Open Access
ARTICLE
Repair of Second-Generation Recycled Fine Aggregate of Waste Concrete from Freeze-Thaw Environment by Carbonation Treatment
School of Building Engineering, Taizhou Polytechnic College, Taizhou, 225300, China
* Corresponding Author: Jie Huang. Email:
Journal of Renewable Materials 2024, 12(1), 187-201. https://doi.org/10.32604/jrm.2023.044232
Received 24 July 2023; Accepted 25 September 2023; Issue published 23 January 2024
Abstract
The reuse of waste recycled concrete from harsh environments has become a research hotspot in the field of construction. This study investigated the repair effect of carbonation treatment on second-generation recycled fine aggregate (SRFA) obtained from recycled fine aggregate concrete (RFAC) subjected to freeze-thaw (FT) cycles. Before and after carbonation, the properties of SRFA were evaluated. Carbonated second-generation recycled fine aggregate (CSRFA) at five substitution rates (0%, 25%, 50%, 75%, 100%) to replace SRFA was used to prepare carbonated second-generation recycled fine aggregate concrete (CSRFAC). The water absorption, porosity and mechanical properties of CSRFAC were tested, and its frost-resisting durability was evaluated. The results showed after carbonation treatment, the physical properties of SRFA was improved and met the requirements of II aggregate. The micro-hardness of the interfacial transition zone and attached mortar in CSRFA was 50.5% and 31.2% higher than that in SRFA, respectively. With the increase of CSRFA replacement rate, the water absorption and porosity of CSRFAC gradually decreased, and the mechanical properties and frost resistance of CSRFAC were gradually improved. Carbonation treatment effectively repairs the damage of SRFA caused by FT cycles and improves its application potential.Keywords
Consumption of non-renewable resources, such as natural aggregate and cementitious materials, has continuously increased as a result of the growing urbanization and industrialization of emerging nations in recent years. As a result, there has been significant environmental damage and an enormous buildup of construction waste. In China alone, the total amount of construction waste generated each year has exceeded 2 billion tons [1]. Therefore, the disposal of construction waste has become an urgent issue to address. Given that waste concrete makes up a sizeable fraction of construction waste [2], obtaining recycled aggregate (RA) from it to prepare concrete is a potential strategy to conserve natural resources and encourage the reuse of waste concrete [3,4]. This strategy is essential for encouraging the effective use of construction waste and attaining sustainable growth within the construction industry.
Freeze-thaw (FT) damage is the primary factor in the degradation and spalling of concrete buildings in cold climates [5]. This damage is primarily caused by the concrete pore solution’s volume expanding, which causes expansion pressure to act on the capillary wall [6]. The FT cycles cause the capillary wall to gradually erode under periodic pressure, which in turn leads to the deterioration of mechanical properties and frost-resisting durability of concrete. It is generally believed that concrete with weak frost-resisting durability is not appropriate for recycling, resulting in low utilization of waste concrete in cold regions and the substantial environmental pollution caused by the stacking of waste concrete [7]. Therefore, exploring and enhancing the recycling potential of frost-resisting durability failure concrete can help to further increase the pace at which resources are utilized for construction waste, as well as address the environmental and ecological issues that construction waste raises.
The old cement mortar adheres to the surface of the original aggregate, resulting in multiple interfacial transition zones (ITZ) formed inside the RA [8]. The loose and porous attached mortar (AM) and ITZ lead to the defects of low density, high water absorption and high crushing value of RA [9]. RA produced by recycled aggregate concrete (RAC) subjected to FT cycles frequently has more flaws and is of worse quality [10]. Additionally, the addition of RA has a negative effect on the performance of concrete. Compared with natural aggregate concrete, the splitting tensile strength of RAC was reduced by 30%–40% [11], and the compressive strength was reduced by 30% [12]. Kou et al. [13] reported that the incorporation of RA reduced the chloride ion penetration resistance of RAC. Benignantly, when the replacement rate of recycled coarse aggregate (RCA) was not more than 20%, it can be utilized to create concrete [14], and recycled fine aggregate (RFA) was also allowed to be used to prepare structural concrete to some extent [15]. In recent years, RAC has been favored and will be widely used. RAC will turn into new waste concrete whenever it fails or reaches the end of its service life. The preparation of second-generation RA and second-generation RAC from waste RAC can save natural resources, alleviate environmental crisis and generate considerable economic benefits [16]. As expected, studies have revealed that the second-generation RCA’s physical characteristics were inferior to those of the first generation [17]. Wei et al. [5] reported that the FT damage threshold of RAC based on type II and type III RCA was 0.085 and 0.359, respectively. It is well known that the performance of RA is critical to the mechanical and durability of RAC in complex environments. However, the performance and utilization potential of second-generation recycled fine aggregate (SRFA) are rarely reported. Therefore, in order to safeguard the environment and promote the sustainable development of the construction industry, it is essential to investigate the performance of RFA from RAC affected by FT cycles.
