Open Access
ARTICLE
Peridynamic Shell Model Based on Micro-Beam Bond
1
School of Automotive Engineering, Dalian University of Technology, Dalian, 116024, China
2
State Key Laboratory of Structural Analysis for Industrial Equipment, Dalian University of Technology, Dalian, 116024, China
* Corresponding Author: Guozhe Shen. Email:
(This article belongs to the Special Issue: Peridynamics and its Current Progress)
Computer Modeling in Engineering & Sciences 2023, 134(3), 1975-1995. https://doi.org/10.32604/cmes.2022.021415
Received 13 January 2022; Accepted 13 April 2022; Issue published 20 September 2022
Abstract
Peridynamics (PD) is a non-local mechanics theory that overcomes the limitations of classical continuum mechanics (CCM) in predicting the initiation and propagation of cracks. However, the calculation efficiency of PD models is generally lower than that of the traditional finite element method (FEM). Structural idealization can greatly improve the calculation efficiency of PD models for complex structures. This study presents a PD shell model based on the micro-beam bond via the homogenization assumption. First, the deformations of each endpoint of the micro-beam bond are calculated through the interpolation method. Second, the micro-potential energy of the axial, torsional, and bending deformations of the bond can be established from the deformations of endpoints. Finally, the micro moduli of the shell model can be obtained via the equivalence principle of strain energy density (SED). In addition, a new fracture criterion based on the SED of the micro-beam bond is adopted for crack simulation. Numerical examples of crack propagation are provided, and the results demonstrate the effectiveness of the proposed PD shell model.Keywords
Peridynamic (PD) theory was proposed by Silling [1] as a new formulation of the classical continuum mechanics (CCM) to solve fracture and failure issues. The PD equations of motion appear as integral-differential equations [2], and the integral does not depend on the continuity of the displacement. Thus, PD theory is spontaneously applied to analyze and solve discontinuity problems, such as crack propagation. In recent years, PD theory has been rapidly developed and applied to fracture or damage analysis of solid structures, such as the fracture problems of isotropic and anisotropic materials [3–5], the problems of plasticity [6–8], the crack branch [9–11] and impact [12] of brittle materials, composite materials [13–15], crack bending problem [16], and nonlinear analysis [17,18].
However, the calculation efficiency of PD models is usually lower than that of other traditional numerical methods, such as the finite element method (FEM), especially for complex structures. The coupling method is a strategy to improve calculation efficiency. Han et al. [19] proposed a local/non-local coupling model via the Arlequin approach; this model couples energy equations of the PD and CCM models in an overlapping domain. Han et al. [20] presented a hybrid adaptive local-continuum damage/PD model by using the morphing method [21,22]. Structural idealization is often employed in engineering as a useful method to reduce the calculation time of PD models. Silling et al. [23] proposed a two-dimensional (2D) PD model for membranes and used this model for the numerical simulation of membrane stretching and dynamic tearing. Gerstle et al. [24] proposed the micropolar PD model that has two stiffness parameters. This model is mainly used to solve 2D plane problems. O’Grady et al. [25] introduced a non-ordinary state-based PD (SBPD) Kirchhoff-Love plate model based on beam models to represent the bending deformation of the plate, which is derived from the concept of a rotating spring with the bond between two material points. Taylor et al. [26] presented a 2D bond-based PD (BBPD) plate model through the asymptotic analysis of thin plates. This model can effectively analyze thin plate structures, including fractures caused by bending. Diyaroglu et al. [27] proposed a new PD Mindlin plate model based on the BBPD formulation while accounting for transverse shear deformation. The PD equations of motion were established and simplified to the same form as those of the classical Mindlin plate equations. Chowdhury et al. [28] proposed an SBPD model for linear elastic