Open Access
ARTICLE
Analysis of the Performances and Optimization of Polyurethane Concrete with a Large Percentage of Fly Ash
1 Wuchang University of Technology, Wuhan, 430223, China
2 China Metallurgical Construction Engineering Group Co., Ltd., Chongqing, 400080, China
3 China Construction Fourth Engineering Division Corp., Ltd., Guangzhou, 510665, China
* Corresponding Author: Jiaquan Xue. Email:
(This article belongs to the Special Issue: Advanced Materials, Processing and Testing Technology)
Fluid Dynamics & Materials Processing 2023, 19(2), 437-450. https://doi.org/10.32604/fdmp.2022.020696
Received 07 December 2021; Accepted 06 May 2022; Issue published 29 August 2022
Abstract
The properties of polyurethane concrete containing a large amount of fly ash are investigated, and accordingly, a model is introduced to account for the influence of fly ash fineness, water ratio, and loss of ignition (LOI) on its mechanical performances. This research shows that, after optimization, the concrete has a compressive strength of 20.8 MPa, a flexural strength of 3.4 MPa, and a compressive modulus of elasticity of 19.2 GPa. The main factor influencing 28 and 90 d compressive strength is fly ash content, water-binder ratio, and early strength agent content.Keywords
The background of this study is that the damage to the bottom of the tunnel is a frequent and refractory disease in the tunnel. After the bottom of the tunnel is damaged, it is easy to cause mud and mud on the track, which will affect the regular operation of the train due to the subsidence of the foundation bed. Because the current situation is that the early-strength concrete at the bottom of the tunnel is required to reach the strength of 20 MPa required for train operation within 1–2 d. Additionally, the concrete material needs to bond well with its aggregates and surrounding materials in a wet environment. The use of ordinary cement early-strength repair materials cannot meet the engineering requirements [1]. Due to the complex construction process, high price, and elastic modulus mismatch, epoxy resin materials cannot meet the optimal use requirements in terms of economy and practicability. Because to find a material to use, we conducted the research in this paper to “ design” the chemical structure, specification, variety, etc., of the raw material.
In order to find new material, after many tests, we finally determined that polyurethane concrete is a kind of polymer concrete. This trial process was studied [2].
Generally, polymer concrete can be divided into three types: polymer impregnated concrete (PIC), polymer cement concrete (PCC), and polymer resin concrete (PC). Polymer impregnated concrete is to impregnate hardened ordinary concrete in an organic monomer. Then the monomers immersed in the pores of the concrete are polymerized by heating or radiation. This makes concrete and polymer become one. Polymer cement concrete is a concrete cementing material that uses polymer emulsion and cement [3]. The hydration reaction causes the polymer emulsion particles to wrap the cement hydrate to form a unified whole [4]. Polymer resin concrete is a polymer concrete that uses resin as cementing material. Some scholars have conducted experimental research on polyurethane resin concrete. It is believed that polyurethane resin concrete solidifies quickly, has high early strength, and is suitable for the rapid repair of roads. Some scholars have achieved good results by using polyurethane foam as a rapid repair material for airport road bases [5]. Some scholars have studied the road performance of polymer styrene-butadiene emulsion-modified concrete. The research results show that the cost performance of styrene-butadiene emulsion-modified concrete is higher than that of ordinary cement concrete. Some scholars have developed polymer-modified cement materials suitable for pavement repair. Some scholars have used polymer reinforced concrete in bridge deck paving and achieved good results. Polymer concrete can be mainly used to repair airport runways and highway surfaces partially. Its advantages are quick hardening after construction, good abrasion resistance and impact resistance, good impermeability and frost resistance, and strong adhesion. Generally speaking, its 24 h strength can reach 80% of the final strength. It is an excellent quick repair material. The disadvantages are considerable shrinkage during hardening, poor fire resistance, and high cost per unit volume.
