Open Access
ARTICLE
Numerical Analysis of Residual Strength in the Perforated Casing of Ultra Deep Wells
1 Engineering Technology Research Institute of Petro China Xinjiang Oilfield Company, Karamay, 834000, China
2 School of Petroleum Engineering, China University of Petroleum (East China), Qingdao, 266580, China
3 SINOPEC Xinan Oilfield Service Corporation, Deyang, 618000, China
4 SINOPEC Southwest China Oil & Gas Company, Chengdu, 610041, China
* Corresponding Author: Yuqiang Xu. Email:
(This article belongs to the Special Issue: Dynamics and Materials Processing in Petroleum Engineering)
Fluid Dynamics & Materials Processing 2023, 19(1), 261-271. https://doi.org/10.32604/fdmp.2023.020076
Received 02 November 2021; Accepted 22 December 2021; Issue published 02 August 2022
Abstract
A three-dimensional model for the numerical simulation of casing-cement behavior is used to investigate residual strength in the perforated casing of ultra deep wells. The influence of the hole diameter, hole density and phase angle on the residual strength of the casing under non-uniform stress and fracturing conditions is revealed through the consideration of different perforation parameters. It is shown that the residual strength of the casing increases with the hole diameter and periodically changes with the hole density; the phase angle is the main factor that affects the residual strength of the perforated casing, and the perforation should be avoided in the direction of the minimum principal stress to reduce stress concentration at the perforation hole. Moreover, as shown by a companion orthogonal experiment, the descending order of influence of the different influential parameters is: phase angle, hole diameter, hole density and the thickness of casing.Keywords
Cite This Article
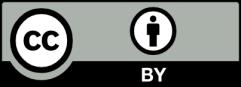