shells by introducing a shear correction factor and a shear deformation correction considering shell thickness. Taştan et al. [29] developed a PD model for orthotropic Kirchhoff thin plates based on the BBPD formulation by using the homogenized approach. Sarego et al. [30] proposed a 2D linearized ordinary SBPD model for elastic deformation and computed the stiffness matrix for 2D plane stress/strain conditions, which is suitable for constructing membrane structures. Yang et al. [31] implemented the PD Mindlin plate formulations presented by Diyaroglu et al. [27] in the FEM framework. Nguyen et al. [32] developed a new ordinary SBPD model to predict the thermomechanical behaviors of 3D shell structures with six degrees of freedom, providing numerical methods and computational steps to deal with complex shell structures. Yang et al. [33] proposed a new PD Kirchhoff plate model based on the SBPD formulation, which is computationally efficient because each material point of the plate model has only one degree of freedom. Yolum et al. [34] presented a PD formulation for orthotropic Mindlin plates with transverse shear deformation. Vazic et al. [35] established a PD model for Mindlin plates based on Winkler’s elastic theory, which is an extension of the Mindlin plate model proposed by Diyaroglu et al. [27]. Oterkus et al. [36] developed a new PD formulation for shell membranes. PD equations of motion were established by using Euler-Lagrange equations, and the bond constant of the shell membrane was determined by comparing PD equations of motion with classical equations of motion under a special condition that horizon tends to zero. Zhang et al. [37] developed a SBPD theory for nonlinear Reissener-Mindlin shells to model and predict large deformations of thick-walled shell structures. The controlling equations of the SBPD shell theory were derived by the non-local balance laws and the kinematic assumptions of Reissner and Mindlin plate and shell theories. Yang et al. [38] proposed a new SBPD model for functionally graded Kirchhoff plates and obtained the equations of motion of the proposed model by using the Euler-Lagrange equations and Taylor expansion. Zhang et al. [39] developed a non-local stress resultant-based geometrically-exact shell theory, which can simulate fracture and crack extension in shell structures under finite deformations. Shen et al. [40,41] proposed a PD shell model based on the micro-beam bond via the interpolation method, which is the foundation of this study.
The structural idealization strategies for PD plate and shell models proposed above can be divided into two types: BBPD model and SBPD model. Compared with the SBPD model, the BBPD model has the advantages of easy programming, simple calculation, and high calculation efficiency and has a wide range of application prospects. In the study, the in-plane deformation part of the PD shell in our previous work [40] is improved, and a new fracture criterion based on the strain energy density (SED) of the micro-beam bond is proposed. The reconstruction process of the whole PD shell model is described in detail through the strain homogenization method. First, the deformations of each endpoint of the micro-beam bond are calculated by the interpolation method. Second, the micro-potential energy of the axial, torsional, and bending deformations of the bond can be established from the deformations of endpoints. Finally, the micro moduli of the shell model can be obtained via the equivalence principle of SED.
The rest of this paper is organized as follows. Section 2 reviews the basic formulations of the micro-beam bond with axial, torsional, and bending deformations. Section 3 mainly describes the derivation process of the micro moduli of various deformations in the PD shell model and presents a new energy failure criterion of the micro-beam bond for PD shells. In Section 4, some numerical examples are given, including a V-shaped notch plate under pressure loading, a notched plate under stretching, a notched cylinder under internal pressure, and a notched S-shaped curved shell under stretching. Finally, Section 5 provides the conclusions.
As shown in Fig. 1, the micro-beam bond is assumed to be composed of point
Figure 1: Micro-beam bond with its (a) horizon and (b) local coordinate system