Polyurethane concrete is often made of thermosetting liquid resin as the binder. This material comprises curing agents, filler, and sand and gravel aggregate. The fillers mainly include silica fume, barium sulfate powder, cement, and fly ash. Aggregate is the same as ordinary concrete but requires sufficient drying. The water content is less than 0.15%. Ordinary polyurethane concrete has poor workability, fast curing, and difficult molding control during construction. This article proposes water-containing unsaturated polyurethane concrete. The purpose is to reduce costs, increase workability, and enable the material to adapt to humid environments. The water-containing unsaturated polyurethane concrete’s mechanical properties and influencing factors are compared and analyzed through the proportioning, strength, immersion, and field sampling tests [6].
In this experiment, sand and gravel materials commonly used in ordinary concrete are used as aggregates, polymer materials are used as binders, and a small amount of cement and early-strength water-reducing agent are used as the basis for mutual matching. We choose the best ratio. The test raw materials are ordinary 425 cement and river sand (Modulus is 2.2, water content is 10%–12%, apparent density is 2.64 g·cm−3, bulk density is 1600 kg·m−3), stones (maximum particle size is 31.5 mm, apparent density is 2.64 g·cm−3, the bulk density is 1590 kg·m−3), early strength agent (MZS high-efficiency early strength agent and FDN naphthalene sulfonate water reducing agent), calcium chloride, unsaturated polyurethane, and curing agent (initiator Methyl ethyl ketone and accelerator cobalt naphthenate).
2.2 Various Polymer Concrete Strength Indexes
Commonly used cementing materials for polymer concrete include epoxy resin, unsaturated polyurethane, furan resin, urea-formaldehyde resin, polyurethane, and methyl methacrylate monomers. Compared with ordinary concrete, unsaturated polyurethane concrete has good durability and mechanical properties. Its compressive strength, flexural strength, and flexural strength are all higher than those of ordinary concrete. The compressive strength can be as high as 80–100 MPa, the tensile strength is about 10 MPa, and the bending strength is 10–30 MPa. The intensity of 1 d age can reach more than 50% of the intensity of 28 d. The intensity of 3 d age can reach more than 70% of 28 d intensity. This is conducive to rapid repair construction. It has good bonding strength to metal, wood, stone, and concrete. The comparison results of various polymer concrete strength indexes are shown in Table 1.
We conducted four sets of comparative experiments. The purpose is to deeply analyze the mechanical properties of unsaturated polyurethane concrete and understand its influencing factors. Test one is a comparative test of the strength of unsaturated polyurethane modified cement concrete under different dosages of initiators and accelerators. Test two is a comparative test of the strength of water-containing unsaturated polyurethane concrete at different temperatures. Experiment 3 is a comparative test of the strength of unsaturated polyurethane concrete under different powder additives. The fourth test compares the strength of various early-strength additive concrete and unsaturated polyurethane concrete. A strength test measures the mechanical strength of polyurethane concrete under various conditions. The test procedure is as follows: First, a sample of unsaturated polyurethane concrete is made. The diameter is 4 cm, and the height is 8 cm. When the 1–2 d strength index reaches 20 MPa, the concrete standard test block is prepared for the strength test.
2.4 Calculation Method of Concrete Crystal Length
The total length of the concrete uniaxial tensile fracture cracks on the mesoscale is set as
Therefore,
The area swept by the unit length
Static problem
3.1 The Strength Change Law of Early-Strength Concrete
Ordinary early-strength concrete is mixed with an early-strength agent to accelerate the early hardening of the concrete. We add dual fast cement to ordinary 425 Portland cement. The more the amount added, the higher the early strength, but it did not reach the ideal index. Later, various early strength agents were added to ordinary cement. The results show that only adding MZS high-efficiency early-strength agent, ordinary early-strength agent, and 30% double fast cement has a better effect, but it still does not meet the requirements. This shows that adding a single type of additive is challenging to achieve the desired effect. Based on this, this article tests the effects of multiple single additives and joint compound additions.
