Open Access
ARTICLE
Comparative Analysis of Reaction to Fire and Flammability of Hemp Shives Insulation Boards with Incorporated Microencapsulated Phase Change Materials
1 Institute of Architecture and Design, Riga Technical University, Riga, LV-1048, Latvia
2 Forest and Wood Products Research and Development Institute, Jelgava, LV-3001, Latvia
* Corresponding Author: Inga Zotova. Email:
(This article belongs to the Special Issue: Renewable Materials and Advanced Technologies for Sustainability)
Journal of Renewable Materials 2024, 12(3), 603-613. https://doi.org/10.32604/jrm.2024.047607
Received 10 November 2023; Accepted 29 December 2023; Issue published 11 April 2024
Abstract
Nowadays buildings contain innovative materials, materials from local resources, production surpluses and rapidly renewable natural resources. Phase Change Materials (PCM) are one such group of novel materials which reduce building energy consumption. With the wider availability of microencapsulated PCM, there is an opportunity to develop a new type of insulating materials, combinate PCM with traditional insulation materials for latent heat energy storage. These materials are typically flammable and are located on the interior wall finishing yet there has been no detailed assessment of their fire performance. In this research work prototypes of low-density insulating boards for indoor spaces from hemp shives using carbamide resin binder and cold pressing were studied. Bench-scale cone calorimeter tests were conducted to evaluate fire risk, with a focus on assessing material flammability properties and the influence of PCM on the results. In this research, the amount of smoke, heat release rate, effective heat of combustion, specific extinction coefficient, mass loss, carbon dioxide yield, specific loss factor, ignition time of hemp straws samples and samples of hemp straws with 10% and without PCM admixture were compared. There is a risk of flammability for PCM and their fire reaction has not been evaluated when incorporating PCM into interior wall finishing boards. The obtained results can be used by designers to balance the potential energy savings of using PCM with a more complete understanding and predictability of the associated fire risk when using the proposed boards. It also allows for appropriate risk mitigation strategies.Graphical Abstract
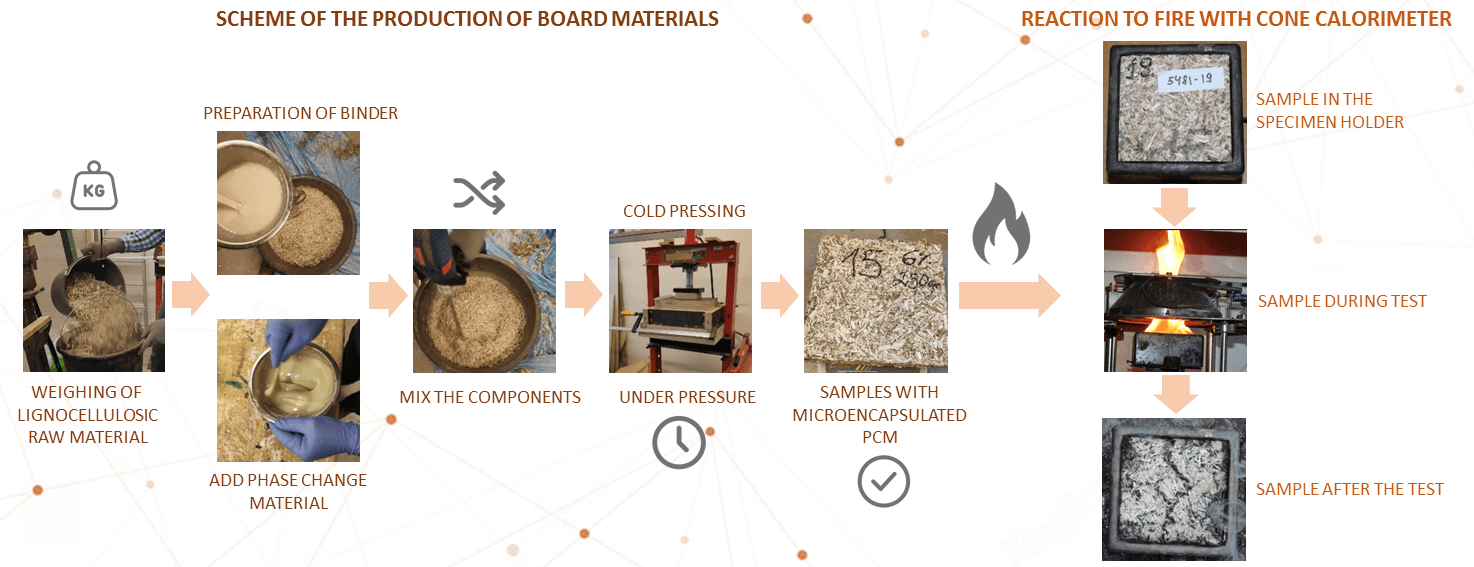
Keywords
Nowadays, the rising energy needs of buildings and the severity of global warming are significant problems. To address these issues, thermal energy storage (TES) building materials are being prepared by incorporating phase change materials (PCM) into construction materials [1–4]. PCM are a group of smart materials, which are becoming increasingly popular because of their potential for reducing building energy consumption [5]. The ability of PCM to absorb and release thermal energy suggests that they might be used to mitigate the effects of temperature fluctuations on building performance as passive thermal control [6–10]. Thus, PCM will serve to simultaneously provide thermal comfort and reduce energy consumption in buildings [11–15].