In order to increase the utilization rate of SRFA and broaden its application range, it is crucial to modify SRFA and improve its performance. In recent years, researchers have found that the performance of RA can be improved after carbonation [18,19]. Carbonation modification treatment can not only enhance the performance of RA, but also effectively use cement-based materials to absorb carbon dioxide [20]. The carbonation treatment based on RA performance enhancement efficiently boosts RA’s sequestration of carbon in the environment while simultaneously reducing carbon emissions. Consequently, it is an environmentally friendly RA performance improvement method with high sustainability. Additionally, the use of carbonated RA to prepare concrete has emerged as a crucial technique to raise the rate at which waste concrete is used. The strength and elastic modulus of concrete prepared by carbonated RCA were significantly improved compared with RAC [21,22]. After 50 and 300 FT cycles, carbonated RCA produced concrete had a lower mass loss rate and a higher relative dynamic elastic modulus (RDEM) than RAC [23,24]. There are few reports on the improvement of RFA by carbonation treatment, especially low-quality RFA, such as SRFA. Therefore, it is of great significance to improve the performance of SRFA by carbonation treatment to promote the utilization of waste RAC.
The purpose of this study was to investigate the effectiveness of carbonation treatment in repairing SRFA from recycled fine aggregate concrete (RFAC) exposed to FT cycles. In particular, the physical properties, micro-hardness, and microscopic features of SRFA before and after carbonation were specifically examined. Carbonated second-generation recycled fine aggregate (CSRFA) was used to prepare concrete at five substitution rates (0%, 25%, 50%, 75%, 100%) to replace SRFA. And the porosity and water absorption of RFAC and carbonated second-generation recycled fine aggregate concrete (CSRFAC) were tested. The mechanical properties and frost-resisting durability of CSRFAC were thoroughly evaluated. The research gap could be filled, which provides a theoretical basis for improving the utilization rate of waste concrete in FT environment.
Fig. 1 is the preparation process of SRFA. In order to simulate the working state of concrete in cold regions, a fast FT cycle test was carried out until RFAC failed. By using a two-stage crushing procedure for waste RFAC in FT environment, SRFA with a particle size of 0.15–4.75 mm was produced. Limestone gravel with a particle size of 5–20 mm was produced in Taizhou, Jiangsu Province as natural coarse aggregate (NCA), and Table 1 lists its physical characteristics. In Fig. 2, the grading curves for SRFA and RFA are displayed, with their gradation in line with class II aggregate.
Figure 1: Schematic for the preparation process of SRFA
Figure 2: Gradation curves
The apparent density of P⋅O 42.5 Portland cement produced by Jiangsu Yangzi Cement Co., Ltd. (China), was 3020 kg/m3. In order to improve the workability and frost resistance durability of concrete, fly ash (FA), silica fume (SF) and slag (SL) were added as mineral admixtures. Table 2 provides a list of the chemical compositions of cementitious materials. In addition, a polycarboxylate superplasticizer (SP) with a water reduction efficiency of 35% and an air entraining agent (AEA) were used as admixtures for concrete.
The temperature of 20°C ± 2°C and the relative humidity of 50% ± 5% are widely considered to be suitable for the carbonation of RA [10,18,25]. According to previous studies, a slight increase in gas pressure was beneficial to increase the carbonation degree of RA [26]. Thus, SRFA was carbonated at a temperature of 20°C ± 2°C, a relative humidity of 50% ± 5%, and a pressure of 0.01 MPa in a carbonation chamber filled with 99.9% carbon dioxide gas until the weight of SRFA was constant. After carbonation treatment, CSRFA was taken out for physical and mechanical properties test.
2.3 Mixture Proportions and Sample Preparation
CSRFAC with a target strength of 40 MPa was prepared by full calculation method [27] and frost resistance mix design method [28] using corresponding CSRFA with different replacement rates (0%, 25%, 50%, 75%, and 100%) to replace SRFA, labeled as CSRFAC0, CSRFAC25, CSRFAC50, CSRFAC75, and CSRFAC100, respectively. Considering the high water absorption of CSRFA and RFA, the amount of water absorbed by CSRFA and RFA at 30 min was added as additional water to ensure the workability of fresh CSRFAC. The mix proportions of RFAC and CSRFAC are shown in Table 3. The simulated CSRFAC and RFAC were used in a FT environment, AEA was added to improve the frost resistance of concrete. In order to reduce the effect of AEA on the porosity and strength of CSRFAC and RFAC, AEA was not added to CSRFAC and RFAC for physical and mechanical properties tests. The concrete mixing process was completed by a two-steps mixing method in order to fully mix the raw materials [29]. After stirring, the mixture was poured into 100 mm × 100 mm × 100 mm and 100 mm × 100 mm × 400 mm molds. The samples were demolded after 24 h and then placed in the standard curing chamber (20°C ± 2°C, RH > 95%) for 28 d.
