Open Access
ARTICLE
Comparison of Combustion Characteristics of Tars Produced with Tobacco Stem Biomass Gasification
1 School of Mechanical Engineering, Hunan Institute of Engineering, Xiangtan, 411104, China
2 School of Automotive Engineering, Xiangtan Institute of Technology, Xiangtan, 411100, China
3 School of Electrical and Information Engineering, Hunan Institute of Engineering, Xiangtan, 411104, China
4 China Metallurgic Jingcheng (Xiangtan) Heavy Industry Equipment Co., Ltd., Xiangtan, 411100, China
5 Hunan Shuanghuan Fiber Molding Machinery Co., Ltd., Xiangtan, 411100, China
* Corresponding Author: Bo Liu. Email:
Journal of Renewable Materials 2024, 12(1), 119-129. https://doi.org/10.32604/jrm.2023.031521
Received 26 June 2023; Accepted 31 July 2023; Issue published 23 January 2024
Abstract
In order to study the combustion characteristics of tar in biomass gasifier inner wall and gasification gas, “tobacco stem semi-tar inside furnace”, “tobacco stem tar inside furnace” and “tobacco stem tar out-of-furnace” were subjected to thermogravimetric experiments, and the combustion characteristics and kinetic characteristics were analyzed. The result shows that “tobacco stem semi-tar inside furnace” has the highest value and “tobacco stem tar out-of-furnace” is has the lowest value on ignition characteristics, combustion characteristics and combustible stability; “tobacco stem semi-tar inside furnace” has the lowest value and “tobacco stem tar outside furnace” has the highest value on burnout characteristics; “tobacco stem tar outside furnace” has the highest value and “tobacco stem tar inside furnace” has the lowest value on integrated combustion characteristics.Graphical Abstract
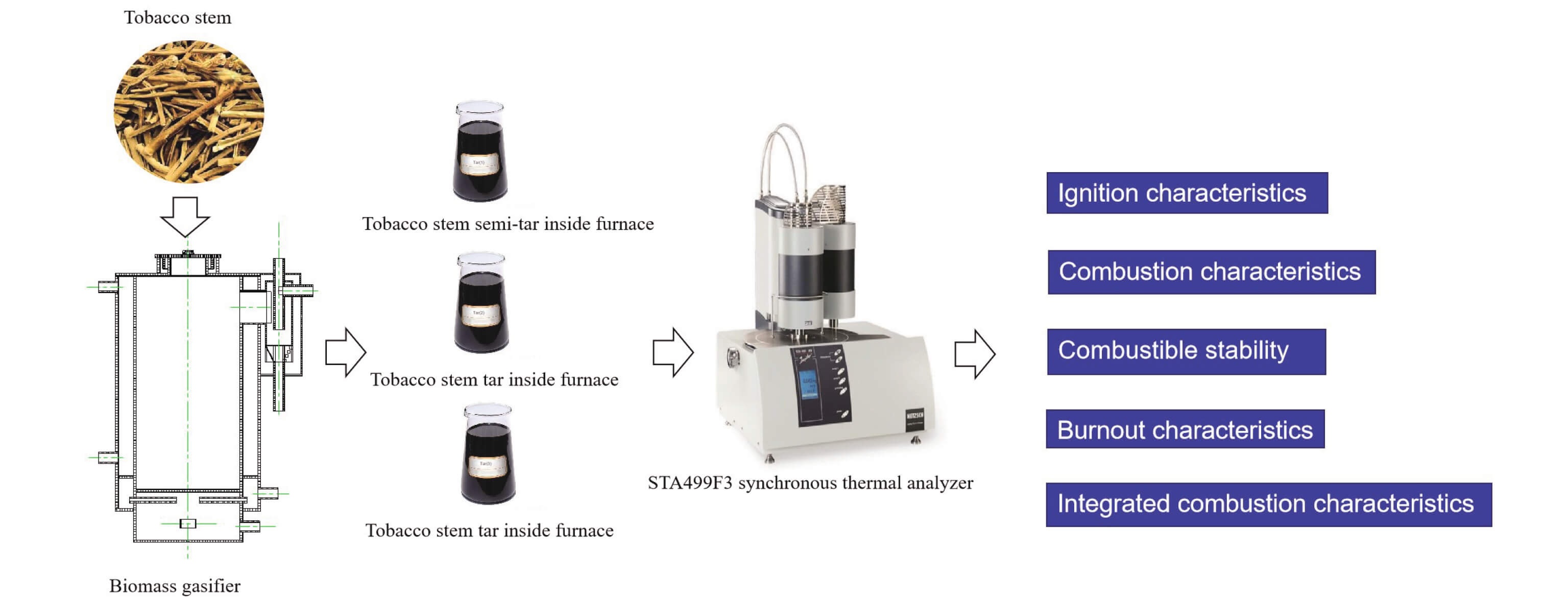
Keywords
Biomass utilization contributes to “Carbon Neutrality” [1]. The study of tar is crucial for the utilization of biomass energy [2]. The definition and classification of biomass tar is very important for tar research. Some scholars define tar from the perspective of chemical composition and molecular weight, and believed that tar is composed of large molecular weight organic compounds containing benzene [3–6]. However, Moersch et al. [7] thought that benzene should not be used as the dividing line to define tar from the perspective of molecular weight, but tar should be defined from the perspective of whether the substance will cause pipe blockage or corrosion. When the tar temperature is reduced to a certain temperature, some compounds of the tar will condense on the inner wall of the equipment, and some dissolve in