Open Access
ARTICLE
Capacity Optimization Configuration of Hydrogen Production System for Offshore Surplus Wind Power
1 Guangzhou Power Supply Bureau, Guangdong Grid Corporation, Guangzhou, 510620, China
2 Sichuan Energy Internet Research Institute, Tsinghua University, Chengdu, 610042, China
3 Energy Development Research Institute Co., Ltd., China Southern Power Grid, Guangzhou, 510530, China
* Corresponding Author: Ruixiao Lin. Email:
Energy Engineering 2023, 120(12), 2803-2818. https://doi.org/10.32604/ee.2023.042328
Received 26 May 2023; Accepted 03 August 2023; Issue published 29 November 2023
Abstract
To solve the problem of residual wind power in offshore wind farms, a hydrogen production system with a reasonable capacity was configured to enhance the local load of wind farms and promote the local consumption of residual wind power. By studying the mathematical model of wind power output and calculating surplus wind power, as well as considering the hydrogen production/storage characteristics of the electrolyzer and hydrogen storage tank, an innovative capacity optimization allocation model was established. The objective of the model was to achieve the lowest total net present value over the entire life cycle. The model took into account the cost-benefit breakdown of equipment end-of-life cost, replacement cost, residual value gain, wind abandonment penalty, hydrogen transportation, and environmental value. The MATLAB-based platform invoked the CPLEX commercial solver to solve the model. Combined with the analysis of the annual average wind speed data from an offshore wind farm in Guangdong Province, the optimal capacity configuration results and the actual operation of the hydrogen production system were obtained. Under the calculation scenario, this hydrogen production system could consume 3,800 MWh of residual electricity from offshore wind power each year. It could achieve complete consumption of residual electricity from wind power without incurring the penalty cost of wind power. Additionally, it could produce 66,500 kg of green hydrogen from wind power, resulting in hydrogen sales revenue of 3.63 million RMB. It would also reduce pollutant emissions from coal-based hydrogen production by 1.5 tons and realize an environmental value of 4.83 million RMB. The annual net operating income exceeded 6 million RMB and the whole life cycle NPV income exceeded 50 million RMB. These results verified the feasibility and rationality of the established capacity optimization allocation model. The model could help advance power system planning and operation research and assist offshore wind farm operators in improving economic and environmental benefits.Keywords
Nomenclature
The rated power of wind turbine, MW | |
The output power of wind turbine, MW | |
The input power of electrolyzer, MW | |
The nominal power capacity of electrolyzer, MW | |
The power consumption of hydrogen storage tank, MW | |
The power consumption of desalinator, MW | |
The power consumption of pressurizer, MW | |
The rated wind speed of wind turbine, m/s | |
Cut-in wind speed, m/s | |
Cut-out wind speed, m/s | |
The surplus wind power, MWh | |
The theoretical wind power generation, MWh | |
The actual wind power generation, MWh | |
The number of wind farms | |
The number of wind farm prototype units | |
The number of wind farm units | |
The power consumed to produce a unit volume of hydrogen | |
The volume of hydrogen produced by the electrolyzer, m3 | |
The volume of stored hydrogen, m3 | |
The volume of hydrogen storage tank, m3 | |
The amount of hydrogen substance, mol | |
The pressure of storage tank, Pa | |
The gas constant, J/(mol·K) | |
The unit time step, h | |
The initial construction cost of the system, ten thousand yuan | |
The real discount rate | |
The life cycle, year | |
The system lifetime, year | |
The start/stop status | |
The annual cycle cost, ten thousand yuan | |
The annual cycle benefit, ten thousand yuan | |
The unit construction cost of electrolyzer, yuan | |
The unit construction cost of hydrogen storage tank, yuan | |
The unit price of the surplus wind power, yuan | |
The unit maintenance costs of electrolyzer, yuan | |
The unit maintenance costs of hydrogen storage tank, yuan | |
The unit replacement cost of electrolyzer, yuan | |
The unit replacement cost of hydrogen storage tank, yuan | |
The unit penalty cost, yuan | |
The selling price per unit volume of hydrogen, yuan | |
The cost per unit volume of hydrogen transported per unit distance, yuan/(m3·km) | |
The offshore distance, km | |
The cost of dismantling, ten thousand yuan | |
The salvage value of the unit, ten thousand yuan | |
The number of units | |
The pollutants produced in coal-based hydrogen production | |
The unit number | |
The type of pollutant | |
The environmental cost of pollutant, yuan | |
The emission of pollutant per unit of coal, g | |
The efficiency of coal to hydrogen | |
The lifetime of the device, year | |