Over the last decade, there has been a significant surge in academic interest in PCM as a result which are used to stabilize indoor temperatures of the widespread availability of products at affordable prices and potential areas of utilization in building applications [16]. Walls, ceilings, and roofs are all examples of building components or structural members that can integrate PCM [17–19]. To develop lighter material structures, PCM integration often reduces the mass density of the final product. The usage of latent heat storage materials like PCM was extensively researched by the technical community due to their significant perspective in relation to the enhanced heat of melting [20–24].
The standard guidelines on the selection process of an adequate PCM for each application depend on two classes of criteria [25–27], as follows:
I Main class criteria: a. The temperature range over which the phase transition process occurs; b. Enthalpy variation during phase transition.
II Secondary class criteria: a. Chemical compatibility with the rest of the system components; b. Constraints related to mass/volume or storage density; c. Supercooling; d. Thermo-physical properties stability; e. Flammability; f. Cost; g. Lifecycle considerations and environmental impact.
While the discussion on PCM from biobased raw materials is relatively new, there are other sectors like the one of plastic production, where biobased materials are being developed and have been discussed for decades. Biobased plastics are typically compared to their fossil-based counterparts in terms of production and end-life sustainability, and it is clear that biobased plastics are not necessarily biodegradable or compostable. Biobased PCM are made of organic components that can be partially or fully obtained from biomass, vegetable and tropical oils or animal/fish fats. Even though it is often assumed that they are biodegradable, this is a point that needs to be carefully studied for the different types of biobased PCM. Biobased PCM are generally nontoxic and can be used in relatively wide temperature ranges for low to high temperature applications (−80 to 275°C). However, one of the major drawbacks of organic PCM implementation is flammability [28]. Plant-based organic PCM, used as a renewable and environmentally friendly, better fire resistance, alternative to paraffin PCM in this study, offers advantages such as non-toxicity and recyclability for thousands of cycles without material degradation. These hydrogenated hydrocarbons possess a saturated electronic configuration, ensuring chemical stability, non-corrosiveness, and potential for long-term use. Nonetheless, bio-based PCM may present some limitations, including a restricted temperature range, limitations in energy storage due to low thermal conductivity, limited commercial availability, and lower thermal conductivity [29–32]. To be protected from the environment, PCMs need to be encapsulated. This also prevents any leakage when the PCM is in the liquid state. Microencapsulation has become a common method to protect the PCMs and thus incorporate it in various components [33].
