Open Access
ARTICLE
Performance Simulation of a Double Tube Heat Exchanger Based on Different Nanofluids by Aspen Plus
1 Fuel and Energy Technologies Engineering Department, Baghdad Engineering Technical College, Middle Technical University, Baghdad, 10074, Iraq
2 Power Mechanics Techniques Engineering Department, Al-Musaib Technical College, Al-Furat Al-Awsat Technical University (ATU), Kufa, 54001, Iraq
* Corresponding Author: Atheer S. Hassoon. Email:
Frontiers in Heat and Mass Transfer 2024, 22(1), 175-191. https://doi.org/10.32604/fhmt.2023.047177
Received 28 October 2023; Accepted 04 December 2023; Issue published 21 March 2024
Abstract
A heat exchanger’s performance depends heavily on the operating fluid’s transfer of heat capacity and thermal conductivity. Adding nanoparticles of high thermal conductivity materials is a significant way to enhance the heat transfer fluid's thermal conductivity. This research used engine oil containing alumina (Al2O3) nanoparticles and copper oxide (CuO) to test whether or not the heat exchanger’s efficiency could be improved. To establish the most effective elements for heat transfer enhancement, the heat exchangers thermal performance was tested at 0.05% and 0.1% concentrations for Al2O3 and CuO nanoparticles. The simulation results showed that the percentage increase in Nusselt number (Nu) for nanofluid at 0.05% particle concentration compared to pure oil was 9.71% for CuO nanofluids and 6.7% for Al2O3 nanofluids. At 0.1% concentration, the enhancement percentage in Nu was approximately 23% for CuO and 18.67% for Al2O3 nanofluids, respectively. At a concentration of 0.1%, CuO nanofluid increased the LMTD and overall heat transfer coefficient (U) by 7.24 and 5.91% respectively. Both the overall heat transfer coefficient (U) and the heat transfer coefficient (hn) for CuO nanofluid at a concentration of 0.1% increased by 5.91% and 10.68%, respectively. The effectiveness (εn) of a heat exchanger was increased by roughly 4.09% with the use of CuO nanofluid in comparison to Al2O3 at a concentration of 0.1%. The amount of exergy destruction in DTHX goes down as Re and volume fractions go up. Moreover, at 0.05% and 0.1% nanoparticle concentrations, the percentage increase in dimensionless exergy is 10.55% and 13.08%, respectively. Finally, adding the CuO and Al2O3 nanoparticles improved the thermal conductivity of the main fluid (oil), resulting in a considerable increase in the thermal performance and rate of heat transfer of a heat exchanger.Keywords
Nomenclature
LMTD | Log mean temperature difference |
DTHX | Double tube heat exchanger |
CV | Control volume |
NF | Nanofluid |
e.g., | |
Temperature (control volume) (K) | |
Dead state temperature (K) | |
Dead state pressure (N/m2) | |
Velocity of water (m/s) | |
Elevation (m) | |
Specific gravity (-) | |
Enthalpy of water (kJ/kg) | |
Entropy of water (kJ/kg.K) | |
Control volume work (W) | |
Heat capacity (kJ) | |
Nanofluid heat transfer coefficient (W/m2.K) | |
k | Thermal conductivity (W/m.K) |
Re | Reynold number (-) |
Nu | Nusselt number (-) |
Mass flow rate of hot and cold fluid (kg/s) | |
Exergy flow (J/kg) | |
Exergy destruction of double tube heat exchanger (W) | |
Dimensionless of exergy destruction (-) | |
Exergy efficiency of double tube heat exchanger (-) | |
Smaller heat capacity rate (W/K) | |
Specific heat at constant pressure (J/kg.K) | |
ρ | Density (kg/m3) |
ε | Effectiveness of a heat exchanger (-) |
µ | Dynamic viscosity (kg/m·s) |
η | Energy efficiency (%) |
Exergy efficiency (%) | |
n | Nano fluid |
p | Nano particle |
f | Base fluid |
c | Cold |
h | Hot |
0 | Dead state |
dest | Destruction |
ex | Exergy |
Heat exchangers transmit thermal energy between two fluid streams with different temperatures and are thermally insulated by solid boundaries [1]. Active, passive, or combination approaches can be used to increase thermal conductivity in heat exchangers [2]. Vibration, electrical fields, mechanical assistance, and magnetic fields are all examples of active techniques that rely on an external power source to improve heat transfer [3]. Expanded surfaces are used instead of an external power source in passive approaches [4]. Turbulators and nanofluids are common passive techniques [5–7].
