Open Access
ARTICLE
Multifunctional Lubricant Additive Improves Lubrication and Antioxidation Properties of Tung Oil
1
Institute of Chemical Industry of Forest Products, CAF, National Engineering Laboratory for Biomass Chemical Utilization, Key
Laboratory of Chemical Engineering of Forest Products, National Forestry and Grassland Administration, Key Laboratory of
Biomass Energy and Material of Jiangsu Province, Jiangsu Co-Innovation Center of Efficient Processing and Utilization of Forest
Resources, Nanjing, 210042, China
2
Institute of Ecological Conservation and Restoration, CAF, Beijing, 100091, China
* Corresponding Author: Haiyang Ding. Email:
Journal of Renewable Materials 2023, 11(7), 3115-3128. https://doi.org/10.32604/jrm.2023.026823
Received 27 September 2022; Accepted 07 December 2022; Issue published 05 June 2023
Abstract
It is of considerable significance to develop efficient and environmentally friendly machinery lubricant additives because of the increasing depletion of petrochemical resources and severe environmental problems. Herein, we proposed a facile strategy to synthesize a multifunctional vegetable oil-based lubricant via the lignin derivative vanillin coupled to amine and diethyl phosphite to produce a lubricating additive with both extreme pressure and antioxidant properties. Compared with pure tung oil, the lubricating and antioxidant performance of tung oil is significantly improved after adding additives. Adding the 1.0 wt% additive to the tung oil reduced the friction wear coefficient and the volume, and the oxidation induction time was much longer than pure tung oil.Graphical Abstract
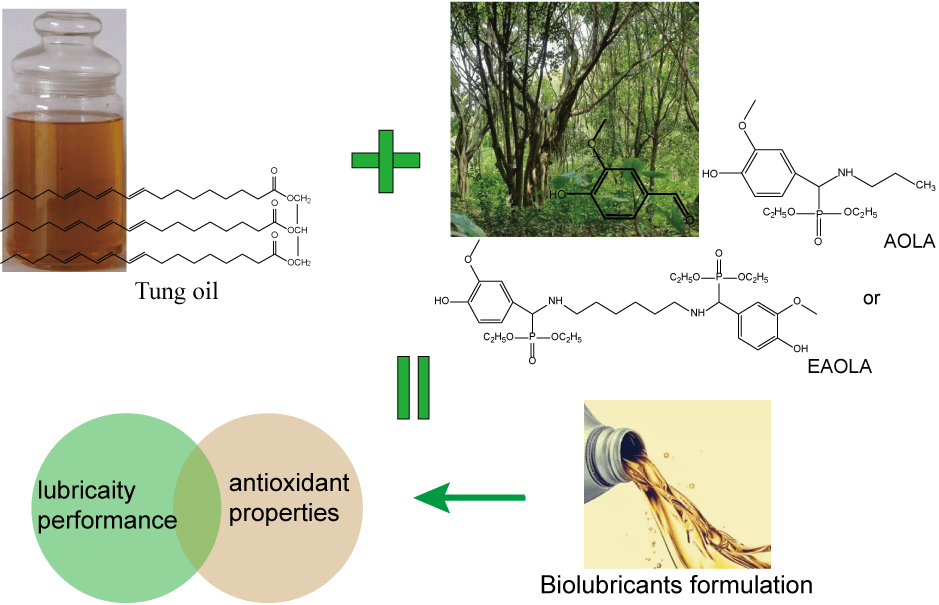
Keywords
Wear caused by friction is the main cause of failure of mechanical parts, and lubrication is the most effective measure to reduce friction and wear [1–3]. Therefore, lubricants play a vital role in the development of world industry and economy. In recent years, with the rapid improvement of the capacity of the global high-end equipment manufacturing industry and the high attention paid by the whole society to environmental protection issues, people have increasingly high requirements for high efficiency, long cycle, degradability, harmless, and other operational performance of lubricating oil [4,5]. Traditional petroleum-based mineral oil has weakened cost advantages and limited biodegradation and service performance, causing it to face the pressure of resources and environmental protection.
Vegetable oils are potential substitutes for petroleum-based oils. It is not only environmentally friendly, renewable, less toxic, and degradable, but also has excellent properties such as high viscosity index, high lubricity, and low volatility [6–8]. The main reason why vegetable oil can be used as an anti-wear additive and friction modifier is the existence of a long fatty acid chain and polar group, which makes them have a good film/force relationship and can be used as boundary lubricants [9,10]. In addition, the structure of triglycerides in vegetable oils ensures their lubricity as a lubricant. Therefore, vegetable oil-based lubricants have received a great demand in many green manufacturing activities, and have become an important research topic in recent years [11–14]. China is the largest producer of tung oil, but the utilization level of tung oil is very low, mainly focusing on the direct use of tung oil as anti-corrosion coatings, ink additives, and mold release oils [15–18]. As an excellent non-edible drying oil, tung oil can avoid competition with feed and food resources as a biological lubricant. Furthermore, tung oil has the characteristics of good glossiness, strong adhesion, acid resistance, alkali resistance, heat resistance, and corrosion resistance. Therefore, it has potential application value as a lubricant [19]. Based on this, we apply tung oil to the research in the field of lubricants, which can not only improve the added value of tung oil products but also further expand its scope of use.