The test plan is shown in Table 2. The test piece is shown in Fig. 1. The test results are shown in Fig. 2. When ordinary cement is used alone, the 1 d compressive strength of concrete is 2.72 MPa, the 7 d strength is 16.98 MPa, and the 28 d strength is 20.93 MPa. The 1d compressive strength of ordinary cement mixed with dual fast cement is 5.47 MPa, the 7 d strength is 15.08 MPa, and the 28 d strength is 27.26 MPa. The 1 d compressive strength of ordinary cement mixed with MZS high-efficiency, early strength agent is 6.55 MPa, the 7 d strength is 18.84 MPa, and the 28 d strength is 22.79 MPa. The 1 d compressive strength of ordinary cement mixed with calcium acrylate is 2.57 MPa, and the 2 d compressive strength of 5.20 MPa. The 1 d strength of ordinary cement mixed with unsaturated polyurethane and urea-formaldehyde resin is 11.77 MPa, and the 2 d strength is 22.66 MPa. The 1 d compressive strength of ordinary cement mixed with unsaturated polyurethane is 20.6 MPa. At this time, the strength required by design can be achieved. The 1 d strength of ordinary cement mixed with unsaturated polyurethane and ZK3 additives reaches 24.5 MPa. It can be seen that the concrete mixed with unsaturated polyurethane obtains good indicators. Still, the lack of water during the production of the specimens leads to poor workability during actual operation [7].
Figure 1: Concrete specimen
Figure 2: Concrete strength of different test schemes
3.2 The Curing Law of Unsaturated Polyurethane Concrete
Unsaturated polyurethane is used as a cementing material for new early-strength concrete. Its curing time and regularity are significant for the formulation design and determining the scope of application of the new polymer concrete. This article first studied the curing characteristics of a single unsaturated polyurethane. The effect of different initiator and accelerator content on the curing law of unsaturated polyurethane under the exact content of unsaturated polyurethane was analyzed through comparative experiments (Table 3) [8]. The curing time of pure unsaturated polyurethane is closely related to the amount of curing agent. As the curing agent increases, the curing time decreases sharply, and the minimum amount of curing agent is 0.25%. The curing time of unsaturated polyurethane cement mortar was tested based on the study of pure unsaturated polyurethane cement mortar. The test plan is shown in Table 4, and the test result is shown in Fig. 3. The test results show that when the amount of sand, cement, and unsaturated polyurethane is the same, the initial setting time is shortened as the curing agent increases. This shows that the accelerator plays a significant role in controlling the initial setting time [9]. Cement plays a role in accelerating coagulation in the batching. The setting time is significantly prolonged without cement.
Figure 3: Curing time of unsaturated polyurethane cement mortar
3.3 The Influence of the Water Content of Polyurethane Concrete
Unsaturated polyurethane concrete is a kind of high-strength fast-setting concrete. Generally, it is not allowed to add water during the construction of unsaturated polyester concrete. Under no water, the 1 d strength of unsaturated polyurethane concrete can reach 48.8 MPa. However, it has poor workability and fast curing, making it difficult to use in construction. Another disadvantage is the higher price. This article introduces water and cement into unsaturated polyurethane concrete. The water can increase the workability of this type of concrete, but the water reacts with the cement to form a binder and release part of the heat [10]. This helps to improve the early strength of this type of concrete. Therefore, selecting a suitable water diversion agent to fuse water and unsaturated polyurethane is necessary. This paper analyzes a comparative test of unsaturated polyurethane mixed with urea-formaldehyde resin, acrylic acid, and calcium acrylate. The results show that the urea-formaldehyde resin added should not exceed 20% of the unsaturated polyurethane. Otherwise, the curing time will be prolonged, and the early strength will be below. According to the curing time of different mortars, it can be concluded that acrylic acid plus cement has the effect of accelerating coagulation and exothermic phenomenon. However, when calcium acrylate is used as an additive, there is no exothermic phenomenon, and the strength after hardening is higher than that of acrylic modified unsaturated polyurethane concrete. Therefore, this article uses calcium acrylate modified unsaturated polyurethane concrete.