The remaining life of the device at the end of its life cycle, year |
To achieve the objectives of the carbon peak and carbon neutrality targets, the National Development and Reform Commission of China, along with the National Energy Board of China and nine other departments, have jointly released the “14th Five-Year” renewable energy development plan. This plan outlines a clear strategy for the development of both onshore and offshore renewable energy for local and outbound consumption. Over recent years, there has been a significant increase in offshore wind power installed capacity, leading to an enrichment in the proportion of grid-connected new energy [1,2]. As of June 2022, the nation had reached a total installed wind power capacity of 342 million kW. Nonetheless, the unpredictability and instability associated with offshore wind power may have an impact on power quality, thereby constraining its widespread adoption and the capacity of societal grid. One potential repercussion of this phenomenon is the prevalence of surplus wind power, which not only wastes natural resources and financial investments but also jeopardizes wind farm profitability, hindering efforts for energy structure improvement and environmental preservation. Currently, the primary concern is how to enhance wind power consumption efficiency.
Hydrogen energy is a form of secondary energy derived from abundant sources, known for its environmentally friendly nature, low carbon emissions, and wide range of applications. Its potential spans various domains, including facilitating large-scale consumption of renewable energy, enabling substantial power grid peaking, and ensuring energy storage across different seasons and regions. Moreover, it promotes the reduction of carbon emissions in industries, construction, and transportation sectors, offering an efficient approach to using fossil energy in a clean and effective manner, while also facilitating the extensive growth of renewable energy. To capitalize on the progress in offshore wind power and hydrogen energy, it is crucial to increase the local capacity of wind power plants and encourage local consumption by deploying hydrogen production systems. Additionally, research efforts should focus on providing clean and green energy for electrolytic water hydrogen production, effectively reducing the cost of hydrogen production. These research areas are of paramount importance at present [3,4].
Currently, both domestic and international research regarding hydrogen production systems for offshore wind power is in an early stage. Xu et al. [5] formulated an optimal configuration model for hydrogen storage capacity for new energy sites with the objective of minimizing investment costs and maximizing CO2 emission reduction, while also minimizing cumulative tracking plan errors. In addition, the model considers constraints such as residual rates and site area. The findings demonstrate that implementing the proposed hydrogen energy storage system can significantly diminish CO2 emissions, system power disposal, and the variance between the actual output and the dispatch command throughout the system’s life cycle. Jia et al. [6] established a capacity optimization configuration model with multiple objectives to achieve coordinated optimization dispatch within a multi-energy system featuring wind power residual rate and power shortage rates, alongside economic indices that incorporate both hydrogen sales revenue and the average cost over the system's lifetime. The proposed model aims to enhance the integration of wind power and hydrogen into the energy system for day-ahead operations. Guo et al. [7] employed a wind-powered hydrogen generator in an integrated energy system and created an optimization framework aimed at integrating multiple energy sources to satisfy electric, hydrogen, and thermal loads simultaneously using a series of diverse control strategies within an electric hydrogen generator equipped system. The findings demonstrate the crucial role of the system in limiting operational expenses and augmenting clean energy usage. Additionally, augmenting the hydrogen load to a specific level is advantageous for both the economic and environmentally friendly-operation of the system. Huang et al. [8] introduced a method to distribute hydrogen production capacity using a hydrogen production system that converts otherwise surplus wind power into hydrogen. The utilization of the interval estimation method aims to establish a statistical model that predicts the annual wind power residual rate. From this model, an optimal capacity configuration scheme for the hydrogen production system is determined by applying interval optimization theory and multi-attribute decision models. The objective of this scheme is to maximize economic returns. The results indicate that it is more reasonable to co-construct a hydrogen production system among wind farm clusters. This approach has