Open Access
ARTICLE
Nanolignin, a Coupling Bio-Agent for Wood-Plastic Composites
1 Department of Wood and Paper Sciences, Faculty of Natural Resources, Semnan University, Semnan, Iran
2 LERMAB, University of Lorraine, Epinal, France
* Corresponding Authors: Hamed Younesi-Kordkheili. Email: ; Antonio Pizzi. Email:
Journal of Renewable Materials 2023, 11(5), 2075-2083. https://doi.org/10.32604/jrm.2023.026706
Received 21 September 2022; Accepted 07 November 2022; Issue published 13 February 2023
Abstract
The influence of nanolignin coupling bio-agent on some characteristics of polypropylene-wood flour composites was studied. Thus, nanolignin was prepared by the acidic method, and then different ratios of it (0, 1, 3 and 5 wt%) were added to a polypropylene-wood flour mixture. After mechanically mixing wood flour, nanolignin, and polypropylene, the mixture was injection molded. ASTM methods were used to measure the structural properties of nanolignin, and prepared composites’ water absorption, thickness swelling, bending modulus, and bending, tensile and impact strengths. Transforming the original lignin to nanolignin did not change the chemical bonds of the material. The addition of nanolignin yielded improved mechanical and physical properties of the composites prepared. Higher strength and dimensional stability are presented by nanolignin-containing composites when comparing them with those prepared with normal lignin. Nanolignin was shown by SEM (Scanning Electron Microscope) observation to be uniformly dispersed within the polymer matrix. Wood polymer composites (WPCs) with nanolignin exhibited comparable properties with the control samples prepared using maleic anhydride polypropylene (MAPP).Keywords
Wood polymer composites (WPCs) are a category of products the market of which is growing. WPCs can be used as flooring, roof gardens, pool covers, city furniture, docks, etc. Although the use of WPC instead of other types of wood-based panels has several advantages, nonetheless the weak compatibility between the polymer and the natural fiber is the main drawback of this type of composite. So far much research has been conducted focusing on the compatibility between the thermoplastic matrix and the natural fibers to enhance the properties of WPCs. It was approved that coupling agents, especially maleic anhydride-grafted polypropylene (MAPP) significantly improve bonding between wood fiber and polymer matrix, and improve the properties of panels prepared [1,2]. However, high cost and toxicity are characteristic of the majority of these coupling agents. Thus, research is now focused on trying to find a good quality, coupling bio-agent for composites based on polymers and natural fibers.
At the same time, lignin is produced yearly by millions of tons in the pulp and paper industry. Among lignin applications, the foremost one is its use in polymer-natural fiber composites as a coupling agent [3,4]. The presence of polar and non-polar sites in the lignin structure, the first being hydrophilic and the second hydrophobic, indicates that it can be used as the coupling agent in WPCs [5,6]. Lignin, however, does not totally meet the required specifications to prepare WPCs as synthetic coupling agents do and needs to be modified. The lignin treatment with ionic liquids found previously [6] showed lignin aptitude to function as a coupling bio-agent and could improve several characteristics of composites of recycled polypropylene-bagasse fiber [6]. However, all ionic liquids are expensive and then increase the price of the composites. Thus, the findings of both green and easier ways to improve lignin performance are needed. Thus, the aim of the work presented here is to find how to improve lignin performance as a WPCs coupling agent in a new way.
The main challenge about the applications of lignin as the coupling agent has been shown by previous work to be complicated by its complex and changeable macromolecular structure [7]. One way to deal with this problem is to convert unordered raw lignin into uniform nanoparticles, which could be promising candidates for various applications. Extensive and recent reviews of the use of nanolignin in nanocomposites exist [7,8]. The control of solvent/anti-solvent reaction conditions such as temperature, pH and lignin concentration has allowed to prepare different morphologies nanoparticles of lignin [9]. Several researchers inferred the potentiality of the use of nanolignin particles as stabilizers, reinforcing additives, antioxidants and nanocarriers. This is due to their advantages of being biocompatible, non-toxic, thermally stable and environmentally durable. Hence, in the present research work, lignin nanoparticles have been used as bio-coupling agents in wood-plastic composites and the properties of the panels so prepared have been investigated.