the syngas. If the temperature is further reduced below the dew point in the cooling equipment, the compounds condensing on the equipment will cause corrosion. If the “tar” cannot condense in the process of gasification, these compounds will not result in clogging or corrosion unless the temperature drops further. Therefore, tar should be defined according to the actual situation. For example, benzene and toluene will not be blocked due to condensation in most cases at 25°C. From this perspective, benzene in syngas at room temperature does not belong to tar. There are some main gases including CO, H2, CO2, CH4, H2O, and N2, and some organic and inorganic impurities and particles in the gasification products. These organic substances can be decomposed into small molecule hydrocarbons and large molecule aromatic compounds. Small molecule hydrocarbons can be used as fuel and large molecule aromatic compounds are tar [8]. Ren et al. [9] defined some condensable components in the liquid product as tar. So far, tar is still difficult to be given a unified definition accurately. There are different definitions from different angles. The reason is that the chemical composition and physical and chemical properties of tar will also change with the change of biomass gasification conditions. Therefore, the definition of tar must be based on the environment in which tar is produced.
There is also no uniform standard for tar classification. Some scholars classified tar according to its composition. Tar was divided into primary tar, secondary tar and tertiary tar, or oxygen-containing mixture, alkylbenzene ether, heterocyclic ether, polycyclic aromatic hydrocarbons and polycyclic aromatic hydrocarbons with more rings [10–12]. The important index for evaluating biomass pyrolysis gasification system is tar dew point, because the dew point of tar is lower than the minimum temperature of the equipment, problems related to clogging caused by tar can be resolved. The tar was divided into GC-undetectable, Heterocyclic, Light aromatic, Light poly-aromatic, and Heavy poly-aromatic based on the dew point [7]. Some scholars also divide tar into two categories according to the reactivity of tar: Tar prone to chemical reaction and tar not prone to chemical reaction [13,14]. Based on the location of tar, it is generally divided into tar of gasified gas and tar condensed in the furnace or pipeline [15]. Although scholars have reached different research conclusions on the definition and classification of tar, it is still difficult to accurately define and unify the standard.
