Open Access
REVIEW
Advances in Research of Molded Pulp for Food Packaging
1
Jiangsu Provincial Key Laboratory of Food Advanced Manufacturing Equipment Technology, Wuxi, 214122, China
2
School of Food Science and Technology, Jiangnan University, Wuxi, 214122, China
* Corresponding Author: Liqiang Wang. Email:
(This article belongs to the Special Issue: Food Packaging Materials Based on Renewable Resources)
Journal of Renewable Materials 2023, 11(11), 3831-3846. https://doi.org/10.32604/jrm.2023.028251
Received 07 December 2022; Accepted 13 February 2023; Issue published 31 October 2023
Abstract
The molded pulp, a product of three-dimensional papermaking technology, is environmentally friendly and has a low environmental impact due to its ability to decompose quickly in the natural environment after disposal. The application of molded pulp for food packaging can replace or reduce the use of plastic food packaging. Researchers extract fibers from plants for the production of safe and hygienic molded pulp for food packaging, and they also study and enhance the qualities of molded pulp to broaden its use in the food industry. This paper reviews the sources and varieties of plant fiber used in molded pulp for food packaging, as well as research on the improvement and optimization of the performance of molded pulp products. Additionally, issues with molded pulp’s actual use for food packaging are reviewed, along with the potential for future research. This work can serve as a reference for molded pulp applications and research in the food industry in the future.Graphical Abstract
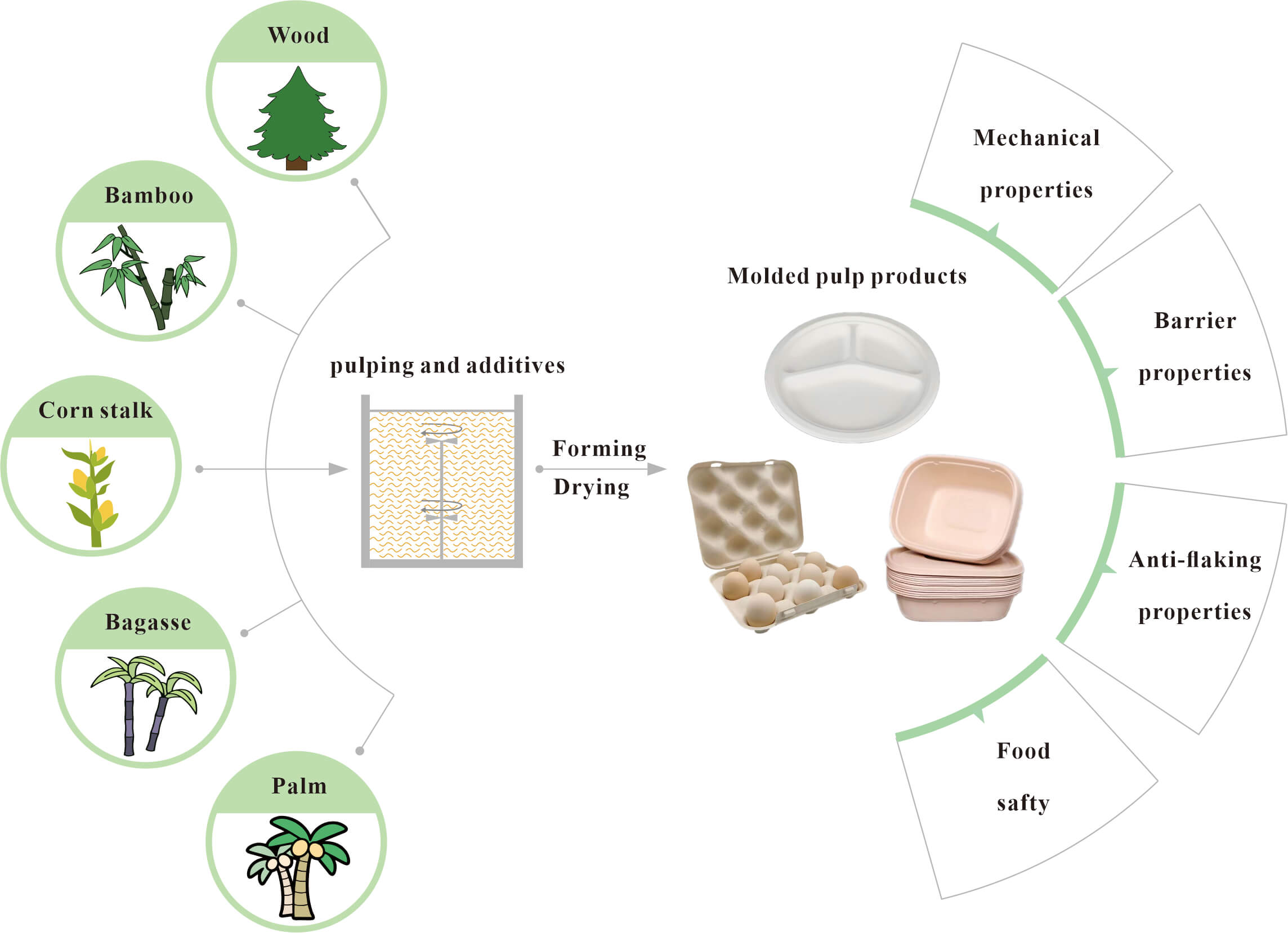
Keywords
The mass production and use of petroleum-based plastic packaging have greatly improved the standard of living of humans, especially in the field of food packaging. However, due to poor management and difficult decomposition, a lot of food packaging waste is produced globally every day [1], resulting in hundreds of millions of tons of white waste. This has seriously and irreparably harmed the human ecological environment, particularly the ocean and freshwater resources of the planet. It is crucial to use naturally degradable biomaterials instead of plastic to package food, and molded pulp, derived from plant fibers, is the best option. The research notes that molded pulp products, which make up about 50% of food packaging (Fig. 1) and are virtually entirely recyclable and biodegradable, are one of the most promising sustainable food packaging materials. This helps to lessen the environmental impact of wastage [2].
Figure 1: Molded pulp packaging segment-wise market share [2]
Molded pulp products first appeared in the 19th century, and in recent years, consumer adoption of this type of packaging has been growing [3]. Molded pulp is a three-dimensional paper making technology that is molded into various shapes of paper products through processes such as mold forming and hot press drying according to different applications [4]. The four varieties of molded pulp products are defined by the International Molded Fiber Association (IMFA) as follows [5]:
※Molded Fiber Products–“Thick Wall”
It is produced using just one molded and has a product wall thickness of about 3/16 to 3/8 inches (5 to 10 mm). One side is rough, whereas one surface is mostly smooth. They are primarily used for support packaging of heavier, non-fragile items (vehicle parts, furniture, motors, etc.), as well as plant, flower and nursery pots and containers.
※Molded Fiber Products–“Transfer Molded”
They are manufactured using one forming mold and one transfer mold with a product wall thickness of about 1/8 to 3/16 inches (3 to 5 mm). The surfaces are quite smooth on one side. The most common use is for egg cartons and trays. New designs are used for many types of electronic product packaging such as cell phones, DVD players, etc. Also, they are used for hospital disposables, electrical appliances, office equipment, tableware and fruit and drink trays.
※Molded Fiber Products–“Thermoformed” (Sometimes called “Thin-Wall”)
They are manufactured using multiple heated molds with a product wall thickness of about 3/32 to 5/32 inches (2 to 4 mm). Forms are well-detailed, with smooth surfaces and few draft angles. Products are dried in the mold, eliminating the need for oven curing. The walls are a little bit denser as a result of the hot mold pressing procedure. Products made from type 3 thermoformed fiber closely resemble thermoformed plastic.
※Molded Fiber Products–“Processed”
This type covers products made of molded fiber that need further processing or specific handing beyond simple molding and curing.