However, when tung oil is used as the base oil of lubricant, it also has the same fatal defect as other vegetable oils. The fatty acid part of tung oil molecules is rich in unsaturated bonds (C=C), which is extremely vulnerable to free radical attack and further oxidative degradation to form the polar oxygen-containing compound [20]. This phenomenon can lead to the formation of insoluble deposits, increase the acidity and viscosity of the oil, and ultimately seriously affect the service life of mechanical equipment, even causing severe corrosion and wear. In order to avoid or delay the problem of lubricating oil, which needs to have good oxidation stability. Therefore, antioxidants are a key additive to prevent oxidative degradation from meeting the industrial application requirements of vegetable oils as lubricants [21,22]. Nevertheless, as people’s requirements for high speed and load efficiency are getting higher and higher, a single antioxidant additive can no longer meet people’s requirements. Sliding friction between mechanical equipment under heavy load and high speed makes mechanical wear faster. After adding extreme pressure lubricant additives, extreme pressure additives can be used to form extreme pressure films on the metal surface to separate the two friction surfaces to reduce the friction coefficient and slow down wear to achieve the purpose of lubrication.
Based on the ability to meet the requirements of tung oil as a lubricant oil with both oxidation stability and extreme pressure properties. In this work, vanillin, the only industrial-scale monoaromatic compound produced in lignin, was used as an antioxidant for asymmetric hindered phenolic. The steric hindrance effect of asymmetric hindered phenolic antioxidants is weak, and the antioxidant effect is more significant than that of traditional symmetrical antioxidants. Theoretically, when the ortho-position of the phenolic hydroxyl group is a bulky substituent, it is beneficial to protect the phenolic hydroxyl group from rapid oxidation and reduce charge transfer, thereby improving the antioxidant efficiency and compatibility with base oils [23,24]. Therefore, we use amine as a coupling agent, and the Schiff base intermediate generated by the coupling reaction of vanillin and amine is not extracted from the system and further reacts directly with diethyl phosphite to obtain phosphorus-containing bifunctional additive for oxidation stability and extreme pressure properties, which is added to the tung oil. Exploring the lubrication and antioxidant mechanism of lubricating additives through experiments and a variety of characterization means is conducive to laying the theoretical foundation for the design and application of bio-based lubricating oil, and meeting the needs of the green, efficient and coordinated development of lubricating oil technology.
This study used environmentally friendly based oil tung oil (TO), a commercial-grade oil supplied by the Luodian County Anling Vegetable Oil Plant, China, without further purification. The structural formula of tung oil is shown in Fig. 1. Vanillin, n-propylamine, Ethylenediamine, 1,3-Diaminopropane, 1,6-Hexamethylenediamine, and Diethyl phosphite, were purchased from Aladdin-Reagent Co., China. Zinc chloride and ethanol were bought from Sinopharm Chemical Reagent Co., China.
Figure 1: Chemical formula of base oil
2.2 Synthesis of Lubrication Additives
Vanillin is coupled to diamine by Schiff base reaction. The obtained Schiff base further reacts with diethyl phosphonate through a phosphorus hydrogen addition reaction to generate phosphorus-containing lubrication additives AOLA and EAOLA [25]. Notably, the formation of the Schiff base and the phosphorus hydrogen addition reaction is completed by one-pot synthesis, where the Schiff base produced during the reaction does not need to be extracted from the system. Detailed synthetic routes as illustrated in Scheme 1. Two kinds of phosphorus-containing lubrication additives AOLA and EAOLA were added to tung oil to study their antioxidant and lubrication properties.
Scheme 1: Preparation of two bio-based multifunctional lubrication additives
FTIR was recorded on Nicolet 6700, with a recording range of 4000–400 cm−1. Proton nuclear magnetic resonance (1H NMR) was recorded by a Bruker 400MHZ AVANCE III spectrometer with CDCl3 as solvent. The TGA was tested on TGA/DSC in Mettler Toledo from room temperature to 800°C, the heating rate of 10 °C/min, and the sample mass was 3–5 mg.
The maximum non-seizure load (PB) was measured using an MRS-10A four-ball tribometer according to the standard method GB/T 3142-82, which is similar to ASTM D2783 [26].