Nanofluid adds nanoscale particles less than 100 nm, such as metals, oxides, and carbides, to water, oil, ethylene, and glycol [8]. This combination improves heat exchanger heat transfer. Over the past decade, nanomaterials technology has advanced, resulting in varied nanofluids that can transport heat. Because nanoparticles with strong thermal conductivity are quickly mixed with nanofluids, temperature profiles are modified to increase energy transmission. Due to their improved thermal properties and heat transfer potential, nanofluids have gained significant interest and research (Akyürek et al. [9]). Numerous scholars have studied how nanoparticles in heat exchange fluids improve efficiency. Al Shdaifat et al. [10] used experimental and theoretical methods to analyze CuO nanoparticles, water thermo-physics, and thermal performance. The study found that nanoparticle concentration, composition, and size affect CuO heat transfer with water nanofluids. Mohammed et al. [11] tested parallel and counter flow DTHX using nanofluids with water and nanoparticles like CuO, Al2O3, and TiO2. The study found a favorable link between nanoparticle concentration and heat exchanger performance. Fares et al. [12] tested Al2O3 nanoparticles in water with used volume concentrations at 0.38%, 0.81%, and 1.30%. The trials were done in a circular tube with turbulent flow. According to experimental results, the heat transfer coefficient increased by up to 19% with Al2O3 content. Shahrul et al. [13] examined the thermal performance of Fe3O4, ZnO, TiO2, CuO, and Al2O3 nanoparticles in a shell-and-tube heat exchanger. The study found that ZnO nanofluid had the highest energy efficacy and Al2O3 had the highest heat transfer coefficient. Albadr et al. [14] studied water-based Al2O3 nanofluid convective heat transfer and flow in a horizontal shell and tube. Experimental results showed a little increase in the heat transfer coefficient. Ghozatloo et al. [15] examined shell-and-tube heat exchanger convective heat transfer coefficients. The research focused on graphene/water nanofluids in laminar flow. The convective heat transfer coefficient increased by 35.6% compared to the reference fluid. Darzi et al. [16] studied the Nu and friction factor of aluminum oxide in a double Tube Heat Exchanger (DTHX) from 5000 to 20000 Reynolds numbers. Nanoparticles had 0.25% to 1% volume and an average diameter of 20 nm. The Nu and friction factor increased 19% and 15% compared to pure water, respectively. The authors found that volume fraction increases Nu and pressure decreases. Nanoparticles also have a more significant influence at higher Reynolds numbers. Aghayari et al. [17] examined how aluminum oxide nanofluid affects heat transfer in a double tube heat exchanger (DTHX) from 15000 to 28000 Reynolds numbers. Nanofluid heat transfer was 12% faster than pure water using a counter flow design. Sarafraz et al. [18] used 40–50 nm silver nitrate and green tea leaf nanoparticles. The researchers mixed the compounds (H2O, C2H4 and C2H6O2) to test the friction factor and heat transfer coefficient in DTHX systems. A counter flow design with 1000–11000 Reynolds numbers was used. A maximum 67% increase in heat transfer coefficient was found. Also, the friction factor rose 11.3%. El-Maghlany et al. [19] examined copper nanofluid in a counterflow DTHX with water as the base fluid. Nanoparticles with volume fractions of 1% to 3% and diameters of 63 to 100 nm were used at Reynolds numbers of 2500 to 5000. The researchers found a 23.4% increase in transfer units (NTU) and a 36% increase in pressure decrease compared to water. Ramirez-Tijerina et al. [20] computationally studied nanofluid flow convection in straight tubes and microtubes. Oil of Turbine, ethylene-glycol, and H2O were used with CuO, Al2O3, SiO2, TiO2, and ZnO nanoparticles to test multiple features. The study found that nanoparticle volume concentration increases Nu by up to 16%. Bahiraei et al. [21] and Bahmani et al. [22] found that water, ethylene glycol, kerosene, and oil have poor thermal conductivity. This limits heat transfer device efficiency and performance improvements. Passive heat transmission can be improved by using nanofluids. This technique has grabbed academics’ and researchers’ interest, as shown by Plant et al. [23–25].
Second-law analysis (or exergy analysis), helps improve heat exchanger efficiency. The irreversibility of a system’s interaction with its environment makes energy analysis insufficient. However, exergy analysis reveals a system’s work potential [26,27]. Previous works have studied how techniques with the highest and lowest exergy destruction can improve system performance. Exercise analysis has garnered global attention as a viable green energy topic. Several studies have examined energy and exergy analysis of diverse systems [28], but few have examined exergy analysis in shell and tube heat exchangers. Al-Abbas et al. [29] analyzed shell and helical-coil heat exchanger exergy. The researchers examined how hot and cold-water entry temperatures and mass flow rates affect energy dissipation. The researchers found that reducing cold water flow velocity and increasing Dean number reduced exergy destruction. Thus, energy efficiency increased. Cut-out conical turbulators affected heat transmission, exergy, and pressure loss in a heat exchanger, according to Durmuş [30]. Sadighi Dizaji et al. [31] evaluated how water flow rates (hot or cold), temperature, and geometrical parameters affect exergy loss, dimensionless exergy loss, and exergy efficacy in TTHC heat exchangers. The scientists found a positive association between energy loss and hot or cold-water flow rates, intake temperatures, and coil diameters. Khairul et al. [32] evaluated energy dissipation in a corrugated plate heat exchanger with water-based CuO nanofluids. Experimental results showed nanofluids reduced exergy destruction compared to base fluid. Esfahani et al. [33] examined shell-and-tube heat exchanger energy dissipation using graphene oxide nanofluid. According to the author, graphene oxide nanofluids as the hot fluid reduced energy loss, whether laminar or turbulent.