Primary fibers and recycled fibers from waste paper are utilized as raw materials in molded pulp products, and the type of raw materials used has a significant impact on products’ quality and cost. Recycled fibers are frequently used as the starting materials for type I and type II molded pulp. However, as the strength of the fibers decreases and the number of tiny fibers increases, it is usually necessary to treat them first to get rid of heavy metals, dirt, inks, dyes and coatings [6]. For packaging that comes into direct contact with food, considering the safety and hygiene requirements of food packaging, molded pulp for food packaging must use non-polluting, non-toxic fiber raw materials. Therefore, molded pulp products for food packaging often use primary plant fiber as the main raw material, while taking into account lint free and flaking, and have a certain degree of stiffness, mechanical strength and hydrophobic and oil-proof properties. Fig. 2 shows a schematic diagram of the vacuum thermoforming process of molded pulp for food packaging.
Figure 2: Vacuum thermoforming process of molded pulp for food packaging
2 Source of Fiber for Molded Pulp
Wood fiber, bamboo fiber, bagasse fiber, crop straw fiber, and other primary fibers from natural plants can be utilized as a fiber source for molded pulp, which is used to manufacture molded pulp for food packaging. These fibers are renewable and biodegradable. Wood, which comes from a variety of sources, is the most commonly used raw material for molded pulp fiber. The strength and properties of the fiber can meet the needs of most molded pulp products. Bamboo is a very promising non-wood raw material. It is well suited for use as a fiber material for molded pulp for food packaging due to its fast growth, low resource cost, and its chemical composition and fiber properties are comparable to wood [7]. As a rich source of cellulose, the basic properties of bagasse are suitable for the manufacture of molded pulp products. However, because the properties of molded pulp products obtained when used alone are average, an attempt can be made to mix it with different cellulose sources to obtain synergistic enhancement and reduce the cost of molded pulp raw materials while making better use of bagasse fiber [8]. Most cellulose-rich plants can be used as a source of fiber for food molded pulp, but due to the difficulties of fiber pulping, low yield, and unstable sources, it is usually not possible to produce molded pulp products on a large industrial scale. Table 1 provides a summary of the primary places of origin and properties of various fibers. The characteristics and properties of each fiber are described in detail in the following article.
The most important pulp and paper raw material is wood fiber, which is divided into coniferous wood and board leaf wood based on its main growth and distribution areas. Coniferous woods with long coniferous wood fibers include pinus massoniana, larch, red pine and spruce. The tissue structure of coniferous wood is tight, with the heterolytic cell. Broadleaf wood includes birch, poplar, linden and eucalyptus, etc. Broadleaf wood fiber is shorter than coniferous wood fiber. Cellulose is produced by the chemical or mechanical removal of the wood’s non-cellulose component, which is usually around 60% [18]. As wood fibers contain more lignin, the color is often darker, and bleaching is often done before use for aesthetic reasons [10]. Fiserova et al. [19] investigated the properties of bleached coniferous and broadleaf kraft pulp. In laboratory pulping, bleached coniferous kraft pulp took longer to achieve the same drainage resistance as broadleaf kraft pulp. Coniferous kraft pulp had higher fiber strength and length than broadleaf kraft pulp, and broadleaf kraft pulp had higher fiber bonding capacity than bleached broadleaf kraft. The water absorption and bulk softness of the pulp are higher than that of the coniferous kraft pulp. The strength and quality of the paper product are affected by the wood’s modulus of elasticity, microfiber angle, fiber length and coarseness [20]. In the study of the chemical makeup and fiber characteristics of various broadleaf wood species, Ihnat et al. [9] discovered that common hornbeam, European ash, European beech and birch had higher polysaccharide content in wood, which was advantageous for pulping, in addition to having longer fiber and higher quality of pulping.
In the context of the global plastic ban and restrictions on their use, bamboo fiber, a unique resource of China, offers significant advantages when utilized as molded pulp for food packaging. Bamboo has lengthy fibers. It is a great raw material for the pulp and paper industry since cells typically range in length from 1 to 4 mm, have a diameter of 0.01 to 0.03 mm [21], and have a high aspect ratio. The pulp production varied between 35.7%–51.7% depending on the species and age of the bamboo [11]. Bamboo contains 20% to 25% lignin, which is a natural binder and filler. Wang et al. [22] developed bamboo residual lignin-based molded pulp products and, by carefully regulating the degree of delignification, produced lunchbox-shaped molded pulp products with long-lasting wet support strength. High-strength molded pulp can be created by removing the lignin from bamboo while keeping the hemicellulose and holocellulose [23]. The pulp production, mechanical and optical properties of various bamboo species influence how well-suited they are for creating pulp and paper. After bleaching, Neosinocalamus affinis bamboo from the Sichuan Province of China produced a pulp with great brightness but poor tensile and tear indices [24]. The average length of bleached bamboo pulp fiber was 1.68 mm, which is between broadleaf and coniferous wood pulp and suitable as a raw material for pulp and paper fibers. Tripathi et al. [25] focused on the physical properties, chemical composition, pulping properties, fiber morphology and strength characteristics of bamboo chips in their study the pulping and paper making properties of the bamboo species “Melocanna”. Bamboo has a quick maturity cycle; however, its pulping and mechanical characteristics vary depending on when it is harvested. Chang et al. [26] investigated how well bamboo aged 0.2, 1.2 and 3 years produced pulp and paper. Although the mature 3-year-old bamboo had a high pulp output (55%), over half of it was trash. The lignin percentage rose with increasing age. In contrast, after treatment, bamboo stems that were roughly 1 year old showed improved brightness and strength and were more suited for pulp and paper production. Suhaimi et al. [11] pulped bamboo that was 1, 3 and 5 years old and discovered, in a similar manner, that bamboo with an age of 1 year had the maximum pulp output and was appropriate as a raw material for molded pulp products. Cao et al. [27] investigated the fiber morphology of green bamboo grown in southeastern China and prepared green bamboo pulp using pre-hydrolysis and sulfate pulping technique. When compared to the cortex and stalk, the stem nodes have shorter fibers and finer fibers, which are unsuitable for pulping and papermaking. By removing the stem nodes before cooking, the pulping quality of green bamboo can be improved.
Sugar cane is a temperate and tropical crop that originated in Asia. Brazil is the world’s largest producer of sugarcane, and sugar cane agriculture generates a large amount of bagasse waste, which contains 40% to 50% cellulose, 20% to 30% hemicellulose, and 18% to 25% of lignin and has a wide range of applications in the paper industry [28]. Bagasse fibers are flaky in small fragments [29], with narrow ends, a high flexibility coefficient, and good adhesion between fibers, making it an ideal raw material for papermaking. Liu et al. [12] created meal box-shaped molded pulps from bagasse-based pulp that are lighter in color and more appealing to consumers. However, because the length and width ratio of bagasse pulp is small, and the fibers contain more short fibers, the mechanical strength of bagasse pulp is not exceptional when it is used to prepare molded pulp alone. When bagasse fibers are combined with other plant fibers, a paper material with good properties is produced [30]. Wang et al. [22] developed high-quality molded pulp with food safety and excellent mechanical strength using sugarcane bagasse fibers, as well as lunchbox-shaped molded pulp by combining a certain percentage of long bamboo fibers with sugarcane fibers. Short bagasse fibers were physically interwoven with long bamboo fibers to form a tight network of interaction, enhancing the mechanical properties of the molded pulp. Because of the many fine particles in bagasse pulp, the production process of molded pulp with bagasse fiber as raw material is prone to causing deposition, blocking pipes, corrosion damage to equipment, increasing the number of cleanings, and thereby increasing the cost and lowing product quality [13]. Furthermore, bagasse molded pulp products lose a significant amount of tensile strength and related properties during the recycling process, limiting their recovery potential [31].
