Open Access
ARTICLE
Effect of Multi-Hydroxyl Polymer-Treated MUF Resin on the Mechanical Properties of Particleboard Manufactured with Reed Straw
1 College of Materials Science and Engineering, Central South University of Forestry and Technology, Changsha, 410004, China
2 Department of Human Resources, Shengao Technology Co., Ltd., Hangzhou, 311217, China
* Corresponding Author: Yiqiang Wu. Email:
(This article belongs to the Special Issue: Bio-Fibres, Biopolymers and Biocomposites – Design for Sustainability, Life Cycle Analysis, Concurrent Materials and Conceptual Design Selection)
Journal of Renewable Materials 2023, 11(9), 3417-3431. https://doi.org/10.32604/jrm.2023.028511
Received 22 December 2022; Accepted 17 January 2023; Issue published 20 July 2023
Abstract
The poor bonding performance between aqueous adhesives represented by melamine-urea formaldehyde (MUF) resins and reed straw hinders their applications in the field of non-wood-based panels. Multi-hydroxyl polymers are highly reactive and are often used as crosslinkers. This study fabricated a resin with a strengthened cross-linked structure by combining a multi-hydroxyl polymer and MUF resin prepolymer. The reed particleboard was prepared by using this resin as an adhesive and reed stalk as the matrix. The results show that neighboring molecules combined to form C–O–C bonds that strengthened the cross-linked structure of the resin. In addition, the viscosity of the resin was increased, and a continuous adhesive layer on the surface of reed particles was formed, which slowed the penetration of reed particles. The adhesive layer significantly improved the mechanical properties of the reed particleboard. The maximum modulus of rupture (MOR), modulus of elasticity (MOE), and internal bonding strength (IB) of the reed particleboard were 33.53, 4126, and 0.79 MPa, respectively. The IB of the board was 3.3 times higher than that of the reed particleboard prepared with a conventional MUF resin. Reed straw is a non-wood biomass material that has the advantage of sustainable development and may replace wood-based materials to produce particleboard. This resin-prepared reed particleboard is expected to be used in areas such as custom furniture and engineering materials.Keywords
Over the past 20 years, the worldwide production of wood-based panels (including plywood, fiberboard, particleboard, and oriented strand board) has increased from 180 million m3 to 361 million m3 [1]. Among these, particleboard is one of the most popular wood-based panels, and the annual demand has increased from 2.0% to 5.0% [2,3]. Large amounts of wood are consumed each year; therefore, it is proposed to use other biomass resources to replace wood to alleviate. Reed is a non-wood material with strong environmental adaptability and a short growth cycle [4,5]. In addition, the fibers of reed straw have a higher tensile strength and better moisture and aging resistance than wood fiber. Its chemical composition is similar to that of wood [6,7]. Thus, it may be suitable as a raw material for particleboard production.
Reed straw is similar to other straw materials, and its epidermis is covered with a waxy layer composed of silicide [8]. This results in poor bonding between the adhesives and reed particles. Although reducing the specific surface area of the waxy layer could improve the mechanical performance of reed particleboard, it still fails to meet relevant particleboard requirements [9,10]. This is often related to the performance of the adhesive itself. Melamine-urea formaldehyde (MUF) resin is the polycondensation product of formaldehyde with urea and melamine and is the most commonly used adhesive for preparing wood-based particleboard [11]. It has a simple synthesis process, low preparation costs, a rapid curing schedule, and strongly bonds to wood-based materials [12]. However, the molar ratio of formaldehyde to melamine and urea (F/(M + U)) affects the bonding performance of MUF resin. MUF resins with a low molar ratio have a unique crystalline structure. The formation of hydrogen bonds between linear molecules induces crystallization, inhibiting the formation of the desired cross-linked structure and reducing MUF resin’s bonding performance [13,14]. Therefore, the cross-linked structure is closely related to the bonding performance of MUF resin.
Branched melamine contains three amino groups that can react with formaldehyde to form N-methylol melamine, which improves the cross-link density [15,16]. Melamine can reduce the free formaldehyde content in resins, but the addition of excess melamine reduces the molar ratio of F/(M + U), resulting in the formation of hydrogen bonds between molecules, which inhibit the intermolecular cross-linked structure and affects the bonding performance of MUF resins [17,18]. This makes it unsuitable for the preparation of reed particleboard. According to the hypothesis that an appropriate cross-linked structure will improve the bonding performance of MUF resin, we can possibly improve the intermolecular cross-link density by chemical bonds between MUF resin prepolymer and other modifiers, reducing the side effects caused by hydrogen bonding. Polyvinyl alcohol (PVA) is a water-soluble linear polymer that contains many hydroxyl groups. PVA and methylol groups can be cross-linked to form an interpenetrating network that will improve the cross-linked structure of MUF resin [19,20]. PVA can also undergo condensation with free formaldehyde [21,22]. Therefore, the amount of PVA can be increased to improve the intermolecular cross-link density of MUF resin.
Here, we attempted to increase the cross-link density between MUF resin to improve the bonding performance of the resin with the reed. A simple alkali-acid-alkali method was used to prepare the P-MUF resin with PVA, melamine, urea, and formaldehyde. The hydroxyl groups of the PVA reacted with the MUF prepolymers to form a highly cross-linked structure, which further improved the cross-linking density between the resin molecules. The chemical structure, curing performance, and thermal stability of the MUF resin or P-MUF resin were compared by using FTIR, XPS, XRD, DSC, TG, and DTG. The influence of the PVA content on the mechanical properties of the reed particleboard was analyzed. The resin and reed formation mechanism was analyzed by scanning electron microscopy (SEM).