When using new materials in construction, research and tests must be carried out. An important aspect is the determination of the flammability properties of the boards and the effect of PCM on the overall results [34–38]. There is a risk of flammability for PCM and their fire reaction has not been evaluated when incorporating PCM into hemp shive wall finishing boards. The fundamental thermal decomposition behaviour is first obtained on a micro-scale under highly controlled conditions in the bench-scale cone calorimeter to evaluate the associated fire risk. This quantifies how the material behaves in a variety of conditions, evaluating its burning rate, rate of heat release, time to ignition, minimum energy for ignition, thermal evolution, and gas emissions. This is finally then validated in the intermediate scale to both understand the behaviour of these materials in the standard test method, as well as ensure that the study is scalable. Results can be used by designers to balance the potential energy savings from using PCM with a complete understanding of the associated fire risks. This also allows them to employ any risk mitigation strategies that they desire [39–41]. Researchers continue to work to improve the flame retardant performance of PCM [42].
The novelty of this research is in the determination of the flammability properties of the boards and the influence of PCM on the overall results. The risk of ignition for phase change materials has not been evaluated, particularly when incorporating PCM into interior wall finishing boards. The obtained results can assist designers in balancing the potential energy savings of using PCM with a comprehensive understanding and predictability of the associated fire risk when employing the proposed boards.
Hemp shives–a by-product of the hemp fiber variety “Bialobrzeskie” grown in Latvia. The average moisture content of hemp shives is 7.9%. Granulometric analysis of the raw materials-the average results of sieving of raw material particle samples are summarized (see Fig. 1). The amount of fractions in the range from 2000 to 5600 μm in the raw material is 48.46%. For hemp shives 29.56% of the fraction is in the size range of 500–2000 μm. Less than 20% of the material has fractions with a size greater than 5600 μm. The granulometric analysis revealed that the fractions which are less than 500 μm in hemp shives contain 3.74% and they are separated before the production of board as in the production of boards fractions larger than 500 μm are used.
Figure 1: Results of granulometric analysis of hemp shives
Urea-formaldehyde resin adhesive Kleiberit 862.0 (UF) with hardener for cold pressing. The choice of a water-soluble binder was important because the PCM material was in the water emulsion slurry. And as well adhesive is selected based on its physical and chemical properties. The binder is supplied in the form of a white powder and is mixed with water at 18°C–20°C.
The encapsulated PCM microcapsule MikroCaps, Ltd. (Ljubljana, Slovenia) product–PCM S50. The appearance of a white aqueous dispersion of formaldehyde-free slurry, average microcapsules particles size 1–15 μm, polyurethane (formaldehyde-free) as a type of membrane, and a Biobased type of PCM with a melting temperature of 23°C–28°C, density 900–970 g/L. Bio-based PCM is a renewable and green alternative in comparison with paraffin PCM. They are non-toxic and can be recycled without material degradation. With PCM, it is possible to innovate traditional insulation materials-to store and release latent heat energy, using a PCM supplemented with microcapsules and incorporating it into heat and sound insulation materials of various structures.
Two groups of samples were prepared for testing varying with the type of raw material and the percentage of microencapsulated PCM with 10% maintaining the specified limits of the target density. The first group of boards is produced without PCM to get Hemp shives (H) basic data, but the second group-hemp shives with 10% PCM (H_10%PCM) to allow comparison of the data.
The publication is based on results obtained during the writing process of the doctoral thesis from Riga Technical University authored by Inga Zotova [43].
3.1 Production of Board Materials
Cold pressing is used to produce board samples (Fig. 2).
Figure 2: Scheme of the production of board materials
First group samples: Weighing of lignocellulosic raw material; Preparation of binder; Being evenly leveled the mixed mass is formed into a matrix; Samples must be kept under pressure in the matrix for a minimum of 12 h.
Second group samples: Weighing of lignocellulosic raw material; Preparation of binder; After mixing PCM is added in the amount of 10% of the mass of the raw material; Mix the components to obtain a homogeneous consistency; Being evenly leveled the mixed mass is formed into a matrix; Samples must be kept under pressure in the matrix for a minimum of 12 h.
Tests are performed using a cone calorimeter GD-ISO5660. The device consists of a sample placement and weighing stand, a conical heating element with a spark ignition device, a combustion gas removal system and measuring instruments.
