Open Access
ARTICLE
Modification of Wood by Tannin-Furfuryl Alcohol Resins–Effect on Dimensional Stability, Mechanical Properties and Decay Durability
1
Université de Lorraine, INRAE, UR 4370 USC 1445 LERMAB, Faculté des Sciences et Technologies, Nancy, France
2
Forest Product Sciences and Technology, Faculty of Forestry and Environment, IPB University, Bogor, Indonesia
* Corresponding Authors: Christine Gérardin-Charbonnier. Email: ; Philippe Gérardin. Email:
(This article belongs to the Special Issue: Advanced Wood Composites from Renewable Materials)
Journal of Renewable Materials 2023, 11(2), 505-521. https://doi.org/10.32604/jrm.2022.024872
Received 10 June 2022; Accepted 27 June 2022; Issue published 22 September 2022
Abstract
Furfurylation is a well-known wood modification technology. This paper studied the effect of tannin addition on the wood furfurylation. Three kinds of dicarboxylic acids, adipic acid, succinic acid, and tartaric acid, as well as glyoxal as a comparing agent, were used to catalyse the polymerisation of furanic or tannin-furanic solutions during wood modification. Impregnation of furanic or tannin-furanic solution at a certain concentration into the wood followed with curing at 103°C for a specific duration was performed for the wood modification. Different properties of the modified woods like dimensional stability, resistance of treatment to leaching, mechanical properties, decay durability against white-rot (Coriolus versicolor, Pycnoporus sanguineus) and brown-rot (Coniophora puteana) as well as their chemical and anatomical characteristics were evaluated. Results revealed that the partial substitution of FA by the tannins improved the fixation of the chemicals impregnated in wood. Further, dimensional stability, leaching resistance, Brinell hardness, modulus of elasticity/modulus of rupture, and decay durability properties of the furfurylated wood were also improved in the presence of tannins. Scanning electron microscopy revealed the deposition of the polymer in the wood lumen cells and in the wood cell walls.Keywords
Tannins, a well-known phenolic rich biomolecule derived from the higher plants, have been used for many applications, such as adhesives, composites, pharmaceuticals, medicals, food and beverage products [1–4]. Due to their low reactivity to the wood, tannins, particularly the condensed tannins, have been used for wood modification with the addition of cross-linkers or other reactive chemicals or additives, such as furfuryl alcohol, hexamine, formaldehyde, maleic anhydride, glyoxal, furfural, caprolactam, or lactic acid [5–10]. However, utilization of high weight ratio of tannins towards the cross-linkers and low concentration of the impregnating solution lead to modified wood with limited properties, particularly in terms of dimensional stability, leaching resistance, and biological durability [6]. Initially, the reaction between tannins and furfuryl alcohol has been studied for more than three decades [11]. This reaction and its application, especially as the excellent abrasive grinding wheels, rigid foams, and adhesives, have also been investigated by our group and others [12–33]. However, the use of different technique and formulations in this recent study, as well as its application for modification of solid wood is still very limited, thus triggering further investigations to develop environmentally friendly non biocide wood modification treatments.
Under an acidic environment, an in situ polymerisation of tannins-furfuryl alcohol for a solid wood modification has been inquired by Sommerauer et al. [6]. However, due to a low concentration of impregnating solution used and a higher weight ratio of tannins (10%) towards the furfuryl alcohol used as a cross-linker (1.25%), the modified wood presented low leaching resistance when cured at 103°C which consequently would lead to poor dimensional stability and poor biological durability. Based on this background, treatments using a higher concentration of impregnating solution with a higher weight ratio of the furfuryl alcohol towards the tannins, as a potential substitution model for furfurylation technology, were of interest.
Furfurylation is an important wood modification technology already developed on industrial scale [34–37]. According to the fact that the polymerisation of furfuryl alcohol depends on many factors, such as the nature and the concentration of the catalyst used and the concentration of FA solution [38–41], it seems interesting to evaluate the effects of the addition of tannins as reticulating agent and of different types of acids as catalysts to improve fixation of the polymer in the wood. Such formulations using already polymerized tannins and FA could enhance reticulation and reactivity of the resin into the wood through electrophilic aromatic substitutions, limiting the release of FA by evaporation during the curing phase or the leaching of FA after treatment.
Defect-free samples of European beech (Fagus sylvatica) (dried density, ±687 Kg.m−3) were prepared and cut into sizes detailed in Table 1. Prior to the cutting process, the wood material was room conditioned at approx. 20°C/60% relative humidity (RH).
Technical grade furfuryl alcohol (approx. 97% in purity) was purchased from Sigma Aldrich. Tan Active tannin powder extract was generously furnished by Sylvateam, Italy. Laboratory-grade of adipic acid, succinic anhydride, tartaric acid, glyoxal 40% solution were purchased from Sigma Aldrich.
2.2 Preparation of Impregnating Solution
Impregnating solution was made according to the formulation described in Table 2. Distilled water, adipic acid (AA), succinic acid (SA), tartaric acid (TA), furfuryl alcohol (FA), glyoxal (glyox), and tannin (Tan) were formulated in weight percent concentration. pH value of each impregnating solution was measured using pH meter from Mettler Toledo, calibrated by two buffer solutions 4.00 and 7.00 from Sigma Aldrich.