2.4.1 Physical Properties of Aggregate
The physical properties of RFA, SRFA, and CSRFA, including apparent density, bulk density, crushing value, soundness and strength ratio (recycled mortar) and water demand ratio (recycled mortar) were examined in accordance with GB/T 25176-2010 [30]. The physical properties of NCA, including water absorption, apparent density and crushing value were examined in accordance with GB/T 14685-2022 [31].
The AM content of SRFA was determined by high temperature heat treatment method [32]. The specific steps in this method are as follows: a dry sample of SRFA (M0) was submerged in water for 2 h to reach a saturated state; the saturated sample was subsequently heated at 500°C for 3 h; it was then instantly submerged in cold water; the remaining mortar surrounding SRFA was further removed with a stiff brush after the cooling process; then, the mass of fine aggregate above 0.15 mm excluding quartz (M1) was then obtained. The AM content in SRFA was calculated by formula (1).
In order to detect the micro-structural mechanical properties of SRFA before and after carbonation treatment, the micro-hardness of ITZ and AM were tested by Vickers hardness tester. The samples with a size of about 5 mm × 5 mm × 3 mm were prepared for micro-hardness test. The surface of each sample was polished to identify the diamond indentation. The prepared samples were put on the Vickers indenter to find the ITZ. Then, the ITZ was subjected to an indentation operation for 10 s under a load of 10 g. The value was the average of three measurements.
Scanning electron microscopy (SEM) was used to observe the micro-pores and micro-cracks of RFA, SRFA and CSRFA with a size of 5 mm × 5 mm × 3 mm. Thermogravimetry (TG) was used to measure the mass change of the sample during the heating process with a heating rate of 10°C/min.
2.4.4 Water Absorption and Porosity of Concrete
The porosity of RFAC and CSRFAC were tested by ASTM C642-21 [33]. The water absorption of RFAC and CSRFAC was tested according to the Chinese standard GB/T 50081-2019 [34]. In order to ensure the accuracy of the test results, the average values of the three groups of test results were taken to guarantee the correctness of the results.
According to Chinese standard GB/T 50107-2010 [35], RFAC and CSRFAC with the size of 100 mm × 100 mm × 100 mm were conducted to determine the compressive strength and splitting tensile strength; RFAC and CSRFAC with the size of 100 mm × 100 mm × 400 mm were used for the flexural strength test and elastic modulus test.
The rapid FT test of CSRFAC with the size of 100 mm × 100 mm × 400 mm was carried out according to the Chinese standard GB/T 50082-2009 [36]. The fast FT test was conducted at a temperature range of −18°C ± 2°C~5°C ± 2°C. The mass loss rate and RDME of the specimen were measured every 50 FT cycles to evaluate the frost resistance durability of CSRFAC.
3.1 Properties of RFA, SRFA and CSRFA
Fig. 3 displays the physical properties of RFA, SRFA, and CSRFA. Compared with RFA, the apparent density, bulk density and strength ratio (recycled mortar) of SRFA decreased significantly, while the crushing value, soundness and water demand ratio (recycled mortar) increased. The soundness of SRFA cannot meet the requirements of class III aggregate in GB/T 25176-2010 [30], which is attributed to the damage process of FT cycles on the compact structure of hydration products [37]. The FT cycles made the bonding mortar of RFAC become porous and its bonding performance decreased, which directly led to the deterioration of the quality of SRFA. This also indicated that with the increase of the number of cycles, the quality of SRFA gradually decreased or even cannot be used in structural concrete, which is similar to the research results of recycled coarse aggregate [10]. Beneficially, carbonation treatment can make up for the deficiency of SRFA performance. Compared with SRFA, the apparent density, bulk density and strength ratio of CSRFA increased by 2.4%, 2.4% and 6.2%, respectively; and crushing value, soundness and water demand ratio decreased by 14.6%, 19.0% and 8.8%, respectively. indicating that CSRFA met the requirements of class II aggregate in GB/T 25176-2010 [30]. Consequently, carbonation treatment effectively refines the pore structure of SRFA, enhances its grade, and properly repairs the SRFA damage caused by FT cycles.
Figure 3: Physical properties of RFA, SRFA, and CSRFA: (a) apparent density; (b) bulk density; (c) crushing value; (d) soundness; (e) strength ratio of recycled mortar; (f) water demand ratio of recycled mortar
Fig. 4 illustrates the micro-hardness of ITZ and AM in RFA, SRFA, and CSRFA. Before carbonation, ITZ had a considerably lower micro-hardness than AM. Following carbonation treatment, the micro-hardness of ITZ and AM increased. The micro-hardness of ITZ and AM in CSRFA was 50.5% and 31.2% higher than that in SRFA, respectively. The research findings are consistent with previous results indicating that ITZ is significantly improved by carbonation treatment more than AM [38]. Only 8.3% and 9.5% less AM and ITZ were found in the CSRFA compared to the RFA, respectively. ITZ and AM were improved by carbonation treatment, according to the findings of the micro-hardness examination. This is because the carbonation products fill the pores and increase the density of the SRFA [19], which enhances the performance of SRFA.