The research on the law of tar formation is generally based on the gasification experiment of tar at different temperatures, and then the composition of gasification tar at different temperatures is detected. Williams et al. [16] conducted a rapid pyrolysis experiment on sawdust. The pyrolysis temperature was 400°C to 600°C, and nitrogen was used as the carrier gas. The research results showed that aromatic compounds such as naphthalene, fluorene, phenanthrene, anthracene, pyrene, and benzopyrene began to form at 400°C, and the yield of PAHs increased with the increase of temperature. Horne et al. [17,18] reached the same conclusion in studying the evolution process of PAHs in pyrolysis tar. Mcgrath et al. [19] used nitrogen as carrier gas (flow rate 120 cm3/min) to pyrolyze cellulose at the temperature of 300°C to 650°C and detected PAHs in tar. The study shows that PAHs of 2–4 rings appeared at a temperature of more than 400°C, and benzopyrene and benzoanthracene were detected at 500°C. Professor Mi et al. [20] used air as a carrier gas for chaff gasification, analyzed the composition of tar produced at different temperature stages, and concluded that the formation of biomass gasification tar is a process of aromatization and deoxidation. Wu et al. [21] took cellulose and lignin as experimental objects and analyzed their pyrolysis products by GC-MS using nitrogen as carrier gas (flow rate 40 ml/min). The study shows that the pyrolysis process of different components is also a process of deoxidation and aromatization, and PAHs are formed at high temperatures, but lignin contributed more to PAHs. Adeleke et al. studied mechanisms, reaction micro-kinetics, and modelling of hydrocracking of tar model compounds [22–24]. Narobe et al. [25–27] studied reaction micro-kinetics and modelling of hydrocracking of aromatic biomass tar model compounds into benzene, toluene, and xylenes (BTX) over H-ZSM-5 catalyst.
The tobacco stem generated in the process of tobacco production and processing mainly was mainly treated as waste through landfill, fixed-point incineration, and destruction in most tobacco processing enterprises, at present, due to the lack of effective energy-saving and environmental protection treatment methods. However, this treatment method not only wastes the limited human, material, and financial resources of enterprises, but also causes the pollution of soil, water, and atmosphere, which makes enterprises face great public opinion pressure.
Therefore, the research on the tobacco stem tar in biomass gasifier inner wall and gasification gas is conducive to the treatment of the tar more targeted.
2.1 Biomass Gasifier Introduction
The gasified tar obtained in this experimental study was mainly obtained by the operation of the water-cooled stationary biomass gasifier as shown in Fig. 1. An annular water tank was attached to the outside of the gasification furnace, which can not only obtain hot water for domestic use, but also effectively ensure a constant furnace temperature and obtain stable thermodynamic gasification conditions. When the gasifier is running stably, the biomass fuel on the grate forms an oxide layer, a reduction layer, a cracking layer, and a preheating drying layer in sequence from bottom to top.
Figure 1: Structure of experimental biomass gasifier
The tobacco stems used in the test were from the redrying workshop of Hunan China Tobacco Group Xiangxi heshengyuan Tobacco Development Co., Ltd. (China), ground into powder, and screened with a 150 mesh standard sieve. The industrial composition analysis and calorific value of tobacco stems are shown in Table 1.
2.2 Extraction of Biomass Gasification Tar
In order to obtain gasified tar, the following operations should be done. The gas outlet and tar return inlet should be blocked by plugs and the tar return outlet should be connected to the tar collector before the experiment starts. When the gasifier was ignited, the valve in the front section of the tar collector should be closed, and the exhaust port on the upper part of the tar separator should be opened. The flue gas containing a large number of black carbon particles should be directly discharged. When the black smoke disappears, indicating the gasifier has entered a stable working state, the inlet valve of the tar collector and emptying port should be closed. The gasification temperature was 1100 K. The airflow was 200 ml/min, and the air material ratio was about 1.
The tobacco stems tar on the water wall of the cracking layer of the furnace was marked as “tobacco stem semi-tar in the furnace”. The tobacco stem on the water wall of the airflow space in the upper part of the furnace was marked as “tobacco stem tar in the furnace”. The tar in the out-of-furnace tar collector was marked as “tobacco stem tar out-of-furnace”. The three tobacco stem tars represent the tar at different strokes of the gasification gas and also represent the tar adhered to the furnace and the tar carried by the gasification gas. Therefore, the three tars were selected as representatives in this study. Because tar was not easy to obtain at high viscosity, the amount of tar could only be roughly equal in each experiment. The component characteristics of the tar test sample are shown in Table 2.