Based on the previously mentioned research study, it is observed that the researchers only used water on the cold side and nanofluid on the hot side. However, there is a limited emphasis on investigating the utilization of nanofluid when combined with oil to augment the thermal characteristics of oil engines. However, this simulation study examined how alumina (Al2O3) and copper oxide (CuO) nanoparticles in engine oil could improve DTHX performance. This study examined heat exchange between the hot side (oil with nanofluid) and the cold side (H2O) at different Al2O3/CuO nanoparticle mixing ratios. The goal was to uncover heat exchange efficiency-boosting factors. A thorough exergy analysis was also undertaken to assess the efficacy of the proposed methodology on the (DTHX) and to examine how nanofluid volume fractions affect exergy degradation and dimensionless exergy.
2 Nanofluids Thermophysical Properties
A Nanoparticle concentration of CuO and Al2O3 in a base fluid (oil) is used to calculate the nanofluid’s thermophysical characteristics. The thermophysical characteristics of nanoparticles are shown in Table 1. Based on the nanoparticle density (
The predicted value of nanofluid specific heat of nanofluid
where
Kn is the nanofluid thermal conductivity and can be obtained from the following equation [35]:
Note the kp and kf, which are represent the nanoparticles thermal conductivity, respectively.
The nanofluid absolute viscosity µn can be computed as following:
where µf is the fluid viscosity.
The nanoparticle volume fraction is computed by applying the given equations [6].
The Eq. (5) may be reformulated as follows:
where
Table 1 shows the engine oil and nanoparticles (0.05, 0.1) concentrations employed in this study and their thermophysical parameters.
In the present research, a DTHX was examined; the nanofluid (hot side) was circulated inside the inner tube, and water (cool side) was circulated inside the outer shell. In order to evaluate the thermal performance of DTHX, a variety of heat transfer properties are calculated. That makes use of nanofluids in the following ways: The equation given in the cited work [36], can be used to calculate:
where U is the overall heat transfer coefficient (W/m2.
LMTD (logarithm mean temperature difference) can be expressed by:
where
Heat transfer rate Q is established by:
where
The following formula can be used to get the coefficient of heat transfer (
where
The effectiveness (ε) of a DTHX can be calculated using the formula below:
Cmin is a representation of the cold and hot fluid’ s minimum value and equal (
The Nu and Re are two critical parameters in fluid mechanics and heat transfer analysis. The determination of the Re for nanofluid flow can be calculated using the following equations:
where:
According to the second law of thermodynamics [29,36], exergy is the greatest amount of work that must be extracted from a system under the existing conditions. The exergy balance can be represented by the following equation [37]:
In the present investigation, the subsequent equation can be employed to assess the quantity of exergy destruction (referred to as exergy destroyed) inside a specific control volume, as expressed by references [31,37].
The dimensionless exergy loss can be determined [38,39] as:
An exergy or second law efficiency can be calculated for a system like heat exchangers that does neither produce nor input work. It measures how much the process accomplishes its goal based on input availability changes. Second-law efficiency of a heat exchanger is described as the ratio of the actual heat transfer to the maximal heat transfer between the high and low temperature of the fluid stream [38,39].
All Many industrial and power plants use process simulation software like ASPEN PLUS and HYSYS to monitor and evaluate system performance. This study examines adding nanofluids to Aspen Plus process modeling. The algorithm should better forecast how nanofluids would affect simulated operations. This could help study nanofluid effects in thermal energy systems and industrial processes. It may also enable nanofluid use. Metals and water are typically found in simulation system databases. Per Aspen Plus, particle size distribution is micron-scale. Modeling energy systems or processes with nanofluids may be impractical or misleading. Al2O3 and CuO nanoparticles can be used in water, oil, and lubricants. If the nanofluids are properly produced and have stable properties throughout the process, Aspen Plus, a process simulation software, is evaluated for simulation. The steps of simulation can be concluded:
1. Select the add components (water, Al2O3, CuO and Oil).
2. Select property method (Pang Robinson as base method and Steam-TA as water method).
3. Go to simulation, main flow sheet as shown in Figs. 1–3 and input all information data such as (temperature, pressure, mass fraction composition ..., etc.).
