fiber mass content, while the strength decreased above 40 mass-% fibers. Other studies dealt with the use of different fabric types (plain weave, twill weave, satin weave and basket weave) as reinforcement in an epoxy matrix [33], the water absorption of VE composite materials produced by hand lay-up with random fiber orientation [34] or compression molded thermoplastic polyurethane (TPU) with random fiber orientation [35]. The effect of fiber length in random oriented fiber-reinforced composites was also investigated. Ramakrishnan et al. [32] investigated the effect of random oriented 3 and 13 mm long fibers in a VE matrix and found that the materials with the longer fibers performed better. A similar conclusion was reached by Singha et al. [36], who introduced 3 and 6 mm long fibers with a random fiber orientation into urea-formaldehyde (UF) matrix. Again, the higher characteristic values were obtained for the material reinforced with the longer fibers [37]. Other studies also addressed the improvement of fiber properties and fiber/matrix adhesion in composites. For example, Azeez et al. [38] used an alkali treatment and a sodium lauryl sulphate treatment to improve the tensile properties of the roselle fiber bundle collectives and to reduce the density and water absorption of the fibers. Chauhan et al. [39,40] have tried different grafting methods with random oriented roselle fibers in phenol-formaldehyde (PF) resin and achieved higher chemical resistance and tensile characteristics compared to composites manufactured from untreated fibers. Alkali treatment of the fibers was carried out by Manickam et al. [30] and Kumar et al. [41]. As a result, the characteristic values of roselle/VE [30] and roselle/unsaturated polyester (UP) composites with random fiber orientation [41] could be clearly improved. There also seems to be a trend towards producing hybrid composites from roselle and other natural resources. For example, roselle has been blended with jute [42], sisal [41,43–46], banana [43], abacá [47] and sugar palm fibers [35,48] or palm seed powder [49].
Fryxell (Hibiscus tiliaceus L.) also belongs to the family of Malvaceae, but different from roselle, for Fryxell, hardly any literature could be found. One reference passage states that the fibers’ tenacity and Young’s modulus values are in the range of well-investigated fibers like cotton, flax and ramie. The results are promising in terms of their employment in thermoset and thermoplastic medium resistance composites [50]. However, no studies were found that investigated the composite properties.
Likewise, there seems to be hardly any application in the field of composite materials for paper mulberry bast fibers. Paper mulberry (Broussonetia papyrifera (L.) Vent) is classified as Moraceae, which belongs to Angiospermae. The structural characteristics of lignin in paper mulberry bast fiber(bundle)s are different compared, e.g., to kenaf [51]. Paper mulberry fibers are mainly used for paper production. Mulberry paper is generally stronger than conventional paper and is also used for electronics applications [52]. Qu et al. [53] compared the characteristics of paper mulberry bast fibers with cotton and flax and found a comparable crystallinity and moisture absorption, with reasonably high tenacity and elongation at break compared to flax. The authors considered paper mulberry bast fibers as an alternative source for natural cellulose fibers. There are attempts to produce yarns and fabrics since paper mulberry has high moisture content and high tenacity [54]. Only a few publications have been found on the use of paper mulberry in composites. Hwang et al. [55] produced cellulose nanofibers from paper mulberry and state that they are suitable for use in nanocomposites, membrane filters, packaging, coatings and reinforcing fillers. Ohsawa et al. [56] presented an approach to process Washi paper from paper mulberry combined with a PLA matrix. Unfortunately, no characteristic values were given in the study. Another study used long, oriented mulberry fiber bundles as reinforcement in a UP matrix from untreated, 5%, 10%, and 15% alkali-treated mulberry fibers by compression molding. Using 10% alkali-treated mulberry fibers as reinforcement considerably increased the tensile, flexural, and impact properties compared to untreated, 5% and 15% alkali-treated mulberry fiber-reinforced composites, while water absorption decreased with increasing alkali concentration [57].
Despite extensive research, the authors were unable to find any studies dealing with injection molded PLA composites reinforced with roselle, Fryxell and paper mulberry during the investigation period. Therefore, the present study aims to determine the fiber and composite properties and to classify the fibers in terms of their reinforcement potential. The aim is to produce completely bio-based composites from natural bast fibers and a bio-based plastic (PLA). Hemp and kenaf serve as well-studied reference samples. The study investigates the influence of processing on fiber morphology, reinforcement potential, and fiber and composite properties. The aim is to achieve similar reinforcement effects as with hemp and kenaf with the less well-known bast fiber species roselle, Fryxell and paper mulberry, and thus to obtain additional raw material sources for the production of biobased composites.
All fibers used belong to the group of bast fibers/bast fiber bundles grown in Thailand (compare Table 1). All raw fibers were collected from farmers in different regions and subjected to an alkali treatment as degumming process with 2% caustic soda [8] for fiber separation from bark to fiber bundle. Then alkali-treated fibers were cut to about 100 mm long sections and were hand-carded four times for mechanical separation and debris removal with a laboratory carding machine (Shirley Developments Limited, Stockport, England; working width 200 mm, cylinder circumference 500 mm). The following fiber types in Table 1 were analysed regarding their mechanical, morphological and chemical properties and were used for the production of injection molded fiber-reinforced polylactide (PLA) composites.
PLA was used as the matrix (type 3251D, NatureWorks LLC, Minnetonka, Minnesota, USA). The PLA has a density of 1.24 g/cm³, a melting temperature of 155°C–170°C and a glass transition temperature of 55°C–60°C. In a previous study [12], a median tensile strength of 57.7 ± 1.1 MPa, Young´s modulus of 3.65 ± 0.20 GPa and an elongation at break of 3.9% ± 2.2% were determined for the unreinforced injection molded PLA according to DIN EN ISO 527-2 [58]. The unnotched Charpy impact strength was determined to be 15.3 ± 0.5 kJ/m² according to DIN EN ISO 179 [59].
PLA granules (70 mass-%) and bast fibers (30 mass-%) were pre-dried at least for 18 h at 60°C in a forced air oven and were then blended by using the CMS-compounder at 3 N (3 N Kompetenzzentrum Niedersachsen-Netzwerk Nachwachsende Rohstoffe & Bioökonomie e.V.), Werlte, Germany. The process temperatures during compounding ranged between 170°C and 180°C (details on the compounding concept are to be found in [60]). After compounding, the compounds were available in granular form. The compounds were then injection molded (Engel E-mac 50 with a screw diameter of 30 mm, ENGEL GmbH, Schwertberg, Austria) into a mold (Axxicon AIM mold) to manufacture a tensile test bar type 1A according to DIN EN ISO 527-2 [58]. The following temperature zones were chosen for the injection molding process: 150°C (zone 1), 165°C (zone 2) and 175°C (zone 3). The nozzle of the injection molding machine was heated to 175°C, and the mold was cooled to 25°C. The machine was operated with an injection pressure of 1500 bar, injection speed of 24 cm³/s, and a cooling time of 30 s.
All fiber(bundle)s were conditioned before analysis for at least 18 h in a standard climate according to DIN EN ISO 139 (20°C, 65% relative humidity) [61].