Reed (Arundo donax L.) was collected in the Dongting Lake area of Hunan, China. Reed straw without roots and leaves was used as the raw material, which was about 0.8 to 1.2 m long and 1.0 to 3.0 cm in diameter. PVA with a degree of polymerization of 800 ± 50 (97%) was purchased from Shanghai Yingjia Industrial Development Co., Ltd. (China). Analytical-grade melamine (99%), urea (99%), formaldehyde (37%) and PVA were used to synthesize P-MUF resin. Aqueous solutions of both HCOOH (25%) and NaOH (25%) were used to adjust the pH level during the P-MUF resin synthesis. An aqueous solution of NH4Cl (25%) was used as a curing agent. The above chemicals were purchased from Sinopharm Chemical Reagent Co., Ltd. (Shanghai, China).
2.2 Preparation of the MUF Resins and P-MUF Resins
This study synthesized MUF and P-MUF resins under ambient laboratory conditions via a three-step alkali-acid-alkali method. The molar ratio of formaldehyde to urea and melamine was 1.10, and the mass ratios of PVA to urea and melamine were 0%, 0.5%, 1.0%, 1.5%, and 2.0%. Formaldehyde was mixed with the first part of urea for the addition reaction (formaldehyde to urea molar ratio of 2.17). During the reaction, the pH was controlled at about 8.0. Then, the pH of the solution was adjusted to about 7.5, and melamine was added to the mixture for the addition reaction (formaldehyde to urea and melamine molar ratio of 2.13) and kept at 88°C for 20 min. Subsequently, the pH of the mixture was adjusted to 5.1 so that the condensation reaction could occur. The mixture was dropped into water and then formed white flocs. The mixture’s pH was controlled at about 6.5. The second portions of urea and melamine were added (formaldehyde to urea and melamine molar ratio of 1.38), and the mixture was heated at about 80°C for 30 min. Finally, the pH was adjusted to 7.5. The third portion of urea was added (formaldehyde to urea and melamine molar ratio of 1.10), and the mixture was naturally cooled to 40°C when the reaction was complete. After that, the pH was adjusted to 8.0 to obtain the MUF resin. Using the same synthesis procedure, PVA was added proportionately with the first portion of urea to obtain the P-MUF resins.
2.3 Preparation of Reed Particleboards
The particleboards used in this study were designed and fabricated under ambient laboratory conditions. The target density of the single-layer reed particleboard was 0.75 g/cm3, and the thickness was 8 mm. Two boards were prepared for each set of resins. The resin content in the reed particleboard was set to 12%, and the resin contained 1% NH4Cl solution (25%) as a curing agent. The preparation process of the reed particleboard is shown in Fig. 1. First, reed straws were shredded using a rotary chipper (PZ8, Pallmann, Germany). After that, the reed particles were dried to a moisture content of 10%, and reed particles with diameters ranging from 0.83 to 1.65 mm were obtained by sieving using a rotary vibrating screen machine (S49, Dezhong Machinery Equipment Co., Ltd., China). Secondly, the resin was sprayed on reed particles in a blender to obtain a homogeneous mixture that was formed in a forming box with dimensions of 300 mm × 300 mm. It was then densified using a hot press (QD, Shanghai Wood-based Panel Machinery Factory Co., Ltd., China) at 170°C and a pressure of 3.5 MPa for 3 min. Finally, the reed particleboards were stored at room temperature for 72 h.
Figure 1: Preparation process of reed particleboard
2.4 Basic Property Tests of the MUF Resins and P-MUF Resins
About 2 g of MUF resin or P-MUF resin was added into a self-made tin foil container and then cured in a thermostat at 120°C for 2 h. The weight of the resin before and after drying was measured to calculate the non-volatile solids content. Each group of experiments was repeated three times, and the average value was taken.
The viscosity of MUF resin or P-MUF resin at 28°C was measured using a digital viscometer (NDJ-5S, Shanghai Hengping Instrument Factory, China) with a No. 1 spindle rotating at 60 rpm. Each group of experiments was repeated three times, and the average value was taken.
The curing time of MUF resin or P-MUF resin was measured using the boiling water bath method. About 10 g of the resin containing 3% NH4Cl solution (25%) was measured at 100°C with a stopwatch. Each group of experiments was repeated three times, and the average value was taken.
The free formaldehyde content in MUF resin or P-MUF resin was determined by titration. About 10 g of resin was dissolved in 50 mL of absolute ethanol, and then 6 to 7 drops of methyl red-blue (0.01%–0.05%) solution, 10 mL of NH4Cl solution (10%), and 10 mL of NaOH solution (1 M) were added, mixed, and left for 0.5 h. Then, the mixture was titrated with 0.49 M HCl. When the color of the mixture was purple-red, the titration was stopped, and the HCl consumption was recorded. The free formaldehyde content was calculated by Eq. (1).
where V1 is the volume (mL) of HCl consumed by distilled water, V2 is the volume (mL) of HCl consumed by resin, C is the concentration of HCl, and M is the weight of resin or distilled water.
2.5 Characterization of the Chemical Structure of the MUF Resins and P-MUF Resins
Fourier-transform infrared spectroscopy (FTIR, Nicolet iS50, Thermo Fisher Scientific, USA) in total reflection scanning mode was used to analyze changes in the functional groups of the resins. The scanning wavelength range was 400 to 4000 cm−1, the scanning time was 64 s, and the resolution was 8 cm−1. During tests, the resins were spiked with potassium bromide.
X-ray photoelectron spectroscopy (XPS, AXIS SUPRA+, Kratos, UK) was used to characterize the bonding of C and O atoms in the resins at room temperature by using high-resolution scans at 20 and 0.1 eV. Before tests, the resins were cured at 105°C, ground, crushed, and passed through a 200-mesh screen at room temperature.
