Open Access
ARTICLE
Influence of High-Robustness Polycarboxylate Superplasticizer on the Performances of Concrete Incorporating Fly Ash and Manufactured Sand
1 Macheng Hubei University Research Academy of Industrial Technology, Huanggang, 438300, China
2 Hubei Jueshuo New Material Technology Co., Ltd., Huanggang, 438300, China
3 School of Materials Science and Engineering, Hubei University, Wuhan, 430000, China
4 School of Resources and Environmental Engineering, Wuhan University of Technology, Wuhan, 430070, China
5 School of Civil Engineering, Architecture and Environment, Hubei University of Technology, Wuhan, 430068, China
* Corresponding Authors: Xiulin Huang. Email: ; Jin Yang. Email:
(This article belongs to the Special Issue: Advances in Solid Waste Processing and Recycling Technologies for Civil Engineering Materials)
Fluid Dynamics & Materials Processing 2023, 19(8), 2041-2051. https://doi.org/10.32604/fdmp.2023.027399
Received 27 October 2022; Accepted 14 December 2022; Issue published 04 April 2023
Abstract
Using ethylene glycol monovinyl polyoxyethylene ether, 2-acrylamido-2-methylpropane sulfonic acid (AMPS) and acrylic acid as the main synthetic monomers, a high robustness polycarboxylate superplasticizer was prepared. The effects of initial temperature, ratio of acid to ether, amount of chain transfer agent, and synthesis process on the properties of the superplasticizer were studied. The molecular structure was characterized by GPC (Gel Permeation Chromatography) and IR (Infrared Spectrometer). As shown by the results, when the initial reaction temperature is 15°C, the ratio of acid to ether is 3.4:1 and the acrylic acid pre-neutralization is 15%, The AMPS substitution is 10%, the amount of chain transfer agent is 8%, and the performance of the synthesized superplasticizer is the best. Compared with commercially available ordinary polycarboxylate superplasticizer in C30 concrete prepared with manufactured sand and fly ash, the bleeding rate decreases by 52%, T50 decreases by 1.2 s, and the slump time decreases by 1.1 s. In C60 concrete prepared with fly ash and river sand, the bleeding rate decreases by 46%, T50 decreases by 0.8 s, and the slump time decreases by 3.2 s.Graphical Abstract
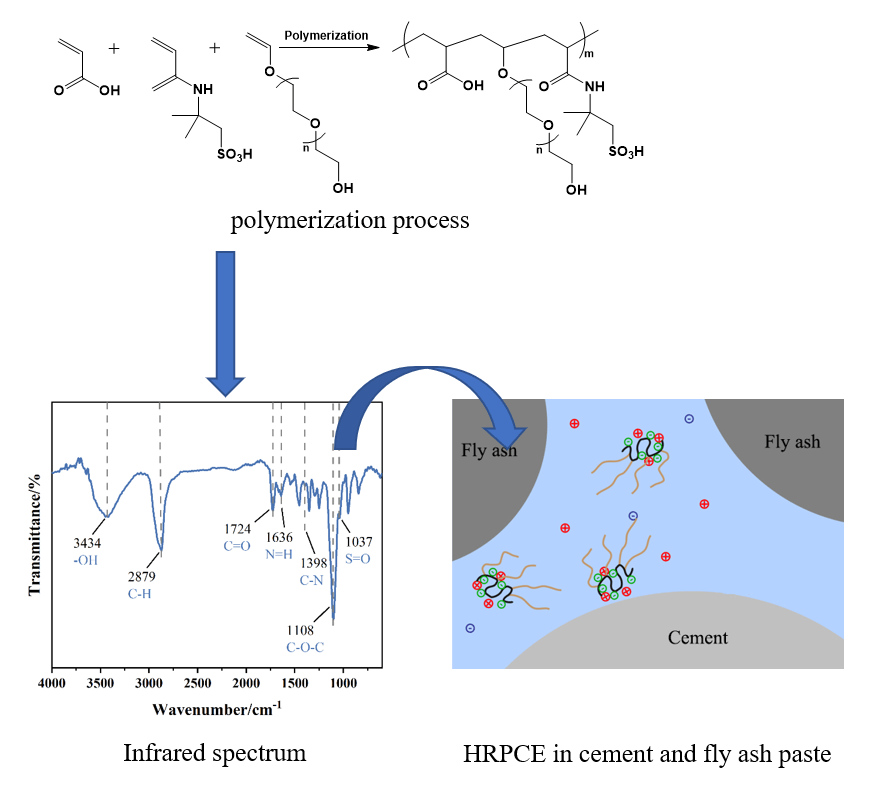
Keywords
Nomenclature
AMPS | 2-acrylamido-2-methylpropane sulfonic acid |
GPC | Gel Permeation Chromatography |
IR | Infrared Spectrometer |
HPEG | Methyl allyl polyethylene glycol ether |
TPEG | Isopentenyl polyethylene glycol ether |
EPEG | Ethylene glycol monovinyl polyethylene glycol ether |
AA | Acrylic acid |
SHP | Sodium hypophosphite |
KPS | Potassium persulfate |
PCE-C | Common water reducer |
HRPCE | High-robustness polycarboxylate superplasticizer |
