Open Access
ARTICLE
Study on Mechanical Properties of High Fine Silty Basalt Fiber Shotcrete Based on Orthogonal Design
1
State Collaborative Innovation Center of Coal Work Safety and Clean-Efficiency Utilization, School of Civil Engineering, Henan
Polytechnic University, Jiaozuo, 454003, China
2
Provincial Key Laboratory of Underground Engineering and Disaster Prevention and Control, School of Civil Engineering, Henan
Polytechnic University, Jiaozuo, 454003, China
3
School of Civil Engineering, Henan Polytechnic University, Jiaozuo, 454003, China
4
Key Laboratory of Mine Ecological Effects and Systematic Restoration, Ministry of Natural Resources, Beijing, 100081, China
* Corresponding Author: Huazhe Jiao. Email:
Journal of Renewable Materials 2023, 11(8), 3351-3370. https://doi.org/10.32604/jrm.2023.027512
Received 02 November 2022; Accepted 13 January 2023; Issue published 26 June 2023
Abstract
In order to improve the comprehensive utilization rate of high fines sand (HFS) produced by the mine, full solid waste shotcrete (HFS-BFRS) was prepared with HFS as fine aggregate in cooperation with basalt fiber (BF). The strength growth characteristics of HFS-BFRS were analyzed. And the fitting equation of compressive strength growth characteristics of HFS-BFRS under the synergistic effect of multiple factors was given. And based on the orthogonal experimental method, the effects on the compressive strength, splitting tensile strength and flexural strength of HFS-BFRS under the action of different levels of influencing factors were investigated. The effect of three factors on the mechanical properties of HFS-BFRS, 3, and 28 d, respectively, was revealed by choosing the colloidal sand ratio (C/H), basalt fiber volume fraction (BF Vol) and naphthalene high-efficiency water reducing agent (FDN) as the design variables, combined with indoor tests and theoretical analysis. The results show that the sensitivity of the three factors on compressive strength and flexural strength is C/H > FDN > BF Vol, and splitting tensile strength is BF Vol > FDN > C/H. Finally, the fitting ratio of HFS-BFRS was optimized by the factor index method, and the rationality was verified by the field test. For the fluidity of HFS-BFRS, the slump can be improved by 139% under the action of 1.2% FDN, which guarantees the pump-ability of HFS-BFRS.Keywords
Nomenclature
HFS | High-fine silt |
FDN | Naphthalene high-efficiency water-reducing agent |
BF | Basalt fiber |
With the rapid development of China’s infrastructure construction and the strengthening of environmental protection, natural sand resources are gradually in shortage, and to meet the increasing demand for engineering construction, the rock is often mined and mechanically crushed to produce mechanism sand (MS). Compared with natural sand, the production process of MS inevitably produces stone powder with a particle size of less than 75 μm and the same lithology as the parent rock, and its excessive content will affect the cracking resistance and mechanical properties of concrete with MS as fine aggregate, and reduce the durability of concrete [1]. Wind sorting, vibratory screening, and water washing are commonly used in engineering to deal with excessive stone powder [2]. However, this is not only detrimental to the full utilization of MS but also raises its production cost, as well as has many negative impacts on sand resources and environmental protection. Therefore, how to resourcefully utilize high fines sand (HFS) has become a hot topic of concern in the industry.
China Henan Jiaozuo Qianye New Material Co., Ltd. produces a large amount of high fine silt (HFS) in the aggregate production process, with an annual output of about 4 million to 5 million tons. The production process is shown in Fig. 1. Compared with ordinary mechanism sand, the most significant feature of HFS is the relatively high content of fines (mainly limestone powder) with particle size less than 75 μm, which is in the range of 20% to 25%, and poor particle size and unstable mud content. Due to the lack of an in-depth theoretical basis or suitable market conditions, its resource utilization has become a major technical problem, but the large amount of work accumulated in the early stage has also laid an important foundation for the further depth of this study.
Figure 1: Production process of high fine silt
Many scholars at home and abroad have studied the effect of stone powder on concrete properties, and when the stone powder is applied to different types of concrete, its optimal admixture rate has significant differences. Rayed et al. [3] found that the compressive strength was increased from 30 to 41 Mpa when stone powder replaced cementitious materials at a replacement rate of 20%. The physical filling effect of stone powder on the concrete matrix [4] helps to improve the particle packing density of HFS, and the tiny particles are filled in the aggregate gaps as micro-aggregates [5–7], and the strength is improved. At the same time, the friction between the solid particles increases, resulting in an increase in yield stress, plastic viscosity, and thixotropy of the concrete, resulting in a decrease in the concrete slump. Westerholm et al. [8] showed that for cement slurry without HFS, the yield stress and plastic viscosity increased by 125%, 500%, and 100%, 500%, respectively, as the limestone rock flour admixture increased from 13.3% to 26.1%. and 100%, 500%. Schmidt etal. [9] and Moir et al. [10] observed that the stone powder’s morphological effect and filler effect was not favorable for the development of concrete compatibility when the stone powder content exceeded 20%. In addition, Aliabdo et al. [11] and Rodrigues et al. [12] found through their studies that the tensile strength and modulus of elasticity of concrete mixed with high content of stone dust were generally reduced. However, the incorporation of fibers can significantly improve fine aggregate concrete’s tensile strength, crack resistance, and ductility.