In the local coordinate system of the micro-beam bond, the relationship between the force/moment densities and displacements of endpoints of the micro-beam bond can be expressed as
where
in which
and
In Eqs. (1)–(3),
As shown in Fig. 2, the horizon
Figure 2: Horizon of point xi is exactly enclosed by a square element
3.1 Micro Moduli of in-Plane Deformation for PD Shells
The in-plane deformation only includes the translational displacement of the
where
The in-plane displacement vector at any position in the square element can be expressed by the Allman interpolation function [42] and Eq. (4) as
where
According to Eq. (5), the in-plane displacement vector at endpoints
where
In the local coordinate system of the micro-beam bond, the in-plane displacement vector at endpoints
Through coordinate transformation, the in-plane displacement vector at endpoints
where
where
As shown in Fig. 3, the micro-beam bond can only be subjected to axial deformation along the
where
where
Figure 3: Micro-beam bond subjected to axial and transversal deformation for the in-plane deformation (a) undeformed state and (b) deformed state
Substituting Eq. (6) into Eq. (7) can be obtained as
According to the homogenization assumption, the strain in the square element is assumed to be equal everywhere and is
where
Substituting Eq. (9) into Eq. (8) can be obtained as
where
The micro moduli matrix of the micro-beam bond corresponding to axial and transversal deformations is defined as
Therefore, the micro-potential energy of the micro-beam bond can be expressed by Eqs. (10) and (11) as
Then, the in-plane SED of point
where the factory
The in-plane SED of point
where
where E is Young’s modulus, and
By setting Eq. (13) equal to Eq. (14), the values of
3.2 Micro Moduli of Bending Deformation for PD Shells
The bending deformation only includes the transversal displacement along the
where
The bending displacement vector at any position of the square element can be expressed by a cubic interpolation function [40] and Eq. (16) as
where
According to Eq. (17), the bending displacement vector at endpoints
where
In the local coordinate system of the micro-beam bond, the bending displacement vector at endpoints
Through coordinate transformation, the bending displacement vector at endpoints
where
As shown in Fig. 4, the micro-beam bond can only be subjected to transversal deformation around the
where
Figure 4: Micro-beam bond subjected to transversal and torsional deformation for the bending deformation (a) undeformed state and (b) deformed state
Substituting Eq. (18) into Eq. (19) can be obtained as
According to the homogenization assumption, the strain in the square element is assumed to be equal everywhere and is
where
Substituting Eq. (21) into Eq. (20) can be obtained as
where
The micro moduli matrix of the micro-beam bond corresponding to bending and torsional deformations is defined as
Therefore, the micro-potential energy of the micro-beam bond can be expressed by Eqs. (22) and (23) as
Then, the bending SED of point
The bending SED of point
where
By setting Eq. (25) equal to Eq. (26), the values of
So far, the four micro moduli of various deformations for the PD shell model in Eqs. (15) and (27) have all been solved, and the stiffness matrix of a micro-beam bond for PD shells can be formed easily.
By comparing the relationship between the elongation rate s and the critical elongation rate
where t is the thickness of the shell and
where
where
Figure 5: Schematic of the fracture surface
Assuming that the micro-beam bond is uniformly deformed in the neighborhood horizon of point
where
Then, substituting Eq. (30) into Eq. (28), the integral fracture energy equation can be calculated as
Finally, the energy failure criterion of a micro-beam bond can be expressed by Eq. (31) as
4.1 V-Shaped Notch Plate under Pressure Loading
A soda-lime brittle glass plate is selected to demonstrate that the proposed shell model can simulate its crack propagation. The geometry and dimensions of the glass specimen are shown in Fig. 6. Thec sample has the dimension of width
Figure 6: Geometry and dimensions of the V-shaped notch plate
Numerical results are shown in Figs. 7a–7c. As the loading time is prolonged, the crack propagates slowly in the pre-crack direction and the crack bifurcation appears at approximately 60