a better effect on dissipating the surplus wind power from wind farms. Scolaro et al. [9] put forward an optimal investment strategy for offshore wind farms, which focuses on constructing hydrogen production facilities. The study employs empirical data obtained from the European electricity market and wind power generation. The findings suggest that offshore wind farms experiencing increased competition and existential threats related to low electricity prices can benefit greatly from investing in hydrogen production. In addition to the advantages of seasonal storage and the sale of hydrogen, this investment has the potential to replace industrial hydrogen while also making significant reductions in emissions. Leahy et al. [10] suggested three potential methods for generating hydrogen via offshore wind farms, which consist of distributed, centralized, and onshore hydrogen production. To determine the most cost-effective approach, the authors conducted a detailed evaluation of the options utilizing NPV calculations, sensitivity analysis, and Monte Carlo simulations. The findings suggest that the distributed hydrogen production strategy is the most financially viable, attributable to the absence of costly high-voltage DC cables and offshore substations. Zhang et al. [11] put forth three distinct energy storage application scenarios for both off-grid and grid-connected systems. These scenarios include electricity, hydrogen, and electricity-hydrogen, with hydrogen energy primarily utilized for storage, transportation, and marketing purposes. Through a comparative and analytical assessment of the capacity configurations of these multi-energy systems, it was determined that the economics of grid-connected systems outperform those of off-grid systems. Furthermore, the net present cost of the system is noticeably impacted by the average wind velocity. Calado et al. [12] provided a summary of the technologies involved in hydrogen production, along with an analysis of two possible hydrogen-producing systems from offshore wind energy. This includes hydrogen storage, the system configuration (i.e., offshore vs. onshore electrolyzer), and the potential uses of hydrogen, e.g., Power to Mobility, Power to Power, and Power to Gas. Compared to wind energy on land, offshore wind has higher wind speeds and is more consistent, making it a more attractive resource to generate electricity. The main drawbacks have been the higher cost and technical challenges associated with transmitting the electricity to shore, though this has improved in recent years. Luo et al. [13] analyzed the methods of producing hydrogen from offshore wind power, including alkaline water electrolysis, proton exchange membrane electrolysis, and solid oxide electrolysis, and revealed that the transportation method of hydrogen is closely related to the offshore distance for the hydrogen production station. Submarine pipeline and liquid hydrogen ship are two promising hydrogen transportation methods for hydrogen production from offshore wind power. According to preliminary estimation, it is more economically advantageous to sell hydrogen than to sell electricity without subsidies. Jang et al. [14] presented a techno-economic analysis of three offshore wind power plant arrangements, including distributed hydrogen production, centralized hydrogen production, and onshore hydrogen production. The analysis results show that the hydrogen production cost was 13.81, 13.85, 14.58 $/kgH2 for the distributed, centralized, and onshore hydrogen production cases, respectively. Therefore, the distributed case has the most competitive advantage due to the absence of expensive High Voltage Direct Current cable and offshore substation. Lucas et al. [15] analyzed the feasibility of hydrogen production employing electricity generated from wind energy, taking the Wind Float Atlantic offshore wind farm and Portugal’s electricity market as a case study. The preliminary study shows that PEM technology is the most suitable for H2 production from wind energy due to its faster responses and better performances at partial load. The H2 production from an offshore wind farm appeared to be promising despite its dependency on different factors, wherein the electrolyzer’s capacity factor is highlighted.
In summary, countries are still exploring feasible technical solutions for offshore wind power consumption, and the research on the capacity configuration of offshore wind power hydrogen production systems is still immature. There are mainly the following problems: the analysis of the whole life cycle cost and benefit of the hydrogen production system is not perfect, especially the end-of-life cost and residual value of the equipment are not considered; the construction cost of the entire industry chain of offshore wind power hydrogen production equipment is not fully considered; the environmental value benefits brought by hydrogen production are not considered.
