Open Access
ARTICLE
A Melamine–Dialdehyde Starch Wood Particleboard Surface Finish without Formaldehyde
1
LERMAB, I.U.T. Hubert Curien, University of Lorraine, Épinal, 88000, France
2
LERMAB-ENSTIB, University of Lorraine, Épinal, 88000, France
* Corresponding Authors: Antonio Pizzi. Email: ; Bengang Zhang. Email:
Journal of Renewable Materials 2023, 11(11), 3867-3889. https://doi.org/10.32604/jrm.2023.028888
Received 13 January 2023; Accepted 10 February 2023; Issue published 31 October 2023
Abstract
Melamine-dialdehyde starch resins used for wood surface finishes have been developed. The reaction of melamine with dialdehyde starch has been shown to occur by FTIR and MALDI ToF spectrometry, with several oligomer species due to the reaction of the two materials being identified, and the resin thermal stability was studied by thermogravimetric analysis. The resins were prepared by two different procedures when it was realized that dialdehyde starch is sensitive to too high a temperature for prolonged times. The melamine-dialdehyde starch resins were applied on particleboard supports as a direct liquid surface finish and a resin-impregnated paper. The surface finishes were tested for adhesion by the cross-cut test, their initial sessile drop contact angle, and the contact angle evolution as a function of time. The best results were obtained by the resins catalyzed by 2% ammonium sulfate and applied to the support surface as a resin-impregnated paper hot pressed for 3 min at 200°C, although the results at 180°C also looked promising.Keywords
Melamine-formaldehyde (MF) and melamine-urea-formaldehyde (MUF) resins are extensively used in industry as wood surface finishes. Both are directly applied on wood but particularly on particleboards of resin-impregnated paper for several commercial uses [1–3]. All formaldehyde-based amino plastic resins can present some formaldehyde emission during their working life. Melamine-formaldehyde resins are well known not to emit formaldehyde or to emit formaldehyde in service to a much lower extent than urea-formaldehyde resins, to the point that a number of different techniques have been developed by using melamine to depress formaldehyde emission from UF-bonded boards [4–8] and even techniques to use less melamine to even depress to a much larger extent formaldehyde emission from UF-bonded boards [9–13], such as using the non-toxic dialdehyde glyoxal [14] Nonetheless, even MF and MUF resins do emit some formaldehyde under some particular conditions, but worse they use formaldehyde, a now recognized toxic and carcinogenic material, during board production and cutting, endangering the health of workers under industrial manufacturing conditions. Thus, it is of interest today to develop clear surface finishes for the impregnated paper to apply on boards where formaldehyde is not used. This is needed because melamine and melamine-urea resins offer several excellent advantages as wood surface finishes, namely transparency, allowing the preparation of any wanted surface color, and resistance to cutting and to water.
Considering the above and the considerable utility and advantages of MF and MUF resins in wood surface finishing, there is then a clear interest in preparing finishes where formaldehyde is not used but which still retain the advantages characteristic of these resins as surface finishes. In such a context, a series of sugars specific oxidation reactions [15] based on the treatment of monomeric, dimeric, and polymeric carbohydrates by the use of sodium periodate [16–19] (Fig. 1) and sodium permanganate [17] or even UV radiation [20] have been recently proposed to prepare resins in which a number of C-C carbon bonds with vicinal –OH groups (HO-C-C-OH) in carbohydrates are cleaved with ease to generate two aldehyde groups. The systems have been shown to yield good results for a number of biomaterials containing carbohydrates to bond wood boards with bio-adhesives [21–23].
Figure 1: Specific oxidation of carbohydrates by sodium periodate leads to non-toxic and non-volatile bio-sourced aldehydes and to different cross-linked products according to the conditions used
A possibly easier approach to the partial oxidation of carbohydrate oligomers and polymers is also based on the use of hydrogen peroxide on starch or other carbohydrate polymers. Hydrogen peroxide oxidation of starch leads to oxidized starch, a product today better known under the name of dialdehyde starch. In a particularly interesting recent research work, Zhao et al. [24] have presented a renewable, zero HCHO-emission and eco-friendly urea-dialdehyde starch (U-OSt) polymer prepared by the condensation reaction between a majority of urea and oxidized starch with the addition of nano-TiO2. OSt replaced HCHO to avoid the emission of HCHO from the nano-TiO2-U-OSt polymer [24]. The scheme of synthesis of OSt, Urea-OSt, and nano-TiO2-Urea-OSt polymer is shown in Fig. 2.
Figure 2: Reaction of permanganate non-specifically oxidized starch, also called dialdehyde starch, cross-linked by urea without any formaldehyde
With the same approach tried by Zhao et al. [24] cross-linking oxidized dialdehyde starch with urea, more recent research has used the same approach to cross-link oxidized starch (dialdehyde starch) with glyoxylated lignin through urea bridges [25] according to the reaction in Fig. 3 to obtain wood particleboard adhesives. Pointed chemical instrumental analysis showed that glyoxalated lignin and hydrogen peroxide-treated starch were cross-linked by the third biomaterial, urea. The urea-oxidized dialdehyde starch results satisfied the internal IB strength requirements of the reference standard, but at a press temperature of 200°C by adding 5% on resin solids of biosourced glycerol diglycidyl ether [25]. As the inner core of a particleboard never reaches a temperature higher than 110°C–120°C the need for an additional cross-linker like glycerol diglycidyl ether indicated that the temperature of curing alone needs to be higher to cure such resins if one does not want to use the additional cross-linker.