Figure 7: Numerical results of crack propagation for the V-shaped notch plate at loading time of (a) 45
4.2 Pre-Notched Plate under Stretching
As shown in Fig. 8, the material characteristics, geometric shape, and boundary conditions of the rectangular thin plate are selected as described in literature [49]. The rectangular thin plate has the dimension of length
Figure 8: Dimensions and boundary conditions of the pre-notched plate
Four discrete mesh sizes of 1.25, 1, 0.8, and 0.5 mm are selected to investigate the effect of mesh refinement on cracks, respectively. The crack propagation paths of the plate using four uniform grids at 47
Figure 9: Crack propagation paths of the pre-notched plane under different discretizations. Mesh spacing
4.3 Pre-Notched Cylinder under Internal Pressure
A cylindrical shell [50] subjected to internal pressure in the axial direction and symmetrical pre-notches with bending deformation and membrane deformation is selected to verify the applicability of the proposed PD shell model to the crack propagation of the ordinary shell model. As shown in Fig. 10, the cylinder has a cross-sectional radius of
Figure 10: Axially pre-notched thin cylinders under internal pressure (a) without tear straps and (b) with tear straps
Figure 11: Crack propagation path of the axially pre-notched cylinder without tear straps under internal pressure (a) 0.81 MPa, (b) 0.49 MPa, (c) 0.35 MPa, (d) 0.24 MPa, (e) 0.16 MPa, and (f) 0.095 MPa
Figure 12: Crack propagation path of the axially pre-notched cylinder with tear straps under internal pressure (a) 0.85 MPa, (b) 0.50 MPa, (c) 0.40 MPa, (d) 0.47 MPa, (e) 0.53 MPa, and (f) 0.46 MPa
4.4 Pre-Notched S-Shaped Curved Shell under Stretching
In this example, an S-shaped curved shell with pre-notches is selected to verify that the proposed PD shell model is applicable to any shell structure and to deal with thin shells with arbitrary cracks. The geometry and dimensions of the long side of the S-shaped curved shell are shown in Fig. 13, which is formed by two arcs tangent to each other with a radius of
Figure 13: S-shaped shell structure with pre-notch (a) parallel to YZ-plane and (b) 45° with YZ-plane
The damage diagrams of the shell structure at different loading times for two cases are shown in Figs. 14 and 15. Fig. 14 shows that the crack parallel to the YZ-plane propagates in two opposite directions, and the propagation path is roughly parallel to the YZ-plane. However, at the end of the crack propagation, crack bifurcation occurs, and two slightly bifurcated crack propagation paths can be observed. As shown in Fig. 15, the crack at an angle of
Figure 14: Propagation of crack parallel to the YZ-plane, and the time of (a) 3
Figure 15: Propagation of the crack at an angle of
In this study, a PD shell model based on the micro-beam bond via the homogenization method is presented. First, the deformations of each endpoint of the micro-beam bond are calculated using the interpolation method. Second, the micro-potential energy of the axial, torsional, and bending deformations of the bond can be established from the deformations of endpoints. Finally, the micro moduli of the shell model can be obtained via the equivalence principle of SED. The most critical aspect is the establishment of the conversion relationship between strains of the micro-beam bond and strains of the square element, which can significantly simplify the process of deriving the micro moduli. Different deformations of the micro-beam bond are considered; thus, it is not restricted by material parameters. On the basis of elasticity and small deformations, the 2D plane stress model and the bending model are combined to form a general PD shell model, which is a combination of axial, torsional, and bending deformations. The effectiveness of the proposed PD shell model is demonstrated by several numerical examples. The strain homogenization method used to construct the PD shell model in this study will be applied to the construction of other models in the future, such as anisotropic and large deformation models.
Acknowledgement: The authors wish to express their appreciation to the reviewers for their helpful suggestions which greatly improved the presentation of this paper.
Funding Statement: This work was funded by Project of the National Natural Science Foundation of China (Grant No. 11872017). The support is gratefully acknowledged.
