Open Access
ARTICLE
Influence of Trailing-Edge Wear on the Vibrational Behavior of Wind Turbine Blades
1 Mechanical College, Shanghai Dian Ji University, Shanghai, 201306, China
2 College of Energy Engineering, Xinjiang Institute of Engineering, Urumqi, 830091, China
* Corresponding Author: Yuanjun Dai. Email:
Fluid Dynamics & Materials Processing 2024, 20(2), 337-348. https://doi.org/10.32604/fdmp.2023.042434
Received 30 May 2023; Accepted 15 August 2023; Issue published 14 December 2023
Abstract
To study the impact of the trailing-edge wear on the vibrational behavior of wind-turbine blades, unworn blades and trailing-edge worn blades have been assessed through relevant modal tests. According to these experiments, the natural frequencies of trailing-edge worn blades −1, −2, and −3 increase the most in the second to fourth order, the fifth order increases in the middle, and the first order increases the least. The damping ratio data indicate that, in general, the first five-order damping ratios of trailing-edge worn blades −1 and trailing-edge worn blades −2 are reduced, and the first five-order damping ratios of trailing-edge worn blades −3 are slightly improved. The mode shape diagram shows that the trailing-edge worn blades −1 and −2 have a large swing in the tip and the blade, whereas the second- and third-order vibration shapes of the trailing edge-worn blade −3 tend to be improved. Overall, all these results reveal that the blade’s mass and the wear area are the main factors affecting the vibration characteristics of wind turbine blades.Keywords
Wind power is a renewable, clean, and nonpolluting energy source that is primarily collected by wind turbines [1,2]. The blades of a wind turbine are a major component, and ensuring their structural strength is important for normal operation [3]. Wind turbine blades are easily worn by sand particles in deserts and dusty regions while offshore wind turbines are worn by the spray from seawater. Blade wear reduces the energy conversion efficiency of the wind turbine. When air and solid particles rub against the worn area, this causes the blade to vibrate, which can affect the overall operation of the wind turbine in serious cases [4]. Meanwhile, the adhesive strength of the glue-coat on the outer layer of the wind turbine blade is worn down to almost nothing after 5 years of operation. The curvature of the original blade surface and the uneven adhesive force easily lead to surface wear along the edges of the blade tip. The blade section is thinnest at the trailing edge, which also has a small cavity area, so it is easily worn by wind and sand particles. Such wear can induce cracks that propagate along the chord until the beam and then tear the blade apart. Therefore, the influence of trailing-edge wear on the vibration characteristics of wind turbine blades has gained much interest as a research topic.
Ulriksen et al. [5] conducted vibration mode analysis on wind turbine blades with structural damage and found that the vibration mode of damaged blades largely depended on the number of measurement points. However, no further research was performed on the mode shape and rotor dynamic frequency of damaged blades. Tejesh et al. [6] identified damaged blades by circular cracks in the leading edge, which indicated that the centrifugal force generated by blade rotation was the main reason for the increased bending stiffness of the structure. However, they did not analyze the natural frequency, mode shape, and vibration acceleration amplitude of damaged blades under fatigue loading. Ernst et al. [7] studied the influence of damage location on blade modal analysis and proposed a method for identifying different damage locations at a high resolution. However, they did not analyze the dynamic frequency and damping ratio data of damaged blades. Jianwei et al. [8] designed a V-shaped blade tip structure and studied the modal and vibration characteristics. However, they did not consider the modal parameters and vibration characteristics of the V-shaped blade tip structure when worn by particles from the environment. Narayanan et al. [9] used finite element analysis to study the vibration characteristics of wind turbine blades by increasing the number of shape memory alloy lines on the blade. They did not consider the wear condition of the blade surface. Pechlivanoglou et al. [10] studied the influence of distributed roughness on wind turbines, which they used in numerical solutions to predict the aerodynamic performance. However, they did not consider the wear effects of wind and sand on the blade mode shapes and natural frequencies. Lixin et al. [11] studied the effect of wind speed on the erosion and wear of wind turbine blades in a sandstorm environment. However, they only used numerical calculations to simulate the wear of the blade tip at different wind speeds, and they did not study the aerodynamic characteristics, blade mode shape, and natural frequency of the wind turbine blade. Kumar et al. [12] used numerical simulations to analyze the vibration fatigue of blades of small horizontal-axis wind turbines. However, they only used numerical calculations for the fatigue analysis and did not conduct relevant tests for verification. Appadurai et al. [13] used numerical simulations for the vibration analysis of a small-scale wind turbine based on composite materials. They analyzed the displacement and stress data of blades to compare the applicability of different materials, but they did not consider modal parameters such as the dynamic frequency and mode shape of the blades. Papi et al. [14] studied the effects of rain-induced erosion on wind turbines. However, they focused only on the production efficiency and neglected the vibration performance. Mishnaevsky et al. [15] studied the effect of leading-edge erosion on the aerodynamic performance of wind turbine blades. However, they did not analyze the vibration shape and natural frequency of the worn blades.