2.3 Thermogravimetric Experiment
In the experiment, the STA499F3 synchronous thermal analyzer produced by the German NETZSCH company was used to conduct the synchronous thermal analysis of TG, DTG, and DSC. The temperature programming rate was set at 20°C/min and the range was from 25°C to 900°C. The rest of the parameters were set as follows: the pressure of N2 is 0.05 MPa, the flow rate was 40 ml/min; the pressure of O2 is 0.03 MPa, and the flow rate was 10 ml/min.
2.4 Analysis of Combustion Characteristics
Based on the results of thermogravimetric analysis, the comparative analysis of the combustion indicators of three different tar samples is an important basis for effectively reflecting the different combustion characteristics of tar at different strokes of gasification gas. In this paper, a comparative analysis was made in terms of ignitability, flammability, stable combustion, burnout characteristics, and comprehensive combustion characteristics.
The ignitability is the ignition temperature, which can be analyzed by the method described in the literature [16]. The temperature corresponding to the peak point of the DTG curve should be found first, then the point corresponding to the TG curve from this temperature can be defined. The temperature corresponding to the intersection of the tangent line of the TG curve passing through this point and the parallel line of the initial segment of the TG curve is the ignition temperature. The lower the ignition temperature, the easier it is for the sample to ignite, conversely, the worse the ignitability.
2.4.2 Flammability and Stability Analysis
According to the results of thermogravimetric analysis, the ignition temperature, the maximum weight loss rate of the combustion peak, and the corresponding temperature under the maximum weight loss rate are different for different samples. The ignition temperature reflects the ignition performance of the sample or the activation energy of the sample. The smaller the value is, the easier it is for the sample to catch fire. The latter reflects the subsequent combustion of the sample after ignition, and the larger the maximum weight loss rate value of the combustion peak is, the smaller the corresponding temperature value is. Those indicate that the faster the burning speed of the sample is after ignition, the stronger the burning stability of the sample is. Therefore, the flammability index Cb [17] and the sample combustion stability discrimination index Cd can be used to judge the ignition characteristics of the sample. Its definitions are:
(dG/dτ)max—the maximum weight loss rate; Tmax—the corresponding temperature at the maximum weight loss rate; Ti—the ignition temperature. The Cb value mainly reflects the reaction ability of the sample in the early stage of combustion. The larger the value is, the better the flammability is. The larger the Cd value is, the better the combustion stability of the sample is.
2.4.3 Burnout Characteristic Analysis
The burnout characteristic is generally determined by the burnout characteristic index that is based on the relationship between the TG curve and time [18], as shown in formula (3).
In the formula: f1—initial burnout rate, f2—late burnout rate and the sum of the two is the total burnout rate. τ0—the time it takes from the start of weight loss to 98%. f1 reflects the burnout characteristics of light hydrocarbons in tar, f2 reflects the burnout characteristics of heavy hydrocarbons, and the burnout characteristic index comprehensively considers the effects of different hydrocarbon components in tar on the ignition and stable combustion, which can better describe the burnout characteristics of tar. In general, the larger the Cs is, the better the burnout characteristics of the tar is.
2.4.4 Comprehensive Combustion Characteristics
The ignitability, flammability, stable combustion, and burnout characteristics reflect different aspects of the combustion characteristics of tar, and the comprehensive combustion index SN can characterize the comprehensive combustion performance of the sample.
According to the initial stage of the combustion reaction in the slow heating combustion process belong to the dynamic region, that is, the chemical kinetics factor controls the reaction rate. Therefore, the combustion rate can be approximately expressed by Arrhenius’s law, which is:
where: dG/dτ—burning rate, A—frequency factor, E—activation energy; T—particle temperature; R—gas constant.
Derivating and arranging formulas (4), and (5) can be got:
At the ignition point, there are:
Eq. (6) can be transformed into:
In the formula: (dG/dτ)max—the maximum combustion rate. (dG/dτ)T=Ti—the combustion rate at the ignition temperature Ti. (dG/dτ)mean—the average combustion rate of the combustible mass, which is the ratio of the amount of combustible matter in the sample to its burnout time. Th—burnout temperature.