Compared to wood, crop straw has received less attention from researchers. China, as a large agricultural country, produces a large amount of various crop straws each year due to agricultural crops, and the dried crop straws contain 30%–36% cellulose and 19%–32% hemicellulose [32], which is a good fiber source for molded pulp. Crop straw as a raw material for the preparation of molded pulp for food packaging has the advantages of being light in weight, low in cost, degradable and renewable. Straw fibers can be converted into pulp with specific strength properties after pre-treatment with alkaline peroxide and mechanical pulping. Tschirner et al. [33] recovered corn straw and wheat straw and discovered that the pulping yield of corn straw was lower and the bonding strength was lower in laboratory pulping. On the contrary, wheat straw fiber had a higher pulping yield and a very good tensile property. Liu et al. [34] prepared molded sheets by molding with rice and wheat straw and starch to study moisture absorption properties, and the results revealed that the moisture absorption rate of rice and wheat straw segments was low. Leponiemi et al. [35] evaluated the suitability of wheat straw as pulp for the production of molded pulp, and the straw pulp can be used to make molded pulp for food packaging after chemical treatment and bleaching. Rattanawongkun et al. [36] prepared molded sheets from rice straw after pulping and molding at 130°C and 0.6 MPa pressure, and the molded sheets had high tensile strength and tensile index. The cross-section of the straw molded sheet revealed small gaps between the fiber layers and relatively good fiber adhesion, indicating that it can be used as a fiber raw material for molded pulp production. Wheat straw fiber has been evaluated as a potential partial replacement for hardwood kraft fiber. However, technological gaps in pulping and bleaching, transportation and storage, and physical strength limit the use of wheat straw materials [14]. As a new source of agricultural fiber, rape straw has some potential for pulp and paper production [37]. Rape straw’s surface and xylem have dense fibrous tissue, and the fibers are tightly packed together, giving it high toughness and tensile strength [38,39]. Hosseinpour et al. [40] pulped rape straw fibers using a chemical-mechanical method, resulting in rape straw fibers with dimensional characteristics and chemical compositions similar to sugar cane bagasse, and these fibers can be used as a raw material for molded pulp.
Oil palm, banana stems and pineapple leaves [36] all contain cellulose, which can be used to make molded pulp. Oil palm residues have been identified as the fifth most promising source of non-wood fiber. Oil palm leaves can be effectively converted into fiber using the sulfate pulping method, which has a low lignin content and a high holocellulose content in oil palm leaf fiber. Lerpong et al. [41] created molded pulp trays out of oil palm fibers and tested them as a shipping package for fresh apples. When used as soft-skinned fruit packaging, the surface roughness of the molded pulp products made of oil palm fiber is high, which will cause some damage to the surface of the fruit. Therefore, the surface smoothness of molded pulp products made from this fiber must be studied and improved further. Liu et al. [42] used atmospheric refining to convert waste oil palm empty fruit bunch fibers into fiber pulp for the production of three-dimensional molded pulp products, which can hold food products such as fruits and vegetables and can be composted or recycled after use. The main chemical composition of pineapple leaf fiber is holocellulose and α-cellulose. Pineapple leaf fiber pulp will be steamed to remove lignin, producing molded pulp products with varying degrees of smoothness [16]. Suwanno et al. [43] created molded pulp trays from pineapple leaf fibers and added chitosan and zinc oxide to improve the tray’s antimicrobial activity against Escherichia coli, Staphylococcus aureus, and Penicillium dijitatum. Apple pomace is a by-product of apple juice processing that has the advantages of low density and low cost. However, its use is limited due to high water absorption and relatively weak mechanical properties. The substances to be removed from apple pomace are pectin and hemicellulose. Liang et al. [17] extracted fibers from apple pomace using various treatments to prepare molded pulp panels and measured their mechanical properties and moisture content.
3 Research on the Properties of Molded Pulp
Fruits with thin skin, such as apples, pears and peaches, are frequently squeezed and deformed during transportation. The taste and appearance of fruit are harmed when the skin is damaged. Therefore, to avoid deformation and damage, food packaging should have certain mechanical properties [44–46]. Water vapor in the air, outside oil and grease in the food will greatly affect the flavor of food, such as cookies, milk and potato chips, etc. Food will also be contaminated, hastening the deterioration of corruption, so food packaging must be waterproof and oil-proof [47–49]. The materials used in packaging will also have an impact on food hygiene. Paper-based materials on the surface of powders and flakes can pollute food, decreasing consumer desire to buy it [50]. Therefore, molded pulp products for food packaging must not only use non-polluting, non-toxic fiber raw materials, but also have certain mechanical properties, hydrophobic and oil resistance, and be lint free and flakes.
The mechanical strength of molded pulp products is an important factor that affects their wider application. In the production of paper-based materials, the mechanisms by which polymers improve the dry and wet strength of fibers have been extensively studied. Polyamide-epichlorohydrin resin (PAE) is the most widely used formaldehyde-free wet strength agent in the production of paper-based food packaging. When PAE is added to the pulp and hot pressed, additional bonds between PAE and cellulose can be formed, thus significantly improving the mechanical properties of the molded pulp products [51]. Cationic starch can improve the mechanical properties of molded pulp [52]. In order to generate molded pulp products with excellent dry and wet strengths, Qin et al. [53] added PAE and cationic starch to the pulp. The synergistic interaction between cationic starch and PAE gave the molded pulp products the desired wet strength even with a lower amount of PAE. Water-soluble amphoteric polyacrylamide (AmPAM) is widely used in paper dry strength agents, when AmPAM dosage of 0.5% can make kraft paper hardwood fiber made of sheet breaking length increased by 25%. However, when AmPAM and cationic starch are combined, there is a negative synergistic effect, indicating that the two are not suitable for simultaneous use [54]. To study how cellulose nanofibers affected the mechanical properties of paper-based materials, Hassan et al. [55] added them to paper pulp. The results showed that using cellulose nanofibers could significantly improve the mechanical properties of paper-based materials and decrease porosity. It has been found that the addition of pre-mixed cellulose nanofibers and cationic starch to paper raw materials can substantially improve the tensile strength of paper [56]. By adding cellulose nanofibers and highly substituted cationic starch, either separately or together, Tajik et al. [57] improved the structure of hand-made paper made from bagasse pulp, improving the strength properties of the paper, with a continuous increase in tensile strength with increasing additive content. By increasing the relative content of molecular hydrogen bonds in cellulose and the contact area between fibers, laccase treatment of pulp containing lignin improves the “self-adhesion” between fibers [58], thereby increasing the wet strength of the pulp. Enzymatic lignin (EHL) is a by-product of bioethanol production from lignocellulosic materials [59] and has higher activity than other types of lignin due to its enzymatic capacity [60]. Zhao et al. [61] investigated the impact of enzymatic lignin (EHL) content on the tensile strength of molded pulp materials. Enzymatic lignin was added to increase the contact area between EHL and fibers, which reduced voids and strengthened the binding of fibers, increasing the tensile strength of molded pulp as a result.
Since most of the food is rich in water and oil, such as cookies, cakes and nuts, etc. As molded pulp products for food packaging, they must possess reliable barrier qualities, such as hydrophobicity and oil barrier, in addition to a certain level of mechanical strength. The plant fibers are naturally hydrophilic and can easily absorb water and oil without the need for additional processing. The reasonable use of hydrophobic and oil repellents agents can improve the barrier properties of molded pulp products to a certain extent. In the past, fluorine-containing reagents were often used as hydrophobic and oil-repellent agents. However, fluoro silane reagents do significant harm to both the human body and the environment, and when used in food packaging, they may enter the body along with food and have negative health effects [62]. Therefore, they are not suitable for food packaging. So, the investigation of fluorine-free and biological additives in pulp and paper has received more attention.