Tensile characteristics of fiber bundles were investigated with a tensile testing machine (type Fafegraph M, Textechno GmbH, Mönchengladbach, DE) with a pneumatic clamping system. 50 fiber bundles were analyzed with a load cell of 1000 cN at a gauge length of 3.2 mm and a testing speed of 2 mm/min. The elongation was determined from the traverse path of the testing machine. The determined strain values were corrected with an internally determined correction factor to account for the machine’s compliance. In order to determine the most accurate fiber cross-sectional area possible, the fibers were prepared in paper frames prior to the experiments and scanned at a resolution of 2400 dpi using a flatbed scanner (Epson Perfection V800 Photo, EPSON GmbH, Meerbusch, Germany) in transmitted light mode. The width of the fiber (bundle) under investigation was measured using ImageJ (National Institutes of Health) prior to the experiments. Internally determined correction factors were created on the basis of an ellipse using cross sections (taken with an SEM) by measuring both ellipse diameters (thickness and width). From more than 100 measurements, a linear relationship was obtained from the two ellipse diameters (thickness vs. width), and a correction factor was determined for each type of fiber. It is assumed that the fiber (bundle) lay on the wide side during preparation. The regression equations obtained were then used to calculate the thicknesses, and the cross-sectional area of each individual fiber (bundle) was approximated from width and thickness on the basis of an ellipse.
Raw fiber(bundle)s were investigated regarding their width with the image analysis software Fibershape (version 5.1.1, IST AG, Vilters, CH). Approximatley 5 mm long fiber bundles were prepared on slide frames and scanned with a slide scanner (CanoScan 4000 US, Canon Inc., Tokyo, JP) at 2000 dpi resolution in transmitted light mode. The evaluation was done with a measuring mask prepared for long fibers in the thickness range between 10 and 10,000 μm with a zoom factor of 0.71. More than 8500 fiber sections were analysed per fiber type.
To investigate the morphology of the fibers and fiber bundles after processing, they were extracted from the composites. For this purpose, 1 g of each composite is weighed into a Duran® filter crucible with a porosity of 3 and a volume of 30 mL (Carl Roth GmbH & Co. KG, Karlsruhe, DE) with a scale (type Kern ABT 120-5 DM, d = 0.00001 g; Kern und Sohn GmbH, Balingen, DE). The filter crucible is placed in a beaker and filled with trichloromethane (chloroform-CHCl3) (ROTISOLV®, Carl Roth GmbH + Co. KG, Karlsruhe, DE). After 1 h, the trichloromethane is sucked out with a water jet pump. The process is then repeated. Afterwards, the fibers were dried in the crucibles at ambient conditions. The fibers were also prepared on slide frames and scanned with the CanoScan slide scanner with a resolution of 4000 dpi. The images were then measured with Fibershape (X-Shape Version 6.1.4, IST AG, Vilters, Switzerland) regarding their width and length. Between 872 and 1827 fibers and fiber bundles were measured per sample. The aspect ratio was calculated from the ratio of object length to width.
The chemical composition of the alkali treated bast fibre bundles was analysed according to Van Soest [62] with an Ankom A200 fibre analyser (ANKOM Technology, Macedon, NY, USA) using a gravimetric analysis technique. Three measurements were performed on each sample at 1 g, respectively. The percentual amount of neutral detergent fibre (NDF), acid detergent fibre (ADF) and acid detergent lignin (ADL) were determined for the calculation of the cellulose (ADF-ADL), hemicellulose (NDF-ADF) and lignin (ADL) content.
The fiber/matrix adhesion between fiber bundles and PLA matrix was investigated with microbond tests. Single fiber bundles were fixed in a metal frame at both ends with adhesive tape (Tesa SE, Hamburg, Germany). Two to three PLA fibers (Ingeo fibers type SLN 2660 D; Eastern Textile, Ltd., Taipei, TW) with a fineness of 6.0 dtex were twisted and knotted around the fiber bundle as described in [63]. Afterwards, the ends of the PLA-fibers were removed with a razor blade close to the fiber bundle. The metal frame was wrapped in aluminium foil and heated for 5 min at 185°C in a forced-air oven type BW91270 (Zwick/Roell GmbH, Ulm, DE), and cooled down at room temperature. The result is a tiny PLA droplet around the single fiber (bundle). After conditioning according to DIN EN ISO 291 [64], the specimens were fixed on a self-manufactured microbond device which was implemented in a Zwick/Roell Z020 testing machine (Zwick/Roell GmbH, Ulm, DE) equipped with a 5 N load cell. The microbond-test was carried out with a testing speed of 1 mm/min at a gauge length of 5 mm. 20 to 24 valid readings were obtained for each fiber type. The IFSS was determined from the maximum force divided by the embedded surface area. The embedded fibre length and fibre width were measured under an optical light microscope to calculate the embedded fibre surface area of the fiber (bundle).
2.5 Scanning Electron Microscopy (SEM)
SEM analyses of selected fiber surfaces and microbond test specimens were done with a SEM type JSM 6510 (Jeol, Eching, Germany) operating with emission electrons. Before the analysis, the samples were sputtered with gold for 90 s under a current of 56 mA with a Bal-Tec sputter coater type SCD 005 (Bal-Tec, Liechtenstein). An accelerating voltage of 10 kV and secondary electrons were used for the experiments.
Before testing, composites were conditioned for at least 18 h in a standard climate according to DIN EN ISO 291 (23°C, 50% relative humidity) [64].
Tensile tests were carried out for 6 test specimens type 1A according to DIN EN ISO 527 [58] with the Zwick Z 020 universal testing machine equipped with a load cell of 20 kN and a pneumatic clamping system. The gauge length was set to 115 mm. After reaching a preload of 20 N, the test was performed at 2 mm/min speed. The elongation was measured with a video extensometer between two measuring marks spaced 80 mm apart (VideoXtens, Zwick/Roell, Ulm, DE). The Young´s modulus was calculated via linear regression between 0.05% and 0.25% elongation.
The unnotched Charpy impact strength was determined with a pendulum impact testing machine (type 5102, Zwick, Ulm, DE) operating with a pendulum hammer of 2 J at a bearing distance of 62.5 mm according to DIN EN ISO 179 [59]. 6 samples per test series were hit on the flatwise impact direction.
The statistical evaluation of the results was done with the open-source software R (http://www.rproject.org/). The results were examined using a Shapiro-Wilk test for normal distribution. The Tukey test was used to evaluate significant differences between results of different samples for normally distributed data with homogenous variances. For data that were not normally distributed, the Wilcoxon test was chosen. All tests were performed with a level of significance α = 0.05. Results are presented as bar plots representing the median value with the mean arithmetic deviation (MAD) as error bars since not all results are normally distributed. Results of Fibershape measurements are shown as Box-Whisker plots showing the median, the Quartile 25, the Quartile 75 and 1.5 times the interquartile length (Whiskers). Significant differences within one series of experiments are marked with different letters above the plots, and an asterisk indicates results that do not follow a normal distribution.
The results of the tensile tests of the different fiber bundle types are shown in Fig. 1. Tensile strength and Young´s modulus of hemp, kenaf, roselle, Fryxell and paper mulberry show similar trends, with the highest values for hemp and the lowest values for paper mulberry. The elongation at break does not show a consistent trend. Hemp and paper mulberry show the lowest values, and kenaf, roselle and Fryxell the highest, which do not differ significantly. While hemp and kenaf do not differ significantly in tensile strength, hemp shows the significantly highest Young’s modulus. Regarding fiber tensile properties, hemp offers the best potential.