A number of research groups have already studied how the WPCs properties have been affected by the addition of different coupling agents [10,11]. Nanoparticles’ influence on WPCs properties has also already been the focus of some research [12,13] as well as for other types of resins and composites [14]. Literature information on how nanolignin affects bio-coupling additive natural fiber-polymer composites properties is however lacking. This work then aims to study how some polypropylene-wood flour composites’ properties are affected by the addition of nanolignin.
Polypropylene (PP) with a grade of SI-080 and a melt flow index (MFI) of 10 g/10 min at 190°C was prepared from Tabriz Petro-chemistry. Oven-dried at 103°C for 24 h industrial waste wood flour was sieved to pass 60/40 mesh. Bagasse Soda black liquor at pH = 13.5% and 70% solid content to be used as a lignin source of lignin was obtained from the Pars Company (Haft Tepe, Iran). Lignin was extracted by sulfuric acid. Maleated Polypropylene (MAPP) was obtained from the Kimia Javid Factory (Isfahan, Iran) with a melt flow index (MFI) of 100 gr/10 min (T = 230°C, load = 2.16 kg). 1.1% coupled maleic anhydride was used as a control coupling agent.
2.2.1 Preparation of Nanolignin
1.4 g lignin was dissolved in 50 mL ethylene glycol, the insoluble impurities were removed by filtration after 4 h stirring, and then hydrochloric acid (4.00 cm3, 0.025 mol L−1) was added to the lignin filtrate solution at the rate of 4 drops per min. The solution was dialyzed in a 3 L beaker for three days with water changed three times a day. The lignin nanoparticles were recovered after precipitating in dilute HCl at pH 2, followed by centrifugation and ultrasonic cleaning to achieve neutral pH.
2.2.2 Fourier Transform Infrared Spectrometry (FTIR)
Lignin and nanolignin FTIR spectra were run on a Shimadzu FTIR 8400S (Japan). KBr pellets with 1 mass% of powdered lignin were used to run the spectra in the 400 and 4000 cm−1 range.
Table 1 shows the mechanically mixed mixtures of wood flour, polypropylene (PP), and either lignin or nanolignin or maleated polypropylene were mechanically mixed (HBI System 90, Buchler American Company, Hainesport, USA). These mixes were prepared with a HAAKE mixer (HBI System 90, USA) for 10 min at 40 rpm and 180°C. A laboratory grinder (WIESER, WGLS 200/200, Saint Louis, MO, USA) was then used to grind the mixtures. Specimens from the obtained granulates were then injection molded at 3 MPa and 180°C. The specimens were then stored at 50% relative humidity and 23°C for at least 40 h before testing.
2.2.4 Water Absorption and Thickness Swelling of the Samples
Water absorption and thickness swelling of the panels were measured according to the ASTM D-7031-04 standard. Five specimens from each type of panel were taken and dried in an oven for 24 h at a temperature of 100 ± 3°C. The weight and thickness of dried specimens were measured with an accuracy of 0.001 g and 0.001 mm, respectively. The specimens were then immersed in distilled water for 24 h and kept at a temperature of 20 ± 2°C. The weight and thicknesses of the specimens were then measured after wiping the excess of water from their surface. The values of the water absorption and thickness swelling in percentage were calculated using the following Eqs. (1) and (2) according to the ASTM D-7031-04 standard, respectively:
WA (t) = percentage water absorption (%) at time t; W0 = oven-dried weight; W (t) = weight of specimen at a given immersion time t.
Also, the values of the thickness swelling in percentage were calculated using Eq. (2).
TS(t) = thickness swelling (%) at time t; T0 = initial specimen’s thickness; T(t) = thickness at time t.
The ASTM D790-03 and ASTM D 638 specifications were used for the composites bending and tensile tests on an Instron universal testing machine (Model 1186, High Wycombe, UK). ASTM-D256 was used for the impact tests on an IZOD testing machine with Model Zwick 5102.
2.2.6 Scanning Electron Microscopy (SEM)
Composites morphology was examined by scanning electron microscopy (XL30, Philips, Nijmegen, The Netherlands). Gold sputter coating was applied on the specimen’s fractured surfaces after the bending test. All images were taken at an accelerating voltage of 17 kV.
Nanolignin and lignin FT-IR spectra are shown in Fig. 1. The band assignments are listed in Table 2.