Wood samples were carefully dried to avoid crack formation at increasing temperature 80°C (24 h), 103°C (24–48 h), and weighed (m0), then the volumes were measured using a digital Caliper (V0). The samples, except for the untreated wood (A), were thereafter impregnated into different impregnating solutions under vacuum (100 kPa, 1 h), and followed by pressure (1200 kPa, 30 min) conditions. At the end of the impregnation process, all samples were removed, and the excess of impregnating solution on the samples was wiped off. Each sample was then re-measured for its wet weight (m1) and wet volume (V1). Afterwards, the samples were re-dried carefully at room condition (3 days), covered with aluminium foil, cured at 103°C (48 h), the aluminium foil was opened, and continued drying at 103°C (24 h). Finally, each cured sample was re-measured for its weight (m2) and volume (V2), then conditioned at room temperature before further characterization.
During the wood modification above, solution uptake and swelling caused by the impregnating solution were calculated as follows (Eqs. (1) and (2)):
where m0 and V0 are the initial mass and volume of oven-dry wood at 103°C, m1 and V1 the wet mass and volume of wood just after impregnation.
After drying and curing process, weight percent gain (WPG) and bulking (B) were calculated as follows (Eqs. (3) and (4)):
where WPG is the weight percent gain, B the bulking value, m2 and V2 are the mass and volume of impregnated wood sample after curing process.
Leaching test referred to NF X 41-568 [42]. Wood samples [5 mm × 20 mm × 20 mm, (L, T, R), n = 18–30], for both treated and untreated wood, were submerged into a distilled water in different chambers separated according to their group of treatment (the volume of water was at least five-fold of the volume of the wood sample). A dynamic leaching test using shaking force (100 linear shakes/minute) was conducted. Leaching water (leachate) was replaced and collected for each leaching period after 1, 2, 4, 8, 16, and 48 h. Between the period of 4 and 8 h, the wood samples were kept without water for 16 h, then continue for the next leaching period. pH value and volume of the leachate from each period was measured. After leaching periods were complete, each water saturated (wet) wood sample was weighed (m3), followed with drying at room temperature for 2 h and at 103°C for 48 h, then weighed (m4). From this leaching test, leaching value and acidity of the total leachates were calculated as the following (Eqs. (5)–(8)):
where water uptake is the amount of water absorbed at saturated condition, L the leaching values, m3 wet mass of water saturated wood sample just after leaching, m4 oven-dry mass of sample after leaching, [H+] the acidity of the leachate in molar (M) unit, mol H+/L the concentration obtained as the sum of 10−pH × volume of each leachate in each water change (leaching period) then divided by a total volume of leachates from the leaching test, pH leachate the pH calculated as −log[H+] of total leachate of the leaching test.
Dimensional stability measured as swelling, anti-swelling efficiency (ASE), and shrinkage was performed using a three-cycles of drying-wetting system. Wood samples [10 mm × 20 mm × 20 mm, (L, T, R), n = 7], for both treated and untreated wood [the actual dried weight (Wd) and volume (Vd) had been recorded], were submerged into the distilled water (the volume of water was at least five-fold of the volume of the wood sample) in different chambers separated based on their treatments, introduced to vacuum condition at 10 kPa for 1 h, and kept submerged in the water at room atmosphere for 23 h. Each wet wood sample was then measured for its wet mass (Ww) and wet volume (Vw). This drying-wetting cycle was repeated for the following second and third cycles. Each wood sample was recorded for its mass and volume during the test. Swelling (S), ASE, shrinkage (Shr), and weight loss due to leaching during ASE test (WLASE) of each wood sample can be calculated as follows (Eqs. (9)–(12)):
where S is the percentage of swelling of wood sample, Vd the dry volume of the sample, Vw the wet volume of the sample.
where ASE is the percentage of anti-swelling efficiency of treated wood, S0 the swelling of untreated wood at cycle 1, S1 the swelling of treated wood.
where Shr is the percentage of shrinkage of wood sample, Vd1 the volume of dried wood before wetting process, Vd2 the volume of dried wood after wetting process.
A recorded dry weight (m5) of samples after three leaching cycles during ASE test can be used for calculating weight losses due to leaching after ASE (WLASE) as follows (Eq. (12)):
where WL ASE is the weight loss after three leaching cycles during ASE test, m5 the dry mass at 103°C of samples after three leaching cycles of ASE test.
2.6 Brinell Hardness Measurements
With similar modification process, wood blocks measuring 50 mm × 20 mm × 20 mm (L × T × R) were modified according to different applied treatments (B–H), with three sample replicates for each treatment. After conditioning at room temperature for at least 2 weeks, the obtained modified woods were then measured for their weight, dimension, and Brinell hardness values by means of INSTRON 4467 universal testing machine on both tangential and radial positions. Brinell hardness measurements referred to NF B51-126 [43] using the following formula (Eq. (13)):
where HB is the Brinell hardness (daN/mm2), F the force positive of the ball received in newtons, D the diameter of a ball (10 mm), and P the depth-point on wood due to the ball indentation in millimetre.
2.7 Modulus of Elasticity (MOE) and Modulus of Rupture (MOR)
The mechanical properties as MOE and MOR of the wood samples were conducted according to EN 310 [44] using three points bending method. Prior to the measurement, wood samples [170 mm × 20 mm × 5 mm, (L, T, R); n = 10] were conditioned in a climatic chamber (65 ± 5% RH; 22 ± 2°C) until constant weight. The dimension and weight of each wood sample after conditioning duration was recorded for its density value. The increment in load and displacement values of each sample were measured by means of INSTRON 4467 universal testing machine. MOE/MOR values were then calculated using the formulas as follows (Eqs. (14) and (15)):
where I is the distance between the centers of support in millimeters, b the width of the sample in millimeters, t the thickness of the sample in millimeters, F2 − F1 the increase in load in newton, on the cross section of the load-deformation curve, F1 should be approximately 10% and F2 approximately 40% of the breaking load, a2 − a1 the increase of deflection at mid-length of the test sample (corresponding to F2 − F1).
where Fmax is the breaking load in Newton.