R/E represents the activity of the sample. The smaller the E is, the stronger the reaction ability is. d(dG/dτ)T = Ti/dT is the rate of change of the combustion speed at the ignition point. The larger the value is, the more violent the ignition is. (dG/dτ)mean/(dG/dτ)T=Ti is the ratio of the peak combustion velocity to the combustion velocity during ignition; (dG/dτ)mean/Th is the ratio of the average combustion velocity of the combustible matter to the burnout temperature. The larger the value is, which means that it burns out faster. Therefore, the product of these terms comprehensively reflects the ignition and burnout characteristics of the sample, and the right side of formula (7) is denoted as SN:
The TG-DTG-DSC of three types tar are shown in the following Figs. 2–4:
Figure 2: TG-DTG-DSC of tobacco stem semi-tar in the furnace
Figure 3: TG-DTG-DSC of pine tar in the furnace
Figure 4: TG-DTG-DSC of out-of-furnace tobacco stem tar
The quality of furnace tobacco stem semi-tar shows a downward trend throughout the thermogravimetric experiment. The downward trend becomes more slowly after 650°C. There is still more than 20% of the residual in the crucible even if the combustion heating temperature reaches the burnout temperature of 820°C, which means that the carbonization degree of the tobacco stem semi-tar in the furnace is high and the ash content is high. The tobacco stem semi-tar in the furnace needs to absorb heat during the combustion process and there are two significant endothermic peaks in the combustion process, which respectively means the combustion of light hydrocarbons and heavy hydrocarbons. The endotherm in the lower temperature range represents the combustion of light hydrocarbons and the endotherm in the higher temperature range represents the combustion of heavy hydrocarbons. The heat released from the combustion of light hydrocarbons is not sufficient for further pyrolysis and combustion of heavy hydrocarbons.
The tobacco stem tar in the furnace basically loses weight slowly at 400°C, which shows that the carbonization degree of the tobacco stem tar in the furnace is lower than that of the tobacco stem semi-tar in the furnace. There are two significant endothermic peaks in the combustion process. The second endothermic peak is lower and the peak width is narrower, indicating that the tobacco stem tar in the furnace is easier to burn and has a higher content of heavy hydrocarbons.
The tobacco stem tar outside the furnace burns completely when it is heated to around 515°C. The quality of the residue tends to be stable and the residual amount is about 10%. These characteristics indicate that the ash content of the tobacco stem tar outside the furnace is low, the exothermic heat is greater than the endothermic heat, and the carbonization degree is low. A violent pyrolysis and combustion reaction occurs between 80°C and 180°C. There is only one endothermic peak, which indicates that the light hydrocarbon content is high and the heat release can satisfy the combustion of heavy hydrocarbons.
The combustion characteristics of the tobacco stem semi-tar in the furnace, the tobacco stem tar in the furnace, and the tobacco stem tar outside the furnace are analyzed respectively, Table 3 shows the ignition temperature of test sample. Fig. 5 shows the flammability index and stable-combustion index of test sample. Fig. 6 shows burnout index of test sample. Fig. 7 shows the integrated combustion characteristics index of the test sample.
Figure 5: Flammability index and stable-combustion index of test sample
Figure 6: Burnout index of test sample
Figure 7: Integrated combustion characteristics index of test sample
It can be concluded from Table 3 and Figs. 5–7 that the carbonization degree of tobacco stem semi-tar in the furnace is high, the ignition performance is the best, the flammability and stability of combustion are the best, the burnout characteristics are the worst, and the comprehensive combustion characteristics are the second. The heavy hydrocarbon content of tobacco stem tar in the furnace is high, the ignition performance is the second, the flammability and stability of the combustion are second, the burnout characteristic is the second, and the comprehensive combustion characteristic is the worst. The tobacco stem tar outside the furnace has high light hydrocarbon content, the worst ignition performance, the worst flammability and stability of combustion, the best burnout characteristics, and the best comprehensive combustion characteristics. The reason for these differences in combustion characteristics is the environment where the tar is located. The location of the tobacco stem semi-tar is the biomass reduction layer and the cracking layer, where the biomass is continuously heated by the high temperature flue gas, and most of the water and light hydrocarbons have already been precipitated. The inner tobacco stem tar adhering to the water wall of the upper airflow space of the furnace is condensed and collected under high temperature conditions, that is mainly heavy hydrocarbon tar components. The tobacco stem tar out of the furnace is condensed under the action of cold water cooling, and the main component is a light hydrocarbon tar component and has higher moisture content.