With the development of modern engineering technology, the super high-rise and long-distance transportation of concrete has become the norm in engineering construction. Higher requirement for the rheological properties of concrete mixture is proposed due to the long distance transportation of concrete in the pump pipe [1,2]. On the other hand, with the gradual scarcity of natural sand, manufactured sand is widely used in concrete production. However, due to the limitations of equipment and technology, the distribution of manufactured sand is often inappropriate, characterized by particles ≥1.18 and ≤0.3 mm content more or 0.3~1.18 mm content less. The intermediate particles of manufactured sand play a crucial role in the encapsulation and cohesion of concrete. The lack of intermediate particles makes concrete prone to bleeding, slurry running, and even segregation, which increases the risk of pump blockage during pumping and threatens the quality of the project [3,4]. Good pumpability requires the concrete mixture to have and maintain good fluidity, small pumping resistance, no segregation, no bleeding, slurry bone coordination and other properties, i.e., high robustness.
Polycarboxylate superplasticizer has become an important part of modern concrete with its excellent dispersion and dispersion retention properties, and greatly affects the working properties of concrete. The decline in the quality of raw materials and the complex and diverse construction status of the engineering environment have posed a huge challenge to the performance of polycarboxylate superplasticizers. As an important raw material in the synthesis of the polycarboxylate superplasticizers, macromolecular monomer polyether has a great impact on the synthesis process and properties of the polycarboxylate superplasticizers. The difference in double bond substituents in the polyether macromonomers will lead to different electron conjugation and induction effects, thus changing the polymerization activity of the double bonds. Polycarboxylate superplasticizers with different properties can be prepared by polyether macromonomers with different polymerization activities, which ultimately affects the performance of the concrete mixtures [5–7]. At present, the polyethers commonly used in the water-reducing agent market are mainly methyl allyl polyethylene glycol ether (HPEG) and isopentenyl polyethylene glycol ether (TPEG). Ethylene glycol monovinyl polyethylene glycol ether (EPEG) is a new type of vinyl ether macromonomer prepared by ethoxylation with ethylene glycol monovinyl ether as the starting agent. Compared with conventional HPEG and TPEG polyether macromonomers, the side chain structure swings more freely and the range of motion is larger. The synthesized polycarboxylate superplasticizer has higher adaptability, low sensitivity, and better slump retention performance. Therefore, it has been widely studied and applied in recent years.
In this paper, a series of polycarboxylate superplasticizers were synthesized by using EPEG as the polyether macromonomer and low temperature initiation technology. The effects of different parameters on the properties of the superplasticizers were studied, and a high robustness polycarboxylate superplasticizer was prepared.