Conflicts of Interest: The authors declare that they have no conflicts of interest to report regarding the present study.
References
1. Silling, S. A. (2000). Reformulation of elasticity theory for discontinuities and long-range forces. Journal of the Mechanics and Physics of Solids, 48(1), 175–209. DOI 10.1016/S0022-5096(99)00029-0. [Google Scholar] [CrossRef]
2. Kan, X., Yan, J., Li, S., Zhang, A. (2021). On differences and comparisons of peridynamic differential operators and nonlocal differential operators. Computational Mechanics, 68(6), 1349–1367. DOI 10.1007/s00466-021-02072-8. [Google Scholar] [CrossRef]
3. D’Antuono, P., Morandini, M. (2017). Thermal shock response via weakly coupled peridynamic thermo-mechanics. International Journal of Solids and Structures, 129, 74–89. DOI 10.1016/j.ijsolstr.2017.09.010. [Google Scholar] [CrossRef]
4. Azdoud, Y., Han, F., Lubineau, G. (2013). A morphing framework to couple non-local and local anisotropic continua. International Journal of Solids and Structures, 50(9), 1332–1341. DOI 10.1016/j.ijsolstr.2013.01.016. [Google Scholar] [CrossRef]
5. Mikata, Y. (2019). Linear peridynamics for isotropic and anisotropic materials. International Journal of Solids and Structures, 158, 116–127. DOI 10.1016/j.ijsolstr.2018.09.004. [Google Scholar] [CrossRef]
6. Chen, H., Lin, E., Liu, Y. (2014). A novel volume-compensated particle method for 2D elasticity and plasticity analysis. International Journal of Solids and Structures, 51(9), 1819–1833. DOI 10.1016/j.ijsolstr.2014.01.025. [Google Scholar] [CrossRef]
7. Madenci, E., Oterkus, S. (2016). Ordinary state-based peridynamics for plastic deformation according to von mises yield criteria with isotropic hardening. Journal of the Mechanics and Physics of Solids, 86, 192–219. DOI 10.1016/j.jmps.2015.09.016. [Google Scholar] [CrossRef]
8. Pashazad, H., Kharazi, M. (2019). A peridynamic plastic model based on von mises criteria with isotropic, kinematic and mixed hardenings under cyclic loading. International Journal of Mechanical Sciences, 156, 182–204. DOI 10.1016/j.ijmecsci.2019.03.033. [Google Scholar] [CrossRef]
9. Ha, Y. D., Bobaru, F. (2011). Characteristics of dynamic brittle fracture captured with peridynamics. Engineering Fracture Mechanics, 78(6), 1156–1168. DOI 10.1016/j.engfracmech.2010.11.020. [Google Scholar] [CrossRef]
10. Ha, Y. D., Bobaru, F. (2010). Studies of dynamic crack propagation and crack branching with peridynamics. International Journal of Fracture, 162(1), 229–244. DOI 10.1007/s10704-010-9442-4. [Google Scholar] [CrossRef]
11. Zhou, X., Wang, Y., Qian, Q. (2016). Numerical simulation of crack curving and branching in brittle materials under dynamic loads using the extended non-ordinary state-based peridynamics. European Journal of Mechanics-A/Solids, 60, 277–299. DOI 10.1016/j.euromechsol.2016.08.009. [Google Scholar] [CrossRef]
12. Chu, B., Liu, Q., Liu, L., Lai, X., Mei, H. (2020). A rate-dependent peridynamic model for the dynamic behavior of ceramic materials. Computer Modeling in Engineering & Sciences, 124(1), 151–178. DOI 10.32604/cmes.2020.010115. [Google Scholar] [CrossRef]
13. Dorduncu, M. (2019). Stress analysis of laminated composite beams using refined zigzag theory and peridynamic differential operator. Composite Structures, 218, 193–203. DOI 10.1016/j.compstruct.2019.03.035. [Google Scholar] [CrossRef]
14. Hu, Y., Yu, Y., Madenci, E. (2020). Peridynamic modeling of composite laminates with material coupling and transverse shear deformation. Composite Structures, 253, 112760. DOI 10.1016/j.compstruct.2020.112760. [Google Scholar] [CrossRef]
15. Diyaroglu, C., Oterkus, E., Madenci, E., Rabczuk, T., Siddiq, A. (2016). Peridynamic modeling of composite laminates under explosive loading. Composite Structures, 144, 14–23. DOI 10.1016/j.compstruct.2016.02.018. [Google Scholar] [CrossRef]
16. Diana, V., Ballarini, R. (2020). Crack kinking in isotropic and orthotropic micropolar peridynamic solids. International Journal of Solids and Structures, 196, 76–98. DOI 10.1016/j.ijsolstr.2020.03.025. [Google Scholar] [CrossRef]
17. Nguyen, C. T., Oterkus, S. (2020). Ordinary state-based peridynamic model for geometrically nonlinear analysis. Engineering Fracture Mechanics, 224, 106750. DOI 10.1016/j.engfracmech.2019.106750. [Google Scholar] [CrossRef]