According to on-site engineering requirements, the 1 d strength of the water-unsaturated polyurethane concrete must reach 20 MPa. To determine the feasibility of the study on the strength change law of unsaturated polyurethane concrete with different temperatures and water content. The test scheme and results are shown in Table 5 and Fig. 4. The test results show that the unsaturated polyurethane concrete can ensure the strength of more than 20 MPa at the age of 1 d by using a suitable amount of water under different temperature conditions. To ensure that the 1 d strength is not less than 20 MPa, the different water content must be used according to the construction temperature (Fig. 5). Do not mix with water when the temperature exceeds 10°C [11]. When the temperature is 10°C–20°C, 15%–20% of the amount of water used for unsaturated polyurethane can be added. When the temperature is above 20°C, 20%–30% of unsaturated polyurethane water can be added.
Figure 4: Feasibility test results of water-containing unsaturated polyurethane concrete
Figure 5: The ratio of water to unsaturated polyurethane at different temperatures
This article preliminarily determines a basic ratio. The mass ratio of unsaturated polyurethane, cement, filler, coarse material (sand + stone), curing agent (initiator + accelerator) is 250:150:200:(800 + 1100):(7.5 + 3.75). On this basis, change the amount of water and measure the 1d strength and elastic modulus of the material to determine the optimal amount of water. The test scheme and results are shown in Table 6 and Fig. 6. There is an optimal water content for water-containing unsaturated polyurethane concrete. When we use it, we should choose according to the actual situation [12].
Figure 6: Concrete strength parameters under different water content conditions
3.4 The Influence of Unsaturated Polyurethane Concrete Powder Additives
In most cases, it is necessary to add suitable fillers to improve the quality of the concrete, increase the density, and reduce the cost. Filler properties must meet the following requirements: inertness, low metal content, and not affect the curing speed of unsaturated polyurethane. The particle diameter is 1–3 mm and is easily dispersed in unsaturated polyurethane. The oil absorption or the absorption of unsaturated polyurethane is negligible. The density is generally lower than 2.5 g·cm−3. The price is low and easy to get, and the quality is stable. The powder additives used in this test are quartz powder, barium sulfate powder, fly ash, and ZK3. The comparative test results are shown in Table 7 [13]. The test results show that quartz sand is better than ZK3, and ZK3 is better than barium sulfate powder and barium sulfate plus fly ash. Fly ash and cement play the same role without adding water. Under the condition of adding water, cement plays a role in accelerating coagulation. The greater the amount of cement, the faster the concrete will cure. We choose ZK3, which we developed as an additive in engineering applications.
4.1 The Influence of Unsaturated Resin on the Performance of Resin Concrete
As the binder, unsaturated polyester resin is also the main liquid component, which significantly influences the workability and mechanical strength of the resin concrete. At the same time, the unsaturated polymer phase is expensive. By reducing the price of the resin and the amount of resin, the cost of resin concrete can be significantly reduced. Therefore, exploring the effect of resin on the performance of resin concrete is of positive significance for solving the production process of resin coagulation, reducing costs, and expanding the application field of resin coagulation. When the amount of resin A is 16%, the compressive strength of resin concrete is 141.38 MPa, and the flexural strength is 22.04 MPa. According to the European Union EN1433 standard, it can be known that the compressive strength of the resin concrete material used in the qualified resin concrete drainage ditch should be greater than 94 MPa, and the flexural strength should be greater than 22 MPa. This shows that resin A meets the requirements of the drainage ditch for the mechanical properties of resin concrete. When resin B is 16%, the compressive strength is 77.75 MPa, and the flexural strength is 18.98 MPa. This does not meet the requirements of the EU EN1443 on the mechanical properties of resin concrete drainage ditch materials. After adding 0.3% KH570, the compressive strength of the resin concrete is 95.20 MPa, and the flexural strength is 23.13 MPa. This meets the European Union EN1443 standard.