2.1 Raw Materials and Equipment
EPEG (M = 3000), industrial grade; 2-acrylamido-2-methylpropane sulfonic acid (AMPS), industrial grade; Acrylic acid (AA), industrial grade; Sodium hypophosphite (SHP), industrial grade; Potassium persulfate (KPS), industrial grade; Reducing agent, industrial grade; Liquid alkali, 32% sodium hydroxide, laboratory homemade; Ferrous sulfate, analytically pure; Deionized water.
2.1.2 Performance Testing of Raw Materials
Cement, P·O42.5; Fly ash, grade I, 45 μm sieve residue 8%; Manufactured sand, gradation is shown in Table 1, fineness modulus 3.4; River sand, fineness modulus 2.6; Stone, 5–25 mm continuous grading gravel; Tap water; Common water reducer PCE-C, solid content 40%.
Four-necked flask with stirring and water bath device; Peristaltic pump; Electronic balance; Viscotek TDA 305 max gel permeation chromatography; Fourier transform infrared spectrometer (FT-IR) (Tensor27, Bruker Company, Germany); Paste mixer; Concrete mixer; Pressure testing machine.
2.2 Preparation of High Robustness Water Reducer
The EPEG and deionized water were added to a four-port flask equipped with a thermometer and a stirrer and stirred at 15°C until completely dissolved. The chain transfer agent, SHP, and an appropriate amount of the catalyst, ferrous sulfate, were added to the flask and well stirred. Materials A, B, and C were dripped in at the same time. The material A is composed of a certain amount of liquid alkali, AA, AMPS and deionized water, the material B is composed of an appropriate amount of KPS and deionized water, and the material C is composed of an appropriate amount of reducing agent and deionized water. The dropping times of materials A, B, and C were 50, 60, and 60 min, respectively, and the holding time is 1 h after the dropping is completed. Finally, a certain amount of liquid alkali was added to adjust the pH of the system to neutral, and an appropriate amount of deionized water was added to dilute to obtain a high robustness polycarboxylate superplasticizer (HRPCE) with a solids content of 40%. During the preparation process, the amount of catalyst ferrous sulfate, oxidant KPS, and reducing agent were 0.02%, 1.8%, 0.5% of the monomer molar number, respectively. The reaction process is shown in Fig. 1.
Figure 1: Preparation process of high robustness polycarboxylate superplasticizer (HRPCE)
(1) Infrared spectroscopy test: The TEN-SOR27 fourier transform infrared spectrometer produced by Bruker company in Germany was used. The samples were dialyzed and filtered with a semi-permeable membrane to remove impurities. After vacuum drying at 60°C, the samples were mixed with KBr powder and ground.
(2) Gel permeation chromatography analysis: Viscotek TDA 305 max multi-detector gel permeation chromatograph produced by Malvern, UK was used for testing. The mobile phase was 0.1 mol/L sodium nitrate solution, the flow rate was 0.7 mL/min, and the chromatographic column was A-Guard+1x A6000M.
(3) Cement paste fluidity test: according to GB/T8077-2012《concrete admixture homogeneity test method》, water-cement ratio is 0.29, the solid content of water reducer is 0.12%.
(4) Concrete performance test: refer to GB8076-2008《concrete admixture》.
3.1 Synthesis Process Research
3.1.1 Effect of Initial Temperature on the Performance of the Water Reducer
Synthesis temperature determines the half-life of the initiator and monomer polymerization rate, and appropriate synthesis temperature can reduce the chemical reaction barrier so that the reaction conditions are relatively mild while, a too high temperature can easily lead to degradation of the EPEG monomer [8]. Aqueous free radical polymerization is an exothermic reaction. As the reaction proceeds, the system temperature gradually increases, so it is necessary to control the appropriate initial reaction temperature. The effect of initial temperature on the performance of the water reducer was studied by maintaining the same other reaction conditions. The results are shown in Fig. 2.