Figure 3: The reaction of H2O2 non-specifically oxidized starch, also called commercial dialdehyde starch, cross-linked by urea with glyoxalated lignin, and without any formaldehyde
A green binder formulation prepared from dialdehyde corn starch (OSt) and urea (U) was developed for wood-based panel production. The adhesive structure obtained was strengthened by using titanium dioxide nanoparticles (nano-TiO2). Using TiO2 as an additional cross-linker helped decrease the press temperature to 175°C [26].
All the above indicated that such type of carbohydrate oxidized resins would be ideal without using any cross-linker for applications where much higher temperatures than 110°C–120°C could be used. In effect, MF and MUF wood panels surface finishes in thin layers are pressed industrially at between 140°C and 200°C [3], where the temperature of the thin finish really reaches much higher temperatures as in direct contact with the hot platen of the press. For this reason, the work presented here was undertaken for application to wood panels surface finishes using dialdehyde starch being cross-linked by melamine, constituting the surface finish resin. Analysis of the chemical species formed was also carried out by MALDI ToF mass spectrometry.
Melamine 99% was obtained from Sigma Aldrich. Dialdehyde starch (powder) was purchased from Taian City Jinshan Modified Starch Co., Ltd. (Shandong, China). Sodium hydroxide (NaOH, 40.00 g/mol, ACS reagent, ≥97.0%, pellets).
2.2 Preparation of Resins for Surface Finishes
(1) After the pH value of the dialdehyde starch reaction system (70 g dialdehyde starch + 70 g water) was adjusted between 5.0 and 5.5 with HCl aqueous solution (37 wt%) or NaOH aqueous solution (40 wt%), and the temperature was raised to 95°C for 30 min.
(2) 33 parts by weight of melamine on 50 parts by weight of dialdehyde starch were added into the reaction system, and the mixture was stirred mechanically and refluxed at 95°C for 30 min.
(3) The pH value was adjusted to between 5.0 and 5.5 with NaOH or HCl aqueous solution, and 17 parts by weight of the remaining residual melamine were added.
(4) The reaction mixture was kept under stirring and reflux for 1 h at 95°C and at pH 5.0–5.5. When the reaction was complete, the pH was adjusted to 7.0 with aqueous NaOH or HCl, and the temperature was lowered to ambient.
On the fourth day of storage at ambient temperature, the adhesive solidified, expelling the residual water as a layer.
(1) After the pH value of the dialdehyde starch reaction system (15 g dialdehyde starch + 30 g water) was adjusted between 6.5 and 7.0 with HCl aqueous solution (37 wt%) or NaOH aqueous solution (40 wt%), and the temperature was raised to 40°C for 30 min.
(2) Add 33 parts by weight of melamine on 50 parts by weight of dialdehyde starch into the reaction system, and stir and reflux at 40°C for 30 min.
(3) Adjust the pH value between 6.5 and 7.0 with NaOH or HCl aqueous solution, and add 17 parts by weight of remaining residual melamine, respectively.
(4) Keep the reaction under stirring and reflux for 1 h at 40°C and pH 6.5–7.0. When the reaction is complete, the temperature is lowered to ambient.
2.3 Physical Properties: Solids Content and Viscosity Measurements
The solids content of the resin samples was determined by placing about 1.0 g of the resin sample in a previously weighed small Petri dish and weighing it again. The Petri dish with the samples was placed afterward in an oven at 120°C for 2 h. The test was done in triplicate, and the measures obtained were averaged.
The resin viscosity was measured at 20°C using a Brookfield RV viscometer (Brookfield Ametek, Middleborough, MA, USA), and each value was taken as the average of three tests.
It can be seen from Table 1 that the solid content of the resin is 42.17%, and the viscosity is 237.8 mPa·s. The samples tested for solids content were ground and tested for FTIR, TG and MALDI TOF. Due to the low viscosity of the resin, filter paper was used for improving the results.
2.4 Application as Wood Surface Finishes
2.4.1 Surface Finishes with Resin 1
Some of the resin prepared was weighed and applied at a load of 150 g/m2 on the surface of particleboard samples of 50 × 50 × 12 mm and hot-pressed at 5 kg/cm2 at 150°C for 2 min, and other samples pressed for 2 min at 180°C.
2.4.2 Surface Finishes with Resin 2
Some of resin 2 was mixed with 2% sodium sulfate (1.5 g) on resin solids and the mix was placed on the surface of particleboard samples of 50 × 50 × 12 mm and hot-pressed at 5 kg/cm2 at 180°C for 3 min, and a second set of samples for 3 min at 200°C. Once finished, the samples were cooled down and the samples tested (Table 2).