Figure 1: FTIR analysis of lignin and nanolignin
It was found that there are no differences in the chemical structure between the resins with lignin and nanolignin. Since the structure of lignin groups is still the same thus, no real differences should be observed from the FTIR spectra. It means that when lignin particle size is reduced to nanoscale the chemical structure appears to be unchanged. For example, the 2840 cm−1 band related to the C-H bonds and the 3421 cm−1 band related to the O-H stretching are similar in the lignin and nanolignin molecules. Zikeli et al. also analyzed the lignin and nanolignin structures by FTIR spectroscopy and indicated that their spectra are strongly overlapping [15].
3.2 Water Absorption and Thickness Swelling
The lignin and nanolignin composites’ thickness swelling and water absorption are shown in Figs. 2 and 3. They also show that adding to composites a coupling additive based on lignin may decrease its thickness swelling and water absorption. This result can be attributed to physical and chemical effects. Previous researchers indicated that some micro-cracks and voids are present in the composites’ structure [16]. As such micro-cracks are filled by the lignin additive it is then clear that water penetration is prevented. Furthermore, WPCs reduction of thickness swelling and the consequent water absorption by adding lignin is due to lignin’s hydrophobic nature.
Figure 2: Composites water absorption after 24 h in cold water
Figure 3: Composites thickness swelling after 24 h in cold water
Figs. 2 and 3 also show that the composites with nanolignin have lower water absorption and thickness swelling compared to those made from normal lignin. Composites added with 1, 3 and 5 wt% nanolignin presented water absorption 37%, 25% and 16% lower than those treated with unchanged lignin. The composites with lignin nanoparticles presented lower thickness swelling and water absorption in relation to a higher proportion of voids and porous structures filled by the nanoscale particles. Moreover, lignin bonding to natural fibers and polypropylene is improved by the addition of nanoparticles thus improving the panel’s dimension stability. The panels made without lignin nano-coupling additive had the highest water absorption while those with 5 wt% nanolignin had the lowest. The composites containing 5 wt% of nanolignin have lower water absorption (5%) and thickness swelling (4%) than those used from MAPP. Lignin’s coupling additive positive effect on WPCs dimensional stability has been reported by several researchers [17,18].
Table 3 shows the prepared composites bending modulus and bending strength. It appears that adding nanolignin coupling agent improves both the composite bending modulus and bending strength. The highest bending modulus was presented by the composites with 3% nanolignin additive (2841 MPa) as well as bending strength (35 MPa). The lowest bending modulus value (1803 MPa) and bending strength (22 MPa) were presented by the composites without any nanolignin coupling additive. It must be pointed out that at parity of lignin content nanolignin-treated composites presented a higher bending strength than those without any nanolignin but just with untreated lignin (Table 3). The different proportions of reactive sites of the two lignin types caused the differences noticed in the bending strength. Reducing lignin size and improvement in reactive sites appeared to increase cross-linking content between the components of the composite. The higher bending characteristics of nanolignin-treated composites are due to the effective transfer of stresses among polymer and natural fibers. Moreover, the excellent dispersive characteristics of nanolignin improve the bending strength of the composite (Fig. 4). The bending properties of the composite are positively affected by adding MAPP (Table 3).
Figure 4: SEM micrographs of the particleboards prepared with (a) PB composites; (b) PB + nanolignin
Table 3 shows the tensile modulus and strengths of composites. The tensile modulus and tensile strengths of the composite containing lignin nanoparticles were higher than those just added of normal lignin. The composites tensile modulus and strengths were improved by adding up to 5 wt% nanolignin. The bonding power of the surface of the bio-fiber to the polymer markedly influences the composite strength. In other words, the mechanical properties of the composites strongly depend on the compatibility of the wood flour with the polypropylene. The lignin nanoparticles high amount and very high specific surface area, improves the bonding between the elements. Qi et al. also indicated that lignin nanoparticles can efficiently disperse in the polymer matrix and strengthen the interfacial interaction in the composite matrix [19]. They also showed that an overall enhancement for mechanical performance and the elongation at break exceeded 1000% for all studied PU nanocomposites. SEM micrographs of the composites prepared also showed the particles of nanolignin being uniformly dispersed within the polymer matrix (Fig. 4) leading to better transfer of stresses from the polymer to the fibers. The interfacial polymer-lignin adhesion has been found to be excellent [20]. At 2432 and 22 MPa tensile modulus and strength for composites with 3 wt% nanolignin these compared well with the lower 1720 and 15 MPa values for the control. Behrooz et al. used lignin as a coupling agent for wood-plastic composites [5] showing that incorporating lignin in the WPCs yielded a higher-quality composite of comparable properties to those made from MAPP. Based on the present research work findings, the composites’ bending and tensile characteristics were slightly decreased by the increase of nanolignin from 3% to 5% by weight. This reduction is probably due to the aggregation of nanoparticles in the polymer matrix. Adding coupling agents (MAPP) improves the composites’ mechanical strength is also shown by the mechanical test results.