Figure 1: Tensile characteristics (tensile strength, Young’s modulus and elongation at break) of bast fiber bundles (median value ± mean arithmetic deviation; different letters indicate significant differences between the test results, a * marks results not subjected to a normal distribution)
The characteristic values of the different fiber types are compared with published data in Table 2, and hemp, kenaf, and roselle data fit well into the ranges mentioned in the literature. For Fryxell, no characteristic values could be found for the Young’s modulus. Wirawan et al. [65] reported a tensile strength of 207 MPa for fiber bundles. This value is within the range of the data obtained in this study. Fineness-specific characteristic values can be found in [50]. Some data were found for paper mulberry. Tensile strength and Young’s modulus are significantly higher than the data measured in this study. One possible reason could be the fact that much coarser fiber bundles were investigated in the present study (size effects). While the tested hemp fiber bundles had an average fiber width of 279 μm, the mean fiber width of paper mulberry was determined to be 356 μm. Fig. 2 shows a typical paper mulberry fiber bundle analysed in the tensile test. The individual fibers in the bundle had already been separated sufficiently and were only connected at individual points. This suggests that the bundle is more susceptible to failure based on the weakest link theory than, for example, a finer fiber bundle in which the individual cells are well connected. This effect has also been demonstrated for jute [66,67], flax and nettle [67]. An increase in fiber cross-sectional area resulted in a decrease in strength [66]. Fig. 3 shows a hemp fiber bundle that is considerably finer. Due to the alkali treatment, the fiber surface is well cleaned. The fiber cells in the bundle appear to be well connected so that a higher tensile load can be absorbed. When testing finer paper mulberry fiber bundles or even single fibers, significantly better tensile characteristics are expected.
Figure 2: SEM micrograph of the surface of a paper mulberry fiber bundle
Figure 3: SEM micrograph of the surface of a hemp fiber bundle
The results of the width measurement of raw fiber(bundle)s are summarized as Box-Whisker plots in Fig. 4. The measurement includes fiber bundles, single fibers, and single cells spliced from the bundle. The median value of paper mulberry is shown to be the lowest. Even though very coarse bundles were tested in the tensile test, Fig. 2 shows that the individual fibers in the bundle have low cohesion, and paper mulberry has the lowest variation in fiber width. Hemp and kenaf do not differ significantly concerning their median values. Nevertheless, the distributions show differences. Overall, the hemp sample has a significantly higher number of finer fibers and fiber bundles than kenaf, while the distributions of kenaf and Fryxell appear to be similar. Fryxell tends to contain some coarser bundles. Roselle has the highest median value but shows a similar distribution to kenaf, with fewer fine individual fibers and fiber bundles in the sample. Table 3 compares the measured median values of the fiber width with published literature values. The literature values include data for single fibers and fiber bundles. Hemp, kenaf, roselle and Fryxell fit very well into the range of the given literature data. For paper mulberry, only one value that refers to a single cell could be found.
Figure 4: Box-Whisker plots of the fiber width of raw bast fiber(bundle)s (different letters indicate significant differences between the test results, a * marks results not subjected to a normal distribution)
The results of the tensile tests of the PLA composites are shown in Fig. 5. The pure PLA matrix was determined to have a median tensile strength of 57.7 ± 1.1 MPa, a mean Young’s modulus of 3.65 ± 0.20 GPa and a mean elongation at break of 3.9% ± 2.2%. With median values of 56 MPa for kenaf/PLA and roselle/PLA and 53 MPa for Fryxell/PLA, no reinforcement could be achieved by the fibers for the tensile strength compared to the pure PLA matrix. On the other hand, with hemp and paper mulberry, an apparent reinforcing effect was achieved with tensile strength values of 70 and 76 MPa, respectively. Concerning Young’s modulus, a clear reinforcement effect could be achieved with all fiber types used. Again, hemp and paper mulberry show the highest reinforcement effect, while kenaf and roselle lead to slightly lower values and Fryxell to significantly lower values. Despite the higher strength and stiffness of kenaf fiber bundles compared to roselle fiber bundles, the tensile properties of kenaf/PLA and roselle/PLA do not differ significantly. It is assumed that the roselle fiber bundles were better separated, and the cohesion of the individual cells in the bundle was lower than that of kenaf, which reduces the characteristic values of the fiber bundle. Due to further separation during processing, the fiber width is significantly reduced, and the cohesion in the bundle plays a minor role. Concerning elongation at break, paper mulberry/PLA tends to show the highest values, hemp/PLA the lowest; kenaf/PLA, roselle/PLA, and Fryxell/PLA range between hemp/PLA and paper mulberry/PLA and do not differ significantly from each other from a statistical point of view.
Figure 5: Tensile characteristics (tensile strength, Young’s modulus and elongation at break) of bast fiber-reinforced PLA composites (median value ± mean arithmetic deviation; different letters indicate significant differences between the test results, a * marks results not subjected to a normal distribution). The values of the neat PLA matrix are shown as dotted line for tensile strength and Young’s modulus. The elongation at break of neat PLA used is 3.9%
Tensile strength and Young’s modulus of the hemp/PLA composite are similar to those reported by Sawpan et al. [81] for injection molded 30 mass-% hemp/PLA (tensile strength 66–76 MPa, Young’s modulus 7.5–8.2 GPa). Chung et al. [82] also determined a similar tensile strength for 30 mass-% kenaf/PLA (58 MPa). No comparative values were found for injection molded roselle/PLA composites. However, one study investigated the use of 30 mass-% roselle in an injection-molded iPP matrix and found values of 35 MPa for tensile strength and 4.8 GPa for tensile modulus (neat iPP matrix: 32 MPa tensile strength, 1.9 GPa Young’s modulus). Other authors processed 30 mass-% roselle with thermosetting plastics and random fiber orientation. For example, a tensile strength of 43, 36, 37 and 31 MPa and a tensile modulus of 1.1, 1.9, 1.1 and 1.2 GPa were achieved in a VE matrix [30–32,83] representing a tensile strength of 18–30 MPa and Young’s modulus of 1.1–1.9 GPa for the neat matrix. Kumar et al. [41] achieved a tensile strength of 49 MPa in a UP matrix, and Sakthi Vadivel et al. [49] a tensile strength of 10 MPa in an epoxy matrix. The data show that the injection-molded material pair roselle/PLA with a tensile strength of 56 MPa and a tensile modulus of 7.3 GPa has potential. The authors are not aware of any characteristic values of composite materials made of Fryxell. For paper mulberry, only one study was found that dealt with the processing of 30 mass-% untreated unidirectional oriented mulberry/isophthalic polyester resin. This composite resulted in tensile strength of 48 MPa and Young’s modulus of 1.1 GPa (values of the neat matrix: 17–20 MPa tensile strength, 0.8–1.1 GPa Young’s modulus) [57]. The results demonstrate that the injection-molded material pair paper mulberry/PLA shows excellent potential, with a tensile strength of 76 MPa and Young’s modulus of 8.0 GPa.