2.8 Decay Resistance Properties
Decay durability against Coriolus versicolor (white-rot), Coniophora puteana (brown-rot), and Pycnoporus sanguineus (tropical white-rot) was performed using a modified method EN 113 [45]. A sterile culture medium, prepared from malt (40 g) and agar (25 g) [purchased from Sigma-Aldrich (France)] in distilled water (1 L), was placed in culture Petri dishes (diameter, ±90 mm), inoculated with a small piece of mycelium of a freshly grown pure culture of Coriolus versicolor Quélet (CV) [Linnaeus, CTB 863 A] and incubated for 2 weeks at 22 ± 2°C and 70 ± 5% RH to allow full colonization of the medium by the mycelium. A similar inoculation procedure was also performed for other fungi, Coniophora puteana (CP) and Pycnoporus sanguineus (PS).
All wood samples [5 mm × 20 mm × 20 mm (L × R × T), n = 6–9, for each treatment] after leaching were sterilized by heating at 103°C for 6 h and cooled in a sterile place before exposing to fungi. Into each fungus containing-petri dish, three wood samples were put and exposed. Untreated beech samples after leaching as virulence samples were also performed with the similar manner. Incubation was carried out for 12 weeks at 22 ± 2°C and 70 ± 5% RH in a climatic chamber. Once the fungal exposure was completed, samples were cleaned from the mycelium and weighed for its humid mass (m5). The humid samples were then oven dried at 103°C for 48 h and weighed (m6). Moisture content and mass loss after decay test were calculated as follows (Eqs. (16) and (17)):
where MC is the percentage of moisture content of wood sample just after decay test before drying, WLD the weight loss percentage of the wood sample due to decay, m6 the humid mass of wood sample just after decay test before drying, m7 the dry mass of wood sample after decay test.
2.9 Fourier Transform Infrared (FTIR) Spectroscopy
FTIR spectra of the untreated wood and the wood modified with the polymer were recorded on an ATR-FTIR Perkin Elmer Spectrum 2000 instrument with 16 scans for each measurement in the range of 4000–600 cm−1 at a resolution of 4 cm−1. The spectra were then based line corrected using IR spectrum software.
FTIR analysis for wood sample powder after vigorous leaching was also conducted. The untreated and treated woods were grounded into a fine powder. Each wood powder (±0.3000 g) was leached vigorously in the water (±8.000 g) by means of Vortex device for 2 min, followed with shaking process (175 linear shakes/min) for 12 h. Afterward, a clear solution was decanted and filtered with a special filter for further analysis. Whereas, the residue was then leached vigorously using acetone as a solvent (10 ml) with sonication for 20 min. The solid leached residue was then dried at room temperature and analyzed using ATR-FTIR Perkin Elmer Spectrum 2000 instrument.
2.10 Scanning Electron Microscope (SEM) Observation
Anatomical observation of the treated and untreated wood was carried out by means of the scanning electron microscope (SEM) HITACHI TM3000 at different magnifying levels.
3.1 Characteristics during Wood Modification Process
During wood impregnation, solution uptake of different impregnating solutions presented approximately similar values (>100%) (Table 3). Comparable results were also observed in their swelling values, indicating that penetration of the impregnating solution was not difficult for all solutions, though treatments using TA slightly gave higher average values than others. Higher topological polar surface area of the TA (115 Ǻ2) compared to SA (74.6 Ǻ2) or AA (74.6 Ǻ2) [46] might explain a higher swelling of the wood cell walls at saturated condition.
After curing process, due to different reactivity of the acid used and/or effect of the tannin addition, each treatment provided variation in its weight percent gain (WPG) and bulking (B) values. Due to higher reactivity of TA (higher dissociation constant) than SA in this furanic or tannin-furanic polymerisation, WPG values of the treatments using TA (F and G) were higher than the treatments using SA. A similar reason was also happened between SA with AA, due to slightly lower dissociation constant of AA than SA, the WPG values of treatments using AA were lower than treatments using SA. Further, bulking (B) values, which relates to the penetration and fixation of the impregnating solution into the wood cell walls [47], mostly increased in harmony with the increase of the WPG values. In this experiment, it seemed that the addition of tannins could increase not only the WPG values but also the bulking values for some treatments due to the increase of polymerization reactivity. An exception for the treatment F, also due to higher reactivity of the tartaric acid than other acids, the addition of tannin increased reactivity of the impregnating solution, intensifying the curing/cross-linking process. Therefore, due to this intensive cross-linking system in the treatment F, the final wood volumes after curing process were slightly smaller than the corresponding treatment without tannin addition (G), decreasing their bulking values.
On the other hand, treatment H presented the highest average WPG values than others, though their bulking effect were comparable with other tannin-addition treatments. Although the estimation of resin/polymeric product of all impregnating solution was made almost similar one and each other during formulation, the wood impregnated with glyoxal-based solution (H) seemed performed better reticulation of FA-tannin than tartaric acid or other acids. The lower molecular weight of glyoxal was possibly the main reason in this case, intensifying cross-linking process due to its higher number of molar ratio than the acids in this study.