Figure 4: Micro-hardness of RFA, SRFA, and CSRFA
Fig. 5 presents the DTG curves of AM from SRFA and CSRFA. The DTG curves in Fig. 5 displayed a significant reduction of the calcium hydroxide (Ca(OH)2) peak, suggesting the carbonation reaction of Ca(OH)2 occurred during the carbonation treatment process. Previous research has shown that Ca(OH)2 decomposes between 450°C and 550°C, whereas the decomposition of calcium carbonate (CaCO3) commences at 550°C and ends at 950°C [39,40]. The findings of the TG curves revealed that the mass loss resulting from CaCO3 decomposition in AM of SRFA and CSRFA was 5.6% and 7.1%, respectively. Hence, the carbon dioxide absorption of SRFA corresponded to 1.5% of AM mass. The findings of the heat treatment revealed that SRFA had an AM content of 74.6%. As a result, 11.2 kg of carbon dioxide may be absorbed by 1 ton of SRFA. This implies that carbonation treatment of RFA not only enhances the SRFA quality but also absorbs carbon dioxide emitted by cement and steel industries.
Figure 5: DTG curves of AM from RFA and CRFA
Fig. 6 depicts the microscopic SEM image of RFA, SRFA, and CSRFA. It can be seen from Fig. 6a that the integrity of RFA was preferable, and no obvious cracks and holes were found. Fig. 6b shows the loose structure of un-carbonated SRFA, and micro-pore and numerous micro-cracks produced by FT cycles were observed. This damage to the microstructure results in the deterioration of the macroscopic physical properties of SRFA. Fig. 6c displays that CSRFA has micro-crack that was not apparent and the harmful micro-pores were filled. A significant number of CaCO3 crystals appeared, and the microstructure of CSRFA became dense, indicating the enhancement of SRFA physical properties. According to Fig. 6, carbonation treatment effectively improves the structure of SRFA and compensates for the serious damage caused by FT to SRFA, despite the fact that the microstructure of CSRFA is inferior to that of RFA.
Figure 6: SEM images: (a) RFA; (b) SRFA; (c) CSRFA
3.2 Water Absorption and Porosity of RFAC and CSRFAC
Fig. 7 shows the water absorption and porosity of RFAC and CSRFAC. Fig. 7a illustrates water absorption of RFAC and CSRFAC. As evidenced by the graph, the water absorption of concrete specimens reached a state of stability after 48 h. At the 72 h mark, the water absorption rates for RFAC, CSRFAC0, CSRFAC25, CSRFAC50, CSRFAC75 and CSRFAC100 were 3.55%, 4.32%, 4.18%, 4.01%, 3.86% and 3.68%, respectively. It is evident that with the increase of CSRFA replacement rate, the water absorption of CSRFAC gradually decreased. Notably, the water absorption rate of CSRFAC100 was only 3.7% higher than that of RFAC and 14.8% lower than that of CSRFAC0. Additionally, Fig. 7b displays the porosity of RFAC and CSRFAC. An increase in porosity can lead to greater water absorption for concrete [10]. The reduction in CSRFAC porosity caused by an increase in CSRFA substitution rate is analogous to the results of water absorption. The porosity of CSRFAC decreased to 11.4%, nearly matching that of RFAC (9.6%), when the CSRFA replacement rate was 100%. The porosity of CSRFAC100 was 26.9% lower than that of CSRFAC0. The porosity and water absorption of CSRFAC were decreased as the substitution rate of CSRFA increased. Carbonation treatment of SRFA has a positive effect on improving the internal structure of CSRFAC, reducing the porosity of CSRFAC and further reducing the water absorption.