With its excellent mechanical properties and environmentally friendly manufacturing process, basalt fiber (BF) is widely used in the field of concrete reinforcement [13–16]. After the incorporation of BF in concrete, a significant yield point in the stress-strain curve appears, and BF at less than 0.3% admixture contributes to the growth of tensile and compressive strength of concrete [17]. SIM [18] showed that BFRC, compared with ordinary concrete, has a high tensile strength of 0.5 to 1.0 times and 3 to 5 times higher elongation. Dias et al. [19] investigated the relationship between BF/concrete fracture toughness and fiber admixture, and the experimental results showed that the ultimate load and ultimate deformation of BF/concrete beams before damage were substantially increased, and the sensitivity to cracking was reduced. Jiao et al. [20] found the effect law of basalt fibers on the toughness of shotcrete with the help of microscopic scanning and obtained the optimum fiber content. At the same time, the network structure formed by the three-dimensional disordered distribution of fibers in the concrete matrix produced a bonding effect, which led to the secondary strengthening of the matrix and reduced the shotcrete resilience.
The orthogonal test is a multi-factor and multi-level experimental design method that can reduce the required tests and optimize the mix ratio to ensure representative test results [21]. Aiming at the raw material system of Qianye’s new material, shotcrete was prepared by using total solid waste aggregate and basalt fiber. Orthogonal experiments studied the mechanical properties of HFS-BFRS with the binder-aggregate ratio (C/H), the volume fraction of basalt fiber (BF), and the content of Naphthalene high-efficiency water-reducing agent (FDN) as factors.
The test cement is P.O42.5 ordinary silicate cement, and the performance index meets the requirements of General Silicate Cement (GB 175-2007). The water the reducing agent is naphthalene, high efficient water-reducing agent, powder, see Fig. 2a. The water reduction rate is 17%. The quick-setting agent is an alkali-free powder quick-setting agent, as is shown in Fig. 2b tested. The initial setting of cement net paste mixed with the quick-setting agent is 2∼3 min, and the final setting is 8∼10 min.
Figure 2: Raw materials for the test
The fiber is 18 mm short-cut BF. See Fig. 2c. Its physicochemical parameters are shown in Table 1. the fine aggregate is high-fine powder sand produced by Qianye New Material, and the fine powder content is 22.2%, composed of stone powder and mud powder. The chemical composition of both is shown in Table 2. The fibers and limestone powder were scanned using the JSM-6390LV SEM introduced by Nippon Electron Corporation, and the results are shown in Fig. 3.
Figure 3: Micro photos of stone powder and fiber morphology
From the SEM image, the stone powder particles are of different sizes, and many small particles adhere to the large particles and are not completely dispersed. The surface morphology of the particles is angular and irregular geometry, and the texture is hard with a clear mineral deconstruction surface. The surface of basalt fiber is smooth overall, but there are defects such as bumps and scratches and stress concentrations may occur at these locations.
The coarse aggregate of shotcrete accounts for a large proportion, which is prone to shrink and crack, thus affecting the strength [22]. Compared with ordinary shotcrete, fine aggregate shotcrete has comprehensive advantages such as low cost, good heat insulation, and durability [23,24]. HFS-related physical performance indexes are shown in Table 3, its MB value is detected in Fig. 4, its particle size distribution is measured in Table 4, and the fluctuation curve of fineness modulus is shown in Fig. 5.
Figure 4: Detection of powder content and MB value
Figure 5: HFS fineness modulus
2.2 Analysis of HFS-BFRS Strength Growth Characteristics
Through the exploratory test carried out in the early stage, the influence trend of water-binder ratio and quick-setting agent on the compressive strength of shotcrete test block with high-fine silt was obtained through comprehensive analysis, as shown in Fig. 6.