To address the aforementioned problems in the field of offshore wind power hydrogen production, this paper investigates the mathematical models of wind power output and wind power abandonment calculation, as well as the hydrogen production/storage characteristics of the electrolyzer and hydrogen storage tank. It innovatively considers the cost-benefit breakdown of equipment end-of-life cost, replacement cost, residual value gain, wind abandonment penalty, hydrogen transportation, and environmental value, and establishes the optimal hydrogen production system with the objective of minimizing the total net present value cost over the entire life cycle. The CPLEX commercial solver based on the MATLAB platform is invoked to solve the model. The results of the optimal capacity allocation of the hydrogen production system in the case scenario and the actual operation verify the role of the hydrogen production system in offshore wind power consumption, improving energy utilization, increasing system revenue, and promoting energy savings and emission reduction.
2 Model of Surplus Wind Power Hydrogen Production System
The offshore wind power hydrogen production system can be divided into in-situ offshore hydrogen production system and off-shore hydrogen production system according to the location of hydrogen production. To avoid the need for additional hydrogen transmission pipelines or high-voltage DC cables, this paper utilizes the in-situ offshore hydrogen production system, which comprises a desalinator, electrolyzer, pressurizer, and hydrogen storage tank. Hydrogen is produced by the electrolyzer and stored in the hydrogen storage tank before being transported by a cargo ship for onshore sales. The structure of the system is schematically depicted in Fig. 1.
Figure 1: Structure of offshore wind power hydrogen production system
For wind speed uncertainty prediction, existing studies typically utilize probabilistic statistics to model wind speed, which is broadly classified into two categories based on the probability density function: two-parameter Weibull distribution and Rayleigh distribution [16]. In this study, the two-parameter Weibull distribution is employed.
The output power of a wind turbine exhibits intermittent and fluctuating characteristics and generally follows a quadratic distribution. The model for its output power is presented as follows [16]:
where
2.3 Calculation of Surplus Wind Power
The amount of unused wind power is determined not solely by the wind farm’s wind resource attributes and the wind power variability pattern, but also by several factors, including the acceptance capacity of the wind power access system. Surplus wind power, excluding the power lost due to equipment malfunction of the turbines, can be described as the difference between the expected power generation and the electricity produced by the wind farm [17].
where
Currently, the prototype method is a mature approach for calculating theoretical power generation [17]. The theoretical power generation of a single prototype is initially calculated by taking the average value of the theoretical power generation of all prototypes and multiplying it by the number of wind farm units.
where
2.4 Electrolyzer Hydrogen Production Model
The production of hydrogen through the electrolyzer involves the electrochemical reaction of water molecules at the anode and cathode electrodes by passing electrical current through an electrolytic apparatus containing an electrolyte. The chemical reaction can be represented by the following expression [18].
The relationship between absorbed electrical power and hydrogen production in an alkaline electrolyzer is shown below [18]:
where
2.5 Hydrogen Storage Tank Storage Model
The high-pressure gaseous hydrogen storage tank is currently the most commonly utilized method for hydrogen storage, due to its mature technology, low cost, and convenient means of transportation. This storage model allows for easy implementation of hydrogen reuse and sale, while satisfying the Clapeyron equation [19].
where
3 Capacity Optimization Configuration Model
The objective to consider is the lowest NPC of the entire life cycle of the hydrogen production system. This involves calculating all costs incurred by the system throughout its lifespan, subtracted from the present value of all benefits derived from it. Among these, the initial construction cost is a one-time capital investment, while the annual cost and annual benefit have a time value and need to be converted into present value [20,21]. The calculation formula is depicted below [22]:
where
Construction costs include the purchase of equipment, installation, commissioning, and other initial investments (construction costs of desalinators, pressurizers, and other supporting facilities are considered as fixed values).