Table 3 also shows the composites’ impact strengths. Adding lignin, MAPP and nanolignin coupling agents to wood flour with PP composites appeared from Table 3 to improve their impact strength with the highest impact strength being reported for the nanolignin-added composites. This is due to the improved adhesion between the wood and polypropylene. The increase in bonding strength causes a better distribution of stress and improves the impact strength of the composites. The nanolignin coupling agent improves the adhesion of the wood flour and the polypropylene matrix at their interface and yields better encapsulated by the plastic of the wood particles thus yielding a better impact strength. The composites with 5 wt% nanolignin had the highest impact strength (1426 J/m2) while the lowest impact strength was presented bt the composite without the coupling agent (800 J/m2). Table 3 shows that the WPCs’ impact strength progressively increases with the progressive increase from 0 to 5 wt% of nanolignin. At the constant level of lignin, the 1, 3 and 5 wt% lignin nanoparticles composites presented 20%, 16% and 10% higher impact strength than with normal lignin.
A nanolignin bio-coupling agent was shown in this work to affect the properties of wood flour with polypropylene composites, yielding the conclusions which follow hereunder:
• There is no difference between the chemical structure of lignin and nanolignin as shown by FTIR spectrometry.
• Progressively increasing from 0 to 5 wt% the proportion of lignin nanoparticles resulted in better dimensional stability and higher mechanical strength.
• Lignin nanoparticles treated WPCs yielded improved dimensional stability and mechanical strength than with unmodified lignin.
• Composites with lignin nanoparticles presented some mechanical and physical characteristics comparable to those with the control sample (MAPP).
• Composites SEM micrographs showed nanolignin being uniformly dispersed in the polymer matrix.
• The results for mechanical and physical characteristics satisfy the relevant standard requirements of composite quality.
Funding Statement: The authors received no specific funding for this study.
Conflicts of Interest: The authors declare that they have no conflicts of interest to report regarding the present study.
References
1. Keener, T. J., Stuart, R. K., Brown, T. K. (2004). Maleated coupling agents for natural fiber composites. Composites Part A: Applied Science and Manufacturing, 35, 357–362. DOI 10.1016/j.compositesa.2003.09.014. [Google Scholar] [CrossRef]
2. Malakani, M., Bazyar, B., Talaiepour, M., Hemmasi, A. (2015). Effect of acetylation of wood flour and MAPP content during compounding on physical properties, decay resistance, contact angle, and morphology of polypropylene/wood flour composites. BioResources, 10, 2113–2129. DOI 10.15376/biores.10.2.2113-2129. [Google Scholar] [CrossRef]
3. Thielemans, W., Wool, R. P. (2004). Butyrated kraft lignin as compatibilizing agent for natural fiber reinforced thermoset composites. Composites Part A: Applied Science and Manufacturing, 35, 327–338. [Google Scholar]
4. Xu, K., Li, K., Zhong, T., Guan, L., Xie, C. et al. (2014). Effect of chitosan as biopolymer coupling agent on the thermal and rheological properties of polyvinyl chloride/wood flour composites. Composite Part B–Engineering, 58, 392–399. DOI 10.1016/j.compositesb.2013.10.056. [Google Scholar] [CrossRef]
5. Behrooz, R., Younesi-Kordkheili, H., Kazemi-Najafi, S. (2012). Physical properties of lignin added wood flour–polypropylene composites: A comparison of direct and solvent mixing technique. Asian Journal of Chemistry, 24, 157–160. DOI 12.3423/Asian23487. [Google Scholar]
