Open Access
REVIEW
Cellulose-Based Films for Food Packaging Applications: Review of Preparation, Properties, and Prospects
1 College of Food Science and Engineering, Henan University of Technology, Zhengzhou, 450001, China
2 Institute of Special Oilseed Processing and Technology, Henan University of Technology, Zhengzhou, 450001, China
* Corresponding Authors: Zhao Qin. Email: ; Huamin Liu. Email:
(This article belongs to the Special Issue: Advances in Application of Biomass-Based Materials in Food Industry)
Journal of Renewable Materials 2023, 11(8), 3203-3225. https://doi.org/10.32604/jrm.2023.027613
Received 08 November 2022; Accepted 16 January 2023; Issue published 26 June 2023
Abstract
Packaging is a food preservation technology widely used in the world. Naturally-sourced, biodegradable polymers are becoming increasingly popular in the food packaging sector. Packaging films prepared using cellulose as raw material would contribute to resource sustainability, but the difficulty of cellulose solubilization limits their further development. In view of this, a series of novel solvent systems (LiCl/DMAc, ILs, TBAH/DMSO, NMMO, alkali/urea solutions, metal-complex solutions) were used to prepare high-strength and high-performance cellulose-based films; their characteristics and the mechanisms involved were investigated. Composite films prepared by blending cellulose with various polymers (synthetic polymers, natural polymers, proteins and enzymes, metal particles, and plant phenols) and their functional properties were also investigated. Problems with cellulose-based films and the outlook for future research are discussed. It is hoped that in the near future high-performance, biodegradable and sustainably-produced cellulose-based films will lead the food packaging industry into a new era and further promote the sustainable use of resources.Graphical Abstract
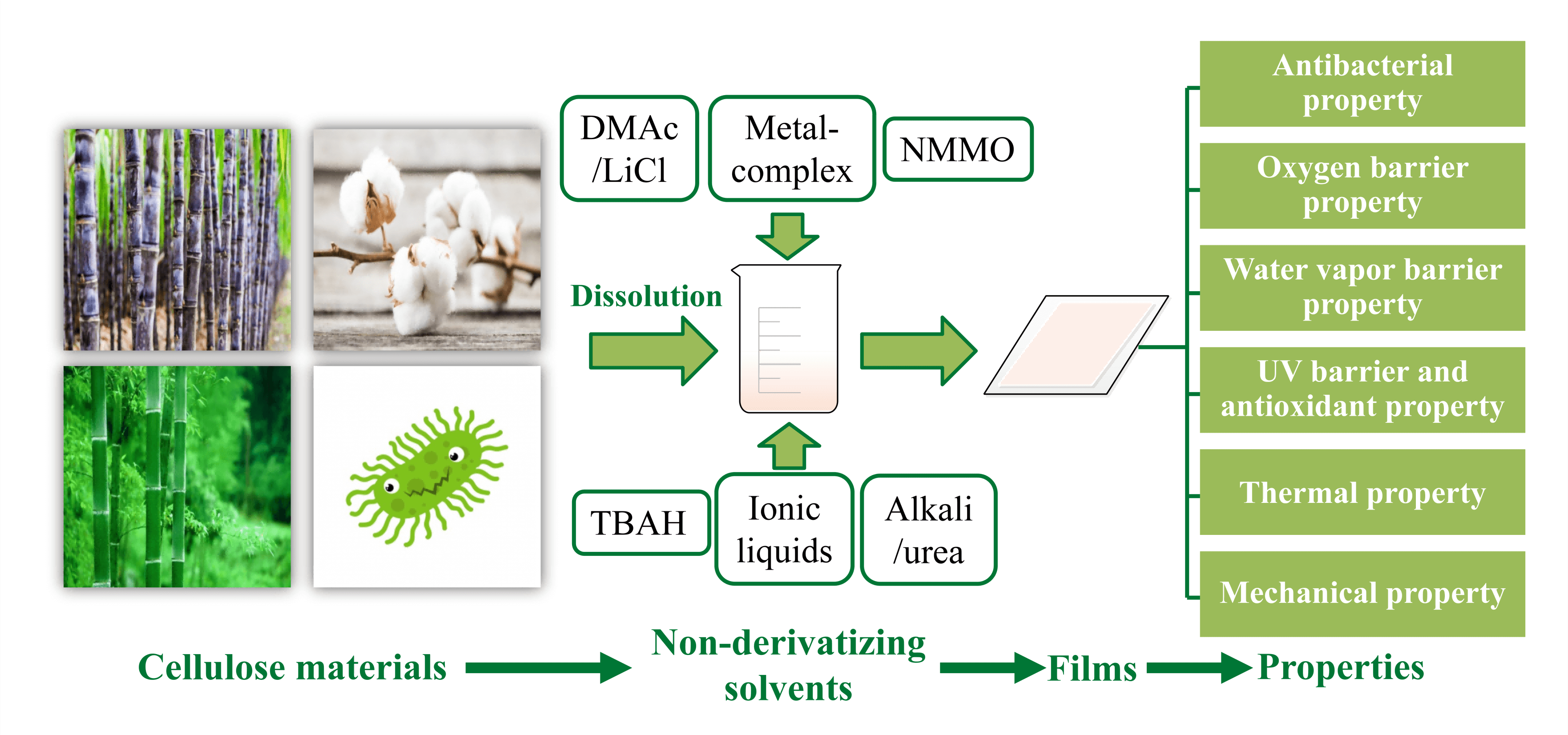
Keywords
Packaging is one of the most important unit operations in any food supply chain [1]. Suitable food packaging materials can maintain the quality of food (e.g., color, flavor, texture), inhibit the growth of microorganisms, and avoid lipid oxidation or loss of nutrients during transportation, storage, distribution, and use of food products [2].
Traditional food packaging materials include glass, metal, and plastic [3]. Glass and metal have excellent barrier properties. They can preserve volatile ingredients in the food while blocking the attack of oxygen and water vapor. However, glass materials are low in strength and fragile; metal materials are prone to denaturation and rusting. Both types of packaging increase production, transportation, and recycling costs [4]. A third type of packaging is plastic, i.e., petroleum-based derivatives. They have become a popular choice for packaging materials because of their ease of processing, low price, and durability. However, the massive use and indiscriminate disposal of plastics are causing serious ecological problems [5,6].
Given all of these factors, the demand for food packaging materials that are made from renewable, biodegradable biological resources has increased [7]. Packaging film is used to protect food from direct contact with the environment, and is widely used in the food packaging industry. Polylactic acid (PLA), polyhydroxy butyric acid (PHB), and thermoplastic starch are considered to be promising alternatives to petroleum-based packaging materials, particularly as packaging films. PLA is a fully biodegradable polymer that degrades to produce carbon dioxide and water. PHB is obtained by fermenting sugar; it can be degraded quickly and will not pollute the environment. However, these “bioplastics” have serious deficiencies—i.e., brittleness, thermal instability, susceptibility to degradation, and difficulty in heat sealing--that limit their development and use [8,9]. One solution to these problems is adding materials with complementary properties to these “bioplastics” to make them more suitable for commercial applications [6,9].
In recent years, cellulose, one of the most abundant natural substances in nature, has emerged as an eco-friendly material with the potential for use as a packaging material. Fig. 1 clearly illustrates this trend in research publications (the data is based on the search results of Web of Science). It is widely available (Fig. 2a), renewable and biodegradable. Cellulose is a natural linear polymer composed of β-(1,4)-linked D-glucose units. This macromolecular sugar chain consists of about 500–14000 D-glucose units [10,11], as seen schematically presented in Fig. 2b. The abundant hydroxyl groups in the cellulose molecular chains promote the formation of hydrogen bonds, thus allowing the molecular chains to form tight cellulose microfibrils by stacking one on top of the other [12]. The conformation of cellulose gives it properties required for bioengineering applications, such as biocompatibility, biodegradability, and appropriate mechanical properties (Fig. 2c). Additionally, cellulose has a high thermal resistance, as well as the ability to carry antioxidant and antibacterial agents [13]. Three problems block the widespread development of cellulose. First is solubility. Cellulose is not readily soluble in conventional solvents due to its complicated hydrogen bonding network and the presence of a partially crystalline region. Solubilization is necessary to develop cellulose into desirable products. The second problem is high hydrophilicity, and the third is the lack of antibacterial ability. Work is being done to address all of these challenges. For example, green solvents that break the hydrogen bonds in the cellulose structure have been investigated [14]. The properties of cellulose-based films have been improved by adding polymers to reduce their hydrophilicity and increase their bacterial inhibition ability [15]. Combining cellulose with bioplastic in composite films is another direction of research [9].
Figure 1: Number of references per year between 2011 and 2021 using the keywords ‘cellulose’, ‘film’, ‘cellulose’ and ‘film’
Figure 2: (a) common sources of cellulose; (b) chemical structure of cellulose; (c) advantages of cellulosic food packaging
Most of the past articles are about the applications of cellulose-based materials in textiles, water treatment, optical/electronic devices, biomedicine, etc. And we focus on the prospect of cellulose-based films in the field of food packaging materials. On this basis, this review discusses seven types of cellulose solvents and the mechanisms involved in the dissolution process, and briefly describes the polymers commonly used for the preparation of cellulose-based food packing films. The importance of barrier capacity, thermal stability, antioxidant capacity, antibacterial capacity, and mechanical strength of cellulose-based packaging films are summarized. Finally, prospects for the application of cellulose-based packaging films are presented.
Although many solvents have been developed to dissolve cellulose, there are still some outstanding problems in practical application, such as toxicity, high cost, non-recyclability, environmental pollution, and high volatility [16]. For example, in the viscose process, the toxic CS2 emitted from wastewater and exhaust gases may cause serious environmental problems [17]. Through the research by many groups, new cellulose solvents with good dissolution rates, better quality, fewer processing steps, and less generation of toxic substances have been developed [18,19]. The most promising new solvent systems are: ionic liquids (ILs), alkali/urea, N, N-dimethylacetamide/lithium chloride (DMAc/LiCl), N-methyl morpholine-N-oxide (NMMO), molten inorganic salt solutions, metal complex solutions, and tetrabutylammonium fluoride/dimethyl sulfoxide (DMSO) [20,21] as shown in Fig. 3. This section summarizes the dissolution mechanisms and the state of research on specific solvent systems.
Figure 3: Non-derivatizing solvent for cellulose
ILs are considered to be green solvents due to their non-volatility and reusability. They have excellent solvent properties, such as high thermal stability, high polarity, good electrical conductivity, and non-flammability [22]. They can efficiently dissolve and process most organic materials, such as wood and wool [23]. In general, ILs exist as liquids at temperatures below 100°C due to cations, anionic bulk, and dissymmetry [24]. The cations in IL systems are organic, while the anions can be organic or inorganic. Organic cations such as imidazolium, piperidinium, phosphonium, piperazine, ammonium, and pyridinium can be combined with anions such as halides and (CF3SO2)2N− to form various ILs [25]. The most common type of IL used to dissolve cellulose is imidazolium-based; these include 1-allyl-3-methylimidazolium chloride (AmimCl), 1-butyl-3-methylimidazolium acetate (BmimOAc), 1-ethyl-3-methylimidazolium acetate (EmimAC), and 1-ethyl-3-methylimidazolium diethyl phosphate (EmimDEP) [26]. Fig. 4 shows the mechanism of cellulose dissolution by ILs.