4.2 The Influence of Unsaturated Resin on the Mechanics of Resin Concrete
Since the unsaturated resin is synthesized from the alcoholysis of PET bottle flakes, the synthesis cost is lower than that of the resin DSM-P68. At the same time, it is more in line with the theme of the era of resource recycling and green environmental protection. However, due to the poor bonding effect of unsaturated resin on inorganic products, the high resin viscosity still affects its scope of use. In this section, the influence of resin on the compressive strength and flexural strength of R-PET resin concrete is studied.
The compressive strength of resin concrete increases with the increase in the amount of resin. When the amount of resin increases from 20% to 22%, the increase in compressive strength is minimal. This is because the resin as the binding material of the resin concrete mainly plays the role of binding aggregate fillers and other components. With the increase in the amount of resin, the resin can completely infiltrate the surface of the aggregate filler, and the increase in the amount of resin will no longer improve these properties. The compressive strength of resin concrete no longer increases. The flexural strength increases first and then decreases as the number of resin increases. When the amount of resin is 20%, the maximum flexural strength is 24.5 MPa, which increases 16.78% when the amount of resin is 14%. The increase in the amount of resin reduces the pores in the resin concrete spline and enhances the resin’s infiltration effect on inorganic components. This improves the flexural strength of resin concrete. However, if the amount of resin is too large, the resin and the aggregate filler will be layered, and the stress will be uneven during the flexural test, which will easily break and reduce the flexural strength.
4.3 The Influence of Filler Content on the Performance of Resin Concrete
Filler is an essential component in unsaturated polyester resin concrete. It can reduce the pores of resin concrete and reduce the roughness of resin concrete drainage ditches. At the same time, excessive fillers will also affect the specific properties of resin concrete. Therefore, the type and amount of fillers need to be selected reasonably. In this experiment, the commonly used 375 mesh calcium carbonate was used as the filler, and the influence of the amount of calcium carbonate on the resin concrete was discussed.
As the amount of filler resin increases, the compressive strength of resin concrete rises and decreases, and the increase in compressive strength tends to be gentle. As the number of filler increases, the pores in the resin concrete are filled. The defects of resin concrete splines are reduced, and the compressive strength increases. When the filler continues to increase, the workability of the resin concrete becomes worse. Porosity is easily formed during the shaking of the sample, and the compressive strength is reduced. As the amount of filler increases, the flexural strength of resin concrete continues to rise. This may be because the components composed of resin, filler, and fine aggregate play a decisive role in the flexural strength of resin concrete. As the proportion of filler increases, the proportion of components in the resin concrete increases. The distance between significant aggregates increases, forming a “sea-island” structure with this component. The more the filler, the more perfect the structure, so the flexural strength is continuously improved.
5 Analysis of Engineering Application Results
According to the modified concrete strength test results, we use urea-formaldehyde resin and unsaturated polyurethane as the cementing material to prepare unsaturated polyurethane cement concrete. The concrete at the bottom of the tunnel was damaged. The reason is that the substrate is not uniformly stressed, and local stress is concentrated, resulting in fracture and failure. The rock layer is weathered, the strength is reduced, and the bearing capacity cannot meet the driving requirements, which causes damage to the paving concrete. The weathered rock layer forms mud from the cracks of the damaged concrete and flows into the roadbed to form mud and mud, and the foundation bed sinks. This will affect the safety of train operations. The design formula is 200 g of unsaturated polyurethane + 50 g of urea-formaldehyde + 400 g of cement + 700 g of sand + 1100 g of stone + 50 g of water. The detected 1 d strength index is only 4.1–4.3 MPa. This did not meet the ideal requirements. It can be seen that in the practice of new materials, many technical parameters have to be re-determined. In this way, the early strength of the material meets the design requirements [14].