6. Younesi-Kordkheili, H., Pizzi, A. (2020). Ionic liquid-modified lignin as a Bio-coupling agent for natural fiber-recycled polypropylene composites. Composite Part B–Engineering, 181, 1–6. DOI 10.1016/j.compositesb.2019.107587. [Google Scholar] [CrossRef]
7. Zhang, Z., Terrasson, V., Guenin, E. (2021). Lignin nanoparticles and their nanocomposites. Nanomaterials, 11(5), 1336. DOI 10.3390/nano11051336. [Google Scholar] [CrossRef]
8. Feldman, D. (2016). Lignin nanocomposites. Journal of Macromolecular Science, Part A, 53, 382–387. DOI 10.1080/10601325.2016.1166006. [Google Scholar] [CrossRef]
9. Chen, Y., Gong, X., Yang, G., Li, Q., Zhou, N. (2019). Preparation and characterization of a nanolignin phenol formaldehyde resin by replacing phenol partially with lignin nanoparticles. RSC Advances, 9, 29255–29262. DOI 10.1039/C9RA04827H. [Google Scholar] [CrossRef]
10. Shen, Z., Ye, Z., Li, K., Qi, C. (2021). Effects of coupling agent and thermoplastic on the interfacial bond strength and the mechanical properties of oriented wood strand–Thermoplastic composites. Polymers, 13, 1–11. DOI 10.3390/polym13234260. [Google Scholar] [CrossRef]
11. Wang, W., Peng, Y., Dong, Y., Wang, K., Li, J. et al. (2018). Effect of coupling agent modified intumescent flame retardant on the mechanical properties, thermal degradation behavior, and flame retardancy of wood-flour/polypropylene composites. Polymer Composites, 39, 826–834. DOI 10.1002/pc.24004. [Google Scholar] [CrossRef]
12. Ashori, A. (2013). Effects of nanoparticles on the mechanical properties of rice straw/polypropylene composites. Journal of Composite Materials, 47(2), 149–154. DOI 10.1177/0021998312437234. [Google Scholar] [CrossRef]
13. Younesi-Kordkeili, H., Rezazadeh, Z., Farsi, M. (2013). Physical, mechanical and morphological properties of polymer composites manufactured from carbon nanotubes and wood flour. Composite Part B–Engineering, 44, 750–755. DOI 10.1016/j.compositesb.2012.04.023. [Google Scholar] [CrossRef]
14. Zhou, X. (2022). Preparation and characterization of waterborne polyurethane with unique nanoparticles by controlling water. Journal of Renewable Materials, 10(6), 1623–1639. DOI 10.32604/jrm.2022.018935. [Google Scholar] [CrossRef]
15. Zikeli, F., Vinciguerra, V., Annibale, A., Capitani, D., Romagnoli, M. et al. (2019). Preparation of lignin nanoparticles from wood waste for wood surface treatment. Nanomaterials, 9, 1–18. DOI 10.3390/nano9020281. [Google Scholar] [CrossRef]
16. Rao, J., Zhou, Y., Fan, M. (2018). Revealing the interface structure and bonding mechanism of coupling agent treated WPC. Polymers, 10, 1–13. DOI 10.3390/polym10030266. [Google Scholar] [CrossRef]
17. Adhikary, K. B., Pang, S., Staiger, M. (2008). Dimensional stability and mechanical behaviour of wood–plastic composites based on recycled and virgin high-density polyethylene (HDPE). Composite Part B–Engineering, 39, 807–815. DOI 10.1016/j.compositesb.2007.10.005. [Google Scholar] [CrossRef]
18. Rozamn, H. D., Kumar, R. N., Abubakr, A. T., Ishak, M. A., Ismail, H. (2000). Effect of lignin as a compatibilizer on the physical properties of coconut fiber-polypropylene composites. European Polymer Journal, 36, 1483–1494. DOI 10.1016/S0014-3057(99)00200-1. [Google Scholar] [CrossRef]
19. Qi, G., Yang, W., Pugila, D., Wang, H., Xu, P. et al. (2020). Hydrophobic, UV resistant and dielectric polyurethane-nanolignin composites with good reprocessability. Materials and Design, 196, 1–11. DOI 10.1016/j.matdes.2020.109150. [Google Scholar] [CrossRef]
20. Kun, D., Pukanszky, B. (2017). Polymer/lignin blends: Interactions, properties, applications. European Polymer Journal, 93, 618–641. DOI 10.1016/j.eurpolymj.2017.04.035. [Google Scholar] [CrossRef]
Cite This Article
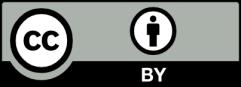