On the MRS-1J four-ball friction meter, the anti-friction and anti-wear properties were evaluated at 1450 rpm, 30 min, and room temperature [27]. Each data was the average from triplicated tests. The coefficient of friction was automatically recorded using a sensor connected to a PC. The wear scar diameters (WSD) were measured using an optical microscope [28]. Repeat to measure the average value of each sample. Wear volume (WV) provided further support for anti-wear behaviors; WV was calculated through the following formula:
where r is the radius of the steel ball, and d is WSD [29]. The balls used in the test are 12.7 mm in diameter and made of GCr 15-bearing steel with an HRC of 59–61 hardness.
To analyze the morphology and wear degree of the wear surface, the FEI Quanta 200 scanning electron microscope (SEM, FEI Co., Ltd., Hillsboro, USA) was used. It can provide more intuitive information about the worn surface. X-ray photoelectron spectroscopy (XPS) was operated on a PHI 5000 Versa Probe using Al Ka excitation radiation, which was used to examine the chemical composition on the worn surfaces.
2.6 Antioxidant Performance Analysis
oxidation onset temperature (OOT) and Oxidation induction time (OIT) were measured in the pressure differential scanning calorimetry (PDSC) by the isothermal and programmed temperature modes. Longer OIT and higher OOT indicate better oxidative stability of the oil [30,31].
Isothermal PDSC of 3.0 ± 0.2 mg samples was placed in open aluminum pans (manufactured by NETZSCH 204HP) under 3.5 MPa high purity oxygen. The test sample was heated from the ambient temperature to 80°C or 100°C at a heating speed of 10 °C/min before remaining in the isothermal mode until the oxidative exothermic peak was measured. The OIT is the extrapolated heat peak and the baseline intercept.
3.0 ± 0.2 mg sample was subjected to programmed temperature PDSC at 3.5 MPa of high-purity oxygen. The oil sample is from room temperature to 350°C at a constant heating rate of 10 °C/min. The OOT is calculated by extrapolation from the maximum heat flow to the baseline.
3.1 Characterization of AOLA and EAOLA
The chemical structure of the extreme pressure antioxidant lubricating additive monomer modified by vanillin was confirmed by FTIR and 1H NMR spectroscopy. Fig. 2a shows the FTIR spectra of vanillin, AOLA, and EAOLA. The FTIR spectrum of pure vanillin exhibited significant characteristic peaks at 1294, 1508, and 1585 cm−1 owing to plane aromatic CH deformation and stretching absorption of the benzene ring. These characteristic peaks are present on the profiles of both AOLA and EAOLA. In the FTIR spectra of AOLA and EAOLA, there are characteristic peaks at 3100–3300 cm−1 belonging to N-H and O-H, a characteristic peak at 1280 cm−1 belonging to P=O, and a characteristic peak belonging to P-O-C at 960 cm−1 [32]. The P=O and P-O-C do not appear in the spectrum of vanillin. The significant characteristic peaks at 810 and 1666 cm−1 are attributable to the stretching of C=O of the aldehyde group in the vanillin structure [33]. The characteristic peak of C=O disappears on the spectra of AOLA and EAOLA due to its participation in the reaction. As can be seen from the 1H NMR spectra in Fig. 2b, the chemical shifts and integral areas of all peaks are in good agreement with the protons and carbon in the chemical structures of vanillin, AOLA, and EAOLA. These results indicate that the target compound has been successfully synthesized.
Figure 2: (a) FTIR and (b) 1H-NMR for Vanillin, AOLA, and EAOLA
The tribological properties were performed in a four-ball tester (load of 200 N, speed of 1450 rpm, and time duration of 1800 s). The four-ball tester presented in Fig. 3, AOLA and EAOLA demonstrates the greater effect in decreasing the coefficient of friction between the metal surfaces, compared to pure tung oil.