Figure 6: Relationship between water-binder ratio, accelerating agent, and compressive strength
It can be seen from Fig. 6 that the compressive strength is negatively correlated with the water-binder ratio, and the compressive strength decreases by 17.8% in 28 d. The high water-binder ratio leads to the migration of free water in the mixture under the action of pore pressure, resulting in the formation of tiny capillary pores, increasing the internal porosity, and then the strength decreases. In addition, with the increase of quick-setting agent dosing, the 28 d compressive strength showed a gradually decreasing trend, and the decreasing trend was gradually slowed down with the increase of quick-setting agent dosing, and the 28 d compressive strength decreased by 13%. This is because the intervention of a quick-setting agent destroys the original setting process of the system and accelerates the hydration of C3A in the early stage, while the normal situation should be C3S hydration to generate early strength, aluminate hydration products compared to silicate hydration products there is a certain instability, the subsequent process may cause crystal transformation, resulting in the appearance of pore holes, affecting the strength. At the same time, the aluminate hydration products formed too quickly in the early hydration are wrapped around the cement, inhibiting further hydration, which in turn leads to late strength decay.
For the 1% admixture of the quick-setting agent, its initial setting time is 8.3 min and the final setting time is 15.5 min, which does not meet the requirements of the standard (GB/T35159-2017). Considering the actual effect and economic benefits, the 2% dose was selected in the subsequent orthogonal test.
Li et al. [25] found that the compressive strength of shotcrete mixed with a quick-setting agent meets the Eq. (1):
where:
To study the strength growth law of HFS-BFRS with different quick-setting agent admixtures, the 1, 7, 14, and 28 d compressive strengths were counted using quick-setting agent admixtures of 2%, 3%, and 4%. The data were fitted using Eq. (1), and the fitted curves are shown in Fig. 7.
Figure 7: Effect of age on the development of compressive strength
As seen in Fig. 7, when using Eq. (1) for fitting, the compressive strength grows faster at the initial stage, and the decreasing trend of the growth rate is obvious with age. The addition of a quick-setting agent greatly improves the early strength of HFS-BFRS. With increasing age, the strength continues to grow, but the decreasing growth rate trend is significant. It can be seen that Eq. (1) can better respond to the strong growth law of HFS-BFRS mixed with a quick-setting agent.
2.3 Strength Growth Characteristics of HFS-BFRS under the Action of Comprehensive Factors
Through the study of the three variables of water binder ratio, quick-setting agent admixture, and age on the compressive strength law of HFS-BFRS, it is concluded that the compressive strength of HFS-BFRS is linearly related to water-cement ratio and quick-setting agent admixture, and exponentially related to age. The final compressive strength prediction model of HFS-BFRS under the three factors was derived in the form of Eqs. (2)–(4).
where:
where:
where:
The influence of quick-setting agent dosage on compressive strength is greatly affected by age, so the quick-setting agent dosage at the same age is considered as a comprehensive effect when fitting the prediction model. The prediction model of HFS-BFRS compressive strength can be expressed as:
where:
The regression curve is obtained by fitting the experimental data with 1stopt software, and the correlation coefficient is 0.967. See Table 5 for model regression parameters.
By introducing the undetermined coefficient of the model into Eq. (5), the fitting equation of HFS-BFRS compressive strength growth characteristics is obtained as follows:
2.4 HFS-BFRS Liquidity Analysis
The moderate amount of stone powder in HFS can increase the fluidity of concrete, and the mechanism of action is expressed as the distribution of stone powder as small particles in the voids between coarse aggregates [26], making it easier for the aggregates to move freely among themselves, i.e., stone powder plays a lubricating role. However, when the stone powder content exceeds 20%, the adsorption of stone powder on the water will reduce free water in the slurry, thus limiting the fluidity of the slurry. Different stone powder contents classify the slurry into three forms, as shown in Fig. 8, the states of cement and fine powder particles in three forms are a. Cement and fine powder particles suspended in water; b. Pores between cement and fine powder particles filled with water; c. Pores between cement and fine powder particles are filled with less water [27]. The porosity between the particles in the slurry can be calculated using Eq. (7), which applies to both forms of a and b.
where:
Figure 8: Physical model of slurry
In addition, the incorporation of basalt fibers increases the viscosity of HFS-BFRS, and a large amount of water and cement is adsorbed on the surface of basalt fibers. At the same time, the mesh structure formed by basalt fibers increased the cohesion of concrete and limited the fluidity and plastic deformation of concrete.
It can be seen that the stone powder (SP) and BF in HFS-BFRS harm the fluidity of HFS-BFRS, while FDN can disperse cement particles by virtue of its comb-like structure through the static repulsion effect, which occurs due to the adsorption of the particle surface or through the spatial site resistance caused by the extension of graft chains from the cement particle surface. For the optimization effect of FDN, this study compared the effect of FDN on the slump of HFS-BFRS at different contents of stone powder with 0% and 1.2% dosing of FDN.