Figure 7: (a) Water absorption of RAC, RFAC and CRFAC and (b) porosity
3.3 Mechanical Performance of RFAC and CSRFAC
Measurements of the mechanical properties of RFAC and CSRFAC were made in order to more accurately gauge the repair of carbonation treatment on SRFA. Fig. 8 demonstrates the mechanical properties of RFAC and CSRFAC, encompassing compressive strength, splitting tensile strength, flexural strength, and elastic modulus. The results show that RFAC had the maximum strength and elastic modulus of all the concrete samples, as was to be expected. The mechanical properties of CSRFAC steadily improved as the rate of CSRFA replacement increased. Notably, the compressive strengths of CSRFAC0 and CSRFAC100 were 40.2 and 43.6 MPa in Fig. 8a, respectively, marking a 13.9% and 6.6% decrease in comparison to RFAC, respectively. The split tensile strengths of CSRFAC0 and CSRFAC100 were 2.6 and 3.3 MPa in Fig. 8b, which were 36.6% and 19.5% lower than that of RFAC, respectively. Similarly, the flexural strengths of CSRFAC0 and CSRFAC100 were 3.4 and 4.1 MPa in Fig. 8c, respectively, representing a 26.1% and 10.9% reduction from that of RFAC. ITZ is regarded as the most vulnerable region in concrete, with a significant impact on the microstructure and performance of concrete [41]. Weak ITZ and porous AM contribute to the poor physical properties of SRFA, which reduces bonding between SRFA and mortar in CSRFAC. Therefore, CSRFAC is prone to damage when subjected to external forces. The carbonation treatment improves the physical properties of SRFA, strengthens the ITZ in CSRFAC, and enhances its strength significantly. From Fig. 8d, the elastic modulus of CSRFAC0 and CSRFAC100 was 20.5% and 8.7% lower than that of RFAC, respectively. This is largely due to the loose porosity and ITZ of AM, as well as the low elastic modulus of SRFA. The micro-cracks found inside the SRFA further contributed to the stiffness reduction of aggregate-mortar composite system. The elastic modulus of CSRFAC100 was 14.9% higher than that of CSRFAC0, which can be attributed to the enhancement of AM and ITZ due to the filling of carbonation products.
Figure 8: Mechanical performance of RFAC and CSRFAC: (a) compressive strength; (b) splitting tensile strength; (c) flexural strength; (d) elastic modulus
The research on the frost resistance of CSRFAC can more comprehensively evaluate the application potential of SRFA before and after carbonation treatment. The mass loss rate and RDEM of CSRFAC are shown in Fig. 9. As the number of FT cycles increased, the mass loss rate of CSRFAC gradually increased, while RDEM decreased, indicating that the degree of damage to the internal structure of CSRFAC gradually increased. This behavior change is similar to that of ordinary concrete and recycled coarse aggregate concrete in FT environment. The mass loss rate of CSRFAC after 350 FT cycles reduced from 4.88% to 3.45% as the CSRFA substitution rate went from 0% to 100%, while RDEM increased from 50.4% to 62.2%. The mass loss rates of CSRFAC were less than 5%, indicating that there was no FT failure based on mass loss rate [36]. However, the RDEM of CSRFAC0, CSRFAC25, CSRFAC50 and CSRFAC100 were 50.4%, 55.6%, 57.5% and 58.8%, respectively, which were lower than 60%, indicating that these samples cannot meet the requirements of 350 FT cycles [36]. It can be seen from Fig. 9b that the relationship between RDEM and the number of FT cycles conformed to the quadratic function. According to the fitting formulas, when the RDEM was 60%, the number of FT cycles experienced by CSRFAC0, CSRFAC25, CSRFAC50, CSRFAC75 and CSRFAC100 was 291, 313, 322, 334, and 352, respectively. Compared with CSRFAC0, the frost resistance life of CSRFAC25, CSRFAC50, CSRFAC75 and CSRFAC100 was increased by 7.6%, 10.7%, 14.8% and 20.9%, respectively.
Figure 9: (a) Mass loss rate and (b) RDEM
The primary objective of this study was to investigate the effectiveness of carbonation treatment in repairing SRFA from RFAC exposed to FT cycles. In particular, the physical properties, micro-hardness, and composition of SRFA before and after carbonation were examined and the microscopic features were observed. CSRFAC was prepared by CSRFA at five substitution rates (0%, 25%, 50%, 75%, 100%). And the porosity and mechanical properties of RFAC and CSRFAC were thoroughly evaluated. During 350 FT cycles, the mass loss rate and RDEM of CSRFAC were tested. The findings are summarized as follows:
1. After carbonation treatment, SRFA met the requirements of class II aggregate. The micro-hardness of ITZ and AM in CSRFA was 50.5% and 31.2% higher than that in SRFA, respectively, and only 8.3% and 9.5% lower than that in RFA, respectively. Carbonation treatment effectively refines the pore structure of SRFA due to the filling of carbonation products and improves the application level of SRFA.
2. With the increase of CSRFA replacement rate, the water absorption and porosity of CSRFAC gradually decreased and mechanical properties were gradually improved. The water absorption rate and porosity of CSRFAC100 were 14.8% and 26.9% lower than those of CSRFAC0, respectively. Compared with CSRFAC0, compressive strength, split tensile strength, flexural strength and elastic modulus of CSRFAC100 increased by 8.5%, 26.9%, 20.6% and 14.9%, respectively.