Figure 2: Effect of initial temperature on the performance of water reducer
When the initial temperature of the reaction is lower than 15°C, the initial dispersion performance of the water reducer is comparable, but the dispersion retention performance increases with increasing temperature. This is because when the reaction temperature is too low, the number of the free radicals produced by the initiator is small, resulting in a decrease in the conversion rate of the system. The unreacted polyether plays a partial dispersion role in the system due to the action of the surfactant. However, due to the small number of water-reducing agent molecules in the system, with the progress of the cement hydration, the water-reducing agent molecules are continuously covered by the hydration products, resulting in a significant decrease of the paste fluidity. When the initial temperature exceeds 15°C, the initial dispersion and dispersion retention properties of the water reducer also decrease. This is because as the temperature increases, the number of free radicals produced by the initiator increases, causing the self-polymerization of the monomer in the system [9]. At the same time, the activity of the chain transfer agent gradually increases, resulting in a decrease in the average molecular weight of the water reducer, thereby reducing the dispersion performance of the water reducer. Therefore, the initial temperature of the selected reaction is 15°C, at which the total temperature rise of the reaction system is 13°C.
3.1.2 Effect of Acid Ether-Ratio on the Performance of the Water Reducer
The EPEG monomer has a higher reactivity than HPEG and TPEG, requiring a lower number of small monomers at the same conversion rate. The initial temperature of the reaction was controlled at 15°C, and the other synthesis conditions were kept the same. The effect of acid-ether ratio on the performance of the water reducer was investigated. The results are shown in Fig. 3.
Figure 3: Effect of acid-ether ratio on the performance of water reducer
With the increase of the acid-ether ratio, the dispersion performance and dispersion retention performance of the water reducer first increase and then decrease. When the acid-ether ratio is 3.4:1, the performance is optimal. This is because when the acid-ether ratio is low, the number of the adsorption groups in the water-reducing agent molecules is small, the adsorption on the surface of the cement particles and the electrostatic repulsion are weak, and the initial dispersion and dispersion retention performance are poor. With the increase of the acid-ether ratio, the proportion of the adsorption groups increased, and the dispersion performance of the water reducer gradually improved. When the acid-ether ratio exceeds a certain value, with the increase of the acid-ether ratio, the side chain density gradually decreases, the thickness of the adsorption layer formed by the superplasticizer on the surface of the cement particles becomes thinner, and the steric hindrance is limited [10]. At the same time, the cement particles with the adsorption layer cannot produce enough electrostatic repulsion when they are close to each other, thus reducing the dispersion performance and dispersion retention performance of the superplasticizer. Therefore, the optimum acid-ether ratio is 3.4:1.
3.1.3 Effect of Chain Transfer Agent on the Performance of the Water Reducer
The chain transfer agent, also known as the molecular weight regulator, is a chemical substance that can transfer free radicals and can be used to control the relative molecular weight of polymers. Studies have shown that the use of a chain transfer agent has no effect on the polymerization rate, and only serves to shorten the length of the polymer chain, that is, to reduce the degree of polymerization of the polymer. The more the amount of the chain transfer agent, the shorter the polymer chain, and the lower the degree of polymerization of the synthesized polymer. The effect of the amount of chain transfer agent on the performance of the water reducer was studied by controlling the initial reaction temperature of 15°C and acid-ether ratio of 3.4:1. The results are shown in Fig. 4.
Figure 4: Effect of chain transfer agent dosage on performance of water reducer
With the increase of the amount of chain transfer agent, the dispersion performance of the water-reducer first increases and then decreases. When the amount of chain transfer agent is 8%, the performance is optimal. This is mainly because when the amount of chain transfer agent is low, the molecular weight of the water-reducing agent is large. At the same chain transfer agent dosage, the number of the molecules is small, and the dispersion ability and dispersion retention ability are poor. With the increase of the amount of chain transfer agent, the molecular weight of the water-reducing agent gradually decreases and the number of molecules increases, which can play a good dispersion effect [11]. However, when the amount of chain transfer agent is too much, it will affect the conversion rate of the reaction system, thus reducing the performance of the water-reducing agent.