Thus, the relevant literature on the vibration characteristics of wind turbine blades is relatively in-depth, and most studies have focused on modifying the blade tip structure or blade materials. Vibration and wear analyses have mostly been carried out by numerical simulations without being verified by experimental tests. The vibration characteristics of wind turbine blades worn at the trailing edge by different degrees have received less attention. In this study, the effects of different degrees of wear on the trailing edge of a wind turbine blade on the blade vibration characteristics were investigated. Then, the BK Connect modal analysis software was used to evaluate the natural frequency, damping ratio, and mode shape of the worn blades.
Fig. 1 shows the equipment used for measurement, which included a force hammer (8206-002 rubber head-type power hammer), data acquisition system (LAN-XI series module chassis equipped with a POE Ethernet power supply and data sampling rate of 131 kHz), collection terminal (3053-B-120), accelerometer (type 4507-B-004), and blade chuck.
Figure 1: Test equipment
The transient excitation method was used for the modal test [16]. The tester used the rubber-headed force hammer to excite a blade clamped on the chuck. Eight acceleration sensors attached to the blade surface measured the vibration. This was then converted into an electrical signal and sent to the data acquisition system, which saved the data in a computer. Finally, the mode shape analysis function in the software BK Connect was used to process the signal and extract modal features such as the natural frequency and damping ratio.
2.3 Measurement Points and Measured Objects
In the modal test, the excitation and response of the blade were measured at multiple points. Fig. 2 shows the points of interest on the blade surface. Points 1–8 correspond to the measurement points where the acceleration sensors were attached. Points 9–12 correspond to the points excited by the hammer. During the test, each excitation point was hit five times. In BK Connect, the oscillation frequency was set to 0–400 Hz, and the measurement data were then processed to obtain the damping ratio, natural frequency, and mode shape at each order.
Figure 2: Layout of measurement points for blade modal test
Unworn blades and blades with different degrees of wear on the trailing edge were measured to explore the influence of trailing-edge wear on the static vibration characteristics. The blades were taken from a small wind turbine with a rated power of 100 W and blade radius of 0.65 m. Three blades and an S-series airfoil were used. Table 1 presents the blade parameters. The blade surface was covered with a layer of glass-fiber material to improve the strength of the tested blades. Fig. 3 maps the physical features of unworn and worn blades.
Figure 3: Measured blade
Different types of wear can occur (e.g., abrasive, erosive, adhesive, fatigue, and corrosive), and they have different effects on an object’s surface [17]. In this study, abrasive wear was considered for the trailing edge of the blade. Abrasive wear is mainly caused by the relative displacement of solid particles making contact with the blade, which produces obvious grooves in the surface [18].
Three different degrees of wear at the trailing edge were obtained by grinding: (1) near the tip (r = 2 mm, d = 4 mm), (2) passing through the middle of the tip (r = 4 mm, d = 8 mm), and (3) almost to the leading edge (r = 5.5 mm, d = 11 mm). Here, r is the grinding radius, and d is the grinding height. Fig. 4 shows two-dimensional models of worn blades 1–3.