(1) The combustion characteristics of tar obtained from different parts of the gasifier are different. The tobacco stem semi-tar in the furnace has a high degree of carbonization and high ash content, and the weight loss becomes slow at about 650°C. The carbonization degree of the tobacco stem tar in the furnace is low, which can basically burn completely at 400°C. The tobacco stem tar in the furnace is mainly composed of heavy hydrocarbons. Tobacco stem tar out-of-furnace has a high content of light hydrocarbons, and a violent pyrolysis and combustion reaction occurs between 80°C and 180°C.
(2) Tobacco stem semi-tar in the furnace has the highest value of ignitability, combustibility, and stable combustion, and has the lowest value of burnout properties. The tobacco stem tar in the furnace has the lowest value of comprehensive combustion properties. The tobacco stem tar out-of-furnace has the lowest value of ignition, combustibility, and stable combustion, and has the highest value of burnout characteristics and comprehensive combustion characteristics.
(3) The ignitability, flammability, and stable combustion of gasified tobacco stem tar first depends on the moisture content. The burnout and comprehensive combustion characteristics mainly depend on the light hydrocarbon content.
Acknowledgement: The authors wish to acknowledge the help of the organization and individuals whose literatures have been cited in this article.
Funding Statement: We also gratefully acknowledge the Financial Supported by Hunan Provincial Natural Science Foundation of China (No. 2023JJ50224), 2021–2022 Hunan Province Enterprise Science and Technology Commissioner Program Project (No. 2021GK5046), Hunan Provincial Natural Science Foundation of China (No. 2022JJ50013), and Hunan Provincial Natural Science Foundation of China (No. 2022JJ50041).
Author Contributions: The authors confirm contribution to the paper as follows: study conception and design: Bo Chen; data collection: Mingjun Wang, Bo Liu; analysis and interpretation of results: Bo Liu, Chunping Lu; draft manuscript preparation: Bo Chen, Guohai Jia, Yong Chao, Chao Zhong. All authors reviewed the results and approved the final version of the manuscript.
Availability of Data and Materials: Due to the nature of this research, participants of this study did not agree for their data to be shared publicly, so supporting data is not available.
Conflicts of Interest: The authors declare that they have no conflicts of interest to report regarding the present study.