2.6 Characterization of Crystallinity of the MUF Resins and P-MUF Resins
A wide-angle X-ray diffractometer (XRD, Empyrean, PANalytical, Netherlands) with a CuKα X-ray source at a wavelength (λ) of 1.5405 Å was used to analyze the crystallinity of the resins. The resins were scanned in the 2θ range of 20–60° with a scanning speed of 10°/min. Before the test, the resins were cured at 105°C, ground, crushed, and passed through a 200-mesh screen at room temperature.
2.7 Curing Reaction of MUF Resins and P-MUF Resins
A differential scanning calorimeter (DSC, TAQ2000, TA Instruments, USA) was used to characterize the curing reaction of the resins. Before the test, the resins were freeze-dried in a vacuum for 48 h, and resins samples were added to an aluminum crucible. The resins were heated from 30°C to 250°C at a heating rate of 10 °C/min under a N2 atmosphere.
2.8 Thermal Properties of MUF Resins and P-MUF Resins
A thermogravimetric analyzer (TG, TGA55, TA Instruments, USA) was used to analyze the resins’ thermal properties using TG and DTG. Before the tests, the resins were cured at 105°C, ground, crushed, and passed through a 200 mesh screen at room temperature. Small samples of resins were added to an aluminum crucible and heated from 30 to 500°C at a heating rate of 10 °C/min under a N2 atmosphere.
2.9 Mechanical Property Tests and Characterization of Reed Particleboards
According to the Chinese standard GB/T 17657–2013, the reed particleboards were cut into test specimens with the corresponding specifications. The universal mechanical testing machine (MUD-10, Jinan Times Assay Testing Machine Co., Ltd., China) was used to assess the mechanical properties of the specimens. Chinese standard GB/T 4897–2017 was used to compare the modulus of rupture (MOR), modulus of elasticity (MOE), and internal bonding (IB) strength of each specimen. At room temperature, each group of samples was tested five times.
2.10 Morphological Characterization of Reed Particleboard
To investigate the forming mechanism of the reed particleboard, bonded reed particles were obtained from the fracture surface of the IB sample. A scanning electron microscope (SEM, Zeiss Sigma 300, Carl Zeiss Jena, UK) was used to compare the reed raw particles and bonded reed particles.
3.1 Basic Properties of the MUF Resins and P-MUF Resins
The basic properties of aldehyde-based resins include the viscosity, non-volatile solids content, curing time, and free formaldehyde content [23]. During the manufacture of reed particleboard, the resin was sprayed on reed particles by atomization, and a glue mixer was used to mix the resin and reed particles. The viscosity affected the distribution, penetration, and dosage of resin in the reed particles, while the non-volatile solids content affected the hot-pressing cycle. For high-solid-content resins, the pressing time required for water evaporation is short [24]. Aldehyde-based resins also contain free formaldehyde.
To meet manufacturing requirements, the traditional alkali-acid-alkali synthesis method was used to prepare MUF resins with different PVA contents. Various indexes were used to investigate the relationship between the MUF resin and PVA content. Fig. 2a shows that the viscosity of the resin increased from 28.8 to 172.1 mPa.s upon increasing PVA content. When the mass ratio of PVA to melamine and urea exceeded 2.0%, the P-MUF resin underwent gelation during the synthesis. This affected the later use of P-MUF resin. For the pure MUF resin, the hydroxymethyl product of the resin underwent excessive polycondensation under acidic conditions, which increased the resin’s viscosity. This showed that the P-MUF resin underwent violent polymerization during synthesis, which rapidly increased the resin’s viscosity. The viscosity of the P-MUF resin was too high, which might affect the resin’s wettability to the reed particles while also reducing the reed particleboard’s mechanical properties. From the apparent viscosity, the mass ratio of PVA to melamine and urea of 2.0% was the limit for synthesizing P-MUF resin. The non-volatile solids content of the P-MUF resin increased from 52.2% to 54.14% upon increasing the PVA content (Fig. 2b). However, the curing time of the resin did not decrease as the non-volatile solids content increased (Fig. 2c). This might have been related to the nature of the PVA, which functioned as a protective glue that inhibited the bonding of functional groups at room temperature, while prolonging the curing time. This showed that the P-MUF resin might have contained “free” PVA. In addition, the formaldehyde to melamine and urea molar ratios of MUF resin and P-MUF resin were both 1.10, but the free formaldehyde content in the resin decreased continuously upon increasing the PVA content (Fig. 2d). This showed that PVA could react with free formaldehyde to reduce its content in the resin. For this, the synthesis mechanism of P-MUF resin was deduced (Fig. 3).
Figure 2: Basic properties of MUF resins with different PVA contents: viscosity (a), solid content (b), curing time (c), free formaldehyde content (d)
Figure 3: Illustration of the formation mechanism of MUF resin and P-MUF resin
3.2 Chemical Functional Groups of the MUF Resins and P-MUF Resins
Fig. 3 shows that the urea and melamine with the formaldehyde completed the methylation reaction under alkaline conditions. Then, the methylol product began to undergo polycondensation into MUF macromolecules under acidic conditions. At the same time, the -OH groups of PVA cross-linked with methylol and MUF polycondensation products to form C–O–C bonds. This made PVA interpenetrate the MUF resin molecules to form a stable cross-linked structure. Through the series of alkali-acid-alkali reactions, entanglements between the resin molecules were increased, and the cross-linked density between resin molecules was improved upon increasing the PVA content.