Figure 4: Blades worn at the trailing edge
Fig. 5 shows the first five orders of natural frequencies of the unworn and worn blades. Overall, the natural frequencies increased with the degree of wear. Compared with the unworn blade, the natural frequencies of the worn blades increased the most at the second to fourth orders, followed by the fifth order and then the first order. Such variations in the natural frequencies will affect the resonance characteristics. A blade resonates when the frequency of the external excitation is equal to its natural frequency. Resonance generally occurs at low frequencies [19]. Therefore, trailing-edge wear will cause the blade to enter resonance earlier than if it was unworn, which will affect the operation of the wind turbine.
Figure 5: First five orders of natural frequencies for each blade
Increasing wear of the trailing edge increased the first-order natural frequency of the blade substantially, which can be attributed to the overall decrease in quality of the blade [20]. The blade is a continuous elastic body, so the natural frequency should be inversely proportional to the mass, which is consistent with the experimental results. When compared with the unworn blade, the natural frequencies of worn blades 1, 2, and 3 increased on average by 96.05%, 120.20%, and 55.56%, respectively. Thus, worn blade 2 showed the most significant change in its natural frequency.
Table 2 lists the first five orders of damping ratios of the blades. For both the unworn and worn blades, the damping ratio generally decreased with increasing order. The damping ratio indicates how the blade attenuates vibration after excitation. A larger damping ratio means a better anti-vibration performance [21]. When compared with the unworn blade, the first five orders of damping ratios of worn blades 1 and 2 decreased on average by 25.12% and 25.91%, respectively [22]. These results indicate that wear of the trailing edge negatively affected the overall vibration characteristics of the wind turbine blade, which would decrease the overall stability of the wind turbine. However, the first five orders of damping ratios for worn blade 3 showed an average increase of 7.29% compared with the unworn blade. This increase in the damping ratio may be attributed to the larger grinding area of worn blade 3, which led to uneven local granular protrusions on the blade surface that increased the roughness of the blade surface. This slightly reduced the vibration response of the wind turbine blade to some extent but did not have a significant impact.
Fig. 6 shows the first five vibration modes of the unworn blade. The first-order mode shape has a small swing at the tip, a larger swing in the leaf, and no obvious vibration at the root. The second-order mode shape has a small swing at the tip and a large swing in the leaf, and the root does not vibrate considerably. The third-order mode shape has a small swing at the tip, large swing at the leaf, and small swing at the root. The fourth- and fifth-order mode shapes are similar. The five vibration modes are relatively regular.
Figure 6: First five vibration modes of the unworn blade
Fig. 7 shows the first five vibration modes of worn blade 1. The first-order mode shape has a small swing at the tip, large swing at the leaf, and small swing at the root. The second-order mode shape has a large swing at the tip, small swing at the leaf, and large swing at the root. The third-order mode shape has a large swing at the tip and small swing at the leaf and root. The fourth-order mode shape has a large swing at the tip, small swing at the leaf, and no obvious vibration at the root. The fifth-order mode is similar to the fourth-order mode shape. Compared with the unworn blade, worn blade 1 has small waves in the first- and second-order mode shapes, a better third-order mode shape at the leaf and root, and large swings at the tip in the fourth- and fifth-order mode shapes. The large swing at the tip indicates a significant reduction in the overall vibration performance of worn blade 1.
Figure 7: First five vibration modes of worn blade 1
Fig. 8 shows the first five vibration modes of worn blade 2. The first-order mode shape has a large swing at the tip and slight waves at the middle and root. The second-order mode shape has a large swing at the tip and small swings at the leaf and root. The third- and fifth-order mode shapes are similar to the second-order mode shape. Compared with the unworn blade, worn blade 2 showed no obvious differences in the first-order mode shape, whereas the second-, fourth-, and fifth-order mode shapes showed a small increase in amplitude at the blade tip and the third-mode shape showed some improvement in the leaf.