A cone calorimeter is a device used to investigate the resistance to ignition and reaction to fire of small samples of various materials. This device allows the surface of the sample to be exposed to heat radiation at various heat capacities. Table 1 shows samples data from the device before testing.
Combustion is a complex chemical oxidation process that is difficult to predict under actual fire conditions [44]. The standard LVS ISO 5660-1:2015/A1:2021 [45] defines a method for assessing the rate of heat release and dynamic smoke generation rate of samples exposed to a controlled level of heat radiation with external ignition. The rate and amount of heat release are assessed by measuring the oxygen consumption obtained by determining the oxygen concentration in the combustion gases and their flow rate. In this test the time until the sample ignites is determined as well.
The dynamic smoke generation rate is calculated by measuring the weakening of the laser light beam in the combustion gas flow. Smoke generation is registered throughout the test, regardless of whether the sample ignites or not. In addition, the mass loss of the samples is measured throughout the test.
In the cone calorimeter fire reaction tests can be performed within the limits of 25–75 kW/m2 heat radiation, according to the standard LVS ISO 5660-1 methodology. A heat power of 50 kW/m2 and prepared samples of 100 mm ×100 mm were used in the research (see Fig. 3).
Figure 3: a–sample in the specimen holder, b–sample during test, c–sample after the test
At the beginning of the test, the holder with the sample is placed on the testing base, which provides continuous fixing of the sample’s mass during the test. An ignition device is placed above the surface of the sample, which ignites the surface of the heated sample by an electric spark. The necessary heat radiation is conducted to the surface of the sample. The spark is removed after the sample is ignited, and if the sample goes out, the sample’s extinction is recorded, but the spark is not re-applied until the end of the test. If the sample re-ignites due to heat radiation, the second, third, etc. ignition of the sample is recorded. The ignition time of the sample is recorded.
During the test the amount of oxygen in the combustion gases is measured, and the mass of the sample at 5 s intervals. The device has a fixed gas extraction rate (0.024 ± 0.002) m3/s. The amount of smoke produced is also measured by measuring the attenuation of the laser beam as it passes through the combustion gases.
In the research, the changes of the samples are analysed for 10 min of test time, and basic data are collected for 1 min before the beginning of the test.
When calculating the amount of generated heat during the combustion process, it is assumed that 13.1 ×103 kJ of energy is released when 1 kg of oxygen is burned. The test results are applicable only to the behaviour of the samples under specific test conditions. They cannot be used as the only criterion to assess the potential fire hazard of the product in use.
Statistical processing methods are used for data processing: descriptive statistics and mutual comparison of data; correlation and regression analysis.
Since the sample groups of fire reaction research are small, the assessment of the influence of factors’ significance is implemented with standardized methods of statistical data processing. It determines the use of an approximate method of assessment of the significance of factors. The factor affecting the fire response is considered significant if the average value of the factor exceeds the limit of one standard deviation for the parameter being compared.
4 Results of Physicochemical Properties
The fire reaction characteristics of the materials were determined for the H and H_10%PCM sample groups. The heat release of both sample groups is similar, but the H_10%PCM group has 6 MJ/m² or 15% higher heat output than the H group. For both sample groups the total amount of released heat is in the range of 45 to 51 MJ/m², but the consumed oxygen is in the range of 28 to 32 g, where the H_10%PCM group has consumed 14 % or 4.5 g more oxygen in comparison with H group samples. This could be explained by the addition of raw material, which also requires more oxygen for combustion. The difference in mass loss for both groups of samples is within 1 %. The specific loss factor differs by 0.3% between the sample groups, where the H group has a loss of 6.89 g/(cm2) and the H_10%PCM group has a loss of 6.97 g/(cm2). Samples with PCM in the composition ignited 1.49 times faster than samples without PCM, which means that the capsules contribute to the combustion of the samples and additional protection against ignition should be considered. The H group samples ignited in 9.67 s and the H_10%PCM group in 6.5 s.