Figure 3: Antiwear and antifriction of different concentrations of two lubricant additives in tung oil. (a) Friction coefficient (COF), (b) Average friction coefficient (ACOF), (c) Wear scar diameters (WSD), (d) Wear volume (WV)
The result of the friction coefficient varying with the concentration shows that the friction coefficient decreases with the additive concentration increasing from 0wt% to 1.0wt%. The results showed that the 1.0wt% AOLA and EAOLA additives in tung oil were the best concentrations to exhibit the minimum friction coefficient, namely 0.065 and 0.055. It was also observed that the friction coefficient increased at concentrations above the optimal concentration. The obtained results can be explained based on the friction film formation on the steel balls. Upon the addition of 1.0wt% of AOLA and EAOLA, the friction coefficient was significantly reduced compared with the tung oil. This may be due to the formation of a protective friction film on the exposed steel balls. Further increases in the concentration can lead to an increase in friction membrane formation with greater surface coverage. Therefore, the friction coefficient decreases simultaneously with increasing concentration. The friction coefficient is reduced to the limit concentration, where the additive molecules have the maximum adsorption in the friction trajectory. Until 1.0wt%, the friction film formation on the steel surface becomes saturated. That is, the higher concentrations of AOLA and EAOLA lead to the formation of a less stable friction film between the two sliding surfaces during the motion, thus showing a higher coefficient of friction. It is worth noting that the friction coefficient of EAOLA is smaller than AOLA at all concentrations. It may be due to the presence of the anti-wear agent phosphorus that enhances the anti-wear performance of the base oil. The phosphorus content of EAOLA is higher than that of AOLA, which makes the anti-wear performance more excellent. The expected reduction in wear volume was also observed from the wear volume test (Fig. 3d). For the formula containing 0.25~1.0wt% EAOLA, the value is 0.0898~0.0156 × 10−3 mm3, and for the formula containing 0.25~1.0wt% AOLA, the value is slightly higher than that of EAOLA. For pure tung oil, this value is 0.25 × 10−3 mm3, and the 1.0wt% EAOLA wear reduction was greatest by 93.8% compared to pure tung oil. The wear scar diameter changes similarly to the wear volume. These results indicate that the vanillin-based lubricating additives have the potential to prepare high-quality lubricating films.
3.2.2 Extreme Pressure Performance
As an extreme pressure (EP) additive containing phosphorus and nitrogen, it is necessary to have the maximum bite-free load value (PB value) to study the EP characteristics of the additive. As shown in Table 1, compared with the base oil tung oil, the EP performance was improved, and the PB value was increased by 12.07% to 46.87%. The improvement in EP performance can be attributed to its higher rate of reaction with metal surfaces or its higher rate of forming tougher EP films. Moreover, the shorter test time also suggests that the interaction between the two additives may be performed quickly. These pleasant results suggest that the application of AOLA and EAOLA under harsh conditions is favorable, especially for EAOLA. The EAOLA is therefore expected to prevent more catastrophic failure modes under harsh conditions such as high speed, high load, or high temperature. It is worth noting that the extreme pressure performance of EAOLA is better than that of AOLA at each concentration, which also confirms the important role of phosphorus and nitrogen on the extreme pressure performance of additives.
3.3 Effect of Lubricant Additives on Oxidation Stability
The friction test in Section 3.2 has proved that AOLA and EAOLA have the best friction performance when the addition amount is 1.0wt%. Therefore, we choose 1.0wt% as the study of antioxidant properties. The thermal decomposition temperatures of TO, AOLA, and EAOLA were comparatively determined by the TGA instrument. Two additives have a relatively high thermal decomposition temperature (above 300°C) which exhibits good thermal stability allowing AOLA and EAOLA to be used at relatively high temperatures. It can be seen from Fig. 4a that the onset thermal decomposition temperatures of AOLA and EAOLA are both higher than that of TO (310.5°C), and the onset thermal decomposition temperature of EAOLA is higher than that of AOLA, which is 324.6°C and 318.6°C, respectively, it shows that EAOLA is more suitable for high-temperature applications. Oxidative degradation of lubricating oil usually leads to changes in the chemical composition of lubricating oil, which in turn affects the physicochemical properties of lubricating oil [34]. PDSC can be used to indirectly measure the ease of oxidation of lubricating oils. To investigate the antioxidant properties of the selected antioxidants, PDSC tests were performed on different samples in isothermal mode and temperature-programmed mode, respectively. Fig. 4c shows the OIT results obtained by PDSC isothermal experiments for different samples at 80°C and 100°C. Pure tung oil has poor oxidative stability at 80°C and 100°C, with OITs of 39.4 min and 4.7 min, respectively. Adding 1.0wt% of the two antioxidants alone to tung oil can significantly improve the OIT level at 80°C, and only slightly increase the OIT level at 100°C compared to pure tung oil. The results show that both antioxidants have good antioxidant properties at 80°C, but the antioxidant properties decrease at higher temperatures (100°C). It is worth noting that the highest OIT value (80°C, 46.1 min) can be obtained at EAOLA 1.0wt%, which indicates that EAOLA has good antioxidant properties. Fig. 4b shows the OOT results of pure tung oil and tung oil added with 1.0wt% of different antioxidants by PDSC temperature-programmed experiments. By mixing two selected antioxidants (AOLA and EAOLA) into tung oil, respectively, the OOT of tung oil was increased from 121.9°C to 138.5°C and 146.5°C, respectively, indicating that all selected antioxidants oxidants can improve the OOT of tung oil to a certain extent. Among the two antioxidants, the antioxidant EAOLA, with more phenolic hydroxyl groups, has the best antioxidant performance [35], which further proves that EAOLA is the most suitable antioxidant for tung oil.