Figure 4: Dissolution mechanism of cellulose in ionic liquids (X represents Amim, Bmim, Emim or Hemim; Y is Cl, Ac, or BF4)
Xia et al. [27] used AmimCl as the solvent to fabricate cellulose-based film, and the film displayed good hydrophobicity and high tensile strength, as well as good UV-shielding properties. These properties give cellulose-based films considerable potential for applications in the packaging industry. In another study, Sundberg et al. [28] used EmimAc solution to dissolve three different molecular weights of cellulose (microcrystalline cellulose (MCC), spruce cellulose, and bacterial cellulose (BC)) to prepare the films. All films were free of EmimAc residues and exhibited good optical transparency. It is worth noting that the mechanical properties of the films were related to the length of the cellulose chains.
The main disadvantage of ILs is the high temperature required for dissolving cellulose in the process. In recent years, organic liquids can be used as co-solvents for imidazolium-based ILs due to the good solubility of ILs in many organic solvents [29]. Besides, the systems consisting of organic solutions and ILs mixed have low viscosity and easily dissolve cellulose at room temperature. Organic solvents commonly used as co-solvents are N, N-dimethylacetamide (DMAc), N, N-dimethylformamide (DMF), 1,3-dimethyl-2-imidazolinone (DMI), and dimethyl sulfoxide (DMSO) [30]. Xu et al. [31] prepared cellulose solvents by adding aprotic polar solvents to BmimOAc. The results showed that the new solvents can efficiently dissolve cellulose at 25°C due to the preferential solemnization of 1-butyl-3-methylimidazolium ([C4mim]+) by the aprotic polar solvent.
Deep eutectic solvents (DESs) are sustainable solvents and constitute a new category of ILs [32]. DESs are eutectic mixtures formed from Louis or Bronsted acids and bases, which have received much attention in the field of cellulose chemistry because of their low cost and environmental protection. However, in comparison with similar solvents, cellulose has a much lower solubility in DESs because the components of DESs usually involve hydrogen bonding interactions, making it difficult for them to break the hydrogen bonds of cellulose [32]. It is unclear whether DESs are a promising solvent for cellulose.
2.2 Lithium Chloride/N, N-Dimethylacetamide (DMAc/LiCl)
DMAc/LiCl is a classical non-aqueous cellulose solvent system that has played an important role in the history of the development of cellulose-based materials [33]. This system can solubilize cellulose with molecular weights above 106 without significant degradation of cellulose [34]. The dissolution of cellulose in the DMAc/LiCl system is due to the fact that the Cl− anions can form OH…Cl− bonds by attacking the OH protons between cellulose chains. Meanwhile, the Li+ cations are solvated by DMAc from Li+-DMAc. In order to maintain the balance of the solution system, the Li+-DMAc further binds to OH…Cl−, which helps to break the hydrogen bonds of cellulose chains, thus allowing the better dissolution of cellulose in the mixed solution [35].
Montoya-Rojo et al. [36] prepared films by dissolving the cellulose from Musaceae leaf sheaths in the DMAc/LiCl system. The film has excellent mechanical properties and optical transparency. Zhao et al. [37] successfully prepared cellulose films by regenerating cellulose from durian rind using a DMAc/LiCl solution system. The film has good biodegradability; it can be 100% degraded in soil within 4 weeks. Recently, one study investigated the relationship between the amount of LiCl (6%–10%) and the solubility of cellulose as well as the performance of regenerated films. The results showed that the solubility of cellulose in the DMAc/LiCl system decreased and the thermal stability of the regenerated films became worse with the increase in LiCl amount [38]. In another study, Gea et al. [39] compared the effect of the dissolution time of cellulose nanofibers (CNFs) from oil palm empty fruit bunches (OPEFB) in LiCl/DMAc solution on the films. Based on the SEM images, it can be seen that the composite films prepared with a dissolution time of 60 min have a smoother surface as well as higher transparency.
2.3 N-Methylmorpholine-N-Oxide (NMMO)
NMMO is an aliphatic cyclic tertiary amine oxide obtained by the reaction of diethylene glycol with ammonia to form morin, followed by methylation and oxidation [38]. According to the theory, the strongly polar and energetically dense N–O bonds of NMMO disrupt the intricate hydrogen bond network of cellulose and instead form hydrogen bonds with the solvent, ultimately causing cellulose to dissolve without the need for any additional activation, derivatization, or complexation [40]. The dissolution process of cellulose material in NMMO is shown in Fig. 5. The NMMO is completely biodegradable, non-toxic, and non-ecotoxic in comparison to the viscose (rayon) technique for treating cellulose, which has raised environmental concerns. Activation of cellulose by NMMO can increase the dissolution rate of cellulose. The shorter preparation time excludes potentially damaging processes in the system, preserving the quality of the film and the possibility to use regenerated solvent [41]. However, there are some unavoidable problems in using NMMO for the preparation of cellulose films. NMMO, as a strong oxidant, is very sensitive to many chemicals and involves a large number of complex homolytic (radical) and heterolytic (ionic) degradation reactions in the reaction system [42].
Figure 5: Dissolution process of cellulose materials in NMMO•H2O
It has been shown that three distinct types of stable hydrates, anhydrous NMMO, monohydrate NMMO (NMMO•H2O), and NMMO•2.5 H2O, can be formed when NMMO is combined with various ratios of water [43]. The best cellulose dissolver is the anhydrous NMMO, but because of its high melting point, it severely damages the cellulose molecules. In the presence of a large number of water molecules, the melting point of NMMO in NMMO•2.5 H2O was lowered, while the ability of NMMO•2.5 H2O to dissolve cellulose was also weakened. The 13.3% water-containing NMMO•H2O, because of its low melting point (76°C), can be used to dissolve cellulose with minimal cellulose damage. However, the water content in commercially available NMMO is typically 50%. Thus, when it is used to dissolve cellulose, the cellulose is so damaged it needs to be reprocessed [43]. When the water content of NMMO is 17%, NMMO can dissolve cellulose; however, as the water content increases, the ability of NMMO to dissolve cellulose decreases, and precipitation occurs. When the water content is below 4%, the dissolution temperature is close to the decomposition point of NMMO; therefore, the water content range of NMMO should be between 4%-17% for dissolving cellulose.
Peng et al. [44] used NMMO and distilled water (87:13 by weight) to dissolve cellulose at 100°C, and the prepared regenerated cellulose film had a dense surface, good light transmission (more than 80% at 600 nm), and good tensile strength (maximum strength reaches 149.5 MPa). Makarov et al. [45] attempted to prepare cellulose films from NMMO solid-phase activated BC, and the resulting films had a monolithic morphology with an average micropore size of 50 nm. This means the films could be used as packaging materials and have future development potential. Ichwan et al. [46] further investigated the effects of cellulose polymerization, concentration, and NMMO addition on the pore size and pore volume of regenerated films using NMMO monohydrate. The porosity and pore volume of these films decreased with decreasing cellulose DP, increasing cellulose concentration, and the addition of NMMO under certain conditions.
2.4 Alkali/Urea Aqueous Solution
Alkali hydroxide solution is an efficient non-derivative solvent widely used to dissolve cellulose. At low temperatures, it can dissolve cellulose with a degree of polymerization below 250. Urea has been introduced into an alkali hydroxide solution in order to improve its ability to dissolve cellulose. The addition (15% of solution weight) of urea increased the ability of the solution to dissolve cellulose by 1.5–2.5 times [47]. Urea does not have the ability to directly dissolve cellulose. The mechanism of cellulose dissolution in alkali/urea aqueous solution has been proposed as follows: Alkali hydroxides in the form of hydrates destroy intramolecular and intermolecular hydrogen bonds in cellulose chains, and urea hydrate prevents the recombination of cellulose molecules. The alkali hydroxide solution, urea, free water, and cellulose then form a special complex to stabilize the cellulose dissolution.
Currently, the alkali/urea aqueous solutions used as cellulose solvents are LiOH/urea and NaOH/urea. The ability of alkali hydroxides to dissolve cellulose differs between the different alkali metal cations, i.e., LiOH/urea is stronger than NaOH/urea. Huh et al. [48] compared the solubility of cellulose in different alkali/urea aqueous solutions using a combination of 3D-RISM and KBI. The results showed the ability of alkali metal hydroxides to dissolve cellulose in the order of LiOH > NaOH > KOH. KOH does not have the ability to dissolve cellulose. Li+ ions are closer to cellulose than Na+ ions, and the average distance between Li+ and the oxygen atoms in cellulose is shorter than between Na+ and oxygen [49]. As a result, the likelihood of finding Li+ ions near the cellulose is higher than the likelihood of finding Na+ ions. Yang et al. [50] used the alkali (NaOH or LiOH)/urea (AU) solutions as the solvent to prepare regenerated cellulose films, and the films all had excellent oxygen barrier properties, even better than conventional packaging materials. Qi et al. [51] successfully prepared transparent, structurally homogeneous cellulose-based films with excellent light transmission and good tensile strength in an aqueous NaOH/urea solution system pre-cooled to −12°C.
Li et al. [52] figured out that the removal of hemicellulose was the key to making high purity cellulose pulp, and investigated the effect on cellulose content of treating pulp with 1% urea/5% NaOH using 6.56% NaOH as a control. Results showed that the cellulose content of pulp treated with 1% urea/5% NaOH was higher than the pulp treated with 6.56% NaOH (96.02% and 93.94%, respectively). In another study, the relationship between molecular weight (6.8 × 104 to 13.5 × 104) and the solubility of cellulose in alkaline/urea water systems was investigated. Based on the analysis of the results, it is clear that the solubility of cellulose solutions decreases with increasing molecular weight of cellulose, but the stability and viscosity of cellulose solutions are basically constant [7]. The effects of NaOH/thiourea, NaOH/urea/thiourea, and NaOH/urea/ZnO were compared on cellulose solubility and films. Among them, the cellulose films prepared by NaOH/urea/ZnO had the highest tensile strength [53].