To verify the above mechanism, the functional groups of MUF resins with different PVA contents were analyzed by FTIR and XPS. Fig. 4a shows the presence of a vibration peak of N–H and -OH groups at 3340 cm−1, as well as vibrational peaks of C–O–C groups at 1030 cm−1 [25]. These peaks were all continuously enhanced upon increasing the PVA content, and the greatest enhancement was obtained at a PVA content of 2.0%. Moreover, PVA contains many -OH groups, and there were unconsumed -OH groups after the resin was cured, indicating the presence of “free” PVA in P-MUF resins. Therefore, the stronger vibrational peaks at 3340 cm−1 were related to the molecular structure of PVA. The -OH group on the PVA molecular chain could bond with the hydrogen atom of methylol and MUF polycondensation products to generate C–O–C bonds, which improved the cross-link density between resin molecules. In addition, PVA could undergo polycondensation with formaldehyde to form polyvinyl formal (PVF), which contained C–O–C bonds. This reaction could occur intermolecularly and intramolecularly to form a stable structure. PVF was viscous, which decreased the free formaldehyde content, so the viscosity was higher in the P-MUF resins. Compared with the MUF resin and P-MUF resins, more C–O–C bonds were generated in the P-MUF resin than in the MUF resin, which showed that the cured product of P-MUF resin had a high-density cross-linked structure. This was verified by the intensity of the C–O peak in the XPS spectra (Figs. 4b and 4c), which was also the result of PVA being interspersed between MUF macromolecules. More functional groups participated in the reaction upon increasing the PVA content. Therefore, the vibrational peak at 1030 cm−1 increased continuously in the FTIR spectrum, but this did not mean that the formation of a high-density cross-linked structure occurred during synthesis. It was also possible that a cross-linking reaction occurred between the molecules during resin curing, but more evidence is needed to draw firmer conclusions.
Figure 4: Chemical structure analysis: Fourier transform infrared spectra (FTIR) of MUF resins with different PVA contents (a), X-ray photoelectron spectroscopy (XPS) of MUF resins with the mass ratio content of PVA to melamine and urea 0% and 2.0% (b), (c)
The vibration peaks at 2160 and 1660 cm−1 were due to the C = O groups in -N = C = O and -HNCONH-, respectively [26,27]. Upon increasing the PVA content, the vibration peak of -N = C = O was continuously enhanced, and the vibration peak of -HNCONH- was continuously weakened. The cause for this is shown by Eqs. (2)–(4) [28]:
Because the formaldehyde solution contained 8%–15% methanol, it acted as a stabilizer that prevented the precipitation of formaldehyde [29]. During the synthesis of P-MUF resins, through the series of reactions in the above formula, a peak at 2160 cm−1 appeared in the FTIR spectrum. Some urea was consumed, which weakened the peak at 1630 cm−1. The appearance of the -N = C = O group replaced the C = O group in -NHCONH-, so the intensity of the C = O group was unchanged (Figs. 4b and 4c). Due to the highly reactive -N = C = O groups, they might have affected the bonding performance of the P-MUF resin. From FTIR and XPS, it was observed that PVA improved the cross-linked structure of the MUF resin, and new functional groups were observed for P-MUF resin, indicating that the bonding performance of P-MUF resins might have changed.
3.3 Cross-Linked Structure of the MUF Resins and P-MUF Resins
Fig. 5a shows the XRD patterns of the MUF resins with different PVA contents. Each resin had a sharp peak around 21°, with three additional peaks around 24°, 31°, and 40°. The MUF resin had a unique crystalline state, and the above peaks indicated these cured resins’ crystalline regions [30]. The intermolecular cross-linked structure was restrained by the crystallization state of the MUF resin. The cross-linked structure was more seriously affected by hydrogen bonds, as indicated by the more intense crystallization peak, which loosened the structure of the cured resin and affected its bonding performance [31]. However, comparing the crystallization peaks of MUF resin and P-MUF resin showed no obvious changes in the crystalline state of either. This showed that the addition of PVA did not affect the crystalline state of MUF resin and that a high-density cross-linked structure was constructed without changing the crystalline state. This indicated that the P-MUF resin had better bonding performance than the MUF resin, which promoted its bonding with reed particles.
Figure 5: Cross-linked structure analysis: X-ray diffraction (XRD) of MUF resins with different PVA contents (a), differential scanning calorimeter (DSC) of MUF resins with different PVA contents (b)
To verify the formation process of the high-density cross-linked structure of P-MUF resin, dynamic DSC was used to analyze the curing reaction of MUF resins with different PVA contents. Generally, the enthalpy of the curing reaction is represented by the region under the curing transition peak in the DSC curve. Fig. 5b shows the exothermic reaction of MUF resin and P-MUF resin during the curing stage, which was mainly attributed to the reaction between resin groups [32,33]. A greater cross-linking degree of the resin, indicated that fewer groups were involved in the curing stage, and less energy was generated by the curing reaction [34,35]. As shown in Fig. 5b, the enthalpy of the curing reaction by the MUF resin was 155.93 J/g, and the onset temperature was 132.16°C. When the molar ratio of F/(M + U) was 1.10, the enthalpy of the curing reaction of the MUF resin decreased from 155.93 to 134.20 J/g, and the onset temperature decreased from 132.16°C to 115.79°C upon increasing the PVA content. The gradual decrease in the energy generated by the reaction between groups indicated that fewer groups were involved in the curing stage. From the chemical structure (Fig. 4), the ether bond content of P-MUF resin was higher than that of the MUF resin, which was due to the combination of PVA and MUF resin. This shows that the PVA and MUF prepolymer cross-linked during the synthesis of P-MUF resin, increasing the cross-linking degree of the resin. At the same F/(M + U) molar ratio, an increase in the cross-linking degree of the resin means that the functional groups were partially consumed during the synthesis stage, which reduced the reaction degree during curing. Therefore, the groups involved in the curing reaction of P-MUF resin decreased upon increasing the PVA content, and the curing reaction enthalpy decreased. The cross-linked structure of the P-MUF resin was formed successively by a series of synthesis and curing processes and finally formed a high-density cross-linked structure. The lower onset temperature of the curing reaction of P-MUF resin might also promote its curing [36], but this was not the case. In the chemical structure of the P-MUF resin (Fig. 4a), the content of -OH groups increased upon increasing the PVA content, indicating that it contained “free” PVA. The PVA functioned as a protective colloid, and melamine has a stable chemical structure that increased the thermal stability of the resin [37,38]. Therefore, the introduction of PVA reduced the curing reaction rate of the MUF resin, which prolonged the curing time of the resin (Fig. 2c).