Equally, resin 2 was used to impregnate samples of Fisherbrand standard filter paper (Fisher Scientific, Illkirch, France) at a level of 170 g/m2 final dry weight. After impregnation, the paper was partially dried and then applied on the surface of particleboard samples of 50 × 50 × 12 mm and hot-pressed either at 5 kg/cm2 at 180°C for 3 min or 3 min at 200°C (Table 2).
A FTIR/NIR spectrometer with attenuated total reflection (ATR) (ATR cell on a Perkin Elmer Spectrum 2000, Perkin Elmer France, Villebon-sur-Yvette, France) was used to analyze the chemical structure of the melamine-dialdehyde starch resin. The FTIR spectra consisted of 32 scans collected per run with a spectral resolution of 4 cm−1 at room temperature in the 4000–650 cm−1 range, each sample being tested 10 times.
The samples (4 mg/mL) were dissolved in water/acetone (50/50 by volume), and the solutions were added to the 10 mg/mL matrix solution in acetone. 2,5-dihydroxy benzoic acid was used as the matrix to ease placing the sample on the sample-holder plate. Red phosphorus was used for instrument calibration (LaserBio Labs, Valbonne, France). A concentrated solution of 10 mg/ml of sodium chloride (NaCl) in distilled water was mixed to the matrix to enhance ion formation. The sample was added to the matrix solutions and was divided into three parts of the matrix solution. Three parts of the sample solution and a part of NaCl solution. 0.5 to 1 μL were put on the MALDI target. The MALDI target was placed into the spectrometer after solvent evaporation. The peaks in the spectrum can present themselves at the actual molecular weight of the chemical species or increased by 23 Da, this being the molecular weight of the Na+ linked to the molecule from the NaCl added to the matrix to facilitate the flight of heavier oligomers. Sometimes both forms of the same species, with and without Na+ can be present in the same spectrum. The MALDI-TOF spectra were recorded on an AXIMA Performance instrument (Shimadzu Scientific Instruments; Manchester, UK). The irradiation source was a pulsed nitrogen laser with 3-ns intervals at a wavelength of 337 nm. The measurements were carried out using the following conditions: polarity: positive; flight path: linear; mass: high (20-kV accelerating voltage) and 100 to 150 pulses per spectrum. The delayed extraction technique was used to apply delay times of 200 to 800 ns, and the ion gate was set at 0, 500, 1000, and 1500 Da, respectively. The spectra are exactly at ±1 Da.
The samples were subjected to an adhesion test by the cross-cut test according to the French (European) standard NF EN ISO 2409 [27]. For this, the hardened surface finishes were cut through to the particleboard substrate with a razor blade to produce edges from which the coating may be lifted. The cutting pattern consisted of a 10 × 10 grid of vertical and horizontal cuts spaced at 1 mm × 1 mm. A strong adhesive tape was then applied over the cut area and tightly pressed. The tape was then rapidly pulled off. This operation was repeated three times. Finally, the surface finishes were examined to determine the number of blocks removed, constituting an evaluation of the coating adhesion.
The contact angles of a drop of water on the two types of surface finishes cured at different temperatures were tested and compared to the same for an untreated surface of uncoated samples from the same particleboard. The contact angle of the treated and untreated board surfaces was obtained from the water drop being placed on the surface with a syringe and measured with an EasyDrop contact angle apparatus using drop shape analysis software (KrüsGmbH, Hamburg, Germany).
2.8 Thermogravimetric Analysis (TGA)
The thermal stability of the coating resins was studied with a TGA 5500 analyzer (Mettler Toledo, Guyancourt, France). About 5–8 mg of dried resin sample powder was put on a platinum pan, and then the sample heated at a rate of 10 °C/min to the desired temperature under a nitrogen atmosphere at a 50 ml/min flow. The testing temperature ranged from 25°C to 790°C.
A Taber Industries 5135 Rotative Platform Abrader [28,29] (Taber Industries, North Tonawanda, NY, USA) was used to measure surface abrasion of some of the melamine-dialdehyde impregnated paper bonded on wood particleboard. The samples 10 cm × 10 cm square clamped to the rotating table were made to spin at 60 revolutions per minute. While the table was spinning, the sample was pressed by the abrasive wheels and additional weights, with the friction so caused inducing surface abrasion. The number of cycles used to see surface wear was taken as the value of abrasion resistance. The test was carried out according to the European Norm EN14323:2021 [30].
Color change of the surface-coated particleboard samples surface coated with impregnated melamine-dialdehyde starch resin samples was measured by a Chroma Meter CR-410 (KONICA MINOLTA, ZI Paris Nord 2, France) spectrophotometer, according to the CIELab system which is based on the L*, a*, b* color coordinate system, where L* represents the black-and-white axis; for black, L* = 0 and for white, L* = 100; a* represents the red-green color based on the positive and negative axes and b* represents the yellow-blue color (positive value for yellow, negative value for blue). The average of 4 points is taken as the final measure. The total color change (ΔE) was calculated according to the equation:
The results of the cut tests for the surface finish realized with resin 1 are shown in Fig. 4 (150°C and 180°C). The disadvantage that is clearly noticeable from Fig. 4 is the dark color of the board, which is a real disadvantage for a surface finish. Notwithstanding this, the resin 1 surface finishes were anyhow tested. Thus, the conditions of the particleboard before and after the application of the melamine-dialdehyde starch finish can be more clearly seen from the small residual pieces of wood chips of the particleboard on the pulled-out adhesive tape in Fig. 4.