Inorganic salt hydrates are environmentally friendly, non-derivatizing, non-toxic, cheap, and easily recyclable solvent systems for dissolving cellulose [54]. Cellulose dissolved in inorganic salt hydrate does not require pretreatment, which gives these solvents broad development prospects. The ability of inorganic salt systems to dissolve cellulose is influenced by a number of factors, such as the species of inorganic salts, acidity, and water content. Many inorganic salt systems can dissolve cellulose: ZnCl2 hydrate, CaCl2 hydrate, LiI⋅hydrate, LiSCN⋅hydrate, as well as the mixture of NaSCN/KSCN with LiSCN⋅3H2O [55]. Shu et al. [56] dispersed cotton linter pulp (source of cellulose) in a ZnCl2/CaCl2 hydrate system and subsequently prepared cellulose films by solvent removal in ethanol solution. The results indicated that the regenerated films exhibited excellent optical, thermal, and mechanical properties. Based on a previous study [57] on the effect of the ZnCl2/CaCl2 hydrate system on the structure of the cellulose network, Lu et al. [58] prepared cellulose films using ZnCl2/CaCl2/cellulose mixture as raw materials by regeneration method, and crosslinked them with sodium lignosulfonate (SLS) through intermolecular hydrogen bonds and “bridge bonds”. The results showed that the antibacterial performance of films was improved due to the presence of phenolic hydroxyl and sulfonate groups from SLS in terms of the enlarged inhibition zone of E. coli and S. aureus.
2.6 Tetrabutylammonium Hydroxide (TBAH)
Tetrabutylammonium hydroxide (TBAH) is an aqueous solvent that has shown the ability to dissolve significant amounts of high molecular weight cellulose under mild conditions [59]. This mixture is a pure liquid at temperatures over 27°C; crystallization occurs at lower temperatures when the water molecules form clathrate cages. TBAH hydrate systems are quite stable throughout the dissolution process, which facilitates the recovery of solvent [60]. Therefore, the TBAH solvent has become a strong contender for industrial cellulose dissolution processing. Moreover, Zhang et al. [61] reported that TBAH as a cellulose solvent can dissolve up to 25% of cellulose at room temperature. Actually, unlike some solvent systems (e.g., ionic liquids, NMMO) that solubilize cellulose, the mechanism of solubilization by TBAH solvents is related to the hydrophobicity of natural cellulose. Both the cellulose and the TBAH solvents are amphipathic, which allows cellulose to be well dissolved in TBAH solvents. The amphiphilicity of TBAH solvent systems is related to temperature, concentration, co-solvent, and the molecular structure of the ammonium cation [59]. Medronho et al. [62] used DMSO as a co-solvent for TBAH (aq). The results showed that clear cellulose solutions could be easily obtained in a few minutes under mild conditions.
3 Blending of Cellulose with Other Polymers
Synthetic polymers are becoming more and more widely used, and their development has huge implications for the economy and the environment. Biodegradable biological-based synthetic polymers are degradable and renewable--therefore, they are environmentally friendly materials [63]. Fig. 6 illustrates the types of polymers that are often blended with cellulose as well as representative polymers. Among biodegradable materials, poly-3-hydroxybutyrate (PHB) and polylactic acid (PLA) are two of the most often utilized. However, these single synthetic polymers have poor heat stability, low elongation at break, and poor impact resistance, and they are soft. Due to these restrictions, they are unstable when subjected to heat manipulation, such as melting, which reduces their potential for use in many commercial applications [64]. Materials made of cellulose and nanocellulose (NC) are frequently utilized to enhance the qualities of different synthetic polymers. Studies have been conducted to combine cellulose with synthetic polymers, which can compensate to some extent for the deficiencies in the properties of synthetic polymers. The composite film with excellent mechanical properties and barrier properties has broad development prospects; it is likely to become widely used in the food packaging industry.
Figure 6: Other polymers that are often blended with cellulose and the representative polymers
In recent years, natural polymers have been in great demand in the industrial sector. They are frequently employed for food packaging because of their biodegradability and practicality from an economic standpoint. Due to its unique structure, cellulose is regarded as a good material for the creation of stable natural films. Other polymers lack strength, thermal stability, and desirable moisture or optical barrier properties [65]. Starch is another natural material often used to prepare laminated films. Straight-chain starch is a linear polymer that is easy to form and produces hard, transparent films due to hydrogen bonding interactions [66]. Therefore, the content of straight-chain starch determines the film-forming properties—and industrial potential-- of starch. However, pure starch films are permeable to moisture and brittle, and their ability to withstand the passage of light is very limited. The preparation of composite films by blending cellulose and NC with plant starch can not only reduce the cost but also improve the overall performance of the films. Chipón et al. [67] blended potato starch with cellulose nanocrystals (CNCs), and the results showed that starch-NC composites are well suited for food packaging and the production of bioplastics. Another polymer that has been employed to create composite films is the polysaccharide chitosan (CS). It can be successfully used as an antimicrobial packaging material to extend the shelf life of food, but the mechanical properties of CS are poor. The addition of plasticizers to CS films can improve their elongation at break, but the mechanical strength is substantially reduced. The presence of hydroxyl groups on cellulose creates the possibility of strong interaction with CS. Sadati et al. [68] prepared films by blending CS with CNF and showed that the barrier and mechanical properties of the films improved as the CNF content increased to 0.5 wt%. Thus, by blending cellulose with other natural polymers, novel, and high-quality packaging materials can be produced.
Protein-based films have the characteristics of simplicity of production, low cost, high practicality, and environmental “greenness”. However, the poor mechanical properties and barrier performance of protein-based films greatly limit their practical applications. In recent years, the development of composite packaging films by blending NC from different sources with a protein matrix has received widespread attention, and overall film performance can be improved by adding complementary film-forming components. For example, Yu et al. [69] used CNC and pine needle extract to develop soybean isolate protein (SPI) films; the addition of CNC led to a decrease in elongation at break, while the strong interaction formed with soy protein polypeptide chains improved the tensile strength of the film. The addition of CNC affected the hydrogen bonding between the N-H group of soy protein and water molecules, thus reducing the water content of the film. González et al. [70] used CNF isolated from bean hulls and pods to enhance the stiffness and resistance of SPI films, probably due to the formation of hydrogen bonds between the functional groups of SPI and the hydroxyl groups of CNF. Shabanpour et al. [71] found that the addition of BC increased the crystallinity and thermal stability of fish myofibrillar protein films. Gelatin is a linear polypeptide produced by the hydrolysis of collagen. However, the same poor mechanical and barrier properties of gelatin make it less used in the packaging industry. Pan et al. [72] prepared composite films by blending microcrystalline cellulose with gelatin. The tensile strength and modulus of elasticity of composite films with microcrystalline cellulose were improved, and the elongation at break and swelling ratios were decreased.
Nanoparticles of some metals have antibacterial activity, such as gold, silver, copper, iron, titanium, and zinc. Metal nanoparticles are able to deactivate microorganisms due to their continuous release of ions that microorganisms tend to adsorb from the reaction medium. Due to the small size of metal particles, they easily adhere to food surfaces and are readily absorbed into the blood when ingested, raising the possibility of liver damage. Therefore, these metal particles need to be used as packaging materials with suitable carriers to avoid as much contact as possible with food. The incorporation of carriers can also prevent agglomeration of metal particles. NC has lately been studied as a unique renewable and biocompatible support matrix due to its superior mechanical strength and biocompatibility. Mamatha et al. [73] prepared antimicrobial cellulose nanocomposite films of silver (Ag) and copper (Cu) bimetallic nanoparticles. The results showed that the bimetallic nanocomposites had higher strength and stability than the monometallic nanocomposite films. The nanocomposites showed good antibacterial activity against both Gram-positive and Gram-negative bacteria. Similarly, Deshmukh et al. [74] doped Au and Ag into CNF films, and these composite films with added metal nanoparticles showed better antioxidant activity and better mechanical properties compared to pristine CNF films. These cellulose nanocomposite films are good candidates for food packaging materials.
Plant phenols have a range of biological activities. Because they are rich in antimicrobial and antioxidant ingredients, when used as food packaging materials, they can reduce the growth of microorganisms and extend the shelf life of products. However, plant phenolic compounds are very sensitive to environmental factors during storage, and suitable matrices need to be selected to preserve their bioactivity. Such bioactive substances are well-suited for encapsulation in cellulose. Sanla-Ead et al. [75] prepared cellulose-based packaging films by mixing eugenol and cellulose. The results showed that the films were able to inhibit a wide range of food pathogenic and spoilage microorganisms (e.g., Aeromonas hydrophila, Enterococcus faecalis, and Saccharomyces cerevisiae). The authors concluded that the cellulose-based edible film could act as a reservoir for the release of eugenol to maintain the antibacterial properties on the food surface. In another study, Huang et al. [76] used nanoscale water-soluble lignin (6–14 nm) as a green enhancement material for CNF films. The results showed that the CNF films containing 10% water-soluble lignin nanoparticles could block 91.5% of UV-A light and 99.9% of UV-B light. Futhermore, the resulting lignin-based CNF films exhibited antibacterial activities against both Escherichia coli and Streptococcus hemolyticus.
4 Properties of Cellulose-Based Films
The use of oxygen barrier materials is becoming increasingly widespread in the food packaging industry. Oxidation in packaged meat, fruits, and vegetables can cause loss of nutrients, color changes, the production of undesirable odors, and—worst of all--the promotion of microbial growth. Grading materials according to their oxygen permeability would greatly facilitate the appropriate usage of different materials. Hult et al. [77] have made one attempt to establish such a scale. They suggest that a material can be considered to have a “strong oxygen barrier” if its oxygen permeability, measured at 25°C and 50% relative humidity, is less than 75 cm3•μm/(m2•day•atm).
Materials commonly used in packaging films include non-degradable (PP, PE and PS) and biodegradable (PLA and PHA) materials. However, because of their poor efficiency in maintaining an oxygen barrier, they are not used for highly perishable foods, such as fresh meat, nor for those very sensitive to oxidation, such as instant coffee. While biodegradable polymers such as PVA have high oxygen barrier properties under certain conditions (due to their hydrogen bonding), their high-water absorption capacity leads to a significant reduction in their oxygen barrier properties under humid conditions. This severely limits their application as food packaging materials. NCs have been reported to show excellent oxygen barrier properties, comparable to those of ethylene vinyl alcohol (EVOH) in the dry state [78]. NCs have the ability to form hydrogen bonds with themselves and with other biopolymers, thereby creating long rod-like or particles that interact through hydrogen bonding to form a dense network, culminating in a special laminar structure. This hinders the passage of various gas molecules due to the small pore size as shown in Fig. 7. In addition, the impermeability of their highly crystalline region to gases gives NCs good oxygen barrier properties [79]. Cellulose nanoparticles, with their high oxygen barrier properties, can be utilized as coatings for low oxygen barrier films, and employed to create composite films with other polymers. Pure cellulose nanoparticles are the basis for CNF, CNC, and BC films. These films are dense, smooth-surfaced, solid films created using a variety of techniques, including vacuum filtration, suspension drying, hot pressing, shear coating, and spin coating [80].