4. Run simulation.
5. Result summary.
Figure 1: Aspen plus simulation of the base fluid and corresponding to pure oil in the thermal energy system
Figure 2: Aspen plus simulation of the base fluid and corresponding nanofluid (0.05, 0.1 vol.% Al2O3) in the thermal energy system
Figure 3: Aspen plus simulation of the base fluid and corresponding nanofluid (0.05, 0.1 vol.% CuO) in the thermal energy system
Moreover, this study examines Al2O3 and CuO nanoparticles with oil. This study used fixed factors like temperature, with heated oil at 60°C and cold water at 20°C. Hot oil and cold-water flow rate at 100 and 60 liters per hour, respectively. The heat exchanger’s long was 3240 mm. The tube had a 13.2 mm internal diameter and 20 mm external diameter. A 35-mm-diameter of heat exchanger shell was also used. In contrast, this study examines how nanoparticle concentrations at 0.05% and 0.1% in volume fraction affect heat transfer characteristics. Nu, LMTD, overall and convection heat transfer coefficients, and heat exchanger efficacy are included. An extensive exergy analysis is also performed to determine how nanofluid affects exergy degradation. Fig. 1 shows a simple flowchart created with Aspen Plus for DTHX where heats oil in the first test. Fig. 2 shows a DTHX with NF1 (Al2O3 + Oil). Finally, Fig. 3 refers for DTHX with NF2 (CuO + Oil).
Fig. 4 demonstrates a positive correlation between Nu and Re across various nanoparticle concentrations and pure oil. It should be noted that Nu exhibits an upward trend as the concentration of nanoparticles is increased. The observed enhancement percentages in Nu for the nanofluid consisting of CuO nanoparticles, compared to pure oil, were found to be 9.71% and 23% for nanoparticle concentrations of 0.05% and 0.1%, respectively. While the Al2O3 nanofluid exhibited increases in the Nu of 6.7% and 18.67% at nanoparticle concentrations of 0.05% and 0.1%, respectively. Moreover, Fig. 4 demonstrates that the Nu was 3.32% greater for the 0.05 concentration of CuO nanofluid compared to the 0.05 concentration of Al2O3 nanofluid. Nevertheless, upon comparing the nanofluids containing 0.1 CuO and 0.1 Al2O3, it was observed that the enhancement in the Nu was 4.09% for 0.1 CuO compared to the 0.05 concentration of Al2O3 nanofluid.
Figure 4: Nu vs. Re for different nanofluid and pure oil
The relation between the Re and the LMTD is illustrated in Fig. 5. When comparing nanofluids containing Al2O3 and CuO to pure oil, it was shown that the LMTD increased by 6.67% and 9.37%, respectively. This improvement in LMTD was observed at a nanoparticle concentration of 0.05%. While at a concentration of 0.1%, the enhancement percentages for Al2O3 and CuO, in comparison to pure oil, were found to be 17.3% and 22.35%, respectively. Fig. 5 demonstrates that the LMTD was 3.3% greater for the nanofluid containing 0.05% copper oxide (CuO) compared to the nanofluid containing 0.05% aluminum oxide (Al2O3). Nevertheless, upon comparing the nanofluid containing 0.1 CuO with the nanofluid containing 0.1 Al2O3, it was observed that the LMTD exhibited an enhancement of 7.24 % for 0.1 CuO campard to the 0.05 concentration of Al2O3 nanofluid.
Figure 5: LMTD vs. Re for different nanofluid and pure oil
Fig. 6 shows the correlation between (U) and (Re) for nanofluids with a 0.05% concentration of both CuO and Al2O3 nanoparticles. The observed enhancement in thermal conductivity for CuO nanofluid was found to be more significant than that for Al2O3 nanofluid, which can be attributed to the superior thermophysical characteristics exhibited by CuO nanoparticles in comparison to Al2O3. The CuO thermal conductivity is comparatively higher, leading to an increased nanofluid heat transfer capacity and consequently, a notable enhancement in the overall heat transfer coefficient. At a Re of 1200, the CuO nanofluid exhibited a 3.14% increase in the value of U compared to the Al2O3 nanofluid. Fig. 6 demonstrates a comparable pattern in the overall heat transfer coefficient with a nanoparticle concentration of 0.1%. However, it is noteworthy that the augmentation percentage in the overall heat transfer coefficient (U) for CuO nanofluid was 5.91%, in contrast to Al2O3 nanofluid.