3.4 Thermal Properties of the MUF Resins and P-MUF Resins
The thermogravimetric (TG) curve of the P-MUF resin in Fig. 6a showed three distinct stages of mass-loss stages, which were similar to those of the MUF resin. These stages included the decomposition of small molecules of the resin (<220°C and 220°C–295°C) and carbonization (>295°C). These mass-loss stages were also reflected in the corresponding derivative thermogravimetric (DTG) curves (Fig. 6b). The mass loss below 220°C was attributed to water evaporation and the release of some formaldehyde gas. This can be seen in the first peak in the DTG curve of each resin. The water inside the resin evaporated, and some methylene ether bonds in the cross-linked structure decomposed to release formaldehyde gas. Between 220°C and 295°C, the cross-linked structure of the resin rapidly disintegrated, and the mass loss increased rapidly. This was also reflected in the large peak in the DTG curve, which indicated a high loss rate. Above 295°C, the resin was gradually carbonized. The last two stages were attributed to the release of volatiles and further degradation. According to the mass loss rate and residual weight ratio, P-MUF resins showed a higher thermal stability than MUF resin. However, the thermal stability of P-MUF resins increased first and then decreased upon increasing PVA content. This was attributed to the poor thermal stability of PVA itself and the existence of “free” PVA in the P-MUF resin. From the TG curves, the MUF resin with a PVA content of 1.0% had a higher thermal stability but was not significantly different. Thus, the P-MUF resins could be used to prepare reed particleboard without changing any hot-pressing parameters.
Figure 6: Thermal properties: the thermogravimetric (TG) of MUF resins with different PVA contents (a), derivative thermogravimetric (DTG) of MUF resins with different PVA contents (b)
3.5 Mechanical Properties of Reed Particleboard
Fig. 7 shows the mechanical properties of reed particleboards prepared from MUF resins with different PVA contents. The IB reflects the applicability of P-MUF resin to reed particles. Fig. 7c shows that the MUF resin had extremely poor bonding performance to reed particles, and the IB of the reed particleboard was only 0.24 MPa (0.05 MPa), which did not meet the minimum requirements of Chinese standard GB/T 4897–2015. The IB of reed particleboard increased gradually upon increasing the PVA content. When the mass ratio of PVA to melamine and urea was 0.5% to 2.0%, the IB of the prepared reed particleboard was 2.4 to 3.3 times that of the pure MUF resin. The IB of reed particleboard for the mass ratios of PVA to melamine and urea of 0.5%, 1.0%, 1.5% and 2.0% were 0.58 MPa (0.05 MPa), 0.60 MPa (0.04 MPa), 0.70 MPa (0.02 MPa), and 0.79 MPa (0.05 MPa). The bonding strength of all reed particleboard samples (thickness: 8 mm) met the requirements for load-bearing (>0.4 MPa) and heavy-duty (>0.6 MPa) particleboard used in the dry state (Chinese standard GB/T 4897-2015). The non-volatile solids content and curing time of the resins are closely related to the hot-pressing conditions of the wood-based board. The resins with a low non-volatile solids content need a longer hot-pressing time or a higher hot-pressing temperature to evaporate, so the resins can be cured quickly [39,40]. As the curing time of the P-MUF resin was longer than that of the MUF resin (Fig. 2c), it required a longer hot-pressing time or higher hot-pressing temperature during curing. However, the non-volatile solids content of the P-MUF resin was higher than that of the MUF resin (Fig. 2b), and its onset temperature of the curing reaction was lower (Fig. 5b). Therefore, the hot-pressing temperature and hot-pressing time prepared by reed particleboard were set at 170°C and 3 min, respectively, to rapidly form of the board. The IB value of the board shows that the conditions helped the P-MUF resin bond the reed particles.
Figure 7: Effect of MUF resins with different PVA contents on the mechanical properties of reed particleboard: MOR of particleboards (a), MOE of particleboards (b), IB of particleboards (c)
Both the MOR and MOE reflected the bonding performance of the reed particleboard. Figs. 7a and 7b show that the bonding performance of the reed particleboard gradually increased upon increasing the PVA content. Among them, the bending performance of the reed particleboard prepared by the MUF resin performed well, in which the MOR and MOE were 25.16 MPa (0.94 MPa) and 3748 MPa (159.5 MPa), respectively. The bonding performance of all particleboard samples (thickness: 8 mm) met the requirements of China standard GB/T 4897-2015 for heavy-duty (MOR: > 20 MPa; MOE: > 3100 MPa) particleboard used in the dry state. Compared with P-MUF resin, the MOR and MOE were 1.3 and 1.1 times higher than those of the reed particleboard prepared from pure MUF resin when the mass ratio of PVA to melamine and urea was 2.0%. Increasing the PVA content improved the bending performance of the board, but the improvement effect was not significant.
3.6 The Formation Mechanism of the Reed Particleboard
To study the formation mechanism of reed particleboard, the interfacial bonding between reed particle and resin was observed by SEM. Fig. 8a shows the microscopic topography of the raw reed material, which shows the tube wall cells of the reed straw. The surface of the tube wall was relatively smooth and contained pores, which were conducive to moisture absorption and penetration of the resin. Figs. 8b–8f show the microtopography of bonding between the reed particle and resin. Fig. 8b shows that the surface of the reed particle wrinkled due to the presence of cured MUF resin inside it. This showed that MUF resin wet the reed particles. Figs. 8c–8f show that the P-MUF resin was simultaneously cured on the surface and inside of the reed particles. More resin remained on the surface of reed particles upon increasing the PVA content, which may be related to the viscosity of the resin. The reed particles were small and exposed more fibers on the surface, which increased the liquid absorption capacity of the reed particles. Coupled with the low viscosity of the MUF resin, this promoted the absorption of reed particles. The resin penetrated the reed particles’ interior and completed the curing, which produced a poor bond between the particles. However, the viscosity of P-MUF resin increased upon increasing the PVA content, and it slowed the penetration rate of the P-MUF resin into the reed particles. A continuous glue layer was formed between the reed particles so that the P-MUF resin better bonded the reed particles together.