The test plan is shown in Table 8, and the test results are shown in Fig. 7. The test results show that the conditions of Scheme 4 are relatively excellent. The 1 d compressive strength can reach 20.25 MPa. The 2 d compressive strength is 28.96 MPa. The amount of the primary material, unsaturated polyurethane, is reduced by 60% compared with the original plan, significantly reducing the material cost.
Figure 7: Test results
Moreover, this scheme can add water to make the unsaturated polyurethane concrete have good workability and easy construction. This site’s primary on-site construction ratio is as follows: cement, sand, stone, ZK3, water, unsaturated polyurethane, and the mass ratio of initiator to the accelerator is 1.000:5.700:7.300:1.300:0.080:2.000:0.050:0.025. The on-site construction time is November, and the outdoor temperature during construction is 14°C–16°C. The on-site construction materials are mixed with a concrete mixer. The mixing time is slightly longer than ordinary concrete by 2–3 min [15]. The amount of water added is automatically controlled according to the design. The mixed unsaturated polyurethane concrete mortar is transported to the paving site in time and poured into the flat roadbed under the track. After leveling the unsaturated polyurethane concrete mortar, it is vibrated and compacted.
Random samples were taken from the mixed unsaturated polyurethane concrete mortar for strength testing during the construction. The 1 d compressive strength is 22.70 MPa. The 28 d strength is 31.72 MPa. Meet the requirements of on-site construction. The unsaturated polyurethane concrete mortar prepared with this formula has good workability, and the initial setting time can be controlled within 25–35 min. After the initial setting, the sample was put into water for an immersion test, and it was found that the sample did not soften and disintegrate. No softening or disintegration was found in the sample after soaking for one month. The experimental research has met the expected requirements.
(1) The value of water content plays a decisive role in water-containing unsaturated polyurethane concrete performance. Using the appropriate amount of water at different temperatures can improve workability and reduce engineering costs. (2) Adding fillers can significantly improve the properties of water-containing unsaturated polyurethane concrete. The fine material used can increase the compactness of the aggregate and improve the workability of the concrete. It improves the strength of water-containing unsaturated polyurethane concrete. (3) Increase the strength of the water-containing unsaturated polyurethane concrete by appropriately increasing the amount of curing agent. As the amount of curing agent increases, the curing time decreases sharply. It is necessary to pay attention to the strict weighing of the curing agent. Minor errors will also bring about more significant changes in the curing speed and mechanical properties. (4) The recommended primary ratio at a temperature of 15°C: the mass ratio of cement, sand, stone, ZK3, water, unsaturated polyurethane, initiator, and accelerator is 1.000:5.700:7.300:1.300:0.080:2.000:0.050:0.025. After our research, it is found that the material’s performance can be effectively improved under the conditions. In the future, we will continue to research and find more and better suitable materials through experiments to serve our world better and make the world a better place.
Funding Statement: This work was financially supported by the funds: (1) The Second Batch of Industry-University Cooperative Education Projects in 2021(202102113047); (2) Science and Technology Project of Hubei Construction Department [2019 (672)].
Conflicts of Interest: The authors declare that they have no conflicts of interest to report regarding the present study.