Figure 4: Cross-cut test for resin 1 coatings hot-pressed for 2 min at 150°C (left) and 180°C (right)
The visual conclusions that can be drawn are:
(1) The 180°C pressed surface finish is clearly better cured and hence more performant than the same resins hot pressed at 150°C.
(2) The 180°C pressed surface finish indicates that the conditions of application should still be improved for optimal adhesion and cohesion results of the cured network. Although at 180°C the performance starts to be rather encouraging, there are three ways that the resin can be cured and cross-linked to a higher degree. This can be achieved just by (i) increasing the temperature of curing, (ii) by adding a suitable curing catalyst such as ammonium sulfate as it is done for melamine–formaldehyde resins, and (iii) by an increase in the relative percentage of either melamine or of dialdehyde starch, thus optimization of the weight ratio of the two materials.
The first approach is advisable only within a limited increase in temperature, no more than 200°C, as a greater increase in the temperature of curing may damage the wood substrate. The second is most suitable because if one considers that the results first presented (Fig. 4) have been obtained without a catalyst, then such an approach should improve resin performance by accelerating and further tightening the cross-linked network formed. The third route should also be explored as an optimization of the relative percentages of melamine and dialdehyde starch may also give increased cross-linking and better water resistance. It must be considered, however, that in the case an increase in melamine percentage is needed, this would also increase the percentage of the more expensive material, hence of the coating resin.
The contact angle of a water drop on the surfaces of panels where the experimental surface finish has been applied is higher when cured at 180°C than at 150°C curing temperature, these being respectively 67° and 44°, while it is less than 3° for an untreated board specimen. This confirms that the higher temperature of application yields a more cross-linked resin coating and that the three routes to a better performance of the coating outlined above are of interest for improving further the results.
Considering the clear disadvantage of the dark color of resin 1 coatings, resin 2 was then prepared. During the work with resin 1 it was realized that one of the problems leading to the unacceptable dark color was the darkening of the dialdehyde starch. This was found to depend on too high a reaction temperature of the resin for too long a time and at a pH too low. Thus, resin 2 was prepared at a higher pH, between 6.5 and 7.0, at a much milder temperature (40°) than the higher temperature used for resin 1 (90°C). Resin 2 than remained white, the normal color of the dialdehyde starch and of melamine. The appearance of resin 2 coatings are shown in Fig. 5.
Figure 5: The appearance of test pieces coated with resin 2. From top to bottom (a) 180°C resin 2 directly applied to the board surface (b) 200°C resin 2 directly applied to the board surface, (c) resin 2 impregnated paper applied on surface at 180°C, (d) resin 2 impregnated paper applied on surface at 200°C
Fig. 5 shows that resin 2 coatings on the board surfaces are much lighter-colored than in the case of resin 1 coatings. However, it is interesting that in the case of resin 2 coatings being applied directly on the board’s surface, the curing at the higher board temperature of 200°C start to slightly darken the coated surface. In the case of the melamine–dialdehyde starch resin 2 impregnated paper, the color of the coatings is definitely more light-colored than when the resin is applied directly on the board surface. Again while sample 6 (samples c, Fig. 5) cured for 3 min at 180°C is definitely white-colored, sample d hot-pressed at 200°C shows still some slight darkening indicating that the temperature should not be raised higher than 180°C. Moreover, the traditional application of resin-impregnated paper clearly gives a better appearance than just applying and curing the coating directly on the board surface. The above is visually confirmed in Fig. 6 by the cross-cutting test on the samples shown in Fig. 6.
Figure 6: Results of the ross-cut test for (a) 180°C resin 2 directly apply to the board surface (b) 200°C resin 2 directly apply to the board surface, (c) resin 2 impregnated paper applied on surface at 180°C, (d) resin 2 impregnated paper applied on surface at 200°C
In Fig. 6, all four resin coatings perform rather acceptably, but samples c and d present a better performance than samples a and b. The cross-cut test performance from best to worse is c > d > a > b, again confirming the degree of cure for the four application types. It confirms that the resin appears to be cured more at 200°C, and that it be applied either directly or through an impregnated paper, although the temperature at 180°C also gives very good results, the results being more acceptable than the 200°C due to the slight darkened color at 200°C.
In Fig. 7 are shown the wetting angle and wetting angle variation as a function of time of resin 2 coatings a, b, c, and d.
Figure 7: Variation as a function of time of the water drop contact angle on the wood surface coating with resin 2
The results in Fig. 7 confirm that, whatever the application method, the curing temperature of 200°C gives high initial wetting angles, 90° for sample d, and 62° for sample b, but both samples show a much slower decrease of the wetting angle as a function of time, with finally stabilizing at 45° for d and 39° for b, without further decreases. This is not the case for sample c, while presenting a high initial contact angle of 82° nonetheless continues to progressively decrease with time. Again a confirmation of the better curing at 200°C by impregnated paper. This is again proof of the effect of the temperature on the coatings cure. The coatings applied by impregnated paper (d) again give better results than the direct coating application (c). At 180°C, coating c with impregnated paper is also better than the direct coatings on the board surface, indicating the greater permeability of the latter.