Figure 4: (a) TGA curves of TO and two antioxidants. (b) The OOT and (c) OIT results of isothermal PDSC for pure TO and with 1.0wt% different antioxidants (AOLA and EAOLA)
3.4.1 Possible Lubrication Mechanisms
SEM is used to observe the wear of the steel ball after the friction test, and the results are shown in Fig. 5. It can be seen from the figure that the steel ball of the lubricant containing only TO is severely worn after the friction test, indicating that there is a strong interaction between the friction pairs of TO. The SEM images of the WSD and wear scars on the steel ball for 1.0wt% AOLA and EAOLA are presented in Fig. 5. Compared with pure tung oil, the WSDs were reduced by ~13.5% (AOLA) and ~27.0% (EAOLA), and the steel ball surface is smoother than that for AOLA because of the presence of long-chain amine molecules. The lubricating additives are prepared with different chain lengths, and the results of the friction coefficient (1.0wt% of the added amount) are presented in Fig. S1. The friction coefficient decreases with the increase in chain length, which may be attributed to the more effective protective film formed by the lubricating additives with longer carbon chains during the lubrication process [36,37].
Figure 5: SEM images of the steel ball after the tribological tests: pure base oil (Tung oil) and additives containing 1.0wt% (AOLA and EAOLA). Up: low-magnification images (for WSD comparison), and Down: high-magnification images (for surface topological analysis)
To further analyze the lubrication mechanism, the friction surface of the steel ball was analyzed by XPS. By measuring XPS, the constituent elements and chemical state of the boundary film on the worn surface can be clearly understood [38]. Figs. 6 and 7 show the XPS spectra of C1s, N1s, P2p, Fe2p, and O1s on the worn surface of steel balls with 1.0wt% AOLA and EAOLA. For AOLA, the Fe2p peaks appear at around 710.8, and 725.5 eV, which can be corresponded to iron oxides (Fe2O3, Fe3O4) and/or iron hydroxides, indicating the lubrication surface is probably slightly oxidized, due to the presence of tung oil [39]. For EAOLA, the peak is a little bit shifting towards the high binding energy direction, which may be due to the formation of FePO4. And for AOLA, the peak is wide and extends towards the low binding energy direction, which can be due to the existence of iron oxides. In the case of N, there is a wide peak at around 399.7 eV for two steel ball surfaces, suggesting that the N element is still in the organic state. It may be the complex compounds of metal surfaces with decomposed additives like organic amine and other N-containing compounds. While for EAOLA, there are wider and larger peak areas, indicating higher relative content of N elements in EAOLA than AOLA. This peak of N1s lubricated by 1.0wt% AOLA is similar to that of 1.0wt% EAOLA. Meanwhile, it is also found the binding energies of C, P, O, N, and Fe lubricated by 1.0wt% AOLA are similar to that of 1.0wt% EAOLA. This reveals they have similar lubrication mechanisms. Moreover, the peak of P2p at 132.8 eV and 133.1eV are possibly ascribed to phosphorus oxide. The peaks quantification obtained from the XPS, the results presented in Table 2, clearly demonstrate that the content of P and N in the friction membrane formed by EAOLA is significantly higher than that of AOLA, P and N are commonly used as a pressure anti-wear additive, which may be why the friction properties of EAOLA are significantly better than AOLA [40]. We will further discuss the antioxidant mechanism in Section 3.4.2.
Figure 6: XPS spectra of worn steel surfaces lubricated with AOLA 1.0wt% (four-ball friction and wear tester)
Figure 7: XPS spectra of worn steel surfaces lubricated with EAOLA 1.0wt% (four-ball friction and wear tester)
From the above results, it can be inferred that 1.0wt% AOLA and 1.0wt% EAOLA can easily form a lubricating film containing various compounds of C, O, Fe, P, and N elements on the surface of the steel ball through adsorption and/or friction reaction, which can significantly improve the tribological properties of tung oil.
3.4.2 Possible Antioxidant Mechanisms
The intramolecular synergy of phenol-amine-type antioxidants can greatly improve antioxidant properties. Both AOLA and EAOLA are phenol-amine-type antioxidants. Similar intramolecular synergistic mechanisms are, therefore, reasonably speculated based on the synergistic mechanism of phenol and amine. For example, in EOLA, during the degradation of tung oil, −NH transfers its protons to both RO• and ROO• to form the −N•-free radicals [29]. The NH may be regenerated either by protons for the −OH of the phenol portion on the vanillin or by protons for the −NH of another part of the EAOLA. With increasing OH number and −NH, the −NH regeneration cycle increases substantially. In contrast to EAOLA, the −NH regeneration of AOLA has only one path, namely only through the −OH on vanilla. Therefore, EAOLA has a better antioxidant performance than AOLA.
