Open Access
ARTICLE
An Analysis of the Formation Mechanisms of Abrasive Particles and Their Effects on Cutting Efficiency
Research Center of Mould Precision Machining & Intelligent Manufacturing Application, Ningbo Polytechnic, Ningbo, 315800, China
* Corresponding Author: Wei Zhang. Email:
Fluid Dynamics & Materials Processing 2022, 18(4), 1153-1167. https://doi.org/10.32604/fdmp.2022.019719
Received 10 October 2021; Accepted 16 February 2022; Issue published 06 April 2022
Abstract
Magnetic induction-free abrasive wire sawing (MIFAWS) is a method that combines magnetic fields with traditional free abrasive wire sawing technologies. Magnetic abrasive particles (MAPs) are attracted on a magnetized wire, thus leading to an increase in their number into the cutting zone. The number of instantaneous-effective abrasive particles (IEAPs) adsorbed on the wire surface has a great influence on the cutting efficiency of the saw wire. In this study, a mathematic model of the movement of the MAP is presented, and the factors influencing the IEAPs number, including slurry-supply speed and slurry dynamic viscosity, are investigated both by means of simulation analysis and experiments. The results indicate that the number of IEAPs decreases with an increase in the slurry supply speed. The cutting efficiency increases gradually with the increase of slurry supply speed, but the growth rate of wire saw cutting efficiency slows down when the slurry supply speed exceeds a given threshold. The number of IEAPs adsorbed by saw wire increases with a decrease in the dynamic viscosity of the cutting fluid, while the cutting efficiency first increases and then decreases. The cutting efficiency attains its highest value when the dynamic viscosity of the cutting fluid is 0.0047 Pa⋅s. The experimental results agree with the simulation results, and provide some guidance for the practical application of the MIFAWS process.Keywords
Cite This Article
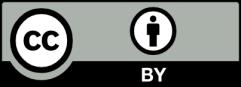