References
1. Cellat, K., Tezcan, F., Kardaş, G., Paksoy, H. (2020). Comprehensive investigation of butyl stearate as a multifunctional smart concrete additive for energy-efficient buildings. International Journal of Energy Research, 43(13), 7146–7158. [Google Scholar]
2. Venkatesh, C., Ruben, N., Chand, M. S. R. (2020). Red mud as an additive in concrete: Comprehensive characterization. Journal of the Korean Ceramic Society, 57(3), 281–289. DOI 10.1007/s43207-020-00030-3. [Google Scholar] [CrossRef]
3. Ahmed, Z. Y., Bos, F. P., van Brunschot, M. C. A. J., Salet, T. A. (2020). On-demand additive manufacturing of functionally graded concrete. Virtual and Physical Prototyping, 15(2), 194–210. DOI 10.1080/17452759.2019.1709009. [Google Scholar] [CrossRef]
4. Zamanian, S., Hur, J., Shafieezadeh, A. (2021). Significant variables for leakage and collapse of buried concrete sewer pipes: A global sensitivity analysis via Bayesian additive regression trees and Sobol’indices. Structure and Infrastructure Engineering, 17(5), 676–688. DOI 10.1080/15732479.2020.1762674. [Google Scholar] [CrossRef]
5. Ashrafi, N., Duarte, J. P., Nazarian, S., Meisel, N. A. (2020). Evaluating the relationship between deposition and layer quality in large-scale additive manufacturing of concrete. Virtual and Physical Prototyping, 14(2), 135–140. DOI 10.1080/17452759.2018.1532800. [Google Scholar] [CrossRef]
6. Azad, A., Mousavi, S. F., Karami, H., Farzin, S. (2020). Application of talc as an eco-friendly additive to improve the structural behavior of porous concrete. Iranian Journal of Science and Technology, Transactions of Civil Engineering, 43(1), 443–453. DOI 10.1007/s40996-018-0177-1. [Google Scholar] [CrossRef]
7. Ismael, S. A. D. M., Ismael, M. Q. (2020). Moisture susceptibility of asphalt concrete pavement modified by nanoclay additive. Civil Engineering Journal, 5(12), 2535–2553. DOI 10.28991/cej-2019-03091431. [Google Scholar] [CrossRef]
8. Adman, A. (2020). Pengaruh penambahan cangkang kemiri dan sikacim concrete additive terhadap kuat tekan beton normal. Jurnal Teknik Sipil, 6(2), 38–45. [Google Scholar]
9. Ershov, V. A., Karlina, A. I., Karlina, Y. I. (2021). Process control system for producing a silica-based modifying additive. Metallurgist, 65(3), 446–453. DOI 10.1007/s11015-021-01175-0. [Google Scholar] [CrossRef]
10. Kroviakov, S., Zavoloka, M., Dudnik, L., Kryzhanovskyi, V. (2020). Comparison of strength and durability of concretes made with sulfate-resistant portland cement and portland cement with pozzolana additive. Electronic Journal of the Faculty of Civil Engineering Osijek-e-GFOS, 10(19), 81–86. [Google Scholar]
11. Tay, Y. W. D., Ting, G. H. A., Qian, Y., Panda, B., He, L. et al. (2020). Time gap effect on bond strength of 3D-printed concrete. Virtual and Physical Prototyping, 14(1), 104–113. DOI 10.1080/17452759.2018.1500420. [Google Scholar] [CrossRef]
12. Rabie, G. M., Abd El-Halim, H., Rozaik, E. H. (2020). Influence of using dry and wet wastewater sludge in concrete mix on its physical and mechanical properties. Ain Shams Engineering Journal, 10(4), 705–712. DOI 10.1016/j.asej.2019.07.008. [Google Scholar] [CrossRef]
13. Mehrani, S. A., Bhatti, I. A., Bhatti, N. B., Jhatial, A. A., Lohar, M. A. (2020). Utilization of rubber powder of waste tyres in foam concrete. Journal of Applied Engineering Sciences, 9(1), 87–90. DOI 10.2478/jaes-2019-0011. [Google Scholar] [CrossRef]
14. Bagio, T. H. (2020). Cement additive use reduction factors to improving the quality concrete bioconc. IJTI International Journal of Transportation and Infrastructure, 2(2), 77–84. [Google Scholar]
15. Lowke, D. N., Herrmann, E. (2020). Reinforcement strategies for 3D-concrete-printing. Civil Engineering Design, 2(4), 131–139. DOI 10.1002/cend.202000022. [Google Scholar] [CrossRef]
Cite This Article
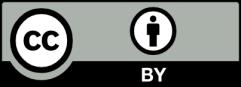