18. Liu, Z., Bie, Y., Cui, Z., Cui, X. (2020). Ordinary state-based peridynamics for nonlinear hardening plastic materials’ deformation and its fracture process. Engineering Fracture Mechanics, 223, 106782. DOI 10.1016/j.engfracmech.2019.106782. [Google Scholar] [CrossRef]
19. Han, F., Lubineau, G. (2012). Coupling of nonlocal and local continuum models by the arlequin approach. International Journal for Numerical Methods in Engineering, 89(6), 671–685. DOI 10.1002/nme.3255. [Google Scholar] [CrossRef]
20. Han, F., Lubineau, G., Azdoud, Y. (2016). Adaptive coupling between damage mechanics and peridynamics: A route for objective simulation of material degradation up to complete failure. Journal of the Mechanics and Physics of Solids, 94, 453–472. DOI 10.1016/j.jmps.2016.05.017. [Google Scholar] [CrossRef]
21. Han, F., Lubineau, G., Azdoud, Y., Askari, A. (2016). A morphing approach to couple state-based peridynamics with classical continuum mechanics. Computer Methods in Applied Mechanics and Engineering, 301, 336–358. DOI 10.1016/j.cma.2015.12.024. [Google Scholar] [CrossRef]
22. Lubineau, G., Azdoud, Y., Han, F., Rey, C., Askari, A. (2012). A morphing strategy to couple non-local to local continuum mechanics. Journal of the Mechanics and Physics of Solids, 60(6), 1088–1102. DOI 10.1016/j.jmps.2012.02.009. [Google Scholar] [CrossRef]
23. Silling, S. A., Bobaru, F. (2005). Peridynamic modeling of membranes and fibers. International Journal of Non-Linear Mechanics, 40(2–3), 395–409. DOI 10.1016/j.ijnonlinmec.2004.08.004. [Google Scholar] [CrossRef]
24. Gerstle, W., Sau, N., Silling, S. (2007). Peridynamic modeling of concrete structures. Nuclear Engineering and Design, 237(12–13), 1250–1258. DOI 10.1016/j.nucengdes.2006.10.002. [Google Scholar] [CrossRef]
25. O’Grady, J., Foster, J. (2014). Peridynamic plates and flat shells: A non-ordinary, state-based model. International Journal of Solids and Structures, 51(25–26), 4572–4579. DOI 10.1016/j.ijsolstr.2014.09.003. [Google Scholar] [CrossRef]
26. Taylor, M., Steigmann, D. J. (2015). A Two-dimensional peridynamic model for thin plates. Mathematics and Mechanics of Solids, 20(8), 998–1010. DOI 10.1177/1081286513512925. [Google Scholar] [CrossRef]
27. Diyaroglu, C., Oterkus, E., Oterkus, S., Madenci, E. (2015). Peridynamics for bending of beams and plates with transverse shear deformation. International Journal of Solids and Structures, 69, 152–168. DOI 10.1016/j.ijsolstr.2015.04.040. [Google Scholar] [CrossRef]
28. Chowdhury, S. R., Roy, P., Roy, D., Reddy, J. (2016). A peridynamic theory for linear elastic shells. International Journal of Solids and Structures, 84, 110–132. DOI 10.1016/j.ijsolstr.2016.01.019. [Google Scholar] [CrossRef]
29. Taştan, A., Yolum, U., Güler, M. A., Zaccariotto, M., Galvanetto, U. (2016). A 2D peridynamic model for failure analysis of orthotropic thin plates due to bending. Procedia Structural Integrity, 2, 261–268. DOI 10.1016/j.prostr.2016.06.034. [Google Scholar] [CrossRef]
30. Sarego, G., Le, Q. V., Bobaru, F., Zaccariotto, M., Galvanetto, U. (2016). Linearized state-based peridynamics for 2D problems. International Journal for Numerical Methods in Engineering, 108(10), 1174–1197. DOI 10.1002/nme.5250. [Google Scholar] [CrossRef]
31. Yang, Z., Oterkus, E., Nguyen, C. T., Oterkus, S. (2019). Implementation of peridynamic beam and plate formulations in finite element framework. Continuum Mechanics and Thermodynamics, 31(1), 301–315. DOI 10.1007/s00161-018-0684-0. [Google Scholar] [CrossRef]
32. Nguyen, C. T., Oterkus, S. (2019). Peridynamics for the thermomechanical behavior of shell structures. Engineering Fracture Mechanics, 219, 106623. DOI 10.1016/j.engfracmech.2019.106623. [Google Scholar] [CrossRef]
33. Yang, Z., Vazic, B., Diyaroglu, C., Oterkus, E., Oterkus, S. (2020). A kirchhoff plate formulation in a state-based peridynamic framework. Mathematics and Mechanics of Solids, 25(3), 727–738. DOI 10.1177/1081286519887523. [Google Scholar] [CrossRef]
34. Yolum, U., Güler, M. A. (2020). On the peridynamic formulation for an orthotropic mindlin plate under bending. Mathematics and Mechanics of Solids, 25(2), 263–287. DOI 10.1177/1081286519873694. [Google Scholar] [CrossRef]