As shown in Fig. 9, the slump of HFS-BFRS with 0% FDN admixture reaches the maximum at about 21% of stone powder content, at which time the slump is 61 mm, and according to the Technical Regulations for Shotcrete Application JGJ/T372-2016, the slump of shotcrete is easy to maintain within 80∼120 mm, which is seen to be unable to meet the requirements of spraying. While for HFS-BFRS mixed with 1.2% FDN, the slump is 95 mm at this time, and the slump is improved by 56%. Compared with the slurry without FDN, the addition of FDN significantly improved the fluidity of HFS-BFRS, and the slump could be increased by up to 139%.
Figure 9: Relationship diagram of FDN, stone powder, and slump
Meanwhile, with the increase of stone powder content, the optimization effect of FDN on slump gradually decreases, because the electrostatic repulsive ability of FDN weakens with the increase of stone powder, and the side chain density of FDN decreases, leading to the weakening of its spatial site resistance.
2.5 HFS-BFRS Production Process
The incorporation method of fibers affects the dispersion of fibers in the concrete. A reasonable incorporation method can make the fiber better dispersed in the concrete and reduce the mixing time [28]. The mainstream fiber incorporation methods are the fiber wrapping method and secondary mixing method, Li et al. [29] compared the effect of the two incorporation methods on the compressive strength and damage of concrete, the mechanical properties of concrete using fiber wrapping method is better than those of secondary mixing method. Therefore, the fiber wrapping method was used in this study, and the test block preparation process is shown in Fig. 10.
Figure 10: Test flow chart
2.6 Orthogonal Experimental Design
Taking C/H, BF, and FDN as factors, the effects of the three factors on the mechanical properties of concrete were compared to find out the optimal mix ratio. The orthogonal table L9(33) was used to arrange the test. The specific factors and levels were shown in Table 6, and the test combination scheme was shown in Table 7.
3.1 Failure Forms of Specimens and Analysis of Experimental Data
The strength of concrete specimens was tested after curing for 3 and 28 d under standard curing conditions. The cube’s uniaxial compressive, splitting tensile, and flexural strength loading rates were 0.5, 0.05, and 0.05 MPa/s, respectively. The dimensions of the specimen and the mechanical test model are shown in Fig. 11. The test results of non-standard specimens were converted according to Eqs. (8)–(10).
Figure 11: Mechanical test
where:
During the destruction of the HFS-BFRS specimen, several cracks appeared along the side of the specimen through the upper and lower surfaces of the specimen, and the fibers were in full contact with the shotcrete. The enhanced surface adhesion effectively prevented the direct spalling of concrete fragments and still showed good integrity after the damage. The damage pattern of the specimen block is shown in Fig. 12.
Figure 12: Failure diagram of a specimen
Uniformly distributed in the BFRS internal fiber lap tandem, forming a structurally stable three-dimensional space-bearing structure to inhibit the generation and development of cracks [30,31]. Immediately after the initial cracking of the test block, the fibers across the crack consume energy through fiber debonding slip work to inhibit crack expansion. At this time, the fibers at the crack can continue to bear the load, and through the role of the bridge and the three-dimensional skeleton will be the uniform transfer of stress to inhibit the matrix Shedding, until the fiber gradually debonding fracture failure, making the BFRS toughness enhanced. Fig. 13 shows the pressure diffusion diagram of BFRS.
Figure 13: Pressure dispersion diagram of basalt fiber shotcrete
3.2 Results of Orthogonal Experiments
The mechanical property test results of nine groups of HFS-BFRS are shown in Fig. 14. Each factor and its corresponding level are evenly distributed. So the results of each factor level are considered as the average of the same level test, and the statistical results of different factor levels reflect the influence of each variable on the performance of HFS-BFRS.
Figure 14: Orthogonal test results
In order to investigate the effects of cement-sand ratio (A), basalt fiber volume fraction (B), and naphthalene-based high-efficiency water-reducing agent (C) on the mechanical properties of concrete, range analysis was conducted on the orthogonal experimental results, as shown in Table 8.