3. The increase of CSRFA substitution rate reduced the mass loss rate of CSRFAC and increased RDEM, the mass loss rate of CSRFAC after 350 FT cycles decreased from 4.88% to 3.45%, and RDEM increased from 50.4% to 62.2%. Compared with CSRFAC0, the frost resistance life of CSRFAC25, CSRFAC50, CSRFAC75 and CSRFAC100 was increased by 7.6%, 10.7%, 14.8% and 20.9%, respectively. The carbonation treatment of SRFA improves the frost resistance durability of CSRFAC.
In general, the use of CSRFA in concrete can significantly increase the effectiveness of waste utilization and the resilience of concrete against freezing. The findings of this research serve as a theoretical cornerstone for boosting the carbon footprint of waste concrete via the effective utilization of SRFA, thus promoting construction solid waste resource recovery in FT environment.
Acknowledgement: The authors would like to thank the laboratory of School of Building Engineering, Taizhou Polytechnic College for allowing us to use instruments for data collection and analysis.
Funding Statement: This work was financially sponsored by Qing Lan Project in Jiangsu Province of China (2023) and Scientific Research Project of Taizhou Polytechnic College (TZYKY-22-4).
Author Contributions: Jie Huang: Conceptualization, Data curation, Writing-original draft, Writing-review & editing, Funding acquisition, Investigation. Rongbin Jiang: Supervision, Project administration, Validation. Xiaobo Sun: Writing-review & editing, Methodology, Formal analysis. Yingyong Shuai: Formal analysis, Validation, Visualization.
Availability of Data and Materials: The data and materials used to support the findings of this paper are available from the corresponding author upon request.
Conflicts of Interest: The authors declare that they have no conflicts of interest to report regarding the present study.
References
1. Zheng, L., Wu, H. Y., Zhang, H., Duan, H. B., Wang, J. Y. et al. (2017). Characterizing the generation and flows of construction and demolition waste in China. Construction and Building Materials, 136, 405–413. https://doi.org/10.1016/j.conbuildmat.2017.01.055 [Google Scholar] [CrossRef]
2. Zhu, P. H., Hao, Y. L., Liu, H., Wei, D., Liu, S. F. et al. (2019). Durability evaluation of three generations of 100% repeatedly recycled coarse aggregate concrete. Construction and Building Materials, 210, 442–450. https://doi.org/10.1016/j.conbuildmat.2019.03.203 [Google Scholar] [CrossRef]
3. Qi, B., Gao, J. M., Chen, F., Shen, D. M. (2018). Chloride penetration into recycled aggregate concrete subjected to wetting-drying cycles and flexural loading. Construction and Building Materials, 174, 130–137. https://doi.org/10.1016/j.conbuildmat.2018.04.122 [Google Scholar] [CrossRef]
4. Bu, C. M., Liu, L., Lu, X. Y., Zhu, D. X., Sun, Y. et al. (2022). The durability of recycled fine aggregate concrete: A review. Materials, 15(3), 1110. https://doi.org/10.3390/ma15031110 [Google Scholar] [PubMed] [CrossRef]
5. Wei, D., Zhu, P. H., Yan, X. C., Liu, H., Chen, C. H. et al. (2022). Potential evaluation of waste recycled aggregate concrete for structural concrete aggregate from freeze-thaw environment. Construction and Building Materials, 321, 126291. https://doi.org/10.1016/j.conbuildmat.2021.126291 [Google Scholar] [CrossRef]
6. Feng, J. C., Zong, N. W., Zhu, P. H., Liu, H., Yao, L. et al. (2020). The frost-resisting durability of high strength self-compacting pervious concrete in deicing salt environment. Journal of Wuhan University of Technology-Materials Science Edition, 35(1), 167–175. https://doi.org/10.1007/s11595-020-2240-6 [Google Scholar] [CrossRef]
7. Pappu, A., Saxena, M., Asolekar, S. R. (2007). Solid wastes generation in India and their recycling potential in building materials. Building and Environment, 42(6), 2311–2320. https://doi.org/10.1016/j.buildenv.2006.04.015 [Google Scholar] [CrossRef]
8. Tam, V. W. Y., Gao, X. F., Tam, C. M. (2005). Microstructural analysis of recycled aggregate concrete produced from two-stage mixing approach. Cement and Concrete Research, 35(6), 1195–1203. https://doi.org/10.1016/j.cemconres.2004.10.025 [Google Scholar] [CrossRef]
9. Zhan, B. J., Poon, C. S., Liu, Q., Kou, S. C., Shi, C. J. (2014). Experimental study on CO2 curing for enhancement of recycled aggregate properties. Construction and Building Materials, 67, 3–7. https://doi.org/10.1016/j.conbuildmat.2013.09.008 [Google Scholar] [CrossRef]