3.1.4 Effect of Pre-Neutralization on the Performance of the Water Reducer
Compared with the HPEG and TPEG monomers, the EPEG monomers can polymerize with small monomers in a shorter time. However, because the reaction system is sensitive to temperature, the temperature is released in a short time, which easily causes the temperature of the reaction system to rise sharply and affects the performance of the water reducer. To slow down the reaction rate of the system, reduce the reaction temperature rise rate and improve the conversion rate, some acrylic acid was pre-neutralized by liquid alkali before dropping. The effect of the amount of pre-neutralization on the performance of the water reducer was studied by controlling other reaction conditions. The results are shown in Fig. 5.
Figure 5: Effect of acrylic acid pre-neutralization percentage on the performance of the water reducer
With the increase of the amount of acrylic acid pre-neutralization, the performance of the water reducer first increases and then decreases. When the acrylic acid pre-neutralization is 15%, the performance is optimal. This is mainly because the non-neutralized acrylic acid and EPEG react rapidly under the initiation of the initiator, and the heat release is concentrated, which accelerates the process of the polymerization reaction, resulting in an increase in molecular weight and a decrease in the initial dispersion performance and dispersion retention performance of the water reducer. When the acrylic acid is partially pre-neutralized, the reaction rate is reduced, the heat release is stable, and the performance of the water-reducing agent is improved [12]. However, when the excessive acrylic acid is neutralized, the polymerization activity is reduced, which affects the normal polymerization of the reaction system, reduces the conversion rate of the system, and then affects the overall performance of the water-reducing agent. Therefore, we chose the amount of acrylic acid pre-neutralization of 15%.
3.1.5 Effect of AMPS Substitution Amount on the Performance of the Water Reducer
The AMPS contains shielding amide group, strong anionic and water-soluble sulfonic acid group. Compared with the carboxyl group in the acrylic acid, the adsorption performance of the AMPS is stronger, which makes it have excellent performance. The unsaturated double bond exposed at the end makes it possible to undergo addition polymerization reactions [13]. The introduction of the AMPS into the superplasticizer can improve the performance of the superplasticizer. Keeping other conditions consistent, the effect of the molar number of the AMPS replacing the acrylic acid on the performance of the water reducer was studied. The results are shown in Fig. 6.
Figure 6: Effect of the AMPS substitution on the performance of the water reducer
With the increase of the amount of AA substituted by the AMPS, the initial dispersion performance of the water reducer is gradually improved. This is mainly because the sulfonic acid group in the AMPS has a stronger adsorption capacity than the carboxyl group in the AA, which contributes to its adsorption on the surface of the cement particles. However, it can also be seen that when the substitution amount of the AMPS exceeds 10%, the dispersion ability is not significantly improved, while the dispersion retention ability is greatly reduced. This is mainly beacause when the substitution amount of the AMPS is too large, the polycarboxylic acid molecules are rapidly adsorbed on the surface of the cement particles [14]. With the progress of cement hydration, these polycarboxylic acid molecules are gradually covered by the hydration products, and the remaining effective components of the water reducer in the solution are also reduced, thus reducing the dispersion retention ability of the water reducer.
3.1.6 Determination of the Synthesis Process
From the results of the single factor experiments, the optimal synthesis process for preparing the high robustness polycarboxylate superplasticizer (HRPCE) can be obtained as follows: acid-ether ratio 3.4:1, in which the acrylic acid is 15% pre-neutralized, the acrylic acid replaced by the AMPS by 10%, the amount of the chain transfer agent is 8%, and the initial temperature of the reaction system at 15°C.
3.2 Gel Permeation Chromatography Analysis
The gel permeation chromatograph of the HRPCE is shown in Fig. 7. Table 2 shows its molecular information. It can be seen that the molecular weight of the prepared HRPCE is moderate and evenly distributed.