Figure 6: Overall heat transfer coefficient vs. Re for different nanofluid and pure oil
The convective heat transfer coefficient (hn) in the heat exchanger has a direct proportionality to the overall heat transfer coefficient. An increase in convective heat transfer leads to a corresponding rise in the overall heat transfer coefficient. The aforementioned phenomenon is evident in Fig. 7, which illustrates the fluctuation of the average nanofluid heat transfer coefficient (hn) with respect to the Re for nanofluids containing 0.05% concentrations of CuO and Al2O3. The percentage of augmentation in heat transfer for the CuO nanofluid in hn was around 9.33% when compared to that of Al2O3. Fig. 7 further demonstrates that at a concentration of 0.1%, the hn enhancement for the CuO nanofluid was close to 10.68% when compared to the Al2O3 nanofluid.
Figure 7: Average heat transfer coefficient vs. Re for different nanofluid and pure oil
Fig. 8 depicts the relationship between heat exchanger effectiveness and Re for three different fluid compositions: pure oil, 0.05% concentration of CuO nanofluid, and 0.1% concentration of Al2O3 nanofluid. There is a notable enhancement in the effectiveness of heat exchangers when using CuO nanofluid as compared to Al2O3. This can be attributed to the more favorable thermal properties exhibited by CuO nanoparticles in comparison to Al2O3. The heat exchanger effectiveness exhibited an increase of around 3.32% when using a 0.05 concentration of CuO nanofluid, as compared to a 0.05 concentration of Al2O3 nanofluid. In contrast, when the nanofluids containing 0.1% CuO and 0.1% Al2O3 were compared, a notable increase of 4.09% in heat exchanger effectiveness was seen.
Figure 8: DTHX effectiveness vs. Re for different nanofluid and pure oil
The incorporation of copper oxide (CuO) and aluminium oxide (Al2O3) nanoparticles has the potential to enhance the thermal conductivity of the underlying fluid medium, specifically oil. This addition can result in an augmented heat transfer surface area inside the nanofluid, as well as induce turbulence in the flow due to the dispersion of particles. The aforementioned impacts have the potential to greatly augment the rate of heat transfer and improve the thermal performance of the DTHX. Because of this, using nanofluids as the working fluid in heat exchangers is widely recognized as a highly effective strategy for boosting heat transfer.
Exergy dimensionless, destruction and efficiency over Re is studied for each scenario at various nanofluid concentration to evaluate system performance. The dimensionless exergy destruction against Re for various nanofluid concentration are drawing in Fig. 9. Exergy destruction is a quantifiable measure of energy breakdown in the (DTHX) because it provides a clear indication of the quantity of possible work wasted during a process. The results show that when Re and volume fractions increase, the exergy destruction in DTHX reduces, and the percentage increase in dimensionless exergy in DTHX is 10.55% and 13.08%, respectively, at 0.05% and 0.1% nano particles concentrations.
Figure 9: Dimensionless exergy vs. Re for different nanofluid and pure oil
Similar behavior can be gotten in Fig. 10 for exergy destruction. This demonstrates that using nanofluids in DTHX reduces energy waste and boosts productivity.
Figure 10: Exergy destruction vs. Re for different nanofluid and pure oil
Fig. 11 illustrates the comparative analysis of exergy efficiency in relation to Re for various nanofluids and pure oil. The simulation results shown that the utilization of nanofluid at various concentrations yields higher exergy efficiency values in comparison to the absence of nanofluid (pure oil). The study observed an increase in exercise exergy efficiency in DTHX of 19% and 24.45% for nanoparticle doses of 0.05% and 0.1%, respectively.
Figure 11: Exergy efficiency vs. Re for different nanofluid and pure oil
According to the results, it appears that the addition of CuO and Al2O3 nanoparticles to the basic fluid (oil) can significantly increase the thermal performance of the DTHX. The use of nanofluids in heat exchangers is the most promising strategy for boosting heat transfer due to their improved transfer characteristics. Important findings from the current research include:
1. Compared to pure oil, nanofluids with 0.05% particle concentration increased Nusselt number (Nu) by 9.71% for CuO and 6.7% for Al2O3. Similarly, at a concentration of 0.1%, the percentage increase in Nu was nearly 23% for CuO nanofluids and 18.67% for Al2O3 nanofluids.
2. The percentage increase in LMTD for CuO nanofluid was 7.24% when compared to Al2O3 at 0.1% concentration.
3. The percentage increase in heat transfer coefficient (
4. The augmentation percentage in total overall heat transfer coefficient (
5. The CuO nanofluid improved heat exchanger effectiveness (
6. The exergy destruction in the double tube heat exchanger (DTHX) reduces with rising Re and volume fractions, with 10.55% and 13.08% enhancement percentages in dimensionless exergy in (DTHX) at nanoparticle concentrations of 0.05% and 0.1%, respectively.
Acknowledgement: The authors would like to acknowledge to the respected editors of Frontiers in Heat and Mass Transfer (FHMT) and the respected reviewers for their comments that clearly enhance the manuscript. Also, the authors would like to thank the Power Mechanics Engineering Department at the Technical College of Al-Musaib and Fuel and Energy Department at Technical College of Baghdad for their support.