The Charpy impact strength results show the significantly highest values for paper mulberry/PLA. The other composites do not statistically differ significantly from each other (Fig. 6). As visible, the impact strength was not improved by incorporating the bast fibers used. These effects represent the problem of the low impact strength of PLA reinforced with bast fibers which can be explained essentially by the low elongation of the bast fibers and the brittle character of the PLA matrix. Due to the low deformability of the fibers, the fibers can absorb only a small amount of energy through fiber pull-outs during the fracture of the specimen. It is assumed that the higher impact strength of paper mulberry reinforced composites is due to a large number of fine and individually located fibers in the composite. This results in a larger specific fiber surface area and allows higher energy absorption by the fiber pull-outs. To improve the toughness of PLA reinforced with bast fibers, plasticisers in the PLA matrix [84] or the addition of more ductile fibers could significantly increase the impact strength [85].
Figure 6: Unnotched Charpy impact strength of bast fiber-reinforced PLA composites (median value ± mean arithmetic deviation; different letters indicate significant differences between the test results). The dotted line shows the impact strength of the neat PLA matrix
In the overall consideration, the results of the impact tests tend to be slightly higher than data from other injection molded 30 mass-% bast fiber/PLA composites. In an earlier series of experiments, an impact strength of 10.7 kJ/m² was achieved for the pure PLA matrix, 9.4 kJ/m² for a ramie/PLA composite and 7.2 kJ/m² for a hemp/PLA composite (unpublished data). However, it should be noted that the impact strength of the unreinforced PLA in the present study was 15.3 kJ/m² and thus higher than in the previous study with 10.7 kJ/m².
Comparing the tensile properties of the fibers (Fig. 1) and the composites (Fig. 5) shows different trends. The reasons for these differences will be explained in the following.
The IFSS was analyzed using microbond tests and is presented in Fig. 7. Here, the hemp/PLA combination shows the highest characteristic values, which does not contradict the good fiber and composite characteristics. On the other hand, paper mulberry fiber bundles show the lowest tensile strength and Young’s modulus, which contradicts the high strength of the PLA composite. The differences become apparent when comparing tested microbond samples made of hemp/PLA and paper mulberry/PLA. While the surface of the hemp fiber bundles appears relatively smooth, as already described for the fiber bundles from the tensile test (Fig. 8), the individual fibers in the paper mulberry bundles are only loosely connected (Fig. 9). Individual fibers are buckled and reoriented due to fiber pull-out. The interface failure has probably occurred between fiber and matrix and in the bundle due to the loose connection of the individual cells. This effect can lead to lower IFSS and should be considered critically. The characteristic IFSS values of kenaf, roselle and Fryxell are slightly lower than those of hemp, but they are not significantly different from a statistical point of view.
Figure 7: Interfacial shear strength (IFSS) of bast fiber bundles in a PLA matrix measured with microbond tests (median value ± mean arithmetic deviation; different letters indicate significant differences between the test results, a * marks results not subjected to a normal distribution)
Figure 8: SEM micrographs of the surface of a hemp fiber bundle embedded in the PLA matrix after the microbond test; (A) whole sample, (B) surface of the hemp fiber bundle and part of the PLA droplet in pull-out direction, (C) surface of the hemp fiber bundle and part of the PLA droplet in the opposite pull-out direction
Figure 9: SEM micrographs of the surface of a paper mulberry fiber bundle embedded in the PLA matrix after the microbond test; (A) whole sample, (B) surface of the paper mulberry fiber bundle and part of the PLA droplet in pull-out direction, (C) surface of the paper mulberry fiber bundle and part of the PLA droplet in the opposite pull-out direction
Furthermore, the fiber dimensions from extracted composites were analyzed using image analysis. Fig. 10 shows the width, length and aspect ratio (fibre width to fibre length). The width results (Fig. 10A) tend to show a similar trend to those of the measurements on the raw fibers (Fig. 4). However, the values are considerably lower. It can be assumed that the fiber bundles are split during the composite processing and thus are significantly finer. With median values of 20.1, 19.9, 19.0 and 19.0 μm for hemp, kenaf, roselle and Fryxell, respectively, the fiber widths are in a similar range. Paper mulberry has a smaller fiber width of 14.4 μm.
Figure 10: Box-Whisker plots of the fiber dimensions (width (A), length (B) and aspect ratio (C)) of extracted bast fiber bundles (different letters indicate significant differences between the test results, a * marks results not subjected to a normal distribution)
Nevertheless, clear differences can be seen in the Box-Whisker plots concerning the distributions. The hemp sample tends to contain considerably fewer coarse bundles than kenaf, roselle and Fryxell. Paper mulberry shows the least variation in width, as already discussed for the raw fiber(bundle)s. The results of the length measurement show a similar trend as the measurement results of the width. Hemp has the highest median value at 151 μm, and paper mulberry has the lowest with 120 μm (compare Fig. 10B). Kenaf, roselle and Fryxell are in between, having values of 147, 145 and 131 μm, respectively. Due to the processing, the single fibers and fiber bundles were significantly shortened. The native lengths of hemp, for example, were given with 5 to 55 mm for the single fiber [14] and up to 4000 mm for the fiber bundle [71]. For paper mulberry, values of 6.0 to 12.5 mm are found for the single fiber and 20.0 to 45.3 mm for the fiber bundle [53,54,80]. On the other hand, roselle displays significantly shorter lengths for the single fiber (0.7–4.1 mm) [23,27]. The aspect ratio was determined from the length divided by the width of the measured objects (see Fig. 10C). Concerning the aspect ratio, only slight differences between hemp, kenaf, roselle and Fryxell can be observed when looking at the median values (6.4–6.8). Paper mulberry shows the highest value, with 7.8. When the mean value is considered, the characteristic values shift slightly upwards. In this case, hemp, with 8.7 and paper mulberry, with 8.8, show the highest aspect ratios. Kenaf, roselle and Fryxell result in aspect ratios of 7.4, 7.5 and 7.0. It can thus be assumed that hemp and paper mulberry have a larger proportion of fibers having a higher aspect ratio than the other fiber types, which would explain a better reinforcement effect. Combined with the smaller width, which results in a larger bonding area between fiber and matrix, the high tensile strength of the composite reinforced with paper mulberry could be explained. Similarly, the higher specific surface area of the finer fibers leads to more absorbed energy at fracture under impact load explaining the higher Charpy impact strength of paper mulberry/PLA.
The chemical composition of the fibers can also influence fiber/matrix adhesion. Previous studies found that lignin can improve fiber/matrix adhesion, as more interactions with the PLA matrix are possible due to the presence of hydrophobic groups [86]. The determined chemical composition is summarised in Table 4 compared with literature data. It is evident that not all values lie within the range of the literature data. It should be noted that the chemical composition determined can vary considerably from method to method and depending on the preparation of the fibers. In our case, the alkali-treated fibers were examined. Hemp has the highest proportion of cellulose. Despite a lower lignin content, hemp and kenaf have the highest IFSS. It is assumed that structural influences of the fiber surface lead to this effect. Paper mulberry and Fryxell exhibit a high lignin content (Table 4). Even though a low IFSS was found for paper mulberry in the microbond tests due to the problem mentioned above of the low cohesion of the individual cells in the fiber bundle (Fig. 7), a better bonding of the paper mulberry fibers to the matrix may be possible, which in combination with the higher aspect ratio leads to the highest tensile strength in the composite (Fig. 5). The higher aspect ratio can also explain the best impact strength of the composite, as the fiber pull-out of the fine and relatively long fibers can absorb more energy than coarser fiber bundles with a lower specific surface area. Due to the short fiber length in the composite, all composites have lower elongation values than the individual components of the material. Overall, the mechanical properties of all composites investigated could be significantly enhanced if longer fibers could be incorporated.