As a result of the smoke release the total amount of smoke in the time period from 0–605 s is 33.70 m²/m² for the H group and 43.95 m²/m² for the H_10%PCM group, as a result, H_10%PCM emitted 30 % more than the H group during the entire test. The H sample group released 3.6 times more smoke than the H_10%PCM sample group in the first 10 s, which is the non-flaming phase. But in the period from 10 to 605 s, in the flaming phase, 1.4 times more smoke was released by samples with PCM composition, respectively H released 31.67, and H_10%PCM 43.4 m²/m². The obtained results lead to the conclusion that the amount of smoke is affected by the PCM composition in the samples (see Fig. 4).
Figure 4: The amount of smoke of the samples
Analyzing the heat release data the conclusion can be made that the sample group with PCM at 60 s has a higher result of 136.92 kW/m2, and for the H group 120.7 kW/m2, which also decreased with a similar difference in results, obtaining that 605 s still has a higher heat release speed 87.11 against 75.82 for H group (see Fig. 5).
Figure 5: Heat release rate
4.4 The Effective Heat of Combustion
Fig. 6 shows the results of the effective heat of combustion, where in the first 60 s the heat of combustion is released rapidly, after 10 s, when the flaming phase begins, the heat of combustion increases rapidly up to 60 s. In the period of time from 60 to 605 s changes occur, stabilizing the result, reaching 12 MJ/kg for the H_10%PCM group and 10.41 MJ/kg for the H group.
Figure 6: Effective heat of combustion
4.5 The Coefficient of Specific Extinction
The coefficient of specific extinction is drastically different for both groups. As can be seen for the group with PCM it happens more slowly and evenly in the first 60 s, reaching a maximum value of 41.78 m²/kg and then this value decreases steadily, while for the samples of the H group, the maximum value is already reached in the first 11 s, reaching 65.3 m²/kg and by 60 s, it is already rapidly falling and then steadily decreased. The value of group H reaches four times higher specific extinction coefficient in the first 11 s (see Fig. 7).
Figure 7: Specific extinction coefficient
Mass loss measurements are used to analyse the development of smouldering in hemp shives insulation boards. The mass loss rate rapidly peaks at 12.1 g/(s·m²) for the H group and 12.64 g/(s·m²) for the H_10% PCM group. The mass loss for both groups of samples starts to decrease from 60 s and it continues to decrease equally for the rest of the test time. Most of the total mass loss is during the downward smouldering regime, despite the low release of recorded temperatures. The reason for that is that the initial combustion involves the pyrolysis process, during which most of the mass is lost, the further process involves reactions of charring oxidation and thus the mass loss is less. Materials containing PCM experience a higher rate of mass loss compared to PCM-free materials due to factors such as the presence of volatile PCM components and PCM decomposition. Interactions with other components and changes in combustion characteristics also play a role in influencing different rates of mass loss. Additionally, the chosen PCM S50 encapsulated PCM membrane is made from polyurethane (formaldehyde-free), which affect or increase flammability.
The first 60 s is the fastest burning process during which carbon dioxide (CO2) is released. It can be seen that the amount of emitted CO2 during the subsequent combustion process decreases. The results of the H_10%PCM group are slightly higher, which could be influenced by the added microencapsulated PCM dispersion (see Fig. 8).
Figure 8: Carbon dioxide yield
• The technology developed to produce insulation boards with integrated PCM dispersion, made from hemp shives in the cold pressing process using urea-formaldehyde resin glue, allows for the creation of low-density boards.
• According to the published studies, the bio-based phase change material has lower flammability and reaction to fire, however, in the conducted study the results are influenced by the encapsulated PCM composition and its interaction with other board materials. In the conducted tests, it was determined that the inclusion of PCM resulted in faster ignition time, increased smoke output throughout the test, higher oxygen consumption, and a higher heat release rate.
• PCM itself may possess specific flammability characteristics, and integrating it into board materials could impact the overall flammability of the composite material. In this study, while samples with PCM exhibited slower ignition, the group with PCM emitted 30% more smoke than the group without PCM throughout the entire test.