The results show that the designed vanillin-based additive added to tung oil has good lubrication and antioxidant properties. Friction and wear properties are sufficient for friction contact. The mechanism of the two additives is similar, but the lubrication properties and antioxidant properties are obviously different. The higher content of the amino group and the phenolic hydroxyl group has a positive effect on the oxidation resistance, oxidative stability, and tribological properties of the lubricating oil. As a base oil, tung oil is a potential renewable raw material directly used for the production of bio-based lubricants and does not compete with food and fuel applications. This result is of great reference significance for reducing the risk of environmental pollution and improving the lubrication and antioxidant performance of vegetable oil in the field of lubricating oil.
Funding Statement: This work was supported by National Natural Science Foundation of China [No. 31901260] and Special Fund of Chinese Central Government for Basic Scientific Research Operations in Commonweal Research Institutes [No. CAFYBB2019SY037].
Conflicts of Interest: The authors declare that they have no conflicts of interest to report regarding the present study.
References
1. Han, Z. B., Wang, Y. S., Qing, X. L. (2017). Characteristics study of in-situ capacitive sensor for monitoring lubrication oil debris. Sensors, 17(12), 2851. https://doi.org/10.3390/s17122851 [Google Scholar] [PubMed] [CrossRef]
2. Xu, A. J., Tian, P. Y., Li, H. J., Wen, S. Z., Tian, Y. (2022). Extreme pressure lubrication between ceramic and bearing steel with liquid metal. Tribology International, 174(96), 107797. https://doi.org/10.1016/j.triboint.2022.107797 [Google Scholar] [CrossRef]
3. Trivedi, K. (2021). Analyzing lubrication properties of magnetic lubricant synthesized in two lubricating oils. Wear, 477, 203861. https://doi.org/10.1016/j.wear.2021.203861 [Google Scholar] [CrossRef]
4. Zhang, Y. X., Cai, T., Shang, W. J., Sun, L. W., Liu, D. et al. (2017). Environmental friendly polyisobutylene-based ionic liquid containing chelated orthoborate as lubricant additive: Synthesis, tribological properties and synergistic interactions with ZDDP in hydrocarbon oils. Tribology International, 115, 297–306. https://doi.org/10.1016/j.triboint.2017.05.038 [Google Scholar] [CrossRef]
5. Trzepiecinski, T. (2020). Tribological performance of environmentally friendly bio-degradable lubricants based on a combination of boric acid and bio-based oils. Materials, 13(17), 3892. https://doi.org/10.3390/ma13173892 [Google Scholar] [PubMed] [CrossRef]
6. Guo, S. M., Li, C. H., Zhang, Y. B., Wang, Y. G., Li, B. K. et al. (2017). Experimental evaluation of the lubrication performance of mixtures of castor oil with other vegetable oils in MQL grinding of nickel-based alloy. Journal of Cleaner Production, 140(12), 1060–1076. https://doi.org/10.1016/j.jclepro.2016.10.073 [Google Scholar] [CrossRef]
7. Keshtiban, P. M., Ghaleh, S. S. G., Alimirzaloo, V. (2019). Performance evaluation of vegetable base oils relative to mineral base oils in the lubrication of cold forming processes of 2024 aluminum alloy. Proceedings of the Institution of Mechanical Engineers Part J–Journal of Engineering Tribology, 233(7), 1068–1073. https://doi.org/10.1177/1350650118813801 [Google Scholar] [CrossRef]
8. Bai, X. F., Zhou, F. M., Li, C. H., Dong, L., Lv, X. J. et al. (2020). Physicochemical properties of degradable vegetable-based oils on minimum quantity lubrication milling. International Journal of Advanced Manufacturing Technology, 106(9), 4143–4155. https://doi.org/10.1007/s00170-019-04695-x [Google Scholar] [CrossRef]
9. Lee, C. T., Lee, M. B., Hamdan, S. H., Chong, W. W. F., Chong, C. T. et al. (2022). Trimethylolpropane trioleate as eco-friendly lubricant additive. Engineering Science and Technology, an International Journal, 35(2), 101068. https://doi.org/10.1016/j.jestch.2021.09.014 [Google Scholar] [CrossRef]
10. Siniawski, M. T., Saniei, N., Stoyanov, P. (2011). Influence of humidity on the tribological performance of unmodified soybean and sunflower oils. Lubrication Science, 23(7), 301–311. https://doi.org/10.1002/ls.157 [Google Scholar] [CrossRef]