In the present study, different bast fibers from typical Thai bast fiber plants were used to evaluate their potential for use in injection molded fiber-reinforced PLA composites. The mechanical properties and the width distributions of hemp, kenaf, roselle, Fryxell and paper mulberry fiber bundles were analysed. The hemp fiber bundles showed the highest tensile strength and the highest Young´s modulus, followed by kenaf, roselle, Fryxell and paper mulberry. The IFSS between fiber bundles and PLA matrix reflected the same trend. Despite these results, the highest tensile strength for the composites was found for paper mulberry/PLA followed by hemp/PLA. Hemp/PLA reached the best value for the Young’s modulus, followed by paper mulberry/PLA. Kenaf/PLA and roselle/PLA were comparable in terms of both properties, despite the better fiber properties of kenaf; Fryxell/PLA shows lower characteristic values. Further structural analyses were carried out to find out why paper mulberry leads to good tensile properties in composites. It turned out that the fiber bundles of paper mulberry tested in the fiber tensile test were significantly coarser and the cohesion of the single fibers in the bundle was low. On the one hand, the significantly lower tensile properties of the fiber bundles can be attributed to size effects and, on the other hand, to the limited cohesion of the individual fibers in the bundle. The limited length of the individual cells increases the probability of slipping off each other during the fiber tensile test under less force than in fiber bundles in which the individual cells are well adhered to each other. Furthermore, paper mulberry represented the highest aspect ratio of fibers extracted from the composite, followed by hemp. The measured fiber width was also smaller, resulting in a larger specific fiber surface area in the composite for the matrix to bond to the fiber. Overall, it can be concluded that the Thai bast fibers investigated can be well used for composite applications, with paper mulberry and hemp offering the greatest potential of the variants examined. Paper mulberry fibers show an exciting reinforcement potential in composite materials. The potential of these fibers should be evaluated in further studies in the future. For example, the availability, price and, most importantly, the environmental footprint of extracting and processing these fibers should be investigated.
Acknowledgement: We would like to thank Vincent Röhl (HSB, The Biological Materials Group, Bremen, Germany) for the fiber extraction and Hansjörg Wieland (3 N, Werlte, Germany) for the production of the granules. The authors would also like to thank the Bremen State and University Library (Bremen, Germany) for funding the open access publication fee.
Funding Statement: The present work was funded within the framework of the BMBF Exchange Project “Thai-German Agro-Based Fiber Exchange Programme-Sustainable Development: From Plant to Product (Acronym: AgroFiber)” under Registration No. 01DP15016.
Conflicts of Interest: The authors declare that they have no conflicts of interest to report regarding the present study.
References
1. Rattana, S., Gheewala, S. H. (2019). Environment impacts assessment of petroleum plastic and bioplastic carrier bags in Thailand. Journal of Sustainable Energy & Environment, 10, 9–17. [Google Scholar]
2. Wichai-utcha, N., Chavalparit, O. (2019). 3Rs policy and plastic waste management in Thailand. Journal of Material Cycles and Waste Management, 21(1), 10–22. DOI 10.1007/s10163-018-0781-y. [Google Scholar] [CrossRef]
3. Gupta, A. K., Kumar, V. (2007). New emerging trends in synthetic biodegradable polymers–polylactide: A critique. European Polymer Journal, 43, 4053–4074. DOI 10.1016/j.eurpolymj.2007.06.045. [Google Scholar] [CrossRef]
4. Sudamrao Getme, A., Patel, B. (2020). A review: Bio-fiber™ as reinforcement in composites of polylactic acid (PLA). Materials Today: Proceedings, 26, 2116–2122. [Google Scholar]
5. Raj, S., Kannan, T., Babu, M., Vairavel, M. (2019). Processing and testing parametes of PLA reinforced with natural plant fiber composite materials—A brief review. International Journal of Mechanical and Production Engineering Research and Development, 9, 933–940. [Google Scholar]
6. Pappu, A., Pickering, K. L., Thakur, V. K. (2019). Manufacturing and characterization of sustainable hybrid composites using sisal and hemp fibres as reinforcement of poly (lactic acid) via injection moulding. Industrial Crops and Products, 137, 260–269. DOI 10.1016/j.indcrop.2019.05.040. [Google Scholar] [CrossRef]
7. Tümer, E. H., Yildirim Erbil, H. (2021). Extrusion-based 3D printing applications of PLA composites: A review. Coatings, 11(4), 390. DOI 10.3390/coatings11040390. [Google Scholar] [CrossRef]
8. Sengloung, T., Kaveeta, L., Müssig, J. (2008). Physical properties of traditional Thai hemp fiber (Cannabis sativa L.). Journal of Industrial Hemp, 13(1), 20–36. DOI 10.1080/15377880801898709. [Google Scholar] [CrossRef]
9. Sadrmanesh, V., Chen, Y. (2019). Bast fibres: Structure, processing, properties, and applications. International Materials Reviews, 64(7), 381–406. DOI 10.1080/09506608.2018.1501171. [Google Scholar] [CrossRef]
10. Amaducci, S., Scordia, D., Liu, F. H., Zhang, Q., Guo, H. et al. (2014). Key cultivation techniques for hemp in Europe and China. Industrial Crops and Products, 68, 2–16. DOI 10.1016/j.indcrop.2014.06.041. [Google Scholar] [CrossRef]
11. Shahzad, A. (2012). Hemp fiber and its composites–A review. Journal of Composite Materials, 46(8), 973–986. DOI 10.1177/0021998311413623. [Google Scholar] [CrossRef]
12. Müssig, J., Haag, K., Musio, S., Bjelková, M., Albrecht, K. et al. (2020). Biobased ‘mid-performance’ composites using losses from the hackling process of long hemp–A feasibility study as part of the development of a biorefinery concept. Industrial Crops and Products, 145, 111938. DOI 10.1016/j.indcrop.2019.111938. [Google Scholar] [CrossRef]
13. Rehman, M., Fahad, S., Du, G., Cheng, X., Yang, Y. et al. (2021). Evaluation of hemp (Cannabis sativa L.) as an industrial crop: A review. Environmental Science and Pollution Research, 28(38), 52832–52843. [Google Scholar]