Figure 8: Scanning electron microscopy (SEM) of the adhesion of MUF resins with different PVA contents to reed particles: raw of reed particle (a), reed particles with MUF resins (b), MUF resins with 0.5 wt.% PVA contents (c), MUF resins with 1.0 wt.% PVA contents (d), MUF resins with 1.5 wt.% PVA contents (e), and MUF resins with 2.0 wt.% PVA contents (f)
Figs. 8c–8f show that the surface glue layer of reed particles was severely torn, which indicated that the tensile fracture of the specimen occurred in the glue layer on the surface of the reed particles during the test. Generally, MUF resin is brittle, so it cannot provide good IB for reed particleboard. The MOE reflects the toughness of the board, which increased continuously upon increasing the PVA content. This showed that PVA decreased the brittleness of MUF resin and strengthened the mechanical and tensile properties of the continuous glue layer through the formation of a high-density cross-linked structure.
In this study, a simple alkali-acid-alkali synthetic method was used to chemically cross-link and form a P-MUF resin by PVA and hydroxymethyl groups. The results showed differences between the bonding performance of the MUF resin and P-MUF resin for reed particles. This was attributed to the introduction of PVA, which increased the cross-link density and improved the bonding performance of the MUF resin. SEM observations showed that the P-MUF resin formed a continuous glue layer between reed particles, providing great mechanical properties to the reed particleboard. In particular, the IB of the board was 2.4 to 3.3 times higher than that of the MUF resin and was comparable to that of wood-based particleboard. However, when the mass ratio of PVA to melamine and urea exceeded 2.0%, gelation occurred during resin synthesis, which was not conducive to the preparation of reed particleboard. In addition, FTIR and XPS analyses confirmed that PVA improved the cross-linked structure of the MUF resin, and new functional groups were observed for the P-MUF resin. The crosslink density did not change the unique crystallization behavior. TG analysis confirmed that the thermal properties of the P-MUF resin were similar to those of the MUF resin, which shows that the P-MUF resin can be used to prepare reed particleboard without changing any hot-pressing parameters. In summary, it is highly feasible to use P-MUF resin to prepare reed particleboard for custom furniture and engineering materials. The reed materials can be used as a substitute for wood-based materials to slow the consumption of forest resources.
Funding Statement: This work was supported by the Hunan Province Science and Technology Major Project [2021NK1050]; Strategic Research and Consulting Project of the Chinese Academy of Engineering: Research on Green and Low-Carbon Technology Innovation Strategy of Wood-Based Panel Industry [2022-XY-62]; Changsha Science and Technology Project [kq2004096]; Hunan Provincial Technical Innovation Platform and Talent Program in Science and Technology [2016TP1013]. The authors thank the Hunan Key Discipline of Forestry Engineering of Central South University of Forestry and Technology, Hunan Engineering Research Center of Bamboo and Wood Processing, Hunan Engineering Research Center of Bamboo Industry, Provincial and Ministerial Co-Construction Collaborative Innovation Center for High-Efficiency Utilization of Wood and Bamboo Resources, and the Key Laboratory of Biomass Composite Materials in ordinary colleges and universities in Hunan Province provides the platform.
Conflicts of Interest: The authors declare that they have no conflicts of interest to report regarding the present study.
References
1. Neitzel, N., Hosseinpourpia, R., Walther, T., Adamopoulos, S. (2022). Alternative materials from agro-industry for wood panel manufacturing—A review. Materials, 15(13), 4542. https://doi.org/10.3390/ma15134542 [Google Scholar] [PubMed] [CrossRef]
2. Hýsková, P., Hýsek, Š., Schönfelder, O., Šedivka, P., Lexa, M. et al. (2020). Utilization of agricultural rests: Straw-based composite panels made from enzymatic modified wheat and rapeseed straw. Industrial Crops and Products, 144, 112067. https://doi.org/10.1016/j.indcrop.2019.112067 [Google Scholar] [CrossRef]
3. Tupciauskas, R., Rizhikovs, J., Grinins, J., Paze, A., Andzs, M. et al. (2019). Investigation of suberinic acids-bonded particleboard. European Polymer Journal, 113, 176–182. https://doi.org/10.1016/j.eurpolymj.2019.01.061 [Google Scholar] [CrossRef]
4. Zhou, L., Zhou, G., Liu, S., Sui, X. (2010). Seasonal contribution and interannual variation of evapotranspiration over a reed marsh (Phragmites australis) in Northeast China from 3-year eddy covariance data. Hydrological Processes, 24(8), 1039–1047. https://doi.org/10.1002/hyp.7545 [Google Scholar] [CrossRef]