Figure 7: Schematic illustration of oxygen permeation through polymers with NC materials
Each processing method has a different impact on the packing density and free volume of the films produced. The 2,2,6,6-tetramethylpiperidine-1-oxyl radical (TEMPO) oxidation, enzymatic hydrolysis, and acidic hydrolysis of NC all affect the gas barrier properties of NC film materials [81]. NCs end up with a variety of crystalline structures, surface functional groups, and aspect ratios. Overall, this has an impact on the packing density, dispersion and surface energies, and hydroxyl number of the materials, which determine the film’s properties following solidification.
It has been shown that, due to the amorphous structure of CNF and the presence of hydroxyl groups on the surface of the molecule, the oxygen barrier strength of CNF films drastically decrease with increasing relative humidity [82]. In one study, the permeability of CNF increased 1000 times when the relative humidity increased from 0% to 65%, and the oxygen transmission rate (OTR) in the CNF films was about 17 mL/m2/day [78]. Zhang et al. [83] reported a CNF film produced by LiOH/urea/H2O solution, which has an OTR value of 3.34 mL/m2/day⋅atm at 0% relative humidity. Films containing large amounts of CNCs are less sensitive to humidity compared to CNF but are weaker oxygen barriers. The highly crystalline structure gives CNCs high brittleness and reduces the possibility of hydrogen bonding interactions, which leads to a weakening of oxygen barrier properties. According to Tyagi et al. [84], comparing paper coated with a double layer of CNF/CNC and uncoated paper, the air permeability was decreased by roughly 300 times, OTR by about 260 times, and WVTR by 30%.
Mixing in other polymers can improve the oxygen barrier qualities of cellulose films. In one study, researchers prepared a composite coating by adding chitosan to CNF to reduce oxygen diffusion, and the results indicated that the film’s ability to block oxygen became stronger with increasing CNF content [85]. In another noteworthy result, Mondragon et al. [86] created a film using gelatin and NCs. OTR values of the gelatin decrease after the addition of NCs, especially for 5 and 10 wt% contents due to the glass state of gelatin and the longer diffusion path created by the NCs.
4.2 Water Vapor Barrier Properties
A food’s shelf life is significantly influenced by the exchange of water vapor between it and its environment. With fresh foods like vegetables and meat, water loss must be prevented while with dry items like bread and puffed foods exposure to moisture in the environment must be prevented [76]. Table 1 shows the research progress in improving the water vapor barrier performance of cellulose-based composite films. The water contact angle is an important indicator of the hydrophilicity of the film surface; cellulose-based film surfaces with contact angle below 90° are considered hydrophilic, while above 90° are called hydrophobic surface. The contact angle depends on the size, pore size and roughness of the surface of the prepared film material. Shabanpour et al. [71] showed that the high surface roughness of the BC film can improve its hydrophilicity. Despite not being a water-soluble polymer, cellulose has many polar groups on its surface that interact with water molecules via hydrogen bonds. As a result, cellulosic materials slowly absorb or desorb water from the environment during storage and use until they reach an equilibrium moisture content (EMC) that matches the surrounding environment [87]. Hydrogen bonding between the cellulose chains also affects the solubility of the film, and the bonds are broken by the adsorbed water molecules, thus loosening the intermolecular interactions between the cellulose chains, promoting swelling, and raising the free volume, which has the effect of plasticizing. This not only changes the shape of the film material produced but also inevitably affects the quality of the food product. In addition, the permeability of oxygen in the film is directly impacted by the water vapor permeability (WVP) in the film. According to research, at 80% relative humidity, the presence of water-plasticized films containing cellulose fibers results in a 20-fold increase in OTR. At higher humidity levels, the gas diffusion rate spikes when water molecules weaken the cohesion of the film [88]. Factors affecting the water vapor transmission rate (WVTR) of polymeric composite films are pressure, temperature, crystallinity (diffusion and adsorption occur mainly in the amorphous regions of the polymer), hydrophilicity (polysaccharides are hydrophilic), film density, thickness, pore size, and structure. The use of films for prolonging food shelf life requires avoiding exposing them to moisture during transport, storage, and use of the film.
The moisture adsorption isotherm of the film predicts the moisture content in the polymer material in the range of water activity (aw) at a given temperature, as well as the expansion of water-polymer chain interactions [89]. Adsorption isotherms can be used to forecast stability and quality changes in packaged food products by studying the functional qualities as a function of moisture content. The Brunauer, Emmett, and Teller (BET) equation were, until a few years ago, the model that was most frequently employed to describe adsorption isotherms. The moisture content of the monolayer that had developed on the surface of the material could be estimated using this model. The BET model, however, falters at aw values greater than 0.5. The multilayer adsorption model developed by Guggenheim, Anderson, and de Boer (GAB) has drawn interest for the study of adsorption isotherms up to an aw of 0.90. The European Project Group COST 90 proposed the GAB model in 1985 for characterizing the moisture adsorption isotherms of food-related materials. The polymer samples interact with the water molecules in the microclimate in hermetically enclosed microclimates at various relative humidity levels (RHeq) at a specific temperature until they reach a moisture content equilibrium. The link between equilibrium moisture content and apparent water content in a material at a specific temperature is established when the aw of the film is equal to the RHeq at the equilibrium point. As a result, GAB can be used as a tool to estimate the moisture content of samples under a variety of environmental relative humidities [89].
4.3 UV Barrier and Antioxidant Properties
The covalent connections between organic components are not very strong, and ultraviolet (UV) photons have higher energy than visible light. Thus, UV photons can break the covalent bonds in some polymeric materials exposed to sunlight, which induces physical and/or chemical changes, ultimately degrading them. UV radiation, particularly UV-A (315–400 nm) and UV-B (280–315 nm) promote free radical generation through a variety of photochemical processes. These alterations in chemical composition can result in the oxidation of proteins, lipids, and vitamins as well as the breakdown of antioxidants, the development of off-tastes, and modifications of texture and color [90]. Therefore, the ability of packaging materials to block light has a significant effect on the quality of packaged products. This emphasizes the value of antioxidant and radical-scavenging capabilities in food packaging. Generally, the UV-shielding performance of CNF films is poor, and UV absorbers are needed to enhance their UV-shielding ability. Interestingly, it has been shown that heat treatment can improve the UV shielding of films. At a temperature of 160°C, CNF films had almost complete UV shielding ability while transmitting up to 72% of visible light [91]. In another study, the effects of pretreatment methods on the UV resistance of CNFs were compared. The results showed that the UV resistance of CNF films prepared with a hot water pretreatment was better than that of CNF films prepared with green liquor and sodium chlorite pretreatment [92]. The addition of some chemicals can also change the UV resistance of a film. Cazon et al. [93] prepared BC composite films by adding chitosan, and polyvinyl alcohol (PVOH). These films showed excellent UV-blocking properties, with constant UV-blocking values over a wide range of water activity. On this basis, they developed BC, glycerol, and PVOH composite films with GLY as a plasticizer. The films had good antioxidant and mechanical properties [94]. Wei et al. [95] used CNC as a base and added modified lignin to produce UV-blocking and antioxidant activities of CNC/lignin films with good thermal stability and high crystallinity.
Although some antioxidants can bind directly to food, the physicochemical nature of antioxidants can change the sensory properties of the food. Therefore, a packaging system is needed to control the release of these antioxidants. Lipid oxidation is one of the common reactions in food, which can lead to rancidity. Antioxidant compounds can play a role in delaying lipid oxidation in food. Some synthetic and natural substances show high antioxidant properties, such as berry polyphenols, essential oils, coffee leaves, and polypyrrole. Tannins with phenolic hydroxyl structures are natural plant antioxidants that have the functions of resisting biological oxidation and scavenging reactive oxygen species. Recently, Huang et al. [96] used tannins and cellulose to prepare a film that has good antioxidant, UV resistance, and mechanical properties and shows great potential for application in food packaging. Based on this, CNF-tannin-gelatin films with strong antioxidant properties have also been developed [97]. In addition, NC films with good antioxidant activity were successfully prepared by adding TOCNC-g-PEI nanoparticle-encapsulated oregano essential oil [98].
Mechanical properties directly determine the range of use and service life of the material in practical applications. Therefore, the mechanical properties of films play a decisive role in packaging. Table 2 shows the research progress in improving the mechanical strength properties of cellulose-based composite films. Cellulose-based materials are mainly used to prepare laminated films. The addition of cellulose contributes to polymer blending and enhances the mechanical properties of the film [83]. For packaging materials, Young’s modulus, stress (σ), strain (ε), and tensile strength (T) are the parameters generally used to evaluate a material’s mechanical characteristics. Supanakorn et al. [99] prepared ternary composite films using natural rubber, cellulose microfibers, and carboxymethylcellulose with excellent mechanical properties, biodegradability, and chemical resistance. Carboxymethylcellulose helped to establish the interaction between natural rubber and cellulose microfiber. The developed composite films have the advantages of good mechanical properties, high water absorption capacity, good water vapor permeability, solvent resistance, and biodegradability. Cebrián-Lloret et al. [100] prepared films from saccharin and cellulose residues of members of the Araliaceae family. The results showed that the higher the purity of the cellulose, the better the mechanical properties (elastic modulus of about 5∼7 GPa and elongation of about 3%∼5%) and appearance of the films. In another experiment, Yuwono et al. [101] investigated the effect of NC concentration (3%, 6%, and 9%) on the mechanical strength of the films. The results showed that the films prepared with an NC concentration of 9% were more prone to fracture when 2% hydroxypropyl methylcellulose (HPMC) was added. Li et al. [102] investigated the effect of unmodified MCC content on the mechanical properties of MCC/PLA biocomposite films by setting the unmodified MCC content to 0%, 5%, 10%, 15%, 20%, and 25%. The results of decreasing tensile strength and elongation at the break of the films were obtained with the increase of unmodified MCC content. Film strength is also related to the treatment temperature. The strength of the films gradually decreased as the treatment temperature increased from room temperature to 175°C. This is due to the decomposition of the amorphous cellulose polymer network and the increase in the crystallinity of the material leading to an increase in film brittleness. Additionally, it is thought that water acts as a plasticizing agent enhancing the tensile property of the material. With removal of the water held in the pores of the films, the plasticizing effect is reduced and the films show a loss of strength and an increase in brittleness [103].
In certain food packaging applications, especially involving reheatable food, the packaging must remain stable under high temperatures and prolonged heating conditions. In a study, the thermal stability of NFC films prepared from Mahang Gajah NFC and thin films from commercial NFC was compared. The results indicated they were similar [104]. Subsequently, Bian et al. [105] compared the effect of the methods of cellulose extraction (i.e., acid-base and extracting methods) on the thermal stability of regenerated films. The regenerated films prepared from cellulose extracted by the extracting method showed high thermal stability. Both the method of cellulose extraction and the presence of certain chemical substances affects the thermal stability of film. For example, cellulose/iron oxide was confirmed to be more thermally stable than cellulose films by improved integrated program decomposition temperature (IPDT) values [106]. The amount of cellulose added affects the thermal stability of cellulose-based composite films. Suwanprateep et al. [107] prepared films by blending cellulose fibers with rice starch bases. The content of rice starch in the films was maintained at 2%, and the mass fractions of cellulose fibers were 4%, 6%, and 8%. The results showed that the thermal stability increased with the increase of cellulose proportion. The highest thermal stability was obtained for the composite film with 8% cellulose fiber content.