Cellulose is a hydrophilic material that tends to absorb moisture when it comes in contact with a humid environment, so changing its hydrophilicity to obtain hydrophobic or superhydrophobic properties can make molded pulp products better for use in food packaging and other industries. By structurally altering epoxidized castor oil through ester exchange and silylation processes, then hydrolyzing and cross-linking silylated bioresins with cellulose paper substrates through a condensation process, Parvathy et al. [63] were able to create silylated castor oil and silylated castor oil methyl ester. This resulted in paper-based materials with hydrophobic properties and water contact angles as high as 97 degrees. The hydrophobicity of paper products can also be improved by adding tannins to the pulp raw material. Ji et al. [64] produced hydrophobic papers with contact angles greater than 90 degrees by periodate oxidizing pulp fibers and reacting it with tannin to create covalent bonds between aldehyde groups on cellulose and hydrogen bonds on tannin. Nanofibrillated cellulose (NFC) was chemically modify by Klayya et al. [65] using fatty acids to create modified NFC (mNFC), which was then added to bagasse pulp at 5 wt% to create molded sheets. The final obtained molded sheets demonstrated satisfactory surface water resistance thanks to mNFC with 0.55 ester group substitution in the experiments. The water resistance was significantly improved, and the water contact angle was increased by 70%. Chen et al. [66] created a high-strength superhydrophobic paper-based packaging material. By first laminating microfibrillated cellulose (MFC) and then spraying silica, which gave the cellulose paper base’s two surfaces super hydrophpbicity and a water contact angle of 151.2 degrees.
Palmitic acid is a saturated chain fatty acid with polar groups that can bind to metal cations. Izadyar et al. [67] created layered double hydroxides using zinc and aluminum hydroxide. The layered double hydroxides then used to synthesize cellulose fibers that had been palmitic acid-functionalized, and the modified fiber-based materials displayed hydrophobic properties with a water contact angle of 140 ± 0.2 degrees. Zeng et al. [68] used palm kernel oil as a water repellent and hydrophobic agent, which was mixed with solvent and furfuryl alcohol to make palm kernel oil formulation and applied to paper-based materials, and the obtained materials had measured water contact angle close to 120 degrees and water vapor transmission rate was reduced by 22%, and this hydrophobic and water repellent agent made from biodegradable oil has green and low-cost characteristics.
According to research, oil can penetrate molded pulp products primarily through the capillary phenomenon of the fiber. There are two ways to improve the oil resistance of molded pulp products: first, improve the pulp pulping degree, which reduces permeability, and thus improves the oil resistance; second, add pulp or surface coating of certain oil inhibitors. Chitosan is a bio-based material that degrades naturally in the environment. Many researchers have used it in food packaging [69,70]. Chitosan alone can provide some oil resistance to the molded pulp, while chitosan combined with other components can provide synergistic enhanced oil resistance [71]. Shi et al. [72] coated paper-based materials with chitosan and carboxymethyl cellulose sequentially, which effectively improved the barrier property of paper-based materials to oil. Wang et al. [73] added montmorillonite to chitosan to enhance the oil repellency of chitosan coating. They discovered that at 2% and 0.1% chitosan and montmorillonite concentrations, respectively, the oil repellency grade of the coated paper was optimal up to grade 9 with an oil repellency penetration time of 290.8 s due to the filling of montmorillonite into the cellulose fiber network. Jiao et al. [74] successfully prepared paper-based materials with oil resistance properties by dissolving filter paper made from cellulose fibers in an aqueous solution of NaOH/urea/ZnO (mass ratio 8:12:0.25), then rinsing with ultrapure water to remove NaOH and urea after treatment, and finally drying under vacuum for 10 min. The treated paper was completely oil-resistant within 24 h.
3.2.3 Water and Oil Resistance
Since most food packaging needs to be both waterproof and oil-proof, research on paper-based packaging materials that take into account both waterproof and oil-proof properties has started. Polydimethylsiloxane (PDMS) is an environmentally friendly material with excellent water and oil repellency [75]. The synthetic coated paper base material can have significant water and oil resistance by successively coating the surface of the paper base material with chitosan and hydrophobic corn alcohol soluble protein solutions [76]. Hamdani et al. [77] used PDMS to react with chitosan to create chitosan graft dimethyl siloxane copolymer, which was mixed in ethanol and applied as a coating on paper-based materials to obtain water and oil repellent materials. Li et al. [78] used the response surface method to determine the optimal concentration of chitosan and PDMS to use on paper-based materials, and the paper-based materials coated with 8.6 wt% chitosan and 2.2% PDMS exhibited excellent oil and water resistance. Yi et al. [79] created a hydrophobic and oleophobic paper-based material with a water contact angle of up to 144 degrees and oil resistance up to class 12 by encapsulating a mixture of cellulose nanofibrils (CNF), polydimethylsiloxane (PDMS) and CNF particles on conventional paper. The ester modified nanofibrillated cellulose (mNFC) and natural polyester gum are combined to cover the surface of the molded pulp, and due to the ester modification of nanocellulose, and the hydrophobicity of the surface of the molded pulp is improved and the oil resistance level reaches class 7 [80]. The polar groups such as urethane, ester groups, and ether bonds in water-based polyurethane form a dense film on the surface of the paper material through hydrogen bonding, thus preventing the penetration of water and oil. Li et al. [81] coated dimer acid-based waterborne polyurethanes (DWPUs) on the surface of paper-based materials and investigated their water and oil resistance properties, discovering that the water absorption of DWPUs-coated paper-based materials was reduced by 88% when compared to uncoated paper-based materials, and the oil resistance was further improved. Researchers have studied the water and oil repellency of paper-based materials by coating the paper surface with polymeric materials, and the same can be accomplished by coating molded pulp with these coating materials that can achieve water and oil repellency. More research is needed to determine whether the same excellent water and oil repellency can be achieved by adding polymer materials to the pulp and thermoforming it into molded pulp products.
Molded pulp is frequently plagued by issues such as rough surface and easy linting and scraping, especially when used as food packaging. The issue of linting and scraping limits the large-scale application of molded pulp. Fiber modification, in-pulp additive addition, and surface coating are all methods for improving molded pulp linting and flaking. Nanofibrillated cellulose (NFC) is frequently used as a reinforcing additive for paper-based materials, and it has shown great potential in reducing linting and flaking on paper-based materials, with NFC added to the pulp reducing linting and flaking by 47% [82]. Balea et al. [83] extracted cellulose nanofibers (CNFs) from eucalyptus, pine and wheat straw and added them to paper pulp to investigate their effect on paper-based material linting and flaking. The addition of 3 wt% CNFs resulted in a 40% reduction in paper-based material linting, indicating that CNFs have great potential as anti-flaking agents in paper manufacturing. The surface treatment can enhance the surface strength of paper-based materials and reduce the occurrence of linting and flaking. The combination of microfibrillated cellulose (MFC) and anionic starch for surface treatment of molded pulp sheets has a strong synergistic effect, and the mixture can improve the anti-linting and flaking performance more than either additive alone [84]. At present, research on paper-based material linting and flaking is limited and primarily focused on paper, with almost no research on the surface treatment of molded pulp. One of the main reasons for the limited use of molded pulp is that its surface lacks the aesthetic appearance of plastic products and has linting and flaking. Therefore, the anti-flaking performance of molded pulp products can be studied further by referring to research on paper anti-flaking.
Food packaging protects meals from mechanical and chemical harm during transportation, ensuring that consumers obtain wholesome and satisfying food. With increased consumer health awareness, people are more aware of whether the packaging contains dangerous materials and whether these compounds migrate into food through food contact [85]. Therefore, when molding pulp, the impact of additives on food safety should be taken into account. Fluorine-containing additives are currently regulated in food packaging by the United States and the European Union [86]. The additives used to improve the performance of pulp-moulded products are included in Table 2 along with information on their suitability for use as food packaging.