As can be seen from the range values of each factor of test block strength in Table 8, when C/H is between 0.22 and 0.28, FDN is between 1% and 1.5%, and BF Vol is between 0.05% and 0.15%: 1) FDN has a great influence on 3 d compressive strength, R is 3.8 MPa, followed by C/H, R is 3.5 MPa, and BF Vol, R is 2.1 MPa. The main and secondary influencing factors of 28 d compressive strength are C/H > FDN > BF Vol, R is 7.1, 2.9, 2.8 MPa, respectively, which has a greater advantage on 28 d compressive strength C/H. 2) The main influencing factor of 3 d splitting tensile strength is FDN, followed by BF Vol, C/H, and R is 0.7, 0.5, and 0.4 MPa, respectively. BF Vol has the greatest influence on 28 d splitting tensile strength, and R is 0.8 MPa, while FDN and C/H have little influence, and R is 0.4 and 0.2 MPa. 3) 3 d flexural strength is significantly affected by FDN and BF Vol, while C/H has little effect. The flexural strength of 28 d was most significantly affected by C/H.
The idea of range analysis is simple and clear, but it has limitations, and it is impossible to distinguish the experimental results caused by different factor levels or test errors. In this study, the statistical analysis software SPSS was used to conduct ANOVA on the experimental results, and the significant results are shown in Table 9.
According to the P values in Table 9, it can be concluded that: 1) FDN has a highly significant influence on 3 d compressive and splitting tensile strength, and C/H and BF Vol are significant influences. In the 28 d compressive strength, only C/H has a significant effect, and the other effects are not significant. In the 28 d tensile strength, only BF Vol is significant, which is consistent with the range analysis results. 2) 3 d flexural strength is most significantly affected by FDN, followed by BF Vol, while C/H has no significant effect. The 28 d flexural strength was significantly affected by C/H and FDN but not by BF Vol, which was consistent with the range analysis results.
3.5 Analysis of Factor Indicators
To analyze the relationship between factors and mechanical property indexes, the corresponding k values of each factor (k1, k2, k3) were taken as the ordinate, and the level of each factor was taken as the abscissa to make the relationship trend chart between factors and indexes, as shown in Fig. 15.
Figure 15: Trend chart of factor indicators
3.5.1 Compressive Strength Analysis
Fig. 15a shows that the 3 and 28 d compressive strengths first increase and then decrease with the increase of C/H, indicating that the optimal strengthening effect of C/H is not simply linear with the dosage. HFS fine powder can optimize the particle size of cementitious materials to improve the compacting degree of the system [32]. When it exceeds a certain limit, the physical filling effect of fine powder particles on the particle size optimization of cementitious materials is smaller than its dilution effect, which leads to the weakening of the skeleton function of sand particles and the difficulty in maintaining the strength improvement. When C/H is 0.25, the strength reaches its best. In addition, the influence trend of FDN and BF Vol on 3 d compressive strength is similar, which increases first and then decreases. For 28 d compressive strength, FDN and BF Vol are linearly and negatively correlated with each other. According to range analysis, the extreme values of the two are 2.9 and 2.8, respectively, which are relatively small. The optimal combination of early and late compressive strength at a given level is H0.25B0.10F1.2.
3.5.2 Splitting Tensile Strength Analysis
Fig. 15b shows the changing trend of splitting tensile strength. Since BF Vol and C/H are significant influencing factors on the early tensile strength, they show a positive correlation trend on the early and late tensile strength. When BF Vol is 0.15% and C/H is 0.28, the tensile strength reaches the maximum, the 3 d tensile strength increases by 24% and 19%, and the 28 d tensile strength increases by 8% and 34%, respectively. The increase of C/H is conducive to the improvement of its gradation, thus reducing the amount of free water in concrete and the leakage of water enriched on the sand surface in concrete, resulting in the reduction of the thickness of the interfacial transition zone and the enhancement of the splitting tensile strength [33]. With the addition of BF, the generation and development of micro-cracks in the concrete matrix are effectively suppressed, the stress concentration of the crack tip is delayed, the ultimate stress time of concrete is delayed, and the splitting tensile strength is improved. With the increase of FDN content, the early tensile strength first increased and then decreased, reaching the peak value when FDN was 1.2%. According to range analysis and variance analysis, the extreme value of FDN for the late tensile strength was 0.4 MPa, which was not a significant influencing factor. The optimal combination of tensile strength is H0.28B0.15F1.2.
3.5.3 Flexural Strength Analysis
Fig. 15c shows the changing trend of flexural strength. Combined with Table 8, it can be seen that the extreme value of C/H on the early flexural strength is 0.2 MPa, and the curve in the trend chart is relatively gentle. Table 9 shows that C/H has no significant influence on the early flexural strength, while for the later flexural strength, the strength value gradually increases with the increase of C/H, and reaches the maximum when C/H is 0.28. When the FDN increased from 1% to 1.5%, the early and late flexural strength decreased by 14% and 24%, respectively. When BF Vol is increased from 0.05% to 0.15%, the early and late flexural strength can be increased by 15.7% and 6.7%, respectively. Therefore, the optimal combination of flexural strength is H0.28B0.15F1.0.