Based on the leaching test (Table 4), a relatively low leaching value was observed for all modified woods. However, among the modified woods, treatment D and E presented higher leaching values than others. In this regard, the lower reactivity of SA or AA towards the polymerization of FA than TA or glyoxal might also explain this difference, liberating some unfixed products/unreacted components during leaching test. At the same time, the detected leaching values on the untreated wood was mostly due to the release of water-soluble extractive from the beech wood [48]. On the other hand, the acidity test results have shown that the leachate obtained from the FA-TA treatment (G) gave the highest acidic value with a pH value of 2.93. A stronger acidic property of the TA (pKa1 = 2.89) could certainly be the reason in this point. Further, the results show that the addition of tannin could reduce the water uptake recorded at the end of the leaching test, increased the leaching resistance, and slightly reduced the acidic value (increased pH value) of the acid-catalyzed wood furfurylation. From this leaching property, it was obvious that the addition of tannins could increase fixation of the polymeric products in wood due to higher reticulation occurred among the reactants during curing process.
During this dimensional stability test, all treated wood presented far lower water uptake values than untreated wood (A) (Table 5). The addition of tannins into the acid-catalysed furfurylation could decrease water uptake values of the modified wood, lowering the swelling due to lower water uptake and increasing the ASE values. In addition, a higher leaching resistance was also observed for the tannin-furanic treated wood. Higher reticulation system happened in the tannin-furanic treated wood might also be the reason in this case, increasing dimensional stability of the modified wood. Among the treatments, however, treatment G presented the highest ASE values than others. Higher reactivity due to the higher dissociation constant of TA and its higher polarity, allowing itself to penetrate well into the wood cell walls, could be the reason for its highest ASE values. These highest ASE were also similar with the results obtained by Prabu et al. (66%) [49], working with almost similar technique, wood impregnation with a solution containing TA (5%)-FA (50%)-water (45%) followed with curing at 120°C for 18–24 h.
On the other hand, shrinkage values recorded at the end of the cycle 2 showed that all treated woods presented slightly higher shrinkage values than untreated wood. The leaching of some unfixed polymers/unreacted components from the treated wood during ASE test might explain this behavior, decreasing slightly bulking values of the modified woods.
Brinell hardness values of all modified wood were higher than untreated wood (A) (Table 6). The addition of tannin into the acid-catalysed furfurylation (especially treatment D and E) could increase their Brinell hardness values, either in radial or in tangential direction. A slight increase in their elastic recovery values was also recorded due to these tannin addition treatments (B, C, F, H). Unfortunately, due to higher density of the modified wood obtained as the results of the tannin addition (F, H), the modified wood samples were broken during this Brinell hardness test. An intensive reticulation that occurred in the treatment F and H, due to the high reactivity of the FA/Tan/TA solution in the first case, or to the addition of glyoxal and Tan in the second case, associated to an higher density of the wood samples, might explain the ruptures observed, which were not outweighed by the wood mechanical origin. On the other hand, due to higher reactivity of the TA than AA or SA, treatment G presented the modified wood with higher Brinell hardness values than the modified wood made of treatment D or E.
3.5 Modulus of Elasticity and Modulus of Rupture
Mechanical properties as MOE/MOR revealed that MOE/MOR values of all modified woods were lower than untreated wood (A) (Table 7). The low pH (higher acidity) of the impregnating solution in wood during modification, particularly during curing process, where the water evaporated and solution concentrated, could be the main reason in this case, deteriorating some wood components, particularly hemicelluloses. As a supporting matrix in the wood cell walls through hydrogen bonding, hemicelluloses are more susceptible to acid and thermal degradation [50,51]. Moreover, mechanical properties are function of the chemical bond strength (the collective interaction of the chemical bonds consisting of hydrogen and covalent intrapolymer bonds, covalent and hydrogen interpolymer bonds, and fibre-to-fibre bonding with middle lamella playing as the adhesive) [51]. On the other words, interruption on these interactions, especially due to acid, decay or heat, could degrade these mechanical properties [52,53]. Therefore, due to the highest acidity of the impregnating solution, the wood modified with treatment G provided the lowest MOE/MOR values than others. On the other hand, it seemed that the partial substitution of FA by the tannins could slightly increase the MOE/MOR values, though this increase approximately was outweighed by the increase of its modified wood density.
Durability test against decay, white-rot [Coriolus versicolor (CV), Pycnoporous sanguineus (PS)] and brown-rot [Coniophora puteana (CP)], showed that almost all modified woods after leaching process presented far lower mass loss values due to decay than their corresponding untreated wood (Table 8). Among these fungi used, it seemed that most of the modified woods were more intensely attacked by the CV, presenting higher decay mass losses than against other fungi. Irbe et al. reported that CV could produce not only endoglucanase, xylanase, and filter paper activity (cellulose) as CP does but also generate laccase and manganese-dependent peroxide for the lignin degradation during its decay activity [54]. Hence, among the modified woods, due to the lower reactivity of the acid used in treatment D and E which providing their lower WPG and higher leaching values, the modified wood underwent far higher mass losses due to CV. On the other hand, the wood modified with tannin-furanic polymer presented higher durability against decay than the wood modified with only furanic polymer (furfurylation), particularly against CV. A higher hydrophobic property of the modified wood due to a blocking effect of the constructed polymer in the lumen cell, bulking effect of the wood cell walls, and structural changes of some wood components which were no longer recognized by the fungi due to the deep wood modification explained previously were some possible factors influencing this higher decay resistance. Among these tannin-furanic polymers, the wood modified with polymer F presented the lowest mass loss values. The higher reactivity of TA in treatment F might also explain its higher decay resistance, especially in comparison with the treatments using other dicarboxylic acids. Treatment G, which also used TA during formulation, presented its furanic modified wood (furfurylated wood) with lower decay mass loss values than other dicarboxylic acid-based furanic modified wood (D, E), notably also against decay CV. At the WPG and leaching values of 30% and 2%, respectively, the wood modified with treatment G presented similar decay mass loss values against CV with the wood modified with almost similar furfurylation technique (WLD = 2.7 ± 0.6%) [49].