Funding Statement: The authors received no specific funding for this study.
Author Contributions: The authors confirm their contribution to the paper as follows: study conception and design: Fawziea M. Hussien; data collection: Atheer S. Hassoon, Fawziea M. Hussien; analysis and interpretation of results: Atheer S. Hassoon, Fawziea M. Hussien, Ghaidaa M. Ahmed; draft manuscript preparation: Atheer S. Hassoon. All authors reviewed the results and approved the final version of the manuscript.
Availability of Data and Materials: The data that support the findings of this study are openly available at this link https://iieta.org/journals/ijht/paper/10.18280/ijht.410314, in reference [37].
Conflicts of Interest: The authors declare that they have no conflicts of interest to report regarding the present study.
References
1. Liu, S., Sakr, M. (2013). A comprehensive review on passive heat transfer enhancements in pipe exchangers. Renewable and Sustainable Energy Reviews, 19, 64–81. https://doi.org/10.1016/j.rser.2012.11.021 [Google Scholar] [CrossRef]
2. Thapa, S., Samir, S., Kumar, K., Singh, S. (2021). A review study on the active methods of heat transfer enhancement in heat exchangers using electroactive and magnetic materials. Materials Today: Proceedings, 45, 4942–4947. https://doi.org/10.1016/j.matpr.2021.01.382 [Google Scholar] [CrossRef]
3. Bhattacharyya, S., Vishwakarma, D. S., Srinivasan, A., Soni, M. K., Goel, V. et al. (2022). Thermal performance enhancement in heat exchangers using active and passive techniques: A detailed review. Journal of Thermal Analysis and Calorimetry, 147(17), 9229–9281. https://doi.org/10.1007/s10973-021-11168-5 [Google Scholar] [CrossRef]
4. Kapıcıoğlu, A., Esen, H. (2020 January). Experimental investigation on using Al2O3/ethylene glycol-water nano-fluid in different types of horizontal ground heat exchangers. Applied Thermal Engineering, 165, 114559. https://doi.org/10.1016/j.applthermaleng.2019.114559 [Google Scholar] [CrossRef]
5. Khoshvaght-Aliabadi, M., Khoshvaght, M., Rahnama, P. (2016). Thermal-hydraulic characteristics of plate-fin heat exchangers with corrugated/vortex-generator plate-fin (CVGPF). Applied Thermal Engineering, 98, 690–701. https://doi.org/10.1016/j.applthermaleng.2015.12.135 [Google Scholar] [CrossRef]
6. Wijayanta, A., Pranowo, Mirmanto, Kristiawan, B., Aziz, M. (2019). Internal flow in an enhanced tube having square-cut twisted tape insert. Energies, 12(2), 306. https://doi.org/10.3390/en12020306 [Google Scholar] [CrossRef]
7. Duangthongsuk, W., Wongwises, S. (2010). An experimental study on the heat transfer performance and pressure drop of TiO2-water nanofluids flowing under a turbulent flow regime. International Journal of Heat and Mass Transfer, 53(1–3), 334–344. https://doi.org/10.1016/j.ijheatmasstransfer.2009.09.024 [Google Scholar] [CrossRef]
8. Kirubadurai, B. (2014). Heat transfer enhancement of nano fluids-a review. International Journal of Research in Engineering and Technology, 3(7), 483–486. https://doi.org/10.15623/ijret.2014.0307083 [Google Scholar] [CrossRef]
9. Akyürek, E. F., Geliş, K., Şahin, B., Manay, E. (2018). Experimental analysis for heat transfer of nanofluid with wire coil turbulators in a concentric tube heat exchanger. Results in Physics, 9, 376–389. https://doi.org/10.1016/j.rinp.2018.02.067 [Google Scholar] [CrossRef]
10. Al Shdaifat, M. Y., Zulkifli, R., Sopian, K., Salih, A. A. (2020). Thermal and hydraulic performance of CuO/water nanofluids: A review. Micromachines, 11(4), 416. https://doi.org/10.3390/mi11040416 [Google Scholar] [PubMed] [CrossRef]
11. Mohammed, B., Hasan, M. F., Urtekin, L. (2022). Thermal performance investigation of double pipe heat exchanger embedded with extended surfaces using nanofluid technique as enhancement. SSRN Electronic Journal. https://doi.org/10.2139/ssrn.4313033 [Google Scholar] [CrossRef]
12. Fares, M., AL-Mayyahi, M., AL-Saad, M. (2020). Heat transfer analysis of a shell and tube heat exchanger operated with graphene nanofluids. Case Studies in Thermal Engineering, 18, 100584. https://doi.org/10.1016/j.csite.2020.100584 [Google Scholar] [CrossRef]