The widespread use of petroleum-based food packaging has resulted in waste-related environmental degradation, and the production of molded pulp for food packaging using renewable and biodegradable plant fibers has emerged as a significant market trend. Considering that considerable research has been done and some progress has been made in the area of molded pulp for food packaging, the authors believe that some of the following concerns merit additional investigation:
1) Non-wood fibers can also be used to make molded pulp products in addition to wood fibers, which are traditionally used in the largest quantities, at lower costs and higher yields. However, there are still many challenges in the extraction and processing of these fibers, which is one of the reasons limiting their industrial-scale production.
2) Varied plant fibers have different morphologies and characteristics, and the molded pulp products that are produced have different properties. Future research can be done on the synergistic use of various fiber formulations to enhance the performance of molded pulp products in the future.
3) Molded pulp products for food packaging need to be waterproof, oilproof, chip proof and have a higher strength and stiffness. These high-performance requirements undoubtedly present greater challenges in the production and preparation of molded pulp products.
Funding Statement: The research work presented in this paper is supported by the Special Funds for Fundamental Scientific Research Funds of Central Universities (JUSRP21115) and Independent Research Project Funding Project of Jiangsu Key Laboratory of Advanced Food Manufacturing Equipment Technology (FMZ201902). Any research results expressed in this paper are those of the writers and do not necessarily reflect the views of the foundations.
Conflicts of Interest: The authors declare that they have no conflicts of interest to report regarding the present study.
References
1. Navarre, N., Mogollon, J. M., Tukker, A., Barbarossa, V. (2022). Recycled plastic packaging from the Dutch food sector pollutes asian oceans. Resources Conservation and Recycling, 185, 106508. https://doi.org/10.1016/j.resconrec.2022.106508 [Google Scholar] [CrossRef]
2. Singh, A. K., Itkor, P., Lee, M., Shin, J., Lee, Y. S. (2022). Promoting sustainable packaging applications in the circular economy by exploring and advancing molded pulp materials for food products: A review. Critical Reviews in Food Science and Nutrition, 16. https://doi.org/10.1080/10408398.2022.2088686 [Google Scholar] [PubMed] [CrossRef]
3. Didone, M., Saxena, P., Brilhuis-Meijer, E., Tosello, G., Bissacco, G. et al. (2017). Moulded pulp manufacturing: Overview and prospects for the process technology. Packaging Technology and Science, 30(6), 231–249. https://doi.org/10.1002/pts.2289 [Google Scholar] [CrossRef]
4. Semple, K. E., Zhou, C. L., Rojas, O. J., Nkeuwa, W. N., Dai, C. P. (2022). Moulded pulp fibers for disposable food packaging: A state-of-the-art review. Food Packaging and Shelf Life, 33, 100908. https://doi.org/10.1016/j.fpsl.2022.100908 [Google Scholar] [CrossRef]
5. Dislaire, C., Grohens, Y., Seantier, B., Muzy, M. (2021). The impact of molded pulp product process on the mechanical properties of molded bleached chemi-thermo-mechanical pulp. Functional Composite Materials, 2(1), 1–10. https://doi.org/10.1186/s42252-021-00023-3 [Google Scholar] [CrossRef]
6. Manandhar, S., Shrestha, B., Sciortino, F., Ariga, K., Shrestha, L. K. (2022). Recycling waste paper for further implementation: XRD, FTIR, SEM, and EDS studies. Journal of Oleo Science, 71(4), 619–626. https://doi.org/10.5650/jos.ess21396 [Google Scholar] [PubMed] [CrossRef]
7. Yuan, Z. Y., Wei, W. Q., Wen, Y. B. (2019). Improving the production of nanofibrillated cellulose from bamboo pulp by the combined cellulase and refining treatment. Journal of Chemical Technology and Biotechnology, 94(7), 2178–2186. [Google Scholar]
8. Liu, C., Luan, P. C., Li, Q., Cheng, Z., Sun, X. et al. (2020). Biodegradable, hygienic, and compostable tableware from hybrid sugarcane and bamboo fibers as plastic alternative. Matter, 3(6), 2066–2079. [Google Scholar]
9. Ihnat, V., Fiserova, M., Opalena, E., Russ, A., Bohacek, S. (2021). Chemical composition and fibre characteristics of branch wood of selected hardwood species. Acta Facultatis Xylologiae Zvolen, 63(2), 17–30. [Google Scholar]
10. Tripathi, S. K., Bhardwaj, N. K., Ghatak, H. R. (2020). Developments in ozone-based bleaching of pulps. Ozone-Science & Engineering, 42(2), 194–210. https://doi.org/10.1080/01919512.2019.1647407 [Google Scholar] [CrossRef]
11. Suhaimi, N. M., Hassan, N. H. M., Ibrahim, R., Jasmani, L. (2022). Pulping yield and mechanical properties of unbeaten bamboo paper. Pertanika Journal of Science and Technology, 30(2), 1397–1408. [Google Scholar]
12. Liu, L., Lei, Y., Chen, G. (2018). Research on the preparation and properties of water resistant and oil resistant paper tableware made by bagasse brown pulp. In: Applied sciences in graphic communication and packaging, pp. 609–615. USA: Springer. [Google Scholar]
13. Luan, P. C., Li, J., He, S. M., Kuang, Y. S., Mo, L. H. et al. (2019). Investigation of deposit problem during sugarcane bagasse pulp molded tableware production. Journal of Cleaner Production, 237, 117856. [Google Scholar]
14. Hart, P. W. (2020). Wheat straw as an alternative pulp fiber. Tappi Journal, 19(1), 41–52. [Google Scholar]
15. Subramaniam, V., Muhamad, H., Hashim, Z., May, C. Y. (2014). Water footprint: Part 3–The production of crude palm oil in Malaysian palm oil mills. Journal of Oil Palm Research, 26(4), 292–299. [Google Scholar]
16. Iewkittayakorn, J., Khunthongkaew, P., Wongnoipla, Y., Kaewtatip, K., Suybangdum, P. et al. (2020). Biodegradable plates made of pineapple leaf pulp with biocoatings to improve water resistance. Journal of Materials Research and Technology, 9(3), 5056–5066. [Google Scholar]
17. Liang, C. V., Wang, T., Zhao, Y. (2021). Investigation of eco-friendly chemical treatments of apple pomace for producing high quality molded pulp biocomposite. Journal of Applied Polymer Science, 138(46). https://doi.org/10.1002/app.51363 [Google Scholar] [CrossRef]
18. Poletto, M., Zattera, A. J., Forte, M. M. C., Santana, R. M. C. (2012). Thermal decomposition of wood: Influence of wood components and cellulose crystallite size. Bioresource Technology, 109, 148–153. [Google Scholar] [PubMed]
19. Fiserova, M., Gigac, J., Stankovska, M., Opalena, E. (2019). Influence of bleached softwood and hardwood kraft pulps on tissue paper properties. Cellulose Chemistry and Technology, 53(5–6), 469–477. [Google Scholar]