• Lignocellulosic board materials pose a high risk of ignition. To reduce flammability in the process of making the material the addition of microcapsules with flame retardant filling or treat hemp shives pre-treatment with a flame retardant recommended.
Acknowledgement: Thanks to the help provided by the Institute of Design Technologies Riga Technical University for the material and technical support for the successful implementation of the PhD.
Funding Statement: This work was supported by the European Regional Development Fund Postdoctoral Research Support “Structures and Technology Development of Smart Insulation Materials for Indoor Microclimate Regulation” 1.1.1.2/VIAA/1/16/152 and the European Social Fund within the Project “Development of the Academic Personnel of Riga Technical University in the Strategic Fields of Specialization” Nr. 8.2.2.0/18/A/017.
Author Contributions: The authors confirm contribution to the paper as follows: study conception and design: I.Z. and E.K.; data collection: I.Z.; analysis and interpretation of results: I.Z., E.K., and L.Z.; draft manuscript preparation: I.Z., E.K., and L.Z.; All authors reviewed the results and approved the final version of the manuscript.
Availability of Data and Materials: Data available on request from the authors.
Conflicts of Interest: The authors declare that they have no conflicts of interest to report regarding the present study.
References
1. Joulin, A., Zalewski, L., Lassue, S., Naji, H. (2014). Experimental investigation of thermal characteristics of a mortar with or without a micro-encapsulated phase change material. Applied Thermal Engineering, 66, 171–180. [Google Scholar]
2. Karaipekli, A., Sarı, A., Biçer, A. (2016). Thermal regulating performance of gypsum/(C18-C24) composite phase change material (CPCM) for building energy storage applications. Applied Thermal Engineering, 107, 55–62. [Google Scholar]
3. Zhang, Y., Ding, J., Wang, X., Yang, R., Lin, K. (2006). Influence of additives on thermal conductivity of shape-stabilized phase change material. Solar Energy Materials and Solar Cells, 90, 1692–1702. [Google Scholar]
4. Cabeza, L. F., Castell, A., Barreneche, C., de Gracia, A., Fernández, A. I. (2011). Materials used as PCM in thermal energy storage in buildings: A review. Renewable and Sustainable Energy Reviews, 15, 1675–1695. [Google Scholar]
5. Kuznik, F., David, D., Johannes, K., Roux, J. J. (2011). A review on phase change materials integrated in building walls. Renewable and Sustainable Energy Reviews, 15, 379–391. [Google Scholar]
6. Dhaidan, N. S., Kokz, S. A., Rashid, F. L., Hussein, A. K., Younis, O. et al. (2022). Review of solidification of phase change materials dispersed with nanoparticles in different containers. Journal of Energy Storage, 51, 1–29. [Google Scholar]
7. Rashid, F. L., Hussein, A. K., Malekshah, E. H., Abderrahmane, A., Guedri, K. et al. (2022). Review of heat transfer analysis in different cavity geometries with and without nanofluids. Nanomaterials, 12, 1–30. [Google Scholar]
8. Tiji, M. E., Al-Azzawi, W. K., Mohammed, H. I., Dulaimi, A., Rashid, F. L. et al. (2022). Thermal management of the melting process in a latent heat triplex tube storage system using different configurations of frustum tubes. Journal of Nanomaterials, 2022, 7398110. [Google Scholar]
9. Rashid, F. L., Basem, A., Khalaf, F. A. A., Abbas, M. H., Hashim, A. (2022). Recent breakthroughs and improvements in phase change material melting in a triple-tube thermal storage unit. Revue des Composites et des Matériaux Avancés, 32, 295–304. [Google Scholar]
10. Hashim, A., Braihi, A. J., Rashid, F. L., Hashim, M. S. (2019). Synthesis and characterization of novel cement/polyvinyl pyrrolidone-carboxymethyl cellulose-Y2O3 nanocomposites for piezoelectric application. Advanced Science Engineering and Medicine, 11, 419–422. [Google Scholar]