Figure 7: Gel permeation chromatograph of HRPCE
3.3 Infrared Spectrum Analysis
The infrared spectrum of the HRPCE is shown in Fig. 8. As shown in Fig. 8: 1108 cm−1 is the characteristic absorption peak of the C-O-C, 1724 cm−1 is the stretching vibration peak of the C=O in the carboxyl group, 3434 cm−1 is the stretching vibration peak of the -OH, 2879 cm−1 is the stretching vibration peak of the C-H in the methyl and methylene, 1037 cm−1 is the symmetrical stretching vibration peak of the S=O in the -SO3, 1636 cm−1 is the bending vibration peak of the N-H, 1398 cm−1 is the stretching vibration peak of the C-N. It shows that the acrylic acid and the AMPS have been successfully polymerized with the polyether macromonomers.
Figure 8: Infrared spectrum of the HRPCE
3.4 Application Performance Test of Concrete
Using C30 and C60 concrete (mix ratio is shown in Table 3), as the research object, the prepared HRPCE and commercially available PCE-C were diluted to 10% concentration. Under the same dosage, the effect of the two kinds of water reducer on the performance of the concrete was investigated, and the results are shown in Table 4.
Under the same dosage, the two superplasticizers have basically the same initial dispersion, and the HRPCE has a slight advantage. However, from the working performance of concrete after 1 h, in the C30 and C60 concrete, the HRPCE has obvious advantages in the slump spread, indicating that HRPCE has a better dispersion retention performance. At the same time, the bleeding rate of the C30 concrete prepared with the manufactured sand and fly ash in the HRPCE group decreased by 52%, The T50 decreased by 1.2 s, and the slump time decreased by 1.1 s; the bleeding rate of the C60 concrete prepared with the fly ash and river sand decreased by 46%, the T50 decreased by 0.8 s, and the slump time decreased by 3.2 s, which indicate that the HRPCE has a better workability in the low-grade concrete and high-grade concrete. In addition, due to the introduction of the amide groups in the AMPS, the HRPCE shows certain advantages in the development of early strength of concrete. Good workability and dispersion retention ensure the robustness of the concrete mixture in long distance and super high-rise transportation processes. The aggregate is evenly distributed in the slurry, and the concrete with slurry bone synergy also ensures the quality of the concrete engineering.
A new type of EPEG polyether, acrylic acid and AMPS were used to carry out free radical polymerization in aqueous phase by low temperature initiation technology. Conclusions can be drawn as follows:
1) When the initial reaction temperature is 15°C, the ratio of acid to ether is 3.4:1, and the acrylic acid pre-neutralization is 15%, the AMPS substitution is 10%, the amount of chain transfer agent is 8%, and a high robustness polycarboxylate superplasticizer (HRPCE) was prepared.
2) Gel permeation chromatography showed that the weight average molecular weight of the HRPCE was 35567, the PDI was 1.45, the molecular weight was moderate and the distribution was uniform. Infrared spectroscopy showed that the acrylic acid and AMPS had been successfully polymerized with the polyether macromonomers.
3) The performance of the prepared HRPCE superplasticizer was evaluated by the C30 and C60 concrete. The results showed that the HRPCE had better dispersion retention performance, better concrete workability and robustness than ordinary superplasticizer, and has an advantages of early strength.
Funding Statement: The authors would like to acknowledge the Scientific Research Foundation of Hubei University of Technology (GCRC2020012).
Conflicts of Interest: The authors declare that they have no conflicts of interest to report regarding the present study.