3.3 Color Measurement and Color Change
Tables 3 and 4 show that there are variations of color of the paper impregnated with the melamine-dialdehyde starch once applied to the particleboard surface once this is pressed at 180°C and 200°C. From ΔL*, the paper progressively becomes slightly darker as the temperature increases, indicating chemical reactions occurring when heat is applied. As Δb* is 0.16 at 180°C this indicates almost no change of color between blue and yellow, but its slight increase 0.79 at 200°C indicates a slight yellowing of the paper, again indicating that pressing temperature influences the color of the surface finish based on paper impregnation. Thus, as the heat treatment temperature increases, the degree of white decreases, and the degree of yellow increases. It must be pointed out that such variations are likely to be lower if TiO2 is added to the resin.
The average abrasion test results for resin 2 impregnated paper applied on the particleboard surface at 180°C and 200°C were, respectively. The abrasion resistance test was done to determine the resistance of the coating material to the abrasive stress [31]. The abrasion test with the paper applied and cured at 200°C gave better abrasion resistance at the higher level of 268 revolutions of the rotating platform, while the surface at 180°C curing gave a level of 246 revolutions. This indicates that resin curing and abrasion resistance are dependent on the temperature of curing, a balance needed between the level of curing, favored by the higher temperature, and conservation of a lighter color, favored by the lower temperature of curing.
3.5 Thermogravimetruc Analysis (TGA)
To investigate the thermal stability of the fully cured series of melamine-dialdehyde starch wood coating resin, thermogravimetric analysis (TGA) was carried out. The corresponding resulting curve and particularly its first derivate (DTG) are shown in Figs. 8a and 8b. From the DTG curve, there appear to be several stages in the thermal degradation process. Thus, in the 50°C–200°C, 200°C–270°C (shoulder), 270°C–300°C (shoulder), 300°C–400°C, and 480°–550°C ranges, with two plateaus in the DTG curve, namely in the 400°–480°C and 550°–800°C ranges. First, in the lower temperature range, the weight loss can be attributed to the residual water evaporation and some small molecular impurities degradation [32,33]. The second series of small stages between 200°C and 300°C correspond to some degradation of unreacted starch and some impurities. Finally, the third series of degradation stages in the 400°C–600°C range is due to the degradation of the cured coating resin skeletal chain. Some more stable chemical bonds, such as C-C and C-O, are cleaved within this temperature range [32–34].
Figure 8: Thermogravimetric analysis curve (TGA) and its first derivate (DTG) for the experimental melamine-dialdehyde starch resin
The FTIR analysis (Fig. 9) shows a new bond structure being obtained during the curing process. Thus, the new structure which appears to be formed during the curing process contributes to improving the thermal stability of the wood coating resin. In the spectrum of the melamine-dialdehyde starch, several peaks are noticeable. The peaks at 3350 and 3200 cm−1 belong respectively at CH-OH stretching and to the C-NH- stretching of unreacted –NH2 groups of melamine [35,36]. The band at 2400 cm−1 is also assigned to the –N-H stretch of unreacted melamine. The aldehyde –C=O group of oxidized starch is observed as shoulders at 1720 and at 1637 cm−1 [25,26]. The two vicinal peaks at 1621 and 1556 cm−1 [34] belong respectively to the signals of unreacted and reacted melamine, while the shoulder signals at 1373 and at 1360 cm−1 are respectively assigned to the N-C of substituted melamine and to the N-C-N asymmetric stretching of substituted melamine [35,36]. The small shoulder at 1150 cm−1 is attributed to the N-C-N symmetric stretching of substituted melamine [34]. The strong peak at 1046 cm−1 belongs to the numerous alcoholic C-OH of the starch [25]. The sharp peak at 800 cm−1 can be attributed to either substituted or unsubstituted –NH- groups of melamine [36].
Figure 9: FTIR of the experimental melamine-dialdehyde starch resin
Thus the patterns that one can distinguish from the FTIR spectrum are (i) one of the C-OH groups of the starch at 3200 and 1046 cm−1, (ii) one of unreacted melamine, the 2400 cm−1 peak of the unreacted –NH2 group, the 1621 cm−1 peak of the -N= group of the melamine triazine ring, and possibly by the 800 cm−1 peak, (iii) one of reacted melamine at 1556, 1373, 1360, 1150 cm−1, and possibly also at 800 cm−1, and (iv) one of the unreacted –C=O groups of oxidized starch at 1720 and 1637 cm−1.
The conclusions that can be drawn from these patterns are that melamine has reacted with several of the aldehyde groups of oxidized starch.
The MALDI ToF spectra of the coating are shown in Figs. A1a–A1e (Appendix 1), and the attribution to the series of oligomers formed is shown in Table A1 (Appendix 1). Several species of interest are present such as a number of oligomers of dialdehyde starch in which all the glucose units are oxidized and others in which there are glucose units oxidized and not oxidized, such as (I) and (II).