20. Blanchette, D., Fournier, R. A., Luther, J. E., Cote, J. F. (2015). Predicting wood fiber attributes using local-scale metrics from terrestrial LiDAR data: A case study of newfoundland conifer species. Forest Ecology and Management, 347, 116–129. [Google Scholar]
21. Boakye, B. K., Michael, A., Agyapong, A. K., Elizabeth, N. A. (2022). Pulp and paper making characteristics of fibers from plantation-grown Oxythenantera abyssinica and beema bamboo (A tissue cultured clone from Bambusa balcooa). Journal of Natural Fibers, 19(11), 4198–4209. [Google Scholar]
22. Wang, H. Q., Wang, J. L., Si, S. R., Wang, Q., Li, X. S. et al. (2021). Residual-lignin-endowed molded pulp lunchbox with a sustained wet support strength. Industrial Crops and Products, 170. https://doi.org/10.1016/j.indcrop.2021.113756 [Google Scholar] [CrossRef]
23. Tao, S. M., Zhang, C. Z., Chen, Y., Qin, S. L., Qi, H. S. (2022). High strength holocellulose paper from bamboo as biodegradable packaging tape. Carbohydrate Polymers, 283. https://doi.org/10.1016/j.carbpol.2022.119151 [Google Scholar] [PubMed] [CrossRef]
24. Zhang, Y. C., Hou, Q. X., Fu, Y. J., Xu, C. L., Smeds, A. I. et al. (2018). One-step fractionation of the main components of bamboo by formic acid-based organosolv process under pressure. Journal of Wood Chemistry and Technology, 38(3), 170–182. https://doi.org/10.1080/02773813.2017.1388823 [Google Scholar] [CrossRef]
25. Tripathi, S. K., Mishra, O. P., Bhardwaj, N. K., Varadhan, R. (2018). Pulp and papermaking properties of bamboo species melocanna baccifera. Cellulose Chemistry and Technology, 52(1–2), 81–88. [Google Scholar]
26. Chang, F. J., Wang, E. I. C., Perng, Y. S., Chen, C. C. (2013). Effect of bamboo age on the pulping properties of bambusa stenostachya hackel. Cellulose Chemistry and Technology, 47(3–4), 285–293. [Google Scholar]
27. Cao, S. L., Ma, X. J., Lin, L., Huang, F., Huang, L. L. et al. (2014). Morphological and chemical characterization of green bamboo (Dendrocalamopsis oldhami (Munro) keng f.) for dissolving pulp production. BioResources, 9(3), 4528–4539. https://doi.org/10.15376/biores.9.3.4528-4539 [Google Scholar] [CrossRef]
28. Andrade, M. F., Colodette, J. L. (2014). Dissolving pulp production from sugar cane bagasse. Industrial Crops and Products, 52, 58–64. https://doi.org/10.1016/j.indcrop.2013.09.041 [Google Scholar] [CrossRef]
29. Li, Z. Z., Zhang, X. L., Fa, C. G., Zhang, Y. Y., Xiong, J. P. et al. (2020). Investigation on characteristics and properties of bagasse fibers: Performances of asphalt mixtures with bagasse fibers. Construction and Building Materials, 248, 118648. https://doi.org/10.1016/j.conbuildmat.2020.118648 [Google Scholar] [CrossRef]
30. Jafari-Petroudy, S. R., Resalati, H., Rezayati-Charani, P. (2011). Newsprint from soda bagasse pulp in admixture with hardwood CMP pulp. BioResources, 6(3), 2483–2491. [Google Scholar]
31. Fares, Y. G. D., Taha, A. S., Elgat, W., Salem, M. Z. M., Al-Huqail, A. A. et al. (2020). Ecologically friendly modified green liquor method for enhancing the technological properties of sugarcane bagasse (Saccharum officinarum L.) pulp. BioResources, 15(4), 7458–7474. https://doi.org/10.15376/biores.15.4.7458-7474 [Google Scholar] [CrossRef]
32. Razali, N. A. M., Sohaimi, R. M., Othman, R., Abdullah, N., Demon, S. Z. N. et al. (2022). Comparative study on extraction of cellulose fiber from rice straw waste from chemo-mechanical and pulping method. Polymers, 14(3). https://doi.org/10.3390/polym14030387 [Google Scholar] [PubMed] [CrossRef]
33. Tschirner, U., Barsness, J., Keeler, T. (2007). Recycling of chemical pulp from wheat straw and corn stover. BioResources, 2(4), 536–543. [Google Scholar]
34. Liu, J., He, C. (2012). Preparation of rice straw and starch-based biodegradable decorative materials. Transactions of the Chinese Society of Agricultural Engineering, 28(6), 283–288. [Google Scholar]
35. Leponiemi, A., Johansson, A., Edelmann, K., Sipila, K. (2010). Producing pulp and energy from wheat straw. Appita Journal, 63(1), 65–73. [Google Scholar]
36. Rattanawongkun, P., Kunfong, N., Klayya, S., Chotimarnon, T., Duangphet, S. et al. (2020). Comparison of molded pulps from rice straw, pineapple leaf and banana stem pulps. Scienceasia, 46, 79–84. https://doi.org/10.2306/scienceasia1513-1874.2020.S011 [Google Scholar] [CrossRef]
37. Mousavi, S. M. M., Hosseini, S. Z., Resalati, H., Mandavi, S., Garmaroody, E. R. (2013). Papermaking potential of rapeseed straw, a new agricultural-based fiber source. Journal of Cleaner Production, 52, 420–424. https://doi.org/10.1016/j.jclepro.2013.02.016 [Google Scholar] [CrossRef]
38. Lu, X. Y., Zhao, Z. (2022). Effect of rape straw fiber on mechanical properties and microstructure of fly ash concrete. Advances in Civil Engineering, 2022, 3002430. https://doi.org/10.1155/2022/3002430 [Google Scholar] [CrossRef]
39. Jerman, M., Bohm, M., Dusek, J., Cerny, R. (2022). Effect of steaming temperature on microstructure and mechanical, hygric, and thermal properties of binderless rape straw fiberboards. Building and Environment, 223. https://doi.org/10.1016/j.buildenv.2022.109474 [Google Scholar] [CrossRef]
40. Hosseinpour, R., Fatehi, P., Latibari, A. J., Ni, Y. H., Sepiddehdam, S. J. (2010). Canola straw chemimechanical pulping for pulp and paper production. Bioresource Technology, 101(11), 4193–4197. https://doi.org/10.1016/j.biortech.2010.01.055 [Google Scholar] [PubMed] [CrossRef]
41. Lerpong, J., Ratanapat, H. U., Nattinee, B. (2022). Potential use of oil palm fronds for papermaking and application as molded pulp trays for fresh product under simulated cold chain logistics. Journal of Natural Fibers, 19(7), 2772–2784. [Google Scholar]
42. Liu, Q. Y., Loxton, C., Mohamed, A. A., Jawaid, M., Braganca, R. et al. (2021). Development of pulp moulded packaging samples from empty fruit bunch fibre. Pertanika Journal of Science and Technology, 29(4), 2901–2912. https://doi.org/10.47836/pjst.29.4.36 [Google Scholar] [CrossRef]
43. Suwanno, T., Soykeabkaew, N., Tongdeesoontorn, W. (2019). ‘Phulae’ pineapple leaf molded pulp tray with znops. Italian Journal of Food Science, 31(5), 116–121. [Google Scholar]
44. Bhat, S. A., Rizwan, D., Mir, S. A., Wani, S. M., Masoodi, F. A. (2022). Advances in apple packaging: A review. Journal of Food Science and Technology, 60, 1847–1859. https://doi.org/10.1007/s13197-022-05447-8 [Google Scholar] [PubMed] [CrossRef]
45. Wang, L. J., Zhang, Q., Song, H. Y., Wang, Z. W. (2022). Mechanical damage of ‘Huangguan’ pear using different packaging under random vibration. Postharvest Biology and Technology, 187, 10. https://doi.org/10.1016/j.postharvbio.2022.111847 [Google Scholar] [CrossRef]