According to FTIR analysis, though not all the modified wood spectra are presented here, slight modifications appeared for the wood modified with tannin-furanic solution (F) at the WPG level of 46% (Fig. 1).
Figure 1: FTIR spectra of untreated beech, tannin-furanic polymer and tannin-furanic-treated beech (A = absorbance)
Differences in FTIR spectra due to the modification with FA-Tan-TA solution were relatively weak. Only small variations can be observed with the FTIR spectra of untreated beech. A small increase of the signal at 1733 cm−1 with slight broadening assigned to C=O stretching vibration is observed in treated beech. Similarly, signals at 1652 cm−1 assigned to C=C stretching vibration, 1593 cm−1 assigned to C=C stretching aromatic skeletal vibration and 1506 cm−1 assigned to C=C–H stretching asymmetric aromatic in-plane (furans also) increase indicating presence of additional aromatic moieties. New signals at 787 cm−1 assigned to C–H bending aromatic out of plane of furans and 733 cm−1 assigned to C–C–C ring bending symmetric of furans indicated the presence of polyfurfuryl alcohol [55,56]. All the new signals appearing in the FTIR spectrum of beech treated FA-Tan-TA solution are present in the FTIR spectrum of crude FA-Tan-TA polymer.
Based on these results and since most of the modifications took place via electrophilic aromatic substitution, lignin could be the main wood component modified during treatments with FA and tannins, supporting the statement of a strong affinity of FA towards non-cellulosic cell wall constituents during polymerization [37,57,58]. Even if it remains difficult to certify SEAr between tannins, lignin and furfuryl alcohol based on the FTIR analysis performed in this study, additional studies indicate the possibility of such reactions [59,60]. Fixation of the polymer into the wood structure was evaluated after leaching using water and acetone (Fig. 2).
Figure 2: FTIR spectra differences of untreated beech vs. tannin-furanic-treated wood before and after vigorous leaching process with water and acetone
The modified wood sample powder presented almost similar FTIR characteristic even after vigorous leaching process, showing no differences of the FTIR spectra of modified samples before and after leaching process indicating good fixation of the polymer into the wood structure.
Potential reaction between furfuryl alcohol polymer and aromatic moiety of tannins or lignin is proposed in Fig. 3.
Figure 3: Potential reaction between furfuryl alcohol polymer and tannins
3.8 Scanning Electron Microscope (SEM) Observation
SEM analysis disclosed that the wood modified with tannin-furanic based polymer (B or H) provided higher deposits not only in the wood cell walls (bulking effect) but also in the wood lumen cells (Fig. 4).
Figure 4: SEM images of untreated beech (A), furanic treated beech (D), and tannin-furanic treated beech (B, H)
With the similar acidic medium used (AA in this case) and WPG estimation of the modified wood during solution formulation, it was obvious that the partial substitution of FA by the tannins in AA-based furfurylation could increase the reactivity of the polymerisation, increasing WPG values through this deposit formation (D vs. B). An intense deposit formation could also be observed in the wood modified with treatment H, using glyoxal as acid and cross-linker. Ultimately, due to these chemical (e.g., polymerisation of impregnated chemicals, reaction with the wood components) and physical (e.g., bulking effect, deposit formation) modifications of wood, the modified wood provided better dimensional and biological durability properties.
The partial substitution of FA by the tannins during wood furfurylation in the acidic medium provided various advantages. Dimensional stability, leaching resistance, Brinell hardness, MOE/MOR, and decay durability of the furfurylated wood were improved. From the three dicarboxylic acids studied, acid with higher dissociation constant performed higher reactivity towards polymerisation of FA and furfurylation. Through this tannin addition, polymerisation of the tannin-furanic solution could be occurred even under acidic medium with lower dissociation constant, generating better modified wood properties. However, due to a black polymer characteristic obtained from this tannin-furanic system, the modified wood has a darker colour than its corresponding furfurylated wood. Nevertheless, this renewable based modification technology might stimulate the application of the modified woods for other advanced research work or other special products.
Funding Statement: LERMAB is supported by a grant overseen by the French National Research Agency (ANR) as part of the “Investissements d’Avenir” Program (ANR-11-LABX-0002-01, Lab of Excellence ARBRE). The authors gratefully acknowledge the “Institut Carnot Énergie et Environnement en Lorraine (ICÉEL)” for the financial support through “Eco-Value” Project and Lab of Excellence ARBRE for the financial support of “ChemXtraMat” Project.
Conflicts of Interest: The authors declare that they have no conflicts of interest to report regarding the present study.