Exposure to microorganisms in the environment affects the freshness and quality of food [108]. Thus, food packaging materials with antimicrobial properties can help prevent food spoilage caused by microorganisms. The biodegradable film based on cellulose and thiazolidine with extremely high UV blocking (99.8%) and with good antibacterial activity has been prepared [109]. In another experiment, the antibacterial ability of composite films prepared from enoki mushroom-mediated sulfur nanoparticles (SNPs), gelatin, and CNFs were studied. It was shown that the incorporation of SNPs had a strong antibacterial effect against foodborne pathogenic bacteria without significantly altering other physical properties of the films [110]. Hu et al. [111] prepared cellulose-based films containing lysozyme (lyys), and antibacterial tests showed that the films inhibited common foodborne pathogenic bacteria. Similarly, the cellulose-based composite film with the addition of blackcurrant anthocyanin (BCA) and konjac glucomannan (KGM) also inhibited foodborne pathogenic bacteria well [112]. Dhandapani et al. [113] prepared PVOH and cellulose-based films and then improved their properties by cross-linking the cellulose with amino acids. The results showed that L-histidine cross-linked PVA/cellulose films are a suitable material for food packaging applications with antimicrobial properties. Composite films with antibacterial effects have potentially broad applications in the development of new packaging materials.
In order to reduce environmental pollution caused by the excessive use of petroleum-based synthetic food packaging films, renewable, degradable, and environmentally friendly food packaging films have received more attention using natural polymers as raw materials. Cellulose has a great prospect in the field of food packing materials due to its widest source in nature and its special microstructure and properties. However, the complicated inter- and intramolecular hydrogen bonds within the cellulose network structure make it difficult to dissolve and further process. To address this problem, scientists have developed a range of new environmentally friendly solvents. Cellulose-based food packaging films prepared with these new solvent systems have a variety of barrier functions and excellent mechanical properties.
A series of cellulose solvent systems (LiCl/DMAc, ILs, TBAH/DMSO, NMMO, alkali/urea solutions, and metal-complex solutions) are reviewed here, and composite membranes prepared by blending cellulose with various polymers and their functional properties are presented. Although great breakthroughs have been made in the preparation of cellulose-based films, there are still some drawbacks that need to be addressed. For example, the green solvent used in the cellulose regeneration process is subject to its own, as well as some external, processing conditions. Second, the current industrial applications are limited by production costs and some material properties (e.g., poor water resistance). In order to realize the economic benefits of cellulose-based materials in the field of food packaging, quality, utility, and cost must be considered. Cellulose can be blended with various polymers to prepare composite films, and this approach must also be investigated. Therefore, future research and development of recycled cellulose films should be directed in the following directions. First, the development of new cellulose solvents that are efficient, stable, and easy to recover should be a priority. Second, the construction of high-performance (e.g., high-strength, hydrophobic, biodegradable) cellulose-based food packaging films should be promoted to further bring products to market. Third, new biodegradable and environmentally friendly materials should also be sought to blend with cellulose to develop composite films with multi-functionality. Through this research, packaging materials with high strength, antimicrobial properties, antioxidant properties, and biodegradability can be created, developed, and manufactured.
Funding Statement: This study was supported by the financial support of the Doctor Foundation of Henan University of Technology (No. 2021BS051), the Natural Science Foundation of Excellent Youth for Henan (222300420038).
Conflicts of Interest: The authors declare that they have no conflicts of interest to report regarding the present study.
References
1. Cazon, P., Vazquez, M., Velazquez, G. (2018). Cellulose-glycerol-polyvinyl alcohol composite films for food packaging: Evaluation of water adsorption, mechanical properties, light-barrier properties and transparency. Carbohydrate Polymers, 195, 432–443. https://doi.org/10.1016/j.carbpol.2018.04.120 [Google Scholar] [PubMed] [CrossRef]
2. Deng, J., Zhu, E. Q., Xu, G. F., Naik, N., Murugadoss, V. et al. (2022). Overview of renewable polysaccharide-based composites for biodegradable food packaging applications. Green Chemistry, 24(2), 480–492. https://doi.org/10.1039/d1gc03898b [Google Scholar] [CrossRef]
3. Alamri, M. S., Qasem, A. A. A., Mohamed, A. A., Hussain, S., Ibraheem, M. A. et al. (2021). Food packaging’s materials: A food safety perspective. Saudi Journal of Biological Sciences, 28(8), 4490–4499. https://doi.org/10.1016/j.sjbs.2021.04.047 [Google Scholar] [PubMed] [CrossRef]
4. Saravanakumar, K., Sathiyaseelan, A., Mariadoss, A. V. A., Xiaowen, H., Wang, M. H. (2020). Physical and bioactivities of biopolymeric films incorporated with cellulose, sodium alginate and copper oxide nanoparticles for food packaging application. International Journal of Biological Macromolecules, 153, 207–214. https://doi.org/10.1016/j.ijbiomac.2020.02.250 [Google Scholar] [PubMed] [CrossRef]
5. Mendes, A. C., Pedersen, G. A. (2021). Perspectives on sustainable food packaging: Is bio-based plastics a solution? Trends in Food Science & Technology, 112, 839–846. https://doi.org/10.1016/j.tifs.2021.03.049 [Google Scholar] [CrossRef]
6. Jiang, Z., Ngai, T. (2022). Recent advances in chemically modified cellulose and its derivatives for food packaging applications: A review. Polymers, 14(8), e1533. https://doi.org/10.3390/polym14081533 [Google Scholar] [PubMed] [CrossRef]
7. Xie, K., Tu, H., Dou, Z. L., Liu, D. Y., Wu, K. et al. (2021). The effect of cellulose molecular weight on internal structure and properties of regenerated cellulose fibers as spun from the alkali/urea aqueous system. Polymer, 215, e123379. https://doi.org/10.1016/j.polymer.2021.123379 [Google Scholar] [CrossRef]
8. Phuong, V. T., Verstichel, S., Cinelli, P., Anguillesi, I., Coltelli, M. B. et al. (2014). Cellulose acetate blends—Effect of plasticizers on properties and biodegradability. Journal of Renewable Materials, 2(1), 35–41. https://doi.org/10.7569/JRM.2013.634136 [Google Scholar] [CrossRef]
9. Huang, L. J., Xu, H., Zhao, H. Y., Xu, M. Z., Qi, M. H. et al. (2019). Properties of thermoplastic starch films reinforced with modified cellulose nanocrystals obtained from cassava residues. New Journal of Chemistry, 43(37), 14883–14891. https://doi.org/10.1039/c9nj02623a [Google Scholar] [CrossRef]
10. Trovatti, E. (2013). The future of bacterial cellulose and other microbial polysaccharides. Journal of Renewable Materials, 1(1), 28–41. https://doi.org/10.7569/JRM.2012.634104 [Google Scholar] [CrossRef]
11. Zhang, J. M., Luo, N., Zhang, X. Y., Xu, L. L., Wu, J. et al. (2016). All-cellulose nanocomposites reinforced with in situ retained cellulose nanocrystals during selective dissolution of cellulose in an ionic liquid. ACS Sustainable Chemistry & Engineering, 4(8), 4417–4423. https://doi.org/10.1021/acssuschemeng.6b01034 [Google Scholar] [CrossRef]
12. An, N. L., Qin, J. X., Zhou, X., Wang, Q. D., Fang, C. Q. et al. (2022). Recent progress in cellulose-based flexible sensors. Journal of Renewable Materials, 10(9), 2319–2334. https://doi.org/10.32604/jrm.2022.021030 [Google Scholar] [CrossRef]
13. Bayram, B., Ozkan, G., Kostka, T., Capanoglu, E., Esatbeyoglu, T. (2021). Valorization and application of fruit and vegetable wastes and by-products for food packaging materials. Molecules, 26(13), e4031. https://doi.org/10.3390/molecules26134031 [Google Scholar] [PubMed] [CrossRef]
14. Acharya, S., Liyanage, S., Parajuli, P., Rumi, S. S., Shamshina, J. L. et al. (2021). Utilization of cellulose to its full potential: A review on cellulose dissolution, regeneration, and applications. Polymers, 13(24), e4344. https://doi.org/10.3390/polym13244344 [Google Scholar] [PubMed] [CrossRef]
15. Zhang, B. X., Azuma, J. I., Uyama, H. (2015). Preparation and characterization of a transparent amorphous cellulose film. RSC Advances, 5(4), 2900–2907. https://doi.org/10.1039/c4ra14090g [Google Scholar] [CrossRef]
16. Yang, Y. J., Shin, J. M., Kang, T. H., Kimura, S., Wada, M. et al. (2014). Cellulose dissolution in aqueous lithium bromide solutions. Cellulose, 21(3), 1175–1181. https://doi.org/10.1007/s10570-014-0183-9 [Google Scholar] [CrossRef]
17. Pang, J. H., Liu, X., Wu, M., Wu, Y. Y., Zhang, X. M. et al. (2014). Fabrication and characterization of regenerated cellulose films using different ionic liquids. Journal of Spectroscopy, 2014, 1–8. https://doi.org/10.1155/2014/214057 [Google Scholar] [CrossRef]