11. Rashid, F. L., Al-Obaidi, M. A., Dulaimi, A., Bahlol, H. Y., Hasan, A. (2023). Recent advances, development, and impact of using phase change materials as thermal energy storage in different solar energy systems: A review. Designs, 7(3), 66. [Google Scholar]
12. Mehrizi, A. A., Karimi-Maleh, H., Naddafi, M., Karimi, F. (2023). Application of bio-based phase change materials for effective heat management. Journal of Energy Storage, 61, 106859. [Google Scholar]
13. Meng, B., Zhang, X., Hua, W., Liu, L., Ma, K. (2022). Development and application of phase change material in fresh e-commerce cold chain logistics: A review. Journal of Energy Storage, 55, 87–93. [Google Scholar]
14. Sharshir, S. W., Joseph, A., Elsharkawy, M., Hamada, M. A., Kandeal, A. et al. (2023). Thermal energy storage using phase change materials in building applications: A review of the recent development. Energy and Buildings, 285, 112908. [Google Scholar]
15. Ong, P. J., Lum, Y. Y., Soo, X. Y. D., Wang, S., Wang, P. et al. (2023). Integration of phase change material and thermal insulation material as a passive strategy for building cooling in the tropics. Construction and Building Materials, 386, 131583. [Google Scholar]
16. Kalnæs, S. E., Jelle, P. B. (2015). Review. Phase change materials and products for building applications: A state-of-the-art review and future research opportunities. Energy and Buildings, 94, 150–176. [Google Scholar]
17. Alqallaf, H. J., Alawadhi, E. M. (2013). Concrete roof with cylindrical holes containing PCM to reduce the heat gain. Energy and Buildings, 61, 73–80. [Google Scholar]
18. Royon, L., Karim, L., Bontemps, A. (2013). Thermal energy storage and release of a new component with PCM for integration in floors for thermal management of buildings. Energy and Buildings, 63, 29–35. [Google Scholar]
19. Navarro, L., de Gracia, A., Castell, A., Álvarez, S., Cabeza, L. F. (2015). PCM incorporation in a concrete core slab as a thermal storage and supply system: Proof of concept. Energy and Buildings, 103, 70–82. [Google Scholar]
20. Giro-Paloma, J., Al-Shannaq, R., Fernández, A. I., Farid, M. M. (2016). Preparation and characterization of microencapsulated phase change materials for use in building applications. Materials, 9, 11. [Google Scholar]
21. Zhou, D., Zhao, C. Y., Tian, Y. (2012). Review on thermal energy storage with phase change materials (PCMs) in building applications. Applied Energy, 92, 593–605. [Google Scholar]
22. Baetens, R., Jelle, B. P., Gustavsen, A. (2010). Phase change materials for building applications: A state-of-the-art review. Energy and Buildings, 42, 1361–1368. [Google Scholar]
23. Sukontasukkul, P., Nontiyutsirikul, N., Songpiriyakij, S., Sakai, K., Chindaprasirt, P. (2016). Use of phase change material to improve thermal properties of lightweight geopolymer panel. Materials and Structures, 49, 4637–4645. [Google Scholar]
24. Bentz, D. P., Turpin, R. (2007). Potential applications of phase change materials in concrete technology. Cement and Concrete Composites, 29(7), 527–532. [Google Scholar]
25. Diaconu, B., Cruceru, M., Anghelescu, L. (2023). Fire retardance methods and materials for phase change materials: Performance, integration methods, and applications—A literature review. Fire, 6(175), 1–56. [Google Scholar]
26. Lane, G. A. (1983). Solar heat storage: Latent heat material. Florida: CRC Press. [Google Scholar]
27. Abhat, A. (1983). Low temperature latent heat thermal energy storage: Heat storage materials. Solar Energy, 30, 313–332. [Google Scholar]
28. Simonsen, G., Ravotti, R., O’Neill, P., Stamatiou, A. (2023). Biobased phase change materials in energy storage and thermal management technologies. Renewable and Sustainable Energy Reviews, 184, 113546. [Google Scholar]