References
1. Pizzi, A. (2019). Tannins: Prospectives and actual industrial applications. Biomolecules, 9(8), 1–30. DOI 10.3390/biom9080344. [Google Scholar] [CrossRef]
2. Dhawale, P. V., Vineeth, S. K., Gadhave, R. V., Fatima, J., Supekar, M. V. et al. (2022). Tannin as a renewable raw material for adhesive applications: A review. Material Advances, 3, 3365–3388. DOI 10.1039/D1MA00841B. [Google Scholar] [CrossRef]
3. Pizzi, A. (2019). Tannin-based biofoams–A review. Journal of Renewable Material, 7(5), 477–492. DOI 10.32604/jrm.2019.06511. [Google Scholar] [CrossRef]
4. Shirmohammadli, Y., Efhamisisi, D., Pizzi, A. (2018). Tannins as a sustainable raw material for green chemistry: A review. Industrial Crops and Products, 126, 316–332. DOI 10.1016/j.indcrop.2018.10.034. [Google Scholar] [CrossRef]
5. Grosse, C., Noël, M., Thévenon, M., Gérardin, P., Grosse, C. et al. (2019). Improvement of modified wood properties with addition of chestnut tannins in lactic acid-based treatments. Journal of Wood Chemistry and Technology, 39(2), 124–135. DOI 10.1080/02773813.2018.1513035. [Google Scholar] [CrossRef]
6. Sommerauer, L., Thevenon, M. F., Petutschnigg, A., Tondi, G. (2019). Effect of hardening parameters of wood preservatives based on tannin copolymers. Holzforschung, 73(5), 457–467. DOI 10.1515/hf-2018-0130. [Google Scholar] [CrossRef]
7. Tondi, G. (2017). Tannin-based copolymer resins: Synthesis and characterization by solid state 13C NMR and FT-IR spectroscopy. Polymers, 9(6), 223. DOI 10.3390/polym9060223. [Google Scholar] [CrossRef]
8. Tondi, G., Hu, J., Rizzo, F., Buh, J., Medved, S. et al. (2017). Tannin-caprolactam and tannin-PEG formulations as outdoor wood preservatives: Weathering properties. Annals of Forest Science, 74(1), 19. DOI 10.1007/s13595-016-0605-y. [Google Scholar] [CrossRef]
9. Saražin, J., Poljanšek, I., Pizzi, A., Šernek, M. (2022). Curing kinetics of tannin and lignin biobased adhesives determined by DSC and ABES. Journal of Renewable Materials, 10(8), 2117–2131. DOI 10.32604/jrm.2022.019602. [Google Scholar] [CrossRef]
10. Amari, M., Khimeche, K., Hima, A., Chebout, R., Mezroua, A. (2021). Synthesis of green adhesive with tannin extracted from eucalyptus bark for potential use in wood composites. Journal of Renewable Materials, 9(3), 463–475. DOI 10.32604/jrm.2021.013680. [Google Scholar] [CrossRef]
11. Foo, L. Y., Hemingway, R. W. (1985). Condensed tannins: Reactions of model compounds with furfuryl alcohol and furfuraldehyde. Journal of Wood Chemistry and Technology, 5(1), 135–158. DOI 10.1080/02773818508085184. [Google Scholar] [CrossRef]
12. Lagel, M. C., Pizzi, A., Basso, M. C., Abdalla, S. (2015). Development and characterization of abrasive grinding wheels with a tannin-furanic resins matrix. Industrial Crops and Products, 65, 343–348. DOI 10.1016/j.indcrop.2014.11.020. [Google Scholar] [CrossRef]
13. Lagel, M. C., Zhang, J., Pizzi, A. (2015). Cutting and grinding wheels for angle grinders with a bioresin matrix. Industrial Crops and Products, 67, 264–269. DOI 10.1016/j.indcrop.2015.01.046. [Google Scholar] [CrossRef]
14. Li, X., Nicollin, A., Pizzi, A., Zhou, X., Sauget, A. et al. (2013). Natural tannin-furanic thermosetting moulding plastics. RSC Advances, 3(39), 17732–17740. DOI 10.1039/c3ra43095b. [Google Scholar] [CrossRef]
15. Baradun, G. A., Schönenberger, D., Sahin, O., Bianchi, S., Mayer, I. (2018). Biocomposites based on plant material. Advanced Materials Letters, 9(12), 876–879. DOI 10.5185/amlett.2018.2165. [Google Scholar] [CrossRef]
16. Cefarin, N., Bedolla, D. E., Surowka, A., Donato, S., Sepperer, T. et al. (2021). Study of the spatio-chemical heterogeneity of tannin-furanic foams: From 1D FTIR spectroscopy to 3D FTIR micro-computed tomography. International Journal of Molecular Sciences, 22(23), 12869. DOI 10.3390/ijms222312869. [Google Scholar] [CrossRef]
17. Cesprini, E., Šket, P., Causin, V., Zanetti, M., Tondi, G. (2021). Development of quebracho (Schinopsis balansae) tannin-based thermoset resins. Polymers, 13(24), 4412. DOI 10.3390/polym13244412. [Google Scholar] [CrossRef]
18. Fraga-Corral, M., Garcia-Oliveira, P., Pereira, A. G., Lourenço-Lopes, C., Jimenez-Lopez, C. et al. (2020). Technological application of tannin-based extracts. Molecules, 25(3), 614. DOI 10.3390/molecules25030614. [Google Scholar] [CrossRef]
19. Li, J., Liao, J., Essawy, H., Zhang, J., Li, T. et al. (2021). Preparation and characterization of novel cellular/nonporous foam structures derived from tannin furanic resin. Industrial Crops & Products, 162, 113264. DOI 10.1016/j.indcrop.2021.113264. [Google Scholar] [CrossRef]
20. Liu, B., Zhou, Y., Essawy, H., Chen, Q., Liang, J. et al. (2022). Formaldehyde free tannin-based adhesive with epoxy as 2 hardeners for plywood. Maderas: Ciencia y Tecnologia, 24(33), 1–33. [Google Scholar]