where
1) Running costs
All the equipment in the hydrogen production system requires electricity to start up and operate normally, and the electricity consumed is purchased from the surplus wind power generated by offshore wind farms, which adds to the operating cost of the system.
where
2) Maintenance costs
Equipment during the operation process requires manual maintenance, repair, and replacement of loss materials, resulting in maintenance costs for the system (desalinator, pressurizer, and other ancillary facilities have O&M costs proportional to the construction costs, using an O&M coefficient of 0.01).
where
3) Replacement cost
When the equipment needs to be replaced at the end of its life to continue production with the same product added to the system, the system will incur replacement costs (desalinators, pressurizers, and other ancillary facilities have the same lifespan as the system life cycle and do not need to be replaced).
where
4) Penalty cost
To ensure that the surplus wind power is utilized by the hydrogen production system as much as possible, a penalty is imposed when the actual power consumed by the configured electrolyzer is less than the surplus wind power.
where
5) Transportation costs
Whenever the hydrogen in the storage tank reaches full capacity, it needs to be transported by cargo ship to the shore for sale, and the transportation cost is dependent on the volume of hydrogen stored and the distance from the shore.
where
6) End-of-life costs
When the system life cycle ends, the related facilities and equipments need to be dismantled, scrapped, and destroyed, and the resulting scrapping costs are usually estimated using historical empirical data.
where
1) Gain from hydrogen sales
Electricity represents the primary cost factor in the process of producing hydrogen from water electrolysis, thereby resulting in a comparatively elevated retail price of green hydrogen and presenting less of a commercial edge in contrast to gray and blue hydrogen. Utilizing untapped wind power to generate hydrogen is anticipated to make this renewable energy source more competitively priced in the hydrogen fuel market.
where
2) Environmental value
The hydrogen produced by water electrolysis using wind power is called green hydrogen, which has a high environmental value compared to the traditional coal-based hydrogen production process, as it avoids the emission of various pollutants.
where
3) Equipment salvage value
where
Although the hydrogen production system equipment has a certain residual value gain, considering the offshore location of the wind power project, the high transportation cost after equipment dismantling, and the harsh natural environment and high manual dismantling cost, the residual value of the equipment is usually considered to be offset by the scrapping cost.
In summary, the annual cycle cost and annual cycle benefit can be respectively expressed as:
3.2.1 Wind Turbine Operating Constraints
where
3.2.2 Hydrogen Production System Operating Constraints
where
In this paper, an offshore wind power farm project in Guangdong Province was analyzed. The annual average wind speed of the offshore wind farm is shown in Fig. 2 (data from Guangzhou Power Supply Bureau of Guangdong Power Grid Company, China), and the annual average surplus wind power of the offshore wind farm is shown in Fig. 3. The operating parameters of wind turbines are presented in Table 1, while the parameters of hydrogen production system equipment are shown in Table 2. The parameters of hydrogen production system supporting facilities are provided in Table 3, and the pollutant emissions generated by industrial hydrogen production and their environmental value are shown in Table 4. It was proposed to set the lifetime of the hydrogen production system as 25 years, the real discount rate as 6%, the unit price of surplus wind power as 0.3 yuan/kWh, the unit cost of hydrogen transportation as 1 yuan/kg·km−1, and the selling price of hydrogen as 55 yuan/kg. Since the capacity optimization configuration model built in this paper is a typical mixed-integer linear programming problem, it can be solved using the MATLAB platform by calling the CPLEX commercial solver.
Figure 2: Annual average wind speed of the offshore wind farm
Figure 3: Annual average surplus wind power of the offshore wind farm
The results of the optimal capacity configuration of the hydrogen production system under the arithmetic scenario set in this paper are shown in Table 5. The configuration includes two electrolyzers with a single hydrogen production power of 1 MW, 34 hydrogen storage tanks with a single bottle storage capacity of 35 kg, a desalinator, and a pressurizer. The cost-benefit breakdown is presented in Table 6, revealing that the total net present value cost is negative at the end of the system’s life cycle, while the realized benefit exceeds 50 million yuan. This indicates that the system is economical based on the results of the optimal capacity configuration model. The annual abandonment penalty cost is zero, signifying that the capacity configuration is reasonable and the hydrogen production system can fully consume the residual power from wind sources, demonstrating the system’s feasibility. Among the costs, construction and replacement costs represent the most significant incremental capital investments, while operation and transportation costs account for the highest annual ongoing capital investments. In terms of benefits, the revenue and environmental value associated with hydrogen sales are high due to the current high commercial hydrogen sales price and the reduction of pollutant emissions. Equipment end-of-life costs and equipment salvage value balance each other out and therefore negligible.