13. Shahrul, I. M., Mahbubul, I. M., Saidur, R., Khaleduzzaman, S. S., Sabri, M. F. M. et al. (2014). Effectiveness study of a shell and tube heat exchanger operated with nanofluids at different mass flow rates. Numerical Heat Transfer, Part A: Applications, 65(7), 699–713. https://doi.org/10.1080/10407782.2013.846196 [Google Scholar] [CrossRef]
14. Albadr, J., Tayal, S., Alasadi, M. (2013). Heat transfer through heat exchanger using Al2O3 nanofluid at different concentrations. Case Studies in Thermal Engineering, 1(1), 38–44. https://doi.org/10.1016/j.csite.2013.08.004 [Google Scholar] [CrossRef]
15. Ghozatloo, A., Rashidi, A., Shariaty-Niassar, M. (2014). Convective heat transfer enhancement of graphene nanofluids in shell and tube heat exchanger. Experimental Thermal and Fluid Science, 53, 136–141. https://doi.org/10.1016/j.expthermflusci.2013.11.018 [Google Scholar] [CrossRef]
16. Darzi, A. R., Farhadi, M., Sedighi, K. (2013). Heat transfer and flow characteristics of Al2O3-water nanofluid in a double tube heat exchanger. International Communications in Heat and Mass Transfer, 47, 105–112. https://doi.org/10.1016/j.icheatmasstransfer.2013.06.003 [Google Scholar] [CrossRef]
17. Aghayari, R., Maddah, H., Ashori, F., Hakiminejad, A., Aghili, M. (2014). Effect of nanoparticles on heat transfer in mini double-pipe heat exchangers in turbulent flow. Heat and Mass Transfer, 51(3), 301–306. https://doi.org/10.1007/s00231-014-1415-0 [Google Scholar] [CrossRef]
18. Sarafraz, M., Hormozi, F. (2015). Intensification of forced convection heat transfer using biological nanofluid in a double-pipe heat exchanger. Experimental Thermal and Fluid Science, 66, 279–289. https://doi.org/10.1016/j.expthermflusci.2015.03.028 [Google Scholar] [CrossRef]
19. El-Maghlany, W. M., Hanafy, A. A., Hassan, A. A., El-Magid, M. A. (2016). Experimental study of Cu-water nanofluid heat transfer and pressure drop in a horizontal double-tube heat exchanger. Experimental Thermal and Fluid Science, 78, 100–111. https://doi.org/10.1016/j.expthermflusci.2016.05.015 [Google Scholar] [CrossRef]
20. Ramirez-Tijerina, R., Rivera-Solorio, C., Singh, J., Nigam, K. (2018). Numerical study of heat transfer enhancement for laminar nanofluids flow. Applied Sciences, 8(12), 2661. https://doi.org/10.3390/app8122661 [Google Scholar] [CrossRef]
21. Bahiraei, M., Naghibzadeh, S. M., Jamshidmofid, M. (2017). Efficacy of an eco-friendly nanofluid in a miniature heat exchanger regarding to arrangement of silver nanoparticles. Energy Conversion and Management, 144, 224–234. https://doi.org/10.1016/j.enconman.2017.04.076 [Google Scholar] [CrossRef]
22. Bahmani, M. H., Akbari, O. A., Zarringhalam, M., Ahmadi Sheikh Shabani, G., Goodarzi, M. (2019). Forced convection in a double tube heat exchanger using nanofluids with constant and variable thermophysical properties. International Journal of Numerical Methods for Heat & Fluid Flow, 30(6), 3247–3265. https://doi.org/10.1108/hff-01-2019-0017 [Google Scholar] [CrossRef]
23. Plant, R. D., Saghir, M. Z. (2021). Numerical and experimental investigation of high concentration aqueous alumina nanofluids in a two and three channel heat exchanger. International Journal of Thermofluids, 9, 100055. https://doi.org/10.1016/j.ijft.2020.100055 [Google Scholar] [CrossRef]
24. Alhajaj, Z., Bayomy, A., Saghir, M. (2020). A comparative study on best configuration for heat enhancement using nanofluid. International Journal of Thermofluids, 7–8, 100041. https://doi.org/10.1016/j.ijft.2020.100041 [Google Scholar] [CrossRef]
25. Al Kalbani, K. S., Rahman, M., Ziad Saghir, M. (2020). Entropy generation in hydromagnetic nanofluids flow inside a tilted square enclosure under local thermal nonequilibrium condition. International Journal of Thermofluids, 5–6, 100031. https://doi.org/10.1016/j.ijft.2020.100031 [Google Scholar] [CrossRef]
26. Hossain, S., Chowdhury, H., Chowdhury, T., Ahamed, J. U., Saidur, R. et al. (2020). Energy, exergy and sustainability analyses of Bangladesh’s power generation sector. Energy Reports, 6, 868–878. https://doi.org/10.1016/j.egyr.2020.04.010 [Google Scholar] [CrossRef]