Carry out on-site spraying experiments with a small shotcrete truck of the enterprise. See Table 10 for the mixed proportion of the spraying test. The size of the injection mold is 460 mm × 460 mm × 120 mm. The air pressure of the jet is controlled at about 0.25 MPa. The water pressure at the nozzle is controlled at about 1 MPa, and the distance between the nozzle and the template is kept at 1 m. And the nozzle is perpendicular to the surface of the template, after spraying, it is covered with plastic film, and the spraying process is shown in Fig. 16. Cutting after 28 d of maintenance of the large plate, the cutting size is 100 mm × 100 mm × 100 mm.
Figure 16: Field injection test diagram
The spring back rate of the injection test was calculated to be about 8.9%. The slurry fluidity was good during the injection process, and there was no pipe-blocking phenomenon. The strength test of the cut cube test block met the design requirements.
1. The compressive strength of HFS-BFRS increases exponentially at the same age, and decreases linearly with the water binder ratio and accelerator dosage. A fitting equation for the growth characteristics of HFS-BFRS compressive strength is proposed with the water binder ratio, accelerator dosage, and age as variables.
2. The addition of Naphthalene high-efficiency water-reducing agent makes up for the deficiency of the working performance of HFS-BFRS, the cohesion and water retention of HFS-BFRS are improved, and the slump can be increased by up to 139%, which not only ensures the mechanical properties of HFS-BFRS but also guarantees its pump-ability and ejection ability.
3. The 3 d strength of HFS-BFRS is greatly affected by FDN, and the strength of HFS-BFRS is mainly affected by C/H when the age reaches 28 d. Specific performance: 3 d splitting tensile strength, flexural strength, FDN > BF > C/H, 3 d pressure resistance, FDN > C/H > BF. 28 d compressive and flexural strength, C/H > FDN > BF, 28 d splitting tensile strength, BF > FDN > C/H.
4. C/H, FDN and BF have significant effects on 3 d compressive strength. When the age reaches 28 d, only C/H is a significant influencing factor, and the optimal ratio is recommended as H0.25B0.10F1.2. BF was the significant influencing factor of splitting tensile strength, and the recommended optimal ratio was H0.25B0.10F1.2. The significant influencing factor of bending strength was FDN, and the optimal mixing ratio was H0.28B0.15F1.0.
5. C/H and compressive strength are not a simple linear relationship, and there will be a limit between the two, beyond which the strength will be weakened. Secondly, BF can improve the three strengths to a certain extent, and the splitting tensile strength is the most obvious increase, up to 24%. At this time, its dosage is 4.07 kg/m³.
6. Through indoor and field tests, the shotcrete prepared with high silt content as fine aggregate and basalt fiber is feasible, which greatly improves the utilization value of high silt content and can provide a reference for similar problems in the future.
Funding Statement: This work was supported by the National Natural Science Foundation of China (51834001, 52104129), a project supported by the China Postdoctoral Science Foundation (2020M672226, 2022T150195), Key Laboratory of Mine Ecological Effects and Systematic Restoration, Ministry of Natural Resources, Open Fund (MEER-2022-09).
Conflicts of Interest: The authors declare that they have no conflicts of interest to report regarding the present study.