References
1. Spinti, J. P., Smith, P. J., Smith, S. T., Díaz-Ibarra, O. H. (2023). Atikokan digital twin, Part B: Bayesian decision theory for process optimization in a biomass energy system. Applied Energy, 334(4), 120625. https://doi.org/10.1016/j.apenergy.2022.120625 [Google Scholar] [CrossRef]
2. Chen, B., Liu, B., Shi, Z. M. (2020). Combustion characteristics and combustion kinetics of dry distillation coal and pine tar. International Journal of Aerospace Engineering, 2020, 8888556–8888557. https://doi.org/10.1155/2020/8888556 [Google Scholar] [CrossRef]
3. Kong, X. Z., Wu, A. J., Fu, S. M., Xu, R. Y., Zhao, Y. C. et al. (2021). Comparatively investigation of real MSW and biomass tar treatment by a rotating gliding arc. Fuel, 298, 120745. https://doi.org/10.1016/J.FUEL.2021.120745 [Google Scholar] [CrossRef]
4. Devi, L., Ptasinski, K. J., Janssen, F. J. J. G., Paasen, S. V. B. V., Bergman, P. C. A. (2005). Catalytic decomposition of biomass tars: Use of dolomite and untreated olivine. Renewable Energy, 4(30), 565–587. https://doi.org/10.1016/j.renene.2004.07.014 [Google Scholar] [CrossRef]
5. Milne, T. A., Abatzoglou, N., Evans, R. J. (1998). Biomass gasification “tars”: Their nature, formation and conversion. NERL Technical Report (NERL/TP-570-25357). https://doi.org/10.2172/3726 [Google Scholar] [CrossRef]
6. Chen, B., Liu, B., Chao, Y., Zhong, C. (2022). Formation mechanism of biomass aromatic hydrocarbon tar on quantum chemistry. Journal of Renewable Materials, 10(12), 3491–3504. https://doi.org/10.32604/jrm.2022.021302 [Google Scholar] [CrossRef]
7. Moersch, O., Spliethoff, H., Hein, K. R. G. (2000). Tar quantification with a new online analyzing method. Biomass and Bioenergy, 18(1), 79–86. https://doi.org/10.1016/S0961-9534(99)00068-9 [Google Scholar] [CrossRef]
8. Li, C. S., Suzuki, K. (2009). Tar property, analysis, reforming mechanism and model for biomass gasification—An overview. Renewable and Sustainable Energy Reviews, 13(3), 594–604. https://doi.org/10.1016/j.rser.2008.01.009 [Google Scholar] [CrossRef]
9. Ren, J., Liu, Y. L. (2020). Progress and prospects of produced gas utilization from biomass tar reforming. Journal of Hazardous Materials Letters, 1, 100008. https://doi.org/10.1016/j.hazl.2020.100008 [Google Scholar] [CrossRef]
10. Li, X. Q., Liu, P., Huang, S., Wu, S. Y., Li, Y. L. et al. (2023). Study on the mechanism of syngas production from catalytic pyrolysis of biomass tar by Ni–Fe catalyst in CO2 atmosphere. Fuel, 335(12), 126705. https://doi.org/10.1016/J.FUEL.2022.126705 [Google Scholar] [CrossRef]
11. Cavalli, A., Aravind, P. V. (2021). Effect of selected representative biomass gasification tar compounds on Ni-GDC solid oxide fuel cells. International Journal of Hydrogen Energy, 46(40), 21124–21135. https://doi.org/10.1016/J.IJHYDENE.2021.03.188 [Google Scholar] [CrossRef]
12. Hasler, P., Nussbaumer, T. (2000). Sampling and analysis of particles and tars from biomass gasifiers. Biornass and Bioenergy, 18(1), 61–66. https://doi.org/10.1016/S0961-9534(99)00071-9 [Google Scholar] [CrossRef]
13. Perez, P., Aznar, P. M., Caballero, M. A., Gil, J., Martin, J. A. et al. (1997). Hot gas cleaning and upgrading with acalcined dolomite located downstream a biomass fluidised bed gasifier operating with steam-oxygen mixtures. Energy Fuels, 11, 1194–1203. https://doi.org/10.1021/ef970046m [Google Scholar] [CrossRef]
14. Corella, J., Toledo, J. M., Aznar, M. P. (2002). Improving the modeling of the kinetics of the catalytic tar elimination in biomass gasification. Industrial and Engineering Chemistry Researchs, 41(14), 3351–3356. https://doi.org/10.1021/ie0110336 [Google Scholar] [CrossRef]