10. Liu, H., Zhu, X. D., Zhu, P. H., Chen, C. H., Wang, X. J. et al. (2022). Carbonation treatment to repair the damage of repeatedly recycled coarse aggregate from recycled concrete suffering from coupling action of high stress and freeze-thaw cycles. Construction and Building Materials, 349, 128688. https://doi.org/10.1016/j.conbuildmat.2022.128688 [Google Scholar] [CrossRef]
11. Xiao, J. Z., Li, W. G., Poon, C. S. (2012). Recent studies on mechanical properties of recycled aggregate concrete in China—A review. Science China Technological Sciences, 55(6), 1463–1480. https://doi.org/10.1007/s11431-012-4786-9 [Google Scholar] [CrossRef]
12. Kazmi, S. M. S., Munir, M. J., Wu, Y. F., Patnaikuni, I., Zhou, Y. W. et al. (2019). Influence of different treatment methods on the mechanical behavior of recycled aggregate concrete: A comparative study. Cement and Concrete Composites, 104, 103398. https://doi.org/10.1016/j.cemconcomp.2019.103398 [Google Scholar] [CrossRef]
13. Kou, S. C., Poon, C. S. (2012). Enhancing the durability properties of concrete prepared with coarse recycled aggregate. Construction and Building Materials, 35, 69–76. https://doi.org/10.1016/j.conbuildmat.2012.02.032 [Google Scholar] [CrossRef]
14. Luo, M., Dai, J. J., Ding, Z. Q., Liu, Y. (2022). Properties of mortar containing recycled fine aggregate modified by microbial mineralization. Buildings, 12(11), 2035. https://doi.org/10.3390/buildings12112035 [Google Scholar] [CrossRef]
15. Zhu, P. H., Chen, K., Hu, K. (2019). Carbonation behavior of repeated recycled fine aggregate concrete under bending load. KSCE Journal of Civil Engineering, 23(2), 729–736. https://doi.org/10.1007/s12205-018-0348-4 [Google Scholar] [CrossRef]
16. Zhu, P. H., Hao, Y. L., Liu, H., Wang, X. J., Gu, L. (2020). Durability evaluation of recycled aggregate concrete in a complex environment. Journal of Cleaner Production, 273, 122569. https://doi.org/10.1016/j.jclepro.2020.122569 [Google Scholar] [CrossRef]
17. Chen, C. H., Liu, R. G., Zhu, P. H., Liu, H., Wang, X. J. (2020). Carbonization durability of two generations of recycled coarse aggregate concrete with effect of chloride ion corrosion. Sustainability, 12(24), 10544. https://doi.org/10.3390/su122410544 [Google Scholar] [CrossRef]
18. Pu, Y. H., Li, L., Wang, Q. Y., Shi, X. S., Luan, C. C. et al. (2021). Accelerated carbonation technology for enhanced treatment of recycled concrete aggregates: A state-of-the-art review. Construction and Building Materials, 282, 122671. https://doi.org/10.1016/j.conbuildmat.2021.122671 [Google Scholar] [CrossRef]
19. Liang, C. F., Pan, B. H., Ma, Z. M., He, Z. H., Duan, Z. H. (2020). Utilization of CO2 curing to enhance the properties of recycled aggregate and prepared concrete: A review. Cement and Concrete Composites, 105, 103446. https://doi.org/10.1016/j.cemconcomp.2019.103446 [Google Scholar] [CrossRef]
20. Fang, X. L., Xuan, D. X., Shen, P. L., Poon, C. S. (2021). Fast enhancement of recycled fine aggregates properties by wet carbonation. Journal of Cleaner Production, 313, 127867. https://doi.org/10.1016/j.jclepro.2021.127867 [Google Scholar] [CrossRef]
21. Tam, V. W. Y., Butera, A., Le, K. N. (2016). Carbon-conditioned recycled aggregate in concrete production. Journal of Cleaner Production, 133, 672–680. https://doi.org/10.1016/j.jclepro.2016.06.007 [Google Scholar] [CrossRef]
22. Lu, B., Shi, C. J., Cao, Z. J., Guo, M. Z., Zheng, J. L. (2019). Effect of carbonated coarse recycled concrete aggregate on the properties and microstructure of recycled concrete. Journal of Cleaner Production, 233, 421–428. https://doi.org/10.1016/j.jclepro.2019.05.350 [Google Scholar] [CrossRef]
23. Liang, C. F., Lu, N., Ma, H. W., Ma, Z. M., Duan, Z. H. (2020). Carbonation behavior of recycled concrete with CO2-curing recycled aggregate under various environments. Journal of CO2 Utilization, 39, 101185. https://doi.org/10.1016/j.jcou.2020.101185 [Google Scholar] [CrossRef]
24. Li, Y., Wang, R. J., Li, S. Y., Zhao, Y. (2017). Assessment of the freeze-thaw resistance of concrete incorporating carbonated coarse recycled concrete aggregates. Journal of the Ceramic Society of Japan, 125(11), 837–845. https://doi.org/10.2109/jcersj2.17111 [Google Scholar] [CrossRef]