References
1. Wang, D., Shi, C., Farzadnia, N., Shi, Z., Jia, H. (2018). A review on effects of limestone powder on the properties of concrete. Construction and Building Materials, 192, 153–166. https://doi.org/10.1016/j.conbuildmat.2018.10.119 [Google Scholar] [CrossRef]
2. Fang, H., Yang, J., Song, Y., Huang, W., Chen, J. (2020). Simulation and experimental study on the stone powder separator of a vertical shaft impact crusher. Advanced Powde Technology, 31(3), 1013–1022. https://doi.org/10.1016/j.apt.2019.12.035 [Google Scholar] [CrossRef]
3. Rayed, A., Omrane, B., Chokri, S., Mohamed Amine, K. (2019). Effects of incorporation of marble powder obtained by recycling waste sludge and limestone powder on rheology, compressive strength, and durability of self-compacting concrete. Advances in Materials Science and Engineering, 2019, 4609353. https://doi.org/10.1155/2019/4609353 [Google Scholar] [CrossRef]
4. He, H., Wang, Y. L., Wang, J. J. (2020). Compactness and hardened properties of machine-made sand mortar with aggregate micro fines. Construction and Building Materials, 250, 118828. https://doi.org/10.1016/j.conbuildmat.2020.118828. [Google Scholar] [CrossRef]
5. Knop, Y., Peled, A., Cohen, R. (2014). Influences of limestone particle size distributions and contents on blended cement properties. Construction and Building Materials, 71, 26–34. https://doi.org/10.1016/j.conbuildmat.2014.08.004 [Google Scholar] [CrossRef]
6. Shen, W. G., Wu, J. L., Du, X. J., Li, Z. T., Wu, D. et al. (2022). Cleaner production of high-quality manufactured sand and ecological utilization of recycled stone powder in concrete. Journal of Cleaner Production, 375, 134146. https://doi.org/10.1016/j.jclepro.2022.134146 [Google Scholar] [CrossRef]
7. Wang, X. H., Zhan, Q. Q., Chen, H., Zhang, Y. S., Zhang, J. H. (2022). The influence of stone powder content on the strength and frost resistance of machine-made sand concrete. Journal of Hefei University of Technology (Natural Science Edition), 45(4), 500–504+525. [Google Scholar]
8. Westerholm, M., Lagerblad, B., Silfwerbrand, J., Forssberg, E. (2008). Influence of fine aggregate characteristics on the rheological properties of mortars. Cement and Concrete Composites, 30(4), 274–282. https://doi.org/10.1016/j.cemconcomp.2007.08.008 [Google Scholar] [CrossRef]
9. Schmidt, M., Harr, K., Boeing, R. (1993). Blended cement according to ENV 197 and experiences in Germany. Cement, Concrete and Aggregates, 45(2). [Google Scholar]
10. Moir, G. K., Kelham, S. (1997). Developments in the manufacturing and use of portland limestone cement. Proceedings of Third CANMET/ACI International Conference. American Concrete Institute (ACI), pp. 172–42. [Google Scholar]
11. Aliabdo, A. A., Abd Elmoaty, A. E. M., Auda, E. M. (2013). Re-use of waste marble dust in the production of cement and concrete. Construction and Building Materials, 50, 28–41. https://doi.org/10.1016/j.conbuildmat.2013.09.005 [Google Scholar] [CrossRef]
12. Rodrigues, D. F., Pan, X. Y., Gencturk, B., Alnaggar, M., Sohail, M. G. et al. (2023). Numerical simulation of the fracture and compression response of self-healing concrete containing engineered aggregates. Cement and Concrete Composites, 136, 104858. https://doi.org/10.1016/j.cemconcomp.2022.104858 [Google Scholar] [CrossRef]
13. Kizilkanat, A. B., Kabay, N., Akyüncü, V., Chowdhury, S., Akça, A. H. (2015). Mechanical properties and fracture behavior of basalt and glass fiber reinforced concrete: An experimental study. Construction and Building Materials, 100, 218–224. https://doi.org/10.1016/j.conbuildmat.2015.10.006 [Google Scholar] [CrossRef]
14. Deng, Y. G., Zhao, B. J., Dai, T. T., Li, G. Q., Li, Y. (2022). Study on the dispersibility of modified basalt fiber and its influence on the mechanical properties of concrete. Construction and Building Materials, 350, 128839. https://doi.org/10.1016/j.conbuildmat.2022.128839 [Google Scholar] [CrossRef]
15. Wang, Y. M., Hu, S. W., Sun, X. P. (2022). Experimental investigation on the elastic modulus and fracture properties of basalt fiber–reinforced fly ash geopolymer concrete. Construction and Building Materials, 338, 127570. https://doi.org/10.1016/j.conbuildmat.2022.127570 [Google Scholar] [CrossRef]
16. Cakir, F. (2021). Evaluation of mechanical properties of chopped glass/basalt fibers reinforced polymer mortars. Case Studies in Construction Materials, 15, e00612. https://doi.org/10.1016/j.cscm.2021.e00612 [Google Scholar] [CrossRef]