Figs. 4 and 5 show the annual average hydrogen production and hydrogen storage of the hydrogen production system, respectively. It can be observed that the overall residual power of the offshore wind farm, as shown in the scenario of this paper, is higher during winter and spring, and lower during summer and autumn. Correspondingly, the hydrogen production of the electrolyzer also follows this pattern, with higher production during winter and spring, and lower production during summer and autumn. Additionally, the growth rate of hydrogen storage in the hydrogen storage tank is faster in winter and spring compared to summer and autumn. The switching of hydrogen storage status in the tank is more frequent and intensive during winter and spring than in summer and autumn.
Figure 4: Annual average hydrogen production of the hydrogen production system
Figure 5: Annual average hydrogen storage capacity of hydrogen production system
From the perspective of annual operation, the capacity optimization configuration model proposed for the offshore wind power hydrogen production system enables the consumption of 3800 MWh of surplus electricity from offshore wind power each year. This allows for the complete utilization of surplus wind power without incurring penalties, resulting in the production of 66,500 kg of green hydrogen from wind power. Consequently, it yields 3.63 million yuan in revenue from hydrogen sales, reduces 1.5 tons of pollutant emissions compared to coal-based hydrogen production, and provides an environmental value of 4.83 million yuan. The annual net income exceeds 6 million yuan. These results once again validate the conclusions reached in references [5–15], highlighting that hydrogen production systems can effectively utilize wind power residuals while boosting operational revenues for wind farms.
By studying the mathematical model of wind power output and the calculation of residual wind power, along with the hydrogen production/storage characteristics of the electrolyzer and hydrogen storage tank, a capacity optimization allocation model for the hydrogen production system is developed. The model aims to minimize the total net present value cost over the entire life cycle, considering the cost-benefit breakdown of equipment end-of-life cost, residual value gain, wind abandonment penalty, hydrogen transportation, and environmental value. The model is implemented using the MATLAB platform, calling CPLEX solver to solve the model. Combined with the analysis of the annual average wind speed data of an offshore wind farm in Guangdong Province, the optimal capacity configuration results and annual operation of the hydrogen production system were obtained, and the conclusions are as follows:
(1) The capacity optimization allocation model established in this paper thoroughly examines all the costs and benefits associated with the entire life cycle of the hydrogen production system. It specifically includes the equipment scrapping cost (offset by equipment salvage value), replacement cost, wind abandonment penalty, hydrogen transportation, and environmental value. This comprehensive consideration aligns the model more closely with the real-life cycle of a project.
(2) By analyzing the capacity optimization allocation results and cost-benefit breakdown of the hydrogen production system in the calculation scenario, it is revealed that the optimal allocation results allow for the complete consumption of wind power surplus energy. Additionally, the system achieves significant benefits throughout the entire life cycle. This demonstrates the rationality and feasibility of the capacity optimization allocation model for the offshore wind power hydrogen production system presented in this paper.
(3) By proposing the capacity optimization configuration model of offshore wind power hydrogen production, the system can consume 3800 MWh of surplus electricity from offshore wind power annually. This enables the complete utilization of surplus electricity from wind power without incurring the penalty cost of abandoning wind power. The system can produce 66,500 kg of green hydrogen from wind power, and generated revenue of 3.63 million yuan from hydrogen sales. It also reduces 1.5 tons of pollutant emissions compared to coal-based hydrogen production and realizes an environmental value of 4.83 million yuan. The annual net income of operation exceeds 6 million yuan, with system revenues surpassing 50 million yuan at the end of the system’s life cycle. This demonstrates that by appropriately allocating a certain capacity of electrolytic cells to consume waste energy from wind farms, higher additional revenue can be attained. Investing in hydrogen production systems at offshore wind farms to utilize surplus wind power not only facilitates seasonal storage and sales of hydrogen but also holds significant potential for emission reduction.