5. Kabbaj, K., Mahi, M., Saoiabi, A. (2013). Influence of environmental parameters on reed beds in wastewater treatment in a small community in Morocco. Journal of Water Reuse and Desalination, 3(2), 169–174. https://doi.org/10.2166/wrd.2013.068 [Google Scholar] [CrossRef]
6. Caparrós, S., Ariza, J., Hernanz, D., Díaz, M. J. (2006). Arundo donax L. valorization under hydrothermal and pulp processing. Industrial & Engineering Chemistry Research, 45(9), 2940–2948. https://doi.org/10.1021/ie0580811 [Google Scholar] [CrossRef]
7. Flores, J. A., Pastor, J. J., Martinez-Gabarron, A., Gimeno-Blanes, F. J., Rodríguez-Guisado, I. et al. (2011). Arundo donax chipboard based on urea-formaldehyde resin using under 4 mm particles size meets the standard criteria for indoor use. Industrial Crops and Products, 34(3), 1538–1542. https://doi.org/10.1016/j.indcrop.2011.05.011 [Google Scholar] [CrossRef]
8. Trischler, J., Sandberg, D. (2014). Monocotyledons in particleboard production: Adhesives, additives and surface modification of reed canary grass. BioResources, 9(3), 3919–3938. https://doi.org/10.15376/BIORES.9.3.3919-3938 [Google Scholar] [CrossRef]
9. Andreu-Rodriguez, J., Medina, E., Ferrandez-Garcia, M. T., Ferrandez-Villena, M., Ferrandez-Garcia, C. E. (2013). Agricultural and industrial valorization of Arundo donax L. Communications in Soil Science and Plant Analysis, 44(1–4), 598–609. https://doi.org/10.1080/00103624.2013.745363 [Google Scholar] [CrossRef]
10. Ferrandez-García, M. T., Ferrandez-Garcia, M., Garcia-Ortuño, T., Ferrandez-Garcia, C. E., Ferrandez-Vill, M. (2020). Assessment of the physical, mechanical and acoustic properties of Arundo donax L. biomass in low pressure and temperature particleboards. Polymers, 12(6), 1361. https://doi.org/10.3390/polym12061361 [Google Scholar] [PubMed] [CrossRef]
11. Liu, M., Wang, Y., Wu, Y., Wan, H. (2018). Hydrolysis and recycling of urea formaldehyde resin residues. Journal of Hazardous Materials, 355, 96–103. https://doi.org/10.1016/j.jhazmat.2018.05.019 [Google Scholar] [PubMed] [CrossRef]
12. Dunky, M. (1998). Urea-formaldehyde (UF) adhesive resins for wood. International Journal of Adhesion and Adhesives, 18(2), 95–107. https://doi.org/10.1016/S0143-7496(97)00054-7 [Google Scholar] [CrossRef]
13. Wibowo, E. S., Park, B. D., Causin, V. (2021). Recent advances in urea-formaldehyde resins: Converting crystalline thermosetting polymers back to amorphous ones. Polymer Reviews, 62(4), 1–35. https://doi.org/10.1080/15583724.2021.2014520 [Google Scholar] [CrossRef]
14. Wibowo, E. S., Park, B. D., Causin, V. (2020). Hydrogen-bond-induced crystallization in low-molar-ratio urea-formaldehyde resins during synthesis. Industrial & Engineering Chemistry Research, 59(29), 13095–13104. https://doi.org/10.1021/acs.iecr.0c02268 [Google Scholar] [CrossRef]
15. Siimer, K., Kaljuvee, T., Pehk, T., Lasn, I. (2010). Thermal behaviour of melamine-modified urea-formaldehyde resins. Journal of Thermal Analysis and Calorimetry, 99(3), 755–762. https://doi.org/10.1007/s10973-009-0617-z [Google Scholar] [CrossRef]
16. Park, B. D., Lee, S. M., Roh, J. K. (2009). Effects of formaldehyde/urea mole ratio and melamine content on the hydrolytic stability of cured urea-melamine-formaldehyde resin. European Journal of Wood and Wood Products, 67(1), 121–123. https://doi.org/10.1007/s00107-008-0277-x [Google Scholar] [CrossRef]
17. Hua, L. S., Ashaari, Z., Chen, L. W., San, H. P., Peng, T. L. et al. (2015). Properties of particleboard with oil palm trunk as core layer in comparison to three-layer rubberwood particleboard. Journal of Oil Palm Research, 27(1), 67–74. https://doi.org/10.13140/RG.2.1.3003.2801 [Google Scholar] [CrossRef]
18. Park, S., Jeong, B., Park, B. D. (2021). A comparison of adhesion behavior of urea-formaldehyde resins with melamine-urea-formaldehyde resins in bonding wood. Forests, 12(8), 1037. https://doi.org/10.3390/f12081037 [Google Scholar] [CrossRef]
19. Wang, Y., Gao, Z., Guan, S., Ye, Z., Yu, Z. et al. (2016). Trifunctional cross-linker trimethylol melamine enhancing adhesive force of PVA hydrogels. Journal of Applied Polymer Science, 133(31), 43774. https://doi.org/10.1002/app.43774 [Google Scholar] [CrossRef]
20. Liu, Y., Yuan, J., Zhao, X., Ye, L. (2018). Reactive toughening of urea-formaldehyde resin with poly(vinyl alcohol) by formation of interpenetrating networks. Polymer Engineering and Science, 58(11), 2031–2038. https://doi.org/10.1002/pen.24814 [Google Scholar] [CrossRef]
21. Han, D., Guo, Z., Chen, S., Xiao, M., Peng, X. et al. (2018). Enhanced properties of biodegradable poly (propylene carbonate)/polyvinyl formal blends by melting compounding. Polymers, 10(7), 771. https://doi.org/10.3390/polym10070771 [Google Scholar] [PubMed] [CrossRef]
22. Hse, C. Y., Higuchi, M. (2010). Melamine-bridged alkyl resorcinol modified urea-formaldehyde resin for bonding hardwood plywood. Journal of Applied Polymer Science, 116(5), 2840–2845. https://doi.org/10.1002/app.31766 [Google Scholar] [CrossRef]