Several higher oligomers with mixed oxidized and non-oxidized glucose in the chain, such as the species at 683 Da (tetramer) and 1009 Da (hexamer), are also present.
Most interesting for the melamine-dialdehyde starch coating are the species where reactions have occurred between the aldehydes of dialdehyde starch and the –NH2 groups of melamine. These are of different types, from oligomers such as dialdehyde starch oligomers to which are linked to one or two melamine molecules, such as the species at 757 Da (III) and 851 Da (IV).
And species in which two melamine molecules have reacted with both aldehyde groups of a single oxidized glucose (V), as well as melamine chains linked by a glyoxal (peak at 58 Da, Fig. 6a) reacted with a oxidized glucose unit (VI) in a starch dimer, glyoxal being produced in very small amount by the oxidation process of the starch itself [16,21].
To complete the type of oligomer species present and to understand how the cross-linking proceeds, there are species in which one melamine links two separate oxidized starch oligomers such as those represented y the peaks at 889, 1013, 1055, 1350, and 1638, 1782, and 1943 Da, thus even rather long chains of dialdehyde starch linked by a melamineas for example structure (VII), where the starch chains can be either linear or branched, a point valid for all the structural assignments in Table A1 (Appendix 1).
At the highest molecular weights there is a periods of either 162 or of 165 Da regularly intervening between the peaks of the main high MW oligomers. This. Indicates the presence of longer chains with either one more glucose unit added (165 Da interval) or an open oxidized glucose unit (162 Da) which differ of 3 Da. This indicates that also much longer linear or branched oxidized starch chains are able to react and to be linked by reacting with melamine. Moreover compounds that indicate that the melamine constitutes a tridimensional knot of a cross-linked network are also found as for instance the compound at 2277 Da (VIII).
Considering the randomly alternating periods of 162 and 165 Da, this leads to the peaks of 2438 Da by just adding an oxidized glucose unit, and to 2626 Da to add a further non-oxidized glucose unit plus one extra Na+, and so on to ever higher MW oligomers.
Melamine-dialdehyde starch resins have been shown to have encouraging results as surface finishes of wood panels, with the application by resin-impregnated paper yielding better results than direct application of the liquid resin on the surface of the support. The sensitivity of dialdehyde starch to high temperatures and low pH for prolonged times limits the higher temperature to be used in the synthesis of the resin itself, with 90°C turning the finish dark brown, while with 40°C, the resin remains transparent. The resins need a curing accelerator/hardener, sodium sulfate, as for all existing aminoresin wood adhesives. Both 180°C and 200°C temperatures of hot-pressing of the surface finish on the support yield encouraging results, 180°C giving a slightly better transparency, a whiter color with little or no indication of yellowing, with 200°C yielding slightly improved mechanical resistance due to improved resin curing; but a slightly less white color and a slight shift towards the yellow. Instrumental chemical analysis by FTIR and MALDI ToF spectrometry has shown that the melamine and dialdehyde starch react, forming a number of different linear and branched oligomers showing that a chemically cross-linked network is the final form of the surface finish. Of the proposed routes for improving the resin performance, namely by (i) increasing the temperature of curing, (ii) by adding a suitable curing catalyst such as ammonium sulfate, and (iii) by an increase in the relative percentage of either melamine or of dialdehyde starch, the use of the option (i) and (ii) has been applied with some success, while route (iii) has not been tried as yet because an increase the percentage of the expensive melamine would lead to a more expensive surface finish resin.
Funding Statement: The LERMAB is supported by a Grant of the French Agence Nationale de la Recherche (ANR) in the Ambit of the Laboratory of Excellence (Labex) ARBRE. This work was also supported by “The 111 Project (D21027)”.
Conflicts of Interest: The authors declare that they have no conflicts of interest to report regarding the present study.
