Open Access
PROCEEDINGS
Numerical Study on the Thermal Management of Lithium-Ion Battery Pack Based on Heat Pipes and Phase Change Material
1 Lanzhou Jiaotong University, Lanzhou, 730070, China
2 Qinghai Minzu University, Xining, 810007, China
3 Tianjin University, Tianjin, 300350, China
* Corresponding Author: Kewei Song. Email:
The International Conference on Computational & Experimental Engineering and Sciences 2023, 27(4), 1-3. https://doi.org/10.32604/icces.2023.08905
Abstract
As the fossil energy is increasingly exhausted and air pollution becomes more and more serious, blade electric vehicles equipped with rechargeable lithium-ion battery turns into the major developing direction of new energy automobile [1-3]. Lithium-ion batteries have the advantages of high energy density, light weight, and no pollution, and thereby are widely used in electric vehicles [4,5]. However, the working performance and service life of lithium-ion batteries are greatly affected by temperature [6]. Excessive high and low temperature will reduce the charge and discharge capacity of lithium-ion batteries, shorten their service life, and even lead to safety accidents [7]. Therefore, in order to ensure that the lithium-ion batteries can work safely and efficiently within a suitable temperature range, the research and design of battery thermal management systems are of great significance. The heat pipe (HP) has the advantages of high heat transfer efficiency and flexible arrangement. The phase change material (PCM) has the advantages of simple structure, low cost, and strong temperature control ability. Therefore, the HP auxiliary PCM is used to study the hybrid battery thermal management system (BTMS) [8,9].In this paper, numerical simulation is used to study the influence of the hybrid BTMS on the heat dissipation performance of 18650 cylindrical batteries with 4*4 arrangement.
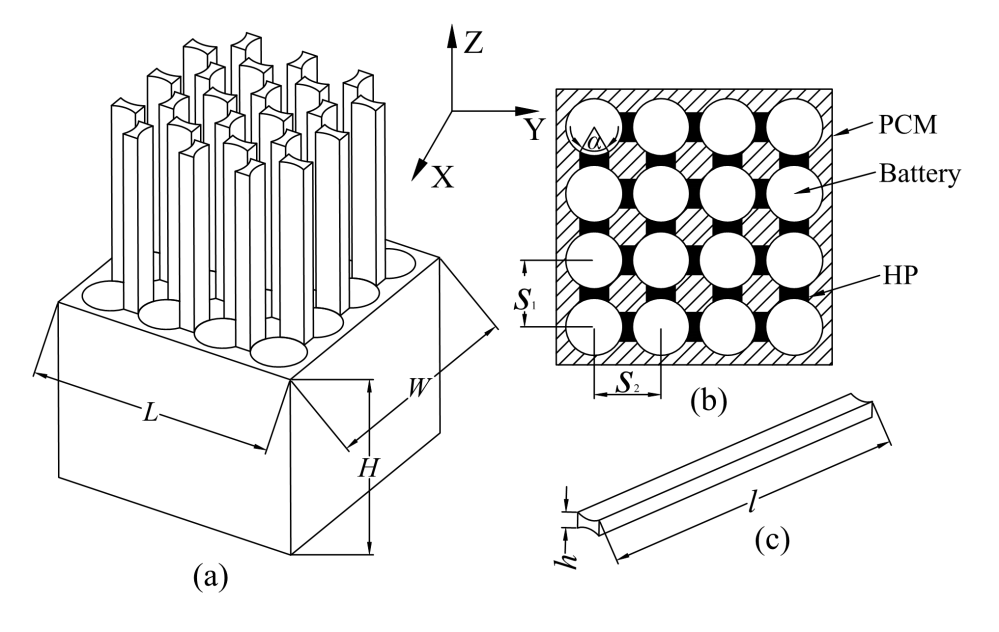
Figure 1: Schematic view of the battery pack. (a) Schematic diagram of the all model, (b) Top view, (c) Schematic diagram of the HP
As shown in Fig.1(a), the battery pack consists of 18650 cylindrical batteries, HP, and PCM. The HPs are placed vertically between two adjacent batteries and contact well with the batteries. The other space in the battery pack is filled with PCM, that is, the battery and HP are completely wrapped by the PCM. The whole size of the battery pack is L*W*H. The spacings between batteries are S1= mm and S2= mm. The fitting angle between HP and battery is α, as shown in Fig.1 (b).
It can be seen from Fig.2 that the maximum temperature of the battery pack combined with both PCM and HP decreases significantly compared with that of the battery pack with only PCM. For different discharge rates of 2C, 3C and 4C, the maximum temperatures of the battery pack with both PCM and HP are 35.44°C, 43.53°C and 49.33°C, which are 33.55%, 35.73% and 52.5% lower than that of the model with only PCM.