14. Manaia, J. P., Manaia, A. T., Rodriges, L. (2019). Industrial hemp fibers: An overview. Fibers, 7(12), 1–16. DOI 10.3390/fib7120106. [Google Scholar] [CrossRef]
15. Aji, I. S., Sapuan, S. M., Zainudin, E. S., Abdan, K. (2009). Kenaf fibres as reinforcement for polymeric composites: A review. International Journal of Mechanical and Materials Engineering, 4(3), 239–248. [Google Scholar]
16. Ramesh, M. (2016). Kenaf (Hibiscus cannabinus L.) fibre based bio-materials: A review on processing and properties. Progress in Materials Science, 78–79, 1–92. DOI 10.1016/j.pmatsci.2015.11.001. [Google Scholar] [CrossRef]
17. Ayadi, R., Hanana, M., Mzid, R., Hamrouni, L., Khouja, M. l. et al. (2017). Hibiscus cannabinus L.–kenaf: A review paper. Journal of Natural Fibers, 14(4), 466–484. [Google Scholar]
18. Bourmaud, A., Beaugrand, J., Shah, D. U., Placet, V., Baley, C. (2018). Towards the design of high-performance plant fibre composites. Progress in Materials Science, 97, 347–408. DOI 10.1016/j.pmatsci.2018.05.005. [Google Scholar] [CrossRef]
19. Inder Preet Singh, J., Singh, S., Dhawan, V., Pannu, A. S., Bahl, A. et al. (2021). Kenaf-fiber-based bio-materials: A review on processing and mechanical properties. In: Parey, A., Kumar, R., Singh, M. (Eds.Recent trends in engineering design, pp. 87–94. Singapore: Springer. [Google Scholar]
20. Ilyas, R. A., Sapuan, S. M., Kirubaanand, W., Zahfiq, Z. M., Atikah, M. S. N. et al. (2021). Chapter 1-Roselle: Production, product development, and composites. In: Sapuan, S. M., Nadlene, R., Radzi, A. M., Ilyas, R. A. (Eds.Roselle, pp. 1–23. London: Academic Press. [Google Scholar]
21. Nadlene, R., Sapuan, S. M., Jawaid, M., Ishak, M. R., Yusriah, L. (2016). A review on roselle fiber and its composites. Journal of Natural Fibers, 13(1), 10–41. DOI 10.1080/15440478.2014.984052. [Google Scholar] [CrossRef]
22. Thiruchitrambalam, M., Athijayamani, A., Sathiyamurthy, S., Syed Abu Thaheer, A. (2010). A review on the natural fiber-reinforced polymer composites for the development of roselle fiber-reinforced polyester composite. Journal of Natural Fibers, 7(4), 307–323. DOI 10.1080/15440478.2010.529299. [Google Scholar] [CrossRef]
23. Crane, J. C. (1949). Roselle: A potentially important plant fiber. Economic Botany, 3(1), 89–103. DOI 10.1007/BF02859509. [Google Scholar] [CrossRef]
24. Wilson, F. D. (1967). An evaluation of kenaf, roselle, and related hibiscus for fiber production. Economic Botany, 21(2), 132–139. DOI 10.1007/BF02897861. [Google Scholar] [CrossRef]
25. Nadlene, R., Sapuan, S. M., Jawaid, M., Ishak, M. R., Yusriah, L. (2015). Material characterization of roselle fibre (Hibiscus sabdariffa L.) as potential reinforcement material for polymer composites. Fibres & Textiles in Eastern Europe, 114(6), 23–30. [Google Scholar]
26. Junkasem, J., Menges, J., Supaphol, P. (2006). Mechanical properties of injection-molded isotactic polypropylene/roselle fiber composites. Journal of Applied Polymer Science, 101(5), 3291–3300. DOI 10.1002/(ISSN)1097-4628. [Google Scholar] [CrossRef]
27. Naraprateep, T. (2007). Effect of compatibilizer and silanecoupling agents on physical properties of natural fiber-polypropylene composites (Master Thesis). Suranaree University of Technology, Thailand. [Google Scholar]
28. Manickam, C., Kumar, J., Athijayamani, A., Karthik, K. (2015). Modeling and multiresponse optimization of the mechanical properties of roselle fiber-reinforced vinyl ester composite. Polymer-Plastics Technology and Engineering, 54(16), 1694–1703. DOI 10.1080/03602559.2015.1036438. [Google Scholar] [CrossRef]
29. Nallusamy, S. (2016). Analysis of mechanical properties on roselle fibre with polymer matrix reinforced composite. Advanced Engineering Forum, 16, 1–6. DOI 10.4028/www.scientific.net/AEF.16.1. [Google Scholar] [CrossRef]
30. Manickam, C., Kumar, J., Athijayamani, A., Diwahar, N. (2015). Mechanical and wear behaviors of untreated and alkali treated roselle fiber-reinforced vinyl ester composite. Journal of Engineering Research, 3(3), 98–109. DOI 10.7603/s40632-015-0025-4. [Google Scholar] [CrossRef]
31. Navaneethakrishnan, S., Sivabharathi, V., Ashokraj, S. (2021). Weibull distribution analysis of roselle and coconut-shell reinforced vinylester composites. Australian Journal of Mechanical Engineering, 19(4), 457–466. DOI 10.1080/14484846.2019.1637089. [Google Scholar] [CrossRef]
32. Ramakrishnan, M., Ramasubramanian, S., Subbarayalu, V., Ayyanar, A. (2021). Study of mechanical properties of roselle fiber reinforced vinyl ester biocomposite based on the length and content of fiber. Mechanika, 27(33), 265–269. DOI 10.5755/j02.mech.26603. [Google Scholar] [CrossRef]
33. Mubarak Kazi, A., Devika D., Waddar, S., Ramasastry, D. V. A. (2021). Characterization of roselle fiber composites for low load bearing structures. Polymer Composites, 42(5), 2589–2597. DOI 10.1002/pc.26004. [Google Scholar] [CrossRef]
34. Manickam, C., Kumar, J., Athijayamani, A., Easter Samuel, J. (2015). Effect of various water immersions on mechanical properties of roselle fiber-vinyl ester composites. Polymer Composites, 36(9), 1638–1646. DOI 10.1002/pc.23072. [Google Scholar] [CrossRef]
35. Radzi, A. M., Sapuan, S. M., Jawaid, M., Mansor, M. R. (2019). Water absorption, thickness swelling and thermal properties of roselle/sugar palm fibre reinforced thermoplastic polyurethane hybrid composites. Journal of Materials Research and Technology, 8(5), 3988–3994. DOI 10.1016/j.jmrt.2019.07.007. [Google Scholar] [CrossRef]
36. Singha, A. S., Thakur, V. K. (2008). Mechanical properties of natural fibre reinforced polymer composites. Bulletin of Materials Science, 31(5), 791–799. DOI 10.1007/s12034-008-0126-x. [Google Scholar] [CrossRef]
37. Ain, S. N., Nadlene, R., Ilyas, R. A., Radzi, A. M., Sivakumar, D. (2021). Chapter 14-The effect of fiber length on mechanical and thermal properties of roselle fiber-reinforced polylactic acid composites via Ansys software analysis. In: Sapuan, S. M., Nadlene, R., Radzi, A. M., Ilyas, R. A. (Eds.Roselle, pp. 215–235. London: Academic Press. [Google Scholar]
38. Azeez, T., Onukwuli, O. (2018). Properties of white roselle (Hibiscus sabdariffa) fibers. Journal of Scientific and Industrial Research, 77, 525–532. [Google Scholar]