46. Sasaki, Y., Orikasa, T., Nakamura, N., Hayashi, K., Yasaka, Y. et al. (2022). Determination of the most environmentally friendly packaging for peach during transportation by modeling the relationship between food loss reduction and environmental impact. Journal of Food Engineering, 331, 12. https://doi.org/10.1016/j.jfoodeng.2022.111120 [Google Scholar] [CrossRef]
47. Baele, M., Vermeulen, A., Adons, D., Peeters, R., Vandemoortele, A. et al. (2021). Selecting packaging material for dry food products by trade-off of sustainability and performance: A case study on cookies and milk powder. Packaging Technology and Science, 34(5), 303–318. https://doi.org/10.1002/pts.2561 [Google Scholar] [CrossRef]
48. Bertolini, M., Bottani, E., Vignali, G., Volpi, A. (2016). Comparative life cycle assessment of packaging systems for extended shelf life milk. Packaging Technology and Science, 29(10), 525–546. https://doi.org/10.1002/pts.2235 [Google Scholar] [CrossRef]
49. Agarwal, A., Raheja, A., Natarajan, T. S., Chandra, T. S. (2014). Effect of electrospun montmorillonite-nylon 6 nanofibrous membrane coated packaging on potato chips and bread. Innovative Food Science & Emerging Technologies, 26, 424–430. https://doi.org/10.1016/j.ifset.2014.09.012 [Google Scholar] [CrossRef]
50. Boelsen-Robinson, T., Orellana, L., Backholer, K., Kurzeme, A., Jerebine, A. et al. (2020). Change in drink purchases in 16 Australian recreation centres following a sugar-sweetened beverage reduction initiative: An observational study. BMJ Open, 10(3), e029492. https://doi.org/10.1136/bmjopen-2019-029492 [Google Scholar] [PubMed] [CrossRef]
51. Guo, X., Ma, Z. Y., Wang, H. S., Lv, Y. N. (2021). Design and mechanism of controllable respiration polyamideamine-epichlorohydrin modied sugarcane bagasse pith hemicellulose film. Journal of Applied Polymer Science, 138(27). https://doi.org/10.1002/app.50653 [Google Scholar] [CrossRef]
52. Sandak, A., Jaszczur, A., Sandak, J., Modzelewska, I. (2015). Near infrared assessment of biodegradability and mechanical properties of paper made of cellulose sulfate bleached coniferous pulp with addition of cationic starch and resinous adhesive. International Biodeterioration & Biodegradation, 97, 31–39. https://doi.org/10.1016/j.ibiod.2014.09.019 [Google Scholar] [CrossRef]
53. Qin, C. R., Li, J., Wang, W., Li, W. (2022). Improving mechanical strength and water barrier properties of pulp molded product by Wet-end added polyamide epichlorohydrin/Cationic starch. ACS Omega, 7(26), 22173–22180. https://doi.org/10.1021/acsomega.1c07369 [Google Scholar] [PubMed] [CrossRef]
54. Wang, P. P., Zhu, Y. Y., Wang, X. Y., Zhang, X. Y., Zhu, W. Y. et al. (2018). Application of amphoteric polyacrylamide solely or with the combination of cationic starch for paper strength improvement. BioResources, 13(4), 7864–7872. https://doi.org/10.15376/biores.13.4.7864-7872 [Google Scholar] [CrossRef]
55. Hassan, M., Berglund, L., Hassan, E., Abou-Zeid, R., Oksman, K. (2018). Effect of xylanase pretreatment of rice straw unbleached soda and neutral sulfite pulps on isolation of nanofibers and their properties. Cellulose, 25(5), 2939–2953. https://doi.org/10.1007/s10570-018-1779-2 [Google Scholar] [CrossRef]
56. Hubbe, M. A. (2019). Nanocellulose, cationic starch and paper strength. Appita Journal, 72(2), 82–94. [Google Scholar]
57. Tajik, M., Torshizi, H. J., Resalati, H., Hamzeh, Y. (2018). Effects of cationic starch in the presence of cellulose nanofibrils on structural, optical and strength properties of paper from soda bagasse pulp. Carbohydrate Polymers, 194, 1–8. https://doi.org/10.1016/j.carbpol.2018.04.026 [Google Scholar] [PubMed] [CrossRef]
58. Wang, Q. L., Xiao, S. L., Shi, S. Q., Cai, L. P. (2018). Mechanical strength, thermal stability, and hydrophobicity of fiber materials after removal of residual lignin. BioResources, 13(1), 71–85. [Google Scholar]
59. Zhou, J., Zhou, Y., Bo, C., Li, P., Liang, B. (2015). Advances in the extraction and application of enzymatic lignin. New Chemical Materials, 4, 245–246. [Google Scholar]
60. Yu, C., Zhang, W., Bekele, L. D., Duns, G. J., Jin, L. et al. (2018). Characterization of thermoplastic composites developed with wheat straw and enzymatic-hydrolysis lignin. BioResources, 13(2), 3219–3235. https://doi.org/10.15376/biores.13.2.3219-3235 [Google Scholar] [CrossRef]
61. Zhao, Y. L., Xiao, S. L., Yue, J. Q., Zheng, D. Y., Cai, L. P. (2020). Effect of enzymatic hydrolysis lignin on the mechanical strength and hydrophobic properties of molded fiber materials. Holzforschung, 74(5), 469–475. https://doi.org/10.1515/hf-2018-0295 [Google Scholar] [CrossRef]
62. Qiu, Y., Zhang, Z., Liang, S. B., Miao, Y. N., Yao, C. L. (2022). Preparation of fluorine-free and stable superhydrophobic paper for packaging. Journal of Wood Chemistry and Technology, 42(4), 222–234. https://doi.org/10.1080/02773813.2022.2070646 [Google Scholar] [CrossRef]
63. Parvathy, P. A., Sahoo, S. K. (2021). Hydrophobic, moisture resistant and biorenewable paper coating derived from castor oil based epoxy methyl ricinoleate with repulpable potential. Progress in Organic Coatings, 158. https://doi.org/10.1016/j.porgcoat.2021.106347 [Google Scholar] [CrossRef]
64. Ji, Y. Z., Xu, Q. H., Jin, L. Q., Fu, Y. J. (2020). Cellulosic paper with high antioxidative and barrier properties obtained through incorporation of tannin into kraft pulp fibers. International Journal of Biological Macromolecules, 162, 678–684. https://doi.org/10.1016/j.ijbiomac.2020.06.101 [Google Scholar] [PubMed] [CrossRef]
65. Klayya, S., Tawichai, N., Intatha, U., Zhang, H., Bilotti, E. et al. (2021). Tailoring nanofibrillated cellulose through sonication and its potential use in molded pulp packaging. Nanocomposites, 7(1), 109–122. https://doi.org/10.1080/20550324.2021.1949517 [Google Scholar] [CrossRef]
66. Chen, H. Y., Wang, B., Li, J. P., Ying, G. D., Chen, K. F. (2022). High-strength and super-hydrophobic multilayered paper based on nano-silica coating and micro-fibrillated cellulose. Carbohydrate Polymers, 288. https://doi.org/10.1016/j.carbpol.2022.119371 [Google Scholar] [PubMed] [CrossRef]
67. Izadyar, S., Aghabozorgi, M., Azadfallah, M. (2020). Palmitic acid functionalization of cellulose fibers for enhancing hydrophobic property. Cellulose, 27(10), 5871–5878. https://doi.org/10.1007/s10570-020-03174-x [Google Scholar] [CrossRef]
68. Zeng, K. X., Gu, J., Cao, C. Y. (2020). Facile approach for ecofriendly, low-cost, and water-resistant paper coatings via palm kernel oil. ACS Applied Materials & Interfaces, 12(16), 18987–18996. https://doi.org/10.1021/acsami.0c00067 [Google Scholar] [PubMed] [CrossRef]
69. Li, Y. N., Ren, J. Z., Zhang, G. Q., Li, X. O. (2021). High-barrier and antibacterial films based on PET/SiOx for food packaging applications. Food Science and Technology, 41(3), 763–767. https://doi.org/10.1590/fst.37720 [Google Scholar] [CrossRef]