18. Yang, M. K., Zhao, W. W., Wang, S. Z., Yu, C. Y., Singh, S. et al. (2019). Dimethyl sulfoxide assisted dissolution of cellulose in 1-ethyl-3-methylimidazoium acetate: Small angle neutron scattering and rheological studies. Cellulose, 26(4), 2243–2253. https://doi.org/10.1007/s10570-018-2218-0 [Google Scholar] [CrossRef]
19. Gao, X., Li, M., Zhang, H., Tang, X. N., Chen, K. L. (2021). Fabrication of regenerated cellulose films by DMAc dissolution using parenchyma cells via low-temperature pulping from Yunnan-endemic bamboos. Industrial Crops and Products, 160, e113116. https://doi.org/10.1016/j.indcrop.2020.113116 [Google Scholar] [CrossRef]
20. Takegawa, A., Murakami, M. A., Kaneko, Y., Kadokawa, J. I. (2010). Preparation of chitin/cellulose composite gels and films with ionic liquids. Carbohydrate Polymers, 79(1), 85–90. https://doi.org/10.1016/j.carbpol.2009.07.030 [Google Scholar] [CrossRef]
21. Shao, H. J., He, L., Xiang, L., Tang, K., Li, X. Z. et al. (2021). Transparent and UV-absorbing nanocellulose films prepared by directly dissolving microwave liquefied bamboo in TBAA/DMSO co-solvent system. Industrial Crops and Products, 171, e113926. https://doi.org/10.1016/j.indcrop.2021.113899 [Google Scholar] [CrossRef]
22. Rabideau, B. D., Soltani, M., Parker, R. A., Siu, B., Salter, E. A. et al. (2020). Tuning the melting point of selected ionic liquids through adjustment of the cation’s dipole moment. Physical Chemistry Chemical Physics, 22(21), 12301–12311. https://doi.org/10.1039/d0cp01214a [Google Scholar] [PubMed] [CrossRef]
23. Xu, Z., Zhou, Q. W., Wang, L. X., Xia, G. M., Ji, X. X. et al. (2021). Transparent cellulose-based films prepared from used disposable paper cups via an ionic liquid. Polymers, 13(23), e4209. https://doi.org/10.3390/polym13234209 [Google Scholar] [PubMed] [CrossRef]
24. Park, S., Oh, Y., Yun, J., Yoo, E., Jung, D. et al. (2020). Characterization of blended cellulose/biopolymer films prepared using ionic liquid. Cellulose, 27(9), 5101–5119. https://doi.org/10.1007/s10570-020-03152-3 [Google Scholar] [CrossRef]
25. Cassity, C. A., Siu, B., Soltani, M., McGeehee, J. L., Strickland, K. J. et al. (2017). The effect of structural modifications on the thermal stability, melting points and ion interactions for a series of tetraaryl-phosphonium-based mesothermal ionic liquids. Physical Chemistry Chemical Physics, 19(47), 31560–31571. https://doi.org/10.1039/c7cp06278h [Google Scholar] [PubMed] [CrossRef]
26. Azimi, B., Maleki, H., Gigante, V., Bagherzadeh, R., Mezzetta, A. et al. (2022). Cellulose-based fiber spinning processes using ionic liquids. Cellulose, 29(6), 3079–3129. https://doi.org/10.1007/s10570-022-04473-1 [Google Scholar] [CrossRef]
27. Xia, G. M., Zhou, Q. W., Xu, Z., Zhang, J. M., Ji, X. X. et al. (2021). Cellulose-based films with ultraviolet shielding performance prepared directly from waste corrugated pulp. Polymers, 13(19), e3359. https://doi.org/10.3390/polym13193359 [Google Scholar] [PubMed] [CrossRef]
28. Sundberg, J., Toriz, G., Gatenholm, P. (2013). Moisture induced plasticity of amorphous cellulose films from ionic liquid. Polymer, 54(24), 6555–6560. https://doi.org/10.1016/j.polymer.2013.10.012 [Google Scholar] [CrossRef]
29. Xia, J., King, A. W. T., Kilpeläinen, I., Aseyev, V. (2021). Phase-separation of cellulose from ionic liquid upon cooling: Preparation of microsized particles. Cellulose, 28(17), 10921–10938. https://doi.org/10.1007/s10570-021-04230-w [Google Scholar] [CrossRef]
30. Lopatina, A., Anugwom, I., Blot, H., Sánchez Conde, Á. S., Mänttäri, M. et al. (2021). Re-use of waste cotton textile as an ultrafiltration membrane. Journal of Environmental Chemical Engineering, 9(4), e105705. https://doi.org/10.1016/j.jece.2021.105705 [Google Scholar] [CrossRef]
31. Xu, A. R., Zhang, Y. J., Zhao, Y., Wang, J. J. (2013). Cellulose dissolution at ambient temperature: Role of preferential solvation of cations of ionic liquids by a cosolvent. Carbohydrate Polymers, 92(1), 540–544. https://doi.org/10.1016/j.carbpol.2012.09.028 [Google Scholar] [PubMed] [CrossRef]
32. Chen, Y. L., Zhang, X., You, T. T., Xu, F. (2019). Deep eutectic solvents (DESs) for cellulose dissolution: A mini-review. Cellulose, 26(1), 205–213. https://doi.org/10.1007/s10570-018-2130-7 [Google Scholar] [CrossRef]
33. Ali, N., Hamouda, H. I., Su, H., Li, F. L., Lu, M. (2020). Combinations of alkaline hydrogen peroxide and lithium chloride/N,N-dimethylacetamide pretreatments of corn stalk for improved biomethanation. Environmental Research, 186, e109563. https://doi.org/10.1016/j.envres.2020.109563 [Google Scholar] [PubMed] [CrossRef]
34. Zhang, S. M., Shan, S. Y., Zhang, H., Gao, X., Tang, X. N. et al. (2022). Antimicrobial cellulose hydrogels preparation with RIF loading from bamboo parenchyma cells: A green approach towards wound healing. International Journal of Biological Macromolecules, 203, 1–9. https://doi.org/10.1016/j.ijbiomac.2022.01.046 [Google Scholar] [PubMed] [CrossRef]
35. Dupont, A. L. (2003). Cellulose in lithium chloride/N,N-dimethylacetamide, optimisation of a dissolution method using paper substrates and stability of the solutions. Polymer, 44(15), 4117–4126. https://doi.org/10.1016/s0032-3861(03)00398-7 [Google Scholar] [CrossRef]
36. Montoya-Rojo, U., Alvarez-López, C., Ganan-Rojo, P. (2021). All-cellulose composites prepared by partial dissolving of cellulose fibers from musaceae leaf-sheath waste. Journal of Composite Materials, 55(22), 3141–3149. https://doi.org/10.1177/00219983211006886 [Google Scholar] [CrossRef]
37. Zhao, G. L., Lyu, X. M., Lee, J., Cui, X., Chen, W. N. (2019). Biodegradable and transparent cellulose film prepared eco-friendly from durian rind for packaging application. Food Packaging and Shelf Life, 21, e100345. https://doi.org/10.1016/j.fpsl.2019.100345 [Google Scholar] [CrossRef]
38. Egorov, Y. A., Makarova, V. V., Shandryuk, G. A., Kulichikhin, V. G. (2021). Behavior of cellulose–poly(N-vinylpyrrolidone) systems in N-methylmorpholine-N-oxide and new fibers on their basis. Polymer Science, Series A, 64(1), 38–52. https://doi.org/10.1134/s0965545x22010023 [Google Scholar] [CrossRef]
39. Gea, S., Andita, D., Rahayu, S., Nasution, D. Y., Rahayu, S. U. et al. (2018). Preliminary study on the fabrication of cellulose nanocomposite film from oil palm empty fruit bunches partially solved into licl/damc with the variation of dissolution time. Journal of Physics: Conference Series, 1116, 1–8. https://doi.org/10.1088/1742-6596/1116/4/042012 [Google Scholar] [CrossRef]
40. Kim, C. J., Khan, W., Kim, D. H., Cho, K. S., Park, S. Y. (2011). Graphene oxide/cellulose composite using NMMO monohydrate. Carbohydrate Polymers, 86(2), 903–909. https://doi.org/10.1016/j.carbpol.2011.05.041 [Google Scholar] [CrossRef]
41. Rosenau, T., French, A. D. (2021). N-Methylmorpholine-N-oxide (NMMOHazards in practice and pitfalls in theory. Cellulose, 28(10), 5985–5990. https://doi.org/10.1007/s10570-021-03860-4 [Google Scholar] [CrossRef]
42. Nguyen, H. V. D., de Vries, R., Stoyanov, S. D. (2020). Natural deep eutectics as a “Green” cellulose cosolvent. ACS Sustainable Chemistry & Engineering, 8(37), 14166–14178. https://doi.org/10.1021/acssuschemeng.0c04982 [Google Scholar] [CrossRef]
43. Rosenau, T., Potthast, A., Sixta, H., Kosma, P. (2001). The chemistry of side reactions and byproduct formation in the system NMMO/cellulose (Lyocell process). Progress in Polymer Science, 26(9), 1763–1837. https://doi.org/10.1016/S0079-6700(01)00023-5 [Google Scholar] [CrossRef]
44. Peng, J. W., Li, Y. N., Liu, X. L., Ke, G. Z., Song, D. P. et al. (2021). Cellulose film with air barrier and moisture-conducting character fabricated by NMMO. Journal of Materials Science, 56(32), 18313–18326. https://doi.org/10.1007/s10853-021-06499-5 [Google Scholar] [CrossRef]
45. Makarov, I. S., Shambilova, G. K., Vinogradov, M. I., Zatonskih, P. V., Gromovykh, T. I. et al. (2020). Films of bacterial cellulose prepared from solutions in N-Methylmorpholine-N-Oxide: Structure and properties. Processes, 8(2), 1–12. https://doi.org/10.3390/pr8020171 [Google Scholar] [CrossRef]
46. Ichwan, M., Son, T. W. (2012). Preparation and characterization of dense cellulose film for membrane application. Journal of Applied Polymer Science, 124(2), 1409–1418. https://doi.org/10.1002/app.35104 [Google Scholar] [CrossRef]
47. Isobe, N., Noguchi, K., Nishiyama, Y., Kimura, S., Wada, M. et al. (2013). Role of urea in alkaline dissolution of cellulose. Cellulose, 20(1), 97–103. https://doi.org/10.1007/s10570-012-9800-7 [Google Scholar] [CrossRef]
48. Huh, E., Yang, J. H., Lee, C. H., Ahn, I. S., Mhin, B. J. (2021). RISM-assisted analysis of role of alkali metal hydroxides in the solvation of cellulose in alkali/urea aqueous solutions. Cellulose, 28(18), 11247–11259. https://doi.org/10.1007/s10570-021-04214-w [Google Scholar] [CrossRef]
49. Wang, S., Lyu, K. J., Sun, P., Lu, A., Liu, M. L. et al. (2017). Influence of cation on the cellulose dissolution investigated by MD simulation and experiments. Cellulose, 24(11), 4641–4651. https://doi.org/10.1007/s10570-017-1456-x [Google Scholar] [CrossRef]
50. Yang, Q. L., Fukuzumi, H., Saito, T., Isogai, A., Zhang, L. N. (2011). Transparent cellulose films with high gas barrier properties fabricated from aqueous alkali/urea solutions. Biomacromolecules, 12(7), 2766–2771. https://doi.org/10.1021/bm200766v [Google Scholar] [PubMed] [CrossRef]