The innovation in this paper lies in analyzing the cost and benefit breakdown of the complete life cycle of the offshore wind power hydrogen production system. Specifically, it includes the consideration of equipment end-of-life cost, replacement cost, residual value gain, wind abandonment penalty, hydrogen transportation, and environmental value. Additionally, the paper establishes an optimal capacity allocation model for the hydrogen production system with the objective of minimizing the total net present value cost throughout the entire life cycle. The results of this paper serve as support for addressing the capacity allocation issues in offshore wind power hydrogen production systems. They can also aid in power system planning and operation studies, while assisting offshore wind farm operators in improving economic and environmental benefits. However, economic comparisons with wind power feed-in and the cost analysis of different hydrogen transportation methods from offshore platforms have not been performed. The next step could be to explore options for utilizing offshore wind power by studying the capacity allocation of onshore hydrogen production platforms.
Acknowledgement: We would like to thank all those who have reviewed and contributed to this paper for their valuable assistance.
Funding Statement: This work is supported by Manage Innovation Project of China Southern Power Grid Co., Ltd. (No. GZHKJXM20210232).
Author Contributions: The authors confirm contribution to the paper as follows: study conception and design: Yanshan Lu; data collection: Binbin He, Jun Jiang; modelling: Ruixiao Lin, Xinzhen Zhang; analysis and interpretation of results: Zaimin Yang, Zhi Rao; draft manuscript preparation: Wenchuan Meng, Siyang Sun. All authors reviewed the results and approved the final version of the manuscript.
Availability of Data and Materials: The data of Annual Average Wind Speed and Annual Average Surplus Wind Power of an Offshore Wind Power Farm Project in Guangdong Province, China used in this study is provided by the Guangzhou Power Supply Bureau of Guangdong Power Grid Company with confidentiality agreement. The data is not made open access.
Conflicts of Interest: The authors declare that they have no conflicts of interest to report regarding the present study.
References
1. Ruan, Q. Q., Chen, Y., Pan, Z. J. (2022). Discussion on contributions of novel power system to achieving carbon emission peak and carbon neutrality of coastal city. Automation of Electric Power Systems, 46(14), 11–18. [Google Scholar]
2. Ren, D., Xiao, J., Hou, J., Du, E., Jin, C. et al. (2022). Construction and evolution of China’s new power system under dual carbon goal. Power System Technology, 46(10), 3831–3839. [Google Scholar]
3. Li, Z. Q., Qiao, Y., Lu, Z. X. (2022). Operation mode analysis and configuration optimization of offshore wind-hydrogen system. Automation of Electric Power Systems, 46(8), 104–112. [Google Scholar]
4. Jiang, D. F., Jia, Y. L., Lu, Q., Hong, B., Shen, R. B. et al. (2020). Application prospect of hydrogen energy in integrated energy systems. Electric Power, 53(5), 135–142. [Google Scholar]
5. Xu, C. B., Zhao, Y. H., Wang, X. C., Ke, Y. M. (2022). Optimal configuration of hydrogen energy storage for wind and solar power stations considering electricity-hydrogen coupling under carbon neutrality vision. Electric Power Construction, 43(1), 10–18. [Google Scholar]
6. Jia, C. Z., Wang, L. M., Meng, E. M., Yang, D. R., Guo, D. J. et al. (2020). Optimal capacity configuration and day-ahead scheduling of wind-solar-hydrogen coupled power generation system. Electric Power, 53(10), 80–87. [Google Scholar]