17. Song, S., Li, X. L., Wang, Z., Wang, W. M. (2022). Orthogonal experimental and theoretical study on mechanical properties of fiber-reinforced recycled powder concrete. Case Studies in Construction Materials, 17, e01546. https://doi.org/10.1016/j.cscm.2022.e01546 [Google Scholar] [CrossRef]
18. Sim, J., Park, C., Moon, D. Y. (2005). Characteristics of basalt fiber as a strengthing material for concrete structures. Composites Part B, 36(6), 504–512. https://doi.org/10.1016/j.compositesb.2005.02.002 [Google Scholar] [CrossRef]
19. Dias, D. P., Thaumaturgo, C. (2005). Fracture toughness of geopolymeric concretes reinforced with basalt fibers. Cement & Concrete Composites, 27(1), 49–54. https://doi.org/10.1016/j.cemconcomp.2004.02.044 [Google Scholar] [CrossRef]
20. Jiao, H. Z., Zhang, W. X., Yang, Y. X., Chen, X. M., Yang, L. H. (2023). Static mechanical characteristics and meso-damage evolution characteristics of layered backfill under the condition of inclined interface. Construction and Building Materials, 336, 130113. https://doi.org/10.1016/j.conbuildmat.2022.130113 [Google Scholar] [CrossRef]
21. Abbas, Y. M., Iqbal Khan, M. (2016). Fiber–matrix interactions in fiber-reinforced concrete: A review. Arabian Journal for Science and Engineering, 41(4), 1183–1198. https://doi.org/10.1007/s13369-016-2099-1 [Google Scholar] [CrossRef]
22. Wang, J., Zhan, L. F., Zhang, Y. L. (2022). Analysis of mechanical properties of high-performance shotcrete. Journal of Jilin Jianzhu University, 39(3), 47–51. [Google Scholar]
23. Cusson, D., Hoogeveen, T. (2008). Internal curing of high-performance concrete with pre-soaked fine lightweight aggregate for prevention of autogenous shrinkage cracking. Cement and Concrete Research, 38(6), 757–765. https://doi.org/10.1016/j.cemconres.2008.02.001 [Google Scholar] [CrossRef]
24. Shi, J. Y., Tan, J. X., Liu, B. J., Chen, J. Z., Dai, J. D. (2021). Experimental study on full-volume slag alkali-activated mortars: Air-cooled blast furnace slag versus machine-made sand as fine aggregates. Journal of Hazardous Materials, 403, 123983. https://doi.org/10.1016/j.jhazmat.2020.123983 [Google Scholar] [PubMed] [CrossRef]
25. Li, P. L., Yue, L., Ma, H., Yang, X. Y. (2022). Research on influencing factors and growth characteristics of shotcrete strength. Journal of Guangxi University (Natural Science Edition), 47(5), 1174–1183. https://doi.org/10.13624/j.cnki.issn.1001-7445.2022.1174 [Google Scholar] [CrossRef]
26. He, X. Y., Zheng, Z. Q., Yang, J., Su, Y., Wang, T. W. et al. (2020). Feasibility of incorporating autoclaved aerated concrete waste for cement replacement in sustainable building materials. Journal of Cleaner Production, 250, 119455. https://doi.org/10.1016/j.jclepro.2019.119455 [Google Scholar] [CrossRef]
27. Cepuritis, R., Wigum, B. J., Garboczi, E. J. (2014). Filler from crushed aggregate for concrete: Pore structure, specific surface, particle shape and size distribution. Cement and Concrete Composites, 54, 2–16. https://doi.org/10.1016/j.cemconcomp.2014.03.010 [Google Scholar] [CrossRef]
28. Zieliński, K., Olszewski, P. (2005). The impact of basaltic fibre on selected physical and mechanical properties of cement mortar. Betonwerk und Fertigteil-Technik/Concrete Precasting Plant and Technology, 71(3), 28–33. [Google Scholar]
29. Li, X. D., Meng, Q., Wang, W. H., Wang, Q. T. (2019). Effects of basalt fiber admixture amount and admixture method on compressive strength and damage morphology of concrete. Concrete and Cement Products, 4, 55–58. [Google Scholar]
30. Chen, F., Chen, X. (2014). Orthogonal experimental research on strength of concrete reinforced by basalt fiber. Journal of Fuzhou University (Natural Science Edition), 42(1), 134–137. [Google Scholar]
31. Yang, J., Zeng, J. Y., He, X. Y., Hu, H. C., Su, Y. et al. (2021). Eco-friendly UHPC prepared from high volume wet-grinded ultrafine GGBS slurry. Construction and Building Materials, 308, 125057. https://doi.org/10.1016/j.conbuildmat.2021.125057 [Google Scholar] [CrossRef]
32. Kim, J., Na, S., Zhang, W. (2017). Effect of limestone powder and gypsum on the compressive strength mixture design of blast furnace slag blended cement mortar. Journal of Advanced Concrete Technology, 15(2), 67–80. https://doi.org/10.3151/jact.15.67 [Google Scholar] [CrossRef]
33. Zhang, L. Q., Chen, Q., Huang, X., Li, B. X. (2020). Effect of stone powder content on properties of C50 granite machine-made sand concrete. Silicate Bulletin, 39(7), 2154–2158+2177. https://doi.org/10.16552/j.cnki.issn1001-1625.2020.07.019 [Google Scholar] [CrossRef]
Cite This Article
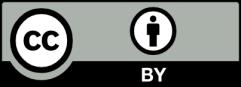