70. Wang, F. J., Wang, L. Q., Zhang, X. C., Ma, S. F., Zhao, Z. C. (2022). Study on the barrier properties and antibacterial properties of cellulose-based multilayer coated paperboard used for fast food packaging. Food Bioscience, 46, 101398. https://doi.org/10.1016/j.fbio.2021.101398 [Google Scholar] [CrossRef]
71. Long, Z., Wu, M. Y., Peng, H., Dai, L., Zhang, D. et al. (2015). Preparation and oil-resistant mechanism of Chitosan/Cationic starch oil-proof paper. BioResources, 10(4), 7907–7920. https://doi.org/10.15376/biores.10.4.7907-7920 [Google Scholar] [CrossRef]
72. Shi, H. B., Wu, L. H. Y., Luo, Y. D., Yu, F. Y., Li, H. (2022). A facile method to prepare cellulose fiber-based food packaging papers with improved mechanical strength, enhanced barrier, and antibacterial properties. Food Bioscience, 48, 101729. https://doi.org/10.1016/j.fbio.2022.101729 [Google Scholar] [CrossRef]
73. Wang, K., Zhao, L., He, B. (2021). Chitosan/Montmorillonite coatings for the fabrication of food-safe greaseproof paper. Polymers, 13(10), 1607. https://doi.org/10.3390/polym13101607 [Google Scholar] [PubMed] [CrossRef]
74. Jiao, L., Ma, J. X., Dai, H. Q. (2015). Preparation and characterization of self-reinforced antibacterial and oil-resistant paper using a NaOH/Urea/ZnO solution. PLoS One, 10(10), 179–183. https://doi.org/10.1371/journal.pone.0140603 [Google Scholar] [PubMed] [CrossRef]
75. Khan, F., Rabnawaz, M., Li, Z., Khan, A., Naveed, M. et al. (2019). Simple design for durable and clear self-cleaning coatings. ACS Applied Polymer Materials, 1(10), 2659–2667. https://doi.org/10.1021/acsapm.9b00596 [Google Scholar] [CrossRef]
76. Kansal, D., Hamdani, S. S., Ping, R. Q., Sirinakbumrung, N., Rabnawaz, M. (2020). Food-safe chitosan-zein dual-layer coating for water- and oil-repellent paper substrates. ACS Sustainable Chemistry & Engineering, 8(17), 6887–6897. https://doi.org/10.1021/acssuschemeng.0c02216 [Google Scholar] [CrossRef]
77. Hamdani, S. S., Li, Z., Rabnawaz, M., Kamdem, D. P., Khan, B. A. (2020). Chitosan-graft-poly (dimethylsiloxane)/Zein coatings for the fabrication of environmentally friendly oil- and water-resistant paper. ACS Sustainable Chemistry & Engineering, 8(13), 5147–5155. https://doi.org/10.1021/acssuschemeng.9b07397 [Google Scholar] [CrossRef]
78. Li, Z., Rabnawaz, M. (2019). Oil- and water-resistant coatings for porous cellulosic substrates. Acs Applied Polymer Materials, 1(1), 103–111. https://doi.org/10.1021/acsapm.8b00106 [Google Scholar] [CrossRef]
79. Yi, K., Fu, S. Y., Zhang, H., Zhang, H. C., Wang, Y. et al. (2022). Cellulose nanofibrils/polydimethylsiloxane double-layer coating for fabrication of high barrier and excellent water- and oil-resistance paper. Progress in Organic Coatings, 172. https://doi.org/10.1016/j.porgcoat.2022.107123 [Google Scholar] [CrossRef]
80. Klayya, S., Tawichai, N., Intatha, U., Zhang, H., Bilotti, E. et al. (2022). Sustainable nanocomposite coating for moulded pulp with enhanced barrier properties for food packaging applications. Polymer International, 72(3), 323–332. [Google Scholar]
81. Li, D. D., Hu, D. G., Tan, J. H., Zhu, Q. H., Liu, Z. L. et al. (2021). Design and synthesis of dimer acid-based waterborne polyurethane as water- and oil-resistant coating for paper substrates. Materials & Design, 211. https://doi.org/10.1016/j.matdes.2021.110142 [Google Scholar] [CrossRef]
82. Balea, A., Blanco, A., Merayo, N., Negro, C. (2016). Effect of nanofibrillated cellulose to reduce linting on high filler-loaded recycled papers. Appita, 69(2), 148–156. [Google Scholar]
83. Balea, A., Merayo, N., Fuente, E., Negro, C., Delgado-Aguilar, M. et al. (2018). Cellulose nanofibers from residues to improve linting and mechanical properties of recycled paper. Cellulose, 25(2), 1339–1351. https://doi.org/10.1007/s10570-017-1618-x [Google Scholar] [CrossRef]
84. Song, H. N., Ankerfors, M., Hoc, M., Lindstrom, T. (2010). Reduction of the linting and dusting propensity of newspaper using starch and microfibrillated cellulose. Nordic Pulp & Paper Research Journal, 25(4), 495–504. https://doi.org/10.3183/NPPRJ-2010-25-04-p495-504 [Google Scholar] [CrossRef]
85. Alamri, M. S., Qasem, A. A. A., Mohamed, A. A., Hussain, S., Ibraheem, M. A. et al. (2021). Food packaging’s materials: A food safety perspective. Saudi Journal of Biological Sciences, 28(8), 4490–4499. https://doi.org/10.1016/j.sjbs.2021.04.047 [Google Scholar] [PubMed] [CrossRef]
86. Ham-Pichavant, F., Sebe, G., Pardon, P., Coma, V. (2005). Fat resistance properties of chitosan-based paper packaging for food applications. Carbohydrate Polymers, 61(3), 259–265. https://doi.org/10.1016/j.carbpol.2005.01.020 [Google Scholar] [CrossRef]
87. Osman, W. H. W., Abdullah, S. R. S., Mohamad, A., Kadhum, A. A. H., Abd Rahman, R. (2013). Simultaneous removal of AOX and COD from real recycled paper wastewater using GAC-SBBR. Journal of Environmental Management, 121, 80–86. https://doi.org/10.1016/j.jenvman.2013.02.005 [Google Scholar] [PubMed] [CrossRef]
88. Liu, Y. H., Liu, M. Y., Zhang, L. L., Cao, W. Q., Wang, H. et al. (2022). Preparation and properties of biodegradable films made of cationic potato-peel starch and loaded with curcumin. Food Hydrocolloids, 130, 107690. https://doi.org/10.1016/j.foodhyd.2022.107690 [Google Scholar] [CrossRef]
89. Khatami, S. H., Vakili, O., Movahedpour, A., Ghesmati, Z., Ghasemi, H. et al. (2022). Laccase: Various types and applications. Biotechnology and Applied Biochemistry, 69(6), 2658–2672. https://doi.org/10.1002/bab.2313 [Google Scholar] [PubMed] [CrossRef]
90. Chandra, R. P., Lehtonen, L. K., Ragauskas, A. J. (2004). Modification of high lignin content kraft pulps with laccase to improve paper strength properties. 1. Laccase treatment in the presence of gallic acid. Biotechnology Progress, 20(1), 255–261. https://doi.org/10.1021/(ISSN)1520-6033 [Google Scholar] [CrossRef]
91. Xu, L. N., Liu, Y. Y., Yang, M. M., Cao, W. H., Zhang, H. J. et al. (2019). Properties of soy protein isolate/nano-silica bilayer films during storage. Journal of Food Process Engineering, 42(2), e12984. https://doi.org/10.1111/jfpe.12984 [Google Scholar] [CrossRef]
92. Younes, M., Aggett, P., Aguilar, F., Crebelli, R., Filipic, M. et al. (2017). Re-evaluation of alginic acid and its sodium, potassium, ammonium and calcium salts (E 400-E 404) as food additives. EFSA Journal, 15(11), e05049. [Google Scholar] [PubMed]
93. Sheng, J. J., Li, J. R., Zhao, L. H. (2019). Fabrication of grease resistant paper with non-fluorinated chemicals for food packaging. Cellulose, 26(10), 6291–6302. https://doi.org/10.1007/s10570-019-02504-y [Google Scholar] [CrossRef]
Cite This Article
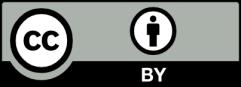