27. Razzaq, M. A., Ahamed, J. U., Hossain, M. M. (2020). Effect of TiO2/MO nano-lubricant on energy and exergy savings of an air conditioner using blends of R22/R600a. International Journal of Automotive and Mechanical Engineering, 17(4), 8283–8297. https://doi.org/10.15282/ijame.17.4.2020.06.0626 [Google Scholar] [CrossRef]
28. Gojak, M., Bajc, T. (2021). Thermodynamic sustainability assessment for residential building heating comparing different energy sources. Science and Technology for the Built Environment, 28(1), 73–83. https://doi.org/10.1080/23744731.2021.1908043 [Google Scholar] [CrossRef]
29. Al-Abbas, A. H., Mohammed, A. A., Hassoon, A. S. (2020). Exergy analysis of shell and helical coil heat exchanger and design optimization. Heat and Mass Transfer, 57(5), 797–806. https://doi.org/10.1007/s00231-020-02993-9 [Google Scholar] [CrossRef]
30. Durmuş, A. (2004). Heat transfer and exergy loss in cut out conical turbulators. Energy Conversion and Management, 45(5), 785–796. https://doi.org/10.1016/s0196-8904(03)00186-9 [Google Scholar] [CrossRef]
31. Sadighi Dizaji, H., Khalilarya, S., Jafarmadar, S., Hashemian, M., Khezri, M. (2016). A comprehensive second law analysis for tube-in-tube helically coiled heat exchangers. Experimental Thermal and Fluid Science, 76, 118–125. https://doi.org/10.1016/j.expthermflusci.2016.03.012 [Google Scholar] [CrossRef]
32. Khairul, M., Alim, M., Mahbubul, I., Saidur, R., Hepbasli, A. et al. (2014). Heat transfer performance and exergy analyses of a corrugated plate heat exchanger using metal oxide nanofluids. International Communications in Heat and Mass Transfer, 50, 8–14. https://doi.org/10.1016/j.icheatmasstransfer.2013.11.006 [Google Scholar] [CrossRef]
33. Esfahani, M. R., Languri, E. M. (2017). Exergy analysis of a shell-and-tube heat exchanger using graphene oxide nanofluids. Experimental Thermal and Fluid Science, 83, 100–106. https://doi.org/10.1016/j.expthermflusci.2016.12.004 [Google Scholar] [CrossRef]
34. Nazarzade, S., Ghorbani, H. R., Jafarpourgolroudbary, H. (2019). Synthesis, preparation and the experimental study of silver/water nanofluid to optimize convective heat transfer in a shell and tube heat exchanger. Inorganic and Nano-Metal Chemistry, 49(6), 173–176. https://doi.org/10.1080/24701556.2019.1606827 [Google Scholar] [CrossRef]
35. Davarnejad, R., Barati, S., Kooshki, M. (2013). CFD simulation of the effect of particle size on the nanofluids convective heat transfer in the developed region in a circular tube. SpringerPlus, 2(1), 192. https://doi.org/10.1186/2193-1801-2-192 [Google Scholar] [PubMed] [CrossRef]
36. Hussien, F. M., Faraj, J. J., Hamad, A. J. (2021). Experimental investigation of double pipe heat exchanger performance based on alumina and copper oxide working nanofluids. IOP Conference Series: Materials Science and Engineering, 1105(1), 012061. https://doi.org/10.1088/1757-899x/1105/1/012061 [Google Scholar] [CrossRef]
37. Hussien, F. M., Hassoon, A. S., Faraj, J. J. (2023). Performance analysis of a triple pipe heat exchanger with phase change materials for thermal storage. International Journal of Heat and Technology, 41(3), 619–628. https://doi.org/10.18280/ijht.410314 [Google Scholar] [CrossRef]
38. Das, U. D., Hossain, M. A. M., Ahamed, J. U., Razzaq, M. E. A. (2022). Heat transfer and exergy analysis of a shell and tube heat exchanger using PGW based ZnO nanofluids. International Journal of Automotive and Mechanical Engineering, 19(2), 9773–9789. https://doi.org/10.15282/ijame.19.2.2022.12.0754 [Google Scholar] [CrossRef]
39. Tavousi, E., Perera, N., Flynn, D., Hasan, R. (2023). Numerical investigation of laminar heat transfer and fluid flow characteristics of Al2O3 nanofluid in a double tube heat exchanger. International Journal of Numerical Methods for Heat & Fluid Flow. https://doi.org/10.1108/hff-03-2023-0114 [Google Scholar] [CrossRef]
Cite This Article
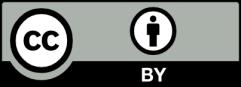