7. Guo, M. J., Yan, Z., Zhou, Y., Zhang, P. C. (2020). Optimized operation design of integrated energy system with wind power hydrogen production. Electric Power, 53(1), 115–123+161. [Google Scholar]
8. Huang, D. W., Qi, D. Q., Yu, N., Cai, G. W. (2017). Capacity configuration method of hydrogen production system consuming abandoned wind power. Acta Energiae Solaris Sinica, 38(6), 1517–1525. [Google Scholar]
9. Scolaro, M., Kittner, N. (2022). Optimizing hybrid offshore wind farms for cost-competitive hydrogen production in germany. International Journal of Hydrogen Energy, 47(10), 6478–6493. [Google Scholar]
10. Leahy, P., McKeogh, E., Murphy, J., Cummins, V. (2021). Development of a viability assessment model for hydrogen production from dedicated offshore wind farms. International Journal of Hydrogen Energy, 46(48), 24620–24631. [Google Scholar]
11. Zhang, Y., Sun, H., Tan, J., Li, Z., Hou, W. et al. (2022). Capacity configuration optimization of multi-energy system integrating wind turbine/photovoltaic/hydrogen/battery. Energy, 252(7), 124046. [Google Scholar]
12. Calado, G., Castro, R. (2021). Hydrogen production from offshore wind parks: Current situation and future perspectives. Applied Sciences, 11(12), 5561. [Google Scholar]
13. Luo, Z., Wang, X., Wen, H., Pei, A. (2022). Hydrogen production from offshore wind power in South China. International Journal of Hydrogen Energy, 47(58), 24558–24568. [Google Scholar]
14. Jang, D., Kim, K., Kim, K. H., Kang, S. (2022). Techno-economic analysis and Monte Carlo simulation for green hydrogen production using offshore wind power plant. Energy Conversion and Management, 263(9), 115695. [Google Scholar]
15. Lucas, T. R., Ferreira, A. F., Pereira, R. S., Alves, M. (2022). Hydrogen production from the WindFloat Atlantic offshore wind farm: A techno-economic analysis. Applied Energy, 310(104), 118481. [Google Scholar]
16. Zhang, J. A., Qiu, S., Song, G. Y., Li, F., Liu, D. et al. (2020). Wind speed distribution description method considering time series fluctuationg. Acta Energiae Solaris Sinica, 41(8), 330–336. [Google Scholar]
17. Han, Z., Zhi, Z. Y., Jia, H., Lu, L., Wang, J. et al. (2011). Study on calculation methods of wind farm's abandoned energy. 2011 International Conference on Advanced Power System Automation and Protection, vol. 3, pp. 1996–1999. Beijing, China. [Google Scholar]
18. Hu, S., Guo, B., Ding, S., Yang, F., Dang, J. et al. (2022). A comprehensive review of alkaline water electrolysis mathematical modeling. Applied Energy, 327(61), 120099. [Google Scholar]
19. Agbossou, K., Kolhe, M., Hamelin, J., Bose, T. K. (2004). Performance of a stand-alone renewable energy system based on energy storage as hydrogen. IEEE Transactions on Energy Conversion, 19(3), 633–640. [Google Scholar]
20. Shafiee, M., Brennan, F., Espinosa, I. A. (2016). A parametric whole life cost model for offshore wind farms. The International Journal of Life Cycle Assessment, 21(7), 961–975. [Google Scholar]
21. Wang, S., Fan, Y., Jin, S., Takyi-Aninakwa, P., Fernandez, C. (2023). Improved anti-noise adaptive long short-term memory neural network modeling for the robust remaining useful life prediction of lithium-ion batteries. Reliability Engineering & System Safety, 230(2), 108920. [Google Scholar]
22. Wang, S., Takyi-Aninakwa, P., Jin, S., Yu, C., Fernandez, C. et al. (2022). An improved feedforward-long short-term memory modeling method for the whole-life-cycle state of charge prediction of lithium-ion batteries considering current-voltage-temperature variation. Energy, 254(5), 124224. [Google Scholar]
Cite This Article
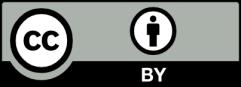