11. Mukchortov, I., Zadorozhnaya, E., Kandeva, M., Yakunina, K., Dorokhova, O. (2020). Non-toxic antiwear additive for food and biodegradable lubricants. Journal of Environmental Protection and Ecology, 21(4), 1326–1335. [Google Scholar]
12. Karmakar, G., Ghosh, P., Sharma, B. K. (2017). Chemically modifying vegetable oils to prepare green lubricants. Lubricants, 5(4), 44. https://doi.org/10.3390/lubricants5040044 [Google Scholar] [CrossRef]
13. Zainal, N. A., Zulkifli, N. W. M., Gulzar, M., Masjuki, H. H. (2018). A review on the chemistry, production, and technological potential of bio-based lubricants. Renewable & Sustainable Energy Reviews, 82, 80–102. https://doi.org/10.1016/j.rser.2017.09.004 [Google Scholar] [CrossRef]
14. Bongfa, B., Syahrullail, S., Hamid, M. K. A., Samin, P. M. (2016). Suitable additives for vegetable oil-based automotive shock absorber fluids: An overview. Lubrication Science, 28(6), 381–404. https://doi.org/10.1002/ls.1337 [Google Scholar] [CrossRef]
15. Fang, S. Q., Zhang, H., Zhang, B. J., Li, G. Q. (2014). A study of tung-oil-lime putty—A traditional lime based mortar. International Journal of Adhesion and Adhesives, 48, 224–230. https://doi.org/10.1016/j.ijadhadh.2013.09.034 [Google Scholar] [CrossRef]
16. Yan, K. Z., Peng, Y., You, L. Y. (2020). Use of tung oil as a rejuvenating agent in aged asphalt: Laboratory evaluations. Construction and Building Material, 239(6), 117783. https://doi.org/10.1016/j.conbuildmat.2019.117783 [Google Scholar] [CrossRef]
17. Huang, J. J., Yuan, T., Ye, X. Y., Man, L. M., Zhou, C. et al. (2018). Study on the UV curing behavior of tung oil: Mechanism, curing activity and film-forming property. Industrial Crops and Products, 112, 61–69. https://doi.org/10.1016/j.indcrop.2017.10.061 [Google Scholar] [CrossRef]
18. Lin, H., Liu, F. Y., Lourenco, S. D. N., Schwantes, G., Trumpf, S. et al. (2021). Stabilization of an earthen material with Tung oil: Compaction, strength and hydrophobic enhancement. Construction and Building Material, 290, 123213. https://doi.org/10.1016/j.conbuildmat.2021.123213 [Google Scholar] [CrossRef]
19. Ju, Y. H., Sari, N. N. F., Go, A. W., Wang, M. J., Agapay, R. C. et al. (2020). Preparation of epoxidized fatty acid ethyl ester from Tung oil as a bio-lubricant base-stock. Waste and Biomass Valorization, 11(8), 4145–4155. https://doi.org/10.1007/s12649-019-00749-z [Google Scholar] [CrossRef]
20. de Souza, M. C., Goncalves, J. F. D., Lutif, S. Y. S., Gomes, J. D. (2019). Tribological evaluation of the Jatropha and Tung-based oils as bio-lubricants on Al-7050-T7451 alloy. Journal of the Brazilian Society of Mechanical Sciences and Engineering, 41(6), 243. https://doi.org/10.1007/s40430-019-1746-3 [Google Scholar] [CrossRef]
21. Drabik, J., Trzos, M. (2013). Improvement of the resistance to oxidation of the ecological greases by the additives. Journal of Thermal Analysis and Calorimetry, 113(1), 357–363. https://doi.org/10.1007/s10973-013-3090-7 [Google Scholar] [CrossRef]
22. He, Z. Y., Xiong, L. P., Xie, F., Shen, M. X., Han, S. et al. (2018). Tribological and antioxidation properties study of two N-containing borate ester derivatives as additive in rapeseed oil. PLoS One, 13(12), 0207267. https://doi.org/10.1371/journal.pone.0207267 [Google Scholar] [PubMed] [CrossRef]
23. Ohkatsu, Y., Matsuura, T., Yamato, M. (2003). A phenolic antioxidant trapping both alkyl and peroxy radicals. Polymer Degradation and Stability, 81(1), 151–156. https://doi.org/10.1016/S0141-3910(03)00084-3 [Google Scholar] [CrossRef]
24. Kim, T. H., Song, Y. R., Kim, J. N. (2003). Synthesis and properties of new polymer having hindered phenol antioxidants. Bulletin of the Korean Chemical Society, 12(24), 1853–1855. [Google Scholar]
25. Wang, S., Ma, S. Q., Xu, C. X., Liu, Y., Dai, J. Y. et al. (2017). Vanillin-derived high-performance flame retardant epoxy resins: Facile synthesis and properties. Macromolecules, 50(5), 1892–1901. https://doi.org/10.1021/acs.macromol.7b00097 [Google Scholar] [CrossRef]