39. Chauhan, A., Kaith, B. (2012). Accreditation of novel roselle grafted fiber reinforced bio-composites. Journal of Engineered Fibers and Fabrics, 7, 66–75. DOI 10.1177/155892501200700210. [Google Scholar] [CrossRef]
40. Chauhan, A., Kaith, B. (2012). Versatile roselle graft-copolymers: XRD studies and their mechanical evaluation after use as reinforcement in composites. Journal of the Chilean Chemical Society, 57, 1262–1266. DOI 10.4067/S0717-97072012000300014. [Google Scholar] [CrossRef]
41. Kumar, T. V., Chandrasekaran, M., Vivek, P., Arunkumar, S., Padmanabhan, S. (2019). Mechanical characterization of roselle and sisal fibre reinforced polymer composites. International Journal of Vehicle Structures & Systems, 11(2), 203–208. [Google Scholar]
42. Hamdan, M. H. M., Siregar, J. P., Thomas, S., John Jacob, M., Jaafar, J. et al. (2019). Mechanical performance of hybrid woven jute-roselle-reinforced polyester composites. Polymers and Polymer Composites, 27(7), 407–418. DOI 10.1177/0967391119847552. [Google Scholar] [CrossRef]
43. Chandramohan, D., Bharanichandar, J. (2013). Natural fiber reinforced polymer composites for automobile accessories. American Journal of Environmental Sciences, 9, 494–504. DOI 10.3844/ajessp.2013.494.504. [Google Scholar] [CrossRef]
44. Athijayamani, A., Thiruchitrambalam, M., Natarajan, U., Pazhanivel, B. (2009). Effect of moisture absorption on the mechanical properties of randomly oriented natural fibers/polyester hybrid composite. Materials Science and Engineering: A, 517(1), 44–353. [Google Scholar]
45. Athijayamani, A., Thiruchitrambalam, M., Natarajan, U., Pazhanivel, B. (2010). Influence of alkali-treated fibers on the mechanical properties and machinability of roselle and sisal fiber hybrid polyester composite. Polymer Composites, 31(4), 723–731. [Google Scholar]
46. Athijayamani, A., Thiruchitrambalam, M., Manikandan, V., Pazhanivel, B. (2010). Mechanical properties of natural fibers reinforced polyester hybrid composite. International Journal of Plastics Technology, 14(1), 104–116. DOI 10.1007/s12588-009-0016-0. [Google Scholar] [CrossRef]
47. Vinod, B., Anandajothi, M. (2020). Mechanical and tribological properties of abaca-roselle/cardanol formaldehyde hybrid composites. Materials Research Express, 6(12), 125363. DOI 10.1088/2053-1591/ab66fa. [Google Scholar] [CrossRef]
48. Radzi, A. M., Sapuan, S. M., Jawaid, M., Mansor, M. R. (2018). Mechanical performance of roselle/sugar palm fiber hybrid reinforced polyurethane composites. BioResources, 13(3), 6238–6249. DOI 10.15376/biores. [Google Scholar] [CrossRef]
49. Sakthi Vadivel, K., Vigneshwaran, K., Sivaraj, C. (2021). Study on the mechanical properties of roselle fiber and palm seed powder reinforced epoxy hybrid composite. Journal of Manufacturing Engineering, 16(1), 001–006. DOI 10.37255/jme.v16i1pp001-006. [Google Scholar] [CrossRef]
50. Gama Guimarães, B. M., Cayuela Marn, D., Fernando Zonatti, W., Mantovani, W., Relvas, C. et al. (2016). Study of the potential employment of Malvaceae species in composites materials. conventional materials and technologies for sustainable development. In: Key engineering materials, pp. 75–85. Switzerland: Trans Tech Publications, Ltd. [Google Scholar]
51. Jin, Z., Jin, G., Shao, S., Katsumata, K. S. (2012). Lignin characteristics of bast fiber and core in kenaf, bark and wood of paper mulberry and mulberry. Journal of Wood Science, 58(2), 144–152. DOI 10.1007/s10086-011-1228-4. [Google Scholar] [CrossRef]
52. Seo, Y., Hwang, B. (2019). Mulberry-paper-based composites for flexible electronics and energy storage devices. Cellulose, 26(16), 8867–8875. DOI 10.1007/s10570-019-02686-5. [Google Scholar] [CrossRef]
53. Qu, L., Tian, M., Guo, X., Pan, N., Zhang, X. et al. (2014). Preparation and properties of natural cellulose fibres from Broussonetia papyrifera (L.) Vent. Bast. Fibres & Textiles in Eastern Europe, 4(106), 24–28. [Google Scholar]
54. Chonsakorn, S., Piromthamsiri, K., Sirikasemlert, C. (2014). Physical properties of woven fabric from paper mulberry yarn. Materials Engineering and Technology, 849, 157–161. [Google Scholar]
55. Hwang, S., Kim, H. (2019). Studies on the characteristics of CNF from paper mulberry bast fiber. Journal of Korea Technical Association of the Pulp and Paper Industry, 51, 88–99. DOI 10.7584/JKTAPPI.2019.04.51.2.88. [Google Scholar] [CrossRef]
56. Ohsawa, I., Uzawa, K., Kanai, M., Murayama, H., Kageyama, K. (2007). Tensile properties of Washi-paper reinforced polylactic acid (PLA) as a green composites. 10th Japan International SAMPE Symposium & Exhibition (JISSE-10), pp. 1–6. Tokyo, Japan. [Google Scholar]
57. Shanmugasundaram, N., Rajendran, I., Ramkumar, T. (2018). Static, dynamic mechanical and thermal properties of untreated and alkali treated mulberry fiber reinforced polyester composites. Polymer Composites, 39(S3), E1908–E1919. DOI 10.1002/pc.24890. [Google Scholar] [CrossRef]
58. Deutsches Institut für Normung. DIN EN ISO 527-2:1996. Plastics–Determination of tensile properties–Part 2: Test conditions for moulding and extrusion plastics (2010). [Google Scholar]
59. Deutsches Institut für Normung. DIN EN ISO 179-1 Plastics–Determination of Charpy impact properties–Part 1: Non-instrumented impact test (2010). [Google Scholar]
60. Müssig, J., Graupner, N. (2013). Injection moulded hemp fibre-reinforced thermoplastics. 10th International Conference of the European Industrial Hemp Association, pp. 1–30. Hürth, Germany. [Google Scholar]
61. Deutsches Institut für Normung. DIN EN ISO 139:2005–Textiles–Standard atmospheres for conditioning and testing (2005). [Google Scholar]
62. Van Soest, P. J. (1963). Use detergents in the analysis of fibrous feeds II. A rapid method for the determination of fibre and lignin. Journal-Association of Official Analytical Chemists, 46, 829–835 [Google Scholar]
63. Müssig, J., Graupner, N. (2020). Test methods for fibre/matrix adhesion in cellulose fibre-reinforced thermoplastic composite materials: A critical review. Reviews of Adhesion and Adhesives, 8(2), 68–129. DOI 10.7569/RAA.2020.097306. [Google Scholar] [CrossRef]
64. Deutsches Institut für Normung. DIN EN ISO 291:2005–Plastics–Standard atmospheres for conditioning and testing (2006). [Google Scholar]