35. Vazic, B., Oterkus, E., Oterkus, S. (2020). Peridynamic model for a mindlin plate resting on a winkler elastic foundation. Journal of Peridynamics and Nonlocal Modeling, 2(3), 229–242. DOI 10.1007/s42102-019-00019-5. [Google Scholar] [CrossRef]
36. Oterkus, E., Madenci, E., Oterkus, S. (2020). Peridynamic shell membrane formulation. Procedia Structural Integrity, 28, 411–417. DOI 10.1016/j.prostr.2020.10.048. [Google Scholar] [CrossRef]
37. Zhang, Q., Li, S., Zhang, A. M., Peng, Y., Yan, J. (2021). A peridynamic reissner-mindlin shell theory. International Journal for Numerical Methods in Engineering, 122(1), 122–147. DOI 10.1002/nme.6527. [Google Scholar] [CrossRef]
38. Yang, Z., Oterkus, E., Oterkus, S. (2021). Peridynamic modelling of higher order functionally graded plates. Mathematics and Mechanics of Solids, 26(12), 1737--1759. DOI 10.1177/10812865211004671. [Google Scholar] [CrossRef]
39. Zhang, Q., Li, S., Zhang, A. M., Peng, Y. (2021). On nonlocal geometrically exact shell theory and modeling fracture in shell structures. Computer Methods in Applied Mechanics and Engineering, 386, 114074. DOI 10.1016/j.cma.2021.114074. [Google Scholar] [CrossRef]
40. Shen, G., Xia, Y., Hu, P., Zheng, G. (2021). Construction of peridynamic beam and shell models on the basis of the micro-beam bond obtained via interpolation method. European Journal of Mechanics-A/Solids, 86, 104174. DOI 10.1016/j.euromechsol.2020.104174. [Google Scholar] [CrossRef]
41. Shen, G., Xia, Y., Li, W., Zheng, G., Hu, P. (2021). Modeling of peridynamic beams and shells with transverse shear effect via interpolation method. Computer Methods in Applied Mechanics and Engineering, 378, 113716. DOI 10.1016/j.cma.2021.113716. [Google Scholar] [CrossRef]
42. Nguyen-Van, H., Mai-Duy, N., Tran-Cong, T. (2009). An improved quadrilateral flat element with drilling degrees of freedom for shell structural analysis. Computer Modeling in Engineering & Sciences, 49(2), 81–110. DOI 10.3970/cmes.2009.049.081. [Google Scholar] [CrossRef]
43. Foster, J. T., Silling, S. A., Chen, W. (2011). An energy based failure criterion for use with peridynamic states. International Journal for Multiscale Computational Engineering, 9(6), 675--688. DOI 10.1615/IntJMultCompEng.2011002407. [Google Scholar] [CrossRef]
44. Yu, H., Li, S. (2020). On energy release rates in peridynamics. Journal of the Mechanics and Physics of Solids, 142, 104024. DOI 10.1016/j.jmps.2020.104024. [Google Scholar] [CrossRef]
45. Mehrmashhadi, J., Bahadori, M., Bobaru, F. (2020). On validating peridynamic models and a phase-field model for dynamic brittle fracture in glass. Engineering Fracture Mechanics, 240, 107355. DOI 10.1016/j.engfracmech.2020.107355. [Google Scholar] [CrossRef]
46. Sundaram, B. M., Tippur, H. V. (2018). Dynamic fracture of soda-lime glass: A full-field optical investigation of crack initiation, propagation and branching. Journal of the Mechanics and Physics of Solids, 120, 132–153. DOI 10.1016/j.jmps.2018.04.010. [Google Scholar] [CrossRef]
47. Silling, S. A., Askari, E. (2005). A meshfree method based on the peridynamic model of solid mechanics. Computers & Structures, 83(17–18), 1526–1535. DOI 10.1016/j.compstruc.2004.11.026. [Google Scholar] [CrossRef]
48. Zheng, G., Wang, J., Shen, G., Xia, Y., Li, W. (2021). A new quadrature algorithm consisting of volume and integral domain corrections for two-dimensional peridynamic models. International Journal of Fracture, 229(1), 39–54. DOI 10.1007/s10704-021-00540-z. [Google Scholar] [CrossRef]
49. Dipasquale, D., Zaccariotto, M., Galvanetto, U. (2014). Crack propagation with adaptive grid refinement in 2D peridynamics. International Journal of Fracture, 190(1–2), 1–22. DOI 10.1007/s10704-014-9970-4. [Google Scholar] [CrossRef]
50. Kiendl, J., Ambati, M., de Lorenzis, L., Gomez, H., Reali, A. (2016). Phase-field description of brittle fracture in plates and shells. Computer Methods in Applied Mechanics and Engineering, 312, 374–394. DOI 10.1016/j.cma.2016.09.011. [Google Scholar] [CrossRef]
Appendix A. Shape functions for in-plane deformation of the PD shell model
The parameters of the bottom right corner mentioned in Eq. (A1) can be defined as
where
where K, I, J is an ordered triplet, and the order of value is (5, 1, 2), (6, 2, 3), (7, 3, 4), (8, 4, 1).
Appendix B. Shape functions for bending deformation of the PD shell model
where
Cite This Article
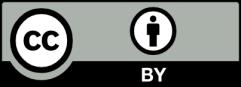