25. Li, Y., Fu, T., Wang, R., Li, Y. (2020). An assessment of microcracks in the interfacial transition zone of recycled concrete aggregates cured by CO2. Construction and Building Materials, 236, 117543. https://doi.org/10.1016/j.conbuildmat.2019.117543 [Google Scholar] [CrossRef]
26. Fang, X. L., Xuan, D. X., Poon, C. S. (2017). Empirical modelling of CO2 uptake by recycled concrete aggregates under accelerated carbonation conditions. Materials and Structures, 50(4), 200. https://doi.org/10.1617/s11527-017-1066-y [Google Scholar] [CrossRef]
27. Chen, J. K., Wang, D. M. (2000). A new method for mix proportion design of high performance concrete (HPC)—Overall calculation method. Journal of the Chinese Ceramic Society, 28(2), 194–198. https://doi.org/10.14062/j.issn.0454-5648.2000.02.023 [Google Scholar] [CrossRef]
28. Wang, X. J., Liu, W. Y., Wei, D., Zhu, P. H., Hu, K. (2017). A simple mix proportion design method based on frost durability for recycled high performance concrete using fully coarse recycled aggregate. Journal of Wuhan University of Technology-Materials Science Edition, 32(5), 1119–1124. https://doi.org/10.1007/s11595-017-1720-9 [Google Scholar] [CrossRef]
29. Tam, V. W. Y., Tam, C. M., Wang, Y. (2007). Optimization on proportion for recycled aggregate in concrete using two-stage mixing approach. Construction and Building Materials, 21(10), 1928–1939. https://doi.org/10.1016/j.conbuildmat.2006.05.040 [Google Scholar] [CrossRef]
30. Standardization Administration of China (2010). GB/T 25176-2010-Recycled fine aggregate for concrete and mortar. Beijing, China: China Standards Press. [Google Scholar]
31. Standardization Administration of China (2022). GB/T 14685-2022-Pebble and crushed stone for construction. Beijing, China: China Standards Press. [Google Scholar]
32. De Juan, M. S., Gutiérrez, P. A. (2009). Study on the influence of attached mortar content on the properties of recycled concrete aggregate. Construction and Building Materials, 23(2), 872–877. https://doi.org/10.1016/j.conbuildmat.2008.04.012 [Google Scholar] [CrossRef]
33. ASTM (2021). ASTM C642-21-Standard test method for density, absorption, and voids in hardened concrete. West Conshohocken, PA, USA: ASTM. [Google Scholar]
34. Standardization Administration of China (2019). GB/T 50081-2019-Standard for test methods of concrete physical and mechanical properties. Beijing, China: China Architecture and Building Press. [Google Scholar]
35. Standardization Administration of China (2010). GB/T 50107-2010-Standard for evaluation of concrete compressive strength. Beijing, China: China Architecture and Building Press. [Google Scholar]
36. Standardization Administration of China (2009). GB/T 50082-2009-Standard for test methods of long-term performance and durability of ordinary concrete. Beijing, China: China Architecture and Building Press. [Google Scholar]
37. Liu, H., Hua, M. Q., Zhu, P. H., Chen, C. H., Wang, X. J. et al. (2021). Effect of freeze-thaw cycles on carbonation behavior of three generations of repeatedly recycled aggregate concrete. Applied Sciences, 11(6), 2643. https://doi.org/10.3390/app11062643 [Google Scholar] [CrossRef]
38. Fang, X. L., Zhan, B. J., Poon, C. S. (2021). Enhancement of recycled aggregates and concrete by combined treatment of spraying Ca2+ rich wastewater and flow-through carbonation. Construction and Building Materials, 277, 122202. https://doi.org/10.1016/j.conbuildmat.2020.122202 [Google Scholar] [CrossRef]
39. Alarcon-Ruiz, L., Platret, G., Massieu, E., Ehrlacher, A. (2005). The use of thermal analysis in assessing the effect of temperature on a cement paste. Cement and Concrete Research, 35(3), 609–613. https://doi.org/10.1016/j.cemconres.2004.06.015 [Google Scholar] [CrossRef]
40. Morandeau, A., Thiéry, M., Dangla, P. (2014). Investigation of the carbonation mechanism of CH and C-S-H in terms of kinetics, microstructure changes and moisture properties. Cement and Concrete Research, 56, 153–170. https://doi.org/10.1016/j.cemconres.2013.11.015 [Google Scholar] [CrossRef]
41. Xiao, J. Z., Li, W. G., Sun, Z., Lange, D. A., Shah, S. P. (2013). Properties of interfacial transition zones in recycled aggregate concrete tested by nanoindentation. Cement and Concrete Composites, 37, 276–292. https://doi.org/10.1016/j.cemconcomp.2013.01.006 [Google Scholar] [CrossRef]
Cite This Article
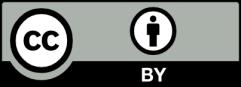