References
1. Roberts, R. J., Evans, P. D. (2005). Effects of manufacturing variables on surface quality and distribution of melamine formaldehyde resin in paper laminates. Composites Part A: Applied Science and Manufacturing, 36, 95–104. https://doi.org/10.1016/S1359-835X(04)00127-7 [Google Scholar] [CrossRef]
2. Kirchgaessner, U., Niessner, M. (1992). Schnell penetrierende aminoplastharzlösungen. German Patent Application DE 4117841A1. [Google Scholar]
3. Kandelbauer, A., Petek, P., Medved, S., Pizzi, A., Teischinger, A. (2010). On the performance of a melamine–urea–formaldehyde resin for decorative paper coatings. European Journal of Wood and Wood Products, 68, 63–75. https://doi.org/10.1007/s00107-009-0352-y [Google Scholar] [CrossRef]
4. Paiva, N., Henriques, A., Cruz, P., Ferra, J., Carvalho, L. H. et al. (2012). Production of melamine fortified urea-formaldehyde resins with low formaldehyde emission. Journal of Applied Polymer Science, 124(3), 2311–2317. https://doi.org/10.1002/app.35282 [Google Scholar] [CrossRef]
5. Liu, K., Su, C., Ma, W., Li, H., Zeng, Z. et al. (2020). Free formaldehyde reduction in urea-formaldehyde resin adhesive: Modifier addition effect and physicochemical property characterization. BioResources, 15(2), 2339–2355. [Google Scholar]
6. Zhang, J., Wang, X., Zhang, S., Gao, Q., Li, J. (2013). Effects of melamine addition stage on the performance and curing behavior of melamine-urea-formaldehyde (MUF) resin. BioResources, 8(4), 5500–5514. https://doi.org/10.15376/biores.8.4.5500-5514 [Google Scholar] [CrossRef]
7. Ghani, A., Ashaari, Z., Bawon, P., Lee, S. H. (2018). Reducing formaldehyde emission of urea formaldehyde-bonded particleboard by addition of amines as formaldehyde scavenger. Building and Environment, 142, 188–194. https://doi.org/10.1016/j.buildenv.2018.06.020 [Google Scholar] [CrossRef]
8. Saitoa, K., Hirabayashi, Y., Yamanaka, S. (2021). Reduction of formaldehyde emission from urea-formaldehyde resin with a small quantity of graphene oxide. RSC Advances, 11, 32830–32836. https://doi.org/10.1039/D1RA06717F [Google Scholar] [PubMed] [CrossRef]
9. Prestifilippo, M., Pizzi, A., Norback, H., Lavisci, P. (1996). Low addition of melamine salts for improved UF adhesives water resistance. Holz als Roh und Werkstoff, 54(6), 393–398. https://doi.org/10.1007/s001070050208 [Google Scholar] [CrossRef]
10. Zanetti, M., Pizzi, A. (2003). Low addition of melamine salts for improved MUF adhesives water resistance. Journal of Applied Polymer Science, 88(2), 287–292. https://doi.org/10.1002/(ISSN)1097-4628 [Google Scholar] [CrossRef]
11. Zanetti, M., Pizzi, A., Faucher, P. (2004). Low-volatility acetals to upgrade the performance of MUF wood adhesives. Journal of Applied Polymer Science, 92(1), 672–675. https://doi.org/10.1002/(ISSN)1097-4628 [Google Scholar] [CrossRef]
12. Zanetti, M., Pizzi, A. (2004). Dependance on the adhesive formulation of the upgrading of MUF particleboard adhesives and decrease of melamine content by buffer and additives. Holz als Roh und Werkstoff, 62(6), 445–451. https://doi.org/10.1007/s00107-004-0518-6 [Google Scholar] [CrossRef]
13. Zanetti, M., Pizzi, A., Kamoun, C. (2003). Upgrading of MUF particleboard adhesives and decrease of melamine content by buffer and additives. Holz als Roh und Werkstoff, 61(1), 55–65. https://doi.org/10.1007/s00107-002-0352-7 [Google Scholar] [CrossRef]
14. Deng, S., Pizzi, A., Du, G., Lagel, M. C., Delmotte, L. et al. (2018). Synthesis, structure characterization and application of melamine-glyoxal adhesive resins. European Journal of Wood and Wood Products, 76(1), 283–296. https://doi.org/10.1007/s00107-017-1184-9 [Google Scholar] [CrossRef]
15. Bobbitt, J. M. (1956). Periodate oxidation of carbohydrates. Advanced Carbohydrates Chemistry, 11, 1–41. https://doi.org/10.1016/S0096-5332(08)60115-0 [Google Scholar] [PubMed] [CrossRef]
16. Frihart, C. R., Pizzi, A., Xi, X., Lorenz, L. (2019). Reactions of soy flour and soy protein by non-volatile aldehydes generation by specific oxidation. Polymers, 11, 1478. https://doi.org/10.3390/polym11091478 [Google Scholar] [PubMed] [CrossRef]
17. Frihart, C. R., Lorenz, L. (2019). Specific oxidants improve the wood bonding strength of soy and other plant flours. Journal of Polymer Science, Part A: Polymer Chemistry, 57, 1017–1023. https://doi.org/10.1002/pola.29357 [Google Scholar] [CrossRef]
18. Guigo, N., Mazeau, K., Putaux, J. L., Heux, L. (2014). Surface modification of cellulose microfibrils by periodate oxidation and subsequent reductive amination with benzylamine: A topochemical study. Cellulose, 21, 4119–4133. https://doi.org/10.1007/s10570-014-0459-0 [Google Scholar] [CrossRef]
19. Codou, A., Guigo, N., Heux, L., Sbirrazzuoli, N. (2015). Partial periodate oxidation and thermal cross-linking for the processing of thermoset all-cellulose composites. Composites Science and Technology, 117, 54–61. https://doi.org/10.1016/j.compscitech.2015.05.022 [Google Scholar] [CrossRef]