15. Hernandez, S. P., Chiappero, M., Russo, N., Fino, D. (2011). A novel ZnO-based adsorbent for BiogasPurification in H2 production systems. Chemical Engineering Journal, 176(8), 272–279. https://doi.org/10.1016/j.cej.2011.06.085 [Google Scholar] [CrossRef]
16. Williams, P. T., Horme, P. A. (1996). Polycyclic aromatic hydrocarbons in catalytically upgraded biomass pyrolysis oils. Journal of the Institute of Energy, 69(481), 176–191. https://doi.org/10.1016/S0140-6701(97)84811-4 [Google Scholar] [CrossRef]
17. Horme, P. A., Williams, P. T. (1996). Reaction of oxygenated biomass pyrolysis model compounds over a ZSM-5 catalyst. Renewable Energy, 7(2), 131–144. https://doi.org/10.1016/0960-1481(96)85423-1 [Google Scholar] [CrossRef]
18. Pakdel, H., Roy, C. (1996). Hydrocarbon content of liquid product and tar from pyrolysis and gasification of woods. Energy Fuels, 5(3), 427–436. https://doi.org/10.1021/ef00027a012 [Google Scholar] [CrossRef]
19. Mcgrath, T. E., Chan, W. G., Hajaligol, M. R. (2003). Low temperature mechanism for the formation of polycyclic aromatic hydrocarbons from the pyrolysis of cellulose. Journal of Analytical and Applied Pyrolysis, 66(1), 51–57. https://doi.org/10.1016/S0165-2370(02)00105-5 [Google Scholar] [CrossRef]
20. Mi, T., Wu, Z. S., Yu, X. M., Wu, X. J. (2011). The experimental study on biomass tar-cracking by CaO catalyst. Acta Energlae Solaris Sinica, 32(5), 724–728. https://doi.org/10.19912/j.0254-0096.2011.05.021 [Google Scholar] [CrossRef]
21. Wu, Z. S., Mi, T., Chen, Y. F. (2010). The research of tar variation mechanism for biomass gasification. Acta Energlae Solaris Sinica, 31(2), 233–235. https://doi.org/10.19912/j.0254-0096.2010.02.017 [Google Scholar] [CrossRef]
22. Adeleke, A. A., Odusote, J. K., Ikubanni, P. P., Lasode, O. A., Malathi, M. et al. (2020). The ignitability, fuel ratio and ash fusion temperatures of torrefied woody biomass. Heliyon, 6(3), e03582. https://doi.org/10.1016/j.heliyon.2020.e03582 [Google Scholar] [PubMed] [CrossRef]
23. Peng, Z. F., Ning, X. J., Wang, G. W., Zhang, J. L., Li, Y. J. et al. (2020). Structural characteristics and flammability of low-order coal pyrolysis semi-coke. Journal of the Energy Institute, 93(4), 1341–1353. https://doi.org/10.1016/j.joei.2019.12.004 [Google Scholar] [CrossRef]
24. Wang, C. W., Wang, C. A., Feng, Q. Q., Mao, Q. S., Gao, X. Y. et al. (2022). Experimental evaluation on NOx formation and burnout characteristics of oxy-fuel co-combustion of ultra-low volatile carbon-based solid fuels and bituminous coal. Energy, 248, 123578. https://doi.org/10.1016/j.energy.2022.123578 [Google Scholar] [CrossRef]
25. Narobe, M., Golob, J., Klinar, D., Likozar, B. (2014). Co-gasification of biomass and plastics: Pyrolysis kinetics studies, experiments on 100 kW dual fluidized bed pilot plant and development of thermodynamic equilibrium model and balances. Bioresource Technology, 162, 21–29. https://doi.org/10.1016/j.biortech.2014.03.121 [Google Scholar] [PubMed] [CrossRef]
26. Lasic, J. D., Kostyniuk, A., Likozar, B. (2022). Mechanisms, reaction micro-kinetics and modelling of hydrocracking of aromatic biomass tar model compounds into benzene, toluene and xylenes (BTX) over H-ZSM-5 catalyst. Chemical Engineering Journal, 445, 136898. https://doi.org/10.1016/j.cej.2022.136898 [Google Scholar] [CrossRef]
27. Andrii, K., Miha, G., Blaz, L. (2019). Catalytic cracking of biomass-derived hydrocarbon tars or model compounds to form biobased benzene, toluene, and xylene isomer mixtures. Industrial & Engineering Chemistry Research, 58, 7690–7705. https://doi.org/10.1021/acs.iecr.9b01219 [Google Scholar] [CrossRef]
Cite This Article
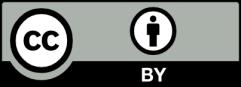