29. Hassan, A., Shakeel Laghari, M., Rashid, Y. (2016). Micro-encapsulated phase change materials: A review of encapsulation, safety and thermal characteristics. Sustainability, 8, 1046. [Google Scholar]
30. Okogeri, O., Vassilis, N., Stathopoulos, V. N. (2021). What about greener phase change materials? A review on biobased phase change materials for thermal energy storage applications. International Journal of Thermofluids, 10, 1–12. [Google Scholar]
31. Chalkia, V., Tachos, N., Pandis, P. K., Giannakas, A., Koukou, M. K. et al. (2018). Influence of organic phase change materials on the physical and mechanical properties of HDPE and PP polymers. RSC Advances, 48, 1–10. [Google Scholar]
32. Socaciu, L., Plesa, A., Unguresan, P., Giurgiu, O. (2014). Review on phase change materials for building applications. Leonardo Electronic Journal of Practices and Technologies, 25, 179–194. [Google Scholar]
33. Pignata, A., Demetrio Minuto, F., Lanzini, A., Papurello, D. (2023). A feasibility study of a tube bundle exchanger with phase change materials: A case study. Journal of Building Engineering, 78, 107622. [Google Scholar]
34. Sharma, A., Tyagi, V. V., Chen, C. R., Buddhi, D. (2009). Review on thermal energy storage with phase change materials and applications. Renewable and Sustainable Energy Reviews, 13, 318–345. [Google Scholar]
35. Ismail, A., Wang, J., Salami, B. A., Oyedele, L. O., Otukogbe, G. K. (2023). Microencapsulated phase change materials for enhanced thermal energy storage performance in construction materials: A critical review. Construction and Building Materials, 401, 132877. [Google Scholar]
36. Ismail, A., Zhou, J., Aday, A., Davidoff, I., Odukomaiya, A. et al. (2023). Microencapsulation of bio-based phase change materials with silica coated inorganic shell for thermal energy storage. Journal of Building Engineering, 67, 105981. [Google Scholar]
37. Diaconu, B. M., Cruceru, M., Anghelescu, L. (2022). Phase change materials—Applications and systems designs: A literature review. Designs, 6, 117. [Google Scholar]
38. Radouane, N. (2022). A comprehensive review of composite phase change materials (cPCMs) for thermal management applications, including manufacturing processes, performance, and applications. Energies, 15, 8271. [Google Scholar]
39. Law, M. (1986). Translation of research into practice: Building design. Fire Safety Science, 1, 603–609. [Google Scholar]
40. Png, Z. M., Soo, X. Y. D., Chua, M. H., Ong, P. J., Xu, J. et al. (2022). Triazine derivatives as organic phase change materials with inherently low flammability. Journal of Materials Chemistry A, 10, 3633–3641. [Google Scholar]
41. McLaggan, M. S., Hadden, R. M., Gillie, M. (2018). Fire performance of phase change material enhanced plasterboard. Fire Technology, 54, 117–134. [Google Scholar]
42. Zhang, Y., Tang, B., Wang, L., Lu, R., Zhao, D. et al. (2017). Novel hybrid form-stable polyether phase change materials with good fire resistance. Energy Storage Materials, 6, 46–52. [Google Scholar]
43. Zotova, I. (2023). Ligno-cellulosic insulation boards of improved performance and the technology of their manufacture (Ph.D Thesis). Riga Technical University, Latvia. https://doi.org/10.7250/9789934229954 [Google Scholar] [CrossRef]
44. Buksans, E. (2009). Different factor influence on fire safety of wood materials and prediction of the reaction to fire (Ph.D. Thesis). Latvia University of Agriculture, Jelgava. [Google Scholar]
45. LVS ISO 5660-1:2015/A1:2021 (2021). Reaction-to-fire tests—Heat release, smoke production and mass loss rate. https://www.lvs.lv/lv/products/149817 (accessed on 15/10/2021). [Google Scholar]
Cite This Article
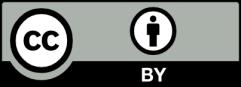