51. Qi, H., Chang, C., Zhang, L. (2009). Properties and applications of biodegradable transparent and photoluminescent cellulose films prepared via a green process. Green Chemistry, 11(2), 177–184. https://doi.org/10.1039/b814721c [Google Scholar] [CrossRef]
52. Li, J. G., Liu, X., Zheng, Q. H., Chen, L. H., Huang, L. L. et al. (2019). Urea/NaOH system for enhancing the removal of hemicellulose from cellulosic fibers. Cellulose, 26(11), 6393–6400. https://doi.org/10.1007/s10570-019-02587-7 [Google Scholar] [CrossRef]
53. Han, J., Seo, Y. (2021). Comparison of cellulose dissolution behavior by alkaline and sulfuric acid solvents and their films’ physical properties. Materials, 14(18), 5273. https://doi.org/10.3390/ma14185273 [Google Scholar] [PubMed] [CrossRef]
54. Mary, I. A., Selvanayagam, S., Selvasekarapandian, S., Srikumar, S. R., Ponraj, T. et al. (2019). Lithium ion conducting membrane based on K-carrageenan complexed with lithium bromide and its electrochemical applications. Ionics, 25(12), 5839–5855. https://doi.org/10.1007/s11581-019-03150-x [Google Scholar] [CrossRef]
55. Zhang, X. Q., Xiao, N. Y., Wang, H. H., Liu, C. F., Pan, X. J. (2018). Preparation and characterization of regenerated cellulose film from a solution in lithium bromide molten salt hydrate. Polymers, 10(6), 614. https://doi.org/10.3390/polym10060614 [Google Scholar] [PubMed] [CrossRef]
56. Shu, L., Zhang, X. F., Wang, Z., Yao, J. (2022). Structure reorganization of cellulose hydrogel by green solvent exchange for potential plastic replacement. Carbohydrate Polymers, 275, 118695. https://doi.org/10.1016/j.carbpol.2021.118695 [Google Scholar] [PubMed] [CrossRef]
57. Xu, Q., Chen, C., Rosswurm, K., Yao, T. M., Janaswamy, S. (2016). A facile route to prepare cellulose-based films. Carbohydrate Polymers, 149, 274–281. https://doi.org/10.1016/j.carbpol.2016.04.114 [Google Scholar] [PubMed] [CrossRef]
58. Lu, X., Que, H., Guo, H., Ding, C., Liu, X. et al. (2021). Α-cellulose-based films: Effect of sodium lignosulfonate (SLS) incorporation on physicochemical and antibacterial performance. Cellulose, 28(11), 7243–7256. https://doi.org/10.1007/s10570-021-03949-w [Google Scholar] [CrossRef]
59. Wang, M. D., Yu, T. T., Tan, L., Li, W., Wei, W. et al. (2020). An eco-friendly approach to preparing cellulose nanocrystals by precisely controlling the dissolution of natural cellulose in TBAH/H2O solvent. Cellulose, 27(16), 9311–9324. https://doi.org/10.1007/s10570-020-03418-w [Google Scholar] [CrossRef]
60. Li, W., Tan, L., Fan, Q. D., Wei, W., Zhou, Z. W. (2021). Effect of storage time and temperature on dissolved state of cellulose in TBAH-based solvents and mechanical property of regenerated films. Reviews on Advanced Materials Science, 60(1), 466–478. https://doi.org/10.1515/rams-2021-0034 [Google Scholar] [CrossRef]
61. Zhang, J. Y., Wang, M. D., Li, W., Wei, W., Li, J. Y. et al. (2019). TBAH/urea/H2O solvent for room temperature wet-spinning of cellulose and optimization of drawing process. Cellulose, 26(11), 6959–6977. https://doi.org/10.1007/s10570-019-02536-4 [Google Scholar] [CrossRef]
62. Medronho, B., Duarte, H., Magalhães, S., Alves, L., Valente, A. J. M. et al. (2017). From a new cellulose solvent to the cyclodextrin induced formation of hydrogels. Colloids and Surfaces A: Physicochemical and Engineering Aspects, 532, 548–555. https://doi.org/10.1016/j.colsurfa.2017.03.047 [Google Scholar] [CrossRef]
63. Jung, K., Corrigan, N., Wong, E. H. H., Boyer, C. (2022). Bioactive synthetic polymers. Advanced Materials, 34(2), e2105063. https://doi.org/10.1002/adma.202105063 [Google Scholar] [PubMed] [CrossRef]
64. Yu, H. Y., Qin, Z. Y., Zhou, Z. (2011). Cellulose nanocrystals as green fillers to improve crystallization and hydrophilic property of poly(3-hydroxybutyrate-co-3-hydroxyvalerate). Progress in Natural Science: Materials International, 21(6), 478–484. https://doi.org/10.1016/s1002-0071(12)60086-0 [Google Scholar] [CrossRef]
65. Diaz-Cruz, C. A., Caicedo, C., Jimenez-Regalado, E. J., de Leon, R. D., Lopez-Gonzalez, R. et al. (2022). Evaluation of the antimicrobial, thermal, mechanical, and barrier properties of corn starch-chitosan biodegradable films reinforced with cellulose nanocrystals. Polymers, 14(11), e2166. https://doi.org/10.3390/polym14112166 [Google Scholar] [PubMed] [CrossRef]
66. Chen, H. Y., Yuan, Y. L., Li, Q. Q. (2020). Preparation and characterization of corn starch-based composite films containing corncob cellulose and cassia oil. Starch—Stärke, 72(5–6), e1900209. https://doi.org/10.1002/star.201900209 [Google Scholar] [CrossRef]
67. Chipón, J., Ramirez, K., Morales, J., Diaz-Calderon, P. (2022). Rheological and thermal study about the gelatinization of different starches (potato, wheat and waxy) in blend with cellulose nanocrystals. Polymers, 14(8), e1560. https://doi.org/10.3390/polym14081560 [Google Scholar] [PubMed] [CrossRef]
68. Sadati, S. M. M., Shahgholian-Ghahfarrokhi, N., Shahrousvand, E., Mohammadi-Rovshandeh, J., Shahrousvand, M. (2021). Edible chitosan/cellulose nanofiber nanocomposite films for potential use as food packaging. Materials Technology, 37(10), 1276–1288. https://doi.org/10.1080/10667857.2021.1934367 [Google Scholar] [CrossRef]
69. Yu, Z. L., Sun, L., Wang, W., Zeng, W. C., Mustapha, A. et al. (2018). Soy protein-based films incorporated with cellulose nanocrystals and pine needle extract for active packaging. Industrial Crops and Products, 112, 412–419. https://doi.org/10.1016/j.indcrop.2017.12.031 [Google Scholar] [CrossRef]
70. González, A., Gastelu, G., Barrera, G. N., Ribotta, P. D., Igarzabal, C. I. A. (2019). Preparation and characterization of soy protein films reinforced with cellulose nanofibers obtained from soybean by products. Food Hydrocolloids, 89, 758–764. https://doi.org/10.1016/j.foodhyd.2018.11.051 [Google Scholar] [CrossRef]
71. Shabanpour, B., Kazemi, M., Ojagh, S. M., Pourashouri, P. (2018). Bacterial cellulose nanofibers as reinforce in edible fish myofibrillar protein nanocomposite films. International Journal of Biological Macromolecules, 117, 742–751. https://doi.org/10.1016/j.ijbiomac.2018.05.038 [Google Scholar] [PubMed] [CrossRef]
72. Pan, L., Li, P., Tao, Y. B. (2020). Preparation and properties of microcrystalline cellulose/fish gelatin composite film. Materials, 13(19), e4370. https://doi.org/10.3390/ma13194370 [Google Scholar] [PubMed] [CrossRef]
73. Mamatha, G., Sowmya, P., Madhuri, D., Babu, N. M., Kumar, D. S. et al. (2020). Antimicrobial cellulose nanocomposite films with in situ generations of bimetallic (Ag and Cu) nanoparticles using Vitex negundo leaves extract. Journal of Inorganic and Organometallic Polymers and Materials, 31(2), 802–815. https://doi.org/10.1007/s10904-020-01819-9 [Google Scholar] [CrossRef]
74. Deshmukh, A. R., Dikshit, P. K., Kim, B. S. (2022). Green in situ immobilization of gold and silver nanoparticles on bacterial nanocellulose film using punica granatum peels extract and their application as reusable catalysts. International Journal of Biological Macromolecules, 205, 169–177. https://doi.org/10.1016/j.ijbiomac.2022.02.064 [Google Scholar] [PubMed] [CrossRef]
75. Sanla-Ead, N., Jangchud, A., Chonhenchob, V., Suppakul, P. (2012). Antimicrobial activity of cinnamaldehyde and eugenol and their activity after incorporation into cellulose-based packaging films. Packaging Technology and Science, 25, 7–17. https://doi.org/10.1002/pts.952 [Google Scholar] [CrossRef]
76. Huang, G. X., Dong, H. L., Zhang, Z. P., Bian, H. Y., Yong, Q. (2020). Procuring the nano-scale lignin in prehydrolyzate as ingredient to prepare cellulose nanofibril composite film with multiple functions. Cellulose, 27, 9355–9370. https://doi.org/10.1007/s10570-020-03427-9 [Google Scholar] [CrossRef]
77. Hult, E. L., Iotti, M., Lenes, M. (2010). Efficient approach to high barrier packaging using microfibrillar cellulose and shellac. Cellulose, 17(3), 575–586. https://doi.org/10.1007/s10570-010-9408-8 [Google Scholar] [CrossRef]
78. Wang, J. W., Gardner, D. J., Stark, N. M., Bousfield, D. W. (2018). Moisture and oxygen barrier properties of cellulose nanomaterial-based film. ACS Sustainable Chemistry & Engineering, 6(1), 49–70. https://doi.org/10.1021/acssuschemeng.7b03523 [Google Scholar] [CrossRef]
79. Wu, Y. J., Liang, Y. Y., Mei, C. T., Cai, L. P., Nadda, A. et al. (2022). Advanced nanocellulose-based gas barrier materials: Present status and prospects. Chemosphere, 286, e131891. https://doi.org/10.1016/j.chemosphere.2021.131891 [Google Scholar] [PubMed] [CrossRef]
80. Jafarzadeh, S., Mohammadi Nafchi, A., Salehabadi, A., Oladzad-Abbasabadi, N., Jafari, S. M. (2021). Application of bio-nanocomposite films and edible coatings for extending the shelf life of fresh fruits and vegetables. Advances in Colloid and Interface Science, 291, e102405. https://doi.org/10.1016/j.cis.2021.102405 [Google Scholar] [PubMed] [CrossRef]
81. Du, L. X., Yu, H. N., Zhang, B. H., Tang, R. L., Zhang, Y. et al. (2021). Transparent oxygen barrier nanocellulose composite films with a sandwich structure. Carbohydrate Polymers, 268, e118206. https://doi.org/10.1016/j.carbpol.2021.118206 [Google Scholar] [PubMed] [CrossRef]