Figure 8: First five vibration modes of worn blade 2
Fig. 9 shows the first five vibration modes of worn blade 3. The first-order mode shape has a small swing at the tip, large swing at the leaf, and small swing at the root. The second-order mode shape is similar to the first-order mode shape. The third-order mode shape has a small swing at the tip, large swing at the leaf, and small swing at the root. The fourth-order mode shape has large swings at the tip and leaf and a small swing at the root. The fifth-order mode shape is similar to the third-order mode shape. Compared with the unworn blade, worn blade 3 had a small wave in the first-order mode shape while the second- and third-order mode shapes showed some improvement at the tip and leaf. No significant differences were observed for the fourth- and fifth-order mode shapes.
Figure 9: First five vibration modes of worn blade 3
The analysis of the damping ratio and mode shape indicates that worn blade 3 showed some improvement in the second- and third-order vibration modes, which can mainly be attributed to the larger wear area. However, the overall blade quality was reduced. The improvement in the second- and third-order vibration modes can be attributed to locally uneven granular protrusions in the worn area from grinding, which increased the surface roughness and helped dissipate the vibration energy from the hammer in the form of heat energy.
The natural frequencies, damping ratios, and mode shape diagrams of unworn and worn blades were analyzed to determine the effect of trailing-edge wear on the vibration characteristics. The following conclusions were obtained:
(1) Abrasive trailing-edge wear increases the natural frequency of a blade at a given order, and the increase in frequency is related to the degree of wear.
(2) When compared with the unworn blade, worn blades 1 and 2 showed decreases in the damping ratio. However, worn blade 3 showed an increase in the damping ratio, which improved the vibration performance to some extent.
(3) The vibration mode shapes of worn blades 1 and 2 showed large swings at the tip and leaf, and worn blade 3 showed improvement in the second- and third-order vibration mode shapes.
Overall, trailing-edge wear increased the vibration of the blade from external excitation, which affected the normal operation of the wind turbine. However, the vibration characteristics were also affected by the mass of the blade and wear area of the trailing edge. The results of this study can serve as a reference for future research on design modification and vibration reduction of wind turbine blades.
Acknowledgement: None.
Funding Statement: This study was supported by the National Natural Science Foundation Project (Nos. 51966018 and 51466015) and the Key Research & Development Program of Xinjiang (Grant No. 2022B01003).
Author Contributions: The authors confirm contribution to the paper as follows: study conception and design: Yuanjun Dai, Xin Wei, Cong Wang, Baohua Li, Kunju Shi; data collection: Yuanjun Dai, Xin Wei, Baohua Li; analysis and interpretation of results: Yuanjun Dai, Xin Wei, Baohua Li; draft manuscript preparation: Yuanjun Dai, Xin Wei, Cong Wang, Kunju Shi. All authors reviewed the results and approved the final version of the manuscript.
Availability of Data and Materials: The authors confirm that the data supporting the findings of this study are available within the article.
Conflicts of Interest: The authors declare that they have no conflicts of interest to report regarding the present study.
References
1. Sadorsky, P. (2021). Wind energy for sustainable development, driving factors and future outlook. Journal of Cleaner Production, 289, 125779. [Google Scholar]
2. García Márquez, F. P., Peinado Gonzalo, A. (2021). A comprehensive review of artificial intelligence and wind energy. Archives of Computational Methods in Engineering, 1–24. [Google Scholar]
3. Aihara, A., Kawaguchi, T., Miki, N., Azami, T., Sakamoto, H. (2017). A vibration estimation method for windTurbine blades. Experimental Mechanics, 57(8), 1213–1224. [Google Scholar]
4. Wang, C., Gu, Y. Q. (2022). Research on infrared nondestructive detection of small wind turbine blades. Results in Engineering, 15, 1–9. [Google Scholar]