References
1. Li, H., Sun, D., Wang, Z., Huang, F., Yi, Z. et al. (2020). A review on the pumping behavior of modern concrete. Journal of Advanced Concrete Technology, 18(6), 352–363. https://doi.org/10.3151/jact.18.352 [Google Scholar] [CrossRef]
2. Kim, J., Han, S., Choi, B. (2020). Influence of pumping pressure on the viscosity curve and rheological stability of mortar incorporating polycarboxylate. Cement & Concrete Composites, 105, 103419. https://doi.org/10.1016/j.cemconcomp.2019.103419 [Google Scholar] [CrossRef]
3. Altuki, R., Ley, M., Cook, D., Gudimettla, M., Praul, M. (2022). Increasing sustainable aggregate usage in concrete by quantifying the shape and gradation of manufactured sand. Construction and Building Materials, 321(6), 125593. https://doi.org/10.1016/j.conbuildmat.2021.125593 [Google Scholar] [CrossRef]
4. Pilegis, M., Gardner, D., Lark, R. (2016). An Investigation into the use of manufactured sand as a 100% replacement for fine aggregate in concrete. Materials, 9(6), 9060440. https://doi.org/10.3390/ma9060440 [Google Scholar] [PubMed] [CrossRef]
5. Plank, J., Sakai, E., Miao, C. (2015). Chemical admixtures-chemistry, applications and their impact on concrete microstructure and durability. Cement and Concrete Research, 78, 81–99. https://doi.org/10.1016/j.cemconres.2015.05.016 [Google Scholar] [CrossRef]
6. Liu, J., Yu, C., Shu, X., Ran, Q., Yang, Y. (2019). Recent advance of chemical admixtures in concrete. Cement and Concrete Research, 124, 105834. https://doi.org/10.1016/j.cemconres.2019.105834 [Google Scholar] [CrossRef]
7. Dalas, F., Pourchet, S., Nonat, A., Rinaldi, D., Sabio, S. et al. (2015). Fluidizing efficiency of comb-like superplasticizers: The effect of the anionic function, the side chain length and the grafting degree. Cement and Concrete Research, 71, 115–123. https://doi.org/10.1016/j.cemconres.2015.02.001 [Google Scholar] [CrossRef]
8. Chomyn, C., Plank, J. (2019). Impact of different synthesis methods on the dispersing effectiveness of isoprenol etherbased zwitterionic and anionic polycarboxylate (PCE) superplasticizers. Cement and Concrete Research, 119, 113–125. https://doi.org/10.1016/j.cemconres.2019.02.001 [Google Scholar] [CrossRef]
9. Erzengin, S., Kaya, K., Ozkorucuklu, S., Ozdemir, V., Yildirim, G. (2018). The properties of cement systems superplasticized with methacrylic ester-based polycarboxylates. Construction and Building Materials, 2018, 166, 96–109. https://doi.org/10.1016/j.conbuildmat.2018.01.088 [Google Scholar] [CrossRef]
10. Fan, W., Stoffelbach, F., Rieger, J., Regnaud, L., Vichot, A. et al. (2012). A new class of organosilane-modified polycarboxylate superplasticizers with low sulfate sensitivity. Cement and Concrete Research, 42(1), 166–172. https://doi.org/10.1016/j.cemconres.2011.09.006 [Google Scholar] [CrossRef]
11. Lange, A., Plank, J. (2015). Optimization of comb-shaped polycarboxylate cement dispersants to achieve fast-flowing mortar and concrete. Journal of Applied Polymer, 132(37). https://doi.org/10.1002/app.42529 [Google Scholar] [CrossRef]
12. Chen, X., Tang, X., Zhang, C., Lu, X., Guo, H. et al. (2022). Synthesis and property of EPEG-based polycarboxylate ether superplasticizers via RAFT polymerization. Polymer Engineering and Science, 62(9), 2769–2778. https://doi.org/10.1002/pen.26060 [Google Scholar] [CrossRef]
13. Tang, S., Zhu, C., Wang, W., Feng, Z., Lin, H. et al. (2019). Effects of AMPS-NNDMA and polycarboxylate superplasticizer on the adsorption and hydration properties of tricalcium silicate. Journal of Dispersion Science and Technology, 40(11), 1575–1580. https://doi.org/10.1080/01932691.2018.1494604 [Google Scholar] [CrossRef]
14. Uzer, E., Plank, J. (2016). Impact of welan gum stabilizer on the dispersing performance of polycarboxylate superplasticizers. Cement and Concrete Research, 82, 100–106. https://doi.org/10.1016/j.cemconres.2015.12.009 [Google Scholar] [CrossRef]
Cite This Article
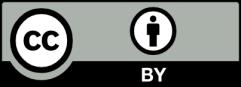