21. Marie, Z., Nicolas, V., Celzard, A., Fierro, V. (2019). Experimental investigation of the physical foaming of tannin-based thermoset foams. Industrial Crops & Products, 138, 111424. DOI 10.1016/j.indcrop.2019.05.073. [Google Scholar] [CrossRef]
22. Morandini, M. C., Kain, G., Eckardt, J., Petutschnigg, A., Tippner, J. (2022). Physical-mechanical properties of peat moss (Sphagnum) insulation panels with Bio-based adhesives. Materials, 15(9), 3299. DOI 10.3390/ma15093299. [Google Scholar] [CrossRef]
23. Ndiwe, B., Pizzi, A., Tibi, B., Danwe, R., Konai, N. et al. (2019). African tree bark exudate extracts as biohardeners of fully biosourced thermoset tannin adhesives for wood panels. Industrial Crops & Products, 132, 253–268. DOI 10.1016/j.indcrop.2019.02.023. [Google Scholar] [CrossRef]
24. Santiago-Medina, F. J., Tenorio-Alfonso, A., Delgado-Sánchez, C., Basso, M. C., Pizzi, A. et al. (2018). Projectable tannin foams by mechanical and chemical expansion. Industrial Crops & Products, 120, 90–96. DOI 10.1016/j.indcrop.2018.04.048. [Google Scholar] [CrossRef]
25. Sepperer, T., Ket, P., Petutschnigg, A., Hüsing, N. (2021). Tannin-furanic foams formed by mechanical agitation: Influence of surfactant and ingredient ratios. Polymers, 13(18), 3058. DOI 10.3390/polym13183058. [Google Scholar] [CrossRef]
26. Sepperer, T., Tondi, G., Petutschnigg, A., Young, T. M., Steiner, K. (2020). Mitigation of ammonia emissions from cattle manure slurry by tannins and tannin-based polymers. Biomolecules, 10(4), 581. DOI 10.3390/biom10040581. [Google Scholar] [CrossRef]
27. Shirmohammadli, Y., Moradpour, P., Abdulkhani, A., Efhamisisi, D., Pizzi, A. (2019). Water resistance improvement by polyethyleneimine of tannin-furfuryl alcohol adhesives. International Wood Products Journal, 10(1), 16–21. DOI 10.1080/20426445.2019.1600814. [Google Scholar] [CrossRef]
28. Varila, T., Romar, H., Luukkonen, T., Hilli, T., Lassi, U. (2020). Characterization of lignin enforced tannin/furanic foams. Heliyon, 6(1), e03228. DOI 10.1016/j.heliyon.2020.e03228. [Google Scholar] [CrossRef]
29. Wu, X., Yan, W., Zhou, Y., Luo, L., Yu, X. et al. (2020). Thermal, morphological, and mechanical characteristics of sustainable tannin bio-based foams reinforced with wood cellulosic fibers. Industrial Crops & Products, 158, 113029. DOI 10.1016/j.indcrop.2020.113029. [Google Scholar] [CrossRef]
30. Zhang, J., Xi, X., Liang, J., Pizzi, A., Du, G. et al. (2019). Tannin-based adhesive cross-linked by furfuryl alcohol-glyoxal and epoxy resins. International Journal of Adhesion and Adhesives, 94, 47–52. DOI 10.1016/j.ijadhadh.2019.04.012. [Google Scholar] [CrossRef]
31. Zhang, J., Xiong, L., Zhou, X., Du, G., Liang, J. et al. (2019). Development of mimosa tannin-based adhesive cross-linked by furfuryl alcohol formaldehyde and epoxy resins. Wood Research, 64(5), 847–858. [Google Scholar]
32. Zhang, J., Liu, B., Zhou, Y., Essawy, H., Li, J. et al. (2021). Preparation and performance of tannin-glyoxal-urea resin-bonded grinding wheel loaded with SiO2 reinforcing particles. Maderas: Ciencia y Tecnología, 23(48), 1–16. DOI 10.4067/S0718-221X2021000100448. [Google Scholar] [CrossRef]
33. Zhou, X., Li, B., Xu, Y., Essawy, H., Wu, Z. et al. (2019). Tannin-furanic resin foam reinforced with cellulose nanofibers (CNF). Industrial Crops & Products, 134, 107–112. DOI 10.1016/j.indcrop.2019.03.052. [Google Scholar] [CrossRef]
34. Gérardin, P. (2016). New alternatives for wood preservation based on thermal and chemical modification of wood–A review. Annals of Forest Science, 73(1), 559–570. DOI 10.1007/s13595-015-0531-4. [Google Scholar] [CrossRef]
35. Lande, S., Westin, M., Schneider, M. (2008). Development of modified wood products based on furan chemistry. Molecular Crystals and Liquid Crystals, 484, 37–41. DOI 10.1080/15421400801901456. [Google Scholar] [CrossRef]
36. Mantanis, G. I. (2017). Chemical modification of wood by acetylation or furfurylation: A review of the present scaled-up technologies. BioResources, 12(2), 4478–4489. DOI 10.15376/biores.12.2.Mantanis. [Google Scholar] [CrossRef]
37. Nordstierna, L., Lande, S., Westin, M., Karlsson, O., Furó, I. (2008). Towards novel wood-based materials: Chemical bonds between lignin-like model molecules and poly (furfuryl alcohol) studied by NMR. Holzforschung, 62(6), 709–713. DOI 10.1515/HF.2008.110. [Google Scholar] [CrossRef]
38. Goldstein, I., Dreher, W. (1960). Stable furfuryl alcohol impregnating solutions. Industrial and Engineering Chemistry, 52(1), 57–58. DOI 10.1021/ie50601a039. [Google Scholar] [CrossRef]
39. Lande, S., Eikenes, M., Westin, M. (2004). Chemistry and ecotoxicology of furfurylated wood. Scandinavian Journal of Forest Research, 19, 14–21. DOI 10.1080/02827580410017816. [Google Scholar] [CrossRef]
40. Marefat Seyedlar, R., Imani, M., Mirabedini, S. M. (2016). Curing of poly (furfuryl alcohol) resin catalyzed by a homologous series of dicarboxylic acid catalysts: Kinetics and pot life. Journal of Applied Polymer Science, 133(43), 44009. DOI 10.1002/app.44009. [Google Scholar] [CrossRef]