5. Ulriksen, M. D., Tcherniak, D., Kirkegaard, P. H., Damkilde, L. (2016). Operational modal analysis and wavelet transformation for damage identification in wind turbine blades. Structural Health Monitoring, 15(4), 381–388. [Google Scholar]
6. Tejesh, S., Mohankumar, B., Rajesh, M. (2018). Modeling and analysis of flexural and torsional modes of gas turbine blades considering the foreign object damage. International Journal of Innovative Research and Advanced Studies, 8(5), 66–70. [Google Scholar]
7. Ernst, R., Lauridsen, P., Klein, C., Buffetti, B. (2022). The effect of damage position on operational modal analysis of wind turbine blades for SHM. Journal of Physics: Conference Series, 2265, 032099. [Google Scholar]
8. Zhang, J. W., Dai, Y. J., Li, B. H., Ren, C. Z. (2018). Experimental study on the influence of V-shaped tip structure on structural dynamics of wind turbine. China Test, 44(3), 137–141. [Google Scholar]
9. Narayanan, M. R., Nallusamy, S. (2018). Analysis on vibration characteristics of wind turbine blade to improve the effectiveness through cfd developed by ANSYS. Materials Science Forum, vol. 937, pp. 43–50. Trans Tech Publications, Ltd. [Google Scholar]
10. Pechlivanoglou, G., Fuehr, S., Nayeri, C. N., Paschereit, C. O. (2010). The effect of distributed roughness on the power performance of wind turbines. ASME Turbo Expo: Power for Land, Sea, and Air, 44007, 845–855. [Google Scholar]
11. Zhang, L. X., Sheng, W., Tang, M. L. (2021). Numerical simulation of wind speed on erosion wear of wind turbine blade in aeolian sand environment. Journal of Shenyang Institute of Engineering, 17(1), 5–8. [Google Scholar]
12. Kumar, M. S., Krishnan, A. S., Vijayanandh, R. (2018). Vibrational fatigue analysis of naca 63215 small horizontal axis wind turbine blade. Materials Today: Proceedings, 5(2), 6665–6674. [Google Scholar]
13. Appadurai, M., Fantin, I. R. E., Lurthupushparaj, T. (2022). Sisal fiber-reinforced polymer composite-based small horizontal axis wind turbine suited for urban applications-a numerical study. Emergent Materials, 5(2), 565–578. [Google Scholar]
14. Papi, F., Balduzzi, F., Ferrara, G., Bianchini, A. (2021). Uncertainty quantification on the effects of rain-induced erosion on annual energy production and performance of a multi-MW wind turbine. Renewable Energy, 165, 701–715. [Google Scholar]
15. Mishnaevsky, L., Hasager, C. B., Christian, B., Anna-Maria, T., Fster, S. (2021). Leading edge erosion of wind turbine blades: Understanding, prevention and protection. Renewable Energy, 169, 953–969. [Google Scholar]
16. Ma, J. L., Wang, J. W., Liu, B., Chi, F., Liu, X. F. (2013). Study on the influence of airfoil and blade mounting changes on the natural frequencies of each stage of wind turbine. Journal of Engineering Thermophysics, 34(6), 1069–1073. [Google Scholar]
17. Zhang, T. L., Zhang, Z. M. (1997). Types, mechanisms and tests of surface wear. Journal of Beijing Institute of Graphic Communication, 1997(1), 27–35. [Google Scholar]
18. OuYang, X. K., Jiang, Y. H., Zhou, R. (2004). Development of abrasive wear theory. Water Resources and Electric Power Machinery, 2004(6), 25–28. [Google Scholar]
19. L.Q., AN., Zhou, X. Y., Zhao, H. X., Wang, Z. Q. (2013). Modal analysis of 5 MW wind turbine blades. Journal of Chinese Society of Power Engineering, 33(11), 890–894. [Google Scholar]
20. Dai, Y. J., Zhang, J. W., Ma, J. H. Z. (2018). Experimental study on the influence of V-shaped leaf tip on vibration characteristics of wind turbine. Journal of Engineering Thermophysics, 39(11), 2439–2443. [Google Scholar]
21. Ma, J. L., Wang, J. W., Dong, B., Wei, H. J. (2013). Research on improved method of damping ratio aboutwind wheel. Renewable Energy Resources, 31(10), 65–69. [Google Scholar]
22. Marulo, F., Petrone, G., Dalessandro, V. (2014). Operational modalanalysis on a wind turbine blade. Proceedings of the 26th International Conference on Noise and Vibration Engineering, the 5th International Conference on Uncertainty in Structural Dynamics, pp. 96–108. Leuven, Belgium. [Google Scholar]
Cite This Article
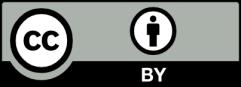