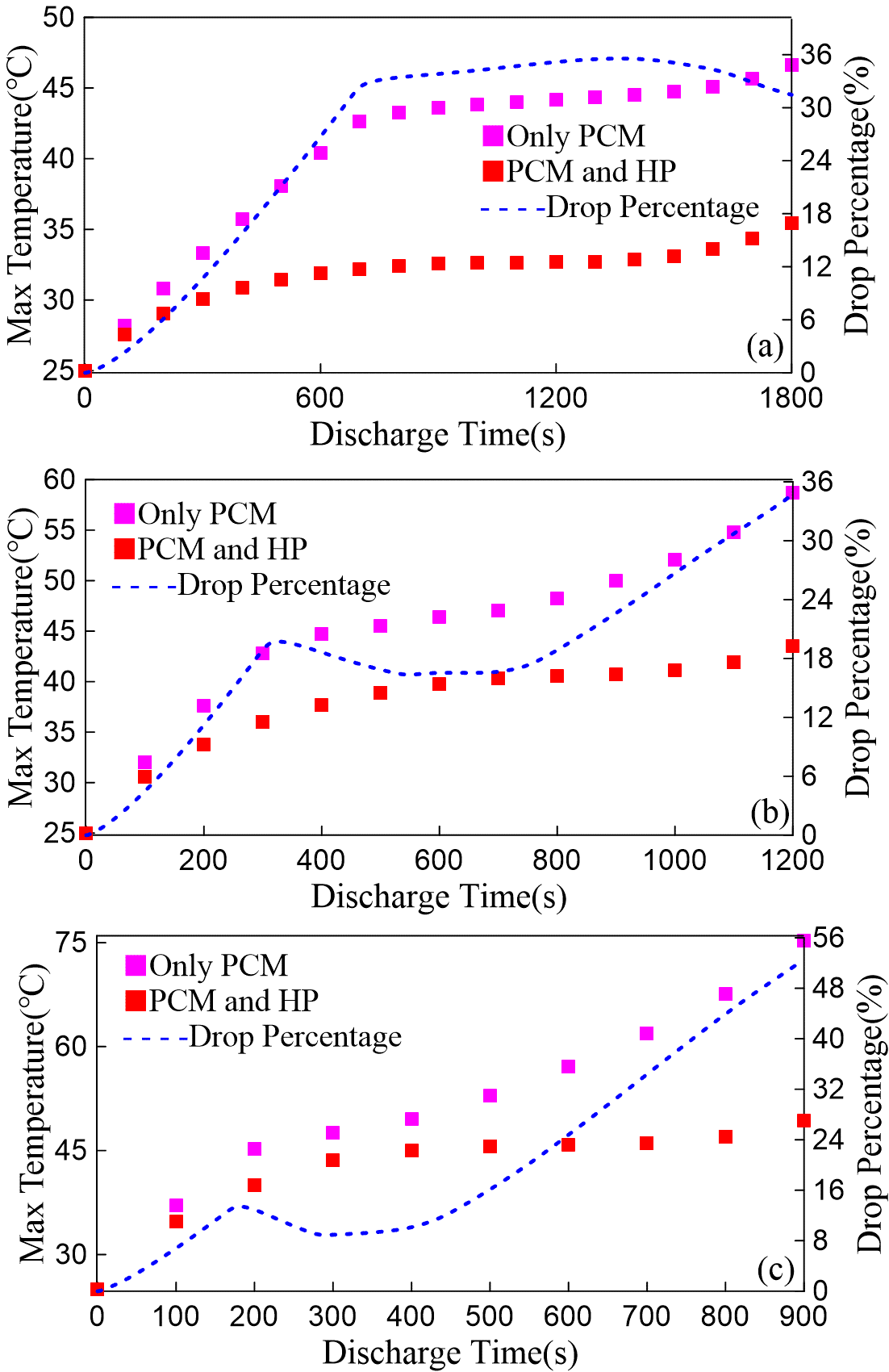
Figure 2: Battery maximum temperature of different BTMS at different discharge rates (a) 2C, (b) 3C, (C) 4C
The major conclusions are as follows:
(1) For the model with only PCM, the temperature of the battery first increase sharply before the PCM starts melting under the temperature of melting point due to the increase of temperature of PCM. During the melting process, the increase of temperature of the battery becomes smooth. At the end of the discharge process, the maximum temperatures of the battery pack with discharge rates of 2C, 3C and 4C are 46.66°C, 58.66°C and 75.23°C, respectively.
(2) For the model combined with PCM and HP, the PCM does not melt completely during the discharge process. The temperature of the battery is significantly smaller than the model with only PCM. At the end of discharge, the maximum temperatures are 35.44°C, 43.53°C, and 49.33°C for 2C, 3C and 4C, respectively, which are 33.53%, 35.73%, and 52.5% lower than that of the model with only PCM.
(3) With the increase of heat transfer coefficient of HP, the phase change time of the PCM continuous increases, while the battery pack temperature and the liquid fraction of the PCM decreases gradually. When h changes from 15 to 60, the maximum temperature decreases by 19.5%, 17.4% and 22.1% for 2C, 3C and 4C, respectively.
Nomenclature
h heat transfer coefficient (W/m2 ·K)
Subscripts
PCM phase change material
HP heat pipe
BTMS battery thermal management system
Keywords
Cite This Article
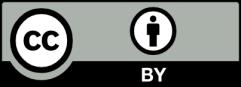