26. Ding, H. Y., Wang, M., Li, M., Huang, K., Li, S. H. (2018). Synthesis of a water-soluble, rubber seed oil-based sulfonate and its tribological properties as a water-based lubricant additive. Journal of Applied Polymer Science, 135(15), 1–7. https://doi.org/10.1002/app.46119 [Google Scholar] [CrossRef]
27. Cai, M. R., Zhao, Z., Liang, Y. M., Zhou, F., Liu, W. M. (2010). Alkyl imidazolium ionic liquids as friction reduction and anti-wear additive in polyurea grease for steel/steel contacts. Tribology Letters, 22(40), 215–224. https://doi.org/10.1007/s11249-010-9624-2 [Google Scholar] [CrossRef]
28. Sabarinath, S. N., Nair, K. P., Rajendrakumar, P. K. (2019). Experimental and quantum chemical investigations on the oxidative stability of sesame oil base stock with synthetic antioxidant additives. Lubrication Science, 5(31), 179–193. https://doi.org/10.1002/ls.1441 [Google Scholar] [CrossRef]
29. Zhao, H. R., Feng, J. X., Zhu, J., Yu, H. B., Liu, Y. J. et al. (2020). Synthesis and application of highly efficient multifunctional vegetable oil additives derived from biophenols. Journal of Cleaner Production, 242, 118274. https://doi.org/10.1016/j.jclepro.2019.118274 [Google Scholar] [CrossRef]
30. Wu, Y. X., Li, W. M., Zhang, M., Wang, X. B. (2013). Improvement of oxidative stability of trimethylolpropane trioleate lubricant. Thermochimica Acta, 569, 112–118. https://doi.org/10.1016/j.tca.2013.05.033 [Google Scholar] [CrossRef]
31. Wu, W., Liu, J. X., Li, Z. H., Zhao, X. Y., Liu, G. Q. et al. (2021). Surface-functionalized nano MOFs in oil for friction and wear reduction and antioxidation. Chemical Engineering Journal, 410, 128306. [Google Scholar]
32. Feng, Q., Deng, F. K., Li, K. C., Dou, M. Y., Zou, S. et al. (2021). Enhancing the tribological performance of Ti3C2 MXene modified with tetradecylphosphonic acid. Colloids and Surfaces A: Physicochemical and Engineering Aspects, 625, 126903. [Google Scholar]
33. Celebioglu, A., Kayaci-Senirmak, F., Ipek, S., Durgun, E., Uyar, T. (2016). Polymer-free nanofibers from vanillin/cyclodextrin inclusion complexes: High thermal stability, enhanced solubility and antioxidant property. Food Function, 7(7), 3141–3153. [Google Scholar] [PubMed]
34. Chao, M. R., Li, W. M., Chen, L. F., Wang, X. B. (2015). Hindered phenol derivative as a multifunctional additive in lithium complex grease. Industrial Engineering Chemistry Research, 26(54), 6605–6610. [Google Scholar]
35. Wang, S. P., Yu, S. S., Feng, J. X., Liu, S. G. (2019). Multifunctional lubricant additive based on difluoroboron derivatives of a diphenylamine antioxidant. RSC Advances, 60(9), 35059–35067. [Google Scholar]
36. Jumat, S., Nadia, S., Emad, Y. (2012). Triester derivatives of oleic acid: The effect of chemical structure on low temperature, thermo-oxidation and tribological properties. Industrial Crops and Products, 38(5), 107–114. https://doi.org/10.1016/j.indcrop.2012.01.019 [Google Scholar] [CrossRef]
37. Hu, C. H., Ai, J., Ma, L., Wen, P., Fan, M. J. et al. (2021). Ester oils are prepared from fully renewable resources and their lubricant base oil properties. ACS Omega, 6(25), 16343–16355. https://doi.org/10.1021/acsomega.1c00808 [Google Scholar] [PubMed] [CrossRef]
38. Yang, G. B., Zhao, J. H., Cui, L., Song, S. Y., Zhang, S. M. et al. (2017). Tribological characteristic and mechanism analysis of borate ester as a lubricant additive in different base oils. RSC Advances, 7(13), 7944–7953. https://doi.org/10.1039/C6RA26896J [Google Scholar] [CrossRef]
39. Yan, J. C., Zeng, X. Q., Ren, T. H., van der Heide, E., (2014). Boundary lubrication of stainless steel and CoCrMo alloy materials based on three ester-based additives. Tribology International, 73(27), 88–94. https://doi.org/10.1016/j.triboint.2014.01.010 [Google Scholar] [CrossRef]
40. Hamtnami, M., Rodrigues, N., Fernandes, C., Martins, R., Seabra, J. et al. (2017). Axle gear oils: Friction, wear and tribofilm generation under boundary lubrication regime. Tribology International, 114(10), 88–108. https://doi.org/10.1016/j.triboint.2017.04.018 [Google Scholar] [CrossRef]
Appendix
Figure S1: Comparison of friction properties of synthetic lubricant additives from different raw materials (add 1.0wt% in tung oil)
Cite This Article
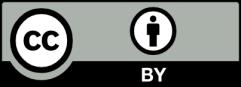