23. Kamke, F. A., Lee, J. N. (2007). Adhesive penetration in wood—A review. Wood and Fiber Science, 39(2), 205–220. https://doi.org/10.1007/s10086-006-0884-2 [Google Scholar] [CrossRef]
24. He, Z., Chapital, D. C., Cheng, H. N., Dowd, M. K. (2014). Comparison of adhesive properties of water-and phosphate buffer-washed cottonseed meals with cottonseed protein isolate on maple and poplar veneers. International Journal of Adhesion and Adhesives, 50, 102–106. https://doi.org/10.1016/j.ijadhadh.2014.01.019 [Google Scholar] [CrossRef]
25. Wang, W., Li, Y., Wang, Y., Huang, W., Lv, L. et al. (2021). A novel covalently grafted binder through in-situ polymerization for high-performance Si-based lithium-ion batteries. Electrochimica Acta, 400, 139442. https://doi.org/10.1016/j.electacta.2021.139442 [Google Scholar] [CrossRef]
26. Sánchez-Ferrer, A., Soprunyuk, V., Engelhardt, M., Stehle, R., Gilg, H. A. et al. (2021). Polyurea networks from moisture-cure, reaction-setting, aliphatic polyisocyanates with tunable mechanical and thermal properties. ACS Applied Polymer Materials, 3(8), 4070–4078. https://doi.org/10.1021/acsapm.1c00578 [Google Scholar] [CrossRef]
27. Liu, M., Wang, Y., Wu, Y., He, Z., Wan, H. (2018). “Greener” adhesives composed of urea-formaldehyde resin and cottonseed meal for wood-based composites. Journal of Cleaner Production, 187, 361–371. https://doi.org/10.1016/j.jclepro.2018.03.239 [Google Scholar] [CrossRef]
28. Alonso-Buenaposada, I. D., Rey-Raap, N., Calvo, E. G., Menéndez, J. A., Arenillas, A. (2015). Effect of methanol content in commercial formaldehyde solutions on the porosity of RF carbon xerogels. Journal of Non-Crystalline Solids, 426, 13–18. https://doi.org/10.1016/j.jnoncrysol.2015.06.017 [Google Scholar] [CrossRef]
29. Lei, C., Wang, Q., Li, L. (2009). Effect of interactions between poly(vinyl alcohol) and urea on the water solubility of poly(vinyl alcohol). Journal of Applied Polymer Science, 114(1), 517–523. https://doi.org/10.1002/app.30504 [Google Scholar] [CrossRef]
30. Ding, Z., Ding, Z., Ma, T., Zhang, H. (2020). Condensation reaction and crystallization of urea-formaldehyde resin during the curing process. BioResources, 15(2), 2924–2936. https://doi.org/10.15376/BIORES.15.2.2924-2936 [Google Scholar] [CrossRef]
31. Wibowo, E. S., Park, B. D. (2022). Enhancing adhesion of thermosetting urea-formaldehyde resins by preventing the formation of H-bonds with multi-reactive melamine. The Journal of Adhesion, 98(3), 257–285. https://doi.org/10.1080/00218464.2020.1830069 [Google Scholar] [CrossRef]
32. Chen, Y., Xiao, H., Xie, J., Qi, J., Li, J. et al. (2017). Qualitative analysis of pre-curing process of UF resin. Thermochimica Acta, 653, 43–48. https://doi.org/10.1016/j.tca.2017.03.026 [Google Scholar] [CrossRef]
33. Zhang, Y., Yang, C., Zheng, J., Lu, M. (2015). Crystallization behavior of stable urea formaldehyde resin dispersed by polyvinyl alcohol. Iranian Polymer Journal, 24(1), 13–20. https://doi.org/10.1007/s13726-014-0295-y [Google Scholar] [CrossRef]
34. Ding, Z., Ding, Z., Liu, J., Xie, Y., Yang, F. (2022). Derivative thermogravimetric analysis curve for characterizing the curing process of urea-formaldehyde resins. International Journal of Adhesion and Adhesives, 117, 103184. https://doi.org/10.1016/j.ijadhadh.2022.103184 [Google Scholar] [CrossRef]
35. Dazmiri, M. K., Kiamahalleh, M. V., Dorieh, A., Pizzi, A. (2019). Effect of the initial F/U molar ratio in urea-formaldehyde resins synthesis and its influence on the performance of medium density fiberboard bonded with them. International Journal of Adhesion and Adhesives, 95, 102440. https://doi.org/10.1016/j.ijadhadh.2019.102440 [Google Scholar] [CrossRef]
36. Chen, Y., Xiao, H., Xu, S., Liu, F., Xie, J. et al. (2018). Significant evaluation of three factors affecting the pre-curing behavior of urea formaldehyde resin: Temperature, solid content, and pH. Journal of Thermal Analysis and Calorimetry, 133(3), 1463–1470. https://doi.org/10.1007/s10973-018-7187-x [Google Scholar] [CrossRef]
37. Kijowska, D., Jankowski, P., Wierzbicka, E. (2019). Halloysite modified by melamine cyanurate and its compositions based on PA6. Polimery, 64(4), 259–266. https://doi.org/10.14314/polimery.2019.4.3 [Google Scholar] [CrossRef]
38. Lei, H., Frazier, C. E. (2015). Curing behavior of melamine-urea-formaldehyde (MUF) resin adhesive. International Journal of Adhesion and Adhesives, 62, 40–44. https://doi.org/10.1016/j.ijadhadh.2015.06.013 [Google Scholar] [CrossRef]
39. Gao, Z., Wang, X., Wan, H., Liu, Z. (2009). DSC characterisation of urea-formaldehyde (UF) resin curing. Pigment & Resin Technology, 38(1), 3–9. https://doi.org/10.1108/03699420910923526 [Google Scholar] [CrossRef]
40. Xing, C., Zhang, S., Deng, J., Wang, S. (2007). Urea-formaldehyde-resin gel time as affected by the pH value, solid content, and catalyst. Journal of Applied Polymer Science, 103(3), 1566–1569. https://doi.org/10.1002/app.25343 [Google Scholar] [CrossRef]
Cite This Article
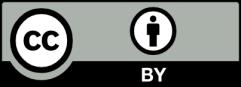