82. Wang, Y., Cao, X., Zhang, L. (2006). Effects of cellulose whiskers on properties of soy protein thermoplastics. Macromolecular Bioscience, 6(7), 524–531. https://doi.org/10.1002/mabi.200600034 [Google Scholar] [PubMed] [CrossRef]
83. Zhang, W. J., Zhang, Y. Q., Cao, J. K., Jiang, W. B. (2021). Improving the performance of edible food packaging films by using nanocellulose as an additive. International Journal of Biological Macromolecules, 166, 288–296. https://doi.org/10.1016/j.ijbiomac.2020.10.185 [Google Scholar] [PubMed] [CrossRef]
84. Tyagi, P., Lucia, L. A., Hubbe, M. A., Pal, L. (2019). Nanocellulose-based multilayer barrier coatings for gas, oil, and grease resistance. Carbohydrate Polymers, 206, 281–288. https://doi.org/10.1016/j.carbpol.2018.10.114 [Google Scholar] [PubMed] [CrossRef]
85. Resende, N. S., Gonçalves, G. A. S., Reis, K. C., Tonoli, G. H. D., Boas, E. V. B. V. (2018). Chitosan/cellulose nanofibril nanocomposite and its effect on quality of coated strawberries. Journal of Food Quality, 2018, 1–13. https://doi.org/10.1155/2018/1727426 [Google Scholar] [CrossRef]
86. Mondragon, G., Peña-Rodriguez, C., González, A., Eceiza, A., Arbelaiz, A. (2015). Bionanocomposites based on gelatin matrix and nanocellulose. European Polymer Journal, 62, 1–9. https://doi.org/10.1016/j.eurpolymj.2014.11.003 [Google Scholar] [CrossRef]
87. Tong, R. P., Chen, G. X., Tian, J. F., He, M. H. (2020). Highly transparent, weakly hydrophilic and biodegradable cellulose film for flexible electroluminescent devices. Carbohydrate Polymers, 227, e115366. https://doi.org/10.1016/j.carbpol.2019.115366 [Google Scholar] [PubMed] [CrossRef]
88. Xie, Y. J., Pan, Y. F., Cai, P. X. (2022). Hydroxyl crosslinking reinforced bagasse cellulose/polyvinyl alcohol composite films as biodegradable packaging. Industrial Crops and Products, 176, e114381. https://doi.org/10.1016/j.indcrop.2021.114381 [Google Scholar] [CrossRef]
89. Cazon, P., Velazquez, G., Vazquez, M. (2020). Bacterial cellulose films: Evaluation of the water interaction. Food Packaging and Shelf Life, 25, e100526. https://doi.org/10.1016/j.fpsl.2020.100526 [Google Scholar] [CrossRef]
90. Guo, R. S., Hu, K., He, P., Ni, Y. H., Liu, K. et al. (2020). Photochromic nanocellulose composite films with excellent anti-UV capacity. Applied Physics A, 126(10), e812. https://doi.org/10.1007/s00339-020-03988-3 [Google Scholar] [CrossRef]
91. Yang, W. S., Gao, Y., Zuo, C., Deng, Y. L., Dai, H. Q. (2019). Thermally-induced cellulose nanofibril films with near-complete ultraviolet-blocking and improved water resistance. Carbohydrate Polymers, 223, e115050. https://doi.org/10.1016/j.carbpol.2019.115050 [Google Scholar] [PubMed] [CrossRef]
92. Luo, L. X., Wang, X. C., Zhang, S., Yuan, X. J., Li, M. F. et al. (2021). Contribution of different pretreatments to the thermal stability and UV resistance performance of cellulose nanofiber films. Coatings, 11(2), e247. https://doi.org/10.3390/coatings11020247 [Google Scholar] [CrossRef]
93. Cazon, P., Vazquez, M., Velazquez, G. (2020). Environmentally friendly films combining bacterial cellulose, chitosan, and polyvinyl alcohol: Effect of water activity on barrier, mechanical, and optical properties. Biomacromolecules, 21(2), 753–760. https://doi.org/10.1021/acs.biomac.9b01457 [Google Scholar] [PubMed] [CrossRef]
94. Cazon, P., Vazquez, M., Velazquez, G. (2020). Characterization of mechanical and barrier properties of bacterial cellulose, glycerol and polyvinyl alcohol (PVOH) composite films with eco-friendly UV-protective properties. Food Hydrocolloids, 99, e105323. https://doi.org/10.1016/j.foodhyd.2019.105323 [Google Scholar] [CrossRef]
95. Wei, Z. C., Cai, C. Y., Huang, Y. Z., Wang, P., Song, J. Y. et al. (2020). Strong biodegradable cellulose materials with improved crystallinity via hydrogen bonding tailoring strategy for UV blocking and antioxidant activity. International Journal of Biological Macromolecules, 164, 27–36. https://doi.org/10.1016/j.ijbiomac.2020.07.100 [Google Scholar] [PubMed] [CrossRef]
96. Huang, X. D., Ji, Y. Z., Guo, L. K., Xu, Q. H., Jin, L. Q. et al. (2022). Incorporating tannin onto regenerated cellulose film towards sustainable active packaging. Industrial Crops and Products, 180, e114710. https://doi.org/10.1016/j.indcrop.2022.114710 [Google Scholar] [CrossRef]
97. Kriechbaum, K., Bergstrom, L. (2020). Antioxidant and UV-blocking leather-inspired nanocellulose-based films with high wet strength. Biomacromolecules, 21(5), 1720–1728. https://doi.org/10.1021/acs.biomac.9b01655 [Google Scholar] [PubMed] [CrossRef]
98. Wu, M., Yang, J., Chen, S. L., Lu, P., Wang, R. F. (2021). TOCNC-G-PEI nanoparticle encapsulated oregano essential oil for enhancing the antimicrobial activity of cellulose nanofibril packaging films. Carbohydrate Polymers, 274, e118654. https://doi.org/10.1016/j.carbpol.2021.118654 [Google Scholar] [PubMed] [CrossRef]
99. Supanakorn, G., Taokaew, S., Phisalaphong, M. (2021). Ternary composite films of natural rubber, cellulose microfiber, and carboxymethyl cellulose for excellent mechanical properties, biodegradability and chemical resistance. Cellulose, 28(13), 8553–8566. https://doi.org/10.1007/s10570-021-04082-4 [Google Scholar] [CrossRef]
100. Cebrián-Lloret, V., Metz, M., Martínez-Abad, A., Knutsen, S. H., Ballance, S. et al. (2022). Valorization of alginate-extracted seaweed biomass for the development of cellulose-based packaging films. Algal Research-Biomass Biofuels and Bioproducts, 61, e102576. https://doi.org/10.1016/j.algal.2021.102576 [Google Scholar] [CrossRef]
101. Yuwono, M., Fauziyah, B., Isnaeni, Nisak, A. (2020). Tensile strength and elongation analysis on nano cellulose film isolated from sugarcane bagasse. IOP Conference Series: Earth and Environmental Science, 456(1), 1–8. https://doi.org/10.1088/1755-1315/456/1/012088 [Google Scholar] [CrossRef]
102. Li, X., Deng, L. G., Li, Y., Li, K. (2020). Preparation of microcrystalline cellulose from bagasse bleached pulp reinforced polylactic acid composite films. Sugar Tech, 22(6), 1138–1147. https://doi.org/10.1007/s12355-020-00827-w [Google Scholar] [CrossRef]
103. Sharma, S., Zhang, X., Nair, S. S., Ragauskas, A., Zhu, J. et al. (2014). Thermally enhanced high performance cellulose nano fibril barrier membranes. RSC Advances, 4(85), 45136–45142. https://doi.org/10.1039/c4ra07469f [Google Scholar] [CrossRef]
104. Jasmani, L., Adnan, S., Ainun, Z. M. A. (2018). Nanofibrillated cellulose from mahang gajah as thin film. IOP Conference Series: Materials Science and Engineering, 368, 1–9. https://doi.org/10.1088/1757-899x/368/1/012015 [Google Scholar] [CrossRef]
105. Bian, H., Tu, P., Chen, J. Y. (2020). Fabrication of all-cellulose nanocomposites from corn stalk. Journal of the Science of Food and Agriculture, 100(12), 4390–4399. https://doi.org/10.1002/jsfa.10476 [Google Scholar] [PubMed] [CrossRef]
106. Yadav, M. (2018). Study on thermal and mechanical properties of cellulose/iron oxide bionanocomposites film. Composites Communications, 10, 1–5. https://doi.org/10.1016/j.coco.2018.04.010 [Google Scholar] [CrossRef]
107. Suwanprateep, S., Kumsapaya, C., Sayan, P. (2019). Structure and thermal properties of rice starch-based film blended with mesocarp cellulose fiber. Materials Today: Proceedings, 17, 2039–2047. https://doi.org/10.1016/j.matpr.2019.06.252 [Google Scholar] [CrossRef]
108. Ali, M. A. S. S., Jimat, D. N., Nawawi, W. M. F. W., Sulaiman, S. (2021). Antibacterial, mechanical and thermal properties of PVA/starch composite film reinforced with cellulose nanofiber of sugarcane bagasse. Arabian Journal for Science and Engineering, 47(5), 5747–5754. https://doi.org/10.1007/s13369-021-05336-w [Google Scholar] [CrossRef]
109. Baseer, R. A., Dacrory, S., El Gendy, M. A. M., Ewies, E. F., Kamel, S. (2022). A biodegradable film based on cellulose and thiazolidine bearing UV shielding property. Scientific Reports, 12(1), e7887. https://doi.org/10.1038/s41598-022-11457-5 [Google Scholar] [PubMed] [CrossRef]
110. Roy, S., Rhim, J. W. (2022). Gelatin/cellulose nanofiber-based functional films added with mushroom-mediated sulfur nanoparticles for active packaging applications. Journal of Nanostructure in Chemistry, 12(5), 979–990. https://doi.org/10.1007/s40097-022-00484-3 [Google Scholar] [CrossRef]
111. Hu, X. X., Liu, Y. F., Zhu, D. D., Jin, Y. G., Jin, H. B. et al. (2022). Preparation and characterization of edible carboxymethyl cellulose films containing natural antibacterial agents: Lysozyme. Food Chemistry, 385, e132708. https://doi.org/10.1016/j.foodchem.2022.132708 [Google Scholar] [PubMed] [CrossRef]
112. You, P. Q., Wang, L., Zhou, N., Yang, Y., Pang, J. (2022). A pH-intelligent response fish packaging film: Konjac glucomannan/carboxymethyl cellulose/blackcurrant anthocyanin antibacterial composite film. International Journal of Biological Macromolecules, 204, 386–396. https://doi.org/10.1016/j.ijbiomac.2022.02.027 [Google Scholar] [PubMed] [CrossRef]
113. Dhandapani, E., Suganthi, S., Vignesh, S., Dhanalakshmi, M., Kalyana Sundar, J. K. et al. (2020). Fabrication and physicochemical assessment of L-histidine cross-linked PVA/CMC bio-composite membranes for antibacterial and food-packaging applications. Materials Technology, 37(2), 124–134. https://doi.org/10.1080/10667857.2020.1816383 [Google Scholar] [CrossRef]
Cite This Article
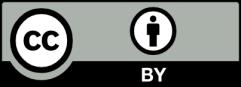