20. Quispe, M. M., López, O. V., Villar, M. A. (2019). Oxidative degradation of thermoplastic starch induced by UV radiation. Journal of Renewable Materials, 7(4), 383–391. https://doi.org/10.32604/jrm.2019.04276 [Google Scholar] [CrossRef]
21. Xi, X., Pizzi, A., Frihart, C. R., Lorenz, L., Gerardin, C. (2020). Tannin plywood adhesives by non-volatile aldehydes generation from specific oxidation of mono-and disaccharides. International Journal of Adhesion and Adhesives, 98, 102499. https://doi.org/10.1016/j.ijadhadh.2019.102499 [Google Scholar] [CrossRef]
22. Chen, X., Xi, X., Pizzi, A., Fredon, E., Du, G. et al. (2020). Oxidized demethylated lignin as a bio-based adhesive for wood bonding. Journal of Adhesion, 97, 873–890. https://doi.org/10.1080/00218464.2019.1710830 [Google Scholar] [CrossRef]
23. Xi, X., Pizzi, A., Lei, H., Chen, X., Zhang, B. et al. (2022). Environmental friendly chitosan adhesives for plywood bonding. International Journal of Adhesion and Adhesives, 112, 103027. https://doi.org/10.1016/j.ijadhadh.2021.103027 [Google Scholar] [CrossRef]
24. Zhao, X., Peng, L., Wang, H., Wang, Y., Zhang, H. (2018). Environment-friendly urea-oxidized starch adhesive with zero formaldehyde-emission. Carbohydrate Polymers, 181, 1112–1118. https://doi.org/10.1016/j.carbpol.2017.11.035 [Google Scholar] [PubMed] [CrossRef]
25. Chen, X., Pizzi, A., Zhang, B., Zhou, X., Fredon, E. et al. (2022). Particleboard bioadhesive by glyoxalated lignin and oxidized dialdehyde starch cross-linked by urea. Wood Science and Technology, 56, 63–85. https://doi.org/10.1007/s00226-021-01344-z [Google Scholar] [CrossRef]
26. Oktay, S., Kızılcan, N., Bengu, B. (2021). Oxidized cornstarch–urea wood adhesive for interior particleboard production. International Journal of Adhesion and Adhesives, 110, 102947. https://doi.org/10.1016/j.ijadhadh.2021.102947 [Google Scholar] [CrossRef]
27. AFNOR (Association Française de Normalisation) (2020). Norme Francaise NF EN ISO 2409—Peintures et Vernis—Essai de Quadrillage; AFNOR: La plaine Saint Denis, France. [Google Scholar]
28. Righeira Carnegie, M., Sherine, A., Sivagami, D., Sakthivel, S. (2016). Anti-reflection coatings with enhanced abrasion and scratch resistance properties. Journal of Sol-Gel Science and Technology, 78(1), 176–186. https://doi.org/10.1007/s10971-015-3924-9 [Google Scholar] [CrossRef]
29. Nandipati, M. R., Suman, K. N. S. (2021). Improving abrasion resistance of laminate floor with additional curing prior to final coating–An experiment and SAS program. International Journal of Innovative Science and Research Technology, 6(12), 780–784. [Google Scholar]
30. European Norm EN 14323:2021 (2021). Wood-based panels-melamine faced boards for interior uses-test methods. Bruxelles, Belgium: European Committee for Standardization. [Google Scholar]
31. Istek, A., Aydemir, D., Aksu, S. (2010). The effect of decor paper and resin type on the physical, mechanical, and surface quality properties of particleboards coated with impregnated décor papers. BioResources, 5(2), 1074–1083. [Google Scholar]
32. Chen, X., Li, J., Xi, X., Pizzi, A., Zhou, X. et al. (2020). Condensed tannin-glucose-based NIPU bio-foams of improved fire retardancy. Polymer Degradation and Stability, 175, 109121. https://doi.org/10.1016/j.polymdegradstab.2020.109121 [Google Scholar] [CrossRef]
33. Luo, J., Zhou, Y., Gao, Q., Li, J., Yan, N. (2020). From wastes to functions: A new soybean meal and bark-based adhesive. ACS Sustainable Chemistry and Engineering, 8(29), 10767–10773. https://doi.org/10.1021/acssuschemeng.0c02413 [Google Scholar] [CrossRef]
34. Chen, X., Xi, X., Pizzi, A., Fredon, E., Zhou, X. J. et al. (2020). Preparation and characterization of condensed tannin non-isocyanate polyurethane (NIPU) rigid foams by ambient temperature blowing. Polymers, 12(4), 750. https://doi.org/10.3390/polym12040750 [Google Scholar] [PubMed] [CrossRef]
35. Kandelbauer, A., Despres, A., Pizzi, A., Taudes, I. (2007). Testing by FT-IR species variation during MUF resins preparation. Journal of Applied Polymer Science, 106(4), 2192–2197. https://doi.org/10.1002/(ISSN)1097-4628 [Google Scholar] [CrossRef]
36. Pretsch, E., Clerc, T., Seibl, J., Simon, W. (1989). Tables of spectral data for structure determination of organic compounds: 13C-NMR, 1H-NMR, IR, MS, UV/VIS, 2nd ed Berlin, Germany: Springer-Verlag. [Google Scholar]
Figure A1: MALDI ToF spectra of the experimental melamine-dialdehyde starch resin used for wood surface coating; (a) 10–1000 Da range, (b) 10–500 Da range, (c) 500–1000 Da range, (d) 1000–1500 Da range, (e) 1500–2000 Da range, (f) 2000–2500 Da range, (g) 2500–3000 Da range
Cite This Article
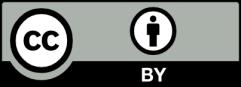