65. Wirawan, W. A., Choiron, M. A., Siswanto, E., Widodo, T. D. (2022). Morphology, structure, and mechanical properties of new natural cellulose fiber reinforcement from waru (Hibiscus tiliaceus) bark. Journal of Natural Fibers, 1–13. DOI 10.1080/15440478.2022.2060402. [Google Scholar] [CrossRef]
66. Xia, Z. P., Chen, L. D., Liu, L. F., Wang, W. M. (2009). Study on the breaking strength of jute fibres using modified Weibull distribution. Composites Part A-Applied Science and Manufacturing, 40, 54–59. DOI 10.1016/j.compositesa.2008.10.001. [Google Scholar] [CrossRef]
67. Summerscales, J., Hall, W., Singh Virk, A. (2011). A fibre diameter distribution factor (FDDF) for natural fibre composites. Journal of Materials Science, 46(17), 5876–5880. DOI 10.1007/s10853-011-5569-6. [Google Scholar] [CrossRef]
68. Abdul Khalil, H. P. S., Ireana Yusra, A. F., Bhat, A. F., Jawaid M, A. H. (2010). Cell wall ultrastructure, anatomy, lignin distribution, and chemical composition of Malaysian cultivated kenaf fiber. Industrial Crops and Products, 31(1), 113–121. DOI 10.1016/j.indcrop.2009.09.008. [Google Scholar] [CrossRef]
69. Sreenivas, H. T., Krishnamurthy, N., Arpitha, G. R. (2020). A comprehensive review on light weight kenaf fiber for automobiles. International Journal of Lightweight Materials and Manufacture, 3(4), 328–337. DOI 10.1016/j.ijlmm.2020.05.003. [Google Scholar] [CrossRef]
70. Jariwala, H., Jain, P. (2019). A review on mechanical behavior of natural fiber reinforced polymer composites and its applications. Journal of Reinforced Plastics and Composites, 38(10), 441–453. DOI 10.1177/0731684419828524. [Google Scholar] [CrossRef]
71. Gholampour, A., Ozbakkaloglu, T. (2020). A review of natural fiber composites: Properties, modification and processing techniques, characterization, applications. Journal of Materials Science, 55(3), 829–892. DOI 10.1007/s10853-019-03990-y. [Google Scholar] [CrossRef]
72. Lotfi, A., Li, H., Viet Dao, D., Prusty, G. (2019). Natural fiber-reinforced composites: A review on material, manufacturing, and machinability. Journal of Thermoplastic Composite Materials, 34(2), 238–284. DOI 10.1177/0892705719844546. [Google Scholar] [CrossRef]
73. Kurien, R. A., Santhosh, A., Paul, D., Kurup, G. B., Reji, G. S. (2021). A review on recent developments in kenaf, sisal, pineapple, bamboo and banana fiber-reinforced composites. In: Patnaik, A., Kozeschnik, E., Kukshal, V. (Eds.Advances in Materials Processing and Manufacturing Applications, pp. 301–310. Singapore: Springer. [Google Scholar]
74. Hamidon, M. H., Sultan, M. T. H., Ariffin, A. H., Shah, A. U. M. (2019). Effects of fibre treatment on mechanical properties of kenaf fibre reinforced composites: A review. Journal of Materials Research and Technology, 8(3), 3327–3337. DOI 10.1016/j.jmrt.2019.04.012. [Google Scholar] [CrossRef]
75. Chandramohan, D., Marimuthu, K. (2011). A review on natural fibers. International Journal of Research & Reviews in Applied Sciences, 8(2), 194–206. [Google Scholar]
76. Razali, N., Sapuan Salit, M., Jawaid, M., Ridzwan Ishak, M., Lazim, Y. (2015). A study on chemical composition, physical, tensile, morphological, and thermal properties of roselle fibre: Effect of fibre maturity. BioResources, 10(1), 1803–1824. DOI 10.15376/biores.10.1.1803-1824. [Google Scholar] [CrossRef]
77. Mazian, B., Bergeret, A., Benezet, J. C., Malhautier, L. (2019). A comparative study of the effect of field retting time on the properties of hemp fibres harvested at different growth stages. Fibers, 7(12), 108. DOI 10.3390/fib7120108. [Google Scholar] [CrossRef]
78. Karimah, A., Rasyidur Ridho, M., Munawar, S. S., Sudarwoko Adi, D., Ismadi, R. D. et al. (2021). A review on natural fibers for development of eco-friendly bio-composite: Characteristics, and utilizations. Journal of Materials Research and Technology, 13, 2442–2458. DOI 10.1016/j.jmrt.2021.06.014. [Google Scholar] [CrossRef]
79. Sari, N. H., Padang, Y. A. (2019). The characterization tensile and thermal properties of Hibiscus tiliaceus cellulose fibers. IOP Conference Series: Materials Science and Engineering, 539(1), 012031. DOI 10.1088/1757-899X/539/1/012031. [Google Scholar] [CrossRef]
80. Bledzki, A., Sperber, V., Faruk, O. (2002). Natural and wood fibre reinforcement in polymers. Shropshire, UK: Rapra Technology, Ltd. [Google Scholar]
81. Sawpan, M. A., Pickering, K. L., Fernyhough, A. (2011). Improvement of mechanical performance of industrial hemp fibre reinforced polylactide biocomposites. Composites Part A–Applied Science and Manufacturing, 42(3), 310–319. DOI 10.1016/j.compositesa.2010.12.004. [Google Scholar] [CrossRef]
82. Chung, T. J., Park, J. W., Lee, H. J., Kwon, H. J., Kim, H. J. et al. (2018). The improvement of mechanical properties, thermal stability, and water absorption resistance of an eco-friendly PLA/kenaf biocomposite using acetylation. Applied Sciences, 8(3), 376. DOI 10.3390/app8030376. [Google Scholar] [CrossRef]
83. Razali, N., Sapuan, S. M., Jawaid, M., Ridzwan Ishak, M., Lazim, Y. (2016). Mechanical and thermal properties of roselle fibre reinforced vinyl ester composites. BioResources, 11(4), 9325–9339. [Google Scholar]
84. Scaffaro, R., Morreale, M., Mirabella, F., La Mantia, F. P. (2011). Preparation and recycling of plasticized PLA. Macromolecular Materials and Engineering, 296(2), 141–150. DOI 10.1002/mame.201000221. [Google Scholar] [CrossRef]
85. Graupner, N., Müssig, J. (2012). The influence of lyocell and kenaf fibres on the mechanical characteristics of poly(lactic acid) (PLA) composites. Journal of Biobased Materials and Bioenergy, 6(4), 500–507. DOI 10.1166/jbmb.2012.1239. [Google Scholar] [CrossRef]
86. Graupner, N. (2008). Application of lignin as natural adhesion promoter in cotton fibre-reinforced poly(lactic acid) (PLA) composites. Journal of materials science, 43(15), 5222–5229. DOI 10.1007/s10853-008-2762-3. [Google Scholar] [CrossRef]
87. Zhang, X., Qu, L. J., Qing Guo, X. (2011). Study on structure and property of Broussonetia papyrifera (BP) fiber. In: Advanced materials research, pp. 1593–1596. Switzerland: Trans Tech Publications, Ltd. [Google Scholar]
Cite This Article
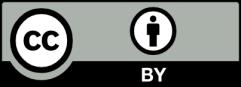