41. Marefat Seyedlar, R., Imani, M., Mirabedini, S. M. (2017). Rheokinetics in curing process of polyfurfuryl alcohol: Effect of homologous acid catalysts. Iranian Polymer Journal (English Edition), 26(4), 281–293. DOI 10.1007/s13726-017-0518-0. [Google Scholar] [CrossRef]
42. NF X 41-568 (2014). Wood preservatives-laboratory method for obtaining samples for analysis to measure losses by leaching into water or synthetic sea water. European Committee for Standardization, AFNOR. [Google Scholar]
43. NF B51-126 (2007). NF B51-126-wood-based panels brinell hardness test. European Committee for Standardization. [Google Scholar]
44. EN 310 (1993). Determination of modulus elasticity on flextion and resistance on flextion. European Committee for Standardization. [Google Scholar]
45. EN 113 (1996). EN 113-wood preservatives—Determination of toxic values of wood preservatives against wood destroying basidiomycetes cultured on agar medium. European Committee for Standardization. [Google Scholar]
46. NCBI National Center for Biotechnology Information (2021). PubChem compound summary for CID 1110 (Succinic acidCID 875 (Tartaric acidCID (Adipic acid) 196. [Google Scholar]
47. Kocaefe, D., Huang, X., Kocaefe, Y. (2015). Dimensional stabilization of wood. Current Forestry Reports, 1, 151–161. DOI 10.1007/s40725-015-0017-5. [Google Scholar] [CrossRef]
48. Bodirlau, R., Teaca, C. A., Spiridon, I. (2008). Chemical modification of beech wood: Effect on thermal stability. BioResources, 3(3), 789–800. DOI 10.15376/biores. [Google Scholar] [CrossRef]
49. Sejati, P. S., Imbert, A., Gérardin-Charbonnier, C., Dumarçay, S., Fredon, E. et al. (2017). Tartaric acid catalyzed furfurylation of beech wood. Wood Science and Technology, 51(2), 379–394. DOI 10.1007/s00226-016-0871-8. [Google Scholar] [CrossRef]
50. Sweet, M. S., Winandy, J. E. (1999). Influence of degree of polymerization of cellulose and hemicellulose on strength loss in fire-retardant-treated southern pine. Holzforschung, 53(3), 311–317. DOI 10.1515/HF.1999.051. [Google Scholar] [CrossRef]
51. Winandy, J. E., Rowell, R. M. (2005). Chemistry of wood strength. In: Handbook of wood chemistry and wood composites. USA: CRC Press. [Google Scholar]
52. Winandy, J. E., Lebow, P. K. (2001). Modeling strength loss in wood by chemical composition. Part I. An individual component model for southern pine. Wood and Fiber Science, 33(2), 239–254. [Google Scholar]
53. Winandy, J. E., Morrell, J. J. (1992). Relationship between incipient decay, strength, and chemical composition of douglas-fir heartwood. Wood and Fiber Science, 25(3), 278–288. [Google Scholar]
54. Irbe, I., Elisashvili, V., Asatiani, M. D., Janberga, A., Andersone, I. et al. (2014). Lignocellulolytic activity of coniophora puteana and trametes versicolor in fermentation of wheat bran and decay of hydrothermally modified hardwoods. International Biodeterioration and Biodegradation, 86, 71–78. DOI 10.1016/j.ibiod.2013.06.027. [Google Scholar] [CrossRef]
55. Gupta, B. S., Jelle, B. P., Gao, T. (2015). Wood facade materials ageing analysis by FTIR spectroscopy. Proceedings of Institution of Civil Engineers: Construction Materials, 168(5), 219–231. [Google Scholar]
56. Tondi, G., Link, M., Oo, C. W., Petutschnigg, A. (2015). A simple approach to distinguish classic and formaldehyde-free tannin based rigid foams by ATR FT-IR. Journal of Spectroscopy, 2015, 902340. DOI 10.1155/2015/902340. [Google Scholar] [CrossRef]
57. Lems, E. M., Winklehner, S., Hansmann, C., Gindl-Altmutter, W., Veigel, S. (2019). Reinforcing effect of poly (furfuryl alcohol) in cellulose-based porous materials. Cellulose, 26(7), 4431–4444. DOI 10.1007/s10570-019-02348-6. [Google Scholar] [CrossRef]
58. Santiago-Medina, F. J., Pizzi1, A., Abdalla, S. (2017). Hydroxymethylfurfural hardening of pine tannin wood adhesives. Journal of Renewable Materials, 5(5), 435–447. DOI 10.7569/JRM.2017.634166. [Google Scholar] [CrossRef]
59. Martha, R., Mubarok, M., Batubara, I., Rahayu, I. S., Setiono, L. et al. (2021). Effect of furfurylation treatment on technological properties of short rotation teak wood. Journal of Materials Research and Technology, 12, 1689–1699. DOI 10.1016/j.jmrt.2021.03.092. [Google Scholar] [CrossRef]
60. Zhang, J., Wang, W., Zhou, X., Liang, J., Du, G. et al. (2019). Lignin-based adhesive crosslinked by furfuryl alcohol–glyoxal and epoxy resins. Nordic Pulp and Paper Research Journal, 34(2), 228–238. DOI 10.1515/npprj-2018-0042. [Google Scholar] [CrossRef]
Cite This Article
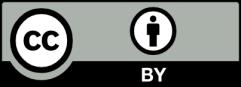
This work is licensed under a Creative Commons Attribution 4.0 International License , which permits unrestricted use, distribution, and reproduction in any medium, provided the original work is properly cited.